`
`(12) INTERNATIONAL APPLICATION PUBLISHED UNDER THE PATENT COOPERATION TREATY (PCT)
`
`,
`(19) World Intellectual Property Organization a | I
`International Bureau
`
`p
`
`2) VAIO MTUAAA
`
`(43) International Publication Date
`30 July 2009 (30.07.2009)
`
`(51) International Patent Classification:
`HOLL 31/042 (2006.01)
`
`(21) International Application Number:
`PCT/US2009/03 1886
`
`(22) International Filing Date: 23 January 2009 (23.01.2009)
`
`(25) Filing Language:
`
`(26) Publication Language:
`
`English
`
`English
`
`WO 2009/094578 A2
`
`(81) Designated States (unless otherwise indicated, for every
`kind of national protection available): AE, AG, AL, AM,
`AO, AT, AU, AZ, BA, BB, BG, BH, BR, BW, BY, BZ, CA,
`CH, CN, CO, CR, CU, CZ, DE, DK, DM,DO,DZ, EC, EE,
`EG, ES, FI, GB, GD, GE, GH, GM, GT, HN, HR, HU,ID,
`IL, IN,IS, JP, KE, KG, KM, KN, KP, KR, KZ, LA, LC, LK,
`LR, LS, LY, LU, LY, MA, MD, ME, MG, MK, MN, Mw,
`Mx,MY, MZ, NA,NG,NI, NO, NZ, OM,PG,PH,PL, PT,
`RO, RS, RU, SC, SD, SE, SG, SK, SL, SM, ST, SV, SY. TJ,
`‘TM, ‘IN, TR, TT, 17Z, UA, UG, US, UZ, VC, VN, ZA, 2M,
`ZW.
`
`(30) Priority Data:
`61/023,342
`
`24 January 2008 (24.01.2008)
`
`US
`
`(71) Applicant (for all designated States except US): AP-
`PLIED MATERIALS, INC.
`[US/US]; 3050 Bowers
`Avenue, Santa Clara, CA 95054 (US).
`
`(72) Inventor: BORDEN,Peter; 118 Seville Way, San Mateo,
`CA 94402 (US).
`
`(84) Designated States (unless otherwise indicated, for every
`kind of regional protection available): ARIPO (BW, GH,
`GM, KL, LS, MW, MZ, NA, SD, SL, SZ, TZ, UG, ZM,
`ZW), Eurasian (AM, AZ, BY, KG, KZ, MD, RU, TJ, ‘I'M),
`European (AT, BE, BG, CH, CY, CZ, DE, DK,EE, ES, FI,
`FR, GB, GR, IIR, IIU, TE, IS, IT, LT, LU, LV, MC, MK,
`MT, NL, NO, PL, PL, RO, SE, SL SK, TR), OAPI (BE, BJ,
`CE, CG, CI, CM, GA, GN, GQ, GW, ML, MR, NE, SN,
`TD, TG).
`
`(74) Agent: DANIELSON, Mark, J.; Pillsbury Winthrop
`Shaw Pittman LLP, P.O. Box 10500, McLean, VA 22102
`(US).
`
`Published:
`
`without international search report and to be republished
`upon receipt ofthat report
`
`(54) Title: IMPROVED HIT SOLAR CELL STRUCTURE
`
`S F
`
`IG. 2A
`
`TCO 222
`
`7 ¥Si(p) 224 (50A)
`__-— a-Si(i) 226 (S0A)
`—— SiO, 228 (12A)
`
`__ Si 206
`
`(57) Abstract: The present invention relates to improved IIIT type or polysilicon emitter solar cells. According to certain aspects,
`the invention includes forming a masking oxidelayer on the front and backofthe cell and then patterning holes in the masking oxide.
`N
`© A HIT cell structure or polysilicon emitter solar cell structure is then formed overthe patterned oxide, creating the cell junction only
`© in the areas where holes have been cut. Benefits of the invention include thatit provides a controlled interface for the IIIT cell
`through insertion of a thin tunnel oxide. Moreover, the tunnel oxide prevents epitaxial growth of amorphoussilicon, allowing it to
`remain amorphousfor the optimum band structure. Still further, it provides a layer to protect the surface from plasma damage during
`
`iS deposition ofthe a-Si layer. Further, it may be used in conjunction with a point contact structure to further increase efficiency.
`
`094578AIMMUNITYATICA
`
`
`
`WO 2009/094578
`
`PCT/US2009/031886
`
`IMPROVED HIT SOLAR CELL STRUCTURE
`
`CROSS-REFERENCE TO RELATED APPLICATIONS
`
`(0001)
`
`The presentapplication claimspriority to U.S. Prov. Appin. No.61/023,342 filed
`
`January 24, 2008,the contents of which are incorporated herein by referencein their entirety.
`
`FIELD OF THE INVENTION
`
`[0002]
`
`The present invention relates to photovoltaic devices, and more particularly to
`
`methods and apparatuses for providing an improved structure of a HIT type or polysilicon emitter
`
`type solar cells.
`
`BACKGROUND
`
`[0003]
`
`HITtype solar cells are high efficiency devices with relatively simple structures.
`
`Sanyo Corporation of Japan has reported lab efficiencies of 21.5% and manufacturingefficiency
`
`in the mid-19% range. Many other groups have worked on this device, although none has shown
`
`as high efficiencies.
`
`[0004]
`
`A typical HIT typesolarcell structure is shown in FIG. 1A and 1B. Thedevice is
`
`symmetric, with the front and backof the n-type substrate 106 both coated with a coating 102
`
`and 110, respectively and metal grid lines 104 and 108, respectively. As shown in the blowup
`
`portion of FIG. 1B,the coating 102 on the front consists of two amorphoussilicon layers, an
`
`intrinsic layer 126 under a p-type layer 124, both about 50 Angstromsthick. On the back,the
`
`amorphoussilicon layer consists of an intrinsic (i) layer under an n-type layer. As further shown
`
`in FIG. 1B,the coating 102 further includesa layer of transparent conductive oxide (TCO) 122.
`
`
`
`WO 2009/094578
`
`PCT/US2009/031886
`
`[0005]
`
`The purpose ofthe thin a-Si layers is to both passivate the surface and to provide a
`
`heterojunction with a wide bandgap windowlayer to improve the open circuit voltage, as shown
`
`in FIG. 1C. Moreparticularly, FIG.
`
`1C illustrates the band structure of such a device. As shown
`
`in FIG. 1C,there is a large potential step at the front surface, creating a junction muchlike a
`
`junction found at the step between p- and n-type dopants. However, because this junction is
`
`formed by depositing a layer of amorphoussilicon, it is very abrupt, and nearly ideal.
`
`[0006]
`
`Despite their benefits, these amorphoussilicon layers also introduce considerable
`
`complexity into the fabrication of the HIT cell. For example, the layers must be formed on a
`
`carefully prepared surface, whose preparation details have not been published. Further, they
`
`must notcrystallize, as can happen when the amorphoussilicon is seeded by the crystal silicon
`
`substrate, as this will eliminate the beneficial passivation and heterojunction effects.
`
`[0007]
`
`Therefore, there is a lingering need for an improvedinterface that is well
`
`controlled and understood and easy to manufacture, and does not seed crystal growth.
`
`SUMMARY
`
`[0008]
`
`The present invention relates to improved HIT type or polysilicon emitter solar
`
`cells. Accordingto certain aspects, the invention includes forming a masking oxide layer on the
`
`front and back ofthe cell and then patterning holes in the masking oxide. A HIT cell structure or
`
`polysilicon emitter solar cell structure is then formed overthe patterned oxide, creating the cell
`
`junction only in the areas where holes have been cut. Benefits of the inventionincludethatit
`
`provides a controlled interface for the HIT cell throughinsertion ofa thin tunneloxide.
`
`Moreover, the tunnel oxide prevents epitaxial growth of amorphoussilicon, allowing it to remain
`
`amorphousfor the optimum bandstructure. Still further, 1t provides a layer to protect the surface
`
`
`
`WO 2009/094578
`
`PCT/US2009/031886
`
`from plasma damage during deposition of the a-Si layer. Further, it may be used in conjunction
`
`with a point contact structure to further increase efficiency.
`
`[0009]
`
`In furtherance of these and otheraspects,a solar cell according to embodiments of
`
`the invention comprises an amorphous semiconductor layer formed over a substrate; and a
`
`dielectric layer interposed between the substrate and the amorphous semiconductorlayer,
`
`wherein the dielectric layer is sufficiently thin so as to support a tunneling current therethrough.
`
`[0010]
`
`In additional furtherance of these and other aspects, a method offabricating a
`
`solar cell according to embodiments of the invention includes forming a dielectric layer on a
`
`substrate, wherein the dielectric layer is sufficiently thin so as to support a tunneling current
`
`therethrough; and forming an amorphous semiconductorlayer formed overthe dielectric layer.
`
`BRIEF DESCRIPTION OF THE DRAWINGS
`
`(0011)
`
`These and other aspects and featuresof the present invention will become
`
`apparent to those ordinarily skilled in the art upon review of the following description of specific
`
`embodiments ofthe invention in conjunction with the accompanying figures, wherein:
`
`[0012]
`
`[0013]
`
`FIGs. 1A to 1C show a conventional HITcell and its bandstructure.
`
`FIGs. 2A and 2B show an examplesolar structure of the present invention andits
`
`bandstructure, respectively.
`
`[0014]
`
`FIG.3 is a diagram illustrating an example process flow to form the structure of
`
`FIG. 2 according to aspects of the invention.
`
`DETAILED DESCRIPTION
`
`(0015]
`
`The present invention will now be described in detail with reference to the
`
`drawings, which are providedasillustrative examples of the invention so as to enable those
`
`
`
`WO 2009/094578
`
`PCT/US2009/031886
`
`skilled in the art to practice the invention. Notably, the figures and examples below are not meant
`
`to limit the scope of the present invention to a single embodiment, but other embodiments are
`
`possible by way of interchange of some orall of the describedorillustrated elements. Moreover,
`
`wherecertain elements of the present invention can bepartially or fully implemented using
`
`known components, only those portions of such known components that are necessary for an
`
`understanding of the present invention will be described, and detailed descriptions of other
`
`portions of such known components will be omitted so as not to obscure the invention. In the
`
`present specification, an embodiment showing a singular component should not be considered
`
`limiting; rather, the invention is intended to encompass other embodiments includinga plurality
`
`of the same component, and vice-versa, unless explicitly stated otherwise herein. Moreover,
`
`applicants do notintend for any term in the specification or claimsto be ascribed an uncommon
`
`or special meaning unless explicitly set forth as such. Further, the present invention
`
`encompassespresent and future known equivalents to the known components referred to herein
`
`by way ofillustration.
`
`[0016]
`
`In general, the present inventors recognize that thin tunnel oxide layers can be
`
`used in solar cells. For example, some MIS cells can be made using aluminum overtunnel
`
`oxides. The present inventors further recognize that tunnel oxides can be used betweenaheavily
`
`doped or insulating layer of polysilicon and a crystal silicon substrate, forming a polysilicon
`
`emitter solar cell. Such a solar cell has a similar band structure to a HIT cell, essentially
`
`replacing the TCO and a-Silayers with polysilicon. However, such cells do not provide the
`
`heterojunction and its benefit of a higher cell voltage due to the higher bandgapof a-Si.
`
`
`
`WO 2009/094578
`
`PCT/US2009/031886
`
`[0017]
`
`An example solar cell structure according to embodimentsof the invention and
`
`the associated band structure is shown in FIGs, 2A and 2B, respectively.
`
`[0013]
`
`As shown in FIG, 2A, which can be part of a front surface of a HIT-type solar cell
`
`similar to that shown in FIG.1, a thin dielectric layer 228 (e.g. tunnel oxide) is provided between
`
`the a-Si layers 224 and 226 and the n-type substrate 206 in a HIT cell. The dielectric layeris
`
`preferably thin, on the order of 8-15A,in order to support a tunneling current between the
`
`substrate and a-Si layers. As will be described in more detail below, layer 228 can be formed
`
`using conventional methods such as rapid thermal oxidation, furnace oxidation, or the Chemox
`
`process (formation in an ozonated H)O, bath). In some cases, the layer maybenitrided or
`formed using other materials such assilicon nitride or silicon oxynitride.
`
`[0019]
`
`As shown in FIG. 2B, added dielectric layer at the interface provides a bandgap
`
`much larger than the bandgap of the semiconductors. Carriers cannot get over the energy barrier,
`
`but tunnel throughif the layer is sufficiently thin (<15A). Note that oxide and nitride will have
`
`different barrier heights, so the layer shown is not meant to represent any one material. The
`
`barrier height for nitride is about 2.5 eV and is symmetric. The barrier height for oxide is
`
`asymmetric (lower for electrons).
`
`[0020]
`
`The benefits provided by dielectric layer 228 are several-fold. For example,it
`
`may be formed using conventional surface cleaning and preparation methods, as are used to make
`
`MOS gates for ICs. Therefore, the surface preparation is well known and understood, and
`
`routinely implemented in high volume manufacturing. Moreover,as it is an amorphouslayer,it
`
`separates the subsequenta-Si layer from the substrate, preventing epitaxial seeding of crystal
`
`
`
`WO 2009/094578
`
`PCT/US2009/031886
`
`growth in the a-Si layer. Further, it provides an intervening layer to protect the crystal silicon
`
`surface from plasma damage during deposition of the a-Silayer.
`
`[0021}
`
`It should be noted that, although benefits of the invention are obtained with a-Si
`
`layers formed overa crystalline silicon substrate, that this is not limiting, and that the invention
`
`can be applied to other types of substrates and thin semiconductor layers. It should be further
`
`noted that many solar cells use heterojunctions. So, for example, the invention could be used
`
`with a thin film solar cell with amorphoussilicon on micro-crystal silicon. It could also be used
`
`on CdTe, CIGS or AlGaAs/GaAscells, all of which use heterojunctions.
`
`{0022}
`
`That said, it should bestill further noted that amorphoussilicon onsilicon is
`
`known to provide excellent passivation properties, nearly eliminating surface recombination.
`
`This is because the high band bendingat the surfacerepels carriers. Accordingly,this is one
`
`advantage of using amorphoussilicon onsilicon.
`
`[0023]
`
`FIG.3 is a diagram illustrating an example processflow used to makethe
`
`structure of FIG. 2A. First, in step $302, the front surface of the n-type substrate is textured.
`
`This may be accomplished using conventional etching, such as isopropyl] alcohol and KOH.
`
`Next in step $304, the surface is provided with a standard MOS clean to remove native oxides,
`
`ionic contamination, and organics.
`
`[0024]
`
`In one embodiment, a rapid thermal oxide processis then used in step $306 to
`
`form a thin tunnel oxide, typically 12A thick, on the front surface. In another embodiment of the
`
`invention, the oxide is formed on both front and back at the same time. Next the a-Si layers are
`
`deposited on the front surface. In one embodiment, the a-Si is formed as a two layer stack on the
`
`front surface, with an intrinsic a-Si, 20-50 A thick formedfirst in step S308, for example by
`
`
`
`WO 2009/094578
`
`PCT/US2009/031886
`
`plasma enhanced chemical vapor deposition (PE-CVD), which is the decompositionofsilane in a
`
`plasma, often with hydrogen present. These processes are well known in theliterature. Boron
`
`may be addedto provide p-type doping, and phosphorous may be addedto provide n-type
`
`doping. Next, a p-type a-Si, 20-50 A thick is formed ontopofthe intrinsic a-Si layer in step
`
`S312, for example by the same PE-CVDprocess. In another embodiment, only a doped p-type
`
`layer is formed on the front surface in step S310, withoutthe i-type layer. The TCO is deposited
`
`in step S314, which may be a quarter wavethick layer of indium tin oxide.
`
`[0025]
`
`The wafer is then flipped over in step $316, and the structure is deposited in the
`
`same manneronthe back side, now using n-type a-Si instead of p-type. As shown, depending on
`
`whetherthe oxide layer has already been formed, processing returns to step $306 or step $308. It
`
`should be further apparent that processing could also return to step $310 if the oxide layer has
`
`already been formed. Finally, contacts are formed in step S318, for example by screen printing
`
`or sputtering.
`
`[0026]
`
`Additionally or alternatively to the process described above, a method to form
`
`point contacts for HIT or polysilicon emitter solar cells, as described in co-pending application
`
`No. _ (AMAT-12964), the contents of which are incorporated herein by reference in their
`
`entirety, may be performed.
`
`[0027]
`
`Althoughthe present invention has been particularly described with reference to
`
`the preferred embodimentsthereof, it should be readily apparentto those of ordinary skill in the
`
`art that changes and modifications in the form and details may be made without departing from
`
`the spirit and scope of the invention.
`
`It is intended that the appended claims encompass such
`
`changes and modifications.
`
`
`
`WO 2009/094578
`
`PCT/US2009/031886
`
`WHATIS CLAIMEDIS:
`
`1. A solar cell comprising:
`
`an amorphous semiconductor layer formed over a substrate;
`
`a dielectric layer interposed between the substrate and the amorphous semiconductor
`
`layer, wherein the dielectric layer is sufficiently thin so as to support a tunneling current
`
`therethrough.
`
`2. A solar cell according to claim 1, wherein the substrate comprises silicon and the dielectric
`
`layer comprises silicon dioxide.
`
`3. Asolar cell according to claim 1, wherein the substrate comprises silicon and the dielectric
`
`layer comprisesnitrogen.
`
`4. A solar cell according to claim 1, wherein the amorphous semiconductor layer comprises
`
`silicon.
`
`5. A solar cell according to claim 1, wherein the amorphous semiconductor layer comprises a
`
`two-layer stack of an intrinsic amorphoussilicon layer and a doped amorphoussilicon layer.
`
`6. A solar cell according to claim 1, wherein the amorphous semiconductorlayer is formed on a
`
`front surface of the substrate, wherein the solar cell further comprises:
`
`
`
`WO 2009/094578
`
`PCT/US2009/031886
`
`another amorphous semiconductor layer is formed on an opposite back surtace of the
`
`substrate; and
`
`anotherdielectric layer interposed between the substrate and the another amorphous
`
`semiconductor layer, wherein the another dielectric layer is sufficiently thin so as to support a
`
`tunneling current therethrough.
`
`7. A solar cell according to claim 6, wherein both the amorphous semiconductorlayer and the
`
`another amorphous semiconductor layer comprise a two-layer stack of an intrinsic amorphous
`
`silicon layer and a doped amorphoussilicon layer.
`
`8. A methodoffabricating a solar cell, comprising:
`
`forming a dielectric layer on a substrate, wherein the dielectric layer is sufficiently thin so
`
`as to support a tunneling current therethrough; and
`
`forming an amorphous semiconductor layer formed overthe dielectric layer.
`
`9. A method according to claim 8, wherein the step of forming the amorphous semiconductor
`
`layer includes forming a two-layer stack of an intrinsic amorphoussilicon layer and a doped
`
`amorphoussilicon layer.
`
`10. A method according to claim 8, further comprising:
`
`texturing a surface of the substrate before forming the dielectric layer.
`
`
`
`WO 2009/094578
`
`PCT/US2009/031886
`
`11. A method according to claim 8, wherein a rapid thermal oxide process is used to form the
`
`dielectric layer.
`
`12. A method according to claim 9, wherein the intrinsic and doped amorphoussilicon layers are
`
`both about 20-50 A thick.
`
`13. A method accordingto claim 8, further comprising depositing a layer of TCO over the
`
`amorphous semiconductorlayer.
`
`14. A method according to claim 13, wherein the TCO comprises a quarter wavethick layer of
`
`indium tin oxide.
`
`15. A method according to claim 8, wherein the amorphous semiconductor layer is formed on a
`
`front surface of the substrate, wherein the method further comprises:
`
`forming anotherdielectric layer on an opposite back surface of the substrate, wherein the
`
`anotherdielectric layer is sufficiently thin so as to support a tunneling current therethrough, and
`
`forming another amorphous semiconductor layer over the anotherdielectric layer.
`
`10
`
`
`
`WO 2009/094578
`
`PCT/US2009/031886
`
`
`
`FIGLIA
`
`
`
`
`
`
`
`
`
`
`IN /,
`YN \YI
`
`
`
`\—
`
`a-Si(p) 124 (504)
`
`
`
`a-Sid) 126 (504)
`n-Si 106
`
`BIG. 1B
`
`G-SEEip) @-SLA
`
`
`
` c-Siai Ex
`
`Jront
`
`back
`
`FIG ic
`
`1/3
`
`
`
`WO 2009/094578
`
`PCT/US2009/031886
`
`IW/\JwTCO222
`NW)J
`
`U7 #Silp) 224 (50A)
`_— a-Si(i) 226 (50A)
`—— SiO, 228 (12A)
`
`_ Si 206
`
`FIG. 2A
`
`pli}
`
`o@-SiHi{p) o-Si]
`
`
`
`
`
`
`c-Sitni Ey OSH)sit)
`
`Added tunnel
`oxide
`
`
`
`
`Jront
`
`back
`
`FIG. 2B
`
`2/3
`
`
`
`WO 2009/094578
`
`PCT/US2009/031886
`
`
`
`
`Texture front
`surface
`$302
`
`MOS clean
`$304
`
`a-Si(doped)
`$310
`
`
`S316 a-Si(doped)
`
`
`
`
`
`Flip wafer
`
`
`$312
`
`Contacts
`$318
`
`FIG. 3
`
`3/3
`
`
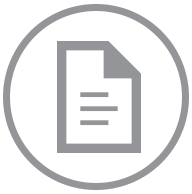
Accessing this document will incur an additional charge of $.
After purchase, you can access this document again without charge.
Accept $ ChargeStill Working On It
This document is taking longer than usual to download. This can happen if we need to contact the court directly to obtain the document and their servers are running slowly.
Give it another minute or two to complete, and then try the refresh button.
A few More Minutes ... Still Working
It can take up to 5 minutes for us to download a document if the court servers are running slowly.
Thank you for your continued patience.
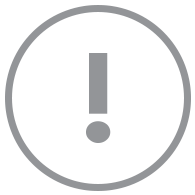
This document could not be displayed.
We could not find this document within its docket. Please go back to the docket page and check the link. If that does not work, go back to the docket and refresh it to pull the newest information.
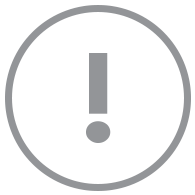
Your account does not support viewing this document.
You need a Paid Account to view this document. Click here to change your account type.
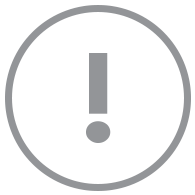
Your account does not support viewing this document.
Set your membership
status to view this document.
With a Docket Alarm membership, you'll
get a whole lot more, including:
- Up-to-date information for this case.
- Email alerts whenever there is an update.
- Full text search for other cases.
- Get email alerts whenever a new case matches your search.
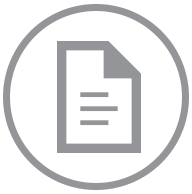
One Moment Please
The filing “” is large (MB) and is being downloaded.
Please refresh this page in a few minutes to see if the filing has been downloaded. The filing will also be emailed to you when the download completes.
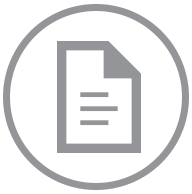
Your document is on its way!
If you do not receive the document in five minutes, contact support at support@docketalarm.com.
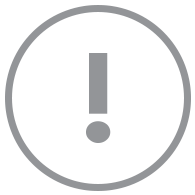
Sealed Document
We are unable to display this document, it may be under a court ordered seal.
If you have proper credentials to access the file, you may proceed directly to the court's system using your government issued username and password.
Access Government Site