`TACKY ADHESIVE LAYER, TRANSPARENT SURFACE MATERIAL HAVING TACKY
`ADHESIVE LAYER, AND DOUBLE-SIDED TACKY-ADHESIVE FILM
`
`Data originating from sources other than the EPO may not be accurate, complete, or up to date.
`
`The wording below is an initial machine translation of the original publication. To generate a version using the
`latest translation technology, go to the original language text and use Patent Translate.
`
`Production method of transparent surface material with adhesive layer, transparent surface material with
`adhesive layer, double-sided adhesive film
`
`[0001] The present invention relates to a method for producing a transparent surface material with an adhesive
`layer, a transparent surface material with an adhesive layer, and a double-sided adhesivefilm.
`
`[0002] DESCRIPTION OF RELATED ARTThe display apparatus by which the surface of the display panel
`(object to be bonded) was protected by the transparent surface material is known conventionally (for example,
`refer patent document 1). In a display device in which a display panel is protected by a transparent surface
`material, a transparent surface material with an adhesive layer having an adhesive layer attached to one surface
`of the transparent surface material is bonded to the surface of the display panel via the adhesive layer. It
`manufactures by bonding the display panel with the adhesion layer by which the adhesion layer was stuck on
`one surface of the display panel on the surface of a transparent surface material through the adhesion layer. In
`the following description, the case where the transparent surface material to which the adhesive layer is attached
`is attached to the display panel will be described as an example.
`
`[0003] In addition, "transparent" said here means having transparency with respectto visible light generally.
`Therefore, the “transparent surface material” also means a surface material having optical transparency to
`visible light.
`
`
`
`
`FEIBRABRHES 201171489905
`
`
`
`[0004]
`
`[0005] By the way, when manufacturing the transparent surface material with the adhesion layer mentioned
`above, a double-sided adhesive film in which separators (also referred to as a protective film and a release film)
`are peelably attached to both sides of the adhesion layer is prepared in advance Do. Andafter peeling one
`separator from this double-sided adhesive film, the transparent surface material can be efficiently manufactured
`by sticking a transparent surface material on the surface of an adhesive layer. Moreover,in the case of this
`manufacturing method, it can respond to the further enlargementof the transparent surface material with an
`adhesion layer. Furthermore, if this manufacturing method is performed by a continuousprocess, the production
`efficiency of the transparent layer with the adhesive layer can be enhanced.
`
`[0006] An aspect of the present invention aims to provide a method for producing a transparent surface material
`with a pressure-sensitive adhesive layer, a transparent surface material with a pressure-sensitive adhesive layer,
`and a double-sided pressure-sensitive adhesive film, which can improve productivity.
`
`[0007] In order to achieve the above object, in the method for producing a transparent surface material with an
`adhesive layer according to one aspect of the present invention, an adhesive layer and a metal layer are
`releasably adhered to one surface of the adhesive layer. A double-sided adhesive film comprising a first
`separator provided and a second separator releasably attached to the other surface of the adhesive layeris
`irradiated with laser light from the second separator side, Cutting the second separator and the adhesive layer
`into a sticking area and a non-sticking area, peeling the second separator in the sticking area from the adhesive
`layer, and the second separator And attaching the adhesive area of the pressure-sensitive adhesive layer to the
`transparent surface material, and cutting the double-sided adhesive film at the non-adhesive area.
`
`[0008] Moreover, the transparent surface material with the adhesion layer which concerns on one aspectofthis
`invention can peel on one surface of a transparent surface material, the 1st adhesion layer provided on the said
`transparent surface material, and the said 1st adhesion layer. And a first adhesive layer provided with a metal
`
`
`
`layer, and the first adhesive layer and a second adhesive layer separated from thefirst adhesive layer through a
`groove and one surface of whichis attachedto the first separator. And a second separator attached to the other
`surface of the second adhesive layer.
`
`[0009] Moreover, the double-sided pressure-sensitive adhesive film according to one aspect of the present
`invention comprises a pressure-sensitive adhesive layer, a first separator attached releasably to one surface of
`the pressure-sensitive adhesive layer, and a metal layer provided thereon; A second separator releasably attached
`to the other surface is provided, and the second separator and the adhesive layer are each cut into a plurality of
`attached areas and a non-adheredarea..
`
`[0010] As described above, according to one aspect of the present invention, it is possible to provide a method
`for producing a transparent surface material with a pressure-sensitive adhesive layer, a transparent surface
`material with a pressure-sensitive adhesive layer, and a double-sided pressure-sensitive adhesive film that can
`improve productivity.
`
`[0011] It is sectional drawing which showsschematic structure of the transparent surface material with the
`adhesion layer which concerns on one Embodimentofthis invention.It is sectional drawing which shows
`schematic structure of a display apparatus provided with the display panel in whichthe said transparent layer
`with the adhesion layer shown in FIG. 1 was bonded. BRIEF DESCRIPTION OF THE DRAWINGSItis
`sectional drawing which shows schematic structure of the double-sided adhesive film which concerns on one
`Embodimentofthis invention. It is a perspective view which shows the raw fabric of a double-sided adhesive
`film. It is a schematic diagram which showsschematic structure of the manufacturing apparatus used for
`manufacture of the transparent surface material with the adhesion layer shown in FIG. It is a figure for
`demonstrating the manufacturing processof the transparent surface material with the adhesion layer shown in
`FIG. 1, and is a perspective view which shows the process of giving a cutting process with respect to an original
`fabric. It is a figure for demonstrating the manufacturing process of the transparent surface material with the
`adhesion layer shownin FIG. 1, and is sectional drawing which shows the state which cut-processed with
`respect to the original fabric. It is a figure for demonstrating each manufacturing process of the transparent
`surface material with an adhesion layer shownin FIG. 1, and is a perspective view which shows the process of
`peeling the 2nd separator of the part used as a double-sided adhesive film from raw fabric. It is a figure for
`demonstrating each manufacturing processof the transparent surface material with an adhesion layer shownin
`FIG. 1, and is sectional drawing which shows the state which removed the 2nd separator of the part used as a
`double-sided adhesive film from a raw fabric. It is a figure for demonstrating each manufacturing process of the
`transparent surface material with an adhesion layer shownin FIG. 1, and is a perspective view which shows the
`processofsticking a transparent surface material on the adhesion layer on a Ist separator. It is a figure for
`demonstrating each manufacturing processof the transparent surface material with an adhesion layer shown in
`FIG. 1, and is sectional drawing which shows the state which stuck the transparent surface material on the
`adhesion layer on a Ist separator.
`
`[0012] Hereinafter, embodiments of the present invention will be described in detail with reference to the
`drawings. In the following description, in order to make each componenteasyto see, the scale of dimensions
`may be shown differently depending on the componentin the drawings.
`
`[0013] First, an outline of a method for producing a transparent surface material with a pressure-sensitive
`adhesive layer using a double-sided pressure-sensitive adhesive film will be described. First, a long strip-shaped
`double-sided adhesive comprising an adhesivelayer, a first separator peelably attached to one surface of the
`adhesive layer, and a second separator peelably attached to the other surface of the adhesive layer Prepare a film
`source. It is necessary to cut out the double-sided adhesive film corresponding to the size of the transparent
`surface material from the raw fabric of the double-sided adhesive film by punchingorthe like. A transparent
`surface material with an adhesive layer is manufactured by peeling off one separator of the cut-out double-sided
`adhesive film and sticking to a transparent surface material.
`
`[0014] The pressure-sensitive adhesive layer-carrying transparent surface material is for peeling off the
`separator andsticking it to the object to be bonded, and therefore the separator having a larger area than the
`pressure-sensitive adhesive layer is easier to peel off. Therefore, after the said punching process,the operation|
`work which affixes the separator on oneside to a bigger thing was needed, and the process was complicated.
`
`
`
`[0015] Moreover, in the punching process using the above-mentioned punching blade,after the adhesive layer is
`cut, the cut surface of the adhesive layer may be attached between the portion to be the double-sided adhesive
`film and the margin portion, There is a problem that the possibility of failure is high. For example, when there is
`a possibility that display unevenness may occur in the liquid crystal panel as in a liquid crystal panel of IPS
`mode, adhesion with a low elastic modulus (high flexibility) in the bonding step with the transparent surface
`material via the adhesive layer Layers may be used.In this case, reattachment on the cut surface is particularly
`likely to occur in the adhesive layer having a low elastic modulus.
`
`[0016] Moreover,it is also possible to manufacture the transparent surface material with an adhesion layer by a
`continuous process as follows. First, a long strip-shaped double-sided adhesive comprising an adhesive layer, a
`first separator peelably attached to one surface of the adhesive layer, and a second separator peelably attached to
`the other surface of the adhesive layer The raw material of this double-sided adhesive film is subjected to a
`punching process using a punching blade while the raw material of the film is conveyed. At this time,the first
`separator is formed by punching a punching blade from the second separator side without cutting the first
`separator and by a depth sufficient to cut the second separator and the adhesive layer. The second separator and
`adhesive layer on top are cut into a size (shape) corresponding to the double-sided adhesive film. In addition, in
`order to facilitate the punching process onthe raw fabric, a long strip-shaped raw fabric may becut into a
`predeterminedsize in advance as a step before the punching process.
`
`[0017] Moreover, since this punching processis continuously performed with respect to the raw fabric of the
`double-sided adhesive film conveyed, the part used as the said double-sided adhesive film is formed along with
`the conveyance direction on a Ist separator. become.
`
`[0018] Next, leaving the part to be the double-sided adhesive film from the raw fabric of the double-sided
`adhesive film, the second separator and the adhesive layer in the other margin part and the second onthe part to
`be the double-sided adhesive film Peel away from the separator.
`
`[0019] Next, a transparent surface material is stuck on the adhesive layer in the part used as the said double-
`sided adhesive film. The transparent surface material is sequentially attached to the portion to be the double-
`sided pressure-sensitive adhesive film aligned in the transport direction described above. Thereafter, the first
`separator is cut at the margin, that is, between the portions to be the double-sided adhesive film. Thereby, the
`transparent layer with the adhesive layer can be produced by a continuous process or a semi-continuousprocess.
`
`[0020] When manufacturing the above-mentioned transparent layer with adhesive layer continuously, leaving
`only the adhesive layer part and removing the adhesive layer and the second separator in the margin, the double-
`sided adhesive film and the transparent layer are When bonding together,the level | step difference between an
`adhesive layer part and a margin part is large, and the problem which can not be pasted well mayarise.
`Therefore, there is a need for a morereliable and efficient method of manufacturing a transparent surface
`material with an adhesivelayer.
`
`[0021] (Adhesive Layer-Containing Transparent Surface Material) First, an adhesive layer-containing
`transparent surface material 1 shown in FIG. 1, for example, will be described as an embodimentofthe present
`invention. In addition, FIG. 1 is sectional drawing which shows schematic structure of the transparent surface
`material 1 with an adhesionlayer.
`
`[0022] The transparent surface material 1 with the adhesive layer is formed by the transparent surface material 5
`bonded via the adhesive layer 2 to the surface of the display panel (bonded material) 101 includedin the display
`device 100 described later. Although it can be used for the use etc. which protect the surface of the object 101, it
`is not restricted to this use.
`
`[0023] Specifically, as shown in FIG. 1, the adhesive layer-attached transparent surface material 1 is adhered to
`the adhesive layer 2 and one surface 2 a of the adhesive layer 2 so as to be peelable, and the metal layer 3 is
`provided. Thefirst separator 4, the transparent surface material 5 attached to the other surface 2 b of the
`adhesive layer 2, the second separator 7 attached releasably to the other surface of the adhesive layer 2, and the
`adhesive layer 2 are transparent A groove portion 9 is provided to divide between a bondedportion (bonded
`region) of the face material 5 and a bonded portion (non-bondedregion) of the second separator 7.
`
`[0024] (Adhesive Layer) The adhesive layer 2 is formed by curing a liquid pressure-sensitive adhesive or a
`precursor material of the pressure-sensitive adhesive, and is made of a transparent resin composition having
`adhesiveness. Specifically, as the pressure-sensitive adhesive, a photocurable resin composition or a
`
`
`
`thermosetting resin composition can be used. Among them, it is preferable to use a photocurable resin
`composition containing a curable compoundand a polymerization initiator from the viewpoint of being curable
`at low temperature and having a high curingrate.
`
`[0025] The curable compoundcontained in the pressure-sensitive adhesive has a curable group and has a
`numberaverage molecular weight of 1000 to 100000, from the viewpoint of easy adjustmentof the viscosity,
`and one or more of oligomer (A) having a number average molecular weight of 1000 to 100000, and a curable
`group. And containing at least one monomer(B) having a molecular weight of 125 to 600, and the proportion of
`the monomer(B) is the total (100% by mass) of the oligomer (A) and the monomer(B) It is preferable to use
`what is 20 mass%-80 mass% among them.
`
`[0026] Examples of the curable group of the oligomer (A) include addition polymerizable unsaturated groups
`(for example, acryloyloxy group, methacryloyloxy group and the like), combinations of unsaturated groups and
`thiol groups, and the like. Among them,as the curable group of the oligomer(A), it is preferable to use a group
`selected from an acryloyloxy group and a methacryloyloxy group from the viewpoint of a high curing speed and
`a highly transparent adhesive layer.
`
`[0027] As an oligomer (A), what has an average of 1.8-4 curable groups per molecule from the point of
`hardenability and mechanical characteristics is preferable. As an oligomer (A), the urethane oligomer which has
`a urethane bond, the poly (meth) acrylate of polyoxyalkylene polyol, the poly (meth) acrylate of polyester
`polyol, etc. are mentioned. In addition, as the oligomer(A), it is preferable to use a urethane oligomer (A1) from
`the viewpoint that the mechanical properties and the adhesion after curing can be widely adjusted by the
`molecular design of the urethane chain and the like. Moreover, an oligomer (A) may be used individually by 1
`type, and may use 2 or more types together.
`
`[0028] Examples of the curable group of the monomer(B) include addition polymerizable unsaturated groups
`such as acryloyloxy group and methacryloyloxy group, or a combination of unsaturated group andthiol group.
`Among them, as the curable group of the monomer(B), it is preferable to use a group selected from an
`acryloyloxy group and a methacryloyloxy group from the viewpoint of a high curing rate and a highly
`transparent adhesive layer.
`
`[0029] The monomer(B) preferably contains a monomer (B3) having a hydroxyl group from the viewpoint of
`adhesion and solubility of various additives. As a monomer (B3) which has a hydroxy! group, it is preferable to
`use the hydroxy acrylate which has a hydroxyl group having a hydroxy] numberof 1 to 2 and a carbon number
`of 3 to 8 or a hydroxy methacrylate. Specifically, for example, 2-hydroxypropyl acrylate, 2-hydroxybutyl
`acrylate, 4-hydroxybuty] acrylate, 6-hydroxyhexyl] acrylate, 2-hydroxypropyl methacrylate, 2-hydroxybuty]
`methacrylate, 4-hydroxybutyl methacrylate, 6 -Hydroxyhexy] methacrylate and the like. Among these, 4-
`hydroxybutyl acrylate and 2-hydroxybutyl methacrylate are particularly preferably used. Moreover, a monomer
`(B) may be used individually by 1 type, and may use 2 or more types together.
`
`[0030] The adhesive may contain the following non-curable oligomers (D). Specifically, this non-curable
`oligomer (D) is an oligomer having a hydroxyl group which doesnot cure with the oligomer (A) and the
`monomer(B) at the time of curing, and its number average molecular weight (Mn) is 400 to 8000. The number
`of hydroxyl groups per molecule is 0.8 to 3.
`
`[0031] When the non-curable oligomer(D)is contained, the non-curable oligomer (C) after curing by the
`interaction between the hydroxyl group derived from the cured product containing the monomer (B3) and the
`hydroxy] group of the non-curable oligomer(D)It is easy to obtain the effect of stabilizing D). Also, it is
`speculated that the interaction between the monomer(B3) and the non-curable oligomer (D) involves hydrogen
`bonding.
`
`[0032] Examples of the non-curable oligomer (D) containing a hydroxyl group include high molecular weight
`polyols and the like. Among them,as the non-curable oligomer (D), it is preferable to use polyoxyalkylene
`polyol, polyester polyol and polycarbonate polyol. The non-curable oligomer (D) improves the affinity of the
`pressure-sensitive adhesive before curing by including the polyol used for the synthesis of the oligomer(A).
`Moreover, a non-curable oligomer (D) may be used individually by 1 type, and may use 2 or more types
`together.
`
`[0033] Examples of the polymerization initiator include photopolymerization initiators of acetophenone type,
`ketal type, benzoin or benzoin ether type, phosphine oxide type, benzophenonetype, thioxanthone type, quinone
`
`
`
`type and the like. By using two or more types of polymerization initiators having different absorption
`wavelength ranges in combination, the curing time can be further accelerated or the surface curability of the
`adhesive layer 2 can be enhanced.
`
`[0034] The viscosity of the adhesive or the precursor material of the adhesive is preferably 1 Pa - s to 100 Pa-s,
`more preferably 2 Pa - s to 50 Pa- s, and 3 Pa- s to 30 Pa- s Is more preferred. If the viscosity of the pressure -
`sensitive adhesive or the precursor material of the pressure-sensitive adhesive is 1 Pa - s or more, the pressure-
`sensitive adhesive or the pressure-sensitive adhesive precursor can sufficiently maintain the height of the layer.
`On the other hand, if the viscosity of the pressure-sensitive adhesive or the precursor material of the pressure-
`sensitive adhesive is 100 Pa - s orless, the pressure-sensitive adhesive or the precursor material of the pressure-
`sensitive adhesive can be easily applied. In the present embodiment, the viscosity of the pressure-sensitive
`adhesive or the precursor material of the pressure-sensitive adhesive at 25 ° C. was measured using an E-type
`viscometer.
`
`[0035] The shear modulusofelasticity of the adhesive layer 2 at 25 ° C. is preferably 10 3 Pa to 10 6 Pa, more
`preferably 10 3 Pa to 10 5 Pa, and 10 3 Pa to 10 4 Pa Morepreferable.
`
`[0036] If the shear modulus of the adhesive layer 2 is 10 3 Pa or more, the shape of the adhesive layer 2 can be
`maintained. In addition, even when the thickness of the adhesive layer 2 is relatively thick, the thickness of the
`adhesive layer 2 can be maintained uniform. Furthermore, when the shear modulusof the adhesive layer 2 is 10
`3 Pa or more, deformation of the adhesive layer 2 can be easily suppressed when the first separator 4 is peeled
`off. On the other hand, if the shear modulusof the adhesive layer 2 is 10 6 Pa or less, good adhesion can be
`exhibited at the interface between the adhesive layer 2 and the display panel. Moreover, about the adhesion layer
`2 by which the transparent surface material 5 was stuck, even if a shear elasticity modulus is made smallin the
`range of 10 3 Pa-10 6 Pa, for example, by supporting by the transparent surface material 5, that The shape can
`be sufficiently maintained.
`
`[0037] In the present embodiment, the shear modulus of the adhesive layer 2 at 25 ° C. was measured using the
`following method. By using a rheometer (modular rheometer Physica MCR-301, manufactured by Anton Paar),
`the gap between the measuring spindle and the transparent plate is made equal to the average thickness of the
`adhesive layer 2 and uncured in the gap Place the pressure sensitive adhesive. Furthermore, while applying heat
`or light required for curing to the uncured pressure-sensitive adhesive, the shear modulusin the curing processis
`measured, and the measured value under predetermined curing conditions is taken as the shear modulusof the
`adhesive layer2.
`
`[0038] The average thickness of the adhesive layer 2 is preferably 0.03 mm to 2 mm, more preferably 0.1 mm to
`0.8 mm,andstill more preferably 0.3 mm to 0.5 mm.If the average thickness of the adhesive layer 2 is 0.03 mm
`or more, the adhesive layer 2 can effectively buffer an impact or the like due to an external force from the
`transparent surface material 5 side, thereby protecting the display panel. In addition, the average thickness of the
`adhesive layer 2 largely changes evenif foreign matter not exceeding the thickness of the adhesive layer 2 is
`mixed between the transparent surface material 1 with the adhesive layer and the display panelat the time of
`manufacturing the display device. There is little impact on transparency performance. Onthe other hand,if the
`average thickness of the adhesive layer 2 is 2 mm orless, the entire thickness of the display device is not
`unnecessarily increased. In addition, as a method of adjusting the thickness of the adhesion layer 2, the method
`of adjusting the quantity of an adhesive at the time of manufacture is mentioned.
`
`[0039] Further, in the present embodiment, since the non-adhesion area is provided around the adhesion area of
`the adhesive layer 2, the adhesion area is protected from the intrusion of foreign matter into the adhesion area,
`and the impact and stress during transportation.It is desirable because it can be done.
`
`[0040] (Metal Layer) The metal layer 3 is for preventing the first separator 4 from being cut when the adhesive
`layer 2 is cut by the irradiation of a laser beam in the manufacturing process of the present embodiment
`describedlater. . It is preferable that the metal layer 3 be disposedin the layer ofthe first separator 4 in
`consideration of adhesion with the adhesive layer 2. However, the metal layer 3 may be disposed on the surface
`of the first separator 4 on the adhesive layer 2 side or the surface on the oppositeside.
`
`[0041] The metal layer 3 preferably has a function as a reflection layer that reflects laser light and a function as
`a heat sink layer that dissipates heat whenthe laser light is irradiated. In addition, the metal layer 3 has a
`function as a protective layer that protects the adhesive layer 2 together with the first separator 4 by being
`disposedin the layerof the first separator 4. As the metal layer 3 having such a function, an Al film or an Al
`
`
`
`alloy film can be suitably used. Also, other metal films may be used. The metal layer 3 is formed, for example,
`after adhering a metal foil to one surface of the resin layer formingthe first separator 4, or after forming a metal
`film using a vacuum deposition method or sputtering method, etc. By laminating another resin layer forming the
`first separator 4, it can be disposed in the layer ofthe first separator 4.
`
`[0042] (First Separator) The first separator 4 has a function as a protective film for protecting one surface of the
`adhesive layer 2 (the surface opposite to the side on which the transparent surface material 5 is adhered) 2a, and
`the adhesive layer 2 It has a function as a release film pasted so as to be peelable on one side 2a. In addition, as a
`forming material of the first separator 4, it is preferable to use a resin material having a small elongation in the
`process of forming the adhesive layer 2, for example, polyethylene terephthalate (PET), polybutylene
`terephthalate (PBT), polyethylene naphthalate ( Examples thereof include polyester resins such as PEN),
`polyamideresins such as nylon-6 and nylon-66, and olefin resins such as biaxially stretched polypropylene.
`When “elongation” is compared for the forming material of the first separator 4, the value of elongation
`obtained by the method defined in ASTM D638 is used.
`
`[0043] The combined thickness of the first separator 4 and the metal layer 3 (hereinafter referred to as protective
`layer thickness) is different depending on the material, but a relatively flexible resin material such as the
`biaxially stretched polypropylene described aboveis used. In the case, the protective layer thickness is
`preferably in the range of 40 um to 120 xm. Whenthe protective layer thickness is 40 um or more, deformation
`of the first separator 4 and the metal layer 3 can be suppressed when peeling the first separator 4 and the metal
`layer 3 from the adhesive layer 2. On the other hand, whenthe protective layer thickness is 120 um orless, the
`first separator 4 and the metal layer 3 are easily bent at the time of peeling and are easily peeled. In addition,as
`shown in FIG.1, it is preferable that the separator 4 have a larger area than the area bondedto the adhesive layer
`2 because it is easy to peel off.
`
`[0044] Moreover, when using resin materials with comparatively small expansion| extension, such as PET
`mentioned above,it is preferable to make protective layer thickness into the range of 20 micrometers-100
`micrometers. Whenthe protective layer thickness is 20 um or more, excessive deformationofthe first separator
`4 and the metal layer 3 can be suppressed when peeling the first separator 4 and the metal layer 3 from the
`adhesive layer 2. On the other hand, whenthe protective layer thickness is 100 jm orless, the first separator 4
`and the metal layer 3 are easily bent at the time of peeling, and it becomeseasy to peel.
`
`[0045] It is preferable that a release agent is applied to the surface ofthe first separator 4 to be attached to the
`pressure-sensitive adhesive layer 2. Thereby, the adhesion to the adhesive layer 2 can be reduced, and the
`adhesive layer 2 can be easily peeled off. The release agent is not particularly limited, and those conventionally
`used as a release agentfor the first separator 4 can be used. In addition, instead of applying the release agent, a
`release film in which the release agent is applied in advanceto a base film such as a polyester film is applied to
`the side of the first separator 4 to be attached to the adhesive layer 2. The release agent may be bondedso as to
`be in contact with the adhesive layer 2. The dry lamination method etc. can be used for bonding of a release
`film. When the dry lamination methodis used, the base film of the release film and the first separator 4 are
`adhered via another bonding layer. Further, instead of the release film, a resin film having a small adhesion to an
`adhesive layer such as polyolefin or fluorine resin may be used by being bondedto the first separator 4. As
`polyolefin, although polyethylene, a polypropylene, etc. are mentioned, it is preferable to use the biaxially
`stretched polypropylene from a viewpoint of mechanicalstrength.
`
`[0046] Thefirst separator 4 is a resin film (referred to asa first film) to which the above-described release agent
`is applied, and a resin film (referred to as a second film) in which the elongation as a base material is desirably
`small. It may be configured to be laminated via the layer 3. In the case of this configuration,it is preferable that
`the surface of the first film to which the release agent is applied be the adhesive layer 2 side and the second film
`be the opposite side to the adhesive layer 2. Thefirst film and the second film may use the same material or
`different materials.
`
`[0047] In addition, a gas barrier layer (not shown) may be provided onthefirst film or the secondfilm. In the
`case of this configuration, the gap at the time of bonding with the display panel can be suppressed. Asthe gas
`barrier layer, a material in which an inorganic compound or an inorganic compoundis dispersed in a resin can
`be used. In addition, a film having a gas barrier effect may be sandwiched betweenthefirst film and the second
`film. When the metal layer 3 has gas barrier properties, the gas barrier layer can be omitted.
`
`[0048] (Second Separator) The second separator 7 has a function as a protective film for protecting the other
`surface 2 b of the adhesive layer 2 located outside the groove 9. The adhesive layer 2 located outside the groove
`
`
`
`9 prevents the other surface 2 b from being exposed by the second separator 7. As a forming material of the
`second separator 7, the same oneasthe first separator 4 can be used.
`
`[0049] (Grooves) The grooves 9 are formed by cutting the adhesive layer 2 by laser beam irradiation in the
`manufacturing process of the embodiment described later. The adhesive layer 2 prevents the cut surface between
`the adhered portion of the transparent surface material 5 and the adhered portion of the second separator 7 from
`adhering by the groove portion 9. The width W of the groove 9 is preferably at least one tenth of the thickness T
`of the adhesive layer 2 (W 2 T/ 10). Thereby,it is possible to prevent the cut surface from adheringafter the
`adhesive layer 2 is cut.
`
`[0050] (Transparent Surface Material) The transparent surface material 5 has a function as a protective plate for
`protecting the display panel. As a forming material of the transparent surface material 5, it is possible to use a
`parallel flat plate, a plate-like glass having a curved surface or a transparent resin, or a laminate of glass and a
`transparent resin. Among them,it is preferable to use glass in terms of transparency,light resistance, low
`birefringence, plane accuracy, surface scratch resistance (abrasion resistance), mechanical strength andthe like.
`
`[0051] Examples of the glass include glass materials such as soda lime glass. Among them,it is more preferable
`to use high-permeability glass (white plate glass) having lower iron content and less bluish color. Moreover, as
`glass, in order to improve safety, tempered glass may be used, and glass to which chemical strengthening has
`been applied maybe used.
`
`[0052] Examples of the transparent resin include highly transparent resin materials such as polycarbonate (PC)
`and polymethyl methacrylate (PMMA). Moreover,as long as it has the required transparency,a resin plate in
`which two or more types of resin materials are laminated may be used, and a resin plate in which a resin
`composition in which two or more types of resin materials or fillers are mixed is a forming material May be
`used.
`
`[0053] The transparent face material 5 may be subjected to surface treatment for improving the interfacial
`adhesion with the adhesive layer 2. As a method of surface treatment, there is mentioned a methodoftreating
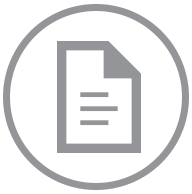
Accessing this document will incur an additional charge of $.
After purchase, you can access this document again without charge.
Accept $ ChargeStill Working On It
This document is taking longer than usual to download. This can happen if we need to contact the court directly to obtain the document and their servers are running slowly.
Give it another minute or two to complete, and then try the refresh button.
A few More Minutes ... Still Working
It can take up to 5 minutes for us to download a document if the court servers are running slowly.
Thank you for your continued patience.
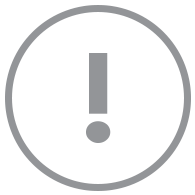
This document could not be displayed.
We could not find this document within its docket. Please go back to the docket page and check the link. If that does not work, go back to the docket and refresh it to pull the newest information.
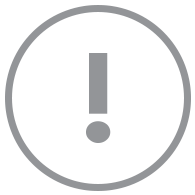
Your account does not support viewing this document.
You need a Paid Account to view this document. Click here to change your account type.
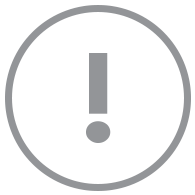
Your account does not support viewing this document.
Set your membership
status to view this document.
With a Docket Alarm membership, you'll
get a whole lot more, including:
- Up-to-date information for this case.
- Email alerts whenever there is an update.
- Full text search for other cases.
- Get email alerts whenever a new case matches your search.
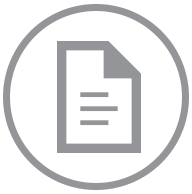
One Moment Please
The filing “” is large (MB) and is being downloaded.
Please refresh this page in a few minutes to see if the filing has been downloaded. The filing will also be emailed to you when the download completes.
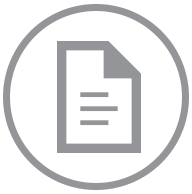
Your document is on its way!
If you do not receive the document in five minutes, contact support at support@docketalarm.com.
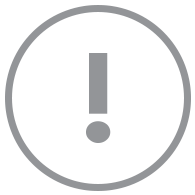
Sealed Document
We are unable to display this document, it may be under a court ordered seal.
If you have proper credentials to access the file, you may proceed directly to the court's system using your government issued username and password.
Access Government Site