`
`Espacenet- Bibliographic data
`
`“,—OouOOLidqnfe48oe5€2ooesosBooe&~x§&33ies“ateiuO£8==éeso425230°Oai,oeRB%-<£8qlql=“swté>I£6ZzZza.ieane£3:oh.
`
`
`‘meéOo2£98gsgg8@7Ben:Zz>ooooonscent?
`
`OTALDosSa_gernay—osete,
`cry,—_pidoete2823&o98agebete-§sir2GB8¢28&83233ites|waeage——=eeonZea¢a8aE9EfaZeoe|&2a=2565={5hedfnaak£03we£<qOoqeacqa,be6,60ht.os
`antefoeloa-ze4oe&.ys“4
`bee!ts£3-@°coO4oeff
`
`
` SSGSORexinIIo=2/8)AiiBeaSawnéJSohtlooestoSBNSByeeaeOmoeopenGePYCOAPLOOHcySo}See}8eryLLomaSsFredBEPeedeetCadse]Ol684|osOoeeeepeeee)eeeee)eyederpee)eyee)ONNaaees<SPSOOCSSOSASaasicwocoonbea=LACAN Boe|peBpOU23andlElotolECTcootafeMBageeseeeeeEl=S5.©SeSs
`oy2ROaegiseorssagogggmsisiroepeeBeBaedatSESaFOoaPatteOOBtgahadONECECEhlONOGuMEOENEao=eSpen@¥1eeoe) saagessa<i#4ehSeSeaaaUl)eS—é43OmedogaUSSySe—a2eeosSHBetTGee]BedeoRONryOFw]eOYLLLOaq¢2SOSuSONSNSeSasa!..tidy,|<n7—_-“7vetlti“gosEFSO)ONSOIGILia}1)co©os
`
`
`
`comEAHebne]9)OEEOS)eeeyzoan&QRgatSHOFOF)|caStbeeoeeo&BieobESSo)oyOSEe90)BeNYESSsSco
`
`gon£4*KoyMSEhakSaloF)cedotP|ge)SNEOG)nmFe=enhyOFseerFSLEETULACulIwlmelOHOTLESYMwoebesavaOWge)OdOeAAN)GdNeSeiwoeo8#EdesAUSNNNgsee9g65apeADECalCNOaCn]ONOEClCEClONYHTtyGEGaODa&aywh>ONelEEAGul
`
`
`nada
`QUEUEGLGulGlCulaEAgo=afren|oZzaeeeeeeeeeeeeeeeeeeeeOQ
`“en4mee8chdSaISIOSIOGiae2)ISSOSGndco)smamSoyOE)CESESE}weSESEE|er
`ennREooAloBBY2S82..,HoGY»-3=ea5aiinhie|
`
`
`
`https://worldwide.espacenet.com/publicationDetails/biblio? DB:
`
`EPODOC&II
`
`O&ND
`
`3&adjacent=true&locale
`
`en_EP&FT=D&date=20210416&CC...
`
`1/2
`
`
`
`
`
`Espacenet- Bibliographic data
`
`oe)
`ooGensaregDe
`
`%
`
`oe@Achews
`Spee.
`eral
`£o%aoage
`tAfnSee
`
`on
`
`tee
`
`oH
`
`ee
`
`ee)
`
`oh.
`
`Ack
`
`"Sta
`
`2022/10/25
`
`oh.3
`cs.
`ateoe
`
`
`
`teregeesre%Py,&isop02fe
`
`gecantfs
`
`wed
`
`https:
`
`Ical
`/worldwide.espacenet.com/publi
`
`ionti
`
`Details/bib|
`
`io?DB=
`
`EPODOC&II=0&ND:
`
`=3&adj
`
`acent=true&locale
`
`en_EP&FT=D&date=20210416&CC.
`
`2/2
`
`ssimOGthem@Megyboneeedrr
`
`EEEowy
`
`
`
`
`
`
`
`
`
`as) United States
`a2) Patent Application Publication 0) Pub. No.: US 2021/0335757 Al
` LIU et al. (43) Pub. Date: Oct. 28, 2021
`
`
`
`US 20210335757A1
`
`(54) METHOD FOR PACKAGING
`SEMICONDUCTOR, SEMICONDUCTOR
`PACKAGE STRUCTURE, AND PACKAGE
`
`(71) Applicant; CHANGXIN MEMORY
`TECHNOLOGIES, INC., Hefei (CN)
`
`(72)
`
`Inventors: Jie LIU, Hefei (CN); Zhan YING,
`Hefei (CN)
`
`(21) Appl. No.: 17/372,530
`
`(22) Filed:
`
`Jul. 12, 2021
`
`Related U.S. Application Data
`
`(63) Continuation of application No. PCT/CN2020/
`096254, filed on Aug. 14, 2020.
`
`(30)
`
`Foreign Application Priority Data
`
`Oct. 16, 2019
`
`(CN)ee 201910982076.1
`
`Publication Classification
`
`(51)
`
`Int. Ch
`HOIL 25/065
`HOIL 23/00
`
`(2006.01)
`(2006.01)
`
`(2006.01)
`(2006.01)
`
`HOIL 21/78
`HOIL 25/00
`(52) US. Cl.
`CPC vases HOLL 25/0657 (2013.01); HOLL 23/562
`(2013.01); HOLE 21/78 (2013.01): HOIL
`2225/06586 (2013.01); HOLL 2225/06513
`(2013.01); HOIL 2225/0654] (2013.01): HOIL
`2225/06548 (2013.01); HOLE 25/50 (2013.01)
`
`(57)
`
`ABSTRACT
`
`Embodiments provide a method for packaging a semicon-
`ductor, a semiconductor package structure, and a package.
`The packaging method includes: providing a substrate wafer
`having a first surface and a second surface arranged opposite
`to each other, the first surface having a pluralityof grooves,
`a plurality of electrically conductive pillars being provided
`at a bottom of the groove, and the electrically conductive
`pillar penetrating through the bottom of the groove to the
`second surface; providing a plurality of semiconductor die
`stacks; placing the semiconductor die stack in the groove;
`and filling an insulating dielectric in a gap between a
`sidewall of the groove and the semiconductor die stack to
`formaninsulating dielectric layer covering an upper surface
`of the semiconductor die stack to seal up the semiconductor
`die stack so as to form the semiconductor packagestructure.
`
`400A
`
`
`
`
`
`Patent Application Publication
`
`Oct. 28,2021 Sheet 1 of 6
`
`US 2021/0335757 Al
`
`
`
`
`Provide a sibsivate wafer having a first surface and a second suriace arranged
`
`~S10
`:
`opposite to cach other, the first surface having a plurality of grooves, a plurality of
`
`electrically conductive pillars being provided at a bottom of the groove, and the
`
`
`
`
` electrically conductive pillar penetrating through the groove tc the second surface Tf pee.
`
` Provide a pintality af semiconductordie stacks
`
`pene
`
`
`
`Place the semiconductor die stack in the groove, ap upper surface of the
`
`
`semsconductordie stack being lower thanor flush with an upper edge af the groove,
`
` and a bottom of the semiconductor die stack being electrically comnected to the
`
`
`electncally conductive pillar
`
`.
`»
`3
`e
`.
`.
`.
`:
`sexmiconductor die stack to forra an insulating dielectnec layer covering an upper
`surface of the semiconductor die stack to seal up the semiconductordie stack so as to
`form a semiconductor package structure
`
`Ful an insulating dielectric ia pap betweona sidewall of the groove and the
`
`
`.
`in
`Loy
`a
`oe
`.
`-
`Cover an upper sutface of the insulating dielectric layer and the Brst surface of
`the substrate wafer with a cover plate water
`
`ie) yo No
`
`O19
`ia
`pia
`
`a
`
`tA
`S14
`
`Dice the semiconductor package structure along the gap between the grooves to
`
`S15
` form. a phirality of packages independent of each other
`
`FIG I
`
`
`
`Patent Application Publication
`
`Oct. 28,2021 Sheet 2 of 6
`
`US 2021/0335757 Al
`
`200A
`
`200
`
` q
`
`
`2008
`
`200
`
`pn
`Z00C
`
`200A
`
`:
`
`\
`4
`204
`
`FIG 2A
`
`200€
`
`202
`
`3008
`
`
`
`Patent Application Publication
`
`Oct. 28,2021 Sheet 3 of 6
`
`US 2021/0335757 Al
`
`2004
`
`201
`
`4
`
`‘)
`O49
`
`2008
`
`200€
`
`202
`
`FIG 2C
`
`FIG 2D
`
`
`
`Patent Application Publication
`
`Oct. 28,2021 Sheet 4 of 6
`
`US 2021/0335757 Al
`
`ye
`21 213
`
`é
`a
`200C
`
`2008
`
`“ \
`
`ANS
`202
`
`:
`
`230
`
`FIG 2E
`
`2008
`
`200
`
`200A 201
`
`
`2600
`
`°
`
`909
`
`2008
`
`FIG 2F
`
`
`
`Patent Application Publication
`
`Oct. 28,2021 Sheet 5 of 6
`
`US 2021/0335757 Al
`
`200A 924
`
`221
`
`299
`
`200 2000
`200A
`
`200C
`
`*
`
`HA
`
`on
`202
`
`FEG 2G
`
`2008
`
`FIG 2H
`
`
`
`Patent Application Publication
`
`
`
`US 2021/0335757 Al
`
`Oct. 28,2021 Sheet 6 of 6
`
`
`
`
`
`[0001] This application is a continuation of PCT/CN2020/
`096254, filed on Aug. 14, 2020, which claims priority to
`Chinese Patent Application No. 201910982076.1,
`titled
`
`“METHOD FOR PACKAGING SEMICONDUCTOR,
`SEMICONDUCTOR PACKAGE STRUCTURE, AND
`PACKAGE?”andfiled on Oct. 16, 2019, the entire contents
`of which are incorporated herein
`byreference.
`
`FIELD OF THE INVENTION
`
`
`
`
`
`
`
`US 2021/0335757 Al
`
`Oct. 28, 2021
`
`METHOD FOR PACKAGING
`SEMICONDUCTOR, SEMICONDUCTOR
`PACKAGE STRUCTURE, AND PACKAGE
`
`CROSS-REFERENCE TO RELATED
`APPLICATION
`
`electrically conductive pillar. An insulating dielectric is
`filled in a gap between a sidewall of the groove and the
`semiconductor die stack to form an insulating dielectric
`layer covering an upper surface of the semiconductor die
`stack to seal up the semiconductor die stack so as to form a
`semiconductor package structure.
`[0007]
`Further, the second surface of the substrate wafer
`has a plurality of electrically conductive blocks electrically
`connected to the electrically conductive pillars.
`[0008]
`Further, the method of forming a groove on the
`substrate wafer includes: planarizing thefirst surface of the
`substrate wafer; and removing a part of the substrate wafer
`fromthe first surface until the electrically conductive pillar
`is exposed to form the groove.
`[0009]
`Further, the substrate wafer has a dicing lane, and
`the dicing lane serves as an alignment mark for forming the
`groove.
`Further, each ofthe plurality of semiconductor die
`[0010]
`stacks is formed by stacking a plurality of semiconductor
`dies electrically connected to each other, and the bottom of
`the semiconductor die stack is electrically connected to the
`electrically conductive pillar through the semiconductordie.
`[0011]
`Further,
`the semiconductor dies are electrically
`connected to eachother through the electrically conductive
`pillar penetrating through each of the semiconductor dies
`and the electrically conductive block between the adjacent
`semiconductor dies.
`
`[0002] The present disclosurerelates to the field of semi-
`conductor package, and more particularly, to a method for
`packaging a semiconductor, a semiconductor packagestruc-
`ture, and a package.
`
`BACKGROUND OF THE INVENTION
`
`[0003] Also knownas a 3D orthree-dimensional packag-
`ing technology, a stacked packaging technology is one of
`current mainstream multi-chip packaging technologies,
`which can stack at least two semiconductor chips (also
`referred to as dies, i.e., blocks having full functions diced
`from a wafer). The stacked packaging technology is gener-
`ally employed to manufacture electronic components such
`as memorychips, logic chips, and processor chips. With the
`developmentofthe electronics industry, the electronic com-
`ponents are required for high capacity, high function, high
`speed and small size. To meet the above requirements, it is
`necessary to incorporate more chips in a single package,
`which may increase a package height of the electronic
`components. Furthermore, when a semiconductor package
`structure moves or vibrates, there maylikely exist slight
`translocation between the chips, which results in poorreli-
`ability of a package structure andhas a negative effect on the
`performance of the package structure.
`[0004] Therefore, how to reduce the package height ofthe
`package and improve the reliability of the package has
`becomea technical problem urgently needing to be solved at
`present.
`
`
`
`SUMMARY OF THE INVENTION
`
`
`
`the
`the
`
`
`
`Further, the bottom of the semiconductordie stack
`[0012]
`is electrically connected to the electrically conductive pillar
`penetrating through the bottom of the groove through the
`electrically conductive block.
`
`
`[0013]
`Further, a thermal expansion coefficient of
`substrate wafer is greater than or equal
`to that of
`insulating dielectric layer.
`[0014]
`Further, the substrate wafer is a silicon wafer, and
`the insulating dielectric layer is a silicon dioxide insulating
`dielectric layer.
`[0015]
`Further, the method for packaging a semiconductor
`also includes: covering an upper surface of the insulating
`dielectric layer and the first surface of the substrate wafer
`with a cover plate wafer.
`[0016]
`Further, a surface of the cover plate wafer facing
`toward the substrate wafer has a plurality of electrically
`conductive pillars, and the electrically conductive pillar is
`electrically connected to the upper surface of the semicon-
`ductor die stack through an electrically conductive structure
`in the insulating dielectric laver.
`[0005] A technical problem to be solved bythe present
`[0017]
`Further, after the step of sealing up the semicon-
`disclosure is to provide a method for packaging a semicon-
`ductor die stack, the method also includes a dicing step:
`ductor, a semiconductor package structure, and a package.
`dicing the semiconductor package structure along the gap
`The present disclosure is characterized by a lower package
`between the grooves to form a plurality of packages inde-
`height, a higher reliability, and a lower warpage.
`pendent of each other.
`[0006]
`‘To solve the above problem, the present disclosure
`[0018] The present disclosure also provides a semicon-
`provides a method for packaging a semiconductor. The
`method includes followings steps. There is provided a
`ductor package structure, which includes a substrate wafer
`substrate wafer, which hasafirst surface and a second
`having a first surface and a second surface arranged opposite
`surface arranged opposite to each other. Thefirst surface has
`to each other. Thefirst surface has a plurality of grooves, a
`a plurality of grooves, a plurality of electrically conductive
`plurality of electrically conductive pillars is provided at a
`pillars is provided at a bottom of the groove, and the
`bottom of the groove, and theelectrically conductive pillar
`electrically conductive pillar penetrates through the bottom
`penetrates through the bottom of the groove to the second
`of the groove to the second surface. A plurality of semicon-
`surface. Moreover,
`the semiconductor package structure
`ductor die stacks is provided and placed in the groove. An
`includesa plurality of semiconductor die stacks placed in the
`upper surface of the semiconductor die stack is lower than
`groove, wherein an upper surface of the semiconductordie
`or flush with an upper edge of the groove, and a bottom of
`stack is lower than orflush with an upper edge ofthe groove,
`the semiconductor die stack is electrically connected to the
`and a bottom of the semiconductor die stack is electrically
`
`
`
`US 2021/0335757 Al
`
`Oct. 28, 2021
`
`ultra-thin packaging can be achieved. In addition, the insu-
`lating dielectric layer fills the gap between the sidewall of
`the groove and the semiconductor die stack, and the insu-
`lating dielectric layer can fix the semiconductor die stack,
`suchthat translocation between the semiconductor dies may
`be prevented even though the semiconductor packagestruc-
`ture movesorvibrates, thereby preventing a poor connection
`between the semiconductor dies and a poor connection
`between the semiconductordie stack and the substrate wafer.
`
`In this way, the stability of the semiconductordie stack is
`improved, and the reliability of the semiconductor package
`structure is improved.
`
`BRIEF DESCRIPTION OF THE DRAWINGS
`
`
`
`FIG. 1 is a schematic diagram showingsteps of a
`[0029]
`method for packaging a semiconductor according to an
`embodimentofthe presentdisclosure;
`[0030]
`FIG. 2A-FIG 2H are schematic flow diagrams of
`the method for packaging a semiconductor according to an
`embodimentofthe presentdisclosure;
`[0031]
`FIG. 3 is a schematic structural diagram of a
`semiconductor package structure according to an embodi-
`mentof the present disclosure; and
`[0032]
`FIG. 4 is a schematic structural diagram of a
`package according to an embodiment ofthe present disclo-
`sure.
`
` .
`
`
`
`DETAIL
` D DESCRIPTION OF THE
`EMBODIMENTS
`
`
`
`[0033] Embodiments of a method for packaging a semi-
`conductor, a semiconductor packagestructure and a package
`provided bythe present disclosure are described below in
`detail with reference to the accompanying drawings.
`[0034]
`FIG. 1 isa schematic diagram showingsteps of the
`method for packaging a semiconductor according to an
`embodimentofthe present disclosure. Referring to FIG.1,
`the method for packaging a semiconductor includes follow-
`ing steps. In Step S10, a substrate waferis provided, and the
`substrate wafer has a first surface and a second surface
`arranged opposite to each other, wherein thefirst surface has
`a plurality of grooves, a plurality of electrically conductive
`pillars is provided at a bottom of the groove, and the
`electrically conductive pillar penetrates through the bottom
`of the groove to the second surface. In Step S11, a plurality
`of semiconductor die stacks is provided. In Step $12, the
`semiconductor die stack is placed in the groove, wherein an
`pper surface of the semiconductor die stack is lower than
`or flush with an upper edge of the groove, and a bottom of
`the semiconductor die stack is electrically connected to the
`electrically conductive pillar. In Step $13, an insulating
`dielectric is filled in a gap between a sidewall of the groove
`and the semiconductor die stack to form an insulating
`dielectric layer covering an upper surface of the semicon-
`ductor die stack to seal up the semiconductordie stack so as
`to form a semiconductor package structure. In Step S14, an
`pper surface of the insulating dielectric layer and the first
`surface of the substrate wafer are covered with a coverplate
`wafer. In Step S15, the semiconductor package structureis
`diced along the gap between the grooves to form a plurality
`of packages independent of each other.
`[0035]
`FIG. 2A-FIG 2H are schematic flow diagrams of
`the method for packaging a semiconductor according to an
`embodimentofthe present disclosure.
`
`
`
`connectedto the electrically conductive pillar. Furthermore,
`the semiconductor package structure also includes an insu-
`lating dielectric layerfilling a gap between a sidewall of the
`groove and the semiconductor die stack and covering an
`upper surface of the semiconductor die stack to seal up the
`semiconductor die stack.
`
`Further, the second surface of the substrate wafer
`[0019]
`has a plurality of electrically conductive blocks, and the
`electrically conductive blocks are electrically connected to
`the electrically conductivepillars.
`[0020]
`Further, each ofthe plurality of semiconductor die
`stacks is formed bystacking a plurality of semiconductor
`dies electrically connected to each other, and the semicon-
`ductor dies are electrically connected to the electrically
`conductive pillars through the bottom of the semiconductor
`die stack.
`
`the semiconductor dies are electrically
`Further,
`[0021]
`connected to each other through the electrically conductive
`pillar penetrating through each of the semiconductor dies
`and the electrically conductive block between the adjacent
`semiconductor dies.
`
`
`
`Further, the bottom of the semiconductordie stack
`[0022]
`is electrically connected to the electrically conductive pillar
`penetrating through the bottom of the groove through the
`electrically conductive block.
`[0023]
`Further, a thermal expansion coefficient of the
`substrate wafer is greater than or equal
`to that of the
`insulating dielectric layer.
`[0024]
`Further, the substrate wafer is a silicon wafer, and
`the insulating dielectric layer is a silicon dioxide insulating
`dielectric layer.
`[0025]
`Further, an upper surface ofthe insulating dielec-
`tric layer and the first surface of the substrate wafer are
`covered with a cover plate wafer.
`[0026]
`Further, a surface of the cover plate wafer facing
`toward the substrate wafer has a plurality of electrically
`conductive pillars, in the insulating dielectric layer there is
`provided with an electrically conductive structure, and the
`electrically conductive pillar is electrically connectedto the
`upper surface of the semiconductor die stack through the
`electrically conductive structure.
`[0027] The present disclosure also provides a package,
`which
`includes a substrate having a first surface and a
`second surface arranged opposite to each other. The first
`surface has at least one groove, a plurality of electrically
`conductivepillars is provided at a bottom of the groove, and
`the electrically conductive pillar penetrates through the
`bottom of the groove to the second surface. Moreover, the
`package includesat least one semiconductordie stack placed
`in the groove, wherein an upper surface of the semiconduc-
`tor die stack is lowerthan orflush with an upper edgeof the
`groove, and a bottom of the semiconductor die stack is
`electrically connected to the electrically conductive pillar.
`Furthermore, the packagealso includes an insulating dielec-
`tric layerfilling a gap between a sidewall of the groove and
`the semiconductor die stack and covering an upper surface
`of the semiconductordie stack to seal up the semiconductor
`die stack.
`
`[0028] Advantagesof the present disclosure are as below.
`A groove is formed on the substrate wafer to accommodate
`the semiconductor die stack, and is sealed up byan insu-
`lating dielectric layer. The height of the semiconductor
`package structure can be greatly reduced while the same
`number of semiconductor dies are packaged, such that
`
`
`
`US 2021/0335757 Al
`
`Oct. 28, 2021
`
`[0036] Referring to Step S10 and FIG. 2C, there is pro-
`other methods may also be employed to form the groove 201
`on the first surface 200A of the substrate wafer 200.
`vided a substrate wafer 200, which hasafirst surface 200A
`and a second surface 200B arranged opposite to each other.
`[0043]
`In this embodiment, the width of the dicing lane
`The first surface 200A has a plurality of grooves 201, a
`203 is equal to the distance between two grooves 201. In
`plurality of electrically conductive pillars 202 is provided at
`other embodiments ofthe present disclosure, the groove 201
`a bottom of the groove 201, and the electrically conductive
`may occupya part of space of the dicing lane 203, such that
`pillar 202 penetrates through the bottomof the groove 201
`the distance between the two adjacent grooves 201 is smaller
`to the second surface 200B.
`than the width of the dicing lane 203, which makesit easier
`to place the semiconductor die stack 210 into the groove 201
`subsequently. Furthermore, a side surface of the semicon-
`ductor die stack 210 can be prevented from touching the
`sidewall of the groove 201 to avoid having a negative effect
`on the performance of the semiconductordie stack 210.
`[0044]
`Further, with continued reference to FIG. 2A, a
`plurality of electrically conductive blocks 204 is provided on
`the second surface 200B ofthe substrate wafer 200, and the
`electrically conductive blocks 204 are electrically connected
`to the electrically conductive pillars 202 to electrically
`connect the electrically conductive pillars 202 to external
`devices such as printed circuit boards. The electrically
`conductive block 204 may be formed on the second surface
`200B of the substrate wafer 200 before the groove 201 is
`formed.
`
`[0037] An embodiment of forming the groove 201 is
`described below by wayofillustration.
`[0038] Referring to FIG. 2A, the substrate wafer 200 has
`a first surface 200A and a second surface 200B arranged
`opposite to each other. The first surface 200A is a back
`surface of the substrate wafer 200, and the second surface
`200B is a front surface of the substrate wafer 200. Thatis,
`on the second surface 200B, the substrate wafer 200 has a
`functional layer 200C. Theelectrically conductivepillar 202
`extends from the second surface 200B into the substrate
`wafer 200, and the surface of the electrically conductive
`pillar 202 is exposed to the second surface 200B. The
`electrically conductivepillar 202 not only canplaya role of
`conducting electricity, but also can play a role of conducting
`heat.
`
`[0039] Referring to FIG. 2B, thefirst surface 200A ofthe
`substrate wafer 200 is planarized to facilitate subsequent
`processes. Further, the first surface 200A of the substrate
`wafer 200 may be planarized by using a chemical mechani-
`cal polishing method. In this step, a thickness of the sub-
`strate wafer 200 is reduced. It is to be noted that after this
`
`
`
`step is performed, a distance H from the first surface 200A
`ofthe substrate wafer 200 to the functional layer 200C of the
`second surface 200B is greater than or equal to a height of
`
`the semiconductor die stack 210 to provide sufficient opera-
`tion space for the subsequent processes, and a width of the
`groove 201 needs to be greater than or equal to that of the
`semiconductor die stack 210. In one embodiment, the width
`of the groove 201 is slightly larger than that of the semi-
`conductor die stack 210, such that the semiconductor die
`stack 210 is placed in the groove 201.
`[0040] Referring to FIG. 2C, a part of the substrate wafer
`200 is removed from the first surface 200A until the elec-
`
`trically conductive pillar 202 is exposed to form the groove
`201. In this step, a photolithography and etching process
`may be employed to remove a part of the substrate wafer
`200, and the etching is not stopped until the electrically
`conductive pillar 202 is exposedat the bottom of the groove
`201. Further, when the etching is about to be stopped,
`etching conditions may be adjusted to ensure that an edge
`etching rate of the groove 201 is smaller than an etching rate
`of a middle part of the groove 201, such that a bottom corner
`of the groove 201 is shaped like an arc, which can enhance
`the stability of the sidewall of the groove 201.
`[0041]
`Further, in this step, the substrate wafer 200 has a
`dicing lane 203. As shown in FIG. 2C, the groove 201 is
`formed when the dicing lane 203 passes through the gap
`between two adjacent grooves 201. The dicing lane 203 may
`serve as an alignment mark for forming the groove 201. In
`this way,
`the accuracy of forming the groove 201 is
`improved, andthere is no need to makeadditional alignment
`marks, such that process steps are saved, and production
`efficiency is improved.
`[0042] The above embodiment is an embodimentof form-
`ing the groove 201 onthefirst surface 200A ofthe substrate
`wafer 200. In other embodiments of the present disclosure,
`
`[0045] Referring to Step S11 and FIG. 2D,a plurality of
`semiconductordie stacks 210 is provided. The numberofthe
`semiconductor die stacks 210 may be equal to that of the
`grooves 201, or the numberof the semiconductordie stacks
`210 may be more than that of the grooves 201. In one
`embodiment, if the number of the semiconductordie stacks
`210 is equal to that of the grooves 201, in the subsequent
`processes, one semiconductordie stack 210 is placed in one
`groove 201. If the number of the semiconductor die stacks
`210 is more than that of the grooves 201, two or more
`semiconductor die stacks 210 may be placed in parallel in
`one groove 201.
`[0046] The semiconductor die stack 210 is formed by
`stacking a plurality of semiconductor dies 210A. In this
`embodiment, three semiconductor dies 210A are schemati-
`cally shown. The three semiconductor dies 210A are sequen-
`tially stacked to form the semiconductordie stack 210. In the
`semiconductor die stack 210, the semiconductor dies 210A
`are electrically connected to each other, such that an elec-
`trical signal of the semiconductor die 210A can be trans-
`mitted to an external structure. In this embodiment, the
`semiconductor dies 210A are electrically connected to each
`other throughthe electrically conductivepillar 211 penetrat-
`ing through each of the semiconductordies and theelectri-
`cally conductive block 212 between the adjacent semicon-
`
`ductor dies. Each of the semiconductor dies 210A has an
`electrically conductive pillar 211 penetrating through the
`semiconductor die 210A, and the electrically conductive
`pillars 211 of the two semiconductor dies 210Aareelectri-
`cally connected by the electrically conductive block 212
`arranged therebetween. The method of forming the electri-
`cally conductive pillar on the semiconductor die 210A
`includes but is not limited to a through silicon via (TSV)
`process well knownin the art.
`[0047] After this step is completed, a surface of the
`electrically conductive pillar is exposed at the bottom of the
`semiconductor die stack 210, and the surface of the electri-
`cally conductive pillar is also exposed on the top of the
`semiconductor die stack 210.
`
`
`
`the
`[0048] With reference to Step S12 and FIG. 2E,
`semiconductor die stack 210 is placed in the groove 201. In
`
`
`
`US 2021/0335757 Al
`
`Oct. 28, 2021
`
`this step, one or more semiconductor die stacks 210 may be
`placed in one of the grooves 201. In this embodiment, one
`semiconductor die stack 210 is placed in one groove 201.
`[0049] The bottom of the semiconductor die stack 210 is
`electrically connected to the electrically conductive pillar
`202 penetrating through the bottom of the groove 201. That
`is,
`the electrically conductive pillar 211 exposed at
`the
`bottom of the semiconductor die stack 210 is electrically
`connected to the electrically conductive pillar 202 exposed
`at the bottom of the groove 201. In one embodiment, the
`electrically conductive pillar 211 and the electrically con-
`ductive pillar 202 maybeelectrically connected through the
`electrically conductive block 213.
`[0050] The upper surface of the semiconductordie stack
`210 is lower than orflush with the upper edge of the groove
`201 to facilitate subsequent processes. In this embodiment,
`the upper surface of the semiconductor die stack 210 is
`lower than the upper edge ofthe groove 201. In addition,to
`makeit easier to place the semiconductor die stack 210 into
`the groove 201, the width of the groove 201 is greater than
`or equal to that of the semiconductor die stack 210. In this
`case, after the semiconductor die stack 210 is placed in the
`groove 201, there is a gap between the side surface of the
`semiconductor die stack 210 and the sidewall of the groove
`201.
`
`[0051] With reference to Step $13 and FIG.2F, an insu-
`lating dielectric is filled in a gap betweenthe sidewall of the
`groove 210 and the semiconductor die stack 210 to form an
`insulating dielectric layer 230, and the insulating dielectric
`layer 230 covers an upper surface of the semiconductor die
`stack 210 to seal up the semiconductordie stack 210. In this
`way, the semiconductor package structure is formed.
`[0052] After this step is performed, the groove 201 is filled
`with the insulating dielectric layer 230, the semiconductor
`die stack 210 is sealed up, the plurality of semiconductor
`dies 210A ofthe semiconductordie stack 210 is fixed to each
`other, and the semiconductor die stack 210 is fixed with
`respect
`to the substrate wafer, such that
`translocation
`between the semiconductor dies and between the semicon-
`
`ductor die stack and the substrate wafer may be prevented
`even though the semiconductor package structure moves or
`vibrates, thereby preventing a poor connection between the
`semiconductor dies and a poor connection between the
`semiconductordie stack andthe substrate wafer. In this way,
`the stability of the semiconductor die stack is improved, and
`the reliability of the semiconductor package structure is
`improved.
`[0053]
`Furthermore, according to the method for packag-
`ing a semiconductor provided by the present disclosure, a
`groove is formed onthe substrate wafer to accommodate the
`semiconductor die stack, and the semiconductordie stack is
`sealed up by an insulating dielectric layer. In this way, the
`height of the semiconductor packagestructure can begreatly
`reduced while the same number of semiconductor dies are
`packaged, such that ultra-thin packaging can be achieved.
`[0054]
`In one embodiment, the thermal expansion coefii-
`cient of the substrate wafer 200 is greater than or equal to
`that of the insulating dielectric layer 230. The advantages of
`the present disclosure are as below. When the semiconductor
`package structure is heated, the deformation of the insulat-
`ing dielectric layer 230 is less thanthat of the substrate wafer
`200, such that the substrate wafer 200 may be prevented
`from being forcedly deform, suchthatit is avoidable to have
`adverse effects on the reliability and warpage of the semi-
`
`conductor packagestructure. Of course, the thermal expan-
`sion coeflicient of the substrate wafer 200 is not allowed to
`
`differ too much fromthe thermal expansion coefficient of the
`insulating dielectric layer 230, otherwise the insulating
`dielectric layer 230 maylikely be divorced from the sidewall
`of the groove 201 of the substrate wafer 200.
`In this
`embodiment, the substrate wafer 200 is a silicon wafer, and
`the insulating dielectric layer 230 is a silicon dioxide insu-
`lating dielectric layer.
`[0055] Alternatively, the method for packaging a semi-
`conductor also includes following steps. With reference to
`Step $14 and FIG. 2G an upper surface of the insulating
`dielectric layer 230 and the first surface of the substrate
`wafer 200 are covered with a cover plate wafer 220 to
`further seal up the semiconductor die stack 210. The cover
`plate wafer 220 and the substrate wafer 200 may be com-
`bined by a bonding process.
`[0056]
`Further, a surface of the cover plate wafer 220
`facing toward the substrate wafer 200 has a plurality of
`electrically conductive pillars 221, and in the insulating
`dielectric layer 230 there is also provided with an electri-
`cally conductive pillar 231. In this case,
`the electrically
`conductive pillar 221 in the cover plate wafer 220 may be
`electrically connected to the upper surface of the semicon-
`ductor die stack 210 through the electrically conductive
`pillar 231 in the insulating dielectric layer 230. That is, the
`electrically conductive pillar 221 on the surface of the cover
`plate wafer 220 is electrically connected to the electrically
`conductive pillar 211 exposed on the upper surface of the
`semiconductordie stack 210. The cover plate wafer 220 may
`provide heat conduction to the semiconductor die stack 210
`through the electrically conductive pillar 221, and may
`further fix the semiconductor die stack 210. In addition, in
`semiconductor packaging, other wafers may be stacked on
`the cover plate wafer 220, and the electrically conductive
`pillar 221 mayfunction as electrical connection. The step of
`arranging the electrically conductive pillar 231 in the insu-
`lating dielectric layer 230 may be performed beforethe step
`of covering the cover plate wafer 220.
`[0057] Alternatively, after Step S13 or Step S14 is per-
`formed,the present disclosure also includesa dicing step. In
`this embodiment, after Step S14 is performed, the present
`disclosure also includes a dicing step. With reference to Step
`S15 and FIG. 2H, the semiconductor package structure is
`diced along the gap between the grooves 201 to form a
`plurality of packages independent of each other. In one
`embodiment, the semiconductor package structure is diced
`along the dicing lane 203 between the grooves 201 to fo
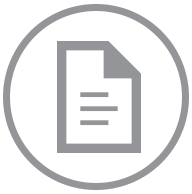
Accessing this document will incur an additional charge of $.
After purchase, you can access this document again without charge.
Accept $ ChargeStill Working On It
This document is taking longer than usual to download. This can happen if we need to contact the court directly to obtain the document and their servers are running slowly.
Give it another minute or two to complete, and then try the refresh button.
A few More Minutes ... Still Working
It can take up to 5 minutes for us to download a document if the court servers are running slowly.
Thank you for your continued patience.
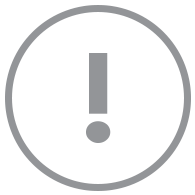
This document could not be displayed.
We could not find this document within its docket. Please go back to the docket page and check the link. If that does not work, go back to the docket and refresh it to pull the newest information.
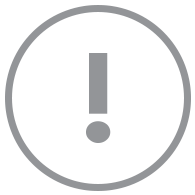
Your account does not support viewing this document.
You need a Paid Account to view this document. Click here to change your account type.
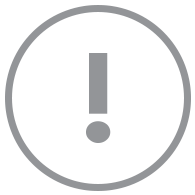
Your account does not support viewing this document.
Set your membership
status to view this document.
With a Docket Alarm membership, you'll
get a whole lot more, including:
- Up-to-date information for this case.
- Email alerts whenever there is an update.
- Full text search for other cases.
- Get email alerts whenever a new case matches your search.
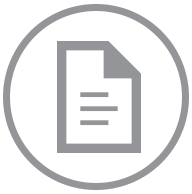
One Moment Please
The filing “” is large (MB) and is being downloaded.
Please refresh this page in a few minutes to see if the filing has been downloaded. The filing will also be emailed to you when the download completes.
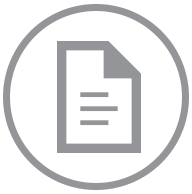
Your document is on its way!
If you do not receive the document in five minutes, contact support at support@docketalarm.com.
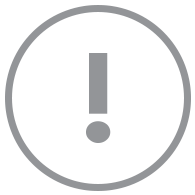
Sealed Document
We are unable to display this document, it may be under a court ordered seal.
If you have proper credentials to access the file, you may proceed directly to the court's system using your government issued username and password.
Access Government Site