`
`(AMAA AOU CAAATA
`
`(10) International Publication Number
`WO 2017/194289 Al
`
`= a
`
`WIPO! PCT
`
`(19) World Intellectual Property
`Organization
`International Bureau
`
`(43) International Publication Date
`16 November 2017 (16.11.2017)
`
`(51) International Patent Classification:
`GO03F 7/20 (2006.01)
`GO3F 9/00 (2006.01)
`GOLN 21/956 (2006.01)
`HOLL 21/66 (2006.01)
`
`(21) International Application Number:
`
`PCT/EP2017/059474
`
`(22) InternationalFiling Date:
`
`21 April 2017 (21.04.2017)
`
`English
`English
`
`(25) Filing Language:
`(26) Publication Language:
`.
`(30) Priority Data:
`EP
`12 May 2016 (12.05.2016)
`16169384.1
`12 September 2016 (12.09.2016) EP
`16188380.6
`29 March 2017 (29.03.2017)
`EP
`17163586.5
`(71) Applicant: ASML NETHERLANDSB.V.[NL/NL]; P.O.
`Box 324, 5500 AH Veldhoven (NL).
`
`(72) Inventors: CEKLI, Hakki, Ergun; P.O. Box 324, 5500
`AH Veldhoven (NL). ISHIBASHI, Masashi; P.O. Box
`324, 5500 AH Veldhoven (NL). VAN DE VEN, Wendy,
`Johanna, Martina; P.O. Box 324, 5500 AH Veldhoven
`(NL). ROELOEFS, Willem, Seine, Christian; P.O. Box
`324, 5500 AH Veldhoven (NL). MC NAMARA,Elliott,
`Gerard; P.O. Box 324, 5500 AH Veldhoven (NL). RAH-
`MAN, Rizvi; P.O. Box 324, 5500 AH Veldhoven (NL).
`KUPERS, Michiel; P.O. Box 324, 5500 AH Veldhoven
`(NL). SCHMITT-WEAVER,Emil, Peter; P.O. Box 324,
`5500 AH Veldhoven (NL). DELVIGNE, Erik, Henri,
`Adriaan; P.O. Box 324, 5500 AH Veldhoven (NL).
`
`(74) Agent: PETERS, John; P.O. Box 324, 5500 AH Veld-
`hoven (NL).
`(81) Designated States (unless otherwise indicated, for every
`kind of national protection available): AE, AG, AL, AM,
`AO, AT, AU, AZ, BA, BB, BG, BH, BN, BR, BW, BY, BZ,
`CA, CH, CL, CN, CO, CR, CU, CZ, DE, DJ, DK, DM, DO,
`
`(54) Title: METHOD OF OBTAINING MEASUREMENTS, APPARATUS FOR PERFORMING A PROCESS STEP AND
`METROLOGY APPARATUS
`
`
`
`[_ 606"
`., oS 4
`
`an
`
` 2
`
`
`Fig. 6
`
`(57) Abstract: Measurements are obtained fromlocations across a substrate (W') before or after performinga lithographic process step.
`Examples of such measurements include alignment measurements madeprior to applying a pattern to the substrate, and measurements of
`performance parameters such as overlay, after a pattern has been applied. A set of measurement locations (606, 606' or 606") is selected
`from amongall possible measurement locations (302). At least a subset of the selected measurementlocations are selected dynamically
`(202c), in response to measurements obtained using a preliminary selection (610) of measurement locations. Preliminary measurements
`of height can be used to select measurement locations for alignment. In another aspect of the disclosure, outlier measurements are
`detected based on supplementary data such as height measurements orhistoric data.
`
`[Continued on next page]
`
`
`
`
`
`wo2017/194299A.IIINININMIINANITATA0AA
`
`
`
`WO 2017/194289 A[IMUM CIMATMT! TAEAAUT
`
`DZ, EC, EE, EG, ES, FL, GB, GD, GE, GH, GM,GT, HN,
`HR, HU,ID, IL, IN, IR, IS, JP, KE, KG, KH, KN, KP, KR,
`KW, KZ, LA, LC, LK, LR, LS, LU, LY, MA, MD, ME, MG,
`MK, MN, MW, MX, MY, MZ, NA, NG, NL NO, NZ, OM,
`PA, PE, PG, PH, PL, PT, QA, RO, RS, RU, RW,SA, SC,
`SD, SL, SG, SK, SL, SM, ST, SV, SY, TIL TJ, TM, TN, TR,
`TT, TZ, UA, UG, US, UZ, VC, VN, ZA, ZM, ZW.
`
`(84) Designated States (unless otherwise indicated, for every
`kind of regional protection available): ARIPO (BW, GH,
`GM,KE, LR, LS, MW, MZ, NA, RW, SD, SL, ST, SZ, TZ,
`UG, ZM, ZW), Eurasian (AM, AZ, BY, KG, KZ, RU,TJ,
`TM), European (AL, AT, BE, BG, CH, CY, CZ, DE, DK,
`EE,ES, FI, FR, GB, GR, HR, HU,IE, IS, IT, LT, LU, LV,
`MC,MK,MT, NL, NO,PL, PT, RO, RS, SE, SL SK, SM,
`TR), OAPI (BF, BJ, CF, CG, CI, CM, GA, GN, GQ, GW,
`KM,ML, MR, NE, SN, TD, TG).
`
`Published:
`
`— with international search report (Art. 21(3))
`
`
`
`WO 2017/194289
`
`PCT/EP2017/059474
`
`METHOD OF OBTAINING MEASUREMENTS, APPARATUS FOR
`PERFORMING A PROCESS STEP AND METROLOGY APPARATUS
`
`BACKGROUND
`
`CROSS-REFERENCE TO RELATED APPLICATIONS
`
`[0001]
`
`This application claims priority of EP application EP16169384 which wasfiled on
`
`May 12, 2016, EP application EP16188380 which was filed on September 12, 2016 and EP
`
`application EP17163586 which was filed on March 29, 2017 which are incorporated herein
`
`in its entirety by reference.
`
`Field of the Invention
`
`[0002]
`
`The present invention relates to methods of obtaining measurements from locations
`
`across one or more substrates. The invention can be applied for example in a lithographic
`
`apparatus, or in a metrology apparatus. The present invention further relates to methods of
`
`manufacturing devices using such lithographic apparatus, and to data processing apparatuses
`
`and computer program products for implementing parts of such a method.
`
`Background Art
`
`[0003]
`
`A lithographic apparatus is a machine that applies a desired pattern onto a substrate,
`
`usually onto a target portion of the substrate. A lithographic apparatus can be used, for
`
`example, in the manufacture of integrated circuits (ICs). In that instance, a patterning device,
`
`which is alternatively referred to as a mask or a reticle, may be used to generate a circuit
`
`pattern to be formed on an individual layer of the IC. This pattern can be transferred onto a
`
`target portion (e.g., comprising part of, one, or several dies) on a substrate (e.g., a silicon
`
`wafer). Transfer of the pattern is typically via imaging onto a layer of radiation-sensitive
`
`material (resist) provided on the substrate. In general, a single substrate will contain a
`
`network of adjacent target portions that are successively patterned. Known lithographic
`
`apparatus include so-called steppers, in which each target portion is irradiated by exposing an
`
`entire pattern onto the target portion at one time, and so-called scanners, in which each target
`
`portion is irradiated by scanning the pattern through a radiation beam in a given direction
`
`(the
`
`“scanning”-direction) while
`
`synchronously scanning the
`
`substrate parallel
`
`or
`
`anti-parallel to this direction.
`
`[0004]
`
`A key performance parameter of the lithographic process is the overlay error. This
`
`error, often referred to simply as “overlay”, is the error in placing product features in the
`
`10
`
`15
`
`20
`
`25
`
`30
`
`35
`
`
`
`WO 2017/194289
`
`2016PO00009WO
`
`2
`
`PCT/EP2017/059474
`
`correct position relative to features formed in previous layers. As device structures become
`
`ever smaller, overlay specifications becomeever tighter.
`
`[0005]
`
`Within the lithographic apparatus, wafer alignment models are conventionally applied
`
`based on measurement of alignment marks provided on the substrate,
`
`the measurements
`
`being made as a preliminary step of every patterning operation. The alignment models
`
`nowadays include higher order models, to correct for non-linear distortions of the wafer. The
`
`alignment models may also be expanded to take into account other measurements and/or
`
`calculated effects such as thermal deformation during a patterning operation. However, the
`
`time available per wafer does not permit measurement of all the alignment marks, and a
`
`compromise between speed and accuracy inevitably has to be made.
`
`[0006]
`
`Currently the overlay crror is controlled and corrected by mcans of mcthods such as
`
`advanced process control (APC) described for example in US2012008127A1 and wafer
`
`alignment models described for example in US2013230797A1. The advancedprocess control
`
`techniques have been introduced in recent years and use measurements of metrology targets
`
`applied to substrates alongside the applied device pattern. The inspection apparatus may be
`
`separate from the lithographic apparatus, or integrated within it.
`
`[0007]
`
`While alignment models and advanced process control have brought great reductions
`
`in overlay, not all errors are corrected. Some of these errors may be uncorrectable noise, for
`
`example, but others are correctable using available techniques
`
`in theory, but not
`
`economically correctable in practice. For example, one can envisage yet higher order models,
`
`but these in turn would require a higher spatial density of position measurements. Again,
`
`even if there is a high spatial density of possible measurementlocations, to actually measure
`
`such a number of measurement
`
`locations would adversely affect
`
`throughput of the
`
`lithographic process of the metrology apparatus.
`
`[0008]
`
`Accordingly, it is common to define a measurement “recipe” that captures the most
`
`important features of a substrate, from the point of view of improving the key performance
`
`parameters, such as overlay. If it is known that a certain type of processing gives rise to a
`
`particular “fingerprint” in the distortions of the substrates that undcrgo that process, the sct of
`
`measurement locations can be selected to capture that fingerprint in a way that maximizes the
`
`chancecorrecting for it in the patterning step. A problem arises, however, in that the process
`
`fingerprints can vary quite widely even with a single lot of wafers. The set of measurement
`
`locations that gives good overlay performance for one wafer may not give good overlay
`
`performance for the next one. The same principles apply to the selection of measurement
`
`locations in a metrology application, on substrates that have already been subject to the
`
`lithographic process.
`
`[0009]
`
`Another problem that affects both alignment and metrology performance is that of
`
`anomalous samples or “outliers”.
`
`In the alignment data, an outlier may be a position
`
`
`
`WO 2017/194289
`
`2016PO00009WO
`
`3
`
`PCT/EP2017/059474
`
`measurement influenced by a very localized cause such as contamination under the wafer.
`
`When this measurement is included in the alignment model, however, the influence of the
`
`anomalous measurement may spread, degrading overlay performance over and unduly wide
`
`area. Similarly, outliers in performance metrology may cause noise and degradation in
`
`advanced performancecontrol loops.
`
`SUMMARYOF THE INVENTION
`
`[0010]
`
`The present invention has the aim of improving relevance of measurement results
`
`(primarily relevance for performance of a lithographic process) without necessarily
`
`increasing the number of measurementlocations required to be measured.
`
`[0011]
`
`According to an aspect of the invention,
`
`there is provided a method of obtaining
`
`measurements from locations across a substrate before or after performing a lithographic
`
`process step, wherein a set of measurement locations is selected from among all possible
`
`measurement locations, and at each selected location a measurement ts made of a property of
`
`a structure on the substrate, wherein at least a subset of the selected measurement locations is
`
`selected dynamically at least partly in response to recognition of a fingerprint associated with
`
`measurements obtained using a preliminary selection of measurement locations.
`
`[0012]
`
`Dynamic selection of the set of measurement locations allows the locations that are
`
`most likely to be relevant for performance improvement to be selected on a per-substrate
`
`basis, without necessarily increasing the total number of measurements and measurement
`
`time. The performance penalty that might otherwise be expected to result from choosing a
`
`limited set of measurement locations can be reduced, even in the presence of process
`variation between substrates.
`
`[0013]
`
`The lithographic process step may be a patterning step performed in a lithographic
`
`apparatus, or it may be a chemical or physical processing step performed in another
`
`apparatus.
`
`[0014]
`
`The measurements made at the preliminary selection of measurementlocations and/or
`
`the measurements made at the selected sect of measurement locations may be made within the
`
`lithographic apparatus or other processing apparatus, or they may be made in a separate
`
`metrology apparatus.
`
`[0015]
`
`The measurements made at the preliminary selection of measurement locations may
`
`be of the type of measurement as the measurements obtained at
`
`the selected set of
`
`measurement locations, or a different type. The measurements made at
`
`the preliminary
`
`selection of measurement locations may made in the same apparatus as the measurements
`
`obtained at the selected set of measurement locations, or a different apparatus.
`
`[0016]
`
`In some examples disclosed herein, locations for alignment measurements (which
`
`measure positional deviations in the plane of the substrate) are dynamically selected based on
`
`10
`
`15
`
`20
`
`25
`
`30
`
`35
`
`
`
`WO 2017/194289
`
`2016PO00009WO
`
`4
`
`PCT/EP2017/059474
`
`alignment measurements at preliminary locations. In other examples, locations for alignment
`
`measurements are dynamically selected based on height measurements
`
`(out-of-plane
`
`positional deviations).
`
`[0017]
`
`Examples of measurements made before a lithographic process
`
`step include
`
`alignment measurements made for positioning a pattern to be applied in a lithographic
`
`apparatus. Examples of measurements made aftcr a lithographic proccss step include
`
`measurements of performance parameter such as overlay.
`
`[0018]
`
`The invention further provides an apparatus for performing a process step in a
`
`lithographic process, the apparatus including a measurement system for making measurement
`
`of a substrate prior to performing said process step, the measurement system being arranged
`
`to obtain mceasurcments at a sclected sct of locations across the substrate using a method
`
`according to the invention as set forth above.
`
`[0019]
`
`The
`
`invention further provides
`
`a metrology apparatus
`
`arranged to obtain
`
`measurements of one or more properties of structures at a selected set of locations across a
`
`substrate using a method according to the invention as set forth above.
`
`[0020]
`
`The invention further provides a method of manufacturing devices including a
`
`lithographic process step, wherein, before or after performing said lithographic process step,
`
`measurements are obtained at a selected set of locations across a substrate by a method
`
`according to the invention as set forth above, and wherein the obtained measurements are
`
`used to adjust parameters of the lithographic process step for the processing of the substrate
`
`and/or further substrates.
`
`[0021]
`
`The invention in a further, independent aspect provides a method of determining a
`
`weighting factor for a measurement made at a measurement location on a substrate, the
`
`method comprising the stepsof:
`
`applying a quality test to the measurement, the quality test being basedat least partly
`
`on supplementary data associated with the measurementlocation; and
`
`determining the weighting factor based on a result of said quality test.
`
`[0022]
`
`The supplementary data in some cmbodiments compriscs statistical data based on
`
`previously processed substrates. The weighting factor can be exploited in various ways, for
`
`example to reduce the influence of outlier measurements on future processing.
`
`[0023]
`
`The apparatus and method of
`
`the invention can be implemented in some
`
`embodiments by modifying control software of existing apparatuses.
`
`[0024]
`
`The invention further provides a computer program product comprising machine-
`
`readable instructions for causing one or more processors to implement aspects of the method
`
`in the apparatus set forth above. The computer program product may comprise said machine
`
`readable instructions stored in a non-transitory storage medium.
`
`10
`
`15
`
`20
`
`25
`
`30
`
`35
`
`
`
`WO 2017/194289
`
`2016PO00009WO
`
`5
`
`PCT/EP2017/059474
`
`BRIEF DESCRIPTION OB'THE DRAWINGS
`
`[0025]
`
`Embodiments of the invention will now be described, by way of example only, with
`
`reference to the accompanying schematic drawings in which:
`
`Tigure | depicts a lithographic apparatus together with other apparatuses forming a production
`
`facility for semiconductor devices;
`
`Figure 2 illustrates schematically measurement and cxposure processes in the lithographic
`
`apparatus of Figure 1, according to knownpractice and modified in accordance with an
`
`embodimentof the present invention;
`
`Figure 3 shows(a) the distribution of measurement locations available for measurement on an
`
`example wafer and (b) an example set of measurementlocations, selected for measurement
`
`during high-volume manufacture;
`
`Figure 4 illustrates (a) an example of a process-induced fingerprint on a semiconductor wafer,
`
`and (b) variation of the fingerprint between wafers in a sample of wafers taken from severallots;
`
`Figure 5 illustrates deviation of performance parameters of the lithographic process, attributable
`
`to using the selected set of measurement locations, over the same sample of wafers shown in
`
`Figure 4 (b);
`
`Figure 6 illustrates a modified method for selecting a set of measurement locations dynamically
`
`for an individual substrate, according to a first embodiment of the present invention;
`
`Figure 7 illustrates deviation of performance parameters of the lithographic process, calculated to
`
`simulate the effect of selecting sets of measurement locations dynamically for each wafer over
`
`the same sample of wafers as Figure 5;
`
`Figure 8 illustrates the spatial distribution of deviation of performance(a) in the case of using the
`
`same selected measurementlocations and (b) using the dynamically selected sets of measurement
`
`locations;
`
`Figure 9 illustrates a method of metrology and process control in a second embodimentof the
`
`present invention;
`
`Figure 10 illustrates the problem of outliers in measurement data, for example alignmentdata in a
`
`real cxample;
`
`Figure 11 illustrates techniques for detecting outliers and reducing their influence in accordance
`
`with various embodiments of the second aspect of the present disclosure;
`
`T'igure 12 illustrates a principle of statistical analysis according to an example outlier detection
`
`method based on principal component analysis;
`
`Figure 13 illustrates detection of outliers using the principle of Figure 12 in the example of
`
`Figure 10;
`
`Figure 14 illustrates improved overlay performance on problem wafers, compared with the
`
`example of Figure 10(a);
`
`10
`
`15
`
`20
`
`25
`
`30
`
`35
`
`
`
`WO 2017/194289
`
`2016PO00009WO
`
`6
`
`PCT/EP2017/059474
`
`Figure 15 illustrates a method of metrology and control in a third embodiment ofthe present
`
`invention, the method comprising (a) an offline process and (b) an inline process;
`
`Figure 16 illustrates height gradient maps and dynamic selection of measurement locationsin the
`
`method of Figure 15; and
`
`Figure 17 illustrates a method of metrology and control in a fourth embodimentof the present
`
`invention, the method comprising (a) an offline process and (b) an inline process.
`
`DETAILED DESCRIPTION OF EXEMPLARY EMBODIMENTS
`
`[0026]
`
`Before describing embodiments of the invention in detail, it is instructive to present
`
`an example environment
`
`in which embodiments of
`
`the present
`
`invention may be
`
`implemented.
`
`[0027]
`
`Figure 1 at 100 showsa lithographic apparatus LA as part of an industrial facility
`
`implementing a high-volume, lithographic manufacturing process. In the present example,
`
`the manufacturing process is adapted for the manufacture of for semiconductor products
`
`(integrated circuits) on substrates such as semiconductor wafers. The skilled person will
`
`appreciate that a wide variety of products can be manufactured by processing different types
`
`of substrates in variants of this process. The production of semiconductor products is used
`
`purely as an example which has great commercial significance today.
`
`[0028]
`
`Within the lithographic apparatus (or “litho tool” 100 for short), a measurement
`
`station MEAis shown at 102 and an exposure station EXP is shown at 104. A control unit
`
`LACUis shown at 106.
`
`In this example, each substrate visits the measurementstation and
`
`the exposure station to have a pattern applied. In an optical lithographic apparatus, for
`
`example, a projection system is used to transfer a product pattern from a patterning device
`
`MAonto the substrate using conditioned radiation and a projection system. This is done by
`
`forming an image ofthe pattern in a layer of radiation-sensitive resist material.
`
`[0029]
`
`The term “projection system” used herein should be broadly interpreted as
`
`encompassing any type of projection system, including refractive, reflective, catadioptric,
`
`magnetic, clectromagnetic and clectrostatic optical systems, or any combination thercof, as
`
`appropriate for the exposure radiation being used, or for other factors such as the use of an
`
`immersion liquid or the use of a vacuum. The patterning MA device may be a mask or
`
`reticle, which imparts a pattern to a radiation beam transmitted or reflected by the patterning
`
`device. Well-known modes of operation include a stepping mode and a scanning mode.Asis
`
`well known, the projection system may cooperate with support and positioning systems for
`
`the substrate and the patterning device in a variety of ways to apply a desired pattern to many
`
`target portions across a substrate. Programmable patterning devices may be used instead of
`
`reticles having a fixed pattern. The radiation for example may include electromagnetic
`
`radiation in the deep ultraviolet (DUV)or extreme ultraviolet (EUV) wavebands. The present
`
`
`
`WO 2017/194289
`
`2016PO00009WO
`
`7
`
`PCT/EP2017/059474
`
`disclosure is also applicable to other types of lithographic process, for example imprint
`
`lithography and direct writing lithography, for example by electron beam.
`
`[0030]
`
`The lithographic apparatus control unit LACU controls all
`
`the movements and
`
`measurements of various actuators and sensors, causing the apparatus to receive substrates W
`
`and reticles MA and to implement the patterning operations. LACU also includes signal
`
`processing and data processing capacity to implement desired calculations relevant to the
`
`operation of the apparatus.
`
`In practice, control unit LACU will be realized as a system of
`
`many sub-units, each handling the real-time data acquisition, processing and control of a
`
`subsystem or component within the apparatus.
`
`[0031]
`
`Before the pattern is applied to a substrate at the exposure station EXP, the substrate
`
`is processed in at the measurement station MEA so that various preparatory steps may be
`
`carried out. The preparatory steps may include mapping the surface height of the substrate
`
`using a level sensor and measuring the position of alignment marks on the substrate using an
`
`alignment sensor. The alignment marks are arranged nominally in a regular grid pattern.
`
`However, due to inaccuracies in creating the marks and also due to deformations of the
`
`substrate that occur throughout
`
`its processing,
`
`the marks deviate from the ideal grid.
`
`Consequently,
`
`in addition to measuring position and orientation of the substrate,
`
`the
`
`alignment sensor in practice must measure in detail the positions of many marks across the
`
`substrate area, if the apparatus is to print product features at the correct locations with very
`
`high accuracy.
`
`[0032]
`
`The lithographic apparatus LA may beof a so-called dual stage type which has two
`
`substrate tables, each with a positioning system controlled by the control unit LACU. While
`
`one substrate on one substrate table is being exposed at the exposure station EXP, another
`substrate can be loaded onto the other substrate table at the measurement station MEAso that
`
`various preparatory steps may be carried out. The measurement of alignment marks is
`
`therefore very time-consuming and the provision of two substrate tables enables a substantial
`
`increase in the throughput of the apparatus.
`
`If the position sensor IF is not capable of
`
`measuring the position of the substrate table whilc it is at the mcasurcment station as well as
`
`at the exposure station, a second position sensor may be provided to enable the positions of
`
`the substrate table to be tracked at both stations. Alternatively, the measurement station and
`
`exposure station can be combined. lor example, it is known to have a single substrate table,
`
`to which a measurement stage is temporarily coupled during the pre-exposure measuring
`
`phase. The present disclosure is not limited to either type of system.
`
`[0033]
`
`Within the production facility, apparatus 100 forms part of a “litho cell” or “litho
`
`cluster” that contains also a coating apparatus 108 for applying photosensitive resist and
`
`other coatings to substrates W for patterning by the apparatus 100. At an output side of
`
`apparatus 100, a baking apparatus 110 and developing apparatus 112 are provided for
`
`
`
`WO 2017/194289
`
`2016PO00009WO
`
`8
`
`PCT/EP2017/059474
`
`developing the exposed pattern into a physical resist pattern. Between all of these
`
`apparatuses,
`
`substrate handling systems
`
`take care of supporting the substrates and
`
`transferring them from one piece of apparatus to the next. These apparatuses, which are often
`
`collectively referred to as the “track”, are under the control of a track control unit which is
`
`itself controlled by a supervisory control system SCS, which also controls the lithographic
`
`apparatus via lithographic apparatus control unit LACU. Thus, the different apparatuses can
`
`be operated to maximize throughput and processing efficiency. Supervisory control system
`
`SCS receives recipe information R which provides in great detail a definition of the steps to
`
`be performedto create each patterned substrate.
`
`[0034]
`
`Oncethe pattern has been applied and developed in the litho cell, patterned substrates
`
`120 are transferred to other processing apparatuses suchasarc illustrated at 122, 124,126. A
`
`wide range of processing steps is
`
`implemented by various apparatuses in a typical
`
`manufacturing facility. For the sake of example, apparatus 122 in this embodiment is an
`
`etching station, and apparatus 124 performs a post-etch annealing step. Further physical
`
`and/or chemical processing steps are applied in further apparatuses, 126, etc.. Numerous
`
`types of operation can be required to make a real device, such as deposition of material,
`
`modification of surface material characteristics (oxidation, doping,
`
`ion implantation etc.),
`
`chemical-mechanical polishing (CMP), and so forth. ‘The apparatus 126 may, in practice,
`
`represent a series of different processing steps performed in one or more apparatuses.
`
`[0035]
`
`As is well known,
`
`the manufacture of semiconductor devices involves many
`
`repetitions of such processing, to build up device structures with appropriate materials and
`
`patterns, layer-by-layer on the substrate. Accordingly, substrates 130 arriving at the litho
`
`cluster may be newly prepared substrates, or they may be substrates that have been processed
`
`previously in this cluster or in another apparatus entirely. Similarly, depending on the
`
`required processing, substrates 132 on leaving apparatus 126 may be returned for a
`
`subsequent patterning operation in the samelitho cluster, they may be destined for patterning
`
`operations in a different cluster, or they may be finished products to be sent for dicing and
`
`packaging.
`
`[0036]
`
`Each layer of the product structure requires a different set of process steps, and the
`
`apparatuses 126 used at each layer may be completely different in type. Further, even where
`
`the processing steps to be applied by the apparatus 126 are nominally the same, in a large
`
`facility, there may be several supposedly identical machines working in parallel to perform
`
`the step 126 on different substrates. Small differences in set-up or faults between these
`
`machines can mean that they influence different substrates in different ways. Even steps that
`
`are relatively commonto each layer, such as etching (apparatus 122) may be implemented by
`
`several etching apparatuses that are nominally identical but working in parallel to maximize
`
`throughput.
`
`In practice, moreover, different layers require different etch processes, for
`
`10
`
`15
`
`20
`
`25
`
`30
`
`35
`
`
`
`WO 2017/194289
`
`2016PO00009WO
`
`9
`
`PCT/EP2017/059474
`
`example chemical etches, plasma etches, according to the details of the material to be etched,
`
`and special requirements such as, for example, anisotropic etching.
`
`[0037]
`
`The previous and/or subsequent processes may be performed in other lithography
`
`apparatuses, as just mentioned, and may even be performed in different types of lithography
`
`apparatus. For example, some layers in the device manufacturing process which are very
`
`demanding in parametcrs such as resolution and overlay may be performed in a morc
`
`advanced lithography tool than other layers that are less demanding. Therefore some layers
`
`may be exposed in an immersion type lithography tool, while others are exposed in a ‘dry’
`
`tool. Some layers may be exposed in a tool working at DUV wavelengths, while others are
`
`exposed using EUV wavelength radiation.
`
`[0038]
`
`In order that the substrates that are exposed by the lithographic apparatus are exposed
`
`correctly and consistently, it is desirable to inspect exposed substrates to measure properties
`
`such as overlay errors between subsequent layers, line thicknesses, critical dimensions (CD),
`
`etc. Accordingly a manufacturing facility in which litho cell
`
`ILC is located also includes
`
`metrology system MET which receives some or all of the substrates W that have been
`
`processed in the litho cell. Metrology results are provided directly or indirectly to the
`
`supervisory control system (SCS) 138. If errors are detected, adjustments may be made to
`
`exposures of subsequent substrates, especially if the metrology can be done soon and fast
`
`enough that other substrates of the same batchare still to be exposed. Also, already exposed
`
`substrates may be stripped and reworked to improve yield, or discarded, thereby avoiding
`
`performing further processing on substrates that are known to be faulty. In a case where only
`
`some target portions of a substrate are faulty, further exposures can be performed only on
`
`those target portions which are good.
`
`[0039]
`
`Also shown in Figure 1 is a metrology apparatus 140 which is provided for making
`
`measurements of parameters of the products at desired stages in the manufacturing process.
`
`A common example of a metrology apparatus in a modern lithographic production facility is
`
`a
`
`scatterometer,
`
`for
`
`example
`
`an angle-resolved scatterometer or
`
`a
`
`spectroscopic
`
`scattcrometcr, and it may be applicd to measure propertics of the developed substrates at 120
`
`prior to etching in the apparatus 122. Using metrology apparatus 140, it may be determined,
`
`for example, that important performance parameters such as overlay or critical dimension
`
`(CD) do not meet specified accuracy requirements in the developed resist. Prior to the
`
`etching step, the opportunity exists to strip the developed resist and reprocess the substrates
`
`120 through the litho cluster. As is also well known, the metrology results 142 from the
`
`apparatus 140 can be used to maintain accurate performance of the patterning operations in
`
`the litho cluster, by supervisory control system SCS and/or control unit LACU 106 making
`
`small adjustments over time, thereby minimizing the risk of products being made out-of-
`
`specification, and requiring re-work. Of course, metrology apparatus 140 and/or other
`
`10
`
`15
`
`20
`
`25
`
`30
`
`35
`
`
`
`WO 2017/194289
`
`2016PO00009WO
`
`10
`
`PCT/EP2017/059474
`
`metrology apparatuses (not shown) can be applied to measure properties of the processed
`
`substrates 132, 134, and incoming substrates 130.
`
`[0040]
`
`The present disclosure concerns the dynamic selection of measurement locations, in
`
`cases where the time available for a set of measurements does not permit measurementofall
`
`possible locations across the substrate. This dynamic selection can be applied in various
`
`operations in the manufacturing facility of Figure 1. For example,
`
`the techniques can be
`
`applied in the selection of measurement locations when measuring alignment marks on the
`
`substrates, as part of the patterning operation. Alternatively, or in addition,
`
`the dynamic
`
`selection of measurementlocations can be applied to the selection of metrology targets in the
`
`metrology apparatus 140. A detailed example will be described in the context of alignment,
`
`which can then be readily applicd in metrology apparatus 140, in a similar manner.
`
`Alignment process background
`
`[0041 ]
`
`Figure 2 illustrates the steps to expose target portions (e.g. dies) on a substrate W in
`
`the dual-stage type of lithographic apparatus, used in the example of Figure |. The process
`
`according to conventional practice will be described first. The present disclosure is not
`
`limited to dual-stage apparatus. The dynamic selection technique disclosed herein can be
`
`applied in any situation where time does not permit measurements of any type to be
`
`measuredat all possible measurement locations on every substrate.
`
`[0042]
`
`On the left hand side within a dotted box are steps performed at a measurement
`
`station MEA, while the right hand side shows steps performed at the exposure station EXP.
`
`From time to time, one of the s
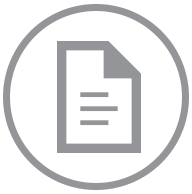
Accessing this document will incur an additional charge of $.
After purchase, you can access this document again without charge.
Accept $ ChargeStill Working On It
This document is taking longer than usual to download. This can happen if we need to contact the court directly to obtain the document and their servers are running slowly.
Give it another minute or two to complete, and then try the refresh button.
A few More Minutes ... Still Working
It can take up to 5 minutes for us to download a document if the court servers are running slowly.
Thank you for your continued patience.
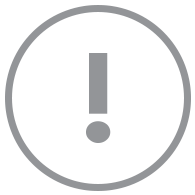
This document could not be displayed.
We could not find this document within its docket. Please go back to the docket page and check the link. If that does not work, go back to the docket and refresh it to pull the newest information.
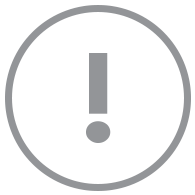
Your account does not support viewing this document.
You need a Paid Account to view this document. Click here to change your account type.
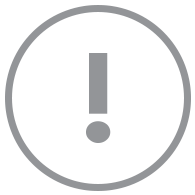
Your account does not support viewing this document.
Set your membership
status to view this document.
With a Docket Alarm membership, you'll
get a whole lot more, including:
- Up-to-date information for this case.
- Email alerts whenever there is an update.
- Full text search for other cases.
- Get email alerts whenever a new case matches your search.
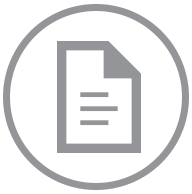
One Moment Please
The filing “” is large (MB) and is being downloaded.
Please refresh this page in a few minutes to see if the filing has been downloaded. The filing will also be emailed to you when the download completes.
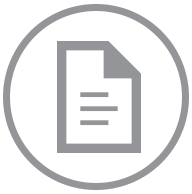
Your document is on its way!
If you do not receive the document in five minutes, contact support at support@docketalarm.com.
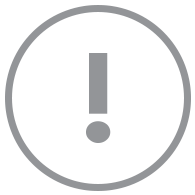
Sealed Document
We are unable to display this document, it may be under a court ordered seal.
If you have proper credentials to access the file, you may proceed directly to the court's system using your government issued username and password.
Access Government Site