`
`CROSS-REFERENCE TO RELATED APPLICATION
`
`This application claims priority to and the benefit of Korean Patent Application No.
`
`10-2021-0107501, filed on August 13, 2021, the disclosure of which is incorporated herein by
`
`reference inits entirety.
`
`10
`
`1.
`
`Field of the Invention
`
`BACKGROUND
`
`The present invention relates to a wafer processing method, and moreparticularly, to
`
`a wafer processing method capable of shortening a wafer part processing time and improving
`
`wafer part processing and cleaning performance.
`
`15
`
`2.
`
`Discussion of Related Art
`
`In general, in a semiconductor process, an etching process of etching wafer parts, a
`
`singulation process of sawing the waferparts into a plurality of dies, and a cleaning process of
`
`cleaning the wafer parts are performed. A wafer processing apparatus is used in the wafer
`
`etching process or the cleaning process.
`
`20
`
`The wafer processing apparatus includes a rotary table which is rotatably installed
`
`and on which a wafer part is mounted, and a sealing ring coupled to an edgearea of the rotary
`
`table in a ring shape. A processing solution is supplied onto the wafer part mounted on the
`
`rotary table while the rotary table rotates.
`
`A background technique of the present
`
`invention is disclosed in Korean Patent
`
`25
`
`Publication No. 10-2016-0122067 (published on October 21, 2016, and titled “Wafer
`
`processing apparatus andsealing ring for wafer processing apparatus’).
`
`SUMMARYOF THE INVENTION
`
`AJU-0021-ZS
`
`1
`
`
`
`The present invention is directed to providing a wafer processing method capable of
`
`shortening a wafer part processing time and improving wafer part processing and cleaning
`
`performance.
`
`According to an aspect of the present invention, there is provided a wafer processing
`
`method includes mounting a wafer part on a chuck table, loading a ring cover unit on the
`
`chuck table to restrain the wafer part to the chuck table, spraying, by a spray suction arm
`
`module, a processing solution onto the wafer part and suctioning, by the spray suction arm
`
`module, foreign materials floating on the processing solution, unloading the ring cover unit
`
`from the chuck table, and spraying, by a spray arm module, a cleaning solution onto the wafer
`
`10
`
`part to clean the waferpart..
`
`The mounting of the wafer part on the chuck table may include holding, by a transfer
`
`device, the wafer part transferred from a second transfer module, and lowering the transfer
`
`device to mount the wafer part on the chucktable.
`
`The loading of the ring cover unit on the chuck table to restrain the wafer part to the
`
`15
`
`chuck table may include restraining the ring cover unit to a holding unit ofa tilting device,
`
`coupling, by the tilting device,
`
`the ring cover unit to an upper side of the chuck table,
`
`restraining, by a chucking module of the chuck table, the ring cover unit, releasing, by the
`
`holding unit, restraint of the ring cover unit, and moving thetilting device outward from the
`
`chucktable.
`
`20
`
`The spraying of, by the spray suction arm module, the processing solution onto the
`
`wafer part and the suctioning of, by the spray suction arm module, the foreign materials from
`
`the processing solution may include moving the spray suction arm module to be positioned
`
`above the wafer part, swinging the spray suction arm module within a set angle range to spray
`
`the processing solution onto the wafer part, and suctioning, by the spray suction arm module,
`
`25
`
`the foreign materials within a certain range.
`
`The unloading of the ring cover unit from the chuck table may include rotating a
`
`tilting device to be positioned above the ring cover unit, restraining, by a holding unit of the
`
`tilting device, the ring cover unit, releasing, by a chucking module of the chucktable, restraint
`
`of the ring cover unit, and rotating, by the tilting device, the ring cover unit to movethe ring
`
`30
`
`cover unit outward from the chucktable.
`
`AJU-0021-ZS
`
`2
`
`
`
`The spraying of, by the spray arm module, the cleaning solution onto the wafer part to
`
`clean the wafer part may include moving the spray arm module to be positioned above the
`
`wafer part, and swinging the spray arm module within a set angle range to spray the cleaning
`
`solution onto the wafer part to perform final—cleaning on the waferpart.
`
`The wafer processing method may further include, before the unloading of the ring
`
`cover unit from the chucktable, spraying, by the spray arm module, the cleaning solution onto
`
`the wafer part to perform intermediate cleaning on the waferpart.
`
`The spraying of, by the spray arm module, the cleaning solution onto the wafer part to
`
`perform the intermediate cleaning on the wafer part may include moving the spray suction
`
`10
`
`arm module outward from the wafer part, moving the spray arm module to be positioned
`
`above the wafer part, and swinging the spray arm module within a set angle range to spray the
`
`cleaning solution onto the waferpart.
`
`The wafer processing method mayfurther include, after the spraying of, by the spray
`
`arm module, the cleaning solution onto the wafer part to perform the intermediate cleaning on
`
`15
`
`the wafer part, primarily drying the wafer part on the chucktable.
`
`The primarily drying of the wafer part on the chuck table may include moving the
`
`spray arm module outward from the chuck table and rotating the chuck table to primarily dry
`
`the waferpart.
`
`The wafer processing method may include, after the spraying of, by the spray arm
`
`20
`
`module, the cleaning solution onto the wafer part to clean the wafer part, secondarily drying
`
`the wafer part on the chucktable.
`
`The secondarily drying of the wafer part on the chuck table may include moving the
`
`spray arm module outward from the chuck table and rotating the chuck table to secondarily
`
`dry the waferpart.
`
`25
`
`BRIEF DESCRIPTION OF THE DRAWINGS
`
`FIG. 1 is a schematic plan view illustrating a wafer part according to one embodiment
`
`of the present invention.
`
`30
`
`FIG. 2 is a schematic block diagram illustrating a wafer processing apparatus
`
`according to one embodimentof the present invention.
`
`AJU-0021-ZS
`
`3
`
`
`
`FIGS. 3A AND 3B show schematic plan views illustrating a vision aligner in the
`
`wafer processing apparatus according to one embodiment of the present invention.
`
`FIG.4 is a schematic plan view illustrating a first processing chamber and a second
`
`processing chamberin the wafer processing apparatus according to one embodimentof the
`
`present invention.
`
`FIG. 5 is a schematic side view illustrating a transfer device in the wafer processing
`
`apparatus according to one embodimentof the present invention.
`
`FIG.6 is a schematic plan view illustrating the transfer device in the wafer processing
`
`apparatus according to one embodimentof the present invention.
`
`10
`
`FIG.7 is a schematic side view illustrating a gripper unit in the transfer device of the
`
`wafer processing apparatus according to one embodiment of the present invention.
`
`FIG. 8 is a schematic side view illustrating a state in which the gripper unit is drawn
`
`out of the transfer device of the wafer processing apparatus according to one embodiment of
`
`the present invention.
`
`15
`
`FIG. 9 is a schematic side view illustrating a tilting device in the wafer processing
`
`apparatus according to one embodimentof the present invention.
`
`FIG. 10 is a schematic side view illustrating a state in which a holding unit is lowered
`
`in the tilting device of the wafer processing apparatus according to one embodiment of the
`
`present invention.
`
`20
`
`FIG. 11 is a schematic plan view illustrating the holding unit of the tilting device in
`
`the wafer processing apparatus according to one embodimentof the present invention.
`
`FIG. 12 is a schematic rear view of the holding unit of the tilting device in the wafer
`
`processing apparatus according to one embodimentof the present invention.
`
`FIG. 13 is a schematic enlarged view illustrating the holding unit of the tilting device
`
`25
`
`in the wafer processing apparatus according to one embodimentof the present invention.
`
`FIG. 14 is a schematic cross-sectional view illustrating a chuck table device in the
`
`wafer processing apparatus according to one embodiment of the present invention.
`
`FIG. 15 is a schematic plan view illustrating a chucking module of the chuck table
`
`device in the wafer processing apparatus according to one embodiment of the present
`
`30
`
`invention.
`
`AJU-0021-ZS
`
`4
`
`
`
`FIG. 16 is a schematic enlarged view illustrating the chucking module in the chuck
`
`table device of the wafer processing apparatus according to one embodiment of the present
`
`invention.
`
`FIG. 17 is a schematic cross-sectional view illustrating a state in which the chucking
`
`module restrains a ring cover unit in the chuck table device of the wafer processing apparatus
`
`according to one embodiment of the present invention.
`
`FIG. 18 is a schematic plan view illustrating a processing solution spray device of the
`
`wafer processing apparatus according to one embodiment of the present invention.
`
`FIG. 19 is a schematic perspective view illustrating a spray arm module in the
`
`10
`
`processing solution spray device of the wafer processing apparatus according to one
`
`embodimentof the present invention.
`
`FIG. 20 is a schematic enlarged view illustrating a first spray nozzle unit of the spray
`
`arm module in the processing solution spray device of the wafer processing apparatus
`
`according to one embodiment of the present invention.
`
`15
`
`FIG. 21 is a schematic enlarged view illustrating a second spray nozzle unit and a
`
`second suction nozzle unit of a spray suction arm module in the processing solution spray
`
`device of the wafer processing apparatus according to one embodiment of the present
`
`invention.
`
`FIG. 22 is a schematic view illustrating a suction tank connected to the second
`
`20
`
`suction nozzle unit of the spray suction arm module in the processing solution spray device of
`
`the wafer processing apparatus according to one embodimentof the present invention.
`
`FIGS. 23A TO 23H show schematic viewsillustrating a wafer processing method
`
`according to one embodiment of the present invention.
`
`FIG. 24 is a schematic flowchart illustrating the wafer processing method according
`
`25
`
`to one embodimentof the present invention.
`
`DETAILED DESCRIPTION OF EXEMPLARY EMBODIMENTS
`
`Hereinafter, embodiments of a wafer processing method according to the present
`
`30
`
`invention will be described with reference to the accompanying drawings.
`
`In describing the
`
`wafer processing method, thicknesses of lines or sizes of components shown in the drawings
`
`AJU-0021-ZS
`
`5
`
`
`
`may be exaggerated for the sake of convenience and clarity in description.
`
`Furthermore,
`
`terminologies used herein are defined by taking functions of the present invention into
`
`account and may be changed according to a custom or the intent of a user or an operator.
`
`Accordingly, the terminologies should be defined based on the following overall description
`
`of the present specification.
`
`FIG. 1 is a schematic plan view illustrating a wafer part according to one embodiment
`
`of the present invention.
`
`FIG. 2 is a schematic block diagram illustrating a wafer processing
`
`apparatus according to one embodiment of the present invention.
`
`FIGS. 3A AND 3B show
`
`schematic plan viewsillustrating a vision aligner in the wafer processing apparatus according
`
`10
`
`to one embodimentof the present invention.
`
`Referring to FIGS.
`
`1
`
`to 3, a wafer processing apparatus 1 according to one
`
`embodiment of the present invention processes a ring frame wafer part 10. The ring frame
`
`wafer part 10 etched in an etching process is sawn in the form of a matrix in a singulation
`
`process. The ring frame wafer part 10 includes a wafer 11 including a plurality of dies sawn
`
`15
`
`and arranged in the form of a matrix, an adhesive sheet 12 to which the wafer 11 is attached,
`
`and a retainer ring portion 13 connected to a circumferential portion of the adhesive sheet 12
`
`to tightly support the adhesive sheet 12. The adhesive sheet 12 is made of a material that is
`
`stretchable or contractible in a horizontal direction. The adhesive sheet 12 is pulled tight by
`
`the retainer ring portion 13 so that the plurality of dies are positioned and fixed, and the die,
`
`20
`
`which is a thin plate, maintains a flat plate shape. Hereinafter, the ring frame wafer part 10
`
`will be referred to as a wafer part 10.
`
`A wafer cassette 20 is a front opening unified pod (FOUP) which has an internal
`
`space sealed from the outside, in which a plurality of wafer parts 10 are loaded, and which,
`
`along with the wafer part 10, moves between unit process apparatuses. The wafer cassette
`
`25
`
`20 transferred to the unit process apparatus is mounted on an upper surface of a load port
`
`module (not shown) disposed at one side of the unit process apparatus, and while an internal
`
`space of the wafer cassette 20 is sealed from the outside, a wafer part cassette door (not
`
`shown)
`
`is opened.
`
`Accordingly,
`
`the wafer part
`
`10 can be prevented from being
`
`contaminated from an external environment and can be moved between the unit process
`
`30
`
`apparatuses.
`
`AJU-0021-ZS
`
`6
`
`
`
`The wafer part 10 loaded in the wafer cassette 20 is adsorbed by a first transfer
`
`module 50 and loaded on a buffer unit 30. The buffer unit 30 includes two pre-slots (not
`
`shown) and two post-slots (not shown). As the first
`
`transfer module 50, a vacuum
`
`adsorption robot for adsorbing the wafer part 10 using a vacuum may be applied.
`
`The wafer part 10 loaded on the buffer unit 30 is mounted on a vision aligner 40 by
`
`the first transfer module 50. The vision aligner 40 includes an aligner table 41 on which the
`
`wafer part 10 is mounted, and a vision unit (not shown) which reads the wafer part 10 by
`
`irradiating light onto the aligner table 41. The vision aligner 40 may rotate at an angle of
`
`about 4° with respect to a center of the aligner table 41 and may laterally move to a distance
`
`10
`
`of about 7 mm with respect to the center of the aligner table 41. The vision unit may read a
`
`position of the wafer part 10 and a center of the wafer 11 to align the position of the wafer
`
`part 10.
`
`In this case, the vision unit reads whether the center of the wafer 11 and a center of
`
`the retainer ring portion 13 match each other and aligns the wafer part 10 such that the center
`
`of the wafer 11 is aligned at a correct position.
`
`15
`
`The wafer part 10 aligned in the vision aligner 40 is loaded into a first processing
`
`chamber70 and a second processing chamber 80 by a second transfer module 60.
`
`In thefirst
`
`processing chamber70, a processing solution is sprayed onto the wafer part 10 to process the
`
`wafer part 10. A plurality of second processing chambers 80 are installed.
`
`In the second
`
`processing chamber 80, a processing solution is sprayed onto the wafer part 10, and
`
`20
`
`simultaneously, foreign materials floating on an upper side of the processing solution are
`
`suctioned to process the wafer part 10.
`
`FIG. 4 is a schematic plan view illustrating the first processing chamber and the
`
`second processing chamberin the wafer processing apparatus according to one embodiment
`
`of the present invention.
`
`25
`
`Referring to FIG. 4, an ionizer 102, a transfer device 100, a tilting device 200, a
`
`chuck table device 300, a spray device 400, and a suction device 500 are installed in the first
`
`processing chamber 70.
`
`Anionizer 102, a transfer device 100, a tilting device 200, a chuck
`
`table device 300, and a spray device 400are installed in the second processing chamber80.
`
`The ionizer 102 is installed above each of the first processing chamber 70 and the
`
`30
`
`second processing chamber 80. The ionizer 102 removesstatic electricity generated during a
`
`processing process and a non-processing process of the wafer part 10.
`
`Since the ionizer 102
`
`AJU-0021-ZS
`
`1
`
`
`
`prevents static electricity from being generated on the wafer part 10 and inside the first
`
`processing chamber 70 and the second processing chamber 80, foreign materials can be
`
`prevented from being reattached to the wafer part 10 by static electricity.
`
`When air as a supply gas is supplied to the ionizer 102 and deionized water (DI
`
`water) as a cleaning solution is supplied, positive ions and negative ions ionized through the
`
`ionizer 102, along with the cleaning solution, may be sprayed onto the wafer part 10.
`
`Before DI water including positive ions and negative ions is sprayed onto the wafer
`
`part 10, an electrostatic potential of the wafer part 10 was measured to be approximately 3.6
`
`kV. On the other hand, after DI water including positive ions and negative ions is sprayed
`
`10
`
`onto the wafer part 10, the electrostatic potential was measured to be in a range of about -0.10
`
`kV to -0.17 kV.
`
`Theelectrostatic potential of such a negative voltage causes an amount of
`
`positive ions to be increased by the ionizer 102, thereby controlling the static electricity of the
`
`wafer part 10 to be close to “zero” whichis an ideal value.
`
`FIG. 5 is a schematic side view illustrating the transfer device in the wafer processing
`
`15
`
`apparatus according to one embodimentof the present invention.
`
`FIG. 6 is a schematic plan
`
`view illustrating the transfer device in the wafer processing apparatus according to one
`
`embodiment of the present invention.
`
`FIG. 7 is a schematic side view illustrating a gripper
`
`unit in the transfer device of the wafer processing apparatus according to one embodimentof
`
`the present invention.
`
`FIG. 8 is a schematic side view illustrating a state in which the
`
`20
`
`gripper unit is drawn out of the transfer device of the wafer processing apparatus according to
`
`one embodiment of the present invention.
`
`Referring to FIGS. 5 to 8, the transfer device 100 is installed at both sides of the
`
`chuck table device 300. The transfer device 100 mounts the wafer part 10 transferred from
`
`the second transfer module 60 on the chuck table device 300.
`
`25
`
`The transfer device 100 includesa lifting unit 120, a transfer unit 130, and a gripper
`
`unit 140.
`
`The lifting unit 120 is installed outside a chuck table 320 and 330. One pair of
`
`lifting units 120 are installed at both sides of the chuck table 320 and 330 in a radial direction.
`
`Thelifting unit 120 is installed under a base unit 110.
`
`Asthelifting unit 120, any type such
`
`30
`
`as a ball screw type, a linear motor types, or a belt driving type may be applied.
`
`AJU-0021-ZS
`
`8
`
`
`
`The transfer unit 130 is connected to the lifting unit 120 to be lifted or lowered by the
`
`lifting unit 120 and is disposed outside the chuck table 320 and 330. The transfer unit 130 is
`
`installed at each of the lifting units 120. The transfer unit 130 is installed above the base unit
`
`110.
`
`The gripper unit 140 is reciprocally installed in the transfer unit 130 to hold or place
`
`the wafer part 10. The gripper unit 140 is installed in each of one pair of transfer units 130.
`
`Onepair of gripper units 140 support both sides of a ring frame portion 15 of the wafer part
`
`10. The gripper unit 140 receives the wafer part 10 transferred by the second transfer
`
`module 60 andis lowered by the lifting unit 120 to mount the gripper unit 140 on the chuck
`
`10
`
`table 320 and 330.
`
`Since the lifting unit 120 and the transfer unit 130 are disposed outside the chuck
`
`table 320 and 330, and the gripper unit 140 is disposed vertically parallel to the lifting unit
`
`120 and the transfer unit 130, it is possible to considerably reduce an installation space of the
`
`gripper unit 140 and a movement path of the gripper unit 140. Accordingly, even in a
`
`15
`
`narrow space, the wafer part 10 can be received from the second transfer module 60 and
`
`mounted on the chuck table 320 and 330, and the processed wafer part 10 can be unloaded
`
`from the chuck table 320 and 330.
`
`Thelifting unit 120 includesa lifting arm driving part 122 disposed underthe transfer
`
`unit 130, a power transmission part 123 connected to the lifting arm driving part 122, and a
`
`20
`
`linear guide part 124 connected to the power transmission part 123 to lift or lower the transfer
`
`unit 130.
`
`Thelifting arm driving part 122 may be disposed outside a case unit 121, and the
`
`power transmission part 123 and the linear guide part 124 may be disposed inside the case
`
`unit 121. When the lifting arm driving part 122 transmits power to the power transmission
`
`part 123, the linear guide part 124 maybe lifted or lowered in the case unit 121 to vertically
`
`25
`
`movethe transfer unit 130.
`
`A motor part may be applied as the lifting arm driving part 122.
`
`The power
`
`transmission part 123 may beaball screw rotated by the lifting arm driving part 122.
`
`The linear guide part 124 includes fixed guide portions 125 vertically disposed in
`
`parallel on the lifting arm driving part 122, a moving guide portion 126 coupled to the fixed
`
`30
`
`guide portion 125 to be lifted or lowered and connected to the power transmission part 123 to
`
`be movable by the powertransmission part 123, and a lifting rod 127 connected to the moving
`
`AJU-0021-ZS
`
`9
`
`
`
`guide portion and the transfer unit 130. The fixed guide portions 125 may be fixed rail
`
`portions vertically disposed in parallel inside the case unit 121. The moving guide portion
`
`126 maybe slidably coupled to the fixed guide portion 125.
`
`Thelifting rod 127 is installed
`
`in the case unit 121 to be vertically movable. When the lifting arm driving part 122 1s driven,
`
`the moving guide portion 126 is moved along the fixed guide portion 125, and thelifting rod
`
`127 is moved by the moving guide portion 126. Accordingly, a vertical stroke of the transfer
`
`unit 130 can be accurately controlled.
`
`The gripper unit 140 includes a gripper driving part 141, at least one pinion portion
`
`142, a plurality of rack gear portions 145 and 146, and a finger part 147.
`
`10
`
`The gripper driving part 141 is installed in the transfer unit 130. As the gripper
`
`driving part 141, any form such as a hydraulic cylinder, a ball screw, or a belt driving type
`
`motor part may be applied.
`
`At least one pinion portion 142is installed to be connected to the gripper driving part
`
`141 and be movable by the gripper driving part 141.
`
`15
`
`The plurality of rack gear portions 145 and 146 are installed to be engaged with the
`
`pinion portion 142 and are movedbythe rotation of the pinion portion 142. The rack gear
`
`portions 145 and 146 are movably installed at both sides of the pinion portion 142. When
`
`one pinion portion 142 is installed, two rack gear portions 145 and 146 maybe installed to be
`
`engaged with both sides of the pinion portion 142. When two pinion portions 142 are
`
`20
`
`installed, three rack gear portions 145 and 146 maybe installed to be engaged with both sides
`
`of the pinion portions 142.
`
`The finger part 147 extends from one rack gear portion 146 to hold the wafer part 10.
`
`In this case, the finger part 147 is installed at one rack gear portion 146 that is moved farthest
`
`from the transfer unit 130 whenthe gripper driving part 141 is driven.
`
`25
`
`Hereinafter, the gripper unit 140 in which one pinion portion 142 and two rack gear
`
`portions 145 and 146 areinstalled will be described.
`
`A pinion tooth portion (not shown) is formed on an outer surface of the pinion portion
`
`142.
`
`In this case, the plurality of rack gear portions 145 and 146 include a first rack gear
`
`portion 145 whichis installed to be engaged with the pinion portion 142 and reciprocates by
`
`30
`
`the rotation of pinion portion 142 and a second rack gear portion 146 whichis installed to be
`
`engaged with the pinion portion 142 and reciprocates by the rotation of the pinion portion 142
`
`AJU-0021-ZS
`
`10
`
`
`
`and from which the finger part 147 extends.
`
`In this case, the pinion portion 142 is disposed
`
`between the first rack gear portion 145 and the second rack gear portion 146.
`
`In addition,
`
`the pinion tooth portion of the pinion portion 142is installed to be engaged with an upperside
`
`of the first rack gear portion 145 and a lowerside of the second rack gear portion 146.
`
`The first rack gear portion 145 is fixed to a housing unit 131 of the transfer unit 130,
`
`and the second rack gear portion 146 is moved bythe translation and rotation of the pinion
`
`portion 142. When the gripper driving part 141 is driven,
`
`the pinion portion 142
`
`simultaneously performs translational motion and rotational motion along the first rack gear
`
`portion 145 so that the second rack gear portion 146 moves to a certain distance by the
`
`10
`
`translational motion and rotational motion of the pinion portion 142. Accordingly,
`
`the
`
`second rack gear portion 146 may moveto a distance about twice a distance by which the
`
`gripper driving part 141 movesthe pinion portion 142 so that a stroke of the finger part 147
`
`may considerably increase as compared with a stroke of the gripper driving part 141.
`
`The pinion portion 142 includes a slider portion 143 which is connected to the gripper
`
`15
`
`driving part 141 andis installed between the first rack gear portion 145 and the second rack
`
`gear portion 146 to reciprocate and a pinion gear portion 144 whichis rotatably coupled to the
`
`slider portion 143 and movesthe second rack gear portion 146 while moving together with the
`
`slider portion 143. The slider portion 143 is disposed parallel with the first rack gear portion
`
`146 and the second rack gear portion 146. When the gripper driving part 141 is driven, the
`
`20
`
`pinion gear portion 144 performs translational motion in a linear direction together with the
`
`slider portion 143 and is engaged with the first rack gear portion 145 to perform rotational
`
`motion.
`
`The gripper driving part 141 includes a cylinder 141a installed in the transfer unit 130,
`
`a moving rod 141b movably installed in the cylinder 141a, and a connection link portion 141¢
`
`25
`
`connected to the moving rod 141b and the slider portion 143. The connection link portion
`
`141c extends upward from the moving rod 141b of the cylinder 141a to be connected to the
`
`slider portion 143. The connection link portion 141c is moved in a linear direction by the
`
`moving rod 141b of the cylinder 141a. As the moving rod 141b is moved,the slider portion
`
`143 is moved.
`
`30
`
`The finger part 147 includes a vacuum adsorption part 148 which holds the wafer part
`
`10 through vacuum adsorption. Two or more vacuum adsorption parts 148 may be installed
`
`AJU-0021-ZS
`
`11
`
`
`
`in the finger part 147. The vacuum adsorption part 148 vacuum-adsorbs the ring frame
`
`portion 15 of the wafer part 10. A vacuum flow path (not shown) may be formed inside the
`
`finger part 147 to form a vacuum in the vacuum adsorption part 148.
`
`FIG. 9 is a schematic side view illustrating a tilting device in the wafer processing
`
`apparatus according to one embodimentof the present invention.
`
`FIG. 10 is a schematic side
`
`view illustrating a state in which a holding unit is lowered in the tilting device of the wafer
`
`processing apparatus according to one embodiment of the present invention.
`
`FIG. 11 is a
`
`schematic plan view illustrating the holding unit of the tilting device in the wafer processing
`
`apparatus according to one embodimentof the present invention.
`
`FIG. 12 is a schematic rear
`
`10
`
`view of the holding unit of the tilting device in the wafer processing apparatus according to
`
`one embodiment of the present invention.
`
`FIG. 13 is a schematic enlarged view illustrating
`
`the holding unit of the tilting device in the wafer processing apparatus according to one
`
`embodimentof the present invention.
`
`Referring to FIGS. 9 to 13, a tilting device 200 includes a tilting motor unit 210, a
`
`15
`
`tilting unit 220,a lifting unit 230, and a holding unit 240.
`
`The chuck table device 300is installed underthe tilting device 200. The chucktable
`
`device 300is installed to be rotatable by a chuck driving unit 310. As the chuck driving unit
`
`310, a motor unit such as a belt driving type or a gear driving type may be applied.
`
`The chuck table device 300 is installed on a rotating shaft 311 to be rotated by the
`
`20
`
`rotating shaft 311. A wafer part 10 is mounted on a vacuum chuckunit 330. A plurality of
`
`chuck pins 303 are installed to protrude from a circumferential portion of the vacuum chuck
`
`unit 330 and fix a ring coverunit 201.
`
`Thetilting device 200 holds the ring cover unit 201 and couples the ring cover unit
`
`201 to the chuck table device 300. A plurality of fixing holes 202 are formed in a lower
`
`25
`
`portion of a circumferential portion of the ring cover unit 201 such that the plurality of chuck
`
`pins 303 are inserted thererin when the ring cover unit 201 is seated on the chuck table device
`
`300.
`
`In addition, a plurality of restraining grooves 203 (see FIG. 17) are formed in an outer
`
`surface of the circumferential portion of the ring cover unit 201 to be held by the holding unit
`
`240. The plurality of restraining grooves 203 are formed to face locking pins 259 of the
`
`30
`
`holding unit 240. The ring cover unit 201 seals a circumferential portion of the wafer part
`
`10 mounted on the vacuum chuck unit 330 to prevent a processing solution from permeating
`
`AJU-0021-ZS
`
`12
`
`
`
`into the circumferential portion of the wafer part 10 and the ring cover unit 201 when the
`
`wafer part 10 is processed.
`
`The tilting unit 220 is rotatably connected to a tilting shaft 212 of the tilting motor
`
`unit 210. A tilting arm 222 is formed in thetilting unit 220 to be connected to the tilting
`
`shaft 212 of the tilting motor unit 210.
`
`Thetilting unit 220 maintainsa state of being erected
`
`upward in a standby state. The tilting motor unit 210 horizontally rotates the tilting unit 220
`
`to be positioned above the vacuum chuck unit 330 when the ring cover unit 201 is coupled to
`
`the circumferential portion of the vacuum chuck unit 330. A setting module (not shown)
`
`capable of setting the initial position of the holding unit 240 in a horizontal direction is
`
`10
`
`installed in the tilting unit 220 to horizontally position the holding unit 240 at a coupling
`
`position of the ring cover unit 201.
`
`installed in a central portion of the tilting unit 220.Alifting rod 233 ofthe lifting unit 230 is
`
`The lifting unit 230 is installed in the tilting unit 220. The lifting unit 230 is
`
`installed to pass through the central portion of the tilting unit 220. A plurality of lifting
`
`15
`
`guide portions are installed in the tilting unit 220 to guide the lifting and lowering of the
`
`lifting unit 230.
`
`The holding unit 240 is connected to the lifting unit 230 to be lifted or lowered by the
`
`lifting unit 230 and holds the ring cover unit 201. Before the wafer part 10 is mounted on
`
`the vacuum chuck unit 330, the holding unit 240 is positioned in a standby state in which the
`
`20
`
`holding unit 240 is vertically erected while holding the ring cover unit 201.
`
`When the wafer part 10 is mounted on the vacuum chuck unit 330, as the tilting
`
`motor unit 210 is driven, the tilting unit 220 and the holding unit 240 are horizontally rotated.
`
`Whenthe rotation of the tilting unit 220 and the holding unit 240 is completed, as thelifting
`
`unit 230 is driven, the holding unit 240 is moved underthe tilting unit 220.
`
`In this case, the
`
`25
`
`tilting unit 220 is not lowered together with the lifting unit 230 and maintains a horizontal
`
`state without any change.
`
`The holding unit 240 is lowered to mount the ring cover unit 201 on the vacuum
`
`chuck unit 330.
`
`In order to continuously maintain a state in which the ring cover unit 201 is
`
`coupled to the vacuum chuck unit 330 until the ring cover unit 201 is completely chucked to a
`
`30
`
`chucking module 350 (see FIG. 15) of the vacuum chuck unit 330, the holding unit 240
`
`maintainsa state of being loweredbythelifting unit 230.
`
`AJU-0021-ZS
`
`13
`
`
`
`When the coupling of the ring cover unit 201 to the vacuum chuck unit 330 is
`
`completed, as the lifting unit 230 is driven, the holding unit 240 is moved upward to come
`
`into contact with a lower side of the tilting unit 220 or to be slightly spaced apart therefrom.
`
`When the holding unit 240 is completely moved upward, as the tilting motor unit 210 is
`
`driven, the tilting unit 220 and the holding unit 240 are rotated to enter a standby state in
`
`whichthetilting unit 220 and the holding unit 240 are erected vertically or almostvertically.
`
`In order to correct a coupling deviation of the holding unit 240 when the holding unit
`
`240 couples the ring cover unit 201 to the vacuum chuck unit 330, position correction units
`
`260 are installed at the lifting unit 230 and the holding unit 240 to be floatable. The
`
`10
`
`coupling deviation refers to a deviation in which the locking pin 259 of the holding unit 240 is
`
`misaligned with the restraining groove 203 of the ring cover unit 201 when the holding unit
`
`240 and the ring cover unit 201 are coupled.
`
`The position correction unit 260 includes a thrust portion 261 and an elastic member
`
`268.
`
`15
`
`A plurality of thrust p
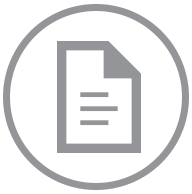
Accessing this document will incur an additional charge of $.
After purchase, you can access this document again without charge.
Accept $ ChargeStill Working On It
This document is taking longer than usual to download. This can happen if we need to contact the court directly to obtain the document and their servers are running slowly.
Give it another minute or two to complete, and then try the refresh button.
A few More Minutes ... Still Working
It can take up to 5 minutes for us to download a document if the court servers are running slowly.
Thank you for your continued patience.
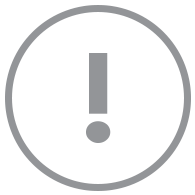
This document could not be displayed.
We could not find this document within its docket. Please go back to the docket page and check the link. If that does not work, go back to the docket and refresh it to pull the newest information.
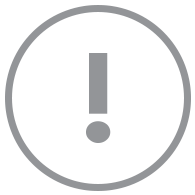
Your account does not support viewing this document.
You need a Paid Account to view this document. Click here to change your account type.
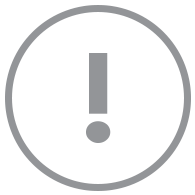
Your account does not support viewing this document.
Set your membership
status to view this document.
With a Docket Alarm membership, you'll
get a whole lot more, including:
- Up-to-date information for this case.
- Email alerts whenever there is an update.
- Full text search for other cases.
- Get email alerts whenever a new case matches your search.
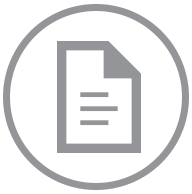
One Moment Please
The filing “” is large (MB) and is being downloaded.
Please refresh this page in a few minutes to see if the filing has been downloaded. The filing will also be emailed to you when the download completes.
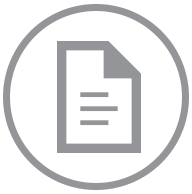
Your document is on its way!
If you do not receive the document in five minutes, contact support at support@docketalarm.com.
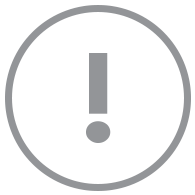
Sealed Document
We are unable to display this document, it may be under a court ordered seal.
If you have proper credentials to access the file, you may proceed directly to the court's system using your government issued username and password.
Access Government Site