`
`PCT/EP2021/077390
`
`MEASUREMENT SYSTEM AND METHOD OF USE
`
`CROSS-REFERENCE TO RELATED APPLICATIONS
`
`[0001]
`
`This application claims priority of EP application 20207351.6 which was filed on
`
`November 13, 2020 and which is incorporated herein in its entirety by reference.
`
`FIELD
`
`[0002]
`
`The present
`
`invention relates to a measurement system and method of use. More
`
`particularly, the method may be for determining optical aberrations for a projection system or measuring
`
`10
`
`alignment.
`
`BACKGROUND
`
`[0003]
`
`A lithographic apparatus is a machine constructed to apply a desired pattern onto a
`
`substrate. A lithographic apparatus can be used, for example, in the manufacture of integrated circuits
`
`15
`
`(ICs). A lithographic apparatus may, for example, project a pattern (also often referred to as “design
`
`layout” or “design’’) of a patterning device (e.g., a mask) onto a layer of radiation-sensitive material
`
`(resist) provided on a substrate (e.g., a wafer).
`
`[0004]
`
`As semiconductor manufacturing processes continue to advance, the dimensionsofcircuit
`
`elements have continually been reduced while the amount of functional elements, such as transistors,
`
`per device has been steadily increasing over decades, following a trend commonly referred to as
`
`‘Moore’s law’. To keep up with Moore’s law the semiconductor industry is chasing technologies that
`
`enable to create increasingly smaller features. To project a pattern on a substrate a lithographic
`
`apparatus may use electromagnetic radiation. The wavelength ofthis radiation determines the minimum
`
`size of features which are patterned on the substrate. Typical wavelengths currently in use are 365 nm
`
`(i-line), 248 nm, 193 nm and 13.5 nm. A lithographic apparatus, which uses extreme ultraviolet (EUV)
`
`radiation, having a wavelength within a range of 4 nm to 20 nm, for example 6.7 nm or 13.5 nm, may
`
`be used to form smaller features on a substrate than a lithographic apparatus which uses, for example,
`
`radiation with a wavelength of 193 nm.
`
`[0005]
`
`Radiation that has been patterned by the patterning device is focussed onto the substrate
`
`using a projection system. The projection system may introduce optical aberrations, which cause the
`
`image formed on the substrate to deviate from a desired image (for example a diffraction limited image
`
`of the patterning device). Alignment in a lithographic apparatus is also an important aspect, e.g. to
`
`make sure the desired imageis positioned in the correct position.
`
`[0006]
`
`It may be desirable to provide methods and apparatus for accurately determining such
`
`aberrations caused by a projection system such that
`
`these aberrations can be better controlled.
`
`Furthermore,
`
`it may be desirable to provide methods and apparatus for accurately determining
`
`alignmentin a lithographic apparatus.
`
`25
`
`30
`
`35
`
`
`
`WO 2022/100930
`
`PCT/EP2021/077390
`
`SUMMARY
`
`[0007]
`
`According to a first aspect of the invention, there is provided a measurement system, the
`
`measurement system comprising: a sensor apparatus; an illumination system arranged to illuminate the
`
`sensor apparatus with radiation, the sensor apparatus comprising a patterned region arranged to receive
`
`a radiation beam and to form a plurality of diffraction beams, the diffraction beams being separated in
`
`a shearing direction; the sensor apparatus comprising a radiation detector; wherein the patterned region
`
`is arranged such that at least someof the diffraction beams form interference patterns on the radiation
`
`detector; wherein the sensor apparatus comprises a plurality of patterned regions, and wherein pitches
`
`of the patterned regions are different in adjacent patterned regions.
`
`[0008]
`
`This has an advantage of increasing the amountof data collected in a single measurement.
`
`Advantagcously, signals corresponding to the adjacent patterned regions can be distinguished without
`
`requiring a particular spatial separation between the adjacent patterned regions.
`
`[0009]
`
`The measurement system may be arranged suchthat the interference patterns from adjacent
`
`patterned regionsat least partially overlap at the radiation detector.
`
`[00010]
`
`Thepitches of alternating patterned regions may be the same.
`
`[00011]
`
`The pitches of the adjacent patterned regions may not be even numberinteger multiples.
`
`[00012]
`
`The pitches of the adjacent patterned regions may not be integer multiples.
`
`[00013]
`
`Theplurality of patterned regions may comprise thirteen patterned regions.
`
`[00014]
`
`The plurality of patterned regions may be positioned at odd and even ficld point locations.
`
`[00015]
`
`The plurality of patterned regions may extend in an x direction and in a second direction
`
`orthogonalto the x direction.
`
`[00016]
`
`The measurement system may further comprise: a patterning device; wherein the
`
`illumination system is arranged to illuminate the patterning device with radiation, the patterning device
`
`10
`
`15
`
`20
`
`25
`comprising a first patterned region arrangedto receive the radiation beam and to formaplurality of first
`
`diffraction beams, the first diffraction beams being separated in the shearing direction; wherein the
`
`patterned region of the sensor apparatus comprises a second patterned region; the projection system
`
`being configured to project the first diffraction beams onto the sensor apparatus, the second patterned
`
`region being arranged to receive the first diffraction beams fromthe projection system and to form a
`
`plurality of second diffraction beams from each of the first diffraction beams such that the first and
`
`second patterned regions form a set; wherein the first and second patterned regions in the set are
`
`matched by matching the pitches ofthe first and second patterned regions in the shearing direction such
`that at least some of the second diffraction beams formed from atleast one ofthe first diffraction beams
`
`are spatially coherent with a second diffraction beam formed fromat least one other first diffraction
`
`beam to form interference patterns on the radiation detector; wherein the patterning device comprises a
`
`plurality of first patterned regions and the scnsor apparatus comprisesa plurality of second patterned
`
`regions such that there is a plurality of sets, each set comprising one of the plurality of first patterned
`
`30
`
`35
`
`
`
`WO 2022/100930
`
`PCT/EP2021/077390
`
`regions and one of the plurality of second patterned regions, and wherein the pitches of the first
`
`patterned regions are different in adjacent sets and/or the pitches of the second patterned regions are
`
`different in adjacentsets.
`
`[00017]
`
`The pitches ofthe first patterned regions and the second patterned regionsin at least one of
`
`the plurality of sets may be the same.
`
`[00018]
`
`The measurement system may further comprise a positioning apparatus configured to move
`
`at least one of the patterning device and the sensor apparatus in the shearing direction; and a controller
`
`configured to: control the positioning apparatus so as to moveat least one of the first patterning device
`
`and the sensor apparatus in the shearing direction such that an intensity of radiation received by each
`
`part of the radiation detector varies as a function of the movement in the shearing direction so as to form
`
`oscillating signals corresponding to the different pitches of the first patterned regions in adjacentsets
`
`and/or the different pitches of the second patterned regions in adjacent sects; determine from the radiation
`
`detector phases of harmonics of the oscillating signals at a plurality of posilions on the radiation
`
`detector; and determinea set of coefficients that characterize an aberration mapof the projection system
`
`from the phase of the harmonicsof the oscillating signals at the plurality of positions on the radiation
`detector.
`
`[00019]
`
`Theset of coefficients that characterize the aberration map of the projection system may be
`
`determined by equating the phases of the harmonics of the oscillating signals to a difference in the
`
`aberration map betweenpositions in the pupil plane that are separated in the shearing direction by twice
`
`a shearing distance which corresponds to the distance in the pupil plane between two adjacent first
`
`diffraction beams and solving to find the set of coefficients.
`
`[00020]
`
`Theset of coefficients that characterize the aberration mapof the projection system may be
`
`determined by simultaneously solving constraints for the shearing direction and for a second, orthogonal
`direction.
`
`[00021]
`
`Theplurality of first patterned regions and the plurality of second patterned regions may be
`
`gratings.
`
`[00022]
`
`A lithographic apparatus comprising the measurement system as described above.
`
`[00023]
`
`According to a second aspect of the present invention, there is provided a method for
`
`measurement,
`
`the method comprising:
`
`illuminating a sensor apparatus with radiation, wherein the
`
`sensor apparatus comprises a patterned region arranged to receive at least a portion of the radiation and
`
`to form a plurality of diffraction beams, the diffraction beams being separated in a shearing direction;
`
`wherein the sensor apparatus comprises a radiation detector arranged to receive at least a portion of the
`
`diffraction beams, wherein the patterned region is arranged such that at least some of the diffraction
`
`beams form interference patterns on the radiation detector; wherein the sensor apparatus comprises a
`
`plurality of patterned regions, and wherein pitches of the patterned regions are different in adjacent
`
`patterned regions.
`
`10
`
`15
`
`20
`
`25
`
`30
`
`35
`
`
`
`WO 2022/100930
`
`PCT/EP2021/077390
`
`[00024]
`
`The method may further comprise: illuminating a patterning device with radiation, wherein
`
`the patterning device comprises a first patterned region arranged to receive at least a portion of the
`
`radiation and to form a plurality of first diffraction beams, the first diffraction beams being separated
`
`in the shearing direction; projecting, with the projection system, at least part of the plurality offirst
`
`diffraction beams onto the sensor apparatus comprising: the patlerned region comprising a second
`
`patterned region arrangedto receive the first diffraction beams from the projection system and to form
`
`a plurality of second diffraction beams from each ofthe first diffraction beams; and a radiation detector
`
`arranged to receive at least a portion of the second diffraction beams, wherein the first and second
`
`patterned regionsin the set are matched by matching the pitches ofthe first and second patterned regions
`
`in the shearing direction such that at least some of the second diffraction beams formed fromat least
`
`one ofthe first diffraction beams are spatially coherent with a second diffraction beam formed from at
`
`Icast onc otherfirst diffraction beam to form interference patterns on the radiation detector; wherein the
`
`patterning device comprises a plurality of first patterned regions and the sensor apparatus comprises a
`
`plurality of second patterned regions such that there is a plurality of sets, each set comprising one of the
`
`plurality of first patterned regions and one of the plurality of second patterned regions, and wherein the
`
`pitches of the first patterned regions are different in adjacent sets and/or the pitches of the second
`
`patterned regions are different in adjacentsets.
`
`[00025]
`
`The method may further comprise moving at least one of the patterning device and the
`
`sensor apparatus in the shearing direction such that an intensity of radiation received by each part of the
`
`radiation detector varics as a function of the movementin the shearing direction so as to form a plurality
`
`of oscillating signals corresponding to the different pitches of the first patterned regions in adjacent sets
`
`and/or the different pitches of the second patterned regions in adjacent sets; determining from the
`
`radiation detector phases of harmonics of the oscillating signals at a plurality of positions on the
`
`radiation detector; and determining a set of coefficients that characterize an aberration map of the
`
`projection system from the phase of the harmonicsof the oscillating signals at the plurality of positions
`
`on the radiation detector.
`
`[00026]
`
`The method may further comprise determining the set of coefficients that characterize the
`
`aberration map of the projection system by equating the phases of the harmonics ofthe oscillating
`
`signals to a difference in the aberration map between positions in the pupil plane that are separated in
`
`the shearing direction by twice a shearing distance which correspondsto the distance in the pupil plane
`
`between two adjacentfirst diffraction beams and solving to find the set of coefficients.
`
`[00027]
`
`The method may further comprise determining the set of coefficients that characterize the
`
`aberration mapof the projection system by simultaneously solving constraints for the shearing direction
`
`and for a second, orthogonal direction.
`
`[00023]
`
`The method may further comprise moving the at least one of the patterning device and the
`
`sensor apparatus in the shearing direction in phase steps in a range of 4-9 to form the plurality of
`
`oscillating signals.
`
`10
`
`15
`
`20
`
`25
`
`30
`
`35
`
`
`
`WO 2022/100930
`
`PCT/EP2021/077390
`
`[00029]
`
`According to a third aspect of the present invention, there is provided a computer readable
`
`mediumcarrying a computer program comprising computer readable instructions configured to cause
`
`a computer to carry out a method as described above.
`
`[00030]
`
`According to a fourth aspect of the present invention,
`
`there is provided a computer
`
`apparatus comprising: a memory storing processor readable instructions, and a processor arranged to
`
`read and execute instructions stored in said memory, wherein said processor readable instructions
`
`comprise instructions arranged to control the computer to carry out the method as described above.
`
`
`BRIEF DESCRIPTION OF THE DRAWINGS
`
`10
`
`15
`
`20
`
`[00031]
`
`Embodiments of the invention will now be described, by way of example only, with
`
`reference to the accompanying schematic drawings, in which:
`
`-
`
`-
`
`-
`
`Figure 1 depicts a schematic overvicw of a lithographic apparatus;
`
`Figure 2 is a schematic illustration of a measurement system according to an example;
`
`Figures 3A and 3B are schematic illustrations of a patterning device and a sensor apparatus
`
`which may form part of the measurement system of Figure 2;
`
`-
`
`Figure 4 is a schematic illustration of a measurement system according to an example, the
`
`measurement system comprising a first patterned region and a second patterned region,
`
`the first
`
`patterned region arranged to receive radiation and to form a plurality of first diffraction beams;
`
`-
`
`Figures 5A to 5C each showsa different set of second diffraction beams formed by the second
`
`patterned region of the measurement system shownin Figure 4, that sct of second diffraction beams
`
`having been produced by a different first diffraction beam formed bythe first patierned region;
`
`-
`
`Figure 6A shows the scattering efficiency for a one dimensionaldiffraction grating with a 50%
`
`duty cycle and which may represent the first patterned region of the measurement system shown in
`
`Figure 4;
`
`25
`
`-
`
`Figure 6B showsthe scattering efficiency for a two dimensional diffraction grating of the form
`
`of a checkerboard with a 50% duty cycle and which mayrepresent the second patterned region of the
`
`measurement system shownin Figure 4;
`
`-
`
`Figure 6C shows an interference strength map for the measurement system shown in Figure 4
`
`when employing the first patterned region shown in Figure 6A and the second patterned region shown
`
`in Figure 6B, each of the interference strengths shownrepresenting the second interference beams which
`
`contribute to the first harmonic of the oscillating phase-stepping signal and which have a different
`
`overlap, at the radiation detector, with a circle that represents the numerical aperture of the projection
`
`system PS;
`
`-
`
`Figures 7A, 7B and 7C show the portion of the numerical aperture of the projection system of
`
`the measurement system shown in Figure 4 thatis filled by the three different first diffraction beams
`
`shownin Figure 4;
`
`30
`
`35
`
`
`
`WO 2022/100930
`
`PCT/EP2021/077390
`
`-
`
`Figures 8A-8C show a portion of the radiation detector of the measurement system shown in
`
`Figure 4 which corresponds to the numerical aperture of the projection system of the measurement
`
`system and whichisfilled by three second diffraction beams which originate from thefirst diffraction
`
`beam represented by Figure 7B;
`
`-
`
`Figures 9A-9C show a portion of the radiation detector of the measurement system shown in
`
`Figure 4 which corresponds to the numerical aperture of the projection system of the measurement
`
`system and whichisfilled by three second diffraction beams which originate from the first diffraction
`
`beam represented by Figure 7A;
`
`10
`
`15
`
`20
`
`-
`
`Figures 10A-10C showa portion of the radiation detector of the measurement system shown in
`
`Figure 4 which corresponds to the numerical aperture of the projection system of the measurement
`
`system and whichisfilled by three second diffraction beams which originate from thefirst diffraction
`
`beam represented by Figure 7C;
`
`-
`
`Figure 11A shows a portion of the radiation detector of the measurement system shown in
`
`Figure 4 which corresponds to the numerical aperture of the projection system of the measurement
`
`system and which represents the overlap between the second diffraction beams shown in Figures 8B
`
`and 9A and the overlap between the second diffraction beams shown in Figures 8A and 10B;
`
`-
`
`Figure 11B shows a portion of the radiation detector of the measurement system shown in
`
`Figure 4 which corresponds to the numerical aperture of the projection system of the measurement
`
`system and which represents the overlap between the second diffraction beams shown in Figures 8B
`
`and 10C and the overlap between the second diffraction beams shown in Figures 8C and 9B;
`
`-
`
`Figure 12 is a schematic illustration of a measurement system according to an embodiment of
`
`the invention;
`
`-
`
`Figures 13A and 13B are schematic illustrations of a patterning device and a sensor apparatus
`
`which may form part of the measurement system of Figure 12;
`
`25
`
`-
`
`Figure 14 shows a spatial intensity plot of measurements taken by a measurement system
`
`according to an embodiment of the invention;
`
`-
`
`Figure 15 shows a graph of phase curves of measurements taken by a measurement system
`
`according to an embodimentofthe invention;
`
`-
`
`Figure 16 shows a graph of simulated measurement repeatability (hereinafter referred to as
`
`reproducibility) (repro (nm)) for a measurement system according to an embodimentof the invention;
`
`-
`
`Figure 17 showsa graph of simulated expected position dependence for a measurement system
`
`according to an embodiment of the invention.
`
`DETAILED DESCRIPTION
`
`[00032]
`
`In the present document, the terms “radiation” and “beam” are used to encompass all types
`
`of clectromagnetic radiation, including ultraviolet radiation (c.g. with a wavelength of 365, 248, 193,
`
`30
`
`35
`
`
`
`WO 2022/100930
`
`PCT/EP2021/077390
`
`157 or 126 nm) and EUV(extremeultra-violet radiation, e.g. having a wavelength in the range of about
`
`5-100 nm).
`
`[00033] The term “reticle’’, “mask” or “patterning device” as employed in this text may be broadly
`
`interpreted as referring to a generic patterning device that can be used to endow an incomingradiation
`
`beamwith a patierned cross-section, corresponding to a pattern thal is to be created in a target portion
`
`of the substrate. The term “light valve” can also be used in this context. Besides the classic mask
`
`(transmissive or reflective, binary, phase-shifting, hybrid, etc.), examples of other such patterning
`
`devices include a programmable mirror array and a programmable LCD array.
`
`[00034]
`
`Figure 1 schematically depicts a lithographic apparatus LA. The lithographic apparatus LA
`
`includes an illumination system (also referred to as illuminator) IL configured to condition a radiation
`
`beam B (e.g., UV radiation, DUV radiation or EUV radiation), a mask support (e.g., a mask table) MT
`
`constructed to support a patterning device (c.g., a mask) MA and connectedto a first positioner PM
`
`configured to accurately posilion the pallerning device MA in accordance with certain parameters, a
`
`substrate support(e.g., a wafer table) WT constructed to hold a substrate (e.g., a resist coated wafer) W
`
`and connected to a second positioner PW configured to accurately position the substrate support in
`
`accordance with certain parameters, and a projection system (e.g., a refractive projection lens system)
`
`PS configured to project a pattern imparted to the radiation beam B by patterning device MA onto a
`
`target portion C (e.g., comprising one or more dies) of the substrate W.
`
`[00035]
`
`In operation, the illumination system IL receives a radiation beam from a radiation source
`
`SO, c.g. via a beam delivery system BD. The illumination system IL may include various types of
`
`optical components, such as refractive, reflective, magnetic, electromagnetic, electrostatic, and/or other
`
`types of optical components, or any combination thereof, for directing, shaping, and/or controlling
`
`radiation. The illuminator IL may be used to condition the radiation beam B to have a desired spatial
`
`and angular intensity distribution in its cross section at a plane of the patterning device MA.
`
`[00036]
`
`The term “projection system” PS used herein should be broadly interpreted as
`
`encompassing various types of projection system,
`
`including refractive,
`
`reflective, catadioptric,
`
`anamorphic, magnetic, electromagnetic and/or electrostatic optical systems, or any combination thereof,
`
`as appropriate for the exposure radiation being used, and/or for other factors such as the use of an
`
`immersion liquid or the use of a vacuum. Any use of the term “projection lens” herein may be
`
`considered as synonymouswith the more general term “projection system” PS.
`
`[00037]
`
`Thelithographic apparatus LA may beof a type wherein at least a portion of the substrate
`
`may be covered by a liquid having a relatively high refractive index, e.g., water, so as to fill a space
`
`between the projection system PS and the substrate W — which is also referred to as immersion
`
`lithography. More information on immersion techniquesis given in US6952253, whichis incorporated
`
`10
`
`15
`
`20
`
`25
`
`30
`
`35
`
`herein by reference.
`
`[00038]
`
`The lithographic apparatus LA may also be of a type having two or morc substrate supports
`
`WT(also named “dual stage”). In such “multiple stage’? machine, the substrate supports WT may be
`
`
`
`WO 2022/100930
`
`PCT/EP2021/077390
`
`used in parallel, and/or steps in preparation of a subsequent exposure of the substrate W may be carried
`
`out on the substrate W located on one of the substrate support WT while another substrate W on the
`
`other substrate support WT is being used for exposing a pattern on the other substrate W.
`
`[00039]
`
`In addition to the substrate support WT, the lithographic apparatus LA may comprise a
`
`Measurement stage. The measurement stage is arranged to hold a sensor and/or a cleaning device. The
`
`sensor may be arranged to measure a property of the projection system PS or a property of the radiation
`
`beam B. The measurement stage may hold multiple sensors. The cleaning device may be arranged to
`
`clean part of the lithographic apparatus, for example a part of the projection system PS or a part of a
`
`system that provides the immersion liquid. The measurement stage may move beneath the projection
`
`system PS when the substrate support WT is away from the projection system PS.
`
`[00040]
`
`In operation, the radiation beam B is incident on the patterning device, e.g. mask, MA
`
`which is held on the mask support MT, and is patterned by the pattern (design layout) present on
`
`patterning device MA. Having traversed the mask MA,
`
`the radiation beam B passes through the
`
`projection system PS, which focuses the beam onto a target portion C of the substrate W. With the aid
`
`of the second positioner PW and a position measurement system IF, the substrate support WT can be
`
`moved accurately, e.g., so as to position different target portions C in the path of the radiation beam B
`
`at a focused and aligned position. Similarly, the first positioner PM and possibly another position sensor
`
`(whichis not explicitly depicted in Figure 1) may be used to accurately position the patterning device
`
`MAwith respect to the path of the radiation beam B. Patterning device MA and substrate W may be
`
`aligned using mask alignment marks M1, M2 and substrate alignment marks Pl, P2. Although the
`
`substrate alignment marks Pl, P2 as illustrated occupy dedicated target portions, they may be located
`
`in spaces betweentarget portions. Substrate alignment marks P1, P2 are knownasscribe-lane alignment
`
`marks when these are located between the target portions C.
`
`[00041] To clarify the invention, a Cartesian coordinate system is used. The Cartesian coordinate
`
`system has three axes, i.e., an x-axis, a y-axis and a z-axis. Each ofthe three axes is orthogonal to the
`
`other two axes. A rotation around the x-axis is referred to as an Rx-rotation. A rotation aroundthe y-
`
`axis is referred to as an Ry-rotation. A rotation around about the z-axis is referred to as an Rz-rotation.
`
`The x-axis and the y-axis define a horizontal plane, whereas the z-axis is in a vertical direction. The
`
`Cartesian coordinate systemis not limiting the invention and is used for clarification only. Instead,
`
`another coordinate system, such as a cylindrical coordinate system, may be used to clarify the invention.
`
`The orientation of the Cartesian coordinate system may be different, for example, such that the z-axis
`
`has a componentalong the horizontal plane.
`
`[00042]
`
`In general, the projection system PS has an optical transfer function which may be non-
`
`uniform, which can affect the pattern which is imaged on the substrate W. For unpolarized radiation
`
`such effects can be fairly well described by two scalar maps, which describe the transmission
`
`(apodization) and relative phase (aberration) of radiation cxiting the projection system PS as a function
`
`of position in a pupil plane thereof. These scalar maps, which may bereferred to as the transmission
`
`10
`
`15
`
`20
`
`25
`
`30
`
`35
`
`
`
`WO 2022/100930
`
`PCT/EP2021/077390
`
`map andthe relative phase map, may be expressed as a linear combination of a complete set of basis
`
`functions. A particularly convenient set is the Zernike polynomials, which form a set of orthogonal
`
`polynomials defined on a unit circle. A determination of each scalar map may involve determining the
`
`coefficients in such an expansion. Since the Zernike polynomials are orthogonal on the unit circle, the
`
`Zermike coefficients may be obtained from a measured scalar map by calculating the inner product of
`
`the measured scalar map with each Zernike polynomial in turn and dividing this by the square of the
`
`norm of that Zernike polynomial.
`
`In the following, unless stated otherwise, any reference to Zernike
`
`coefficients will be understood to mean the Zernike coefficients of a relative phase map (also referred
`
`to herein as an aberration map).
`
`It will be appreciated that in alternative examples other sets of basis
`
`functions may be used. For example some examples may use Tatian Zernike polynomials, for example
`
`for obscured aperture systems.
`
`[00043]
`
`The wavefront abcrration map represents the distortions of the wavefront of light
`
`approaching a point in an image plane of the projection system PS from a spherical wavefront (as a
`
`function of position in the pupil plane or, alternatively, the angle at which radiation approaches the
`
`imageplane of the projection system PS). As discussed, this wavefront aberration map W (x,y) may
`
`be expressed as a linear combination of Zernike polynomials:
`
`Wy) = > Cn * Zn(X,Y)
`
`n
`
`(1)
`
`where x and y are coordinates in the pupil plane, Z,,(x, y) is the nth Zernike polynomial and c, is a
`
`coefficient.
`
`It will be appreciated that in the following, Zernike polynomials and coefficients are
`
`labelled with an index which is commonly referred to as a Noll index. Therefore, Z,,(x,y) is the
`
`Zernike polynomial having a Noll index of n and c, is a coefficient having a Noll index of n. The
`
`wavefront aberration map may then be characterized by the set of coefficients c, in such an expansion,
`
`which maybe referred to as Zernike coefficients.
`
`[00044]
`
`It will be appreciated that only a finite number of Zernike orders are taken into account.
`
`Different Zernike coefficients of the phase map may provide information about different forms of
`
`aberration which are caused by the projection system PS. The Zernike coefficient having a Noll index
`
`of | may be referred to as the first Zernike coefficient, the Zernike coefficient having a Noll index of 2
`
`may be referred to as the second Zernike cocfficicnt and so on.
`
`[00045]
`
`Thefirst Zernike coefficient relates to a mean value (which may be referred to as a piston)
`
`of a measured wavefront. The first Zernike coefficient may be irrelevant to the performance of the
`
`projection system PS and as such may not be determined using the methods described herein. The
`second Zernike coefficient relates to the tilt of a measured wavefront in the x-direction. The tilt of a
`
`wavelront in the x-direction is equivalent to a placement in the x-direction. The third Zernike
`
`coefficient relates to the tilt of a measured wavefront in the y-direction. The tilt of a wavefront in the
`
`10
`
`15
`
`20
`
`25
`
`30
`
`
`
`WO 2022/100930
`
`PCT/EP2021/077390
`
`10
`
`y-direction is equivalent to a placement in the y-direction. The fourth Zernike coefficient relates to a
`
`defocus of a measured wavefront. The fourth Zernike coefficient is equivalent to a placement in the z-
`
`direction. Higher order Zernike coefficients relate to other forms of aberration which are caused by the
`
`projection system (e.g. astigmatism, coma, spherical aberrations and other effects).
`
`[00046]
`
`Throughout this description the term “aberrations” should be intended to includeall forms
`
`of deviation of a wavefront from a perfect spherical wavefront. That is, the term “aberrations” may
`
`relate to the placement of an image(e.g. the second, third and fourth Zernike coefficients) and/or to
`
`higher order aberrations such as those which relate to Zernike coefficients having a Noll index of 5 or
`
`more. Furthermore, any reference to an aberration map for a projection system may includeall forms
`
`of deviation of a wavefront froma perfect spherical wavefront, including those due to image placement.
`
`[00047]
`
`The transmission map and the relative phase mapare field and system dependent. Thatis,
`
`in gencral, cach projection system PS will have a different Zermike expansion for cach ficld point (i.c.
`
`for each spatial location in its image plane).
`
`[00048]
`
`Aswill be described in further detail below, the relative phase of the projection system PS
`
`in its pupil plane may be determined by projecting radiation from an object plane of the projection
`
`system PS (i.e. the plane of the patterning device MA), through the projection system PS and using a
`
`shearing interferometer to measure a wavefront (i.e. a locus of points with the same phase). The
`
`shearing interferometer may comprise a diffraction grating, for example a two dimensionaldiffraction
`
`grating, in an image plane ofthe projection system (i.e. the substrate table WT) and a detector arranged
`
`to detect an interference pattern in a plane that is conjugate to a pupil plane of the projection system PS.
`
`[00049]
`
`The projection system PS comprises a plurality of optical elements (including lenses). The
`
`projection system PS may include a number of lenses (e.g. one,
`
`two, six or eight lenses). The
`
`lithographic apparatus LA further comprises adjusting means PA for adjusting these optical elements
`
`so as to correct for aberrations (any type of phase variation across the pupil plane throughoutthe field).
`
`To achieve this, the adjusting means PA may be operable to manipulate optical elements within the
`
`projection system PS in one or more different ways. The projection system may have a co-ordinate
`
`system wherein its optical axis extends in the z direction (it will be appreciated that the direction of this
`
`z axis changes along the optical path through the projection system, for example at each lens or optical
`
`element). The adjusting means PA may be operable to do any combination of the following: displace
`
`one or more optical elements; tilt one or more optical elements; and/or deform one or moreoptical
`
`elements. Displacement of optical elements may be in any direction (x, y, z or a combination thereof).
`
`Tilting of optical elementsis typically out of a plane perpendicular to the optical axis, by rotating about
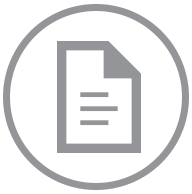
Accessing this document will incur an additional charge of $.
After purchase, you can access this document again without charge.
Accept $ ChargeStill Working On It
This document is taking longer than usual to download. This can happen if we need to contact the court directly to obtain the document and their servers are running slowly.
Give it another minute or two to complete, and then try the refresh button.
A few More Minutes ... Still Working
It can take up to 5 minutes for us to download a document if the court servers are running slowly.
Thank you for your continued patience.
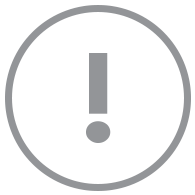
This document could not be displayed.
We could not find this document within its docket. Please go back to the docket page and check the link. If that does not work, go back to the docket and refresh it to pull the newest information.
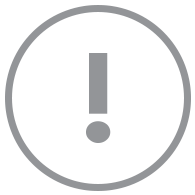
Your account does not support viewing this document.
You need a Paid Account to view this document. Click here to change your account type.
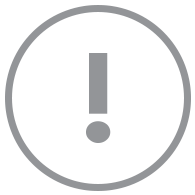
Your account does not support viewing this document.
Set your membership
status to view this document.
With a Docket Alarm membership, you'll
get a whole lot more, including:
- Up-to-date information for this case.
- Email alerts whenever there is an update.
- Full text search for other cases.
- Get email alerts whenever a new case matches your search.
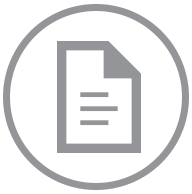
One Moment Please
The filing “” is large (MB) and is being downloaded.
Please refresh this page in a few minutes to see if the filing has been downloaded. The filing will also be emailed to you when the download completes.
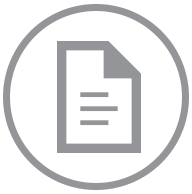
Your document is on its way!
If you do not receive the document in five minutes, contact support at support@docketalarm.com.
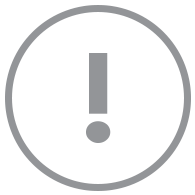
Sealed Document
We are unable to display this document, it may be under a court ordered seal.
If you have proper credentials to access the file, you may proceed directly to the court's system using your government issued username and password.
Access Government Site