`
`Repro
`
`
`0.5
`
`0.45
`
`0.4
`
`
`
`
`
`
`
`Repro(nm)
`
`0.35 F
`
`0.3 F
`
`0.25
`
`0.2
`
`0.15 F
`
`0.1
`
`0.05
`
`
`
`0
`-800
`
`i
`-600
`
`i
`-400
`
`i
`400
`
`J
`600
`
`L
`L
` -200
`0
`200
`Misalignment (nm)
`
`FIG. 16
`
`T
`-0.15
`
`800
`
`
`
`|
`800
`
`Expected position dependence
`
`
`
`
`Expected-Alignedposition(nm)
`
`
`
`
`
`0.2
`
`0.15 F
`
`0.05 F
`
`OF
`
`-0.05 F
`
`0.17
`
`-0.2
`-800
`
`1
`
`A
`
`L
`
`i
`
`i
`
`L
`
`-600
`
`-400
`
` -200
`0
`200
`Misalignment (nm)
`
`400
`
`FIG. 17
`
`i
`600
`
`
`
`
`
`12/13
`
`GbOld
`
`aseud|€0907020070roe9080L
`
`(Id)
`
`
`Vid9poinsesy
`
` -~~—~-gudipsadiioosg———-
`
`SOCLIOI(]sme
`
`gig00¢
`
`S&ov
`
`=oe082.S09
`
`O0L
`
`009005000000¢00}Q
`
`OL
`
`0¢
`
`OV
`
`09
`
`08
`
`
`
`
`11/13
`
`MA” ~
`
`
`16a
`
` 5
`
`5
`5
`WIS
`SX
`ZS:
`foe fo PX
`> 45a)
`| 15b' 15b"
`| 18¢ 15¢
`
`16b”
`
`|
`
`16a’
`
`16 a”
`
`16b’
`
`FIG. 13A
`
`
`
`22
`
` -19a
`
`
`
`20a .49c¢
`
`FIG. 13B
`
`
`
`10/13
`
`
`
`
`
`PA’ CN’
`
`
`
`18a 25a 26a 17b los 26b‘25c
`
`FIG. 12
`
`
`
`9/13
`
`FIG. 11A
`
`FIG. 11B
`
`
`
`
`8/13
`
`FIG. 7A
`
`FIG. 7B
`
`FIG. 7C
`
`FIG. BA
`
`FIG. 8B
`
`FIG. 8C
`
`FIG. 9A
`
`FIG. 9B
`
`FIG. 9C
`
`FIG. 10A
`
`FIG. 10B
`
`FIG. 10C
`
`
`
`
`
`
`
`7/13
`
`grating cifraction field strength
`
`grating difraction field strength
`
`& 6
`
`
`
`
`Diffractionorder(non-shearingditectior)
`&&aw»a
`Interference strength
`
`
`
`
`
`
`
`Diffractionorder(non-shearingdirectior)
`
`Awyey»tea
`
`&
`
`6
`
`4
`
`2
`
`o
`
`2
`
`4
`
`“4
`
`2
`
`8
`
`2
`
`4
`
`6
`
`Diffraction order
`
`(shearing direction)
`
`FIG. 6A
`
`Diffraction order
`
`(shearing direction)
`
`FIG. 6B
`
`
`
`FIG. 6C
`
`
`
`6/13
`
`
`
`
`
`34b —
`
`34d
`
`
`
`34c 34e
`
`34a
`
`39
`
`FIG. 5C
`
`
`
`5/13
`
`
`
`
`
`
`
`
`
`
`
`30 —~
`
`4/13
`
`
`
`
`
`
`
`3/13
`
`
`
`
`
`
`
`
`
`FIG. 3B
`
`
`
`2/13
`
`10
`
`iL
`
`
`
`17a
`
`17b
`
`is 17c
`MA’
`
`15a
`
`15b
`
`15c
`
`17a
`
`17b
`
`
`
`
`
`
`
`PW
`
`
`
`1/13
`
`M,
`
`Ic|cicic]s
`
`
`
`Anta
`falefetetels
`
`
`Y F
`
`i¢{ele]TY
`||tel
`
`IG. 1
`
`
`
`2020P0021 LEP
`
`43
`
`ABSTRACT
`
`A measurement system,
`
`the measurement system comprising: a sensor apparatus; an illumination
`
`system arranged to illuminate the sensor apparatus with radiation, the sensor apparatus comprising a
`
`patterned region arranged to receive a radiation beam and to form a plurality of diffraction beams, the
`
`diffraction beams being separated in a shearing direction; the sensor apparatus comprising a radiation
`
`detector; wherein the patterned region is arranged such that at least some of the diffraction beams form
`
`interference patterns on the radiation detector; wherein the sensor apparatus comprises a plurality of
`
`patterned regions, and wherein pitches of the patterned regions are different in adjacent patterned
`
`regions.
`
`(Fig. 12]
`
`wi
`
`10
`
`
`
`2020P0021 LEP
`
`42
`
`wi
`
`10
`
`21.
`
`The method of any of claims 17 to 20, further comprising moving the at least one of the
`
`patterning device and the sensor apparatus in the shearing direction in phase steps in a range of 4-9 to
`
`form the plurality of oscillating signals.
`
`22,
`
`A computer readable medium carrying a computer program comprising computer readable
`
`instructions configured to cause a computer to carry out a method according to any one ofclaims 16
`to 21.
`
`23.
`
`A computer apparatus comprising:
`
`a memory storing processor readable instructions, and
`
`a processor arranged to read and execute instructions siored in said memory, wherein said
`
`processor readable instructions comprise instructions arranged to control the computer to carry out the
`
`method according to any one of claims 16 to 21.
`
`
`
`2020P0021 LEP
`
`41
`
`the patterned region comprising a second patterned region arrangedto receivethe first diffraction
`
`beams from the projection system and to form a plurality of second diffraction beams from each of the
`
`first diffraction beams; and
`
`wi
`
`10
`
`a radiation detector arranged to receive at least a portion of the second diffraction beams,
`
`wherein the first and second patterned regions in the set are matched by matching the pitches
`
`of the first and second patterned regions in the shearing direction such that at least some of the second
`
`diffraction beams formed from at least one ofthe first diffraction beamsare spatially coherent with a
`seconddiffraction beam formed fromat least one otherfirst diffraction beam to forminterference
`
`patterns on the radiation detector;
`
`wherein the patterning device comprises a plurality of first patterned regions and the sensor
`
`apparatus comprises a plurality of second patterned regions such that there is a plurality of sets, each
`
`sel comprising one ofthe plurality of first patterned regions and oneofthe plurality of second
`
`patterned regions, and
`
`wherein the pitches of the first patterned regions are different in adjacent sets and/or the
`
`pitches of the second patterned regions are different in adjacentsets.
`
`18.
`
`The method of claim 17, further comprising moving at least one of the patterning device and
`
`the sensor apparatus in the shearing direction such that an intensity of radiation received byeach part
`
`of the radiation detector varies as a function of the movement in the shearing direction so as to form a
`
`plurality of oscillating signals corresponding to the different pitches of the first patterned regions in
`
`adjacent sects and/or the different pitches of the second patterned regions in adjacentsets;
`
`determining fromthe radiation detector phases of harmonics of the oscillating signals at a
`
`plurality of positions on the radiation detector; and
`
`determining a set of coefficients that characterize an aberration map ofthe projection system
`
`fromthe phase of the harmonics of the oscillating signals at the plurality of positions on the radiation
`detector.
`
`19.
`
`The methodof cither of claims 17 or 18, further comprising determining the sct of
`
`coefficients that characterize the aberration map of the projection system by equating the phases of the
`
`30
`
`harmonics ofthe oscillating signals to a difference in the aberration map between positions in the
`
`pupil plane that are separated in the shearing direction by twice a shearing distance which corresponds
`
`to the distance in the pupil plane between two adjacentfirst diffraction beams and solving to find the
`set of coefficients.
`
`20.
`
`The method of any of claims 17 to 19, further comprising determining the set of coefficients
`
`that characterize the aberration map of the projection system by simultaneously solving constraints for
`
`the shearing direction and for a second, orthogonaldirection.
`
`
`
`2020P0021 LEP
`
`40
`
`determinea set of coefficients that characterize an aberration map of the projection
`
`system from the phase of the harmonics ofthe oscillating signals at the plurality of positions on the
`radiation detector.
`
`wi
`
`10
`
`30
`
`12.
`
`The measurement system of claim 11, wherein the set of coefficients that characterize the
`
`aberration map of the projection system are determined by equating the phases of the harmonics of the
`
`oscillating signals to a difference in the aberration map between positions in the pupil plane that are
`
`separated in the shearing direction by twice a shearing distance which correspondsto the distance in
`
`the pupil plane between two adjacentfirst diffraction beams and solving to find the set of coefficients.
`
`13.
`
`The measurement system of claim 12, wherein the set of coefficients that characterize the
`
`aberration map of the projection sysiem are determined by simultaneously solving constraints for the
`
`shearing direction and for a second, orthogonal direction.
`
`14.
`
`The measurement system of any of claims 9-13, wherein the plurality offirst patterned
`
`regionsandthe plurality of second patterned regions are gratings.
`
`15.
`
`A lithographic apparatus comprising the measurement system of anyone of claims 1 to 14.
`
`16.
`
`A method for measurement, the method comprising:
`
`illuminating a sensor apparatus with radiation, wherein the sensor apparatus comprises a
`
`patterned region arranged to receive at least a portion of the radiation and to forma plurality of
`
`diffraction beams, the diffraction beams being separated in a shearing direction;
`
`wherein the sensor apparatus comprises a radiation detector arranged to receive at least a
`
`portion of the diffraction beams,
`
`wherein the patterned region is arranged such that at least some of the diffraction beams form
`
`interference patterns on the radiation detector;
`
`whercin the scnsor apparatus comprisesa plurality of patterned regions, and
`
`wherein pitches of the patterned regions are different in adjacent patterned regions.
`
`17.
`
`The method of claim 16, the method further comprising:
`
`illuminating a patterning device with radiation, wherein the patterning device comprises a
`
`first patterned region arranged to receive at least a portion of the radiation and to form a plurality of
`
`first diffraction beams,the first diffraction beams being separated in the shearing direction;
`
`projecting, with the projection system,at least part of the plurality of first diffraction beams
`
`onto the sensor apparatus comprising:
`
`
`
`2020P0021 LEP
`
`39
`
`a patterning device;
`
`wherein the illumination system is arrangedto illuminate the patterning device with radiation,
`
`the patterning device comprising a first patterned region arranged to receive the radiation beam and to
`
`form a plurality of first diffraction beams, the first diffraction beams being separated in the shearing
`
`wi
`
`direction;
`
`wherein the patterned region of the sensor apparatus comprises a second patterned region;
`
`the projection system being configured to project the first diffraction beams onto the sensor
`
`apparatus, the second patterned region being arranged to receive thefirst diffraction beams from the
`
`projection system and to form a plurality of second diffraction beams from each ofthe first diffraction
`
`10
`beams suchthat the first and second patterned regions formaset;
`
`wherein the first and second patterned regions in the set are matched by matching the pitches
`
`of the first and second patterned regions in the shearing direction such that al least some of the second
`
`diffraction beams formed from at least one ofthe first diffraction beamsare spatially coherent with a
`second diffraction beam formed from at least one otherfirst diffraction beam to form interference
`
`patterns on the radiation detector;
`
`wherein the patterning device comprises a plurality of first patterned regions and the sensor
`
`apparatus comprises a plurality of second patterned regions such that there is a plurality of sets, each
`
`set comprising one ofthe plurality of first patterned regions and oneofthe plurality of second
`
`patterned regions, and
`
`wherein the pitches of the first patterned regions are different in adjacent sets and/or the
`
`pitches of the second patterned regions are different in adjacentscts.
`
`10.
`
`The measurement system of claim 9, wherein the pitches of the first patterned regions and the
`
`second patterned regions in at least one ofthe plurality of sets are the same.
`
`11.
`
`The measurement system of either of claims 9 or 10, further comprising a posilioning
`
`apparatus configured to moveat least one of the patterning device and the sensor apparatusin the
`
`shearing direction; and
`
`a controller configured to:
`
`30
`
`control the positioning apparatus so as to moveat least oneofthe first patterning
`
`device and the sensor apparatus in the shearing direction such that an intensity of radiation received
`
`by eachpart of the radiation detector varies as a function of the movement in the shearing direction so
`
`as to form oscillating signals corresponding to the different pitches of the first patterned regions in
`
`adjacent sets and/or the different pitches of the second patterned regions in adjacentsets;
`
`determine from the radiation detector phases of harmonicsof the oscillating signals at
`
`a plurality of positions on the radiation detector; and
`
`
`
`2020P0021 LEP
`
`38
`
`CLAIMS
`
`1.
`
`A measurement system, the measurement system comprising:
`
`a sensor apparatus;
`
`wi
`
`10
`
`an illumination systemarrangedto illuminate the sensor apparatus with radiation, the sensor
`
`apparatus comprising a patterned region arranged to receive a radiation beam andto form a plurality
`
`ofdiffraction beams, the diffraction beams being separated in a shearing direction;
`
`the sensor apparatus comprising a radiation detector;
`
`wherein the patterned region is arranged such that at least some ofthe diffraction beams form
`
`interference patterns on the radiation detector;
`
`wherein the sensor apparatus comprises a plurality of patterned regions, and
`
`wherein piiches of the patterned regions are different in adjacent patterned regions.
`
`2.
`
`The measurement system of claim 1, wherein the measurement system is arranged such that
`
`the interference patterns from adjacent patterned regions at least partially overlap at the radiation
`detector.
`
`3.
`
`The measurement system of either of claims | or 2, wherein the pitches of alternating
`
`patterned regions are the same.
`
`4.
`
`The measurement system of any preceding claim, wherein the pitches of the adjacent
`
`patterned regions are not even numberinteger multiples.
`
`5.
`
`The measurement system of claim 4, wherein the pitches of the adjacent patterned regions are
`
`not integer multiples.
`
`6.
`
`The measurement system of any preceding claim, wherein the plurality of patterned regions
`
`comprise thirtecn patterned regions.
`
`30
`
`7.
`
`The measurement system of any preceding claim, wherein the plurality of patterned regions
`
`are positioned at odd and evenfield point locations.
`
`8.
`
`The measurement system of any preceding claim, wherein the plurality of patterned regions
`
`extend in an x direction and in a second direction orthogonalto the x direction.
`
`9.
`
`The measurement system of any preceding claim, the measurement system further
`
`comprising:
`
`
`
`2020P0021 LEP
`
`37
`
`wi
`
`10
`
`[000169] Although specific reference may be madein this text to the use of a lithographic apparatus
`
`in the manufacture of ICs, it should be understood that the lithographic apparatus described herein may
`
`have other applications. Possible other applications include the manufacture of integrated optical
`
`systems, guidance and detection patterns for magnetic domain memories, flat-panel displays, liquid-
`
`crystal displays (LCDs), thin-film magnetic heads, etc.
`
`[000170] Although specific reference may be madein this text to embodiments of the invention in
`
`the context ofa lithographic apparatus, embodiments of the invention may be used in other apparatus.
`
`Embodiments of the invention may formpart of a mask inspection apparatus, a metrology apparatus, or
`
`any apparatus that measures or processes an object such as a wafer (or other substrate) or mask (or other
`
`patterning device). These apparatus may be generally referred to as lithographic tools. Such a
`
`lithographic tool may use vacuumconditions or ambient (non-vacuum) conditions.
`
`[000171] Although specific reference may have been made above to the use of embodiments of the
`
`invention in the context of optical lithography, it will be appreciated that the invention, where the
`
`context allows, is not limited to optical lithography and maybe used in other applications, for example
`
`imprint lithography.
`
`[000172] Where the context allows, embodiments of the invention may be implemented in hardware,
`
`firmware, software, or any combination thereof. Embodiments of the invention may also be
`
`implemented as instructions stored on a machine-readable medium, which may be read and executed
`
`by one or more processors. A machine-readable medium may include any mechanism for storing or
`
`transmitting information in a form readable by a machine (e.g., a computing device). For example, a
`
`machine-readable medium may include read only memory (ROM); random access memory (RAM);
`
`magnetic storage media; optical storage media; flash memory devices; electrical, optical, acoustical or
`
`other forms of propagated signals (e.g. carrier waves, infrared signals, digital signals, etc.), and others.
`
`Further, firmware, software, routines,
`
`instructions may be described herein as performing certain
`
`actions. However, it should be appreciated that such descriptions are merely for convenience andthat
`
`such actions in fact result from computing devices, processors, controllers, or other devices executing
`
`the firmware, software, routines, instructions, etc. and in doing that may cause actuators or other devices
`
`to interact with the physical world.
`
`[000173] While specific embodiments of the invention have been described above,
`
`it will be
`
`30
`
`appreciated that the invention may be practiced otherwise than as described. The descriptions above are
`
`intended to be illustrative, not limiting. Thus it will be apparent to one skilled in the art that
`
`modifications may be madeto the invention as described without departing fromthe scope of the claims
`set out below.
`
`
`
`2020P0021 LEP
`
`36
`
`wi
`
`10
`
`[000163]
`
`For a third order polynomialfit, that may be used on the seven field point measurements of
`
`a measurement system, the thirteen field point measurements may improve the reproducibility of the
`
`measurement system by 1.5x. For overlapping spots potentially less improvement for higher order
`
`Zernikes may be achieved. Howeverfor a particular system control mainly lower order Zernikes may
`
`be of interest and thus the results for the higher order Zernikes may not be as important. The
`
`measurement may also improve overlay accuracy.
`
`[000164]
`
`In embodiments,
`
`the measurement system may be an alignment sensor rather than a
`
`measurement system for measuring aberrations.
`
`[000165]
`
`For an alignment sensor, generally, an alignment mark, such as a diffraction grating or
`
`another type of alignment mark, is provided on a substrate. The alignment sensor projects optical pulses
`
`onto the alignment mark (e.g. mask alignment marks M1, M2 or substrate alignment marks P1, P2) in
`
`order to be scattered by the alignment mark. An intensity of the scattered optical pulses is measured by
`
`a detector, and position information (expressing the position of the alignment mark in respect of for
`
`example the alignment sensor) is derived therefrom.
`
`[000166]
`
`In the present embodiment, patterned regions (i.e. diffraction gratings) of the sensor
`
`apparatus may be consideredto be the alignment marks. In a similar way as described above, adjacent
`
`diffraction gratings may have different pitches to allow overlapping radiation from the adjacent
`
`diffraction gratings detected by a radiation detector to be disentangled. For example, thirteen field
`
`points, instead of seven field points may be measured using the measurement system to measure
`
`alignment of e.g. a substrate.
`
`[000167]
`
`In cmbodiments, the alignment sensor may have a sensor apparatus comprising a radiation
`
`detector. The alignment sensor may comprise an illumination system arranged to illuminate the sensor
`
`apparatus with radiation. The sensor apparatus may comprise a plurality of patterned regions arranged
`
`to receive a radiation beam and to form a plurality of diffraction beams, the diffraction beams being
`
`separated in a shearing direction. The patterned regions may comprise a diffraction grating, e.g. in the
`
`form of a checkerboard with a 50% duty cycle. In the alignment sensor, the patterning device may not
`
`be needed and thus there may not befirst patterned regions and second patterned regions, although the
`
`patterned regions of the alignment sensor may be considered to be in the same position as the second
`
`patterned regions of the embodiment of Figure 12.
`
`30
`
`[000168]
`
`In the alignment sensor, in a similar way as with the second patterned regions ofthe
`
`embodiment of Figure 13B, the pitches of the patterned regions are different in adjacent patterned
`
`regions. The pitches of the adjacent patterned regions being different allows overlapping radiation at
`
`the radiation detector to he disentangled to differentiate the signals from adjacent patterned regions.
`
`This allows an increased numberof field points to be measured in a single measurement. This allows
`
`an increased amount of data to be used in measuring alignment and may lead to a more accurate
`
`alignment measurement.
`
`
`
`2020P0021 LEP
`
`35
`
`fit B points to provide a decomposition A line and a decomposition B line respectively. As can be seen
`
`from the graph, decomposition A has a period whichis three times the period of decomposition B (i.e.
`
`three full sine waves are shown for decomposition B for the one sine wave of decomposition A) and
`
`thus, decomposition A maps onto the even field points, which, in this case, have gratings with pitches
`
`which are three times less than that of the gratings at the odd field points.
`
`[000158] More particularly, since the period is known (from the pitches of the gratings) the phase
`
`may be determined at each pixel location and a phase map for each ofthe pixels may be provided. In
`
`this case a total of nine phase steps are usedto illustrate the situation. However, it will be appreciated
`
`that, in other embodiments, a different number of phase steps may be used. Tofit the sine wave for the
`
`gratings with a different pitch, then a minimum of 4 phase steps would be required. This is because
`
`wi
`
`10
`
`there are four unknowns, two phases and two amplitudes.
`
`[000159]
`
`The phase map may then be linearly fitted to the Zernike coefficients to provide the
`
`aberration map. The aberration map provides the aberrations for the projection system PS’.
`
`[000160]
`
`Figure 16 shows a graph indicating simulated measurementreproducibility (repro (nm)) for
`
`eight phase steps with one grating having a 3x smaller pitch than the adjacent grating. The
`
`reproducibility per field point may be on par with the reproducibility per field point achieved currently
`
`(straight black line in Figure 16, top). This means that by introducing the additional field points (e.g.
`
`at the even field point locations) the amount of data collected in a single measurement may be increased
`
`from seven field points to thirteen field points with the same or similar reproducibility per field point.
`
`The reproducibility may be considered to be an assessmentof the noise of the measurement.
`
`[000161]
`
`Figure 17 shows a graph indicating simulated expected position dependencefor cight phase
`
`steps and one grating having a 3x smaller pitch than the adjacent grating. Misalignment (nm) may
`
`indicate what happens whenthefirst and second patterned regions are not optimally aligned. That is,
`
`when the patterning device is not at the position expected.
`
`It may be desired to minimize expected
`
`position dependence. This may be donein two ways, increasing the numberof phase steps and choosing
`
`different piiches.
`
`Increasing the number of phase steps has a disadvantage of increasing time of
`
`measurementso it may be desired to optimize these variables for a particular implementation.
`
`[000162]
`
`The reproducibility and expected position dependency may be simulated with a particular
`
`camera non-linearity. With this camera non-linearity, for example, eight phase steps may be needed.
`
`30
`
`With a camera chip having less nonlinearity, less than eight phase steps may be used. Increasing the
`
`number of phase steps may reduce error in measurements but will increase time for the measurements.
`
`With more than 5 phasesteps the actual gain in cycle is small when comparing the two measurements
`
`of the seven field points with the one measurement of the thirteen field points: 2 (separate odd and even
`
`field points measurement) x 2 (u, v directions) x 5 (phase steps) is not that much slower than | (both
`
`odd and even field points in one measurement) x 2 (u, v directions) x 8 (phase steps). In embodiments,
`
`the numberof phase steps used maybe e.g. 4, 5, 6, 7, 8 or 9.
`
`
`
`2020P0021 LEP
`
`34
`
`regions or the second patterned regions in adjacent sets maybe different in adjacentsets, i.e. either the
`
`first or the second patterned regions may have pitches that are the samefor adjacent gratings.
`
`It may
`
`be preferable for the pitches of the second patterned regions in adjacent sets to be different rather than
`
`the pitches of the first patterned regions in adjacentsets to be different.
`
`wi
`[000152]=Tn embodiments, the pitches of alternating patterned regions may be the same. That is, the
`
`pitch of every other diffraction grating may be the same. For example, the pitches of each of the
`
`additional diffraction gratings 20a-20b may be the same and the pitches of each ofthe diffraction
`
`gratings 19a-19c may be the same (with the pitch of the adjacent diffraction gratings still being
`
`different). This may simply require calculations to disentangle the signals. However, in embodiments,
`
`10
`
`the pitches of the alternating patterned regions may be different as well as the adjacent patterned regions
`
`being different.
`
`[000153]
`
`Figure 14 showsa spatial iniensily plot of measurements taken by the measurement system
`
`11 with an example thirteen field points being measured. The x andy axes showthespatial position in
`
`bits with the intensity bar on the right measuring up to 1000. It may be seen that the intensity is highest
`
`in the centre of the field points but that there is some overlap between field points. The field points
`
`have enough separation to allowthirteen field points onto the sensor apparatus 22 without saturating
`
`the radiation detector 24 (e.g. a camera). The thirteen field points may require thirteen sets of first and
`
`second patterned regions.
`
`[000154]
`
`Figure 15 showsthe different phase curves measured on different positions on the camera.
`
`More particularly, Figure 15 shows a front graph of phase (pi) for the camera and a rear graph indicating
`
`the spatial position for the camera for the field points. For the back graph, the x and y axes again show
`
`the spatial position in bits.
`
`[000155]
`
`In this embodiment, the pitches of the additional patterned regions 16a-16b are three times
`
`less than that of patterned regions 15a-15c and the pitches ofthe additional diffraction gratings 20a-20b
`
`are three times less than that of the diffraction gratings 19a-19c. That is, the pitches of the gratings in
`
`the even field point locations are three times less than the pitches in the odd field point locations. For
`
`clarity, Figure 15 only showsthree of the thirteen field points, but it will appreciated that the remaining
`
`ten could be shownsimilarly. The even and odd ficld points may more gencrally be considered to be
`
`adjacent field points.
`
`30
`
`[000156] As can be seen from the position and intensity graph in Figure 15, there are overlapping
`
`regions between the detected radiation for adjacent field points. Each field point may have a plurality
`
`of diffraction beams which interfere (i.e. diffraction beams with different orders). Some of these
`
`diffraction beams may overlap as shown.
`
`[000157]
`
`In the phase and intensity graph of Figure 15, the fit of the measurements taken by the
`
`measurement system 11 is shown (i.e. the measured line) indicating intensity peaks for the field points
`
`locations. The phase and corresponding intensity can be fitted to distinguish between the signals from
`
`the odd field points and the signals from the even field points. Lines may be fitted to fit A points and
`
`
`
`2020P0021 LEP
`
`33
`
`wi
`
`10
`
`at even field point locations, e.g. at positions 2, 4, 6, 8, 10 and 12 in a thirteen field point line. However,
`
`due to the diffraction gratings being closer together, pixels on the radiation detector 24 may receive
`
`signals from more than one diffraction grating (i.e. more than one measurement beam.) Thus, in the
`
`embodiment of Figures 13A and 13B, the interference patterns formedon the radiation detector 24 may
`
`overlap to a certain extent. This is not specifically shown in Figure 12 for clarity reasons.
`
`[000147]
`
`In orderto distinguish the signals from the pixels which have overlapping radiation incident
`
`thereon from more than one measurement beam from adjacent diffraction gratings,
`
`the adjacent
`
`diffraction gratings have different pitches. This introduces encoding for the information from adjacent
`
`diffraction gratings.
`
`[000148]
`
`In the embodiment of Figures 13A and 13B thepitches of the additional patterned regions
`
`16a-16b are shown being two times that of patterned regions 15a-15c. Thatis, the additional patterned
`
`regions 16a-16b are shown having approximately two times the numberof grating lines as that of the
`
`patterned regions 15a-15c.
`
`In addition, the pitches of the additional diffraction gratings 20a-20b are
`
`shown being two times that of the diffraction gratings 19a-19c. That is, the additional diffraction
`
`gratings 20a-20b are shown having approximately two times the numher of checkerboard boxes as that
`
`of the diffraction gratings 19a-19c. However, this is just an example, and in other embodiments, the
`
`pitches of the additional patterned regions 16a-16b maybe different multiples of the patterned regions
`
`15a-15c and the pitches of the additional diffraction gratings 20a-20b maybe different multiples of the
`
`diffraction gratings 19a-19c, e.g. 3 times larger.
`
`[000149]
`
`For example, the pitches of the of the additional patterned regions 16a-16b may be non-
`
`integer multiples of the patterned regions 15a-15c¢ and the pitches of the additional diffraction gratings
`
`20a-20b may be non-integer multiples of the diffraction gratings 19a-19c. Software (e.g. algorithms)
`
`may be programmedto disentangle the signals from adjacent gratings without requiring them to have
`
`pitches ofinteger multiples. Furthermore, having non-integer multiples may provide more freedom to
`
`choose the particular difference in pitch,
`
`i.e.
`
`there may be more choice to obtain the desired
`
`performance.
`
`It may be preferable that the pitches of adjacent diffraction gratings (e.g. additional
`
`diffraction grating 20a and diffraction grating 19a) are not even numberinteger multiples as, since the
`
`gratings may have a 50% duty cycle (i.c. checkerboard design), then even diffraction orders, c.g. factor
`
`2,4, 6 etc. may be difficult, or not possible, to distinguish between adjacent gratings.
`
`30
`
`[000150]
`
`In embodiments, the first and second patterned regions only extend in the x-direction(i.e.
`
`a single direction) so they are 1D but, in other embodiments, the first and second patterned regions may
`
`extend in both the x-direction and the y-direction (i.e. two orthogonal directions) so they are 2D. In the
`
`2D case, adjacent patterned regions may have different pitches in both directions.
`
`[000151]
`
`In embodiments, the pitches of the first patterned regions (patterned regions 15a-15c and
`
`additional patterned regions 16a-16b) may be different in adjacent sets and the pitches of the second
`
`patterned regions (diffraction gratings 19a-19c¢ and additional diffraction gratings 20a-20b) may be
`
`different in adjacent sets. However, in other embodiments, the pitches of either the first patterned
`
`
`
`2020P0021 LEP
`
`32
`
`may control an adjusting means PA’ for adjusting components of the projection system PS’. For
`
`example, the adjusting means PA’ may adjust optical elements of the projection system PS’ so as to
`
`correct for aberrations which are caused by the projection system PS’ and which are determined by the
`controller CN’.
`
`wi
`
`10
`
`[600143] Determining aberrations (which may be caused by the projection system PS or by
`
`placement errors of the patterning device MA or the substrate W) may comprise fitting the
`
`measurements which are made by the sensor apparatus 22 to Zernike polynomials in order to obtain
`
`Zernike coefficients. Different Zernike coefficients may provide information about different forms of
`
`aberration which are caused by the projection system PS’. Zernike coefficients may be determined
`
`independently at different positions in the x and/or the y-directions. For example, in the embodiment
`
`which is shown in Figures 12, 13A and 13B, Zernike coefficients may be determined for each
`measurement beam 17a-17c and for each additional measurement beam 18a-18b.
`
`[000144]
`
`In this embodiment, the measurement patterning device MA’’ comprises five patterned
`
`regions I5a-15c, 16a-16b, and the sensor apparatus 22 comprises five detector regions 25a-25c, 26a-
`
`26b and five measurement beams 17a-17c, 18a-18b are formed. This allows the Zernike coefficients
`
`to be determined at more positions (i.e. more field points) than in the example of Figures 2, 3A and 3B.
`
`In some embodiments the measurement patterning device MA’’ may comprise more than five patterned
`
`regions, the sensor apparatus 22 may comprise more than five detector regions and more than five
`
`measurement beams may be formed.
`
`In some embodiments the patterned regions and the detector
`
`regions may be distributed at different positions in both the x and y-directions. This may allow the
`
`Zernike coefficients to be determined at positions which are separated in both the x and the y-directions.
`
`[000145]
`
`If more field points are measured,
`
`then there is more potential for correction of the
`
`aberrations. For example, by inserting an additional lens to manipulate the wavefront. This may result
`
`in more degrees of freedom and thus a mo
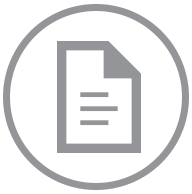
Accessing this document will incur an additional charge of $.
After purchase, you can access this document again without charge.
Accept $ ChargeStill Working On It
This document is taking longer than usual to download. This can happen if we need to contact the court directly to obtain the document and their servers are running slowly.
Give it another minute or two to complete, and then try the refresh button.
A few More Minutes ... Still Working
It can take up to 5 minutes for us to download a document if the court servers are running slowly.
Thank you for your continued patience.
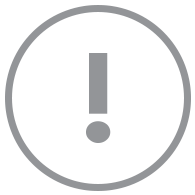
This document could not be displayed.
We could not find this document within its docket. Please go back to the docket page and check the link. If that does not work, go back to the docket and refresh it to pull the newest information.
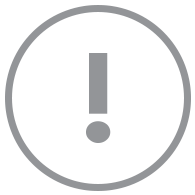
Your account does not support viewing this document.
You need a Paid Account to view this document. Click here to change your account type.
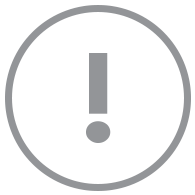
Your account does not support viewing this document.
Set your membership
status to view this document.
With a Docket Alarm membership, you'll
get a whole lot more, including:
- Up-to-date information for this case.
- Email alerts whenever there is an update.
- Full text search for other cases.
- Get email alerts whenever a new case matches your search.
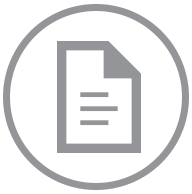
One Moment Please
The filing “” is large (MB) and is being downloaded.
Please refresh this page in a few minutes to see if the filing has been downloaded. The filing will also be emailed to you when the download completes.
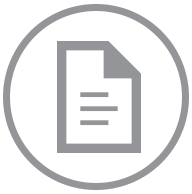
Your document is on its way!
If you do not receive the document in five minutes, contact support at support@docketalarm.com.
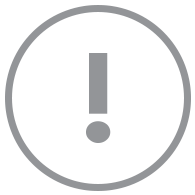
Sealed Document
We are unable to display this document, it may be under a court ordered seal.
If you have proper credentials to access the file, you may proceed directly to the court's system using your government issued username and password.
Access Government Site