`
`,
`(19) World Intellectual Property Organization a | I
`International Bureau
`
`p
`
`2) AITOMTTAAA
`
` (10) International Publication Number
`
`(43) International Publication Date
`30 July 2009 (30.07.2009)
`
`(51) International Patent Classification:
`HOLL 31/042 (2006.01)
`
`(21) International Application Number:
`PCT/US2009/03 1874
`
`(22) International Filing Date: 23 January 2009 (23.01.2009)
`
`(25) Filing Language:
`
`(26) Publication Language:
`
`English
`
`English
`
`(30) Priority Data:
`61/023,328
`
`24 January 2008 (24.01.2008)
`
`US
`
`(71) Applicant (for ali designated States except US): AP-
`PLIED MATERIALS, INC.
`[US/US]; 3050 Bowers
`Avenue, Santa Clara, CA 95054 (US).
`
`(72) Inventor: BORDEN,Peter; 118 Seville Way, San Mateo,
`CA 94402 (US).
`
`WO 2009/094570 A2
`
`(81) Designated States (unless otherwise indicated, for every
`kind of national protection available): AE, AG, AL, AM,
`AO, AT, AU, AZ, BA, BB, BG, BH, BR, BW, BY, BZ, CA,
`CH, CN, CO, CR, CU, CZ, DE, DK, DM,DO,DZ, EC, EE,
`EG,ES, FI, GB, GD, GE, GH, GM, GT, HN, HR, HU,ID,
`IL, IN,IS, JP, KE, KG, KM, KN, KP, KR, KZ, LA, LC, LK,
`LR, LS, LT, LU, LY, MA, MD, ME, MG, MK, MN, Mw,
`Mx, MY, MZ, NA, NG,NI, NO, NZ, OM,PG,PH,PL, PT,
`RO, RS, RU, SC, SD, SE, SG, SK, SL, SM, ST, SV, SY. TJ,
`TM,TN, TR, TY, TZ, UA, UG, US, UZ, VC, VN, ZA, ZM,
`ZW.
`
`(84) Designated States (unless otherwise indicated, for every
`kind of regional protection available): ARIPO (BW, GH,
`GM, KE, LS, MW, MZ, NA, SD, SL, SZ, TZ. UG, ZM,
`ZW), Eurasian (AM, AZ, BY, KG, KZ, MD, RU, TJ, TM),
`European (AT, BE, BG, CH, CY, CZ, DE, DK, EE, ES, FI,
`FR, GB, GR, HR, HU,IE, IS, IT, LT, LU, LV, MC, MK,
`MT, NL, NO,PL,PT, RO, SE, SI, SK, TR), OAPI (BE BJ,
`CE, CG, CI, CM, GA, GN, GQ, GW, ML, MR, NE, SN,
`TD, TG).
`
`Published:
`
`(74) Agent: JAKOPIN, David, A.; Pillsbury Winthrop Shaw
`Pittman LLP, P.o.box 10500, Mclean, VA 22102 (US).
`
`without international search report and to be republished
`upon receipt of that report
`
`(54) Title: PLATING THROUGH TUNNEL DIELECTRICS FOR SOLAR CELL CONTACT FORMATION
`
`Tunnel dielectric 204 Plated metal 202
`
`Dielectric 206
`
`n-type layer 208
`
`p-type substrate 210
`FIG,2
`
`(57) Abstract: In general, the present invention relates to forming electrical contacts in a semiconductor device, including contact
`regions in solar cells. According to certain aspects, the invention provides methods and apparatuses for forming plated contacts in
`the presenceof a thin tunnel oxide. Preferably, the tunnel oxide dielectric layer is thin enough to sustain a tunnel current. Plating over
`the tunnel dielectric is then performed. The benefits of the invention include that no annealing is required to form the metal-silicide
`contact. Moreover, there is no requirement for special metals for n- or p-type contacts. Another advantageis that shallow contacts
`according to the invention avoid punching througha shallow junction, thereby enabling the use of shallower emitters with improved
`blue response. Still further, there is no need to control the amountof suicide metal plated in order to prevent driving the suicide alloy
`through the junction.
`
`
`
`WO2009/094570A2IMMINENTATICTMANTAMTROAC i
`
`
`
`WO 2009/094570
`
`PCT/US2009/031874
`
`PLATING THROUGH TUNNEL DIELECTRICS FOR SOLAR CELL CONTACT
`
`FORMATION
`
`CROSS REFERENCE TO RELATED APPLICATIONS
`
`(0001)
`
`The present application claimspriority to U.S. Prov. Appln. No. 61/023,328 filed
`
`January 24, 2008, the contents of which are incorporated by reference herein in their entirety.
`
`FIELD OF THE INVENTION
`
`{0002}
`
`The present invention relates to forming electrical contacts in a semiconductor
`
`device, and more particularly to methods and apparatuses for plating through tunnel oxides to
`
`metallize contact regionsin solar cells.
`
`BACKGROUND
`
`(0003]
`
`Plating is a known methodto selectively metallize contact regions, including
`
`contact regions for solar cells. FIG. 1 showsa prior art plated contact. As shown in FIG.1, ina
`
`conventional process, a dielectric layer 106 such as a nitride or oxide, is laid down onthe silicon
`
`surface. The silicon has a p-n junction, for example a shallow n-type region 108 over a low
`
`doped p-type substrate 110. Contact holes are openedin the dielectric 106 by etching, for
`
`example. A metal 102 such as nickelis then selectively plated in these contact holes. For
`
`example, a seed material is deposited by electroless plating and then the metalis plated on the
`
`seed material. More particularly, the seed selectively deposits only where the semiconductoris
`
`exposed via the contact holes, and the plating only happens on a conductive surface, which is the
`
`seed layer, but not on the dielectric.
`
`
`
`WO 2009/094570
`
`PCT/US2009/031874
`
`[0004]
`
`Many problemsexist with the prior art approaches and techniques. For example,
`
`the nickel mustbe relatively thick in manycasesto act as a diffusion barrier should a subsequent
`
`layer of copper be plated over the nickel, for example. Accordingly, the wafer must then be
`
`carefully alloyed to form a nickel-silicide contact. However, care must be taken, lest the contact
`
`alloy too deep and short out the p-n junction.
`
`{0005}
`
`Accordingly, there remains a need in the art for improved plated contacts and
`
`contact regions, including for use with solarcells.
`
`SUMMARY
`
`[0006]
`
`In general, the present invention relates to forming electrical contacts in a
`
`semiconductor device, including contact regions in solar cells. According to certain aspects, the
`
`invention provides methods and apparatuses for forming plated contacts in the presence of a thin
`
`tunnel oxide. Preferably, the tunnel oxide dielectric layer is thin enough to sustain a tunnel
`
`current. Plating over the tunnel dielectric is then performed. The benefits of the invention
`
`include that no annealing is required to form the metal-silicide contact. Moreover, there is no
`
`requirement for special metals for n- or p-type contacts. Another advantageis that shallow
`
`contacts accordingto the invention avoid punching through a shallow junction, thereby enabling
`
`the use of shallower emitters with improved blue response. Still further, there is no need to
`
`control the amountofsilicide metal plated in order to prevent driving thesilicide alloy through
`
`the junction.
`
`[0007]
`
`In furtherance ofthese and other aspects, a method of forming a contact in a solar
`
`cell having a p-n junction according to embodiments of the invention includes creating one or
`
`more contact regions overthe p-n junction; forming a tunnel dielectric in the one or more contact
`
`
`
`WO 2009/094570
`
`PCT/US2009/031874
`
`regions, wherein the forming step includes forming the tunnel dielectric thin enough to sustain a
`
`tunnel current therethrough; and plating a metal over the tunnel dielectric material to form the
`
`contact.
`
`[0008]
`
`In additional furtherance of these and other aspects,a solar cell according to
`
`embodiments of the invention comprises a p-n junction; one or more contact regions formed over
`
`the p-n junction; a tunnel dielectric formedin the one or more contact regions, wherein the tunnel
`
`dielectric is thin enough to sustain a tunnel current therethrough; and a metal plated over the
`
`tunnel dielectric material to form a contact to the p-n junction.
`
`BRIEF DESCRIPTION OF THE DRAWINGS
`
`[9009]
`
`These and other aspects and features of the present invention will become
`
`apparent to those ordinarily skilled in the art upon review of the following description ofspecific
`
`embodimentsof the invention in conjunction with the accompanyingfigures, wherein:
`
`FIG. 1 showsa prior art plated contact;
`
`FIG. 2 shows an improved contact according to embodiments of the invention;
`
`]0010]
`
`[0011]
`
`and
`
`[0012]
`
`FIG. 3 shows a process flow according to embodiments ofthe invention.
`
`DETAILED DESCRIPTION
`
`[0013}
`
`The present invention will now be described in detail with reference to the
`
`drawings, which are providedas illustrative examples of the invention so as to enable those
`
`skilled in the art to practice the invention. Notably, the figures and examples below are not meant
`
`to limit the scope of the present invention to a single embodiment, but other embodiments are
`
`possible by wayof interchange of someorall of the described or illustrated elements. Moreover,
`
`3
`
`
`
`WO 2009/094570
`
`PCT/US2009/031874
`
`wherecertain elements of the present invention can bepartially or fully implemented using
`
`known components, only those portions of such known components that are necessary for an
`
`understanding of the present invention will be described, and detailed descriptions of other
`
`portions of such known components will be omitted so as not to obscure the invention.
`
`In the
`
`present specification, an embodiment showing a singular componentshould not be considered
`
`limiting; rather, the invention is intended to encompass other embodiments includingaplurality
`
`of the same component, and vice-versa, unless explicitly stated otherwise herein. Moreover,
`
`applicants do not intend for any term in the specification or claims to be ascribed an uncommon
`
`or special meaning unless explicitly set forth as such. Further, the present invention
`
`encompasses present and future known equivalents to the known componentsreferred to herein
`
`by wayofillustration.
`
`[0014]
`
`In general, the present invention relates to forming plated contacts in the presence
`
`of a thin tunnel oxide. According to certain aspects, the present inventors recognize that a thin
`
`oxide underneath a contact can improve contact properties and eliminate the need for alloying the
`
`contact.
`
`[0015]
`
`Accordingly, in the present invention, a thin tunnel dielectric is formed before
`
`plating. FIG. 2 shows an improved contact according to the invention. As shown in FIG. 2,
`
`similar to a conventional process,a dielectric layer 206 such as a nitride or oxide, is laid down on
`
`a substrate surface. The substrate has a p-n junction, for example a shallow n-type region 208
`
`over a p-type substrate 210. Contact holes are openedin the dielectric 206. In contrast to the
`
`prior art, a tunnel dielectric 204 is provided in the contact region, and then a plated contact 202 is
`
`formed onthe tunnel dielectric 204.
`
`
`
`WO 2009/094570
`
`PCT/US2009/031874
`
`[0016]
`
`In embodiments, substrate 210 is comprisedofsilicon, and is low-doped with p-
`
`type impurities. Many other substrate materials can be used and this and many other methods for
`
`obtaining a desired polarity concentration and type are possible, as will be appreciated by those
`
`skilled in the art. Shallow n-type region 208 is preferred because shallow emitters provide
`
`improved blue response. In such a case, the n-type region 208 may be approximately 0.3-0.5
`
`micronsthick at the surface of the substrate 210. Moreover, as will be described in more detail
`
`below, one advantage of forming the tunnel oxide according to embodimentsofthe inventionis
`
`that an alloyingstep is not necessary, whichalleviates the potential problem ofthe plated contact
`
`punching throughthe shallow p-n junction. However, shallow emitters are not necessary for the
`
`invention.
`
`[0017]
`
`It should be noted that the term contact hole should be construed broadly so as to
`
`relate to many types of openings through dielectric layer 206 and manytypes ofsolar cell
`
`contacts. For example, the holes can provide for point contacts having an area of only a few
`
`square microns or millimeters (e.g. having a diameter from about 2 jum to up to 100-200 pm), or
`
`they can providefor line contacts that span many centimeters or more, and having widths about 2
`
`to 100 um. Thoseskilled in the art of solar cell contacts will appreciate how the teachings of the
`
`invention can be applied to these and other various types of contacts and openings.
`
`{0018}
`
`An example process flow according to embodimentsofthe invention is described
`
`more particularly in connection with FIG.3.
`
`[0019]
`
`In step $302, a substrate with a p-n junction is prepared or obtained. As set forth
`
`above, according to aspects of the invention,a silicon substrate with a shallow emitter is used.
`
`Details of its fabrication are not necessary for an understanding of the present invention. Next, in
`
`
`
`WO 2009/094570
`
`PCT/US2009/031874
`
`step $304,a dielectric layer is formed on the substrate surface. For example,a nitride such as a
`
`silicon nitride with an index of refraction of about 2.1 and thickness of about 76 nm or a
`
`stoichiometric oxide such as SiO. with thickness about 100 nm is laid down by CVD deposition
`
`for nitride or oxide, or thermal oxidation for oxide. A stack could also be used, with a 5 nm SiO,
`
`formed with rapid thermal oxidation and a 70 nm SiNover the oxide (SiNx refers to a material
`
`that may not have the standard Si;N4 stochiometry ofsilicon nitride).
`
`[0020]
`
`Next, in step $306, contact holes are openedin the dielectric layer. This opening
`
`step may be donebyetching, laser ablation, or any other methodthat provides a suitable opening
`
`the dielectric to expose the underlying substrate such as silicon. More particularly, as set forth
`
`above, the type of opening andits dimensions can depend onthe particular solar cell contact
`
`application such as point contacts and other types of contacts. Those skilled in the art will be
`
`able to understand how to form suitable openings for such various types of contacts using various
`
`conventional and proprietary methods. Methods mightincludelaser ablation or patterning and
`
`etching, or local deposition of an etchant.
`
`[0021]
`
`Next, in step $308, a thin tunneldielectric is then formed, using either a wet
`
`process (step S308A)or a dry process (step $308B). A dry process can include oxidation ina
`
`furnace tube or in a rapid thermal annealer. One wet process, called Chemox (developedat
`
`IMEC)formsa thin oxide in an ozonated hydrogen peroxide bath. A wet process (step $308A)
`
`such as Chemoxis preferred because it is a process step that immediately precedes plating, which
`
`is typically another wet processing step. Therefore, both can be donein the same wettool
`
`without additional wafer handling or loading. However,this is not necessary for the invention.
`
`
`
`WO 2009/094570
`
`PCT/US2009/031874
`
`{0022}
`
`In some embodiments,it is important for the dielectric to be thin enoughto carry
`
`sufficient current without creating a series impedance. Layers in the 8 to 12A range are readily
`
`formed using rapid thermal oxidation. Chemoxlayers are on the order of 8A thick. Such thin
`
`layers should readily pass current densities consistent with the requirementsofa solarcell
`
`operating at one sun.
`
`[0023]
`
`Next, in step $310, the contact metal is plated. In the preferred embodiment,
`
`nickel is used,although other metals such assilver, tungsten or copper mayalso be used. A
`
`conventional process for plating including a seed material can be used as described above. Those
`
`skilled in the art will understand manyalternatives, however.
`
`[0024]
`
`According to aspects of the invention,in contrast to the priorart plating process,
`
`no annealing or alloying process is required. Moreover, there is no requirementfor special
`
`metals for n- or p-type contacts, such as, for direct contacts, Al contacts p-type and Ag contacts
`
`n-type. In this case, contacting to reasonably high doped (mid to high 10'° doping can be done
`
`with any metal, although some may provide better contacts that others by virtue of differing work
`
`functions. Still further, there is no need to carefully control the amountofsilicide metal plated in
`
`order to prevent driving thesilicide alloy through the junction as is required in thepriorart.
`
`Accordingly, plating thicknesses down to about 2 jum can be used, for example.
`
`[0025]
`
`In any event, to do the plating in step S310,it is necessary to create a potential
`
`across the tunneldielectric, so that electrons can tunnel through thedielectric to reduce metal
`
`ions. There are two ways to accomplish this, as will be appreciated by thoseskilled in theart.
`
`For example, oneis to place an electrical bias between the solution and the back contact. This
`
`must be donein constantcurrent mode,as it will reverse bias the junction andcarries the risk of
`
`
`
`WO 2009/094570
`
`PCT/US2009/031874
`
`damaging the cell. Another techniqueis the well known methodoflight inducedplating. The
`
`sampleis illuminated, causing a photocurrent to flow through the tunnel dielectric. Those skilled
`
`in the art will be able to understand such conventional techniquesto the overall process flow of
`
`the present invention.
`
`{0026}
`
`Althoughthe present invention has been particularly described with reference to
`
`the preferred embodimentsthereof, it should be readily apparentto those of ordinary skill in the
`
`art that changes and modifications in the form and details may be made without departing from
`
`the spirit and scope ofthe invention. It is intended that the appended claims encompass such
`
`changes and modifications.
`
`
`
`WO 2009/094570
`
`PCT/US2009/031874
`
`WHATIS CLAIMED IS:
`
`1. A method of forming a contact in a solar cell having a p-n junction, comprising:
`
`creating one or more contact regions over the p-n junction;
`
`forminga tunnel dielectric in the one or more contact regions, wherein the formingstep
`
`includes formingthe tunnel dielectric thin enoughto sustain a tunnelcurrent therethrough; and
`
`plating a metal over the tunnel dielectric material to form the contact.
`
`2. A method according to claim 1 wherein the step of forming the tunnel dielectric includes
`
`forming an oxide layer using a Chemox process.
`
`3. A method according to claim 1 wherein the step of forming the tunnel dielectric includes
`
`forming an oxide layer using thermal oxidation.
`
`4. A method according to claim 1 wherein the metal includes nickel.
`
`5. A method according to claim 1 wherein the metal includes copper.
`
`6. A method according to claim | wherein the plating step includes creating a potential across
`
`the tunnel dielectric using a light bias to induce a photocurrent.
`
`7. A method according to claim 1 whereinthe plating step mcludescreating a potential across
`
`the tunnel dielectric using an electricalbias.
`
`
`
`WO 2009/094570
`
`PCT/US2009/031874
`
`8. A method according to claim 1, wherein the step of forming the tunnel dielectric includes
`
`forming a nitride layer.
`
`9. A method according to claim 1, wherein the p-n junction comprisesa silicon substrate doped
`
`with impurities of a first polarity, and an emitter region near a surface of the substrate with a
`
`second polarity opposite the first polarity.
`
`10. A method according to claim 9, wherein the emitter region comprises a shallow emitter,
`
`11. A solar cell, comprising:
`
`a p-n junction;
`
`one or more contact regions formed over the p-n junction;
`
`a tunnel dielectric formed in the one or more contact regions, wherein the tunnel
`
`dielectric is thin enough to sustain a tunnel current therethrough; and
`
`a metal plated over the tunnel dielectric material to form a contactto the p-n junction.
`
`12. A solar cell according to claim 12 wherein the tunnel dielectric comprises an oxide layer.
`
`13. A solar cell according to claim 12 wherein the metal includes one or more of nickel and
`
`copper.
`
`14. A solar cell according to claim 12, wherein the tunnel dielectric comprises a nitride layer.
`
`10
`
`
`
`WO 2009/094570
`
`PCT/US2009/031874
`
`15. A solar cell according to claim 12, wherein the p-n junction comprisesa silicon substrate
`
`doped with impurities ofa first polarity, and a shallow emitter region near a surface of the
`
`substrate with a second polarity opposite the first polarity.
`
`11
`
`
`
`WO 2009/094370
`
`PCT/US2009/031874
`
`1/2
`
`Plated metal 102
`
`Alloyed region 104
`
`.
`.
`Dielectric 106
`
`n-type layer 108
`
`p-type substrate 110
`
`FIG. 1
`(Prior Art)
`
`Tunneldielectric 204
`
`Plated metal 202
`
`p-type substrate 210
`
`Dielectric 206
`
`n-type layer 208
`
`FIG,2
`
`SUBSTITUTE SHEET (RULE 26)
`
`
`
`WO 2009/094370
`
`PCT/US2009/031874
`
`2/2
`
` Prepare substrate with
`
`
`
`shallow emitter
`5302
`
`
`
` Form dielectric layer
`
`5304
`
`
` Open contact holes
`
`
`
`$306
`
`
`
`
`
`
`
`
`
`
`Form oxide using
`rapid oxidation
`5308B
`
`Form oxide using
`Chemox process
`S308A
`
`
`
`
`
`Form plated contact
`S310
`
`
`
`
`FIG. 3
`
`SUBSTITUTE SHEET (RULE 26)
`
`
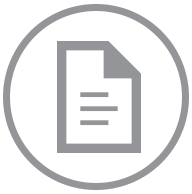
Accessing this document will incur an additional charge of $.
After purchase, you can access this document again without charge.
Accept $ ChargeStill Working On It
This document is taking longer than usual to download. This can happen if we need to contact the court directly to obtain the document and their servers are running slowly.
Give it another minute or two to complete, and then try the refresh button.
A few More Minutes ... Still Working
It can take up to 5 minutes for us to download a document if the court servers are running slowly.
Thank you for your continued patience.
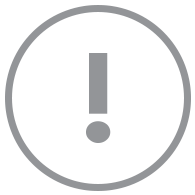
This document could not be displayed.
We could not find this document within its docket. Please go back to the docket page and check the link. If that does not work, go back to the docket and refresh it to pull the newest information.
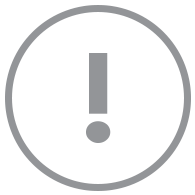
Your account does not support viewing this document.
You need a Paid Account to view this document. Click here to change your account type.
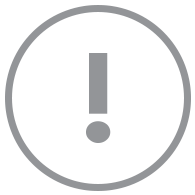
Your account does not support viewing this document.
Set your membership
status to view this document.
With a Docket Alarm membership, you'll
get a whole lot more, including:
- Up-to-date information for this case.
- Email alerts whenever there is an update.
- Full text search for other cases.
- Get email alerts whenever a new case matches your search.
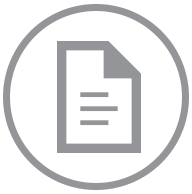
One Moment Please
The filing “” is large (MB) and is being downloaded.
Please refresh this page in a few minutes to see if the filing has been downloaded. The filing will also be emailed to you when the download completes.
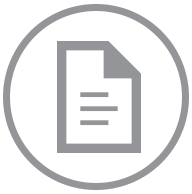
Your document is on its way!
If you do not receive the document in five minutes, contact support at support@docketalarm.com.
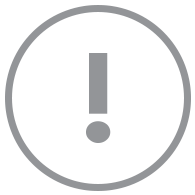
Sealed Document
We are unable to display this document, it may be under a court ordered seal.
If you have proper credentials to access the file, you may proceed directly to the court's system using your government issued username and password.
Access Government Site