`
`PROSTHETIC PARTIAL FINGERS
`
`CROSS-REFERENCE TO RELATED APPLICATIONS
`
`[0001]
`
`This application is a continuation of U.S. Patent Application No. 17/164,480,
`
`filed February 1, 2021, which is a continuation of U.S. Patent Application No.
`
`16/688,719, filed November 19, 2019, which claims priority to U.S. Provisional
`
`Application Serial No. 62/769,360 filed November 19, 2018, the contents of which are
`
`incorporated herein by reference in their entirety for all purposes.
`
`STATEMENT REGARDING FEDERALLY SPONSORED RESEARCH
`
`[0002]
`
`This invention was made with government support under grant numbers
`
`1 41 HD096942-01 awarded by the NIH NICHD. The governmenthascertain rightsin
`
`the invention.
`
`TECHNICAL FIELD
`
`[0003]
`
`Various embodiments of the present invention generally relate to prosthetic
`
`devices. More specifically, some embodiments of the present technology relate to
`
`prosthetic partial fingers.
`
`BACKGROUND
`
`[0004]
`
`There are an estimated 500,000 amputees with partial hand amputations.
`
`Various types of prosthetic devices can be used to replace a missing body parts (e€.g., a
`
`limb, a finger, etc.). The most common upper limb amputation is partial hand
`
`amputation with loss of one or more fingers. Sometraditional devices are purely
`
`cosmetic and providestatic limb replacements no movementor functionality. Other
`
`devices are body poweredwith cabling to the wrist joint or palm of the hand. When the
`
`wrist or palm of the hand is flexed that will cause the prosthetic device to automatically
`
`flex. Moreover, in order to maintain flexion of the finger with these traditional cabled
`
`devices, the user mustcontinually flex the wrist or palm. This can betiring when
`
`manual performing tasks that require flexion of the fingers for an extended period of
`
`time (e€.g., mowing the lawn). Moreover, these traditional devices typically do not create
`
`much mechanical advantage and break easily. As such, new prosthetic designs are
`
`-1-
`
`
`
`neededto provide a costeffective set of fingers that provide a robust set of anatomical
`
`restorations.
`
`PDS0002.USC2
`
`
`
`PDS0002.USC2
`
`SUMMARY
`
`[0005]
`
`Various embodiments of the present invention generally relate to prosthetic
`
`devices. More specifically, some embodiments of the present technology relate to
`
`prosthetic partial fingers. Some embodiments comprise a proximal phalange, a distal
`
`phalange coupled to the proximal phalange, and a knuckle track formed in an arc and
`
`configured to be moveably coupled to the proximal phalange.
`
`In accordance with
`
`various embodiments, the proximal phalange, the distal phalange, and the knuckle
`
`track, can be made out of different materials (e.g., plastic, metal, etc.).
`
`In some
`
`embodiments, the knuckle track can include multiple teeth formed on a first side on
`
`which the proximal phalange slides along. The proximal phalange can include a
`
`ratcheting mechanism to contact the multiple teeth to allow sliding in onlya first
`
`direction while the ratcheting mechanism is engaged. Some embodimentsinclude
`
`release mechanism (e.g., a button) configured to disengage the ratcheting mechanism
`
`from the multiple teeth to allow the distal phalange to slide in a second direction.
`
`In
`
`some embodiments, the distal phalange can be coupled to the proximal phalange using
`
`a SCrew.
`
`[0006]
`
`Some embodiments provide for method that includes exposing a mounting
`
`hole on a mounting bracket after lamination to provide one or more points of
`
`attachment. The mounting bracket can capture a knuckle track beneath providing a
`
`low-profile installation. One or more extensions of the mounting bracket can be bent to
`
`conform the mounting bracket to a socket shape.
`
`[0007]
`
`Some embodiments provide for a device comprising a knuckle track formed
`
`in an arc, a proximal phalange, a distal phalange, and a means for coupling the distal
`
`phalange to the proximal phalange.
`
`In accordance with some embodiments, the
`
`proximal phalange can include a means for moveably coupling the proximal phalange to
`
`the knuckle track that allows the proximal phalange to slide in onlyafirst direction until
`
`released.
`
`In some embodiments, the distal phalange can be coupledto the proximal
`
`phalange using a screw.
`
`[0008]
`
`Some embodiments include a device having a proximal phalange, a distal
`
`phalange coupled to the proximal phalange, a knuckle track moveably coupled to the
`
`
`
`PDS0002.USC2
`
`proximal phalange, a ratcheting mechanism to contact multiple teeth to allow sliding in
`
`only a first direction while the ratcheting mechanism is engaged, and a release button
`
`configured to disengage the ratcheting mechanism from the multiple teeth to allow
`
`motion of the distal phalange or proximal phalange.
`
`[0009]
`
`In some embodiments, a mounting hole can be exposed on a mounting
`
`bracketafter lamination to provide one or more points of attachment. The mounting
`
`bracket can capture a knuckle track beneath providing a low-profile installation. One or
`
`more extensions of the mounting bracket can be bent to conform the mounting bracket
`
`to a socket shape.
`
`[0010]
`
`While multiple embodiments are disclosed, still other embodimentsof the
`
`present technology will become apparent to those skilled in the art from the following
`
`detailed description, which shows and describes illustrative embodiments of the
`
`technology. Aswill be realized, the technology is capable of modifications in various
`
`aspects, all without departing from the scope of the present technology. Accordingly,
`
`the drawings and detailed description are to be regardedasillustrative in nature and not
`
`restrictive.
`
`
`
`PDS0002.USC2
`
`BRIEF DESCRIPTION OF THE DRAWINGS
`
`[0011]
`
`Embodiments of the present technology will be described and explained
`
`through the use of the accompanying drawings.
`
`[0012]
`
`Fig. 1A illustrates an example of a hand with a partial finger amputation in
`
`which some embodiments of the present technology may beutilized.
`
`[0013]
`
`Fig. 1B is a cross-sectional view of an example of a prosthetic device
`
`according to one or more embodimentsof the present technology.
`
`[0014]
`
`Fig. 1C illustrates an example of the range of motion of a prosthetic device
`
`secured to a hand with a silicone and hard shell prosthetic socket to a partial finger
`
`amputation.
`
`[0015]
`
`Figs. 2A-2Cillustrate various views of an example of a mounting bracketfor
`
`a prosthetic finger system that may be used in accordance with various embodimentsof
`
`the present technology.
`
`[0016]
`
`Fig. 3A illustrates an alignment guide that may be used in accordance with
`
`one or more embodiments of the present technology.
`
`[0017]
`
`Fig. 3B illustrates an example of a lamination dummy that may be usedin
`
`accordance with some embodiments of the present technology.
`
`[0018]
`
`Fig. 3C illustrates how the alignment guide and lamination dummyin Figs.
`
`3A-3B can connect in accordance with some embodiments of the present technology.
`
`[0019]
`
`Figs. 4A-4B illustrates a partial prosthetic device in an extended and flexed
`
`position according to one or more embodiments of the present technology.
`
`[0020]
`
`Figs. 5A-5D illustrate various views of an assembled partial system in
`
`accordance with some embodiments of the present technology.
`
`[0021]
`
`Fig. 6 illustrates an exploded viewof a partial finger system illustrating
`
`various component that may be present in accordance with one or more embodiments
`
`of the present technology.
`
`[0022]
`
`Figs. 7A-7Cillustrate various views of a knuckle track that may be usedin
`
`various embodiments of the present technology.
`
`-5-
`
`
`
`PDS0002.USC2
`
`[0023]
`
`Fig. 8 illustrates an example of a mounting tab that may be used in
`
`accordance with various embodimentsof the present technology.
`
`[0024]
`
`Fig. 9 illustrates an example of a set of operations for building a partial
`
`finger system in accordance with some embodiments of the present technology.
`
`[0025]
`
`Fig. 10 illustrates an example of a set of componentsfor a three-
`
`dimensional printing system that may be used in one or more embodiments of the
`
`present technology.
`
`[0026]
`
`Fig. 11 is example of a computer system that may be used in accordance
`
`with various embodiments of the present technology.
`
`[0027]
`
`The drawings have not necessarily been drawn to scale. Similarly, some
`
`components and/or operations may be separated into different blocks or combinedinto
`
`a single block for the purposes of discussion of some of the embodiments of the present
`
`technology. Moreover, while the technology is amenable to various modifications and
`
`alternative forms, specific embodiments have been shown by way of example in the
`
`drawings and are described in detail below. The intention, however,is notto limit the
`
`technology to the particular embodiments described. On the contrary, the technologyis
`
`intended to cover all modifications, equivalents, and alternatives falling within the scope
`
`of the technology as defined by the appendedclaims.
`
`
`
`PDS0002.USC2
`
`DETAILED DESCRIPTION
`
`[0028]
`
`Various embodiments of the present invention generally relate to prosthetic
`
`devices. More specifically, some embodiments of the present technology relate to
`
`prosthetic partial finger designs. One of the most common upper limb amputations is
`
`the partial finger amputation.
`
`Individuals with partial finger amputations often retain one
`
`or more fingers and the missing limbs often include a residual limb that a prothesis can
`
`be mounted onto. Traditional designs are ineffective in allowing the individual to
`
`perform manual tasks over longer periods of time (€.g., mowing the lawn, using a
`
`hammer, etc.) as these traditional devices are purely cosmetic and do notrestore any of
`
`the lost functionality or have complex cabling systems which require the individual to
`
`maintain a flexed wrist or palm.
`
`[0029]
`
`In contrast, various embodiments of the present technology provide a
`
`partial finger device that can mimic the last two joints of the finger. Some embodiments
`
`use a passive design without any cabling but instead include a ratcheting mechanism
`
`that allows the individual to position the device independent of the posture of the
`
`residual limb. Upon completion a release button can be engagedto release the
`
`ratcheting mechanism and allow the finger to be extended.
`
`In some embodiments, the
`
`ratcheting mechanism provides multiple distinct amounts of finger flexion (e.g., five
`
`states, ten states, fifteen states, etc.).
`
`In some embodiments, the device mayinclude a
`
`spring-back capability that automatically extends the finger after reaching full finger
`
`flexion, enabling one-handed use. A mounting track can be used in some embodiments
`
`to provide a center of rotation about the physiological joint recreating the physiological
`
`kinematics. Some embodiments can use of a metal laser sintering 3D printer to
`
`manufacture the components allows for unique mechanical designs to provide high
`
`strength at a low weight. The fingers can be scaledto larger or smaller hand sizes and
`
`customized to match the physiological hand.
`
`[0030]
`
`Some embodiments of the present technology provide a non-powered
`
`ratcheting mechanical prosthetic partial finger. A mounting kit can contain everything
`
`neededfor a trained prosthetist to install one (1) to four (4) point partial(s) into a
`
`prosthetic socket, including mounting brackets, alignment/lamination tools, and
`
`
`
`PDS0002.USC2
`
`mounting screws. The mounting bracket used in some embodiments can provide an
`
`attachment point between the prosthetic socket and the prosthetic finger. Two
`
`mounting brackets may be usedfor each prosthetic finger device in some embodiments.
`
`The mounting bracket can be aligned on the socket and laminatedinto the socket by a
`
`trained prosthetist or technician. Using the mounting screws, lamination spacers can be
`
`attached to the mounting bracket during the lamination process in place of some
`
`embodimentsof the prosthetic fingers to maintain the mounting location. After
`
`lamination, the prosthetic digit can be attached to the mounting bracket using the
`
`mounting screws.
`
`[0031]
`
`Various embodiments of the present technology provide for a wide range of
`
`technical effects, advantages, and/or improvements to computing systems and
`
`components. For example, various embodiments include one or more ofthe following
`
`technical effects, advantages, and/or improvements: 1) prosthetic partial finger that is
`
`durable and can withstand high loads; 2) integrated use of three-dimensionalprinting to
`
`fabricate complex mechanical prosthetic devices that can be automatically scaled; 3)
`
`unique spherical ratcheting mechanism allowing for prolonged flexion without continued
`
`effort on behalf of the user; 4) use of unconventional and non-routine computer
`
`operations to automatically scale point pivot system design to match the size of the
`
`physiological hand; 5) mounting track provides a center of rotation about the
`
`physiological joint recreating the physiological kinematics; 6) push button allowsfor the
`
`finger design to be extended when engaged; and/or 7) unique manufacturing processes
`
`to handle complex system integration.
`
`[0032]
`
`In the following description, for the purposes of explanation, numerous
`
`specific details are set forth in order to provide a thorough understanding of
`
`embodiments of the present technology.
`
`It will be apparent, however, to one skilled in
`
`the art that embodiments of the present technology may be practiced without some of
`
`these specific details. While, for convenience, embodiments of the present technology
`
`are described with reference to single independent ratcheting prosthetic finger, other
`
`embodiments can use a cable to flex the finger instead of external objects which are
`
`necessary with the original design.
`
`
`
`PDS0002.USC2
`
`[0033]
`
`For example, the cable could be anchored to the amputee and wrist flexion
`
`would causethe cable to pull tension and flex the finger. As another example, some
`
`embodiments can provide a coupled prosthetic finger arrangement. As such, a fixture
`
`can beinstalled between prosthetic fingers so that the flexion of one finger causes
`
`flexion (potentially at varying degrees) acrossall other fingers. Still yet, some
`
`embodiments can provide for a prosthetic thumb.
`
`In some of these embodiments, a
`
`prosthetic thumb can have phalange lengths and geometries adjustedtofit the form of a
`
`thumb. However, the ratcheting technology could still be used. As another example,
`
`some embodiments can be usedfor pediatric and/or women sized digits. Women and
`
`children are under-served populations in upper limb prosthetics since most devices are
`
`too large. By using the design of the prosthetic finger, and the custom scaling
`
`techniques, various embodiments allow for the creation of a smaller version for patients
`
`with smaller intact anatomy.
`
`[0034]
`
`The phrases "in some embodiments,"
`
`"according to some embodiments,"
`
`"in the embodiments shown,"
`
`"in other embodiments," and the like generally mean the
`
`particular feature, structure, or characteristic following the phraseis includedin at least
`
`one implementation of the present technology, and may be included in more than one
`
`implementation.
`
`In addition, such phrases do not necessarily refer to the same
`
`embodiments or different embodiments.
`
`[0035]
`
`Fig. 1A illustrates an example of a hand 100 with a partial finger amputation
`
`in which some embodimentsof the present technology maybeutilized. Asillustrated in
`
`hand 100, Fig. 1B illustrates an example of a prosthetic finger prosthetic device
`
`according to one or more embodimentsof the present technology.
`
`In accordance with
`
`various embodiments, a partial finger (or multiple partial finger) prosthetic device can
`
`serve people with amputation(s) (e.g., 110 and 120) between the metacarpophalangeal
`
`(MCP)joint 130 and the proximal interphalangeal (PIP) joint 140 on the index, middle,
`
`ring, and/or little fingers asillustrated in Fig. 1A. Some embodiments provide
`
`anatomical flexion and rotation around the PIP joint 140. Some embodiments of the
`
`prosthetic finger system include the finger prosthesis and mounting brackets (Fig. 2).
`
`
`
`PDS0002.USC2
`
`[0036]
`
`Fig. 1B is a cross-sectional view of an example of a prosthetic device 150
`
`according to one or more embodiments of the present technology. Prosthetic finger
`
`design 150 illustrated in Fig. 1B can serve people with amputation between the
`
`metacarpophalangeal (MCP) joint 130 and the proximal interphalangeal (PIP) joint 140
`
`as described in Fig. 1A. Asillustrated in Fig. 1B, some embodiments can include a
`
`proximal phalange 155, a distal phalange 160 coupled to the proximal phalange 155,
`
`and a knuckle track 165 formedin an arc to allow for placement around residual portion
`
`of afinger. The knuckle track 165 can be configured to be moveably coupled to the
`
`proximal phalange 155.
`
`In some embodiments, knuckle track 165 and proximal
`
`phalange 155 can moverelative through each other through a sliding joint, pin joint, or
`
`the like.
`
`In some embodiments, the distal phalange 160 can be coupled to the proximal
`
`phalange 15 using a screw, pin, or other component.
`
`[0037]
`
`In accordance with various embodiments, the proximal phalange 155, the
`
`distal phalange 160, and the knuckle track 165, can be made out of different materials
`
`(e.g., plastic, metal, etc.).
`
`In some embodiments, the knuckle track 165 can include
`
`multiple teeth 167 formed onafirst side on which the proximal phalange 155 slides
`
`along. The prosthetic device 150 can also include a link bar 170 (or a link chain)
`
`connecting the distal phalange 160 to the curved knuckle track 165. The link bar 170
`
`can cause the distal phalange 160 to moverelative to both the proximal phalange 155
`
`and the knuckle track 165 as the proximal phalange 155 moves relative to the knuckle
`
`track 165. The proximal phalange 155 can include a ratcheting mechanism 157 to
`
`contact the multiple teeth 167 to allow sliding in onlyafirst direction 158 while the
`
`ratcheting mechanism 157 is engaged. Some embodimentsinclude release
`
`mechanism (e.g., a release button 175) configured to disengage the ratcheting
`
`mechanism 157 from the multiple teeth 167 to allow the distal phalange 160 to slide ina
`
`second direction 159.
`
`[0038]
`
`In the embodimentillustrated in Fig. 1B, release mechanism 175 may
`
`include a linkage to a fixed pivot point 180 so that upon engagement of the release
`
`mechanism, the opposite end of the linkage is lifted allowing the proximal phalange 155
`
`to slide in any direction on the knuckle track 165 without engaging the multiple teeth
`
`167.
`
`In some embodiments, an elastic restoring force 171 may movethe partial finger
`
`-10-
`
`
`
`PDS0002.USC2
`
`in a second direction 159 relative to the knuckle track 165 resulting in extension of the
`
`partial finger 173 when the release mechanism 175 is activated. Some embodiments of
`
`the knuckle track 165 may include protruding stops 166 (also shownin Figs. 4A and 4B)
`
`that disengage the release button 175 from the ratcheting mechanism 157 allowing an
`
`elastic restoring force 171 (e.g., a torsion spring 172 located in the interface 185
`
`between the distal phalange 160 and the proximal phalange 155) to movethe partial
`
`finger in the second direction 159 without effort from the user.
`
`[0039]
`
`Fig. 1C illustrates an example of the range of motion 190 of a prosthetic
`
`finger prosthetic device 150 secured to a hand 192 with a partial point finger
`
`amputation. Asillustrated in Figs. 1B and 1C, the prosthetic finger device 150 can
`
`provide a passive functional mechanically articulating prosthetic device for people with 1
`
`— 4 partial finger (e.g., index, middle, ring, little) amputation(s) between the
`
`metacarpophalangeal (MCP)joints and the proximal interphalangeal (PIP) joints.
`
`(see,
`
`e.g., Fig. 1A and Fig. 1B) The knuckle track can be positioned on a prosthetic socket
`
`194 to allow for a PIP center of rotation 196. The length 198 of the prosthetic finger
`
`device 150 can be customized along with other dimensions (e.g., radius and sub-
`
`lengths of the distal and proximal phalanges)for differing limb sizes (e.g., that of a child
`
`or size of an individual).
`
`[0040]
`
`Figs. 2A-2Cillustrate various views of an example of a mounting bracketfor
`
`a prosthetic finger system that may be used in accordance with various embodimentsof
`
`the present technology.
`
`In accordance with various embodiments, one (1) to four (4)
`
`prosthetic partial fingers 150, can be installed onto a mounting system.
`
`In some
`
`embodiments, the mounting system can include: 1) two (2) mounting brackets (see,
`
`e.g., Figs. 2A-2C) for integrating each prosthetic finger device into a prosthetic socket
`
`194 in Fig. 1C (e.g., silicone and hard shell socket fabricated by a certified prosthetist or
`
`technician); 2) one (1) to four (4) lamination spacers (equal to the number of prosthetic
`
`finger devices); and 3) two (2) to eight (8) mounting screws(e.g., two (2) per prosthetic
`
`finger device).
`
`[0041]
`
`Some embodiments of the prosthetic device can include (or consist only of)
`
`a custom prosthetic socket (e.g., 194 in Fig. 1C) and the terminal device. The custom
`
`-11-
`
`
`
`PDS0002.USC2
`
`prosthetic socket can be generally fabricated by a certified prosthetist or technician, and
`
`may consists of a soft inner liner (e.g., silicone), and a hard outer shell (e.g., carbon
`
`fiber).
`
`In some embodiments, the terminal device can be a prosthetic partial finger (see,
`
`e.g., 150 in Figs. 1B-1C). The bridge betweenthe terminal device (e.g., prosthetic
`
`finger) and the prosthetic socket can be the mounting bracket 200 asillustrated in Figs.
`
`2A-2C. The mounting bracket 200 may beintegrated into the prosthetic socket by way
`
`of lamination in some embodiments. As such, only a mounting point 210 may be
`
`exposed (Fig. 2A). The mounting point can be usedtofix the prosthetic device to the
`
`prosthetic socket.
`
`[0042]
`
`In accordance with various embodiments, mounting bracket 200 may
`
`include on or morelattice structures 220 (e.g., made of metal) to create a foundation
`
`allowing socket material to adhere. The one or morelattice structures 220 can be
`
`connected in an anatomical alignment via linking members 230. The mounting points
`
`210 may be threaded mounting holes that can be usedto affix the multiple metallattice
`
`structure to a prosthetic finger.
`
`In some embodiments, mounting bracket 200 may
`
`include a mounting tab which can be conformed to a shape of a socket and provide
`
`additional structural support for the multiple metal lattice structures.
`
`[0043]
`
`Fig. 3Aillustrates an alignment guide 300 that may be used in accordance
`
`with one or more embodimentsof the present technology. Fig. 3B illustrates an
`
`example of a lamination dummy 310 (or lamination tool) that may be used in
`
`accordance with some embodiments of the present technology. The alignment guide
`
`300 and lamination tool 320 that can be attached to brackets that may be used in
`
`accordance with one or more embodiments of the present technology.
`
`In some
`
`embodiments, the brackets may be bent to conform to a prosthetic socket(e.g.,
`
`fabricated bycertified prosthetist or technician), and the assembly can be tacked (or
`
`otherwise secured) to the socketprior to lamination. The lamination dummy 310 can
`
`create a void in a finished socket to allow mounting of a partial finger prosthetic device.
`
`The alignment tool 320 can be attached to the lamination dummy asillustrated in the
`
`sequence shownin Fig. 3C. The alignment tool mimics a full range of motion a
`
`prosthetic partial finger prosthetic device in a plane of motion when in useby a patient.
`
`-12-
`
`
`
`PDS0002.USC2
`
`Fitting Process
`
`[0044]
`
`Various embodimentsof the prosthetic finger system can be compatible
`
`with mostprosthetic sockets and installed into the prosthetic socket by a trained
`
`prosthetist or technician. The mounting bracket can be integrated into a custom
`
`prosthetic socket through the following steps; 1) alignment, 2) lamination, and 3) device
`
`installation.
`
`[0045]
`
`Alignment can be performed using the alignment/lamination tool to align the
`
`bracket appropriately on the socket. Two (2) brackets can be attached to the alignment
`
`tool using the mounting screws. The alignment tool/bracket assembly can then be
`
`optimally positioned by the prosthetist on the socket. The bracket tabs can be bent to
`
`conform to the socket shape, and then the mounting brackets are tacked onto the
`
`socket using medical grade adhesive.
`
`[0046]
`
`During the lamination process, socket material can be added to the
`
`assembly to embed the mounting bracket tabs into the socket. The
`
`alignment/lamination tool can beleft in place during lamination to maintain the mounting
`
`location for each prosthetic finger. The tool prevents any socket material or resin from
`
`obstructing the prosthetic finger mounting space. After lamination, the
`
`alignment/lamination tool can be removed, and each prosthetic finger can be bolted
`
`onto the mounting bracket using two (2) mounting screws in some embodiments.
`
`[0047]
`
`The following features of various embodiments of the prosthetic finger
`
`mounting bracket provide several competitive advantages over other technologies:
`
`1) Exposed mounting hole.
`
`In accordance with various embodiments, the
`
`mounting hole on the mounting bracket can be exposed after lamination,
`
`providing an easy point of attachment for the prosthetic finger. Attachment
`
`points for competing technologies are inside the socket, which complicates
`
`installation.
`
`2) Bracket location.
`
`In some embodiments, the mounting bracket captures the
`
`prosthetic finger knuckle track beneath it, providing a low-profile installation.
`
`In contrast, the mounting brackets of competing technologies lie underneath
`
`the terminal device, increasing build height.
`
`-13-
`
`
`
`PDS0002.USC2
`
`3) Thin bracketprofile.
`
`In some embodiments, the mounting bracket can be
`
`made of stainless steel and may have an optimized thickness to provide
`
`enough stability for the prosthetic finger device while maintaining enough
`
`malleability to easily bend it to conform to the socket shape. The thin bracket
`
`also enables a low-profile installation.
`
`= Relief holes.
`
`In some embodiments, holes can be strategically placed
`
`throughout the mounting bracket tabs to promote bonding during lamination
`
`for added strength, and to facilitate malleability during alignment prior to
`
`lamination.
`
`[0048]
`
`Figs. 4A-4B illustrates a partial prosthetic device in an extended 400 and
`
`flexed 450 position according to one or more embodiments of the present technology.
`
`In accordance with various embodiments, the ratcheting mechanism provides multiple
`
`(e.g., ten) distinct amounts of finger flexion. The push button can allow for the finger to
`
`be extended when engaged. A spring-back capability, present in some embodiments,
`
`can extend the finger after reaching full finger flexion, enabling one-handed use. The
`
`mounting track 460 can provide a center of rotation about the physiological joint
`
`recreating the physiological kinematics.
`
`In some embodiments, a metal laser sintering
`
`3D printer (see, e.g., Fig. 10) can be used to manufacture the componentsallowsfor
`
`unique mechanical designs to provide high strength at a low weight. The fingers can
`
`also be scaled to larger or smaller hand sizes and customized to match the
`
`physiological hand.
`
`[0049]
`
`Figs. 5A-5D illustrate various views of an assembled partial system 500 in
`
`accordance with some embodiments of the present technology.
`
`In the embodiments
`
`illustrated in Figs. 5A-5D, the assembled partial system 500 can include a proximal
`
`phalange 510, a distal phalange 520 coupled to the proximal phalange 510 creating a
`
`joint 530, and a curved knuckle track 540 moveably coupled to the proximal phalange
`
`510.
`
`In some embodiments, the curved knuckle track, the proximal phalange, and the
`
`distal phalange include a ratcheting mechanism to contact multiple teeth to allow
`
`movement in onlyafirst direction while the ratcheting mechanism is engaged. A
`
`release button (e.g., 175, shownin Fig. 1B), when engaged, disengages the ratcheting
`
`-14-
`
`
`
`PDS0002.USC2
`
`mechanism from the multiple teeth allowing a load from a spring (or other elastic
`
`restorative force) to move the proximal phalange 510 or the distal phalange 520 in a
`
`second direction.
`
`[0050]
`
`In some embodiments, curved knuckle track 540 can include an aperture
`
`550 allow for connection of one end of a linking bar or chain 560. Asillustrated in Figs.
`
`5A-5D, the linking bar or chain 560 maybepositioned internally to tot he assembled
`
`partial system 500 connecting the curved knuckle track to the distal phalange 520
`
`causing flexion of the distal phalange 520 relative to the proximal phalange 510 via joint
`
`530. Some embodiments can include props 168 (also shownin Fig. 1B), when
`
`engaged, disengage the release button from the ratcheting mechanism allowing a load
`
`from a spring to move the proximal phalange or the distal phalange in the second
`
`direction. The curved knuckle track 540 can include a channel 169 (e.g., as shownin
`
`Figs. 4A and 4B) on lateral edges ofa first side to allow the props 168 to engage.
`
`In
`
`some embodiments, the curved knuckle track 540 can have protruding stopsata first
`
`end corresponding to full flexion of a finger created by the proximal phalange 510 and
`
`the distal phalange 520. The protruding stops may be adjustable or moveable along the
`
`curved knuckle track 540 resulting in a change in the full flexion of the finger created by
`
`the proximal phalange 510 and the distal phalange 520.
`
`In some embodiments, the
`
`proximal phalange reaches full flexion at the end of the curved knuckle track and
`
`activates a full flexion spring release point to disengage the ratcheting mechanism.
`
`[0051]
`
`Fig. 6 illustrates an exploded view 600 of a partial finger system illustrating
`
`various component that may be present in accordance with one or more embodiments
`
`of the present technology. Asillustrated in Fig. 6, some embodiments of the partial
`
`finger system mayinclude a distal phalange 610, a connecting rod 620, a proximal
`
`phalange 630, link bar 640, a release mechanism 650, knuckle track 660, ratcheting
`
`mechanism 670, and a screw 680. The distal phalange 610 can be coupled to the
`
`proximal phalange 630 using screw 680 (or other coupling member). The knuckle track
`
`660 can be formed in an arc and configured to be coupled to the proximal phalange 630
`
`via rails or bars alongside the knuckle track 660. Figs. 7A-7Cillustrate various viewsof
`
`a knuckle track 660 that may be used in various embodiments of the present
`
`technology.
`
`-15-
`
`
`
`
`
`[0052] The knuckle track can include multiple teeth formed onafirst side on which
`
`PDS0002.USC2
`
`the proximal phalange 630 slides along. The ratcheting mechanism 670 can contact the
`
`multiple teeth to allow sliding in only a first direction while the ratcheting mechanism is
`
`engaged. The release button 650 can coupledto the proximal phalange 630 using bar
`
`640. Release button 650 when pressed can rotate around a pivot point created by bar
`
`640 and disengage the ratcheting mechanism from the multiple teeth (e.g., at leastfive,
`
`ten, fifteen, or more) to allow the distal phalange 610 and/or proximal phalange 630 to
`
`slide in a second direction.
`
`[0053]
`
`In some embodiments, the knuckle track 660 rounds in a lateral direction
`
`anda transverse direction relative to the multiple teeth so that the arc forms a sector of
`
`a sphere. The distal phalange 610, the knuckle track 660, and the release button 650
`
`mayall be printed using additive manufacturing techniques and systems (e.g., a three-
`
`dimensional printer).
`
`In some embodiments, a design tool may automatically scale
`
`(e.g., by a computer system) dimensions of the device based on a parameterized model
`
`of the device and wherein the computer system controls the three-dimensional printer to
`
`print the device in accordance with the dimensions. The link bar 640 and distal
`
`phalange 610 can be three-dimensionally printed assembledwith a live-hinge in some
`
`embodiments. One or more props 675 and the proximal phalange 630 maybe printed
`
`by a three-dimensional printer assembled with a live-hinge (e.g., live-hinge 181, as
`
`shown in Fig. 1B). The proximal phalange 630 and the distal phalange 610 may be
`
`shapedin a form of a finger, thumb, or a toe.
`
`In addition, in some embodiments, partial
`
`finger system mayinclude a ridge simulating a fingernail on the distal phalange 610.
`
`[0054]
`
`The connecting rod 620 can have a proximal end and a distal end. The
`
`proximal end can be affixed to the knuckle track 660 and the distal end is affixed to the
`
`distal phalange 610. For example, in some embodiments, the proximal phalange 630
`
`may include an opening through which the connecting rod 620 is positioned. As the
`
`proximal phalange 630 is slides along the knuc
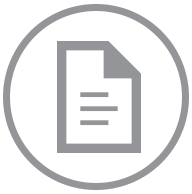
Accessing this document will incur an additional charge of $.
After purchase, you can access this document again without charge.
Accept $ ChargeStill Working On It
This document is taking longer than usual to download. This can happen if we need to contact the court directly to obtain the document and their servers are running slowly.
Give it another minute or two to complete, and then try the refresh button.
A few More Minutes ... Still Working
It can take up to 5 minutes for us to download a document if the court servers are running slowly.
Thank you for your continued patience.
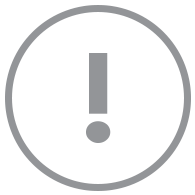
This document could not be displayed.
We could not find this document within its docket. Please go back to the docket page and check the link. If that does not work, go back to the docket and refresh it to pull the newest information.
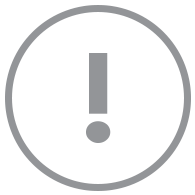
Your account does not support viewing this document.
You need a Paid Account to view this document. Click here to change your account type.
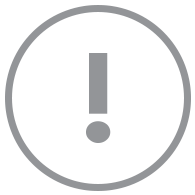
Your account does not support viewing this document.
Set your membership
status to view this document.
With a Docket Alarm membership, you'll
get a whole lot more, including:
- Up-to-date information for this case.
- Email alerts whenever there is an update.
- Full text search for other cases.
- Get email alerts whenever a new case matches your search.
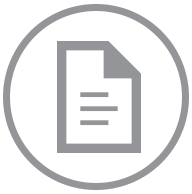
One Moment Please
The filing “” is large (MB) and is being downloaded.
Please refresh this page in a few minutes to see if the filing has been downloaded. The filing will also be emailed to you when the download completes.
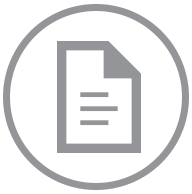
Your document is on its way!
If you do not receive the document in five minutes, contact support at support@docketalarm.com.
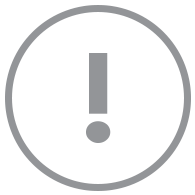
Sealed Document
We are unable to display this document, it may be under a court ordered seal.
If you have proper credentials to access the file, you may proceed directly to the court's system using your government issued username and password.
Access Government Site