`
` T (
`
`(19) World Intellectual Property Organization
`International Bureau
`
`(43) International Publication Date
`10 April 2003 (10.04.2003)
`
`(1) International Patent Classification’:
`F24D 17/00, E03B 7/04
`
`PC
`
`(10) International Publication Number
`WO 03/029721 Al
`
`F17D 1/14,
`
`74)
`
`Agent: BAILEY WALSH & CO; 5 York Place, Leeds
`LS1 2SD (GB).
`
`Q1) International Application Number:
`
`=PCT/GB02/04148
`
`(81)
`
`(22) International Filing Date:
`12 September 2002 (12.09.2002)
`
`(25) Filing Language:
`
`(26) Publication Language:
`
`English
`
`English
`
`Designated States (national): AE, AG, AL, AM, AI, AU,
`AZ, BA, BB, BG, BR, BY, BZ, CA, CH, CN, CR, CU, CZ,
`DE, DK, DM, DZ, EC, EE, ES, FI, GB, GD, GE, GH, GM,
`HR, HU,ID,IL, IN, IS, JP, KE, KG, KP, KR, KZ, LC, LK,
`LR, LS, LT, LU, LV, MA, MD, MG, MK, MN, MW, MX,
`MZ, NO, NZ, PH, PL, PT, RO, RU, SD, SE, SG, SI, SK,
`SL, TJ, TM, TR, TT, TZ, UA, UG, US, UZ, VN, YU, ZA,
`ZM, ZW.
`
`(30) Priority Data:
`0123340.2
`0129813.2
`
`28 September 2001 (28.09.2001)
`13 December 2001 (13.12.2001)
`
`GB
`GB
`
`(71) Applicant (for all designated States except US): HONEY-
`MAN WATER LIMITED [GB/GB]; Harmire Enterprise
`Park, Barnard Castle, County Durham DL12 8BN (GB).
`
`(84)
`
`Designated States (regional): ARIPO patent (GH, GM,
`KE, LS, MW, MZ, SD, SL, SZ, TZ, UG, ZM, ZW),
`Eurasian patent (AM, AZ, BY, KG, KZ, MD, RU, TJ, TM),
`European patent (AT, BE, BG, CH, CY, CZ, DE, DK, EE,
`LS, TI, FR, GB, GR, IE, IT, LU, MC, NL, PT, SE, SK,
`TR), OAPI patent (BE, BJ, CK, CG, Cl, CM, GA, GN, GQ,
`GW, ML, MR, NE, SN, TD, TG).
`
`(72) Inventors; and
`(75) Inventors/Applicants (for US only): HONEYMAN,
`Trevor
`[GB/GB]; Honeyman Water Limited (GB).
`ROBINSON, Kennth [GB/GB]; Honeyman Water T.im-
`ited (GB).
`
`Publ
`
`ished:
`with international search report
`before the expiration of the time limit for amending the
`claims and to he republished in the event of receipt of
`amendments
`
`[Continued on next page]
`
`(54) Title: FLUID DELIVERY SYSTEM
`
`58—~
`52 |
`
`BA
`
`
`U
`
`
`
`( 4
`il
`
`
`Or
`a
`646
`64
`|
`
`Ia
`
`
`Ae
`f
`
`
`i @ uy”?
`Sour
`
`
`
`oS
`4A
`M0 es)
`
`
`O2
`i
`
`se rc 66a| FE
`
`ae.
`J666
`66
`
`50
`S
`
`
`
`(57) Abstract: A fluid delivery system is described whereby sterile liquid may be delivered cfficiently to a number of remote loca-
`tions while nevertheless maintaining a continuousfluid flow throughthe system to prevent any bacterial growth. The systemincludes
`a storage tank feeding a first pipework loop including a first pump which urges fluid through said first loop at a first pressure and
`which returns to the tank, and also includesat least one pipework branch fed from the tank and having a second pump which urges
`fluid through the branch at a second pressure downstream of the second pump. The system functions efficaciously in that a branch
`manifold terminates cach branch and a return manifold is provided in the first pipework loop. Between these two manifolds are
`connected one or more supply hoses interrupted by an offtake component which is a simple valve opening through whichthe fluid
`can be selectively delivered at the desired location. When one or more offtakes are opened, the conventional fluid flow in the hose
`whichlinks that offtake to the return manifold is reversed on account of the pressures at which the two pumps in the firs pipework
`loop and the pipework branches operate. This type of operation allows for practically 100 % diversity, i.e. that condition where as
`many or as few offtakes in the system can be opened simultaneously without any practical reduction in the availability of fluid.
`
`O03/029721Al
`
`
`
`WO 03/029721 Ad
`
`_[IMITIMMTININATA TIA MITATA
`
`For two-letter codes and other abbreviations, refer to the "Guid-
`ance Notes on Codes andAbbreviations" appearing at the begin-
`ning ofeach regular issue ofthe PCT Gazette.
`
`
`
`WO 03/029721
`
`PCT/GB02/04148
`
`Fluid Delivery System
`
`fluid delivery system, and more
`This invention relates to a
`patticularly to a hygienic fluid delivery system, the construction
`of which requires careful planning and analysis to ensute that
`the resulting system has minimal
`stagnancy of flow during
`opetation and
`that bacteria growth is minimised if not
`eliminated entirely. The
`types of
`fluid
`delivery
`systems
`hereinafter described are typically provided in a wide variety of
`plant,
`including Research & Development facilities generally,
`laboratories,
`silicon wafer manufacturing plants, breweries,
`pharmaceutical manufacturing facilities, and any installation
`whete a plurality of sources of sterile water or other liquid may
`be required in a number of different locations remote from a
`supply tank for storing the water or other liquid.
`
`Although the following description is provided with almost
`exclusive teference to hygienic fluid delivery systems which
`deliver so-called Water for Injection (WFI), Purified Water (PW)
`and the like, it will be instantly appreciated that the invention
`has far wider application and may be applied to deliver any
`liquid to a predetermined location remote from a storage vessel
`through distribution pipework.
`
`It is also to be appreciated by the reader that the word “sterile”
`and cognate exptessions
`as used hereinafter
`is not
`to be
`construed in its literal sense and includes liquids having a
`bacteria, germ ort other contaminant content reduced beneath a
`desited level so that the said liquids are safe ot suitable for a
`patticular procedure.
`
`in their
`the delivery of sterile fluids,
`for
`systems
`Current
`simplest form, consist essentially of a storage vessel supplied
`intermittently ot continuously with a sufficient volume of pre-
`
`
`
`WO 03/029721
`
`PCT/GB02/04148
`
`2
`
`sterilised fluid. A system of steel pipework is routed through the
`premises,
`for example a clinical
`laboratory, wherein WFI is
`required, said pipework being for the most part conventionally
`concealed in the ceiling of each room through which said
`pipework passes and descending from the ceiling only in those
`locations either where operatives are likely to regularly requite a
`source of WFI or
`alternatively in locations
`conveniently
`accessible by a number of operatives working proximate said
`location. The pipework is routed through said premises and
`ultimately returns to the storage vessel to return any excess fluid
`thereto.
`
`There are a number of important factors which must be taken
`into account when designing a sterile fluid delivery system, but
`the most important is that the system as a whole must generally
`pteclude anylocalised stagnation of fluid, either in the pipework
`ot the storage vessel and be free from crevices or similar areas
`where bacteria could become trapped and thus allowed to
`proliferate
`
`Accotdingly the pipes ate firstly commonly welded together
`using a very costly technique known as Tungsten Inert Gas
`(TIG) autogenous welding which ensures that
`the butt
`joints
`between adjacent sections of pipe are secured to one another
`without introducing unwanted contaminants into the passageway
`within the pipes and ensuring that
`the join is as smooth as
`possible internally. Furthermore the interior sutface of the
`various pipes which ate joined together throughout the system is
`important in that said interior surface must be as smooth as
`possible and any bends in the pipes must preclude the formation
`of eddy currents during fluid flow therethrough.
`It will be
`appreciated that eddy currents give rise to localised volumes of
`fluid which ate effectively stationary, and thus the temperature
`of these volumes can quickly drop to a level at which bacteria
`
`
`
`WO 03/029721
`
`PCT/GB02/04148
`
`3
`
`most teadily thrive with the result that the sterility of the system
`as a whole is prejudiced.
`
`adjusted
`Secondly, the operating temperature of the system is
`and maintained
`to ensure that any bacteria (for example
`mesophilic
`bacteria
`such
`as
`gram-negative
`pscudomonas
`commonly present
`in water)
`are
`either ptevented from
`multiplying or are actually eliminated. A common temperature
`for WFI systems is 80°C and to prevent any gradual reduction of
`the fluid temperature over time, a heater is commonly connected
`into the system.
`
`It is to be mentioned that PW and other hygienic fluid systems
`can be operated at ambient temperatures, so much greater care
`and attention nceds to be given to the construction of these
`types of systems which on account of the operating temperature
`ate much more prone to bacterial proliferation.
`
`Thirdly, it is important that a turbulent, as opposed to a laminar
`flow characteristic is developed within all sections of
`the
`pipework again to minimise the risk of bacteria proliferation.
`Fort example, in both laminar and turbulent fluid flows, it is well
`known that the velocity of the fluid immediately adjacent a solid
`sutface is minimal if not zero, whereas the velocity of fluid
`remote from such a surface is much greater. Hence the majority
`of the volumetric flow through a pipe is achieved through the
`middle of
`the pipe whereas only a
`comparatively small
`percentage of flow is attributable to the fluid moving proximate
`the interior surfaces of said pipe. This slow moving or stagnant
`fluid has
`the tendency to cool and thus not only are the
`conditions for bacteria proliferation improved adjacent to the
`interior surface of the pipe, but the fact that the fluid is either
`moving very slowly or not at all further increase the likelihood
`that bacteria will find a site on the pipe surface to germinate.
`
`
`
`WO 03/029721
`
`PCT/GB02/04148
`
`Turbulent fluid flows within sterile fluid delivery systems are
`desirable because velocity profile of the fluid proximate the
`interior surface of the pipe increase significantly more sharply
`than that of an equivalent laminar flow and the risk of bacteria
`proliferation and germination
`is
`thus mitigated. Biofilm
`formation on the internal surfaces is discouraged by such fluid
`
`velocities.
`
`However, it is well known in fluid dynamics that the existence
`of turbulent flows within pipes depends on, among other things,
`the diameter of
`the pipe, and the velocity of
`fluid flow
`therethrough. In general, to the development of turbulent flow
`in pipes of a larger diameter requires a significantly larger fluid
`velocity than required to establish turbulent flow in smaller
`diameter pipes.
`
`the storage vessel
`is necessary to ensure that
`it
`Fourthly,
`containing the WFI is recharged over a predetermined period of
`time,
`for example every two hours. Moreover,
`the system
`opetates
`continuously so
`that
`the storage vessel
`is being
`continually emptied and simultaneously recharged to avoid any
`stagnation of fluid therein, and the time petiod is merely an
`indication of the length of time which would be taken to empty
`to the
`storage vessel
`completely under normal operating
`conditions without any simultaneous recharge.
`
`the systems with which this
`It will also be appreciated that
`invention are concerned may have many tens of outlets or so-
`called offtakes usually connected in seties as an entire laboratory
`ot building may need to be served by a single fluid delivery
`system. The diameter of the pipes commonly used in such
`systems may be of the ordet of 1-2% inches (25-64mm), and to
`
`
`
`WO 03/029721
`
`PCT/GB02/04148
`
`5
`
`ensure a turbulent flow within such a pipe the flow velocities are
`typically between 1-3m/s.
`
`In order to develop such a flow velocity, substantial and thus
`costly pumping apparatus
`is
`required, and when it
`is also
`considered that a number of different offtakes may be in use
`simultaneously,
`dynamic
`control
`of
`this
`pump
`and/or
`alternatively some means of pressure regulation is
`required.
`Conventional Fluid delivery systems must possess an ability to
`deliver
`fluid
`through
`a
`number
`of
`off-takes
`opened
`simultaneously while nevertheless operating satisfactorily when
`none of the offtakes are in use,
`for example overnight. The
`inherent disadvantage of series-type systems, in which a plurality
`of offtakes are connected in seties such as described, is that the
`opening of more than a few offtakes simultaneously can have
`detrimental effect both on the flow characteristics and the
`
`the.
`the correct flow and pressure at
`ability to draw water at
`various uset offtakes. The number of offtakes which can be
`opened simultaneously in a system expressed as a percentage of
`the total number of offtakes in a system is known as
`the
`diversity.
`
`Various different pipework loop and sub-loop configurations
`having different benefits and effects on diversity have been
`proposed.
`
`Referring now to Figures 1, 2, 3, and 4 which show different
`fluid delivery systems of prior art configuration, each of these
`systems
`shows
`a
`storage vessel 2 with which pipework 4
`communicates to both feed offtakes 6 which are embodied most
`simply in an openable valve and to return excess fluid to the
`storage vessel at 8.
`
`
`
`WO 03/029721
`
`PCT/GB02/04148
`
`6
`
`Each of the systems shown in the Figures comprises at least one
`pump 10 and in the case of Figure 2 a second pump 12, each of
`which urges fluid through the pipework around the system in a
`flow direction 14.
`
`It can be seen from Figure 1 that the pipework is sloped at 16
`between off takes and this is a common feature of such systems
`to allow for drainage of the fluid from the system for cleaning
`purposes. A heater 18 and a pressure regulating valve 20 ate also
`provided in series with the various offtakes 6 and it will be
`appreciated that this simple series system functions in a very
`similar manner to a simple series electrical circuit, with the
`pump corresponding to a soutce of potential difference,
`the
`offtakes corresponding to resistances dissipating power and the
`flow rate corresponding to the current. Indeed the analogy can
`be extended in the cases of Figures 2, 3, and 4 which effectively
`show parallel circuits.
`
`The importance of this analogy is that as further offtakes are
`added into a particular loop, the fluid flow which the system is
`capable of delivering through each of the offtakes when open is
`reduced depending on the number of offtakes in that loop. This
`is
`identical
`to
`the
`reduction in brightness of
`lightbulbs
`connected in seties in an electrical circuit as more and more
`lightbulbs are connected.
`
`a multiple loop
`2 which shows
`case of Figure
`In the
`artangement, a second pump 12 drives fluid through a second
`loop of the system and effectively provides sufficient
`flow
`through said loop to feed the various offtakes in that loop. In
`the case of Figure 3, a sub-loop or true parallel arrangementis
`shown, and in the case of Figure 4 a more complex main
`loop/sub loop artangement is shown wherein four separate sub
`loops 22, 24, 26, 28 are fed from a main loop 30. Each of the
`
`
`
`WO 03/029721
`
`PCT/GB02/04148
`
`7
`
`sub loops is provided with a diaphragm valve 32 immediately
`after the join to the main loop, and additionally Constaflo™
`flow regulating valves 34 are provided on each of the sub loops,
`at the most remote end of the main loop, and on a return loop
`36 which links the main loop immediately after the pump 10 to
`the stotage vessel 2. Without unnecessary description and
`analysis of the working of this arrangement,
`the diaphragm
`valves, flow regulating valves and return loop are all provided
`with a view to increasing the effective diversity of the system as
`a whole and to ensute correct hydtaulic balancing of the system.
`
`The fundamental disadvantages of the systems described other
`than their limited ability to operate at maximum diversity are
`ptimarily related to the perceived permanent nature of the
`construction. For
`instance,
`in order
`to deliver
`a sufficient
`quantity of fluid around the system, the pipes must be of large
`diameter which both increases
`the cost of materials
`and
`construction. Stainless steel pipe sections currently used in the
`construction of such systems typically are provided in only 6m
`lengths which necessitates a considerable amount of welding and
`increases the tisk of areas of bacterial germination around the
`system due to
`crevices introduced through such welding or
`alternative jointing procedutes.
`
`In the event that an additional offtake is required in an already
`installed system, it is very difficult and/or costly to modify the
`system, but perhaps most
`importantly the disruption to the
`system caused by modification can be severe. For example, the
`insertion of an additional offtake would necessitate a
`full
`draining of
`the system, opening the system to insert
`the
`additional pipework
`and offtake
`tequired,
`together with
`subsequent
`resterilisation and te-chatging. Furthermore,
`the
`additional offtake could foreseeably necessitate a larger pump
`and additional flow and pressure regulating components. It has
`
`
`
`WO 03/029721
`
`PCT/GB02/04148
`
`8
`
`been estimated that the average cost of installation of a fluid
`delivety system is approximately £200 pet metre and it will thus
`be appteciated that these systems can significantly increase the
`cost of ptemises construction. The welding process is also
`subject
`to tigorous and costly inspection and qualification
`procedures as part of the regulatory traceability requirements of
`HM Medicines Inspectorate and the like.
`
`is an object of this invention to provide a fluid delivery
`It
`system whose effective diversity is above 90% and preferably
`approximately 100% but which is significantly less expensive
`than prior art systems to construct ,
`install, and inspect and
`subsequently certify.
`
`It is a further object of the invention to provide a system which
`can be installed with the minimum numbet of crevices and
`imperfections in the interior surface of the pipework through
`which the fluid flows, and additionally to offer the possibility of
`installing a substantially crevice-free system, at
`least
`in ‘the
`pipework coupling the offtakes to the pumping room. It is a
`further object of the invention to provide a system with as few
`joints between respective sections of pipework as possible.
`
`According to the invention there is provided a fluid delivery
`system comptising a storage vessel for fluid which feeds a first
`pipework loop including a first pump which urges fluid through
`said first loop at a first ptessute and which ultimately returns to
`said vessel, said system including at least one pipework branch
`fed from said storage vessel or said first pipework loop, said
`pipework branch including a second pump which urges fluid
`through said pipework branch at a second pressure downstream
`of said second pump, characterised in that each pipework branch
`terminates in a branch manifold having at least a fluid inlet and
`one ot more fluid outlets to the latter of which are connected
`
`
`
`WO 03/029721
`
`PCT/GB02/04148
`
`9
`
`one ot more hoses which feed one ot mote offtakes from which
`fluid can be drawn from the system, and in that for each branch
`manifold there is
`a cotresponding return manifold in fluid
`communication with said first pipework loop to which said
`offtakes are connected by further hoses such that fluid can flow
`from said branch manifold through said hoses and thence
`through said return manifold ultimately being returned to the
`tank when the offtakes
`are closed,
`said first and second
`pressures being both above atmospheric pressure such that the
`opening of said one or more offtakes, and thus the opening of
`said system to atmospheric pressure at one ot mote locations
`causes the direction of fluid flow to reverse in the one or more
`hoses which connects said one or more opened offtakes with the
`retutn manifold, said one ot mote opened offtakes thus being
`supplied with fluid from both the branch manifold and the
`return manifold.
`
`Most preferably,
`vessel.
`
`the branch manifold is fed from the storage
`
`Ideally the branch and return manifolds have at least a fluid inlet
`and one ot mote fluid outlets, said branch and return manifolds
`being disposed downstream of said first and second pumps with
`fluid communication between said manifolds being achieved by
`at
`least one hose connectable to fluid outlets on respective
`manifolds and including one ot more offtakes thus allowing
`fluid flow from the storage vessel through the pipework branch,
`branch manifold, hose, return manifold and first pipewotk loop
`ultimately returning to said storage vessel and permitting fluid
`offtake at a desired location.
`
`Preferably, said retutn manifold is provided with a fluid inlet
`and a ptimary fluid outlet
`to allow for connection of said
`manifold within the first pipework loop and a plurality of
`
`
`
`WO 03/029721
`
`PCT/GB02/04148
`
`10
`
`to which hoses having offtakes may be
`secondary outlets
`connected to allow for fluid communication with the branch
`
`manifold.
`
`Further preferably the branch manifold is provided with a fluid
`inlet and only secondary outlets to which hoses having offtakes
`may be connected such that the fluid flowing into said branch
`manifold is urged into one otf more hoses.
`
`Preferably the fluid pressure within the return manifold is
`greater than the fluid pressure in the branch manifold, and most
`pteferably both these pressures are above ambient atmospheric
`pressure such that the opening of an offtake opens the fluid
`within to atmospheric pressure and the fluid flow direction in
`the length of hose between said offtake and said return manifold
`teverses and both manifolds urge fluid towards
`said open
`offtake.
`
`hose
`of
`plurality
`a
`circumstances,
`pteferable
`In most
`connections ate made between the branch manifold and the
`return manifold, each connection consisting of a first hose, one
`end of which is connected to one fluid outlet
`the branch
`manifold and the alternate end of which is connected to an
`offtake, a second hose having one end connected to the offtake
`and the alternate end connected to a fluid outlet of the return
`manifold. Most preferably,
`each hose connection between
`branch and return manifolds consists only of a single offtake,
`but alternately, each connection may consist of first and second
`hoses, ends of which are connected to the branch and return
`manifolds
`tespectively, alternate ends of
`said hoses being
`connected to first
`and second primary offtakes,
`and the
`connection further comprising one or mote secondary offtakes
`interconnected by intermediaty hoses between said first and
`second ptimaty offtakes and second secondary offtakes.
`
`
`
`WO 03/029721
`
`PCT/GB02/04148
`
`11
`
`Further preferably each hose is made of a flexible polymetic or
`plastics material such as PTFE.
`
`Preferably, the hose diameter is in the region of 5-25mm.
`
`least one of the first or second pumps is
`Most preferably at
`dynamically controlled depending on the fluid pressure within
`the respective return ot branch manifold, and most preferably
`the pump driving fluid through the first pipework loop is
`dynamically controlled depending on the instantaneous fluid
`requirements of the system,
`i.e.
`the number of offtakes which
`are open at any one instant.
`
`Most preferably only the second pump is dynamically controlled
`depending on the fluid pressure within the respective return and
`branch manifolds.
`
`The system described above has the surprising advantage that
`the opening of any offtake provided on any particular hose
`connection between the manifolds causes
`a
`reversal
`in the
`direction of fluid flow in the hose section from the return
`manifold to the said offtake. Such flow direction reversal
`is
`achieved because the fluid pressure developed in the return
`manifold is greater than the pressure developed in the btanch
`manifold and thus the fluid is urged through the offtake (which
`is effectively at atmospheric pressure once opened) along both
`sections of hose linking the offtake to said manifolds.
`
`The system has many attendant advantages resulting from the
`novel atrangement described, particularly including
`1.
`lower cost of installation and associated validation
`
`
`
`2. site-wide welding and_theelimination of need for
`associated hazards of this process;
`
`
`
`WO 03/029721
`
`PCT/GB02/04148
`
`12
`
`facility for installation by non-specialist contractors (as the
`3.
`hoses and offtakes may be installed by for example electrical
`cable installers);
`4.
`easy relocation/isolation of individual offtakes;
`5.
`future pte-cleaned offtakes can be easily added to the
`spate manifold secondary outlets and brought on-line without
`interruption to the live existing system;
`6.
`offtake hoses can be individually sterilised;
`7.
`hoses can be drained by (sterile) air or gas being blown
`therethrough thus avoiding extra costs
`for
`routing gravity
`drainage, and
`8.
`hose sterilisation can be achieved by a number of methods,
`such as chemical recirculation, steam out, hot sterile air (160°C),
`
`ozone.
`
`that provided the
`important advantage is
`the most
`Perhaps
`pumps ate effectively dynamically controlled, the diversity of the
`system remains at almost 100% as more and more offtakes are
`simultaneously opened. The only limit to the number of offtakes
`which can be opened simultaneously without any appreciable
`flow reduction therethrough is the diameter of the pipes and
`manifolds through which the fluid is urged by the pump (and
`thus the volume of fluid which can be delivered to the manifolds
`
`by said pumps).
`
`A specific embodiment of the invention is now described by way
`of example with reference to the accompanying drawings
`wherein
`
`Figures 1-4 schematically show fluid delivery systems of prior
`att configuration,
`
`Figure 5 schematically shows a fluid delivery systems according
`to the invention,
`
`
`
`WO 03/029721
`
`PCT/GB02/04148
`
`13
`
`Figures 6, 7 show details of possible offtake shroud assemblies,
`
`Figures 8, 9 show perspective views of possible loop and branch
`manifold assemblies,
`
`Figures 10, 11 show schematically possible offtake assemblies.
`
`an alternative arrangement
`12 shows
`Figure
`according to the invention.
`
`for
`
`a
`
`system
`
`there is shown a fluid delivery
`Referting firstly to Figure 5
`system 50 comprising a storage vessel
`feeding pipework 52
`which divides into a pipewotk loop 54 and a pipework branch
`56. The loop 54 ultimately returns to the storage vessel 52 at 58
`to recharge said vessel with fluid pump atound the system.
`
`In each of the loop 54 and the branch 56 are provided pumps
`60, 62 respectively which are located upstream of a return
`manifold 64 and a branch manifold 66 each of which has at least
`a ptimary fluid inlet 64A, 66A and a numbet of secondary fluid
`outlets 64B, 66B to which hoses 64C, 66C can be connected.
`Each of the hoses 64C, 66C is connected to an offtake which
`essentially comprises an openable valve which when closed
`allows fluid by pass from the hoses 66C to 64C.
`
`In a preferred embodiment, the pumps 60, 62 ate dynamically
`controlled by coupling the pump motot
`to manifold pressure
`sensors
`schematically represented at 70, 72 in response to
`changes in fluid pressute inside the manifolds 64, 66. In this
`manner,
`the fluid flow and pressure can be automatically
`maintained at required levels when one or mote of the offtakes
`is opened to deliver fluid therethrough. It is to be mentioned
`that this arrangement provides the most accurate control, but
`
`
`
`WO 03/029721
`
`PCT/GB02/04148
`
`14
`
`once the opetating limits of a particular system ate determined it
`is mote likely that only a single pump need be dynamically
`controlled.
`
`there may optionally be
`Downstream of the return manifold,
`provided a sanitisation unit and/or a heat exchanger 73, 74 to
`ensute
`that
`the desited temperature is maintained during
`operation. Thereafter fluid is returned to the vessel 52 from
`which it is later pumped around the system.
`
`Example system operating conditions include a minimum flow
`rate of 100litres/min in the pipework branch, a maximum flow
`rate of 160litres/min, a pressure of 6bar in the branch manifold,
`and a minimum flow rate of 45litres/min in the pipework loop, a
`maximum flow trate of 225litres/min and a tfetutn manifold
`pressure of 2 bar.
`
`Figure 5 also schematically shows a possible layout of the system
`in that the bulk of the apparatus used in the system is located in
`a plant room schematically defined above the dotted line 76, a
`pottion of the length of the hoses 64C, 66C which communicate
`with the offtakes and the respective loop and branch manifolds
`ate disposed in a roof or wall void represented between dotted
`line 76 and a further dotted line 78, and the offtakes 68 are
`optionally connected at the end of shrouds secured to the toof
`ot walls to conceal the hoses.
`
`Examples of such shrouds 80, 82 and offtakes 84, 86 are shown
`in Figures 6 and 7.
`
`Figures 8, 9 show possible embodiments of the return manifold
`64 and btanch manifold 66. The manifolds are different because
`
`fluid is required to flow through the return manifold 64 from a
`ptimaty inlet 64A to a primary outlet 64A’
`in the direction
`
`
`
`WO 03/029721
`
`.
`
`PCT/GB02/04148
`
`15
`
`indicated at 88. There are further provided vatious secondary
`fluid outlets 64B the numbet of which corresponds to the
`number of offtakes desired in a particular system, and although
`the wotd “outlet” is used in connection with these fittings, it is
`to be appreciated that fluid in generally will only flow out of
`same when the particular offtake fed by the hose connected to
`said outlet is opened. In the alternate circumstance when the
`offtake is closed, fluid will flow into the manifold through outlet
`and be combined with the fluid flow through the manifold from
`one end to the other as indicated at 88. A pressure control
`outlet PC for dynamic pump control and a spare instrument
`access 90 are also provided.
`
`In the case of the branch manifold 66, a primary inlet 66A is
`provided, together with a number of secondary outlets 66B to
`which the hoses 66C are connected. A pressure control outlet
`PC is disposed at one end of the manifold 66 whereas the
`opposite end is blanked off at 92 to prevent any fluid escape
`through said end. In the case of the branch manifold, fluid flows
`continually through the outlets 66B regardless of whether the
`offtakes fed by hoses 66C are open or closed.
`
`there is shown a schematic
`Referting to Figures 10 and 11,
`teptesentation of an offtake having connectors 94, 96 to which
`hoses 66C, 64C ate connected to feed the offtake with fluid. A
`chamber 98 is provided which allows for fluid flow from hose
`66C to hose 64C when the offtake is closed and for
`fluid
`
`reversal in hose 64C when the offtake is opened, and this in turn
`is connected to a standard diaphragm valve or similar 100 having
`actuator 102 if necessary.
`
`A schematic sectional view of the chamber is shown in Figure 11
`and it can be seen from this figure that the flow of fluid within
`
`
`
`WO 03/029721
`
`PCT/GB02/04148
`
`16
`
`said component may be achieved by oritice plates 104 provided
`internally thereof.
`
`' In circumstances where a uset only gradually opens a valve to an
`offtake, it is foresceable, depending on the design of the various
`components within a system, that the fluid flow velocity within
`hose 64C could merely reduce as opposed to become reversed,
`and in particular circumstances it may also ttanspite that on
`opening an offtake by a predetermined amount,
`the fluid
`velocity in the hose 64C teduces to zero, said offtake being
`supplied entirely by fluid flow to the offtake through hose 66C.
`Such operating conditions ate envisaged only transiently and
`would not prevail for any significant length of time which could
`materially affect the hygiene of the fluid within the system as a
`whole. It is also to be mentioned that these particular operating
`characteristics will
`only arise
`infrequently,
`and the most
`desirable system operation will involve the reversal of fluid flow
`direction through hose 64C.
`
`there is shown an alternative
`Finally, referring to Figure 12,
`atrangement of a
`fluid delivery system which functions
`in
`accordance with the invention.
`In the arrangement shown, a
`stotage vessel 200 is fed with a supply of purified or sterile
`watet at 202, and the vessel 200 is connected within a first
`pipework loop 204. Within said first pipework loop,
`there is
`disposed a low pressure, high volume pump 206 which causes
`fluid flow around the loop 204. The box 208 in this figure which
`surrounds
`the pump and vessel
`is
`representative of a
`site
`pumping and equipment room, and remaining boxes in dotted
`lines 210, 212, 214 are
`representative of either different
`buildings to which a supply of sterile fluid is required to be
`delivered, or alternatively different but remotely located zones
`in the same building.
`
`
`
`WO 03/029721
`
`PCT/GB02/04148
`
`17
`
`the first pipework loop is constructed around a
`Accotdingly,
`path which approaches each zone at a suitable location. In the
`region of each zone, a branch 218 is taken from the main loop
`and feeds a pump 220 which may be dynamically controlled at
`222 accotding to instantaneous fluid usage requirements at the
`vatious offtakes, 224 required or being used in that zone at any
`time. The pump 220 delivers pressurised fluid to a branch
`manifold 226 which is connected to said offtakes
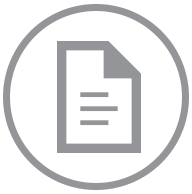
Accessing this document will incur an additional charge of $.
After purchase, you can access this document again without charge.
Accept $ ChargeStill Working On It
This document is taking longer than usual to download. This can happen if we need to contact the court directly to obtain the document and their servers are running slowly.
Give it another minute or two to complete, and then try the refresh button.
A few More Minutes ... Still Working
It can take up to 5 minutes for us to download a document if the court servers are running slowly.
Thank you for your continued patience.
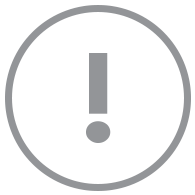
This document could not be displayed.
We could not find this document within its docket. Please go back to the docket page and check the link. If that does not work, go back to the docket and refresh it to pull the newest information.
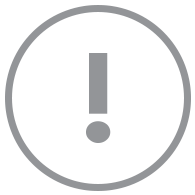
Your account does not support viewing this document.
You need a Paid Account to view this document. Click here to change your account type.
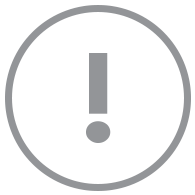
Your account does not support viewing this document.
Set your membership
status to view this document.
With a Docket Alarm membership, you'll
get a whole lot more, including:
- Up-to-date information for this case.
- Email alerts whenever there is an update.
- Full text search for other cases.
- Get email alerts whenever a new case matches your search.
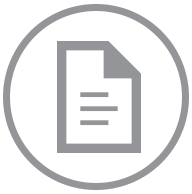
One Moment Please
The filing “” is large (MB) and is being downloaded.
Please refresh this page in a few minutes to see if the filing has been downloaded. The filing will also be emailed to you when the download completes.
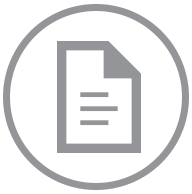
Your document is on its way!
If you do not receive the document in five minutes, contact support at support@docketalarm.com.
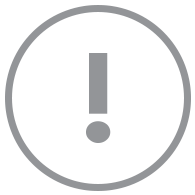
Sealed Document
We are unable to display this document, it may be under a court ordered seal.
If you have proper credentials to access the file, you may proceed directly to the court's system using your government issued username and password.
Access Government Site