`
`FRONT CONTACT SOLAR CELL WITH FORMED EMITTER
`
`Inventor: Peter John Cousins
`
`REFERENCE TO RELATED APPLICATIONS
`
`This application is a continuation of U.S. Application No. 16/460,035, filed July 2,
`
`2019, whichis a continuation of U.S. Application No. 14/504,771, filed on October2,
`
`2014, whichis a continuation of U.S. Application No. 13/495,577, filed on June 13,
`
`2012, now U.S. Patent No. 8,878,053, which is a divisional of U.S. Application No.
`
`12/070,742, filed on February 20, 2008, now U.S. Patent No. 8,222,516. The just-
`
`mentioned disclosures are incorporated herein by referencein their entirety.
`
`BACKGROUND OF THE INVENTION
`
`1.
`
`Field of the Invention
`
`The present invention relates generally to solar cells, and more particularly but
`
`not exclusively to solar cell fabrication processes and structures.
`
`2.
`
`Description of the Background Art
`
`Solar cells are well known devices for converting solar radiation to electrical
`
`20
`
`energy. They may befabricated on a semiconductor wafer using semiconductor
`
`processing technology. A solar cell includes P-type and N-type diffusion regions that
`
`form a junction. Solar radiation impinging on the solar cell creates electrons and holes
`
`that migrate to the diffusion regions, thereby creating voltage differentials between the
`
`-41-
`
`
`
`Attorney Docket No. SKYW00056-1C US
`
`diffusion regions.
`
`In a backside contact solar cell, both the diffusion regions and the
`
`metal contacts coupled to them are on the backside of the solar cell. The metal
`
`contacts allow an external electrical circuit to be coupled to and be poweredbythe solar
`
`cell.
`
`In a front contact solar cell, at least one of the metal contacts making an
`
`electrical connection to a diffusion region is on the front side of the solar cell. The front
`
`side of the solar cell, which is opposite the backside, faces the sun during normal
`
`operation to collect solar radiation. While backside contact solar cells have an aesthetic
`
`advantage over front contact solar cells due to the absence of metal contacts on the
`
`10
`
`front side, and are thus preferred for residential applications, aesthetics is not a major
`
`requirement for power plants and other applications where power generation is the main
`
`concern. Disclosed herein are structures for a relatively efficient and cost-effective front
`
`contact solar cell and processes for manufacturing same.
`
`15
`
`SUMMARY
`
`A bipolar solar cell includes a backside junction formed by an N-type silicon
`
`substrate and a P-type polysilicon emitter formed on the backside of the solar cell. An
`
`antireflection layer may be formed on a textured front surface of the silicon substrate. A
`
`negative polarity metal contact on the front side of the solar cell makes an electrical
`
`20
`
`connection to the substrate, while a positive polarity metal contact on the backside of
`
`the solar cell makes an electrical connection to the polysilicon emitter. An external
`
`electrical circuit may be connected to the negative and positive metal contacts to be
`
`
`
`Attorney Docket No. SKYW00056-1C US
`
`poweredby the solar cell. The positive polarity metal contact may form an infrared
`
`reflecting layer with an underlying dielectric layer for increased solar radiation collection.
`
`These and other features of the presentinvention will be readily apparent to
`
`persons ofordinary skill in the art upon reading the entirety of this disclosure, which
`
`includes the accompanying drawings and claims.
`
`DESCRIPTION OF THE DRAWINGS
`
`FIG. 1 schematically shows a cross-section of a solar cell in accordance with an
`
`embodimentof the present invention.
`
`FIG. 2 is a plan view schematically showing the front side of the solar cell of FIG.
`
`FIG. 3 is a plan view schematically showing the backside of the solar cell of FIG.
`
`FIG. 4, which comprises FIGS. 4A-4M, schematically illustrates the fabrication of
`
`the solar cell of FIG. 1
`
`in accordance with an embodimentof the present invention.
`
`The use of the same referencelabel in different figures indicates the same or like
`
`components. The figures are not drawn to scale.
`
`DETAILED DESCRIPTION
`
`20
`
`In the present disclosure, numerous specific details are provided, such as
`
`examples of apparatus, process parameters, materials, process steps, and structures,
`
`-3-
`
`
`
`Attorney Docket No. SKYW00056-1C US
`
`to provide a thorough understanding of embodiments of the invention. Persons of
`
`ordinary skill in the art will recognize, however, that the invention can be practiced
`
`without one or more of the specific details.
`
`In other instances, well-known details are
`
`not shownor described to avoid obscuring aspects of the invention.
`
`FIG. 1 schematically showsa cross-section of a solar cell 100 in accordance with
`
`an embodimentof the present invention. The solar cell 100 has a front side where a
`
`metal contact 102 is located and a backside on a same side as the metal contact 110.
`
`The front side faces the sun during normal operation to collect solar radiation.
`
`In the example of FIG. 1, the solar cell 100 includes a backside junction formed
`
`by a P-type dopedpolysilicon emitter 108 serving as a P-type diffusion region and an N-
`
`type silicon substrate 101 servings as an N-typediffusion region. The N-typesilicon
`
`substrate 101 may comprise a long lifetime (e.g., 2 to 5ms) N-type silicon wafer and
`
`may have a thickness of about 100 to 250 um as measured from the backside surface
`
`to a tip of the textured front side surface of the substrate. The front side surface of the
`
`substrate 101 is randomly textured (labeled as 113) and includes N-type doped regions
`
`105 and 106 formedin the substrate. The N-type doped region 105 provides low front
`
`surface recombination and improveslateral conductivity whilst not compromising the
`
`blue response ofthe solar cell. The region 106, which may be a phosphorus diffusion,
`
`provides low contact resistance and minimizes contact recombination. The region 106
`
`20
`
`is also referred to as an "N-dot" because, in one embodiment, it forms a dot-shape to
`
`minimize the area of heavily diffused regions on the front surface. The N-type doped
`
`region 105 may have a sheet resistance of 100 to 500 Q/sq, whilst the n-type doped
`
`region 106 may have a sheetresistance of 10 to 50 O/sq.
`
`-4-
`
`
`
`Attorney Docket No. SKYW00056-1C US
`
`An antireflective coating (ARC) of silicon nitride layer 103 is formed on the
`
`textured front side surface of the substrate 101. The texture front side surface and the
`
`silicon nitride layer 103 help improve solar radiation collection efficiency. A passivating
`
`oxide 124 may comprisesilicon dioxide thermally grown to a thickness of about 10 to
`
`250 Angstroms on the front side surface of the substrate 101.
`
`In one embodiment, the polysilicon emitter 108 is formed on a tunnel oxide layer
`
`107. The polysilicon emitter 108 may be formed by forming a layer of polysilicon using
`
`Chemical Vapor Deposition (CVD), such as Low Pressure CVD (LPCVD) or Plasma
`
`Enhanced CVD (PECVD), and thermal anneal. The polysilicon emitter 108 may have a
`
`sheet resistance of 100 O/sq, and a thickness of 1000 to 2000 Angstroms. The tunnel
`
`oxide layer 107 may comprisesilicon dioxide thermally grown to a thickness of about 10
`
`to 50 Angstroms on the backside surface of the substrate 101. A metal contact 110
`
`electrically connects to the polysilicon emitter 108 through contact holes 123 formed
`
`through a dielectric comprising a silicon dioxide layer 109. The metal contact 110
`
`provides a positive polarity terminal to allow an external electrical circuit to be coupled
`
`to and be powered by the solar cell 100. The silicon dioxide layer 109 provides
`
`electrical isolation and allows the metal contact 110 to serve as an infrared reflecting
`
`layer for increased solar radiation collection.
`
`In one embodiment, the metal contact 110
`
`comprisessilver having a conductance of about 5-25 mQ.cm anda thickness of about
`
`20
`
`15-35um.
`
`On the front side of the solar cell 100, the metal contact 102 electrically connects
`
`to the region 106 through a contact hole 120 formed through the silicon nitride layer
`
`103. The metal contact 102 provides a negative polarity terminal to allow an external
`
`-5-
`
`
`
`Attorney Docket No. SKYW00056-1C US
`
`electrical circuit to be coupled to and be poweredbythe solar cell 100.
`
`In one
`
`embodiment, the metal contact 102 comprisessilver having a sheet resistance of about
`
`5mQ.cm and a thickness of about 15um. The pitch between adjacent metal contacts
`
`102 may be about 1 to 4mm.
`
`In one embodiment, the metal contacts 102 are spaced
`
`at 400 to 1000 um along each metal contact 102 (see FIG. 2).
`
`In the example of FIG. 1, the edge isolation trench 111 is formed through the
`
`silicon dioxide layer 109, the polysilicon emitter 108, and a portion of the substrate 101
`
`to provide edge electrical isolation.
`
`FIG. 2 is a plan view schematically showing the front side of the solar cell 100.
`
`In
`
`the example of FIG. 2, two bus bars 201 run parallel on the front side of the substrate
`
`101. The contact holes 120, in which the metal contacts 102 are formed, may each
`
`have a diameter of about 50 to 200 um. A plurality of metal contacts 102 is formed
`
`perpendicular to the bus bars 201. Each metal contact 102 may have a width of about
`
`60-120um.
`
`FIG. 3 is a plan view schematically showing the backside of the solar cell 100.
`
`In
`
`the example of FIG. 3, two bus bars 301, which are electrically coupled to metal
`
`contacts 110, run parallel on the backside.
`
`In practice, the bus bars 201 and 301 will be
`
`electrically connected to corresponding bus bars of adjacent solar cells to form an array
`
`of solar cells.
`
`20
`
`Solar cells have gained wide acceptance among energy consumers asa viable
`
`renewable energy source. Still, to be competitive with other energy sources, a solar cell
`
`manufacturer must be able to fabricate an efficient solar cell at relatively low cost. With
`
`
`
`Attorney Docket No. SKYW00056-1C US
`
`this goal in mind, a process for manufacturing the solar cell 100 is now discussed with
`
`reference to FIGS. 4A-4M.
`
`FIG. 4, which comprises FIGS. 4A-4M, schematically illustrates the fabrication of
`
`the solar cell 100 in accordance with an embodiment of the present invention.
`
`In FIG. 4A, an N-typesilicon substrate 101 is prepared for processing into a solar
`
`cell by undergoing a damage etch step. The substrate 101 is in wafer form in this
`
`example, and is thus typically received with damaged surfaces due to the sawing
`
`process used by the wafer vendor to slice the substrate 101 from its ingot. The
`
`substrate 101 may be about 100 to 200 microns thick as received from the wafer
`
`vendor.
`
`In one embodiment, the damage etch step involves removal of about 10 to 20
`
`uum from eachside of the substrate 101 using a wet etch process comprising potassium
`
`hydroxide. The damage etch step mayalsoinclude cleaning of the substrate 101 to
`
`remove metal contamination.
`
`In FIG. 4B, tunnel oxides 402 and 107 are formed on the front and back surfaces,
`
`respectively, of the substrate 101. The tunnel oxides 402 and 107 may comprisesilicon
`
`dioxide thermally grownto a thickness of about 10 to 50 Angstroms on the surfaces of
`
`the N-typesilicon substrate 101. A layer of polysilicon is then formed on the tunnel
`
`oxides 402 and 107 to form the polysilicon layer 401 and the polysilicon emitter 108,
`
`respectively. Each of the polysilicon layer 401 and the polysilicon emitter 108 may be
`
`20
`
`formed to a thickness of about 1000 to 2000 Angstroms by CVD.
`
`In FIG. 4C, a P-type dopant source 461 is formed on the polysilicon emitter 108.
`
`Asits name implies, the P-type dopant source 461 provides a source of P-type dopants
`
`for diffusion into the polysilicon emitter 108 in a subsequent dopant drive-in step. A
`
`-7-
`
`
`
`Attorney Docket No. SKYW00056-1C US
`
`dielectric capping layer 462 is formed on the P-type dopant source 461 to prevent
`
`dopants from escaping from the backside of the solar cell during the drive-in step.
`
`In
`
`one embodiment, the P-type dopant source comprises BSG (borosilicate glass)
`
`deposited to a thickness of about 500 to 1000 Angstroms by atmospheric pressure CVD
`
`(APCVD) and has a dopant concentration of 5 to 10% by weight, while the capping layer
`
`462 comprises undopedsilicon dioxide formed to a thickness of about 2000 to 3000
`
`Angstroms also by APCVD.
`
`In FIG. 4D, the edge isolation trench 111 is formed near the edge of the
`
`substrate 101 on the backside. The trench 111 is relatively shallow (e.g., 10 um deep
`
`into the substrate 101) and provides edge electrical isolation.
`
`In one embodiment, the
`
`trench 111 is formed by cutting through the capping layer 462, the P-type dopant source
`
`461, the polysilicon emitter 108, the tunnel oxide 107, and into a shallow portion of the
`
`substrate 101 using a laser.
`
`In FIG. 4E, exposed regions on the front surface of the substrate 101 is randomly
`
`textured to form the textured surface 113.
`
`In one embodiment, the front surface of the
`
`substrate 101 is textured with random pyramids using a wet etch process comprising
`
`potassium hydroxide and isopropyl alcohol.
`
`In FIG. 4F, an N-type dopant source 412 is formed on regions of the textured
`
`surface 113 where contact holes 120 (see FIG. 1) will be subsequently formed to allow
`
`20
`
`subsequently formed metal contacts 102 to electrically connect to the substrate 101. As
`
`its name implies, the N-type dopant source 412 provides a source of N-type dopants for
`
`diffusion into the front side of the substrate 101.
`
`In one embodiment, the N-type dopant
`
`
`
`Attorney Docket No. SKYW00056-1C US
`
`source 412 is formed byinkjet printing the dopant material directly onto the substrate
`
`101.
`
`In one embodiment, the N-type dopant source 412 comprisessilicon dioxide
`
`doped with phosphorus. Only one N-type dopant source 412 is shown in FIG. 4F for
`
`clarity of illustration.
`
`In practice, there are several dot-shaped N-type dopant sources
`
`412, one for each region where a contact hole 120 is to be formed (see FIG. 2). This
`
`allows formation of several dot shaped N-type doped regions 106 (see FIG. 1) after a
`
`subsequently performed drive-in step now discussed with reference to FIG. 4G.
`
`In FIG. 4G, a dopant drive-in step is performedto diffuse N-type dopants from
`
`the N-type dopant source 412 into the substrate 101 to form the N-type dope region
`
`106, to diffuse P-type dopants from the P-type dopant source 461 to the polysilicon
`
`emitter 108, and to diffuse N-type dopants into the front side of the substrate 101 to
`
`form the N-type doped region 105. Silicon dioxide layer 109 represents layers 461 and
`
`462 after the drive-in step. The polysilicon emitter 108 also becomes a P-type doped
`
`layer after the drive-in step. The N-type doped region 105 may be formed by exposing
`
`the sample of FIG. 4G to phosphorus in a diffusion furnace, for example. The use of the
`
`N-type dopant source 412 allows for a more controlled and concentrated N-type
`
`diffusion to the N-type doped region 106. The thin thermal silicon dioxide layer 124 may
`
`be grown on the textured surface 113 during the drive-in process.
`
`20
`
`The drive-in step to dopethe polysilicon emitter 108 on the backside and to form
`
`the N-type doped regions 105 and 106 on the front side may be formed in-situ, which in
`
`the context of the present disclosure means a single manual (i.e., by fabrication
`
`personnel) loading of the substrate 101 in a furnace or other single chamber or multi-
`
`-9-
`
`
`
`Attorney Docket No. SKYW00056-1C US
`
`chamber processing tool.
`
`In one embodiment, the drive-in step is performed in a
`
`diffusion furnace. The preceding sequence of steps leading to the drive-in step allows
`
`for in-situ diffusion, which advantageously helps in lowering fabrication cost.
`
`It is to be noted that the step of using an N-type dopant source 412 to diffuse
`
`dopants into the N-type doped region 106 may be omitted in some applications. Thatis,
`
`in an alternative process, the formation of the N-type dopant source 412 in FIG. 4F may
`
`be omitted.
`
`In that case, the N-type doped regions 105 and 106 will be both doped by
`
`introduction of an N-type dopantin the diffusion furnace during the drive-in step. All
`
`other process steps disclosed herein remain essentially the same.
`
`In FIG. 4H, the antireflective coating of silicon nitride layer 103 is formed over the
`
`textured surface 113 after removal of the N-type dopant source 412. Besides being an
`
`antireflective coating, the silicon nitride layer 103 also advantageously serves as a
`
`dielectric, enabling the selective contacts to be formed on the front surface to reduce
`
`front surface recombination. The silicon nitride layer 103 may be formedto a thickness
`
`of about 450 Angstroms by PECVD, for example.
`
`In FIG. 41, a front contact mask 420 is formed on thesilicon nitride layer 103 to
`
`create a pattern 421 defining the contact holes 120 (see FIG. 1). The mask 420 may
`
`comprise an acid resistance organic material, such as a resist, and formed using a
`
`printing process, such as screen printing or inkjet printing.
`
`20
`
`In FIG. 4J, a back contact mask 422 is formed on the silicon dioxide layer 109 to
`
`create patterns 423 defining the contact holes 123 (see FIG. 1). Similar to the mask
`
`420, the mask 422 may comprise an organic material formed using a printing process.
`
`-10-
`
`
`
`Attorney Docket No. SKYW00056-1C US
`
`In FIG. 4K, contact holes 120 and 123 are formed by removing exposed portions
`
`of the silicon nitride layer 103 and the silicon dioxide 109 in a contact etch step.
`
`In one
`
`embodiment, the contact holes 120 are formed by using a selective etch process that
`
`removes exposed portions of the silicon nitride layer 103 and stops on the substrate
`
`101. The same etch process removes exposed portions of the silicon dioxide 109 and
`
`stops on the polysilicon emitter 108.
`
`In one embodiment, the etch process comprises a
`
`BOE (buffered oxide etch).
`
`In FIG. 4L, the metal contact 110 is formed on the silicon dioxide layer 109to fill
`
`the contact holes 123 and makeelectrical connection to the polysilicon emitter 108.
`
`The metal contact 110 may be formed using a printing process. The metal contact 110
`
`may comprise silver, which, together with the silicon dioxide layer 109, makes an
`
`excellent backside infrared reflector. Other metals may also be used as a metal contact
`
`110, such as aluminum, for example.
`
`In FIG. 4M, the metal contact 120 is formed onthe silicon nitride layer 103 tofill
`
`the contact holes 120 and makeelectrical connection to the substrate 101. The metal
`
`contact 120 may comprise silver and formed using a printing process.
`
`Formation of the metal contacts 110 and 102 may be followed bya firing step.
`
`Thefiring step is applicable when using screen printed silver paste as metal contacts,
`
`but not when using other processes or metals. The solar cell 100 may then be visually
`
`20
`
`inspected and tested.
`
`While specific embodiments of the present invention have been provided, it is to
`
`be understood that these embodimentsarefor illustration purposes and notlimiting.
`
`-11-
`
`
`
`Attorney Docket No. SKYW00056-1C US
`
`Many additional embodimentswill be apparent to persons of ordinary skill in the art
`
`reading this disclosure.
`
`-12-
`
`
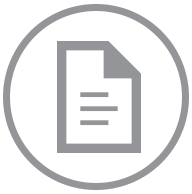
Accessing this document will incur an additional charge of $.
After purchase, you can access this document again without charge.
Accept $ ChargeStill Working On It
This document is taking longer than usual to download. This can happen if we need to contact the court directly to obtain the document and their servers are running slowly.
Give it another minute or two to complete, and then try the refresh button.
A few More Minutes ... Still Working
It can take up to 5 minutes for us to download a document if the court servers are running slowly.
Thank you for your continued patience.
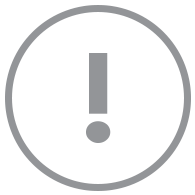
This document could not be displayed.
We could not find this document within its docket. Please go back to the docket page and check the link. If that does not work, go back to the docket and refresh it to pull the newest information.
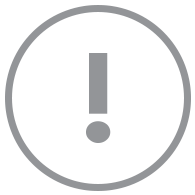
Your account does not support viewing this document.
You need a Paid Account to view this document. Click here to change your account type.
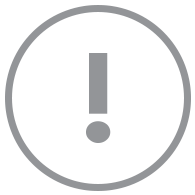
Your account does not support viewing this document.
Set your membership
status to view this document.
With a Docket Alarm membership, you'll
get a whole lot more, including:
- Up-to-date information for this case.
- Email alerts whenever there is an update.
- Full text search for other cases.
- Get email alerts whenever a new case matches your search.
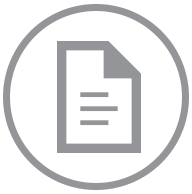
One Moment Please
The filing “” is large (MB) and is being downloaded.
Please refresh this page in a few minutes to see if the filing has been downloaded. The filing will also be emailed to you when the download completes.
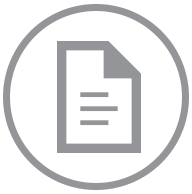
Your document is on its way!
If you do not receive the document in five minutes, contact support at support@docketalarm.com.
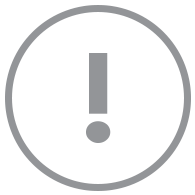
Sealed Document
We are unable to display this document, it may be under a court ordered seal.
If you have proper credentials to access the file, you may proceed directly to the court's system using your government issued username and password.
Access Government Site