`Our Ref: KK-205P
`
`VEHICLE WITH ELECTRIC TRANSAXLE
`
`Inventors: Yoshitaka KOCHIDOMARI & Takashi NISHIZAWA
`
`BACKGROUNDOF THE INVENTION
`
`Field of the Invention
`
`foeed]
`
`The present invention relates to a vehicle, such as a utility vehicle,
`
`equipped with an electric transaxle integrated with an axle and anelectric
`
`motor for driving the axle.
`
`BackgroundArt
`
`[0002]
`
`As disclosed by US 7,946,953 B and US 2010/0263958 A, a
`
`conventional engine utility vehicle is equipped with a mid-shipped engine, a
`
`rear transaxle casing supporting right and lefi rear wheels, a front transaxle
`
`casing supporting right and left
`
`front wheels, and a transmission for
`
`distributing power of the engine between the front and rear transaxle casings.
`
`Each of the front and rear transaxle casings incorporates a differential unit
`
`differentially connecting the right and left front or rear wheels to each other.
`
`The transmission is combination of a hydrostatic stepless transmission (HST)
`
`and a gear transmission, or combination of a belt transmission serving as a
`
`continuously variable transmission (CVT) and a gear transmission,
`
`for
`
`example.
`
`[0003]
`
`Sometypesofsports utility vehicle are mainly used for hunting purpose.
`Silence is a matter of great importance for hunting vehicles. Therefore, many
`utility vehicles used for hunting are electric vehicles equipped with electric
`
`motors. However, hunting vehicles are sometimes desired to have great power,
`such as engine power, for high-speed traveling on road, for high-torque
`traveling on rough fields or for other purposes. Further, recently, people
`dwelling in residential districts greatly demand utility vehicles because the
`
`utility vehicles are convenientfor variousdaily livings, e.g., for taking children
`
`to and from schoolor kindergarten bas stops. The residents search after silence,
`
`
`
`
`
`New U.S. Provisional Patent Application
`Our Ref: KK-205P
`
`compactness and economyofthe utility vehicles. An electric motor is an
`
`effective means for achieving the silence. However,
`
`the residents also
`
`sometimesdesire the utility vehicles to have great power, such as engine power,
`
`for high-speed traveling on road or other purposes.
`
`.
`
`(oaed]
`
`To satisfy the above-mentioned desires, a utility vehicle is expected to
`
`have an engine and anelectric motor and to be configured so that either/both
`
`electric power or/and engine power can be optionally selected as power for
`
`driving the utility vehicle, while ensuring compactness in structure and
`
`economy in structure and in power consumption.
`
`BRIEF SUMMARYOF THE INVENTION
`
`[0005]
`
`Anobject of the invention is to provide a vehicle that is adaptable as a
`
`compact and economyutility vehicle configured so that either electric power or
`
`engine powercan be optionally selected for driving the vehicle.
`
`[0006]
`
`To achieve the object, a vehicle according to the invention comprises
`
`right andleft electric transaxles, right andleft first drive wheels, an engine, right
`
`and left second drive wheels, a transmission for transmitting power from the
`
`engine to the right and left second drive wheels, a generator, a battery, and a
`
`modeselection means. Each of the right and left electric transaxles includes a
`
`casing incorporating a drive train and supporting an axle, and includes an
`
`electric motor mounted on the casing to drive the axle via the drive train. The
`
`right andleft first drive wheels are provided on the axles of the respective right
`
`and left electric transaxles. The generator generates electric power by driving
`
`the engine. The battery reserves the electric power generated by the generator
`
`so as to supply the electric power to the electric motors of the right and left
`
`electric transaxles. The mode selection meansis provided for selecting either a
`
`first drive mode where only the rightandleft first drive wheels are driven by the
`
`electric motors of the respective right and left electric transaxles or a second
`
`drive mode where only the right and left second drive wheels are driven by the
`
`engine via the transmission.
`
`[0007]
`
`Therefore, an operator who operates the vehicle can operate the mode
`
`selection meansso as to optionally select either the first drive mode for driving
`
`the vehicle by only electric power, thereby obtaining silence, or the second
`
`
`
`New U.S. Provisional Patent Application
`Our Ref: KK-205P
`
`drive modefordriving the vehicle by only engine power, thereby obtaining high
`torque for efficient traveling of the vehicle. Such an optional selection of drive
`modeis advantageousin achieving an operator’s desired traveling performance
`
`of the vehicle as well as or rather than economizing power consumptionofthe
`
`vehicle. Further, the vehicle has neither means for transmitting power of the
`
`engineto the first drive wheels nor meansfor transmitting powerofthe electric
`
`motors to the second drive wheels, thereby being simplified and economized in
`
`structure.
`
`[0008]
`
`These,
`
`further and other objects,
`
`features and advantages of the
`
`invention will appear more fully from the following detailed description with
`
`reference to the accompanying drawings.
`
`BRIEF DESCRIPTION OF THE DRAWINGS
`
`[0009]
`
`Fig. 1 is a skeleton diagram of a hybrid vehicle V1 equipped with a pair
`
`of electric transaxles ET1 for driving front wheels 14 and with an engine and
`
`transmission system 20 for driving rear wheels 24.
`
`{0010}
`
`Fig. 2 is a plan view partly in section of electric transaxle ET1 used for
`
`vehicle V1.
`
`[0011]
`
`Fig. 3 is a sectional plan view of engine and transmission system 20
`
`used for vehicle V1.
`
`[0012]
`
`[0013]
`
`Fig. 4 is a side view partly in section of an electric transaxle ET2.
`
`Fig. 5 is a schematic side view ofan electric utility vehicle V2 equipped
`
`with electric transaxle ET2 serving as a rear transaxle from which poweris
`
`taken off and is transmitted into a front transaxle casing via a propeller shaft.
`
`[O014]
`
`Fig. 6 is a schematic side view pf a hybrid utility vehicle V3 equipped
`
`with electric transaxle ET2 serving as a rear transaxle, and equipped with an
`
`engine 80 whose power can be transmitted to the front transaxle casing or/and
`
`electric transaxle ET2 serving as the rear transaxle.
`
`[0015]
`
`Fig. 7 is a fragmentary schematic side view of vehicle V3 equipped with
`
`an electric transaxle ET2a serving as a modification ofelectric transaxle ET2.
`
`[0016]
`
`Fig. 8 is a side view partly in section of an electric transaxle ET2b
`
`serving as another modification of electric transaxle ET2.
`
`
`
`New U.S. Provisional Patent Application
`Our Ref: KK-205P
`
`[0017]
`
`Fig. 9 is a schematic side view pfanelectric utility vehicle V4 equipped
`with electric transaxles ET2b serving as front and rear transaxles.
`
`[00138]
`
`Fig. 10 is a side view partly in section of an electric transaxle ET2c
`
`serving as a modification ofelectric transaxle ET2b.
`
`DETAILED DESCRIPTION OF THE INVENTION
`
`[0019]
`
`Referring to Figs. 1, 2 and 3, a hybrid vehicle (hereinafter, simply
`
`referred to as “vehicle”) V1 will be described. Vehicle V1 is a utility vehicle,
`
`for example. Vehicle V1 is equipped with a pair of electric transaxles ET]
`
`serving as right and left front transaxles for driving respective right and left
`
`front wheels 14, and is equipped with an engine and transmission system 20 for
`
`driving right and left rear wheels 24. Engine and transmission system 20
`
`includes an engine 21, a transaxle casing 22, and a belt transmission BT1 for
`
`transmitting power from engine 21 into transaxle casing 22. Right andleft rear
`
`wheels 24 are provided on distal ends of respective right and left rear axles 23
`
`supported by transaxle casing 22. Transaxle casing 22 incorporates a forward
`
`traveling gear train FG, a backward traveling gear train RG, and a differential
`
`gear unit D differentially connecting proximal ends ofright and left rear axles
`
`23 to each other. Either forward traveling gear train FG or backward traveling
`
`gear train RG is selected to transmit power from belt transmission BT1 to
`
`differential gear unit D.
`
`[0020]
`
`Further, vehicle V1 is equipped with a generator 19 that is driven by
`
`driving engine 21 so as to generate electric power, and is equipped with a
`
`battery 18 for reserving the electric power generated by generator 19 and for
`
`supplying the electric power to electric motors 2 of respective electric
`
`transaxles ET1.
`
`[0021]
`
`Referring to Figs. 1 and 2, each of right and left electric transaxles ET1
`
`will be described. Electric transaxle ET1 includes a reduction gear casing 1, an
`
`axle 12, an electric motor 2, and a reduction gear train RG1 disposed in
`
`reduction gear casing | so as to transmit powerfromelectric motor 2 to axle 12.
`
`fGG22)
`
`Axle 12 is journalled by reduction gear casing 1 via a bearing 16, and is
`
`extended outward from reduction gear casing 1 through an opening of reduction
`
`gear casing 1 so as to be fixedly provided on a distal end portion thereof with a
`
`
`
`New U.S. Provisional Patent Application
`Our Ref: KK-205P
`
`hub 13 that is fixed to a rim 14a of front wheel 14. The opening of reduction
`
`gear casing 1 passing axle 12 therethrough is covered with a cover la. Axle 12
`
`is formed with a flange 12a on a proximal end portion thereof disposed in
`
`reduction gear casing 1, and flange 12ais journalled by reduction gear casing 1
`
`via a bearing 15.
`
`[0023}
`
`Electric motor 2 is fastened to reduction gear casing 1 via a bolt 17 and
`
`so on. A motor output shaft 3 of electric motor2 is inserted at a tip thereof into
`
`reduction gear casing 1 and is extended coaxially to axle 12. Reduction gear
`
`train RG1 interposed between motor output shaft 3 and axle 12 will be detailed.
`
`A motoroutput gear 4 is fixed on thetip of motor output shaft 3. A sun gear8 is
`
`disposed between the tip of motor output shaft 3 and flange 12a of axle 12
`
`coaxially to motor output shaft 3 and axle 12. Sun gear8 is fixedly fitted into a
`
`carrier 7 that is disposed betweenthe tip of motor output shaft 3 and flange 12a
`
`of axle 12, so that sun gear 8 is rotatably integral with carrier 7. Carrier 7 is
`
`extended from sun gear 8 in a radial direction of motor output shaft 3 and axle
`
`12, and pivotally supports a planetary gear 5 via a pivot shaft 6 extended parallel
`
`to motor output shaft 3 and axle 12. Planetary gear 5 meshes with motor output
`
`gear4.
`
`[0024]
`
`Further, an internal gear 10 is fixed on an inner peripheral surface of
`
`reduction gear casing 1, and planetary gear 5 meshes with internal gear 10. On
`
`the other hand, flange 12a of axle 12 pivotally supports a planetary gear 9 via a
`
`pivot shaft 11 extended parallel to motor output shaft 3 and axle 12. Planetary
`
`gear 9 meshes with sun gear 8, and meshes with internal gear 10.
`
`In this way,
`
`motor output gear 4, planetary gear 5, sun gear 8, planetary gear 9 and internal
`
`gear 10 constitute reduction gear train RG1.
`
`[0025]
`
`Powerof electric motor 2 is transmitted to axle 12 via reduction gear
`
`train RG1 in the following way. When motoroutput gear 4 rotates together with
`
`motor output shaft 3, planetary gear 5 is rotated by the rotation of motor output
`
`gear 4 so as to revolve along internal gear 10 around an axis of motor output
`
`shaft 3. The revolution of planetary gear 5 causes rotation of carrier 7 centered
`
`on an axis of sun gear 8, thereby causing rotation of sun gear 8 centered onits
`
`own axis. Planetary gear 9 is rotated by the rotation of sun gear 8 so as to
`
`revolve along internal gear 10 around an axis of axle 12. The revolution of
`
`planetary gear 9 causesrotation of flange 12a centered on the axis of axle 12,
`
`
`
`NewU.S. Provisional Patent Application
`Our Ref: KK-205P
`
`thereby causingrotation of axle 12 centered on its own axis. In this way, due to
`internal gear 10, the rotation of planetary gear 5 followingthe rotation of motor
`output gear 4 is converted into the revolution of planetary gear 5 such as to
`reduce the rotary speed of sun gear 8, andthen,the rotation of planetary gear 9
`following the speed-reduced rotation of sun gear 8 is converted into the
`revolution of planetary gear 9 suchasto further reduce the rotary speed of axle
`12. Therefore, reduction gear train RG1 has a great reduction gearratio while
`
`[0026]
`
`ensuring its compactness.
`Electric motors 2 of respective right and left electric transaxles ET1 are
`supplied with electric power from battery 18, and their turning on and off and
`their output rotary speedsare controlled by a controller (not shown) provided in
`
`vehicle V1. Especially, to turn vehicle V1, the output rotary speedsof electric
`
`motors 2 of right and left electric transaxles ET1 are differentially controlled so
`
`as to differentially rotate right and left front wheels 14.
`
`[0027}
`
`Engine and transmission system 20 will be detailed with reference to
`
`Figs.
`
`1 and 3. Belt transmission BT1 includes a belt transmission cover 25,
`
`pulleys 27 and 29 and a belt 28. An engine output shaft 26 of engine 21 is
`
`extended into belt transmission cover 25 so as to serve as an input shaft of belt
`
`transmission BT1, a transmission input shaft 30 of the gear transmission in
`
`transaxle casing 22 is extended outward from transaxle casing 22 in parallel to
`
`engine output shaft 26 and into belt transmission cover 25 so as to serve as an
`
`output shaft of belt transmission BT1. In belt transmission cover 25, pulley 27
`
`is provided on engine output shaft 26, pulley 29 is provided on transmission
`
`input shaft 30, and belt 28 is interposed between pulleys 27 and 29. Belt
`
`transmission BT1 is a continuously variable transmission (CVT),
`
`in which
`
`pulleys 27 and 29 are split pulleys, configured so that a ratio of a radius of a
`
`looping portion of belt 28 in pulley 27 round engine output shaft 26 to a radius
`
`of a looping portion of belt 28 in pulley 29 round transmission input shaft 30 is
`
`variable.
`
`[0028]
`
`Generator 19 is disposed around engine output shaft 26 in belt
`
`transmission cover 25. Generator 19 includes a stator 21a fixed to engine 21,
`
`and includesa rotor 27afixed to pulley 27. Stator 21a is provided with armature
`
`windings 21b, and rotor 27a is provided with magnets 27b. Stator 21a and rotor
`
`27a are disposed so that magnets 27b face armature windings 21b. Therefore,
`
`
`
`New U.S. Provisional Patent Application
`Our Ref: KK-205P
`
`whenstator 27a rotates together with engine output shaft 26, armature windings
`27a are excited by rotating magnets 27b so as to generate electric power to be
`
`[0029]
`
`reserved in battery 18.
`In transaxle casing 22, transmission input shaft 30, a counter shaft 31,
`andright and let coaxial axles 23 are extendedin parallel and are journalled by
`
`transaxle casing 22 via bearings.
`
`In detail, transaxle casing 22 includes right
`
`and left gear housings 22a and 22b andright and left brake housings 22c¢ and
`
`22d. Right and left gear housings 22a and 22b are joined to each other at a
`
`vertical joint plane so as to define a gear chamber of transaxle casing 22
`
`incorporating forward traveling gear train FG, backwardtraveling gear train RG
`
`and differential gear unit D. Right brake housing 22c is joined to right gear
`
`housing 22a so as to extend rightward from right gear housing 22a, thereby
`
`journaling right axle 23 via bearings, and thereby defining a right brake
`
`chamberoftransaxle casing 22 incorporating a right brake 44 for braking right
`
`axle 23. Left brake housing 22d is joined to left gear housing 22b so as to
`
`extend leftward from left gear housing 22b, thereby journaling left axle 23 via
`
`bearings, and thereby defining a left brake chamber of transaxle casing 22
`
`incorporating a left brake 44 for braking left axle 23. Right and left axles 23
`
`project rightwardly and leftwardly outward from right and left brake housings
`
`22c and 22d, respectively, so as to be provided on respective distal ends thereof
`
`with respective right and left rear wheels 24.
`
`[0030]
`
`In each of the right and left brake chambers of transaxle casing 22,
`
`friction discs that are unrotatable relative to corresponding axle 23 and friction
`
`discs that are unrotatable relative to transaxle casing 22 are alternately aligned
`
`so as to constitute each of right and left brakes 44. A brake shoe 45 is disposed
`
`in each ofthe right and left brake chambers between each brake 44 and each of
`
`right and left gear housings 22a and 22b. Right and left brake arms 46 are
`
`pivoted on outer portions of respective right and left brake housings 22c and
`
`22d, and are operatively connected to respective brake shoes 45 and to a brake
`
`manipulator (not shown) of vehicle V1. When the brake manipulator is
`
`operated for braking, brake arms 46 are rotated to move respective brake shoes
`
`45 toward respective brakes 44 so as to press the friction discs of respective
`
`brakes 44 against one another, thereby applying brakes 44 to stop right andleft
`
`axles 23. When the brake manipulator is operated for unbraking, brake arms 46
`
`
`
`New USS. Provisional Patent Application
`Our Ref: KK-205P
`
`are rotated to move respective brake shoes 45 away from respective brakes 44
`
`so as to separate the friction discs of respective brakes 44 from one another,
`
`thereby allowingrotation of right and left axles 23 freely from respective brakes
`
`44.
`
`[0031]
`
`In the gear chamberof transaxle casing 22, a centrifugal governor 47 is
`
`provided on transmission input shaft 30. Centrifugal governor 47 detects the
`
`rotary speed of transmission input shaft 30 (serving as the output shaft of belt
`
`transmission BT1) and controls engine 21 to change the rotary speed of engine
`
`output shaft 26 (serving as the input shaft of belt transmission BT1) in
`
`correspondenceto the detected rotary speed of transmission input shaft 30.
`
`[0032]
`
`In the gear chamber of transaxle casing 22, a forward traveling drive
`
`gear 32 and a backwardtraveling drive gear 33 are formed (or fixed) on
`
`transmission input shaft 30.
`
`In the gear chamber of transaxle casing 22, a
`
`forward traveling driven gear 34 and a backward traveling driven gear 35 are
`
`fitted on counter shaft 31 so as to be rotatable relative to counter shaft 31.
`
`Forwardtraveling drive gear 32 and forward traveling driven gear 34 mesh with
`
`each other so as to constitute forward traveling gear train FG. Backward
`
`traveling drive gear 33 and backward traveling driven gear 35 mesh with an idle
`
`gear (not shown) so that backward traveling drive gear 33, the idle gear and
`
`backward traveling driven gear 35 constitute backward traveling gear train RG.
`
`Further, a pinion 37 is formed(or fixed) on counter shaft 31 so as to transmit the
`
`rotary force of counter shaft 31 to later-discussed differential gear unit D.
`
`[0033]
`
`Counter shaft 31 is formed with a spline portion between gears 34 and
`
`35, and a reverser shifter 36 is spline-fitted on the spline portion of countershaft
`
`31 so that reverser shifter 36 is unrotatable relative to counter shaft 31 and is
`
`axially slidable on counter shaft 31. Gears 34 and 35 are formed with notches in
`
`respective portions thereof facing reverser shifter 36. Reverser shifter 36 is
`
`formed on axial opposite ends thereof with teeth to befitted into the notches of
`
`respective gears 34 and 35. The notches of forward traveling driven gear 34 and
`
`the teeth on one end ofreverser shifter 36 facing forward traveling driven gear
`
`34 constitute a dog clutch for forward traveling rotation of axles 23. The
`
`notches of backward traveling driven gear 35 and the teeth on the other end of
`
`reverser shifter 36 facing backward traveling driven gear 35 constitute a dog
`
`clutch for backwardtraveling rotation of axles 23.
`
`
`
`New U.S. Provisional Patent Application
`Our Ref: KK-205P
`
`[0034]
`
`Reverser shifter 36 can be shifted among a forward traveling position, a
`
`neutral position and a backward traveling position. When reversershifter 36 is
`
`disposed at the forward traveling position, the teeth on one end of reverser
`
`shifter 36 are fitted into the notches of forward traveling driven gear 34 so as to
`
`rotatably integrate forward traveling driven gear 34 with counter shaft 31 via
`
`reverser shifter 36, so that the rotary force of transmission input shaft 30 driven
`
`by engine 21 via belt transmission BT1 is transmitted to counter shaft 31 via
`
`forward traveling gear train FG, thereby rotating axles 23 in the forward
`
`traveling rotation direction of rear wheels 24.
`
`hen reverser shifter 36 is
`
`
`disposed at the backward traveling position (as shown in Fig. 3), the teeth on the
`
`other end of reverser shifter 36 are fitted into the notches of backward traveling
`
`driven gear 35 so as to rotatably integrate backward traveling driven gear 35
`
`with counter shaft 31 via reverser shifter 36, so that the rotary force of
`
`transmission input shaft 30 is transmitted to counter shaft 31 via backward
`
`traveling gear train RG, thereby rotating axles 23 in the backward traveling
`
`rotation direction of rear wheels 24. Whenreverser shifter 36 is disposed at the
`
`neutral position (as shownin Fig. 1), neither forward traveling driven gear 34
`
`nor backward traveling driven gear 35 hasthe teeth of reverser shifter 36 in the
`
`notches thereof, so that gears 34 and 35 are allowed torotate relative to counter
`
`shaft 31, thereby preventing the rotary force oftransmission input shaft 30 from
`
`being transmitted to counter shaft 31, and thereby making axles 23 free from the
`
`powerof engine 21.
`
`[0035]
`
`In the gear chamber of transaxle casing 22, differential gear unit D
`
`differentially connects proximal end portions of right and left axles 23 to each
`
`other. Differential gear unit D includes a differential input gear (bull gear) 38, a
`
`differential casing 39, a pivot shaft 40, bevel differential pinions 41 and right
`
`and left bevel differential side gears 42. Right and left axles 23 are journalled
`
`by respective right and left gear housings 22a and 22b via respective bearings
`
`and are extended at the respective proximal ends thereof into the gear chamber
`
`of transaxle casing 22 so as to be inserted into differential casing 39, so that
`
`axles 23 are rotatable relative to differential casing 39. In differential casing 39,
`
`right and left bevel differential side gears 42 are fixed on the proximal ends of
`
`respective right andleft axles 23.
`
`
`
`New U.S. Provisional Patent Application
`Our Ref: KK-205P
`
`[0036]
`
`Differential input gear 38 is fixed on differential casing 39 and meshes
`with pinion 37 on counter shaft 31. Pivot shaft 40 is extended in a radial
`
`direction of axles 23, andis fixed to differential casing 39 so as to be rotatably
`
`integral with differential casing 39 and differential input gear 38..Bevel
`
`differential pinions 41 are pivoted on pivot shaft 40. Each of bevel differential
`
`pinions 41 meshes with both right andleft differential side gears 42.
`
`[0037]
`
`Due to the above-mentioned structure, transmission input shaft 30
`
`receives the power of engine 21 via belt transmission BT1, and in transaxle
`
`casing 22, either forward traveling gear train FG or backward traveling gear
`
`train RG is selected by reverser shifter 36 so as to transmit the power of engine
`
`21 from transmission input shaft 30 to counter shaft 31, thereby transmitting
`
`the powerof engine 21 from counter shaft 31 to right and left rear wheels 24 via
`
`pinion 37, differential gear unit D and right andleft axles 23.
`
`[0038]
`
`As understood from the above-mentioned structure and Fig. 1, vehicle
`
`V1 is provided with neither means for distributing the power of engine 21 to
`
`front wheels 14 nor meansfor distributing the powerof electric motors 2 to rear
`
`wheels 24. This is because vehicle V1 rather sets importance on the advantages
`
`in structural simplicity and reduction of components and costs. Assumptive
`
`driving modesof vehicle V1 are two types of 2WD (two wheel drive) mode: a
`
`first 2WD modeto drive vehicle V1 by driving only rear wheels 24 by powerof
`
`engine 21; and a second 2WD modeto drive vehicle V1 by driving only front
`
`wheels 14 by powerofelectric motors 2.
`
`[0039]
`
`In this regard, vehicle V1 is provided with a mode selection means,e.g.,
`
`a switch, a button,a dial, a lever or a pedal, whichis operatedto select either the
`
`first 2WD mode where only rear wheels 24 are driven by engine 21 or the
`
`second 2WD mode whereonly front wheels 14 are driven by electric motors2.
`
`Therefore, an operator who drives vehicle V1 can optionally select either the
`
`first 2WDfor obtaining silence or the second 2WDfor obtaining high power.
`
`[0040]
`
`Various changes and modifications may be made in vehicle V1. For
`
`example, vehicle V1! may be alternatively provided with engine and
`
`transmission system 20 for driving right and left front wheels 14 and with the
`
`pair of electric transaxles ET1 for driving right and left rear wheels 24. Further,
`
`it is possible that vehicle V1 can travel in 4WD (for wheel drive) mode, where
`
`front wheels 14 are driven by electric motors 2 of electric transaxles ET1 and
`
`10
`
`
`
`New U.S. Frovisional Patent Application
`Our Ref: KK-205P
`
`simultaneously rear wheels 24 are driven by engine 21 of engine and
`
`transmission system 20, if rotary speeds of front wheels 14 and rear wheels 24
`
`can be equalized well. Incidentally, if vehicle V1 is provided with means,e.g.,
`a propeller shaft and universal joints, for transmitting power from electric
`
`motors 2 to rear wheels 24 and/orfor transmitting power from engine 21 to front
`
`wheels 14, front wheels 14 can be driven by combined powers of electric
`
`motors 2 and engine 21 and/or rear wheels 24 can be driven by combined
`
`powers of engine 21 and electric motors 2.
`
`[0041]
`
`Referring to Fig.4, an electric transaxle ET2 will be described. Electric
`
`transaxle ET2 is defined as a transaxle integrated with an electric motor 51.
`
`Electric transaxle ET1 includes a reduction gear casing 52, a differential gear
`
`casing 53, and a powertaking-off (PTO) casing 54. Reduction gear casing 52
`
`includes a main housing 52a and a cover 52b joined to each other. Electric
`
`motor 51 and differential gear casing 53 are fixed to main housing 52a of
`
`reduction gear casing 52 so as to be cantilevered from reduction gear casing 52
`
`in the same direction. PTO casing 54 is fixed to cover 52b of reduction gear
`
`casing 52 so as to extend from reduction gear casing 52 opposite to electric
`
`motor 51 and differential gear casing 53. Hereinafter, it is assumedthat electric
`
`motor 51 and differential gear casing 53 are extended rearward from reduction
`
`gear casing 52, and PTO casing 54 is extended forward from reduction gear
`
`casing 52.
`
`[0042]
`
`Electric motor 51 has a motor output shaft 51a that is extended into
`
`reduction gear casing 52. A motor output pinion 51b is fixed on motor output
`
`shaft 51a in reduction gear casing 52. A gear member 55 is formed with a
`
`cup-shaped portion and with an axial shaft 55a extended from the cup-shaped
`
`portion thereof. Gear member55 is disposed in reduction gear casing 52 so as
`
`to have axial shaft 55a journalled by cover 52a via bearings 66. Axial shaft 55a
`
`of gear member55 is extended in the axial direction of motor output shaft 51a,
`
`however, is axially offset from motor output shaft 51a in the radial direction of
`
`motor output shaft 51a, i.e., is not coaxial to motor output shaft 51a.
`
`[9043]
`
`An inner peripheral surface of the cup-shaped portion of gear member
`
`55 is toothed to form an inner peripheral gear 55b, and an outer peripheral
`
`surface of the cup-shaped portion of gear member 55 is toothed to form an outer
`
`peripheral gear 55c. Motor output shaft 51a is inserted into the cup-shaped
`
`li
`
`
`
`New U.S. Provisional Patent Application
`OurRef: KK-205P
`
`[0044]
`
`portion of gear member55 so that motor output pinion 51b meshes with inner
`peripheral gear 55b of gear member55.
`Motor output pinion 51b and inner peripheral gear 55b constitute a
`reduction gear train that is advantageous in its compactness and its large
`reduction gear ratio. More specifically, when viewed in the axial direction of
`motor output shaft 51a and axial shaft 55a, motor output pinion 51b is disposed
`within a circle defined by inner peripheral gear 55b, thereby achieving the
`compactness, especially, minimizing the gear arrangement in radial directions
`of axial shaft 55a. Further, even in the case that the diametrical size of gear
`
`member 55 (i.e., the diameter of inner peripheral gear 55b) is limited, the
`
`diametrical difference between motor output pinion 51b and inner peripheral
`
`gear 55b can be increased by reducing the diametrical size of motor output
`
`pinion 51b,
`
`thereby ensuring a large reduction gear ratio as well as the
`
`compactness.
`
`[0045]
`
`However, it should be considered that as the diametrical size of motor
`
`output pinion 51b is reduced, the axial offset degree of electric motor 51 from
`
`gear member55 (i.e., the deviation of motor output shaft 51a from axial shaft
`
`55a in the radial direction of gear member55)is increased. Therefore, to allow
`
`the diametrical size reduction of motor output pinion 51b relative to inner
`
`peripheral gear 55b for ensuring the large reduction gearratio, electric transaxle
`
`ET2 is configured so that electric motor 51 can be mounted on a portion of
`
`reduction gear casing 52 such as to ensure the required axial offset degree of
`
`electric motor 51 from gear member55 in reduction gear casing 52.
`
`[0046]
`
`A final reduction gear 56 is disposed in reduction gear casing 52 and
`
`mesheswith outer peripheral gear 55c of gear member 55. As a result, motor
`
`output pinion 51b, inner peripheral gear 55b, outer peripheral gear 55c andfinal
`
`reduction gear 56 constitute an entire reduction gear train RG2 in reduction gear
`
`casing 52. Final reduction gear 56 is fixed on a reduction output shaft 57.
`
`Reduction output shaft 57 is journalled by main housing 52a of reduction gear
`
`casing 52 via a bearing 67, and is journalled by cover 52b of reduction gear
`
`casing 52 via a bearing 68 so as to extendin the axial direction of motor output
`
`shaft 51a. A rear end portion of reduction output shaft 57 is inserted into
`
`differential gear casing 53 via main housing 52a of reduction gear casing 52. A
`
`12
`
`
`
`New U.S. Provisional Patent Application
`Our Ref: KK-205F
`
`bevel pinion 37ais formed on the rear end portion of reduction output shaft 37
`
`in differential gear casing 53.
`
`(0047)
`
`A differential gear unit 58 is disposed in differential gear casing 53 so as
`
`to differentially connect proximal ends of right and left axies 59 to each other.
`
`Differential gear unit 58 has a bevel input gear 58a that meshes with bevel
`
`pinion 57a, Right and left axles S9 are journalled by differential gear casing 53
`
`and are extended rightwardly and leftwardly (perpendicular to the axial
`
`direction of motor output shaft 51a) outward from differential gear casing 53.
`
`[0048]
`
`PTOcasing 54 is formed in a rear portion thereof with a clutch chamber
`
`54a, and is formedin a front portion thereof with a PTO shaft chamber 54b that
`
`is opened forwardly outward. A PTOshaft 61 is journalled via a bearing 69 by a
`
`partitioning wall of PTO casing 54 formed between chambers 54a and 54b. A
`
`rear end portion 6fb of PTO shaft 61 is splined on an outer peripheral surface
`
`thereef, and is formed therein with a rearwardly opened recess 6la. Rear end
`
`portion 61b of PTO shaft 61 is disposed in clutch chamber 54a. A front end
`
`portion 6lc of PPO shaft 61 is splined on an outer peripheral surface thereof,
`
`and is disposed in PTO chamber 546. A front portion 37b of reduction output
`
`shaft 57 is splined on an outer peripheral surface thereof, and is disposed in
`
`cluich chamber 54a. A front end projection 57c that is diametrically smaller
`
`than splined front portion 57b of reduction output shaft 57 projects forward
`
`from splined front portion 57b, andis inserted into recess 61a of PTO shaft 61 in
`
`clutch chamber 54a, so that reduction output shaft 57 is rotatable relative to
`
`PTOshaft 61.
`
`[0049]
`
`A clutch 60 is interposed between reduction output shaft 57 and PTO
`
`shaft 61 in clutch chamber 54a. Clutch 60 includes a clutch slider 62, a spline
`
`hub 63, a detent assembly 64 and a spacer 65. Spline hub 63is fixed on splined
`
`front portion 57b of reduction output shaft 57, and spacer 65 is fixed on
`
`reduction output shaft 57 between spline hub 63 and cover 52b ofreduction gear
`
`casing 52. Clutch slider 62 is fitted on the splined outer peripheral surface of
`
`rear end portion 61b of PTO shaft 61 so asto be axially slidable on PTO shaft 61
`
`and so as to be unrotatable relative to PTO shaft 61. Detent assembly 64
`
`includes a pair of balls and a compressed spring sandwiched betweenthe balls,
`
`andis fitted in a diametric through hole of PTO shaft 61, so that the balls are
`
`pressed against clutch slider 62 by the spring.
`
`13
`
`
`
`New U.S. Provisional Patent Application
`Our Ref: KK-205P
`
`[0050]
`
`Clutch slider 62 can be shifted between a clutch-on position and a
`
`clutch-off position, and can be held at either the cl
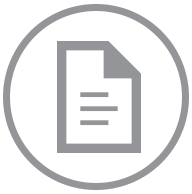
Accessing this document will incur an additional charge of $.
After purchase, you can access this document again without charge.
Accept $ ChargeStill Working On It
This document is taking longer than usual to download. This can happen if we need to contact the court directly to obtain the document and their servers are running slowly.
Give it another minute or two to complete, and then try the refresh button.
A few More Minutes ... Still Working
It can take up to 5 minutes for us to download a document if the court servers are running slowly.
Thank you for your continued patience.
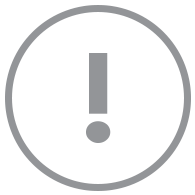
This document could not be displayed.
We could not find this document within its docket. Please go back to the docket page and check the link. If that does not work, go back to the docket and refresh it to pull the newest information.
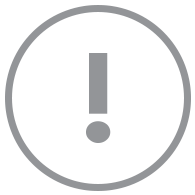
Your account does not support viewing this document.
You need a Paid Account to view this document. Click here to change your account type.
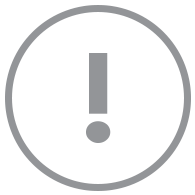
Your account does not support viewing this document.
Set your membership
status to view this document.
With a Docket Alarm membership, you'll
get a whole lot more, including:
- Up-to-date information for this case.
- Email alerts whenever there is an update.
- Full text search for other cases.
- Get email alerts whenever a new case matches your search.
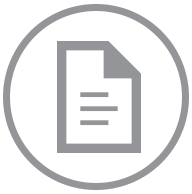
One Moment Please
The filing “” is large (MB) and is being downloaded.
Please refresh this page in a few minutes to see if the filing has been downloaded. The filing will also be emailed to you when the download completes.
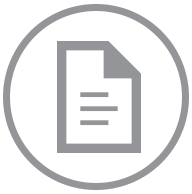
Your document is on its way!
If you do not receive the document in five minutes, contact support at support@docketalarm.com.
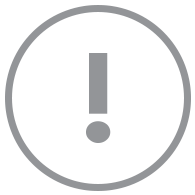
Sealed Document
We are unable to display this document, it may be under a court ordered seal.
If you have proper credentials to access the file, you may proceed directly to the court's system using your government issued username and password.
Access Government Site