`
`SYNCHRONOUS BUCK INVERTER
`
`FIELD OF THE DISCLOSURE
`
`[0001]
`
`The present disclosure relates to power conversion, and, more specifically, the
`
`present disclosure relates to multi-stage switching for inverters, such as may utilize zero-cross
`
`discharge to reduce distortion and increase efficiency.
`
`BACKGROUND
`
`[0002]
`
`Certain power converters are configured to convert direct current (DC) to
`
`alternating current (AC). Such DC-ACconverters are commonly referred to as inverters.
`
`Inverters have many industrial and commercial uses including, for example, converting DC
`
`powcrfrom a battery or photovoltaic source into AC powerfor a load. Inverters may also be
`
`used to supply AC powerto an electric utility grid. A grid-tied inverter is a power inverter that
`
`converts direct current (DC) electricity into alternating current (AC) with an ability to
`
`synchronize to interface with a utility line. The applications for such an inverter include
`
`converting DC sources, such as solar panels or small wind turbines, into AC for tying with the
`
`grid. Photovoltaics (PV) in, for example, the aforementioned solar panels generate electrical
`
`powerby converting solar radiation into direct current electricity using semiconductors that
`
`exhibit the photovoltaic effect.
`
`[0003]
`
`Certain inverters arc commonly configured to opcrate without a transformer.
`
`Examples of such inverters are disclosed in Salmi, et al., ““Transformerless Microinverter for
`
`Photovoltaic Systems’, pp. 639-650, vol. 3, issue 4, Int’] Journal of Energy and Environment
`
`
`
`ATTY. DKT. 63219-821530 (JBL-0071-PV)
`
`(2012); Reddyet al., “Analysis and Modeling of Transformerless Photovoltaic Inverter
`
`Systems”, pp. 2932-2938, vol. 3, issue 5, Int’! Journal of Modern Engineering Research (2013);
`
`and Dreheret al., “Comparison of H-Bridge Single-Phase Transformerless PV String Inverters”’,
`
`10th TIEEE/IAS Int’1 Conference on Industry Applications, pp.1-8 (Nov. 2012).
`
`[0004]
`
`Photovoltaic (PV) power supplied to a utility grid is increasing in popularity as
`
`the world’s power demandsare increasing. Solid-state inverters have been shownto be an
`
`important technology for coupling PV systems into the grid. Integration of PV power generation
`
`systems in the grid plays an important role in supplying electric power in an environmentally-
`
`friendly manner. A commonly-configured grid-connected PV system comprises of a PV panel,
`
`and a DC/AC Inverter that is operatively connected to the grid. This configuration is used for
`
`powergeneration in places or sites accessed by the electric utility grid. Depending on the
`
`application and requirements, a PV system can either be a stand-alone or hybrid system.
`
`Gencrally the PV system comprises of a PV gcncrator whichis a set of scrics-parallcl electrically
`
`interconnected solar panels. PV panels are commonly rated in terms of a nominal peak powerof
`
`the panel at standard test conditions (STC). A PV generator provides the total installed power,
`
`whichis the sum of nominal peak powerof each solar panel present in the PV installation. This
`
`PV generator is connected to an inverter whichis, in turn, connected to an AC/DC load and/or
`
`grid.
`
`[0005]
`
`Inverters are important componentsto grid-connected PV systems and their major
`
`role is to convert DC power into AC power. Furthermore, inverter interfacing PV module(s)
`
`with the grid ensures that the PV module(s) is operated at the maximum power point (MPPT).
`
`Based on the photovoltaic arrays’ output voltage, output power level and applications, the
`
`
`
`ATTY. DKT. 63219-821530 (JBL-0071-PV)
`
`photovoltaic grid-connected system may adoptdifferent topologies. The grid-connected inverter
`
`may be designed for peak power and may obey conditionsrelated to issues like power quality,
`
`detection of islanding operation, grounding, MPPT and long-life. Inverter maximum poweris
`
`typically referred to the total installed powerof the PV generator, and should optimize the energy
`
`injected to grid. Inverter PV topologies may include centralized inverters, string inverters, multi-
`
`string inverter and module inverters.
`
`[0006]
`
`Although the foregoing discussion focuses particularly on PV systems, those
`
`skilled in the art will appreciate that issues that arise in PV systems similarly arise in other
`
`contexts that require power conversion/inversion. Such contexts include, but are not limited to,
`
`sine wave generating inverters, micro-inverters, power supplies, and powerdistribution systems.
`
`[0007]
`
`A significant one of these issues with conventional power inverters is that they
`
`carry excessive noise in the output signal. Therefore, improvements to inverter noise control,
`
`and accordingly efficiency, are neededin theart.
`
`SUMMARY
`
`[0008]
`
`Accordingly, an improved inverter topology is disclosed using high frequency
`
`switching control to generate a low frequency sine wave. The main switching may berealized
`
`using a synchronous-buck topologythat is configured to invert every half cycle of a lower
`
`frequency. The inverting process may create a positive and negative transition true sine wave.
`
`The low frequency switching stage may be configured to operate as a true zero voltage switching
`
`(ZVS) and zero current switching (ZCS) drive.
`
`
`
`ATTY. DKT. 63219-821530 (JBL-0071-PV)
`
`[0009]
`
`The disclosed inverter may be further configured with an output capacitor,
`
`wherein the charge on the output capacitor may be discharged to zero upon every zero crossing
`
`of the low frequency switching stage. The benefit of this topology, as comparedto a traditional
`
`synchronous buckinverter, is that the discharge of energy from the output storage capacitor
`
`every half cycle creates very low distortion. That is, during this discharge of energy, the zero
`
`crossing distortion in the low frequency sine waveis greatly reduced.
`
`[0010]
`
`Comparisons will be madeto a full-bridge topology, currently deployed in a
`
`majority of grid-tied inverters presently, to the presently disclosed exemplary embodimentsto
`
`demonstrate advantageous improvements in efficiency, load variation and total harmonic
`
`distortion.
`
`BRIEF DESCRIPTION OF THE FIGURES
`
`[OO11]
`
`The present disclosure will become more fully understood from the detailed
`
`description given herein below and the accompanying drawings whichare given by way of
`
`illustration only, and which thus do not limit the present disclosure, and wherein:
`
`[0012]
`
`FIG. 1A illustrates an exemplary full bridge inverter topology that is known in the
`
`art;
`
`[0013]
`
`VIG. 1B illustrates a switching sequence for switches S1-S4 of PIG. 1A under a
`
`positive half wave and negative half wave condition;
`
`[0014]
`
`FIGs. 2A-2E illustrate waveforms exemplifying typical operational conditions for
`
`the example of FIG. 1A;
`
`
`
`ATTY. DKT. 63219-821530 (JBL-0071-PV)
`
`[0015]
`
`FIG. 3A illustrates an exemplary synchronous buck inverter topology under one
`
`exemplary embodiment, where the inverter comprises a high-frequency switching portion, a
`
`synchronous buck portion and a low frequency switching stage coupled to a discharge capacitor
`
`configured to be coupledto a load;
`
`[0016]
`
`FIG.3B illustrates a switching sequence for switches A-D of the embodimentof
`
`FIG. 3A underpositive half wave and negative half wave conditions;
`
`[0017]
`
`T'IG. 3C provides another illustration of a synchronous buck inverter under
`
`another embodiment;
`
`[0018]
`
`FIG.4 illustrates a switch sequence diagram that includes four switching sections
`
`over the course of an exemplary sine wave for switches A-D of the embodiments of FIG. 3A and
`
`3C;
`
`[0019]
`
`T'IGs. 4A-B illustrate an exemplary switching transitions of switches A-D ofthe
`
`embodiment of FIG. 3A during a first switching section (at peak of positive sine wave) of FIG.
`
`4;
`
`[0020]
`
`FIG 4C schematically illustrates a synchronous current flow through a load and a
`
`switching configuration for switches A-D for time period (a) of FIG. 4B under one exemplary
`
`embodiment;
`
`[0021]
`
`FIG 4D schematically illustrates a buck current flow through a load and a
`
`switching configuration for switches A-D for time period (b) of FIG. 4B under one exemplary
`
`embodiment;
`
`
`
`ATTY. DKT. 63219-821530 (JBL-0071-PV)
`
`[0022]
`
`FIGs. 4E-Fillustrate an exemplary switching transitions of switches A-D of the
`
`embodiment of FIG. 3A during a second switching section (at positive-negative zero crossing
`
`transition of sine wave) of FIG.4;
`
`[0023]
`
`FIG 4G schematically illustrates a buck/synchronous current flow through a load
`
`and a switching configuration for switches A-D for time period (a) of FIG. 4F under one
`
`exemplary embodiment;
`
`[0024]
`
`T'IG 411 schematically illustrates a synchronous/buck current flow through a load
`
`and a switching configuration for switches A-D for time period (b) of FIG. 4F under one
`
`exemplary embodiment;
`
`[0025]
`
`FIGs. 4]-J illustrate an exemplary switching transitions of switches A-D of the
`
`embodiment of FIG. 3A during a third switching section (at peak negative of sine wave) of FIG.
`
`4;
`
`[0026]
`
`FIG 4K schematically illustrates a synchronouscurrent flow through a load and a
`
`switching configuration for switches A-D for time period (a) of FIG. 4J under one exemplary
`
`embodiment;
`
`[0027]
`
`FIG 4L schematically illustrates a buck current flow through a load and a
`
`switching configuration for switches A-D for time period (b) of PIG. 4] under one exemplary
`
`embodiment;
`
`
`
`ATTY. DKT. 63219-821530 (JBL-0071-PV)
`
`[0028]
`
`FIGs. 4M-Nillustrate an exemplary switching transitions of switches A-D of the
`
`embodiment of FIG. 3A during a fourth switching section (at negative-positive zero crossing
`
`transition of sine wave) of FIG.4;
`
`[0029]
`
`FIG 40 schematically illustrates a synchronous/buck current flow through a load
`
`and a switching configuration for switches A-D for time period (a) of FIG. 4N under one
`
`exemplary embodiment;
`
`[0030]
`
`T'IG 4P schematically illustrates a buck/synchronouscurrent flow through a load
`
`and a switching configuration for switches A-D for time period (b) of FIG. 4N under one
`
`exemplary embodiment;
`
`[0031]
`
`FIGs. 5A-B illustrate an exemplary gate drive waveform and current waveform
`
`for a positive signal condition for switches A andBforthe first switching section illustrated in
`
`the exemplary embodiments of FIG. 4A-D above;
`
`[0032]
`
`FIGs. 6A-B illustrate an exemplary gate drive waveform and current waveform
`
`for a zero crossing condition for switches A and B for the second switching section illustrated in
`
`the exemplary embodiments of FIG. 4E-G above;
`
`[0033]
`
`FIGs. 7A-B illustrate an exemplary gate drive waveform and current waveform
`
`for a negative signal condition for switches A and B for the third switching section illustrated in
`
`the exemplary embodiments of FIG. 4I-L above;
`
`
`
`ATTY. DKT. 63219-821530 (JBL-0071-PV)
`
`[0034]
`
`FIGs. 8A-B illustrate an exemplary gate drive waveform and current waveform
`
`for a zero crossing signal condition for switches A and B for the fourth switching section
`
`illustrated in the exemplary embodiments of FIG. 4M-P above;
`
`[0035]
`
`FIGs. 9A-E illustrate waveforms exemplifying operational conditions for the
`
`embodiment of FIG. 3A;
`
`[0036]
`
`FIG. 10A illustrates an exemplary waveform for the synchronous-buckinverter of
`
`TIG. 3A and FIG. 4 showing improved voltage and current distortion; and
`
`[0037]
`
`FIG. 10B illustrates an exemplary gate drive waveform for switches C and D for
`
`the synchronous-buck inverter of FIG. 3A and FIG.4.
`
`DETAILED DESCRIPTION
`
`[0038]
`
`The figures and descriptions provided herein may have been simplified to
`
`illustrate aspects that are relevant for a clear understanding of the herein described devices,
`
`systems, and methods, while eliminating, for the purpose of clarity, other aspects that may be
`
`found in typical similar devices, systems, and methods. Those of ordinary skill may thus
`
`recognize that other elements and/or operations may be desirable and/or necessary to implement
`
`the devices, systems, and methods described herein. But because such elements and operations
`
`are knownin the art, and because they do not facilitate a better understanding ofthe present
`
`disclosure, a discussion of such elements and operations may not be provided herein. However,
`
`the present disclosure is deemed to inherently include all such elements, variations, and
`
`modifications to the described aspects that would be knownto those of ordinary skill in theart.
`
`
`
`ATTY. DKT. 63219-821530 (JBL-0071-PV)
`
`[0039]
`
`Exemplary embodiments are provided throughoutso that this disclosure is
`
`sufficiently thorough and fully conveys the scope of the disclosed embodiments to those who are
`
`skilled in the art. Numerousspecific details are set forth, such as examples of specific
`
`components, devices, and methods, to provide this thorough understanding of embodiments of
`
`the present disclosure. Nevertheless, it will be apparent to those skilled in the art that specific
`
`disclosed details need not be employed, and that exemplary embodiments may be embodied in
`
`different forms. As such, the exemplary embodiments should not be construed to limit the scope
`
`of the disclosure. In some exemplary embodiments, well-known processes, well-known device
`
`structures, and well-known technologies may not be described in detail.
`
`[0040]
`
`The terminology used herein is for the purpose of describing particular exemplary
`
`embodiments only and is not intendedto be limiting. As used herein, the singular forms "a",
`
`"an
`
`and "the" may be intended to include the plural forms as well, unless the context clearly indicates
`ott
`tts
`"including," and "having," arc inclusive and
`
`otherwise. ‘he terms "compriscs,”
`
`"comprising,"
`
`therefore specify the presence of stated features, integers, steps, operations, elements, and/or
`
`components, but do not preclude the presence or addition of one or more other features, integers,
`
`steps, operations, elements, components, and/or groups thereof. The steps, processes, and
`
`operations described herein are not to be construed as necessarily requiring their respective
`
`performancein the particular order discussedor illustrated, unless specifically identified as a
`
`preferred order of performance.It is also to be understoodthat additional or alternative steps may
`
`be employed.
`
`[0041]
`
`mor
`When an elementor layer is referred to as being "on",
`
`moot
`"engaged to”,
`
`"connected
`
`to" or "coupled to" another elementor layer, it may be directly on, engaged, connected or
`
`
`
`ATTY. DKT. 63219-821530 (JBL-0071-PV)
`
`coupled to the other element or layer, or intervening elements or layers may be present. In
`
`contrast, when an element is referred to as being "directly on," "directly engaged to", "directly
`
`connected to" or "directly coupled to" another elementor layer, there may be no intervening
`
`elements or layers present. Other words used to describe the relationship between elements
`
`should be interpreted in a like fashion (e.g., "between" versus "directly between,”
`
`"adjacent"
`
`versus "directly adjacent," etc.). As used herein, the term "and/or" includes any and all
`
`combinations of one or more of the associated listed items.
`
`[0042]
`
`Although the termsfirst, second, third, etc. may be used herein to describe various
`
`elements, components, regions, layers and/or sections, these elements, components, regions,
`
`layers and/orsections should not be limited by these terms. These terms may be only used to
`
`distinguish one element, component, region, layer or section from another element, component,
`
`region, layer or section. Terms such as "first,"
`
`"second," and other numerical terms when used
`
`hercin do not imply a sequence or order unless clearly indicated by the context.
`
`‘Thus, a first
`
`element, component, region, layer or section discussed below could be termed a second element,
`
`component, region, layer or section without departing from the teachings of the exemplary
`
`embodiments.
`
`[0043]
`
`Turning now to FIG. 1A, a conventional inverter is illustrated and will be used for
`
`reference for the embodiments discussed throughout, such as in connection with the discussion
`
`of FIGs. 3A-10B. It should be understood by those skilled in the art that the specific
`
`configuration in FIG. 1A is merely used for illustrative purposes andis not intended to limit the
`
`present disclosure.
`
`10
`
`
`
`ATTY. DKT. 63219-821530 (JBL-0071-PV)
`
`[0044]
`
`The inverter of FIG. 1A is configured as a full-bridge inverter topology and
`
`comprises of four switches, two output inductors and an output storage capacitor. In this case,
`
`L2 maybe the same as L1 andthe total common-modevoltage Vem is ’Vnc. Conventionally,
`
`the full-bridge uses one of two control strategies. For the bipolar PWM control strategy, one
`
`group of diagonal switches operates at a switching frequency complementaryto the other group
`
`of switches. As a result, the inverter output voltage has only two levels which results in high
`
`current ripple across the output inductors. An exemplary switching sequencefor the circuit of
`
`FIG. 1A is shown where, for a sine wave input, switches S,; and S, are closed, while switches S2
`
`and S3 are open on the positive half wave of the input. Conversely, switches S; and Sy are open,
`
`while switches $2 and $3 are closed on the negative half wave of the input.
`
`[0045]
`
`The major drawback of employing the full-bridge with, for example, bipolar
`
`PWM isthe high powerlosses due to two [actors. Thefirst factor is the internal reactive power
`
`flow inside the inverter, and the second is the double switching frequency required to obtain the
`
`same inductor current ripple frequency. The second control strategy that may be applied to the
`
`full-bridge of FIG. 1A is the unipolar PWM. In such modulation, the inverter output voltage has
`
`three levels, which decreases significantly the current ripple across the inductors. With this
`
`modulation, the inverter has high efficiency due to the absence of the internal reactive power
`
`flow. However, with this control strategy, the inverter generates high leakage currentlevel.
`
`[0046]
`
`Accordingly, other topologies have endeavored to combine the advantages of the
`
`bipolar PWM (Cow leakage current level) and those of the unipolar PWM (Highefficiency, low
`
`current ripple and three level inverter output voltages). These endeavors have been undertaken
`
`by adding extra switches to the full-bridge topology. These extra switches disconnect the PV
`
`11
`
`
`
`ATTY. DKT. 63219-821530 (JBL-0071-PV)
`
`array from the grid during the freewheeling periods. Nevertheless, these and like circuits such as
`
`that illustrated in FIG. 1A carry excessive harmonic distortions in the signal, and thus operate at
`
`a reducedefficiency.
`
`[0047]
`
`FIG. 2A is an exemplary simulated waveform for the circuit of FIG. 1A, operating
`
`under a -0.7 power factor (PF) load, utilizing 100Q in series with a 26.54 uF capacitor. As can
`
`be determined from the voltage (V) and current (I) waveforms, voltage distortion is
`
`approximately 24%, while current distortion is approximately 34.1%. As will be appreciated by
`
`those skilled in the art, the distortion is particularly acute around the zero crossing phases. As
`
`the resistance is reduced to 20.63Q in series with a 130.3 uF capacitor, the total harmonic
`
`distortion increases to a point that it could not be measured,as illustrated in FIG. 2B.
`
`[0048]
`
`In FIG. 2C, utilizing a unity power factor load of 1kQ for the circuit of FIG. 1A,
`
`the total harmonic distortion measured for the voltage (V) in the simulated waveform is 26.9%,
`
`and 25.1% for the current (1). Utilizing a unity power factor with a reduced load of 100Q for the
`
`circuit of FIG. 1A, the total harmonic distortion measured for the voltage (V) is 2.79%, and
`
`3.41%for the current (I), with a total power of 585.6W as illustrated in the simulated waveform
`
`of FIG. 2D. In FIG. 2E, utilizing a unity power factor load of 28.2 at approximately 2kW,total
`
`harmonic distortion measured for the voltage (V) was 1.52%, and 1.71% for the current (1), with
`
`an efficiency of 98.2%.
`
`[0049]
`
`Buck converters, and particularly synchronous buck converters, may
`
`advantageously be configured for inverter applications to provide less noisy and moreefficient
`
`power output. The use of conventional buck converters for inverters is knownin the art, and
`
`examples of such applications may be found in U.S. Pat. No. 8,488,350 to Sigamani, titled “DC-
`
`12
`
`
`
`ATTY. DKT. 63219-821530 (JBL-0071-PV)
`
`AC Inverters’’, issued July 16, 2013, and U.S. Pat. No. 7,872,887 to Nishio etal., tithed “DC-AC
`
`Inverter Powering a Single Phase Commercial Power System’, issued Jan. 18, 2011, both of
`
`which are incorporated by reference in their entirety herein. While the aforementioned
`
`configurations provide some improvement over conventional inverter topologies, further
`
`improvements mayberealized utilizing configurations disclosed herein.
`
`[0050]
`
`Turning now to FIG. 3A, synchronous buck inverter topology 300 is disclosed in
`
`an exemplary embodiment. Inverter 300 comprises a DC source 301 and a house supply 302 for
`
`providing positive and negative voltages to high frequency switches A-B and low frequency
`
`switches C-D, as shown. In an embodiment, switches A-D are comprised of high frequency
`
`switches, such as field effect transistors (FETs). It should be understood by those skilled in the
`
`art that other switches or suitable switching mechanisms may be employed, depending on the
`
`specific application of the inverter. Inverter 300 may comprise a high frequency switching
`
`control (1) comprising controller 303 and sensing circuit 304.
`
`[0051]
`
`In an embodiment, controller may comprise a current-mode PWM controller (see
`
`FIG. 3C) and sensing circuit 304 comprises a peak current sense and an output voltage sense (see
`
`refs. 304A-B of FIG. 3C). Controller 303 may be operatively coupled to a gate of each of
`
`switches A-D, while sensing circuit 304 may be coupled to a load line as is shownillustratively
`
`in FIG. 3A. Alternatively, controller may be a microprocessor running firmware to control
`
`switches A-D.
`
`[0052]
`
`Controller 303 may be configured to provide a low frequency sine wave(or other
`
`suitable signal) to effect switching control on the synchronous-buckportion of inverter 300.
`
`Main switching may berealized using synchronous-buck switching portion (2), comprising
`
`13
`
`
`
`ATTY. DKT. 63219-821530 (JBL-0071-PV)
`
`switches A and B, to invert every half cycle of the frequencyof the signal provided by controller
`
`303. The inverting process thus creates a positive and negative transition of the sine wavesignal.
`
`Low frequency switching stage (3) comprises switches C and D and may be configured to
`
`operate as zero voltage switching (ZVS) and zero current switching (ZCS) drives
`
`[0053]
`
`Notably, using the configuration of FIG. 3A, the charge on output capacitor 305 is
`
`discharged to zero on every zero crossing of low frequency switching stage (3). Compared to a
`
`conventional synchronous buck, the configuration of FIG. 3A advantageously discharges energy
`
`every half cycle. During this discharge of energy, the zero crossing distortion in the low
`
`frequency sine waveis greatly reduced.
`
`[0054]
`
`‘Turning now to FIG. 3B, an exemplary switching scquencecis illustrated whercin
`
`switches A and B of the synchronous-buck switching portion (2) simultaneously andalternately
`
`provide high frequency PWM (x) and high frequency PWM complement (x’) for each positive
`
`half wave and negative half wave. Switches C and D for the low frequency switching stage (3)
`
`are configured such that switch C is Orrfor each positive half wave and ON for each negative
`
`half wave, while switch D is ON for each positive half wave and OFF for each negative half wave.
`
`[0055]
`
`FIG. 3C is another exemplary embodiment of a synchronous buck inverter,
`
`similar to inverter 300, wherein high voltage regulator house supply 302 receives inpul power
`
`(+HV, -HV) from a source (c.g., 301) and produccs output voltage +V for cach of the switch
`
`drives (A-D Drive) and voltage +VL for current-mode PWM controller 303, peak current sense
`
`304A and output voltage sense 304B. Controller 303 may provide low frequencysignals (e.g.,
`
`sine wave) via low frequency oscillator 310. Controller 303 as illustrated in the embodiment of
`
`FIG. 3C may comprise a high frequency (HF) switching portion and low frequency (LF)
`
`14
`
`
`
`ATTY. DKT. 63219-821530 (JBL-0071-PV)
`
`switching portion, wherein HF switching portion activates/deactivates switches associated with
`
`A DRIVE and B bRIVE of synchronous-buck/buck-synchronous stage 311 (see section (2) of FIG.
`
`3A). LF switching portion may activate/deactive switches associated with C DRIVE and D DRIVE
`
`of inverter stage 312 (see section (3) of FIG. 3A).
`
`[0056]
`
`Turning now to FIG. 4, an exemplary switch sequence diagram for the
`
`embodimentof FIG. 3A is provided for one cycle of controller output (Output) illustrated as a
`
`sine wave in the figure. As can be seen, high frequency outputs for switches A and B (Agate,
`
`Beate) are Shown together with low frequency outputs for switches C and D (Ceate, Deate), together
`
`with an inverted half-cycle voltage output (Ref). In the exemplary embodimentof FIG. 4, the
`
`cycle is separated into four sections (1-4) to better describe exemplary operation of the circuit,
`
`whichis provided below.
`
`[0057]
`
`FIGs. 4A-B are exemplary illustrations of a first section (Section 1) during a
`
`positive peak condition (Output) in the circuit, where it can be seen that Agae and Beate provide a
`
`high frequency PWM andhigh frequency PWM complementfor the positive peak. During
`
`switching time (a), output voltage is at a positive peak condition for the sine wave, where Agate
`
`drive is low, Beate drive is high, Ceate drive is low and Deate drive is high. As switches A and C
`
`are open, the inductor current conducts from the B switch to the D switch via inductor 306 and
`
`load 307 in synchronous current flow as shown in F'IG. 4C. During the (b) switching time, the
`
`outputis still at a positive peak condition and the Agate drive goes high, Beate goes low, Ceate drive
`
`is low and Deate drive is high. As switch A opens and switch B closes, inductor current conducts
`
`from the A switch to the D switch as buck current flow as shown in FIG. 4D.
`
`15
`
`
`
`ATTY. DKT. 63219-821530 (JBL-0071-PV)
`
`[0058]
`
`FIGs. 4E-F are exemplary illustrations of a second section (Section 2) during a
`
`first zero crossing (Output) positive to negative transition in the circuit. During switching time
`
`(a), output voltage is at a zero crossing condition (from positive peak to negative peak) for the
`
`sine wave, where Agate drive is high, Beate drive is low, Cate drive is low and Deate drive is high.
`
`As switches B and C are open, the inductor current instantaneously switches directions and
`
`conducts from the A switch to the D switch via inductor 306 and load 307 in buck/synchronous
`
`current flow as shown in FIG. 4G. During the (b) switching time, the output crosses from the
`
`positive peak to the negative peak of the sine wave, causing the Agate drive to go low, Beate to go
`
`high, Cate to go high and Deate gate to go low. As switches B and C open and switches A and D
`
`close, inductor current instantaneously switches directions and conducts from the B switch to the
`
`C switch as synchronous/buckcurrent flow as shownin FIG. 4H.
`
`[0059]
`
`FIGs. 4I-J are exemplary illustrations of a third section (Section 3) during a
`
`negative peak condition (Output) in the circuit, where it can be seen that Agate and Beate provide a
`
`high frequency PWM andhigh frequency PWM complement for the negative peak. During
`
`switching time (a), output voltage is at a negative peak condition for the sine wave, where Agate
`
`drive is high, Bgate drive is low, Cgate drive is high and Dgate drive is low. As switches B and D
`
`are open, the inductor current conducts from the C switch to the A switch in synchronouscurrent
`
`flow as shown in FIG. 4K. During the (b) switching time, the output moves away from the
`
`negative peak condition and the Agate drive goes low, Beate goes high, Cate drive is high and Deate
`
`drive is low. As switch A opens and switch B closes, inductor current conducts from the C
`
`switch to the B switch as buck current flow as shown in FIG. 41..
`
`16
`
`
`
`ATTY. DKT. 63219-821530 (JBL-0071-PV)
`
`[0060]
`
`FIGs. 4M-N are exemplary illustrations of a fourth section (Section 4) during a
`
`second zero crossing (Output) negative to positive transition in the circuit. During switching
`
`time (a), output voltage is approaching a zero crossing condition (from negative peak to positive
`
`peak) for the sine wave, where Agate drive is low, Beate drive is high, Cgate drive is high and Deate
`
`drive is low. As switches A andDare openat zero crossing, the inductor current instantaneously
`
`switches directions from the B switch to the D switch in synchronous/buck current flow as
`
`shown in FIG. 40. During the (b) switching time, the output crosses from the negative peak to
`
`the positive peak of the sine wave, causing the Agate drive to go high, Beate to go low, Ceate to go
`
`low and Deate gate to go high. As switches B and C open and switches A and D close, inductor
`
`current instantaneously switches directions from the A switch to the D switch in
`
`buck/synchronouscurrent flow as shownin FIG. 4P.
`
`[0061]
`
`Exemplary simulated gate drive waveforms and current waveforms for
`
`synchronous-buckcircuit portion (2) of inverter 300, comprising switches A and B, are
`
`illustrated in FIGs. 5A-7B. The exemplary simulated waveforms of FIGs. 5A and 5B illustrate
`
`switching gate drive waveforms and current waveforms during a positive peak condition,
`
`discussed above in connection with FIGs. 4A-D. As can be seen from the simulated current
`
`drive waveform of FIG. 5B, switch A, operating as a buck switch, goes low as switch B,
`
`operating as a synchronous switch, goes high during PWM switching. In the simulated current
`
`waveform of FIG. 5B, it can be seen that when switch A is open, current conducts from the B
`
`switch (to the D switch) as discussed above in connection with FIG. 4C. As switch A opens and
`
`switch B closes current conducts from the A switch (to the D switch) as discussed above in
`
`connection with FIGs. 4C-D.
`
`17
`
`
`
`ATTY. DKT. 63219-821530 (JBL-0071-PV)
`
`[0062]
`
`The exemplary simulated waveforms of FIGs. 6A and 6B illustrate switching gate
`
`drive waveforms and current waveforms duringa first zero crossing condition (i.e., from positive
`
`to negative peak), discussed above in connection with FIGs. 4E-H. As can be seen from the
`
`simulated current drive waveform of FIG. 6B, switch A operates as a buck switch before the zero
`
`crossing, and switch B operates as a buck switch after the zero crossing. As switch B opens,
`
`current instantaneously switches directions and conducts from the A switch (to the D switch).
`
`After the zero crossing (from the positive peak to the negative peak), switch B opens and switch
`
`A closes causing current to instantaneously switch directions and conducts from the B switch (to
`
`the C switch) as discussed above in connection with FIGs. G-H.
`
`[0063]
`
`The exemplary simulated waveforms of FIGs. 7A and 7B illustrate switching gate
`
`drive waveforms and current waveforms during a negative peak condition, discussed above in
`
`connection with FIGs. 4I-L. As can be seen from the simulated current drive waveform of FIG.
`
`7B, as switch B opens, and opcrating as a buck switch, current flows to the A switch (from the C
`
`switch) as a synchronous switch as discussed above in connection with FIG. 4K. As switch A
`
`opens and switch B closes, current conducts to the B switch (from the C switch) as buck current
`
`flow as discussed above in connection with FIG. 4L.
`
`[0064]
`
`The exemplary simulated waveforms of FIGs. 8A and 8Billustrate switching gate
`
`drive waveforms and current waveforms during a second zero crossing condition (1.e., from
`
`negative to positive peak), discussed above in connection with FIGs. 4M-P. As can be seen from
`
`the simulated current drive waveform of FIG. 8B, switch A operates as a synchronous switch
`
`with a large duty cycle, and switch B operates as a buck switch with a very small duty cycle
`
`before the zero crossing. After the zero crossing, A operates as a buck switch with a very small
`
`18
`
`
`
`ATTY. DKT. 63219-821530 (JBL-0071-PV)
`
`duty cycle and switch B operates as a synchronous switch with a large duty cycle. Thus, switch
`
`A opensat zero crossing, current instantaneously switches directions from the B switch (to the D
`
`switch) in synchronous/buck current flow as discussed above in connection with FIG. 40. As
`
`the output crosses from the negalive peak to the positive peak of the sine wave, switch B opens
`
`and switch A closes, causing current to instantaneously switch directions from the A switch (to
`
`the D switch) in buck/synchronouscurrent flow as discusse
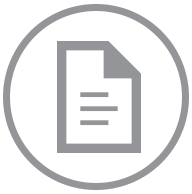
Accessing this document will incur an additional charge of $.
After purchase, you can access this document again without charge.
Accept $ ChargeStill Working On It
This document is taking longer than usual to download. This can happen if we need to contact the court directly to obtain the document and their servers are running slowly.
Give it another minute or two to complete, and then try the refresh button.
A few More Minutes ... Still Working
It can take up to 5 minutes for us to download a document if the court servers are running slowly.
Thank you for your continued patience.
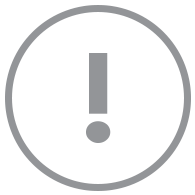
This document could not be displayed.
We could not find this document within its docket. Please go back to the docket page and check the link. If that does not work, go back to the docket and refresh it to pull the newest information.
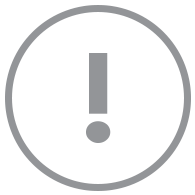
Your account does not support viewing this document.
You need a Paid Account to view this document. Click here to change your account type.
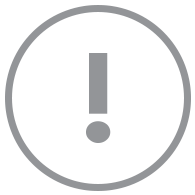
Your account does not support viewing this document.
Set your membership
status to view this document.
With a Docket Alarm membership, you'll
get a whole lot more, including:
- Up-to-date information for this case.
- Email alerts whenever there is an update.
- Full text search for other cases.
- Get email alerts whenever a new case matches your search.
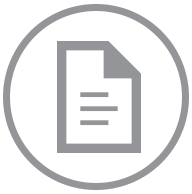
One Moment Please
The filing “” is large (MB) and is being downloaded.
Please refresh this page in a few minutes to see if the filing has been downloaded. The filing will also be emailed to you when the download completes.
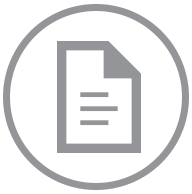
Your document is on its way!
If you do not receive the document in five minutes, contact support at support@docketalarm.com.
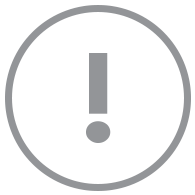
Sealed Document
We are unable to display this document, it may be under a court ordered seal.
If you have proper credentials to access the file, you may proceed directly to the court's system using your government issued username and password.
Access Government Site