`
`(19) —d
`
`Europaisches Patentamt
`
`European Patent Office
`
`Office européen des brevets
`
`(11)
`
`EP 1 376 185 A2
`
`(12)
`
`EUROPEAN PATENT APPLICATION
`
`(48) Date of publication:
`02.01.2004 Bulletin 2004/01
`
`(51) Int cl.7; GO2B 7/18
`
`(21) Application number: 03013982.8
`
`(22) Date offiling: 20.06.2003
`
`(84) Designated Contracting States:
`AT BE BG CH CY CZ DE DKEE ESFI FR GB GR
`HU IE ITLILU MC NL PT RO SE SISK TR
`
`(71) Applicant: Nikon Corporation
`Tokyo 100-8331 (JP)
`
`Designated Extension States:
`AL LT LV MK
`
`(72) Inventor: Sogard, Michael
`Menlo Park, CA 94025 (US)
`
`(80) Priority: 20.06.2002 US 390293 P
`04.06.2003 US 455750 P
`
`(74) Representative: Viering, Jentschura & Partner
`Patent- und Rechtsanwéalte,
`Steinsdorfstr. 6
`
`80538 Miinchen (DE)
`
`(54) Minimizing thermal distortion effects on EUV mirror
`
`has a high heattransfer coefficient even if its pressure
`(57)=Amirroris provided with throughholes, or chan-
`is not too high.
`In some applications the gap may be
`nels, formed through its main body and a coolant pipe
`of a heat-conductive material is inserted in each of the
`filled with a heat-conductive fluid. It may be preferable,
`depending upon the circumstances, to form these chan-
`nels proximally to the surface on which radiation is made
`incident. Additionally, the surface of the side of the mirror
`opposite the reflective side may be heated by auxiliary
`heat sources.
`
`channels for passing a cooling fluid inside. The outer
`wall of the coolant pipe does not contact the inner wall
`of the channel, and thereis left a gap in between. The
`gap contains aheat-conducting gas such as helium. The
`
`
`gap is of a width of less than 100 um such that the gas
`
`EP1376185A2
`
`148
`
`127
`
`FIG. 1A
`
`Printed by Jouve, 75001 PARIS (FR)
`
`
`
`EP 1 376 185 A2
`
`Description
`
`BACKGROUND OF THE INVENTION
`
`[0001] This invention is in the technical field of mirrors such as extreme ultraviolet (EUV) mirrors and relates in
`particular to the problem of minimizing thermal distortion effects on such a mirror.
`[0002] The EUV mirror absorbssignificant amounts of heat from the EUV radiation primarily because its reflectivity
`is not very high. The absorbed heat causesdistortion of the mirror surface from thermal expansion effects. The distortion
`in turn leads to optical aberrations and hence must be minimized as much as possible by whatever means. The thermal
`distortion has been modeled and is generally considered to consist of (1) a local distortion which is associated with
`the local temperature distortion, and (2) a so-called "global distortion" which is related to thermal stresses which alter
`the shape of the entire mirror. Both of these typesof distortion must be appropriately dealt with. The present invention
`relates to the problem of global distortion.
`[0003] The global distortion depends both on the thermal and mechanical boundary conditions and constraints, and
`on the details of the mirror design and illumination pattern. In some studies, it is assumed that the back of the mirror
`is in contact with a temperature reservoir. This may be expected to minimize distortion because a maximum amount
`of heat can thus be removed, but this may be true only with regard to the local distortions. Since the heated front
`surface coupled with the cooled back surface creates a temperature gradient in the direction approximately perpen-
`dicular to the mirror surface, this may lead to "bowing" of the mirror.
`If the mirror is held kinematically, nothing will
`prevent such a bowing effect. Thus, such a cooling technique should be avoided, unless the back of the mirror can be
`attached to a base plate which is a part of the temperature reservoir and is rigid enough to prevent the mirror from
`bowing. Local distortions will still remain.
`
`SUMMARYOF THE INVENTION
`
`10
`
`15
`
`20
`
`25
`
`30
`
`[0004] An EUV mirror embodying this invention may be characterized as having throughholes, or channels, formed
`within the mirror member and a coolantpipe of a heat-conductive material inserted in each of the channels for passing
`a cooling fluid inside, its outer wall not contacting the wall of the channel but leaving a gap in between. It may be
`preferable to form these channels proximally to the surface on which light in made incident. The gap contains a gas
`with high thermal conductivity such as helium which is maintained below atmospheric pressure. The gap is of a width
`of less than 100 um such that the gas hasahigh heattransfer coefficient even if its pressure is not too high. The
`coolant flow may behighly turbulent, to further increase heat transfer from the mirror. Additionally, the mirror may be
`heated on its rear surface, the surface opposite the reflective surface, to eliminate residual global thermal distortion.
`In other applications the gap may contain a thermally conductive fluid maintained at a pressure comparable to the
`ambient pressure surrounding the mirror.
`
`35
`
`BRIEF DESCRIPTION OF THE DRAWING
`
`40
`
`45
`
`50
`
`55
`
`[0005] The invention, together with further objects and advantages thereof, may best be understood with reference
`to the following description taken in conjunction with the accompanying drawings in which:
`
`Fig. 1A is a schematic optical diagram of a representative embodimentof an X-ray microlithography system com-
`prising at least one multilayer-film reflective optical element according to any of the embodiments of this invention,
`Fig 1B is a detailed view of the projection-optical system of the microlithography system shownin Fig. 1A, and
`Fig. 1C is aschematic optical diagram of another representative embodiment of an X-ray microlithography system
`comprising at least one multilayer-film reflective optical element (including a reflective reticle) according to any of
`the embodiments of this invention;
`
`Fig. 2 is a process flow diagram illustrating an exemplary process by which semiconductor devices are fabricated
`by using the apparatus shownin Fig. 1 according to the present invention;
`
`Fig. 3 is a flowchart of the wafer processing step shownin Fig. 2 in the case of fabricating semiconductor devices
`according to the present invention;
`
`Fig. 4 is a schematic drawing of an EUV mirror system embodying this invention, including a EUV mirror of which
`a schematic sectional view is included;
`
`Fig. 5A is a schematic sectional view of one of the cooling channels and Fig. 5B is a schematic sectional view of
`
`
`
`a cooling channel having more than one pipe (two pipes) therethrough;
`
`EP 1 376 185 A2
`
`Fig. 6 is a graph showing the relationship between the heattransfer coefficient of helium gas in a gap and its
`pressurefor different gap widths;
`
`Fig. 7 showsthe heat transfer coefficient of the coolant within the cooling tube for conditions ofa full turbulent flow
`and a laminarflow;
`
`Fig. 8A is a schematic sectional view of a cooling system embodying the invention;
`
`Fig. 8B is a schematic sectional view of the cooling system of Fig. 8A;
`
`Fig. 8C is a schematic sectional view of another cooling system embodying the invention;
`
`Fig. 8D a schematic sectional view of another embodiment of the cooling channels;
`
`Figs. 9A and 9B are schematic sectional viewsofstill another cooling system embodying the invention, Fig. 9A
`being a sectional view taken along line 9A-9A of Fig. 9B and Fig. 9B is a sectional view taken along line 9B-9B of
`Fig. 9A;
`
`Fig. 10 defines the terms and coordinate system describing the temperature distribution in the mirror;
`
`Fig. 11 is a schematic which defines cooling planes relative to the cooling channels;
`
`Fig. 12 shows an embodimentof a control system which provides appropriate heating to the back surface of the
`mirror;
`
`Fig. 13 shows an embodimentof a radiant heating system for the back surface of the mirror;
`
`Fig. 14 shows an embediment of a heating system with a remote radiation source which is projected onto the back
`of the mirror;
`
`Fig. 15 shows another embodimentof part of a projection heating system for the back surface of the mirror; and
`
`Fig. 16 is a schematic illustration of another embodiment of a projection heating system which can provide real
`time correction to the radiation intensity distribution at the back of the mirror.
`
`DETAILED DESCRIPTION OF THE INVENTION
`
`Fig. 4 shows schematically an EUV mirror system 10 embodying this invention, including an EUV mirror 20
`[0006]
`with a front surface 22 and a back surface 24. The front surface 22 is where EUV illumination is intended to impinge.
`The mirror surface is normally curved and is assumed to possess, at least to a near approximation, axial symmetry.
`Throughholes (serving as cooling channels) 30 are provided through the mirror 20,
`lying in a plane approximately
`perpendicular to the axis of symmetry. The cooling channels 30 may serve to cause a cooling fluid (not shown) to flow
`therethrough. Since the coolant may be approximately of an atmospheric pressure or more while the mirror 20 typically
`operates in a vacuum environment, this pressure difference tends to cause some distortion of the mirror 20. One
`method of eliminating the effects of such distortion is to preliminarily polish the mirror 20 with the channels 30 over-
`pressurized by a specified amount such as one atmosphere, such thatthis distortion effect will be preliminarily polished
`out. However, to completely eliminate the distortion effect, this method must include the pressure drop suffered by the
`fluid along the channel length, which is caused bythe fluid's viscosity. Also shownis an auxiliary source of heat 90
`which heats the surface of the mirror opposite the reflective side. This heat source creates thermal stresses in the
`mirror opposite to those created bythe illumination irradiating the reflective side, thereby canceling their effects.
`[0007] Another approach is, as shown in Fig. 5A, to provide a pipe (or a conduit) 32 inside each cooling channel 30.
`The pipe 32 is made of a material with high thermal conductivity and a cooling fluid 34 flows therethrough. As shawn
`in Fig. 5A, the channel 30 is sufficiently oversized that the pipe 32 therein does not contact the inner wall of the channel
`30, leaving an annular gap 36 therebetween. The gap 36 between the inner wall of the channel 30 and the pipe 32 is
`filled with a gas of high thermal conductivity, such as helium gas, for conducting heat between the material of the mirror
`20 and the coolantinside the pipe 32. It now goes without saying that the cross-sectional shape of the channels need
`
`10
`
`15
`
`20
`
`25
`
`30
`
`35
`
`40
`
`45
`
`50
`
`55
`
`
`
`EP 1 376 185 A2
`
`not be circular and that one channel may contain two or more pipes inside, as shown in Fig. 5B.
`[0008]
`Fig. 6 showsthe relationship between the heattransfer coefficient of helium gas in a gap and its pressure for
`different gap widths. The heat transfer coefficient increases with pressure in a lower pressure range but the rate of
`variation decreases at higher pressures. Fig. 6 also showsthat the heat transfer coefficient remains relatively high
`even at lower pressures if the gap width is small. For a gap of the order of a few tens of microns or less, the helium
`gas may be maintained at a fraction of one atmosphere with little reduction in thermal conductivity, thereby reducing
`pressure distortion of the mirror 20. For example, a pressure of 10 kPais just one tenth of atmospheric pressure, yet
`relatively high thermal conductivities remain attainable at that pressure. For the purpose of the present invention, the
`width of the gap is set less than 100um and preferably less than 50um.
`[0009]
`If the mirror material above the channel 30 is approximated by a plate of thickness t,, the deformation from
`the pressureP in the channel maybe estimated from the theory of bending of elastic beams underload. If the width
`of the channel (the channel dimension approximately parallel to the mirror surface) is c, the maximum deformation d
`of the plate normal to the plane of the mirror is given by
`
`d= Pc"/326t,°,
`
`(1)
`
`whereE is Young's modulus for the mirror material. The deformation of the mirror is linearly proportional to the pressure
`inthe channel, so reducing the pressure by a factor of 10 also reduces the deformation by a factor of 10. Alternatively,
`Eq. 1 showsthat for a given amount of deformation, reducing P by a factor of 10 means the distance t, may be reduced
`by the factor 1013 = 2,15, so the channels may be located closer to the mirror surface.
`[0010]
`Fig. 7 showsthe heattransfer coefficient of a typical cooling fluid (Fluorinert FC-3283, manufactured by 3M
`Corp. of Minneapolis, MN) as a function of Reynolds numberfor the cases of laminar flow and full turbulent flow. The
`Reynolds number R is defined by R = pDv/n, where p is the coolant density, D is the coolant pipe inner diameter, v is
`the coolant flow velocity along the pipe axis, and 7 is the coolant viscosity. Creating full turbulent flow conditions in-
`creasesthe heat transfer by several orders of magnitude compared to the case of laminar flow. The expressions used
`to calculate these results are described in the article "Some fundamentals of cooled mirrors for synchrotron radiation
`beam lines" by M. Howells in Optical Engineering 35, 1187(1995), the contents of which are incorporated herein by
`reference. However, associated with turbulent flow are pressurefluctuations in the fluid which can create vibrations.
`Such behavior is absentin laminar flow, so laminar flow conditions have typically been used in the prior art when high
`mechanical stability of the mirror surface is required. Because the coolantpipe is mechanically isolated from the mirror
`by the gap, turbulent flow may be employed with the present invention, thereby permitting higher heat transfers to be
`achieved. Although the cooling fluid is typically a liquid, it might also be a gas.
`[0011]
`To illustrate the advantage of the present invention a calculation was done, comparing the thermal resistance
`between the mirror material and the coolant flowing through a channel under laminar flow conditions (prior art), and
`the thermal resistance associated with heat flow from the mirror material through a 50 tum He gas gap, a copper tube,
`and into the coolant flowing within the tube under full turbulent flow conditions. For a given temperature difference
`between two points, heat flow is inversely proportional to the intervening thermal resistance, so a lower thermalresist-
`ance permits higher heat transfer. The copper tube was assumed to have 4 mm inner diameter and 0.5 mm wall
`thickness. Based on the information presented in Figs. 6 and 7, the heat transfer coefficients for the He gas and the
`coolant flowing under turbulent conditions were assumedto be 1000 W/m2-K, and the heat transfer coefficient for the
`coolantflowing underlaminar conditions was assumed to be 58 W/m2-K. Underthese conditions the thermal resistance
`associated with the prior art case was found to be approximately 17 times larger than that associated with the present
`invention. Therefore heat transfers out of the mirror material can be greater than an order of magnitude higher with
`the present invention.
`[0012] A preferred position for providing the channels 30is difficult to determine because there are many factors to
`be taken into consideration. A model calculation was carried out for a mirror in the shapeof a circular disk of radius r
`being heated uniformly from one side (on the top surface). The channels 30 are assumedto be in a plane (the "cooling
`plane") at distance t, from the top surface which is uniformly heated and at distance tg from the opposite surface, the
`total thickness of the mirror being t = ty + tp. Thus, a uniform temperature gradient is assumed over a distance(in the
`direction of the thickness) of t; and the temperature is assumed to be constant over the adjacent distance of tp. The
`temperature gradient causes the entire disk to deform and the question is how the deformation changesast, is varied.
`[0013] The deformation was calculated by stress and strain formulas in Table 24 of Roark and Young ("Roark's
`Formulas for Stress and Strain," McGraw-Hill, 6th ed.), the contents of which are incorporated herein by reference,
`which were applied by using the assumption that the disk is separated at the cooling plane into a thermally stressed
`top plate and a bottom plate which is deformed by the application of moments along its periphery into a spherical cap.
`Thermal stress alone will deform the upper plate into a spherical cap. An application of additional moments along its
`
`10
`
`15
`
`20
`
`25
`
`30
`
`35
`
`40
`
`45
`
`50
`
`55
`
`
`
`EP 1 376 185 A2
`
`periphery will change its radius of curvature to match that of the lower plate such that they join together. A final defor-
`mation is calculated on the further requirement that the stress of the bottom surface of the top plate be equal to that
`of the top surface of the bottom plate. The final displacement y of the plate center thus calculated is in the form of y =
`(r2yAT/2\/(ty4t5) where ¥ is the coefficient of thermal expansion and ATindicates the temperature difference through
`the thicknessof the top plate. This equation suggests that it does not matter where the cooling plane is. However, for
`a plate heated on one side by a constant heat flux F and cooled by a temperature reservoir on the other side, the
`temperature difference AT betweenthe two sides scales with the quantity AT=Ft,/K whereK is the thermal conductivity
`of the material according to Carslaw and Jaeger in Section III.8 of "Conduction of Heat in Solids," Oxford, the contents
`of which are incorporated herein by reference. It is assumed here and belowthat the heatflux F represents that part
`of the incident flux which is absorbed by the surface. Therefore, the deformation y is in fact proportional to ty, and the
`conclusion hereby obtained is that the cooling plane should be as close to the heated surface as possible.
`[0014] There are factors that limit how small t; can be made.
`If the cooling network involves channels machined
`within the mirror, they must be far enough from the mirror surface such that they will not influence the mirror figure. As
`explained above, the helium gas in the gap 36 is maintained at a low pressure to reducedistortion of the mirror surface,
`while the gap is small enough to ensure a high heat transfer coefficient. However,if the channels are very close to the
`mirror surface, the material directly above the channels may experiencea slightly larger temperature gradient than
`material lying in a plane midway between adjacent channels. This could contribute to local temperature distortion of
`the mirror. In the above cited paper, Howells teachesthat t, should be at least several times the channel width to avoid
`local distortion effects. He also teaches that forces from polishing and coolant pressure dictate a practical range for t,
`of approximately 0.5 mm to 5 mm. Since coolant pressureis significantly reduced in this invention, smaller values of
`t, may be allowed.
`[0015] The coolant 34 flowing within the cooling pipe 36 may be in a turbulent state for higher heat transfer, but the
`consequent vibrations should not perturb the mirror surface. Successful application of this invention requires that the
`cooling pipes be mechanically isolated from the mirror while remaining surrounded by a controlled atmosphere of He
`gas. Some embodiments are described which satisfy these requirements. Figs. 8A and 8B show schematic views of
`a mirror 800 with a series of cooling pipes 810 running through parallel channels 815 in the mirror. Each pipe is centered
`in its channel, and the channels are sealed at the mirror periphery by compliant seals 820 made of rubber or some
`other visco-elastic material. The compliant seals will help to isolate and damp any vibrations the pipe experiences from
`turbulent fluid motion. He gas or some other high thermal conductivity gas is admitted to each channel through an inlet
`825 which is connected to a gas manifold 830. The gas pressurein the manifold 830 and the mirror channels 815 is
`controlled by means of a He gas supply 835, a vacuum pump 840, a valve 845 to switch between them, a pressure
`gauge 850, and a gas pressure controller (not shown). The coolant pipes run to a coolant manifold (not shown) which
`directs coolant to them from a reservoir which may be part of a closed loop system involving a heat exchanger and
`temperature controller (not shown). Such coolant systems are well knownin the art.
`[0016]
`Fig. 8C shows acoolantpipe 810 within a channel 815. The channel has visco-elastic gas tight seals 820 at
`the mirror periphery. In addition, the pipe is centered within the channel by means of a helical coil 822 of visco-elastic
`material. This coil will also help to damp any vibrations the pipe experiences from turbulentfluid motion in the coolant.
`Other designs, employing spacers madeof visco-elastic material may also be used.
`[0017]
`Fig. 8D shows a cross section of several channels 815a and coolant pipes 810a with a rectangular rather
`than circular cross section. The paper by Howells teachesthat a tall, narrow rectangular geometry provides superior
`heattransfer capabilities over a circular cross section, when overall heat transfer is limited by convection in the coolant.
`When overall heat transfer is limited by conduction in the mirror material, the shape of the channels is less important.
`[0018]
`Figs. 9A and 9B show an embodiment where coolant pipes 910 are further mechanically isolated from the
`mirror 800. The pipes make no mechanical contact with the mirror. They are positioned relative to the channels 915
`by a rigid framework (not shown) which is referenced to the mirror or its mounts but isolated from it by visco-elastic
`damping units. The coolant pipes are enclosed in a He gas manifold 930. A bellows 925 or other flexible connection
`servesto isolate the pipes from any stresses associated with the visco-elastic gas seals 920 at the ports of the manifold
`930. The pipes connect to coolant manifolds 960 and the rest of the coolant system (not shown). The gas manifolds
`are sealed to the mirror through compliant visco-elastic seals 932. The gas pressure in the manifold 930 and the mirror
`channels 915 is controlled by means of a He gas supply 935, a vacuum pump 940, a valve 945 to switch between
`them, and a pressure gauge 950. The only mechanical connection to the mirror in this case is at the mirror periphery.
`[0019] As mentioned previously, the He gas pressure is maintained at a small fraction of an atmosphere, so pressure
`distortion of the mirror surface is small. Also, vibrations of the coolant pipe caused by turbulent flow are isolated from
`the mirror by visco-elastic seals and spacers. Nevertheless, some vibrations could be transmitted to the mirror through
`the gas as sound waves. This contribution is expected to be very small, as a simple argument shows. Sound waves
`generated in the coolant propagate through the coolant tube and then through the gas. Since the gap between the
`coolant pipe and the mirror is small, we treat the sound propagation as being one-dimensional. At the outer surfaceof
`the coolant pipe, part of the sound wavesare transmitted into the gas and the rest is reflected back into the pipe. For
`
`10
`
`15
`
`20
`
`25
`
`30
`
`35
`
`40
`
`45
`
`50
`
`55
`
`
`
`EP 1 376 185 A2
`
`simplicity we assume thatall of the transmitted energy is subsequently absorbed by the mirror. The fraction of vibrational
`energy transmitted into the gas dependson the relative density of the two media as well as their speeds of sound and
`is given approximately by
`
`transmitted fraction = 4pgasCgas!/Ppipepipe’
`
`(2)
`
`where p is the density of the medium and c is the speed of sound. This expression is derived in Section 33.6 of B.
`Yavor and A. Detlaf, Handbook of Physics, Mir Publishers, 1975, the contents of which are incorporated herein by
`reference, for the case where pgasCgas << PpipeCpipe- For He gas, pgas~ 0.0166 kg/m? and Cgas ~ 1000 m/sec, at 20 °C
`and a pressure of 10 kPa.If the coolantpipe is made of copper, the corresponding quantities are p,ipg ~ 8930 kg/m
`And Cping ~ 3750 m/sec. As a result the fraction of vibrational energy transmitted into the gas, and assumecto ultimately
`be absorbed by the mirror, is only approximately 2x10-6. Therefore the gas layer is very effective in decoupling vibrations
`of the coolant pipe from the mirror.
`[0020] Although the embodiments described above show straight coolant pipes lying within straight channels in the
`mirror, other geometries are possible as well. If there is an advantage for example in having curved pipes within similarly
`curved channels, the mirror could be fabricated in two parts, split at a plane wherethe pipeswill lie. Channels in the
`two mating surfaces could be suitably machined, the pipes inserted, and the two halves bondedtogether. For some
`geometries, separation of the mirror into more than two pieces may be required.
`[0021]
`In some cases a thermally conductive fluid may be substituted for the gas in the gap between the coolant
`pipe and the mirror channel. The fluid is chosen to maintain its liquid and thermal properties at the operating temperature
`and ambient pressure of the mirror. For example the mirror might operate at atmospheric pressure, so the fluid would
`be maintained at atmospheric pressure. The coolant within the pipe could then have pressures different from an at-
`mosphere without perturbing the mirror surface. The pressure required to provide a given flow of fluid through a pipe
`of a given diameter, and therefore a specified heat transfer, is a strong function of both the flow rate and the pipe
`diameter, so the pressure within the pipe will usually differ from the ambient pressure. In addition, fluid flowing in a
`pipe suffers a significant pressure drop along the length of the pipe because ofthe fluid's viscosity. The effects of this
`pressure gradient on mirror distortion would thus be avoided. Vibrations associated with coolant turbulence within the
`pipe would not be asisolated from the mirror as in the case of a gasfilling the gap, but some lesser vibration isolation
`remains. Assuming the fluid in the gap to be water of density 1000 kg/m® and speed of sound approximately 1500 m/
`sec, and acopper pipe, Eq. 2 estimatesthe fraction of vibrational energy transmitted to the mirror to be approximately
`0.18. Forexample, the thermal conductivity of water exceeds that of He gas, so enhanced cooling is possible. However,
`the fluid heat capacity will be much greater than that of a the gas, and this may complicate temperature control of the
`mirror unless the fluid is circulated. By keeping the gap small, the heat capacity of the fluid can be minimized.
`[0022]
`Providing a plane of cooling channels near the heated surface of the mirror reduces the global thermal de-
`formation of the mirror as shown above. Any residual undesired global thermal deformation may be eliminated by
`applying a distribution of heat sources to the bottom of the mirror, so that thermal stresses in the mirror below and
`abovethe cooling plane cancel out. A fairly general statement can be made about these heat sources, using an argu-
`ment similar to the one above concerning the optinum placementof the cooling plane. Again, treating the mirror as a
`flat plate, divide the plate at the cooling plane into an upper plate and a lower plate. Assume the temperature distribution
`at the top surface is given by T,(x, y), and the temperature distribution in the cooling plane is given by T,(x, y), as
`shown in Fig. 10. In a steady state situation the temperature distribution in an intermediate plane at height z can be
`written as
`
`T(x, y) = T.0% y) + (71% y) - To y))z/ty =T(% y) + ATY(% y)ZAy.
`
`(3)
`
`[0023] Theterm T,(x, y) will cause thermal distortion in the x-y plane but not in z. Only the thermal gradient term AT,
`(x, y)z/t, will cause out-of-plane deformation of the plate. According to a theorem by J. Goodier in ASME J. Applied
`Mechanics 24, 467(1957), the contents of which are incorporated herein by reference, the out-of-plane deformation
`can be canceled by applying a distributed load q,(x, y) in the z direction over the surface of the plate:
`
`a,(x,Go|at Spe(x.y).
`
`Bt; (Oo
`
`(4)
`
`10
`
`15
`
`20
`
`25
`
`30
`
`35
`
`40
`
`45
`
`50
`
`55
`
`
`
`EP 1 376 185 A2
`
`where E is Young's modulus and v is Poisson's ratio for the plate material.
`[0024]
`Similarly, if the temperature distribution on the bottom surfaceis given by To(x, y), we can describe the tem-
`perature at an intermediate plane by
`
`T(x, y) = Tg (x, ¥) + (Tg, y) - Talx, y))Z/Aty = TE (X, y) + ATalX,y)Z/to.
`
`(5)
`
`[0025] Again the lower plate can be flattened by the application of a distributed load qa(x, y), where
`
`Et,
`(@
`@
`aloy)= sq") ox?By? WAT,(x,y).
`
`(6)
`
`By adjusting the temperature distribution T(x, y) so that q4(x, y) + qo(x, y) = 0, we can cancel out the thermal
`[0026]
`stresses in the upper and lower parts of the plate, so that the entire plate (mirror) remainsflat. This condition can be
`shown to be equivalent to
`
`2
`AT2(x, y) = 3 AT, (XY).
`ty
`
`(7)
`
`So the temperaturedifference ATo(x, y) required between the cooling plane and the bottom plate is less than
`[0027]
`that in the upper part of the plate bythe ratio (t4/t)2, and since we saw abovethat the best cooling geometry minimizes
`t, comparedto to, this ratio will typically be quite small. Furthermore, if the variation in the temperature differences with
`position in x and y is relatively small, we can assume the heat absorbedat the surfaces which creates the temperature
`differences scales approximately like AT, = F,t,/K and AT» = Foto/K, as described in the Carslaw and Jaeger reference
`above. Then the heat absorbed at the bottom surface of the plate which is required to flatten the plate will scale with
`the heat absorbedatthe top of the platelike
`
`F(x, y)= (ty/ta)°F4(x, y).
`
`(8)
`
`is less than ty.
`Thus, relatively little additional heat should be neededto flatten the plate if t,
`[0028]
`The result in Eq. 7 is fairly general, since it does not require the cooling plane to be isothermal. However,if
`[0029]
`cooling is accomplished by circulating coolant through channels, the approximation of a single plane, in which cooling
`takes place, may not be justified. A more realistic situation is shownin Fig. 11. Unless a very high cooling rate is needed,
`the temperature in the coolant channels is notlikely to be significantly different at the top and bottom of the channels.
`Therefore, the temperaturedistributions at the cooling planes 1 and 2 should be almostidentical. Then, the arguments
`made above should apply to this case as well. The distances t, and tp are more accurately defined as in Fig. 11 now.
`[0030]
`Eq. 7 is an approximation, because it neglects any variation in t, associated with the mirror surface curvature.
`Therefore, a correction must be determined either empirically or by modeling. Similarly, some correction to Eq. 8 must
`be determined either empirically or by modeling to compensatefor variations in both t, and the variation in temperature
`differences with position on the mirror.
`If the mirror curvature is gentle and the temperature differences don't change
`very much, however, Eqs. 7 and 8 should give reasonable approximations to the final relationships.
`[0031]
`Fig. 12 shows an embodimentof a control system which provides appropriate heating to the back of the mirror
`1200, to eliminate global thermal distortion. The radiation 1210 incident on the mirror surface is monitored by a detector
`1220 or detectors, and the absorbedradiation flux F4(x, y) determined from the Known absorption properties of the
`mirror. Alternatively, a separate monitor (not shown) could measure the surface temperature distribution of the mirror.
`Acontroller 1230 uses the absorbedsurface flux, or surface temperature, along with information describing the coolant
`channel 1240 conditions to determine from models the required absorbed heatflux Fo(x, y) on the back of the mirror.
`The controller then controls a heat source ("heater") 1250 to provide the necessary heat flux. The models in the con-
`troller will be based on the relations in Eqs. 7 and 8, along with corrections to them.
`[0032] The heat source could provide radiant heating of the mirror back from close proximity. Or the heat source
`could be in contact with the mirror back and heatit directly. Or the heat source could be a remote source of radiation
`which is modulated appropriately and projected onto the mirror back by means of an optical system. Fig. 13 shows an
`
`10
`
`15
`
`20
`
`25
`
`30
`
`35
`
`40
`
`45
`
`50
`
`55
`
`
`
`EP 1 376 185 A2
`
`embodiment of a radiant heating system. It consists of a number of bodieslying in a flat plane, temperatures of which
`may be adjusted independently. For example, each body may be heated by an array of resistive heaters of which
`electrical current is controlled. Or they may be heated by a flow of fluid heated remotely by heaters (not shown
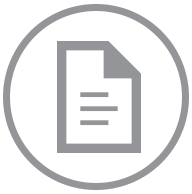
Accessing this document will incur an additional charge of $.
After purchase, you can access this document again without charge.
Accept $ ChargeStill Working On It
This document is taking longer than usual to download. This can happen if we need to contact the court directly to obtain the document and their servers are running slowly.
Give it another minute or two to complete, and then try the refresh button.
A few More Minutes ... Still Working
It can take up to 5 minutes for us to download a document if the court servers are running slowly.
Thank you for your continued patience.
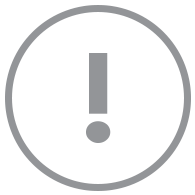
This document could not be displayed.
We could not find this document within its docket. Please go back to the docket page and check the link. If that does not work, go back to the docket and refresh it to pull the newest information.
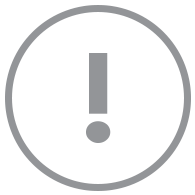
Your account does not support viewing this document.
You need a Paid Account to view this document. Click here to change your account type.
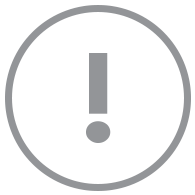
Your account does not support viewing this document.
Set your membership
status to view this document.
With a Docket Alarm membership, you'll
get a whole lot more, including:
- Up-to-date information for this case.
- Email alerts whenever there is an update.
- Full text search for other cases.
- Get email alerts whenever a new case matches your search.
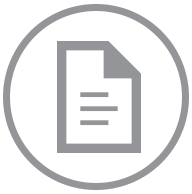
One Moment Please
The filing “” is large (MB) and is being downloaded.
Please refresh this page in a few minutes to see if the filing has been downloaded. The filing will also be emailed to you when the download completes.
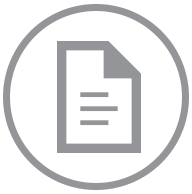
Your document is on its way!
If you do not receive the document in five minutes, contact support at support@docketalarm.com.
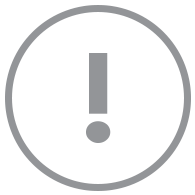
Sealed Document
We are unable to display this document, it may be under a court ordered seal.
If you have proper credentials to access the file, you may proceed directly to the court's system using your government issued username and password.
Access Government Site