`
`Patentamt
`European
`Patent Office
`Office européen
`des brevets
`
`Bescheinigung
`
`Certificate
`
`Attestation
`
`Die angehefteten
`Unterlagen stimmen mit der
`als urspringlich eingereicht
`geltenden Fassung der auf
`dem nachsten Blatt
`bezeichneten europaischen
`Patentanmeldung Uberein.
`
`The attached documents are
`exact copies of the text in
`which the European patent
`application described on the
`following page is deemed to
`have been filed.
`
`Les documentsjoints a la
`présente attestation sont
`conformesautexte,
`considéré comme
`initialement déposé, de la
`demande de brevet
`européen qui est spécifiée a
`la page suivante.
`
`
`
`Patentanmeldung Nr.
`
`Patent application No.
`
`Demande de brevet n°
`
`18199182.9 / EP18199182
`
`The organisation code and number of your priority application, to be used for filing abroad under the Paris
`Convention, is EP18199182.
`
`Der Prasident des Europaischen Patentamts;
`Im Auftrag
`For the President of the European Patent Office
`Le President de l'Office européen des brevets
`p.o.
`
`EPA/EPO/OEB Form 1014
`
`05.17
`
`V. Joseph
`
`
`
`
`
`Anmeldung Nr:
`Application no.:
`Demande no :
`
`18199182.9
`
`Anmelder/ Applicant(s) / Demandeur(s):
`
`ASML Netherlands B.V.
`P.O. Box 324
`5500 AH Veldhoven/NL
`
`Anmeldetag:
`Date offiling:
`Date de dépét :
`
`08.10.18
`
`Bezeichnung der Erfindung / Title of the invention / Titre de I'invention:
`(Falls die Bezeichnung der Erfindung nicht angegeben ist, oder falls die Anmeldung in einer Nicht-Amtssprache des EPA eingereicht
`wurde, siehe Beschreibung beztglich urspriinglicher Bezeichnung.
`If no title is shown, orif the application has been filed in a non-EPO language, please refer to the description for the originaltitle.
`Si aucun titre n'est indiqué, ou si la demande a été déposée dans une langue autre qu'une langue officielle de l'OEB, se référer ala
`description pour le titre original.)
`
`METROLOGY METHOD, PATTERNING DEVICE, APPARATUS AND COMPUTER PROGRAM
`
`In Anspruch genommenePrioritat(en) / Priority(Priorities) claimed / Priorité(s) revendiquée(s)
`Staat/Tag/Aktenzeichen / State/Date/File no. / Pays/Date/Numéro de dépét:
`
`Am Anmeldetag benannte Vertragstaaten / Contracting States designated at date offiling / Etats contractants désignés lors du dépét:
`
`AL AT BE BG CH CY CZ DE DK EE ES FI FR GB GR HR HU IE IS IT LILT LU LV MC MK MT NL NO PL
`PT RO R&SSE SI SK SMTR
`
`EPA/EPO/OEB Form 1014
`
`05.17
`
`2
`
`
`
`2018PO0159EP
`
`-1-
`
`METROLOGY METHOD, PATTERNING DEVICE, APPARATUS AND
`
`COMPUTER PROGRAM
`
`BACKGROUND
`
`10
`
`15
`
`20
`
`Field of the Invention
`
`[0001]
`
`The present invention relates to methods and apparatus for metrology usable, for
`
`example, in the manufacture of devices by lithographic techniques and to methods of
`
`manufacturing devices using lithographic techniques. The invention further relates to
`
`patterning devices and computer program products usable in such methods.
`
`Background Art
`
`[0002]
`
`A lithographic apparatus is a machine that applies a desired pattern onto a substrate,
`
`usually onto a target portion of the substrate. A lithographic apparatus can be used, for
`
`example, in the manufacture of intcgrated circuits (ICs). In that instance, a patterning
`
`device, which is alternatively referred to as a mask or a reticle, may be used to generate
`
`a circuit pattern to be formed on an individual layer of the IC. This pattern can be
`
`transferred onto a target portion (c.g., including part of, one, or sevcral dics) on a
`
`substrate (e.g., a silicon wafer). Transfer of the pattern is typically via imaging onto a
`
`layer of radiauion-sensilive material (resist) provided on the substrate. In general, a
`
`single substrate will contain a network of adjacent target portions that are successively
`
`patterned. In lithographic processes, itis desirable frequently to make measurements of
`
`the structures created, e.g., for process control and verification. Various tools for
`
`making such measurements are known,
`
`including scanning electron microscopes,
`
`which are often used to measure crilical dimension (CD), and specialized tools to
`
`measure overlay, a measure of the accuracy of alignment of two layers in a device.
`
`Overlay may be described in terms of the degree of misalignment between the two
`
`layers, for example reference to a measured overlay of [nm may describe a situation
`
`where two layers are misaligned by Inm.
`
`30
`
`[0003]
`
`Recently, various forms of scatterometers have been developed for use in the
`
`lithographic field. These devices direct a beam of radiation onto a target and measure
`
`one or more properties of the scattered radiation — e.g., intensity at a single angle of
`
`reflection as a function of wavelength; intensity at one or more wavelengths as a
`
`
`
`2018PO0159EP
`
`-2-
`
`function of reflected angle; or polarization as a function of reflected angle — to obtain a
`
`“spectrum” from which a property of interest of the target can be determined.
`
`Determination of the property of interest may be performed by various techniques: e.g.,
`
`reconstruction of the target by iterative approaches such as rigorous coupled wave
`
`analysis or finite clement methods; library scarches; and principal componentanalysis.
`
`[0004] The targets used by conventional scatterometers are relatively large, e.g., 40um by
`
`40um, gratings and the measurement beam generates a spot that is smaller than the
`
`grating (i.e., the grating is underfilled). This simplifies mathematical reconstruction of
`
`the target as it can be regardedasinfinite. However, in order to reduce the size of the
`
`targets, e.g.,
`
`to 1Oum by 10umor less, e.g., so they can be positioned in amongst
`
`product features, rather than in the scribe lane, metrology has been proposed in which
`
`the grating is made smaller than the measurementspot (i.e., the grating is overfilled).
`
`Typically such targets are measured using dark field scatterometry in which the zeroth
`
`orderof diffraction (corresponding to a specular reflection) is blocked, and only higher
`
`orders processed. Examples of dark field metrology can be foundin international patent
`
`applications WO 2009/078708 and WO 2009/106279 which documents are hereby
`
`incorporated by reference in their entirety. Further developments of the technique have
`
`been described in patent publications US20110027704A, US20110043791A and
`
`US20120242970A. Modifications of the apparatus to improve throughput are described
`
`in US2010201963A 1 and US2011102753A1. The contents of all these applications are
`
`also incorporated herein by reference. Diffraction-based overlay using dark-field
`
`detection of the diffraction orders enables overlay measurements on smaller targets.
`
`These targets can be smaller than the Ulumination spot and may be surrounded by
`
`product structures on a wafer. ‘largets can comprise multiple gratings which can be
`
`measured in one image.
`
`10
`
`15
`
`20
`
`[0005] In the known metrology technique, overlay measurement results are obtained by
`
`measuring an overlay target twice under certain conditions, while cither rotating the
`
`overlay target or changing the illumination mode or imaging mode to obtain separately
`
`the -1%t and the +1* diffraction order intensities. The intensily asymmetry, a comparison
`
`30
`
`of these diffraction order intensities, for a given overlay target provides a measurement
`
`of asymmetry in the target. This asymmetry in the overlay target can be used as an
`
`indicator of overlay (undesired misalignment of twolayers).
`
`[0006] In the known method using four distinct sub-targets, a certain portion of the patterned
`
`arca is not usable duc to edge cffects. In semiconductor product designs the efficient
`
`
`
`2018PO0159EP
`
`-3-
`
`use of space is very important. The use of only two specific offsets enforces the above
`
`assumption of linearity, which may lead to inaccuracy whenthetrue relationship is non-
`
`linear. To increase the numberof offsets in the known designs used would increase the
`
`space used.
`
`SUMMARYOF THE INVENTION
`
`[0007] It would be desirable to be able to perform metrology of overlay or other performance
`
`parameters with increased accuracy, and/or with less space usedforthe targets.
`
`[0008] The invention in a first aspect provides a method of measuring a performance parameter
`
`of a lithographic process, as defined in appendedclaim1.
`
`[0009] The invention in a second aspect further provides a patterning device for use in a
`
`lithographic apparatus, the patterning device comprising portions that define one or
`
`more device patterns and portions that define one or more metrology patterns, the
`
`metrology patterns including at least one target for use in a methodof the first aspect
`
`of the invention as set forth above,the target having a bias variation between locations
`
`on the target, said bias variation being in an asymmetry-related property.
`
`[0010] The invention in a further provides a metrology apparatus comprising: an illumination
`
`system configured to illuminate with radiation a target; a detection system configured
`
`to detect scattered radiation arising from illumination of the target; wherein said
`
`metrology apparatus is operable to perform the method of the first aspect of the
`
`invention as set forth above.
`
`10
`
`15
`
`20
`
`[0011] The invention further provides a computer program comprising processor readable
`
`instructions which, when run on suitable processor controlled apparatus, cause the
`
`processor controlled apparatus to perform the methodofthefirst aspect, and a computer
`
`program carrier comprising such a computer program.
`
`[0012] Further features and advantages of the invention, as well as the structure and operation
`
`of various embodiments of the invention, are described in detail below with reference
`
`to the accompanying drawings.
`
`It is noted that the invention is not limited to the
`
`specific embodiments described herein. Such embodiments are presented herein for
`
`30
`
`illustrative purposes only. Additional embodiments will be apparent to persons skilled
`
`in the relevantart(s) based on the teachings contained herein.
`
`BRIEF DESCRIPTION OF THE DRAWINGS
`
`
`
`2018PO0159EP
`
`-4-
`
`[0013] Embodiments of the invention will now be described, by way of example only, with
`
`reference to the accompanying drawings in which:
`
`Figure 1 depicts a lithographic apparatus according to an embodiment of the
`
`invention;
`
`Figure 2 depicts a lithographic cell or cluster according to an embodimentofthe
`
`invention;
`
`Tigure 3 comprises (a) a schematic diagram of a dark field scatterometer for use
`
`in measuring targets using a first pair of illumination apertures, (b) a detail of diffraction
`
`spectrum of a target grating for a given direction of illumination (c) a second pair of
`
`illumination apertures providing further illumination modesin using the scallerometer
`
`for diffraction based overlay measurements and (d) a third pair of illumination apertures
`
`combining the first and second pair of apertures;
`
`Figure 4 depicts a known form of multiple grating target and an outline of a
`
`measurement spot on a substrate;
`
`Figure 5 depicts an imageof the target of Figure 4 obtainedin the scatterometer
`
`of Figure 3;
`
`Figure 6 depicts a first example of a multiple grating target including continuous
`
`bias features according to an aspect of the present disclosure;
`
`Figure 7 depicts an image of the target of Figure 6 obtained in the scatterometer
`
`10
`
`15
`
`20
`
`of Figure 3;
`
`Figure 8 shows in schematic detail the implementation of continuousbias in one
`
`grating of the target of Figure 6 under conditions of (a) zero overlay and (b) non-zero
`
`overlay, according to one embodiment of the present disclosure;
`
`Figure 9 showsin schematic detail the arrangement of continuous bias gratings
`
`in the multiple grating target of Figure 6, according to one embodimentof the present
`
`disclosure;
`
`Figure 10 depicts a second cxample of a modilicd multiple grating target
`
`including continuous bias features according to an aspect of the present disclosure;
`
`Figure 11 depicts an image of the target of Figure 10 obtained in the
`
`30
`
`scatterometer of Figure 3;
`
`Figure 12 (a) shows in schematic detail the implementation of continuous bias
`
`in one grating of the target of Figure 10, while (b) showsthe variation of bias with
`
`position in such a grating;
`
`Figure 13 shows in schematic detail the implementation of continuous bias in
`
`
`
`2018PO0159EP
`
`-5-
`
`two gratings of the multi-grating target of Figure 10 under conditionsof (a) zero overlay
`
`and (b) non-zero overlay, according to one embodimentof the present disclosure;
`
`Figure 14 is a flowchart showing the steps of an overlay measurement method
`
`using the scatterometer of Figure 3;
`
`Figure 15 illustrates (a) signal processing in relation to the first one of the
`
`gratings shown in Figure 13 and (b) signal processing in relation to the other of the
`
`gratings shown in Figure 13,
`
`including graphical illustration of the principles of
`
`calculation of overlay error in one embodimentofthe present disclosure;
`
`Figure 16 shows in schematic detail implementation of continuous bias in two
`
`gratings of a modified mulli-grating target, including the provision of anchor points
`
`according to another embodimentof the present disclosure;
`
`Figure 17 (a) illustrates the inclusion of bias slope changes as an example of
`
`anchor points in the multi-grating target of Figure 16, (b) asymmetry signals obtained
`
`from the gratings shown In Tigure 16 under conditions of non-zero overlay, and (c)
`
`correction of the asymmetry signals using knowledge of the anchor points;
`
`Figure 18 illustrates an example of a grating having multi-step bias as an
`
`alternative to continuous bias, according to another example of the present disclosure;
`
`Figure 19 illustrates a multi-grating target having dual bias gratings according
`
`to another example of the present disclosure;
`
`Figure 20 illustrates an alternative grating target having overlay bias in two
`
`directions, based on L-shaped features;
`
`Figure 21 illustrates a modified version of the grating of Figure 20, modified to
`
`include a multi-step arrangementof bias regions;
`
`Figure 22 illustrates another modified version of the grating of Figure 20,
`
`modified to include continuous bias by rotation of L -shaped features, according to yet
`
`another embodimentof the present disclosure; and
`
`Figures 23 and 24 illustrate targets having multi-step arrangement ofbias
`
`regions in four quadrants, based on the arrangementof Figure 21.
`
`10
`
`15
`
`20
`
`30
`
`DETAILED DESCRIPTION OF EXEMPLARY EMBODIMENTS
`
`[0014] Before describing embodiments of the invention in detail, it is instructive to present an
`
`example environment
`
`in which embodiments of the present
`
`invenuion may be
`
`implemented.
`
`
`
`2018PO0159EP
`
`- 6-
`
`[0015] Figure 1 schematically depicts a lithographic apparatus LA. The apparatus includes an
`
`illumination optical system (illuminator) IL configured to condition a radiation beam B
`
`(e.g., UV radiation or DUV radiation), a patterning device support or support structure
`
`(e.g., a mask table) MT constructed to support a patterning device (e.g., a mask) MA
`
`and connected to a first positioncr PM configured to accurately position the patterning
`
`device in accordance with certain parameters; a substrate table (e.g., a wafer table) WT
`
`constructed to hold a substrate (e.g., a resist coated wafer) W and connected to a second
`
`positioner PW configured to accurately position the substrate in accordancewith certain
`
`parameters; and a projection optical system(e.g., a refractive projection lens system)
`
`10
`
`PS configured to project a pattern imparted to the radiaiion beamB by patterning device
`
`MAonto a target portion C (e.g., including one or more dies) of the substrate W.
`
`[0016] The illumination optical system may include various types of optical or non-optical
`
`components, such asrefractive, reflective, magnetic, electromagnetic, electrostatic or
`
`other types of components, or any combination thereof, for directing, shaping, or
`
`15
`
`controlling radiation.
`
`[0017] The patterning device support holds the patterning device in a manner that depends on
`
`the orientation of the patterning device, the design of the lithographic apparatus, and
`
`other conditions, such as for example whether or not the patterning device is held in a
`
`vacuum environment. The patterning device support can use mechanical, vacuum,
`
`20
`
`electrostatic or other clamping techniques to hold the patterning device. The patterning
`
`device support may be a frame or a table, for example, which may befixed or movable
`
`as required. The patterning device support may ensure that the patterning deviceis at
`
`a desired position, for example with respect to the projection system. Any use of the
`
`terms“reticle” or “mask” herein may be considered synonymouswith the more general
`
`term “patterning device.”
`
`[0018] The term “patterning device” used herein should be broadly interpreted as referring to
`
`any device that can be used to impart a radiation beamwith a paticrn in ils cross-section
`
`suchas to create a pattern in a target portion of the substrate. It should be notedthat the
`
`pattern imparted to the radiation beam may not exactly correspond to the desired pattern
`
`30
`
`in the target portion of the substrate, for example if the pattern includes phase-shifting
`
`features or so called assist features. Generally, the pattern imparted to the radiation
`
`beam will correspond to a particular functional layer in a device being created in the
`
`target portion, such as an integrated circuit.
`
`
`
`2018PO0159EP
`
`-7-
`
`[0019] The patterning device may be transmissive or reflective. Examples of patterning
`
`devices include masks, programmable mirror arrays, and programmable LCD panels.
`
`Masks are well known in lithography, and include mask types such as binary,
`
`alternating phase-shift, and attenuated phase-shift, as well as various hybrid mask types.
`
`An example of a programmable mirror array cmploys a matrix arrangement of small
`
`mirrors, each of which can be individually tilted so as to reflect an incoming radiation
`
`beam in different directions. The tilted mirrors impart a pattern in a radiation beam,
`
`whichis reflected by the mirror matrix.
`
`[0020] As here depicted, the apparatusis of a transmissive type (e.g., employing a transmissive
`
`mask). Alternatively,
`
`the apparatus may be of a reflective type (e.g., employing a
`
`programmable mirror array of a type as referred to above, or employing a reflective
`
`mask).
`
`[0021] The lithographic apparatus may also be of a type wherein at least a portion of the
`
`substrate may be covered by a liquid having a relatively high refractive index, e.g.,
`
`water, so as to fill a space between the projection system and the substrate. An
`
`immersion liquid may also be applied to other spaces in the lithographic apparatus, for
`
`example, between the mask and the projection system. Immersion techniques are well
`
`knownin the art for increasing the numerical aperture of projection systems. The term
`
`“immersion” as used herein does not mean that a structure, such as a substrate, must be
`
`submergedin liquid, but rather only means that liquid is located between the projection
`
`system and the substrate during exposure.
`
`[0022] Referring to Figure 1, the illuminator IL receives a radiation beam from a radiation
`
`source SO. The source and the lithographic apparatus may be separate entities, for
`
`example whenthe source is an excimerlaser. In such cases, the source is not considered
`
`to form part of the lithographic apparatus and the radiation beam is passed from the
`
`source SO to the illuminator IL with the aid of a beamdelivery system BD including,
`
`for cxample, suitable directing mirrors and/or a beam cxpander. In other cases the
`
`source may be an integral part of the lithographic apparatus, for example when the
`
`source is a mercury lamp. The source SO and the illuminator IL, together with the beam
`
`delivery system BD if required, may be referred to as a radiation system.
`
`[0023] The illuminator IL may include an adjuster AD for adjusting the angular intensity
`
`distribution of the radiation beam. Generally, at least the outer and/or inner radial extent
`
`(commonly referred to as o-outer and o-inner, respectively) of the intensity distribution
`
`in a pupil plane of the illuminator can be adjusted. In addition, the illuminator IL may
`
`
`
`2018PO0159EP
`
`-8-
`
`include various other components, such as an integrator IN and a condenser CO. The
`
`illuminator may be used to condition the radiation beam, to have a desired uniformity
`
`and intensity distribution in its cross section.
`
`[0024] The radiation beam B is incident on the patterning device (e.g., mask) MA, which is
`
`held on the patterning device support (c.g., mask table M'l), and is patterned by the
`
`patterning device. Having traversed the patterning device (e.g., mask) MA,
`
`the
`
`radiation beam B passes through the projection optical system PS, which focuses the
`
`beam onto a target portion C of the substrate W, thereby projecting an image of the
`
`pattern on the target portion C. With the aid of the second positioner PW and position
`
`sensor IF (e.g., an interferometric device, linear encoder, 2-D encoder or capacitive
`
`sensor), the substrate table WT can be movedaccurately, e.g., so as to position different
`
`target portions C in the path of the radiation beamB. Similarly, the first positioner PM
`
`and another position sensor (which is not explicitly depicted in Figure 1) can be used
`
`to accurately position the patterning device (e.g., mask) MA with respectto the path of
`
`the radiation beamB, e.g., after mechanical retrieval from a mask library, or during a
`scan.
`
`[0025] Patterning device (e.g., mask) MA and substrate W may be aligned using mask
`
`alignment marks M1, M2 and substrate alignment marks P1, P2. Although the substrate
`
`alignment marksasillustrated occupy dedicated target portions, they may be located in
`
`spaces between target portions (these are known as scribe-lane alignment marks).
`
`Similarly, in situations in which more than onedie is provided on the patterning device
`
`(e.g., mask) MA, the mask alignment marks may be located between the dies. Small
`
`alignment markers may also be included within dies, in amongst the device features, in
`
`which case it is desirable that the markers be as small as possible and not require any
`
`different imaging or process conditions than adjacent features. The alignment system,
`
`which detects the alignment markers is described further below.
`
`10
`
`15
`
`20
`
`[0026] Lithographic apparatus LA in this example is of a so-called dual stage type which has
`
`two substrate tables WTa, WTb and two stations — an exposure station and a
`
`measurement station — between which the substrate tables can be exchanged. While
`
`30
`
`one substrate on one substrate table is being exposed at the exposure station, another
`
`substrate can be loaded onto the other substrate table at the measurement station and
`
`various preparatory steps carried oul. ‘he preparatory steps may include mapping the
`
`surface control of the substrate using a level sensor LS and measuring the position of
`
`
`
`2018PO0159EP
`
`-9-
`
`alignment markers on the substrate using an alignment sensor AS. This enables a
`
`substantial increase in the throughput of the apparatus.
`
`[0027] The depicted apparatus can be used in a variety of modes, including for example a step
`
`mode or a scan mode. The construction and operation of lithographic apparatus is well
`
`knownto those skilled in the art and necd not be described further for an understanding
`
`of the present invention.
`
`[0028] As shown in l'igure 2, the lithographic apparatus LA forms part of a lithographic
`
`system, referred to as a lithographic cell LC or a lithocell or cluster. The lithographic
`
`cell LC may also include apparatus to perform pre- and post-exposure processes on a
`
`substrate. Conventionally these include spin coaters SC to deposit resist layers,
`
`developers DE to develop exposed resist, chill plates CII and bake plates BK. A
`
`substrate handler, or robot, RO picks up substrates from input/output ports I/O1, 1/O2,
`
`moves them between the different process apparatus and delivers then to the loading
`
`bay LB of the lithographic apparatus. These devices, which are often collectively
`
`referred to as the track, are under the control of a track control unit TCU whichis itself
`
`controlled by the supervisory control system SCS, which also controls the lithographic
`
`apparatus via lithography control unit LACU. Thus, the different apparatus can be
`
`operated to maximize throughput and processing efficiency.
`
`[0029] In order that the substrates that are exposed by the lithographic apparatus are exposed
`
`correctly and consistently, it is desirable to inspect exposed substrates to measure
`
`properties such as overlay errors between subsequent layers, line thicknesses, critical
`
`dimensions (CD), etc. Accordingly a manufacturing facility in which lithocell LC is
`
`located also includes metrology system MET which receives some or all of the
`
`substrates W that have been processedin the lithocell. Metrology results are provided
`
`directly or indirectly to the supervisory control system SCS. If errors are detected,
`
`adjusuments may be made to exposures of subsequent substrates, especially if the
`
`inspection can be done soon and fast cnough that other substrates of the same batch are
`
`still to be exposed. Also, already exposed substrates may be stripped and reworkedto
`
`improve yield, or discarded,
`
`thereby avoiding performing further processing on
`
`10
`
`15
`
`20
`
`30
`
`substrates that are known to be faulty.
`
`In a case where only some target portions of a
`
`substrate are faulty, further exposures can be performed only on those target portions
`
`which are good.
`
`[0030] Within metrology system MET, an inspection apparatus is used to determine the
`
`propertics of the substrates, and in particular, how the properties of different substrates
`
`
`
`2018PO0159EP
`
`- 10-
`
`or different layers of the same substrate vary from layer to layer. The inspection
`
`apparatus may be integrated into the lithographic apparatus LA or the lithocell LC or
`
`may be a stand-alone device. To enable most rapid measurements, it is desirable that
`
`the inspection apparatus measure properties in the exposed resist layer immediately
`
`after the exposure. However, the latent image in the resist has a very low contrast —
`
`there is only a very small difference in refractive index between the parts of the resist
`
`which have been exposed to radiation and those which have not — and notall inspection
`
`apparatuses have sufficient sensitivity to make useful measurements of the latent image.
`
`Therefore measurements may be taken after the post-exposure bake step (PEB) which
`
`is customarily the first step carried oul on exposed substrates and increases the contrast
`
`between exposed and unexposed parts of the resist. At this stage, the image in the resist
`
`may be referred to as semi-latent.
`
`It is also possible to make measurements of the
`
`developed resist image — at which point either the exposed or unexposed parts of the
`
`resist have been removed — or after a pattern transfer step such as etching. Thelatter
`
`possibility limits the possibilities for rework of faulty substrates but may still provide
`
`useful information.
`
`[0031] A metrology apparatus is shown in Figure 3(a). A target T and diffracted rays of
`
`measurement radiation used to illuminate the target are illustrated in more detail in
`
`Figure 3(b). The metrology apparatus illustrated is of a type known as a dark field
`
`metrology apparatus. The metrology apparatus depicted here is purely exemplary, to
`
`provide an explanation of dark field metrology. The metrology apparatus may be a
`
`stand-alone device or incorporated in either the lithographic apparatus LA,e.g., at the
`
`measurement station, or the lithographic cell LC. An optical axis, which has several
`
`branches throughout the apparatus, is represented by a dotted line O. In this apparatus,
`
`light emitted by source 11 (e.g., a xenon lamp) is directed onto substrate W via a beam
`
`splitter 15 by an optical system comprising lenses 12, 14 and objective lens 16. These
`
`lenses arc arranged in a double sequence of a 4F arrangement. A different lens
`
`arrangement can be used, provided that it still provides a substrate image onto a
`
`detector, and simulianeously allows for access of an intermediate pupil-plane for
`
`10
`
`15
`
`20
`
`30
`
`spatial-frequency filtering. Therefore, the angular range at which the radiation is
`
`incident on the substrate can be selected by defining a spatial intensity distribution in a
`
`plane that presents the spatial spectrum of the substrate plane, here referred to as a
`
`(conjugate) pupil plane.
`
`In particular, this can be done by inserting an aperture plate
`
`13 of suitable form between Icnses 12 and 14, in a plane which is a back-projected
`
`
`
`2018PO0159EP
`
`-11-
`
`image of the objective lens pupil plane.
`
`In the example illustrated, aperture plate 13
`
`has different forms, labeled 13N and 13S, allowing different illumination modes to be
`
`selected. The illumination system in the present examples forms an off-axis
`
`illumination mode. In the first illumination mode, aperture plate 13N provides off-axis
`
`from a direction designated, for the sake of description only, as ‘north’. In a second
`
`illumination mode, aperture plate 13S is used to provide similar illumination, but from
`
`an opposite direction, labeled ‘south’. Other modes of illumination are possible by
`
`using different apertures. The rest of the pupil plane is desirably dark as any
`
`unnecessary light outside the desired illumination mode will interfere with the desired
`
`10
`
`measurementsignals.
`
`[0032] As shownin Figure 3(b), target T is placed with substrate W normalto the optical axis
`
`15
`
`20
`
`O of objective lens 16. The substrate W may be supported by a support (not shown). A
`
`ray of measurement radiation [ impinging on target T from an angle off the axis O gives
`
`rise to a zeroth order ray (solid line 0) and two first order rays (dot-chain line +1 and
`
`double dot-chain line -1). It should be remembered that with an overfilled small target,
`
`these rays are just one of manyparallel rays covering the area of the substrate including
`
`metrology target T and other features. Since the aperture in plate 13 has a finite width
`
`(necessary to admit a useful quantity of light, the incident rays I will in fact occupy a
`
`range of angles, and the diffracted rays O and +1/-1 will be spread out somewhat.
`
`According to the point spread function of a small target, each order +1 and -1 will be
`
`further spread over a range of angles, not a single ideal ray as shown. Note that the
`
`grating pitches of the targets and the illumination angles can be designed or adjusted so
`
`that the first order rays entering the objective lens are closely aligned with the central
`
`optical axis. ‘The rays illustrated in Figure 3(a) and 3(b) are shown somewhatoff axis,
`
`purely to enable them to be more easily distinguished in the diagram.
`
`[0033] At least the O and +1 orders diffracted by the target T on substrate W are collected by
`
`objective lens 16 and directed back through beamsplitter 15. Returning to Figure 3(a),
`
`both the first and second illumination modes are illustrated, by designating
`
`diametrically opposite apertures labeled as north (N) and south (S). When the incident
`
`30
`
`ray I of measurement radiation is from the north side of the optical axis, that is when
`
`the first Ulumination mode is applied using aperture plate 13N, the +1 diffracted rays,
`
`which are labeled +1(N), enter the objective lens 16. In contrast, when the second
`
`Ulumination mode is applied using aperture plate 13S the -1 diffracted rays
`
`(labeled -1(S)) are the ones which enter the Icns 16.
`
`
`
`2018PO0159EP
`
`-12-
`
`[0034] A second beamsplitter 17 divides the diffracted beams into two measurement branches.
`
`In a first measurement branch, optical system 18 forms a diffraction spectrum (pupil
`
`plane image) of the target on first sensor 19 (e.g. a CCD or CMOSsensor) using the
`
`zeroth and first order diffractive beams. Each diffraction order hits a different point on
`
`the sensor, so that image processing can compare and contrast orders. ‘he pupil plane
`
`image captured by sensor 19 can be used for focusing the metrology apparatus and/or
`
`normalizing intensity measurements of the first order beam. The pupil plane image can
`
`also be used for many measurement purposes such as reconstruction.
`
`[0035] In the second measurementbranch, optical system 20, 22 forms an imageof the target
`
`T on sensor 23 (e.g. a CCD or CMOSsensor).
`
`In the second measurement branch, an
`
`aperture stop 21 is provided in a plane that is conjugate to the pupil-plane. Aperture
`
`stop 21 functions to block the zeroth order diffracted beam so that the image of the
`
`target formed on sensor 23 is formed only from the -1 or +1 first order beam. The
`
`images captured by sensors 19 and 23 are output to processor PU which processes the
`
`
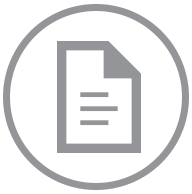
Accessing this document will incur an additional charge of $.
After purchase, you can access this document again without charge.
Accept $ ChargeStill Working On It
This document is taking longer than usual to download. This can happen if we need to contact the court directly to obtain the document and their servers are running slowly.
Give it another minute or two to complete, and then try the refresh button.
A few More Minutes ... Still Working
It can take up to 5 minutes for us to download a document if the court servers are running slowly.
Thank you for your continued patience.
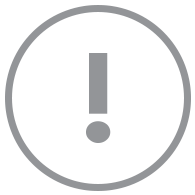
This document could not be displayed.
We could not find this document within its docket. Please go back to the docket page and check the link. If that does not work, go back to the docket and refresh it to pull the newest information.
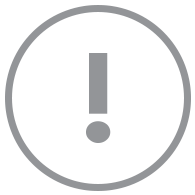
Your account does not support viewing this document.
You need a Paid Account to view this document. Click here to change your account type.
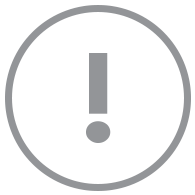
Your account does not support viewing this document.
Set your membership
status to view this document.
With a Docket Alarm membership, you'll
get a whole lot more, including:
- Up-to-date information for this case.
- Email alerts whenever there is an update.
- Full text search for other cases.
- Get email alerts whenever a new case matches your search.
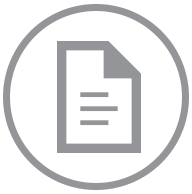
One Moment Please
The filing “” is large (MB) and is being downloaded.
Please refresh this page in a few minutes to see if the filing has been downloaded. The filing will also be emailed to you when the download completes.
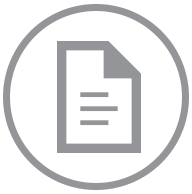
Your document is on its way!
If you do not receive the document in five minutes, contact support at support@docketalarm.com.
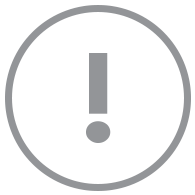
Sealed Document
We are unable to display this document, it may be under a court ordered seal.
If you have proper credentials to access the file, you may proceed directly to the court's system using your government issued username and password.
Access Government Site