`
`16b
`
`21
`
`19
`
`26
`
`16a
`
`18
`
`20
`
`
`
`
`
`4/5
`
`FIG. 7
`
`
`
`3/5
`
`
`
`FIG. 5
`
`
`
`/ 19
`
`2/5
`
`21
`
`FIG. 2
`
`16
`
`
`
`
`
`
`
`
`
`2020P00230EP
`
`14
`
`ABSTRACT
`
`There is provided a conditioning system for a lithographic apparatus, said conditioning system being
`
`configured to condition one or more optical elements of the lithographic apparatus, wherein the
`
`conditioning system is configured to have a sub-atmosphcric pressure at the one or morc optical
`
`elements. Also provided are a lithographic apparatus comprising such a conditioning system, the use
`
`of such a conditioning system, a method of conditioning a system, as well as a lithographic method
`
`comprising a sub-atmospheric pressure cooling system
`
`
`
`2020P00230EP
`
`13
`
`11.
`
`12.
`
`The conditioning system according to any preceding claim, wherein said conditioning system
`
`further includes one or more vibration dampers, optionally wherein the one or more vibration
`
`dampersare in the form of one or more hydraulic accumulators.
`
`The conditioning system according to any of claims 9 to 11 when not dependent on claim6,
`
`wherein a or the conditioning fluid reservoir is disposed below the optical element such that the
`
`hydrostatic pressure difference between the optical element and the conditioning fluid reservoir
`
`reduces the pressure at the optical element to below atmospheric pressure.
`
`10
`
`13.
`
`The conditioning system according to any preceding claim, wherein the system comprisesfirst
`
`and second conditioning fluid reservoirs, whercin the first and second conditioning fluid
`
`reservoirs are in fluid connection with one another via a valve which is operable to control the
`
`level of conditioning fluid in the conditioning fluid reservoir whichis in fluid communication
`
`with the optical element.
`
`15
`
`20
`
`14.
`
`15.
`
`16.
`
`A lithographic apparatus comprising the conditioning system according to any of claims 1 to 13.
`
`The use of a sub-atmosphcric pressure conditioning system in a lithographic apparatus, prefcrably
`
`wherein the conditioning systemis a conditioning system according to any of claims 1 to 13.
`
`A method of conditioning a system or sub-system of a lithographic apparatus, said method
`
`including providing a liquid conditioning fluid at sub-atmospheric pressure to the system or sub-
`
`system to be conditioned.
`
`25
`
`17.
`
`The method according to claim 16, wherein the system or sub-system comprises an optical
`
`element, optionally wherein the optical element is a reflector or mirror.
`
`18. A lithographic method comprising projecting a patterned beam of radiation onto a substrate,
`
`wherein the patterned beam is directed or patterned using at least one optical element comprising a
`
`30
`
`conditioning system according to any of claims 1 to 13 or conditioned according to a method of
`claims 16 or 17.
`
`
`
`2020P00230EP
`
`12
`
`CLAIMS
`
`A conditioning system for a lithographic apparatus, said conditioning system being configured to
`
`condition one or more optical clements ofthe lithographic apparatus, wherein the conditioning
`
`systemis configured to have a sub-atmospheric pressure at the one or more optical elements.
`
`The conditioning system according to claim 1, wherein at least one of the optical elements is a
`reflector or a mirror.
`
`The conditioning system according to claim 1 or claim 2, wherein the conditioning system is
`
`configured to operate at between around 0.02 and 0.9 bara, preferably around 0.3 bara.
`
`The conditioning system according to any of claims | to 3, wherein the conditioning system
`
`includes a liquid conditioning fluid, preferably wherein the liquid conditioning fluid is water.
`
`The conditioning system according to any of claims 1 to 4, wherein the system includes a
`
`conditioning fluid reservoir.
`
`The conditioning system according to any of claims 1 to 5, wherein the system includes a pump
`
`downstream of the optical element and a flowrestrictor upstream of the optical element.
`
`The conditioning system according to any of claims | to 6, wherein the system includes a sub-
`
`atmospheric pressure conditioning fluid reservoir.
`
`The conditioning system according to claim 7, whercin the sub-atmospheric pressure conditioning
`
`fluid reservoir is connected to a vacuum pumpand/ora gasinlet.
`
`The conditioning system according to any of claims 1 to 5 and 7 to 8 when not dependent on
`
`claim 6, wherein the system includes a pump upstream of the optical element, and optionally a
`
`flow restrictor between the pump and the optical element.
`
`10.
`
`The conditioning system according to any of claims 7 to 9, wherein the sub-atmospheric pressure
`
`conditioning fluid reservoir includes a deformable separator, preferably wherein the deformable
`
`separator is disposed betweenthe liquid conditioning fluid and a gas.
`
`10
`
`15
`
`20
`
`25
`
`30
`
`35
`
`
`
`2020P00230EP
`
`11
`
`optical element 19. The hydrostatic pressure difference 25 causes a reduced pressure on the return side
`
`of the optical element 19. The pump 21 compensates for this and is able to provide conditioning fluid
`
`to the supply side of the optical element 19. The dotted box surrounding the conditioning fluid reservoir
`
`16, the pump 21, and the flow restrictor 18 indicates that these clements are located below the optical
`
`elementand that the exact positioning of such elements relative to the optical element 19 is schematic
`
`only.
`
`It will be appreciated that the flowrestrictor 18 may be provided adjacent the return side of the
`
`optical element 19.
`
`[00055]
`
`Figure 8 depicts yet another embodimentof a conditioning system according to the present
`
`invention.
`
`In this embodiment,
`
`there are two conditioning fluid reservoirs l6a, 16b. The two
`
`conditioning fluid reservoirs 16a, 16b are connected via a valve 26 which is operable to control the
`
`water Icvel within conditioning fluid reservoir 16a. This in turn controls the hydrostatic pressure of the
`
`conditioning fluid which is provided to the optical element 19 in combination with the water pump 21
`
`which is connected to the return side of the optical element.
`
`[00056]
`
`In summary, the present invention provides for a sub-atmospheric conditioning system
`
`which enables the conditioning of critical components of a lithographic apparatus and enables such
`
`components directly and therefore increases thermal efficiency and enables improved performance at
`
`higher thermal loads without causing unwanted deformation of the optical elements. The present
`
`invention has particular, but not exclusive application, to the cooling of optical clement of lithographic
`
`apparatuses.
`
`[00057] While specific embodiments of the invention have been described above,
`
`it will be
`
`appreciated that the invention may bepracticed otherwise than as described.
`
`[00058]
`
`The descriptions above are intended to beillustrative, not limiting. Thusit will be apparent
`
`to one skilled in the art that modifications may be made to the invention as described without departing
`
`from the scope of the claims set out below.
`
`10
`
`15
`
`20
`
`
`
`2020P00230EP
`
`10
`
`system 15. The flowrestrictor 18 can be of any suitable design and the present invention is not
`
`particularly limited by the exact nature of the flow restrictor. The flow restrictor 18 functions to provide
`
`the required pressure drop at the optical element 19 such that the conditioning fluid at or within the
`
`optical clement 19 is below atmospheric pressure.
`
`In any of the depicted cmbodiments, the optical
`
`element 19 which is being conditioned contains at least one channel through which conditioning fluid
`
`may pass in order to absorb heat from or provide heat to the optical element 19 and transport it away
`
`thereby conditioning the optical element 19. Thelevel of the conditioning fluid 17 in the conditioning
`
`fluid reservoir 16 is schematic only and may be above or below the point at which conditioning fluid
`
`17 is returned via pump 21.
`
`[00050]
`
`Figure 3 depicts a similar conditioning system as Figure 2 albeit with the difference that
`
`the conditioning fluid reservoir 16 is not at atmospheric pressure.
`
`Instead, the system is scaled such
`
`that ii is taken downto the desired sub-atmospheric pressure and then closed off so that it remains al
`
`sub-atmospheric pressure. A gas connection 22 may be provided which is able to reduce the pressure
`
`within the system should it increase above desired levels. Similarly, additional gas or conditioning fluid
`
`may be addedto the system if the pressure falls too much or more conditioning fluid is required.
`
`[00051]
`
`Figure 4 depicts a similar conditioning system to Figure 3 albeit with a deformable
`
`separator 23, which may be in the form of a membrane, which separates the conditioning fluid 17 from
`
`the gas aboveit within the conditioning fluid reservoir 16. The scparator 23 prevents cvaporation of
`
`any of the conditioning fluid and therefore avoids the loss of conditioning fluid and also avoids the need
`
`to have a vacuum pumpor controlled gas inlet. The separator 23 also dampens flow induced vibration
`
`within the system.
`
`[00052]
`
`Figure 5 depicts a further embodimentof a conditioning system 15 in accordance with the
`
`present invention. This embodiment is similar to that of Figure 2 albeit having a closed system and
`
`having a sub-atmospheric pressure conditioning fluid reservoir 16. The conditioning fluid reservoir 16
`
`is maintained at below atmosphcric pressure by vacuum pump 24. Vacuum pump 24is configured to
`
`reduce the pressure within the system by removing gas present therein. A controlled gas inlet may be
`
`provided which can add or remove gas from the system as required.
`
`[00053]
`
`Figure 6 depicts an embodiment which is similar to that of Figure 5 albeit the pump 21
`
`which is used to move the conditioning fluid through the system is disposed between the conditioning
`
`fluid reservoir 16 and the inlet of the optical element 19.
`
`In this embodiment, conditioning fluid 17 is
`
`pumped by pump 21 via restrictor 18 into the optical element 19. The outlet of the optical element 19
`
`is fluidly connected to the sub-atmospheric pressure conditioning fluid reservoir 16. Vacuum pump 24
`
`and gas connector 22 are operable to remove and introduce gas as appropriate in order to control the
`
`pressure within the system.
`
`[00054]
`
`Figure 7 depicts yet another embodimentof a conditioning system according to the present
`
`invention.
`
`In this embodiment, the low pressure is generated by utilizing the hydrostatic pressure
`
`difference 25 caused by the conditioning fluid reservoir 16 being located at a lower height than the
`
`10
`
`15
`
`20
`
`25
`
`30
`
`35
`
`
`
`2020P00230EP
`
`9
`
`and is incident upon the patterning device MA held bythe support structure MT. Thepatterning device
`
`MAreflects and patterns the radiation beam B. The illumination system IL may include other mirrors
`
`or devices in addition to or instead of the faceted field mirror device 10 and faceted pupil mirror device
`11.
`
`[00045]
`
`Following reflection from the patterning device MAthe patterned radiation beam B enters
`
`the projection system PS. The projection system comprises a plurality of mirrors 13, 14 which are
`
`configured to project the radiation beam B onto a substrate W held by the substrate table WT. The
`
`projection system PS may apply a reduction factor to the radiation beam, forming an image with features
`
`that are smaller than corresponding features on the patterning device MA. A reduction factor of 4 may
`
`for example be applied. Although the projection system PS has two mirrors 13, 14 in Figure 1, the
`
`projection system mayinclude any numberof mirrors (c.g. six mirrors).
`
`[00046]
`
`In use the optical elements of the lithographic apparatus, such as mirrors or reflectors, are
`
`heated by the radiation and it is therefore necessary to condition such optical elements. As such, a
`
`conditioning system according to the present invention is integrated into the lithographic apparatus to
`
`provide the required conditioning. Conditioning usually requires the removal of thermal energy from
`
`10
`
`15
`
`the optical elements as they heat up during use.
`
`[00047]
`
`The radiation sources SO shown in Figure 1 may include components which are not
`
`illustrated. For cxample, a spectral filter may be provided in the radiation source. The spectral filter
`
`may be substantially transmissive for EUV radiation but substantially blocking for other wavelengths
`of radiation such as infrared radiation.
`
`20
`
`[00048]
`invention.
`
`Figures 2 to 8 are schematic depictions of conditioning systems according to the present
`
`25
`
`30
`
`35
`
`[00049]
`
`Figure 2 depicts an embodiment of a condilioning system 15 in accordance with a [first
`
`embodiment of the present invention. The conditioning system 15 includes a conditioning fluid
`
`reservoir 16. In the depicted example, the top of the conditioning fluid reservoir 16 is shown as being
`
`open. Whilst in practice, the conditioning fluid reservoir may or may not be open,it is depicted as being
`
`open to demonstrate that the conditioning fluid 17 therein, which may be water, is not pressurized above
`
`atmospheric pressure and may be at ambient pressure. The conditioning fluid reservoir 17 is connected
`
`to an optical element 19 via optional flow restrictor 18. An optional pressure sensor 20 may be provided
`
`to measure the pressure of the conditioning fluid as it enters the optical element 19 or inside the optical
`
`element 19. A pump 21 is connected between the optical element 19 and the conditioning fluid reservoir
`
`16. In use, conditioning fluid 17 from the conditioning fluid reservoir 16 (which mayalso be reterred
`
`to as a conditioning fluid vessel or container) passes into an optical element 19 via the pressure
`
`difference between reservoir outlet and the pumpinlet, created by the pump.
`
`In other embodiments,
`
`the flow relies on gravity based on the relative position of the tank and optical element. A pump 21
`
`connected to an output side of the optical element 19 pumps the conditioning fluid 17 back to the
`
`conditioning fluid reservoir 16 whereit is able to subsequently be recirculated through the conditioning
`
`
`
`2020P00230EP
`
`8
`
`previously formed patterns. Where this is the case, the lithographic apparatus aligns the patterned
`
`radiation beam B with a pattern previously formed on the substrate W.
`
`[00039]
`
`The radiation source SO, illumination system IL, and projection system PS mayall be
`
`constructed and arranged such that they can be isolated from the external environment. A gas at a
`
`pressure below atmospheric pressure (e.g. hydrogen) may be provided in the radiation source SO. A
`
`vacuum may be provided in illumination system IL and/or the projection system PS. A small amount
`
`of gas (e.g. hydrogen) at a pressure well below atmospheric pressure may be provided in the
`
`illumination system IL and/or the projection system PS.
`
`[00040]
`
`The radiation source SO shownin Figure | is of a type which maybe referred to as a laser
`
`produced plasma (LPP) source. A laser, which may for example be a COzlaser, is arranged to deposit
`
`encrgy via a lascr beaminto a fucl, such as tin (Sn) which is provided from a fucl emitter. Althoughtin
`
`is referred to in the following description, any suitable fuel may be used. The fuel may for example be
`
`in liquid form, and may for example be a metal or alloy. The fuel emitter may comprise a nozzle
`
`configured to direct tin, e.g. in the form of droplets, along a trajectory towards a plasma formation
`
`region. The laser beam is incident upon the tin at the plasma formation region. The deposition of laser
`
`energy into the tin creates a plasmaat the plasma formation region. Radiation, including EUV radiation,
`
`is emitted from the plasma during de-excitation and recombination of ions of the plasma.
`
`[00041]
`
`The EUV radiation is collected and focused by a near normal incidence radiation collector
`
`(sometimes referred to more generally as a normal incidence radiation collector). The collector may
`
`have a multilayer structure which is arranged to reflect EUV radiation (e.g. EUV radiation having a
`
`desired wavelength such as 13.5 nm). The collector may have anelliptical configuration, having two
`
`ellipse focal points. A first focal point may be at the plasma formation region, and a secondfocal point
`
`may be ai an intermediate focus, as discussed below.
`
`[00042]
`
`The laser may be separated from the radiation source SO. Where this is the case, the laser
`
`beam may be passed from the laser to the radiation source SO with the aid of a beam delivery system
`
`(not shown} comprising, for example, suitable directing mirrors and/or a beam expander, and/or other
`
`optics. The laser and the radiation source SO maytogether be considered to be a radiation system.
`
`[00043]
`
`Radiation that is reflected by the collector forms a radiation beam B. The radiation beam
`
`B is focused at a point to form an imageof the plasma formation region, which acts as a virtual radiation
`
`source for the illumination system IL. The point at which the radiation beam B is focused may be
`
`referred to as the intermediate focus. The radiation source SO is arranged such that the intermediate
`
`tocusis located at or near to an opening in an enclosing structure ofthe radiation source.
`
`[00044]
`
`The radiation beam B passes fromthe radiation source SO into the illumination systemIL,
`
`which is configured to condition the radiation beam. The illumination system IL may include a facetted
`
`field mirror device 10 and a facetted pupil mirror device 11. The faceted field mirror device 10 and
`
`faceted pupil mirror device 11 together provide the radiation beam B with a desired cross-sectional
`
`shape and a desired angular distribution. The radiation beam B passes from the illumination system IL
`
`10
`
`15
`
`20
`
`25
`
`30
`
`35
`
`
`
`2020P00230EP
`
`7
`
`such as pipes and manifolds may be provided, to allow the conditioning fluid to be provided to the
`
`optical elements.
`
`[00026]
`
`According to a fifth aspect of the present invention, there is provided a lithographic method
`
`comprising projecting a patterned beam ofradiation onto a substrate, wherein the patterned beam is
`
`directed or patterned using at least one optical element comprising a conditioning system according to
`
`any aspect of the present invention.
`
`[00027]
`
`It will be appreciated that features described in respect of one aspect or embodiment may
`
`be combined with any features described in respect of another aspect or embodiment and all such
`
`combinations are expressly considered and disclosed herein.
`
`
`BRIEF DESCRIPTION OF THE DRAWINGS
`
`[00028]
`
`Embodiments of the invention will now be described, by way of example only, with
`
`reference to the accompanying schematic drawings in which corresponding reference symbols indicate
`
`corresponding parts, and in which:
`
`[00029]
`
`Figure | depicts a lithographic apparatus according to an embodimentof the invention;
`
`[00030]
`
`Figure 2 depicts a first embodiment of a system according to the present invention;
`
`[00031]
`
`Figure 3 depicts a second embodimentof a system according to the present invention;
`
`[00032]
`
`Figure 4 depicts a third cmbodiment of a system according to the present invention;
`
`[00033]
`
`Figure 5 depicts a fourth embodiment of a system according to the present invention;
`
`[00034]
`
`Figure 6 depicts a fifth embodimentof a system according to the present invention;
`
`[00035]
`
`Figure 7 depicts a sixth embodiment of a system according to the present invention; and
`
`[00036]
`
`Figure 8 depicts a seventh embodiment of a system according to the present invention.
`
`[00037]
`
`The features and advantages of the present invention will become more apparent fromthe
`
`detailed description set forth below when taken in conjunction with the drawings, in which like
`
`reference characters identify corresponding clements throughout.
`
`In the drawings, like reference
`
`numbers generally indicate identical, functionally similar, and/or structurally similar elements.
`
`DETAILED DESCRIPTION
`
`[00038]
`
`Figure 1 showsa lithographic according to an embodimentof the present invention. The
`
`lithographic system comprises a radiation source SO and a lithographic apparatus LA. The radiation
`
`source SO is configured to generate an extreme ultraviolet (EUV) radiation beam B. The lithographic
`
`apparatus LA comprises an illumination system IL, a support structure MT configured to support a
`
`patterning device MA(e.g. a mask), a projection system PS and a substrate table WT configured to
`
`support a substrate W. The illumination system IL is configured to condition the radiation beam B
`
`before it is incident upon the patterning device MA. The projection system is configured to project the
`
`radiation beam B (now patterned by the mask MA)onto the substrate W. The substrate W mayinclude
`
`10
`
`15
`
`20
`
`25
`
`30
`
`35
`
`
`
`2020P00230EP
`
`6
`
`[00020]
`
`The conditioning system may include one or more vibration dampers, which mayserve to
`
`dampen pressure control error or flow induced vibrations. The one or more vibration dampers may be
`
`in the form of one or more hydraulic accumulators. As the optical elements are also very sensitive to
`
`vibrations, it is desirable to reduce or climinate vibrations where possible. By providing one or more
`
`vibration dampers, which maybe in the form of one or more hydraulic accumulators, any vibrations
`can be reduced.
`
`[00021]
`
`In embodiments, a or the conditioning fluid reservoir may be disposed below the optical
`
`element such that the hydrostatic pressure difference between the optical element and the conditioning
`
`fluid reservoir reduces the pressure present at the optical element to below atmospheric pressure. As
`
`such, if the conditioning fluid reservoir is provided below the height of the return side of the optical
`
`clement, the hydrostatic pressure difference is sufficient to reduce the pressure of the conditioning fluid
`
`al the optical element to below atmospheric pressure. A pump may be provided to supply conditioning
`
`fluid to the optical element and the pressure being over atmospheric pressure is avoided by the
`
`hydrostatic pressure difference. There may be a pressure control device between the optical element
`
`and the conditioning fluid reservoir. The pressure control device may be configured to control the flow
`
`of conditioning fluid therethrough in order to control the pressure at the optical element. Optionally,
`
`there may be provided a pressure sensor configured to control the pressure control device. A pressure
`
`controller may be provided which receives an input from a pressure sensor and is operable to control
`
`the pump and/or a gasinlet flow controller.
`
`[00022]
`
`In embodiments, the system may comprise first and second conditioning fluid reservoirs.
`
`The first and second conditioning fluid reservoirs may be in fluid communication with one another via
`
`a valve. The valve may be operable to control the level of conditioning fluid in the coolant reservoir
`
`whichis in fluid communication with the optical element to control the pressure.
`
`In an embodiment,
`
`the level of conditioning fluid in the conditioning fluid reservoir, and therefore the static pressure on
`
`the optical clement, may be controlled by the provision of a conditioning fluid overflow in which the
`
`height of the conditioning fluid overflow is related to the height of the optical element.
`
`[00023]
`
`According to a second aspect of the present invention, there is provided a lithographic
`
`apparatus comprising a conditioning system according to the first aspect of the present invention. The
`
`lithographic apparatus may be an EUV lithographic apparatus.
`
`[00024]
`
`According to a third aspect of the present invention, there is provided the use of a sub-
`
`atmospheric pressure conditioning system in a lithographic apparatus. Preferably, the conditioning
`
`system is a conditioning system according to the first aspect of the present invention.
`
`[00025]
`
`According to a fourth aspect of the present invention, there is provided a method of
`
`conditioning a system or sub-system of a lithographic apparatus, wherein said method includes
`
`providing a liquid conditioning fluid at sub-atmospheric pressure to the system or sub-system to be
`
`conditioned. The system or sub-system may comprise an optical element, such as, for example a
`
`reflector or mirror. There may be one or more than one optical elements. Suitable distribution means,
`
`10
`
`15
`
`20
`
`25
`
`30
`
`35
`
`
`
`2020P00230EP
`
`5
`
`[00016]
`
`The system mayinclude a pump downstream of the optical element and a flow restrictor
`
`upstream of the optical element. As such, the suction side of the pump maybein fluid connection with
`
`a conditioning channelof the optical element such that when the pumpis in operation, a pressure which
`
`is below atmospheric pressure is created at the optical clement. The presence ofthe flow restrictor
`
`upstream of the optical element ensures that the pressure at the optical element is below atmospheric
`
`pressure. The present inventionis not particularly limited by the exact dimensionsor nature of the flow
`
`restrictor since these will depend on the dimensions of the pipes which carry the conditioning fluid, the
`
`required flow rate, and the required pressure of the system, but these can be determined routinely by
`
`the skilled person and the pressure at the optical element being conditioned can be measured routinely
`
`to confirm the pressure therein.
`
`[00017]
`
`The system may include a sub-atmosphceric pressure conditioning fluid rescrvoir. As such,
`
`the system may comprise a conditioning fluid reservoir which is al sub-atmospheric pressure. The sub-
`
`atmospheric conditioning fluid reservoir may be connected to a vacuum pump. The vacuum pump may
`
`be configured to allow control of the pressure within the conditioning fluid reservoir by removing gases
`
`from the reservoir to provide the desired sub-atmospheric pressure. A gas inlet may optionally be
`
`provided which allows a gas, such as air or nitrogen, to be introduced into the conditioning fluid
`
`reservoir to increase the pressure should it become too low. The system may include a controller which
`
`is operable to control the vacuum pumpand/or gas inlct in order to achieve the desired sub-atmospheric
`
`pressure.
`
`[00018]
`
`In some embodiments which include a sub-atmospheric conditioning fluid reservoir, a
`
`pumpis provided downstream of the optical element and a flow restrictor is provided upstream of the
`
`optical element.
`
`In other embodiments including a sub-atmospheric pressure conditioning fluid
`
`reservoir, the pump may be provided upstreamof the optical element since the downstream portion of
`
`the conditioning system is connected to the sub-atmospheric conditioning fluid reservoir and therefore
`
`the pressure at the optical clement is able to remain sub-atmosphcric. Optionally, a flow restrictor is
`
`provided upstream of the pump and downstreamof the optical element, namely between the pump and
`
`the optical element, in order to control the flow of conditioning fluid and avoid the pressure at the
`
`optical element from exceeding atmospheric pressure.
`
`[00019]
`
`The sub-atmospheric pressure conditioning fluid reservoir may include a deformable
`
`separator between the liquid conditioning fluid and a gas. The deformable separator may be in the form
`
`of amembrane. By having a deformable separator between the conditioning fluid and a gas within the
`
`sub-atmospheric pressure conditioning fluid reservoir, the sub-atmospheric pressure can be maintained
`
`without any evaporation of the conditioning fluid. The gas above the deformable separator may have
`
`its pressure adjusted to control the pressure within the system. The composition of the gas is not
`
`particularly limiting on the present invention, and may, for example, be air or nitrogen. The pressure
`
`of the gas can be adjusted to adjust the pressure within the system. In addition, the separator is able to
`
`be deformed to take account of any pressure changes and to also act as a vibration damper.
`
`10
`
`15
`
`20
`
`25
`
`30
`
`35
`
`
`
`2020P00230EP
`
`4
`
`operating pressure. As mentioned above, by operating at below atmospheric pressure (1 bara), it is
`
`possible to avoid the problems associated with deformation caused by using pressure above 1 bara and
`
`also allows any conditioning channels to be provided closer to the surface which is to be conditioned
`
`than would otherwise be the case, thereby improving conditioning efficiency. Of course,if the pressure
`
`is too low, then there is a risk of cavitation and there would not be enough pressure difference to cause
`
`conditioning fluid to flow. In addition,if the system goes below the vapour pressure of the conditioning
`
`fluid, which may be water, the conditioning fluid may boil at an undesirably low temperature, for
`
`example 22°C at 0.02 bara for water. It has been foundthat operating pressures of between around 0.02
`
`bara and 0.9 bara provide the correct balance between avoiding deformation, avoiding cavitation,
`
`allowing conditioning fluid channels to be close enoughto the surface to be conditioned efficiently, and
`
`allowing conditioning fluid flow through the system. The conditioning system of the present invention
`
`also allows in some cases the avoidance of the need to manufacture optical elements, such as reflectors,
`
`when underpressure. It will be appreciated that at certain points in the conditioning system, the pressure
`
`may be around atmospheric or even slightly above atmospheric. Even so, the system is configured such
`
`that the pressure at the optical element or elements being conditioned is sub-atmospheric when in use.
`
`Since the optical elements are in a very low pressure environment within the lithographic apparatus of
`
`around a few pascals of hydrogen, the pressure differential between the conditioning fluid channels
`
`within the optical clement and the outside of the optical clementis effectively equal to the pressure of
`
`the conditioning fluid within the conditioning fluid channels.
`
`[00014]
`
`The conditioning system may include a liquid conditioning fluid, preferably water. The
`
`conditioning fluid may be provided with one or more additives to improve performance, such as
`
`corrosion inhibitors to prevent corrosion within the system. Whilst conditioning fluids such as carbon
`
`dioxide may be used in other systems, this usually requires much higher pressures in order to obtain the
`
`necessary mass flowto provide effective conditioning and so there are additional safety considerations
`
`to take into account and the high pressures required, such as from 20 to 100 bar, are not compatible
`
`with avoiding deformation. Whilst other water-cooled systems may describe a broad range of pressures,
`
`there is no realization of the suitability of the specific range described herein, nor of operating at sub-
`
`atmospheric pressures at the units which are being conditioned, namely at the optical elements.
`
`Pressures above atmospheric pressure have previously been used since these can be more readily
`
`achieved bythe provision of standard pumping apparatus, which pressurizes water to above atmospheric
`
`pressure in order to pump the water through the conditioning system, and the problem of deformation
`
`has been addressed by moditying the contiguration of the conditioning channels. Water is preterred
`
`dueto its safety, high thermal mass, and availability.
`
`[00015]
`
`The system may include a conditioning fluid reservoir. The conditioning fluid reservoir
`
`maybeatleast partially filled with conditioning fluid, preferably water. By having a conditioning fluid
`
`reservoir, there is a thermal mass of conditioning fluid which can be circulated through the system to
`removeheat therefrom or add heat thereto.
`
`10
`
`15
`
`20
`
`25
`
`30
`
`35
`
`
`
`2020P00230EP
`
`3
`
`elements of a lithographic apparatus, particularly an EUV lithographic apparatus, are very sensitive to
`
`any deformations, even very small ones.
`
`[00011]
`
`It has been found that if the relative pressure between the conditioning system and the
`
`outside of the optical clement is greater than atmospheric pressure, there will be deformation of the
`
`surface of the optical elements and this deformation impacts the performance of the optical elements.
`
`Since the conditioning system is for a lithographic apparatus,
`
`the main parts of the lithographic
`
`apparatus that are to be conditioned, whether by cooling or heating, are under vacuum or only a very
`
`lowpressure of gas, usually hydrogen, and so it has been found that sub-atmospheric pressures are
`
`desired to avoid deformation of critical components with the associated loss of performance. Whilstit
`
`has previously been mitigated by providing the condition channels deeper within the substrate of the
`
`system being conditioned, this impacts on thermal performance and the conditioning provided is
`
`insufficient in cases where the conditioning channels need to be deep within a substrate in order to
`
`reduce or eliminate deformation. By providing a conditioning system which is configured to operate at
`
`sub-atmospheric pressure
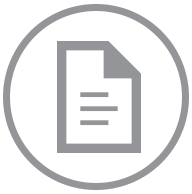
Accessing this document will incur an additional charge of $.
After purchase, you can access this document again without charge.
Accept $ ChargeStill Working On It
This document is taking longer than usual to download. This can happen if we need to contact the court directly to obtain the document and their servers are running slowly.
Give it another minute or two to complete, and then try the refresh button.
A few More Minutes ... Still Working
It can take up to 5 minutes for us to download a document if the court servers are running slowly.
Thank you for your continued patience.
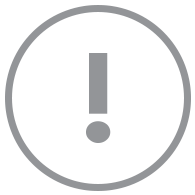
This document could not be displayed.
We could not find this document within its docket. Please go back to the docket page and check the link. If that does not work, go back to the docket and refresh it to pull the newest information.
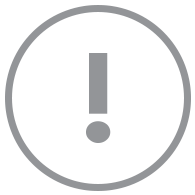
Your account does not support viewing this document.
You need a Paid Account to view this document. Click here to change your account type.
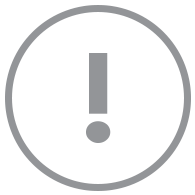
Your account does not support viewing this document.
Set your membership
status to view this document.
With a Docket Alarm membership, you'll
get a whole lot more, including:
- Up-to-date information for this case.
- Email alerts whenever there is an update.
- Full text search for other cases.
- Get email alerts whenever a new case matches your search.
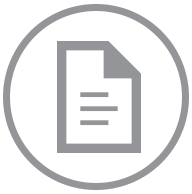
One Moment Please
The filing “” is large (MB) and is being downloaded.
Please refresh this page in a few minutes to see if the filing has been downloaded. The filing will also be emailed to you when the download completes.
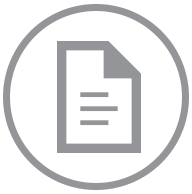
Your document is on its way!
If you do not receive the document in five minutes, contact support at support@docketalarm.com.
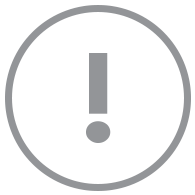
Sealed Document
We are unable to display this document, it may be under a court ordered seal.
If you have proper credentials to access the file, you may proceed directly to the court's system using your government issued username and password.
Access Government Site