`
` To,
`PATENT
`SPECIFICATION
`
`Po be
`k
`
` ty
`
`596.56
`No, 19532/45,
`Application Date: fuly 30, 1745...
`
`Complete Specification Left: Dec, 18, 1945,
`Complete Specification Accepted: Jan, 6, 1948.
`
`
`2
`
`
`
`
`PROVISIONAL SPECIPICATION,=72Ee
`- Laces and Method of Manufacturing the same
`T, Apotpn Rerrer, a citizen of
`the
`apply to the laces a surface configuration.
`which will
`improve their knotproofness 60
`_ United States ofAmerica, residing at 1038,
`.
`and embellish the same.
`West 87th Street; New York, New York,
`United States of America, do hereby
`It is an important object of the inven- ©
`declare the nature of this invention to he
`tion to, simplify the manufacturing process
`reduce the
`- of the laces and to greatly
`as follows: — -
`.
`The invention relates to the manufac-
`manufacturing - costs.
`-
`oe
`It has been found that these and other
`ture of laces used to connect two parts
`provided with eyelets forthe introduction
`objects which will become apparent as this
`of laces andparticularly to the manufac-
`specification proceeds may be successfully
`attained if the laces consist of
`sections
`ture of shoe laces.
`oo ,
`Articles of this type are generally made
`which are severed from thin continuous
`of cireular-or rectangular fabric or leather
`bodies, such as lacings, bands or rods of
`strips aud their union producing- the
`a pliable thermoplastic material having
`closure of individual parts is accomplished
`a restricted elasticity, the pliability being
`by the formation of a knot. A main
`improved by the admixture of suitable
`disadvantage of the customary laces con-.
`plasticizers;
`the sections are shaped or.
`sists therem that a reliable closure by the
`conditioned at their ends preferably in the
`knot is not obtainable; in other words, the
`course of the manufacture of the laces to
`customary laces and shoe strings are not
`be easily introduced into the eyelets.
`sufficiently knot-proof; the Imots - open
`-Thermoplastic materials of the vinyl,
`unintentionally and the shoes become
`vinylchloride, vinylchloride acetate, acryl
`unlaced; this deficiency makes itself
`and methacryl-type have been found to be
`particularly felt in the imitial periods of
`particularly suitable for the purposes of
`the invention, as these plastics acquire,
`use.
`ae
`.
`Another grave manufacturing difficulty
`when. heat shaped,. for
`instance heat-
`resides therein that the ends of shoe and
`extruded or heat-pressed into thin con-
`other laces must be rigidified or shaped or
`tinuous bodies, a high degree of a some-
`both in order to facilitate their introduc-
`what micro-rough surface character which
`tion into the eyelets and to protect un-
`results in perfect -knotproofness. -
`ravelling of the ends; this object is in the
`- The manufacture of shoe laceshas been
`case of shoe laces generally- accomplished
`chosen to illustrate the invention by way
`byencasing the ends in metal tubings.
`of example.
`ot
`oe
`Tt is theobject of
`the invention to
`In conformity with the same pliable
`produce binding’ laces and particularly
`thermoplastic materials are heat-extruded
`shoelaces which do not open unintention-
`into thin- continuous bodies,
`such
`as
`ally and are completely knot-proof from
`bands, tubes or rods in theusual gener-
`ally known manner.
`the first stage of their application.
`As the continuous 96
`It is another object of the invention to
`hody is discharged from the extruding
`shape the endsof the securing laces with-
`press it is severed-by suitable cutters, for
`outtheapplication of additional elements
`instance the known continuous saws used
`in such a manner that theycan beeasily
`for severing extruded metal wire,
`into
`introduced into the eyelets of the articles
`sections of the shoe lace length. The sec- 108
`to be’closed, for instance of shoe uppers.
`tions having, due to the chosen manufac-
`Itis another ‘object of the invention to
`turing material and in spite of their.
`reinforce the ends of the binding laces
`pliability, a substantial amount of body
`without the use of additional measures or
`at their ends, are teduced ineross area oy-
`pointed in order to impart to-them a shape 105
`elements.
`=
`~~
`Se
`It is also an object of the invention to
`which will facilitaté their introduetion
`properly condition theends of the laces
`into the eyelets.
`~~
`—--
`ot
`simultaneously with their manufacture.
`In accordance with another manner of:
`Ti is another object of the invention to
`production the thermoplastic materials
`[Price U]-]
`
`66.
`
`78
`
`10
`
`20
`
`30
`
`36
`
`40
`
`55
`
`— Seaee
`
`
`
`i
`
`
`,
`
`mri:
`
`586,562
`an
`
`==
`
`
`
`The knot proofing property may alse
`be improved by coarsening or roughening
`the surface of the continuous bodies by 30
`adding to the initial thermoplastic masses
`solid substances in powdered form, such
`as for instance a fine silica or clay powder.
`Customary plasticizers are preferably
`used at a percentage of about 5 to 40% 95
`to impart to the thermoplastic materials
`used in the realisation of this invention
`the desired pliahility and bendability; as
`preferable plasticizers butyl compounds
`may be employed.
`.
`. The extruding or pressing temperatures
`are not different from the working tem-
`peratures customarily used in the heat-
`shaping of thermoplastic materials;
`the
`severed sections are cured, if required, in 45
`the manner known in this art.
`
`40
`-
`
`-
`
`.
`
`are pressed inthe form of thin continuous
`bodies and provided in accordance with
`the standard length of shoe laces by a pair
`of correspondingly surfaces rollers with
`6 short portions of a reduced cross area; if
`these rods are then severed at the reduced
`places, thin ends are created which are
`adapted for the introduction into eyelets.
`The invention may be used te manu-
`10 facture laces and strings which are pro-
`vided with specific surface configuration,
`for instanee longitudinal spiral ribs, pro-
`jections,
`grooves, or with decorative
`designs. For this purpose the extrusion
`j§ nozzle may be shaped accordingly .or a
`pair of rollers may be used which are
`provided. with design applying surfaces.
`The
`thin continuous
`thermoplastic
`bodies used for the making of laces in
`20 accordance with the invention may have
`a circular, oval, elipsoidal, quadrangular,
`Dated the 30th day of July, 1945.
`rectangular cross area; the long sides of
`ELKINGTON & FIFE,
`the elipsoidal shapes may he straightened
`-Consulting Chemists and Chartered
`out and opposite sides of the quadran-
`Patent Agents,
`25 gular or the short sides of the rectangular
`.
`Bank Chambers,
`.
`shapes may. he rounded, whereby the knot
`329, High Holborn, London, W.C.1,
`proofness.is greatly enhanced..
`Agents for the Applicant.
`COMPLETE SPECIFICATION
`Laces and Method of Manufacturing the same
`_ J, Avotpa Rerrer, a .citizen of
`the
`and leather made shoe
`laces are the 80
`United States of America, residing at 108,
`following.
`.
`.
`West 87th Street, New. York, New York.
`These shoe laces have practically no
`0 United States of America, do hereby
`extensibility and no elastic
`elongation.
`declare the nature of this invention and
`Therefore, and in order to properly close
`the upper of a ready made shoe, the laces 88
`in what.manner. the same is to be per-
`formed, to be particularly described and
`are severely pulled together. As a conse-
`ascertained in and by thefollowing state-
`quence of the unyielding character of
`ment :—
`.
`.
`these shoe laces the foot is excessively
`The invention relates to strings and
`compressed and tires easily and quickly.
`laces for footwear; it is applicable to other
`The wearer must loosen the shoe after a 90
`types of tying strings and laces where
`comparatively short period of wear, the
`
`G0 similar and—conditionsrequirements
`
`strain.and pressure exerted by the tightly
`prevail.
`.
`_.
`.
`.
`pulled shoe strings becoming unbearable.
`Tt is an established rule in the manu-
`Tf, on the other hand, the strings are
`not properly tied and the upper, conse- 95
`facture of shoes and particularly ready.
`made shoes that the size of the shoes is
`quently, is not properly closed, the foot
`g5 mainly controlled by the length of the.
`has no hold.and the walking in a loosely
`sole; the varying configuration and dimen-
`fitting shoe is, not only annoying. but
`sions of the instep is not considered in
`dangerous.
`_
`_
`the ordinary shoe making art.
`|
`From this failure of fabric or leather 100
`Consequently, the proper closure of the
`made shoe strings the suggestion arose to
`7 shoe upper
`has more or less become
`a
`make the same from rubber bands.
`Rubber bands, however,
`are highly
`;
`mandate of the shoe laces.
`|
`This
`function cannot be properly
`elastic and the easily yielding shoe strings
`made of rubber bands will not produce a 105
`accomplished by a shoe lace which ismade
`of fabrics or leather; this is particularly
`sufficient hold of the foot.
`76 true if the foot of the shoewearer is sensi-
`The use of leather, fabric and rubber
`made shoe strings causes another grave
`tive to pressure or if he suffers from weak-.
`ness or sickness of the upper. foot liga-
`disadvantage which is insufficient knot-
`proofness. The knots made with. this type 110
`ments.
`.
`ae
`The reasons for the failure of fabric
`of laces often open wnintentionally: this
`
`
`
`
`
`396,562
`
`8
`
`70
`
`108
`
`10
`
`deficiency makes itself particularly felt
`elastic elongation of between about 5 to
`during the initial periods of use.
`175 per cent. when subjected to a load
`Moreover, fabric, leather and rubber
`of about 10 pounds; this load corresponds
`shoe strings have the tendency of twist-
`approximately to the average pressure
`5 ing and kinking.
`.
`used forthe tying of a shoe lace.
`“Tt
`is an object of the invention to
`In many cases an elastic elongation of
`remedy the above recited shortcomings of
`about between 10 to 150 and even down to
`unyielding fabric and leather made shoe
`100 per cent. will satisfactorily serve the
`laces.- St
`purposes of this invention.
`¥t is another object of the invention to
`The above given elastic elongation 75
`avoid the disadvantages of highly elastic
`refers to a cross area of about one hundred-
`rubber made shoe laces which do not effect
`thirtieth square inch, which is equal to
`a sufficient hold of the foot.
`the average thickness of a normal shoe
`ace.
`-
`It is an important object of the inven-
`15 tion to manufacture a shoe lace which
`It was not to be foreseen that a shoe 80
`possesses a surprising-knot-proofness and
`lace severed from a band made of plastics
`will not untie itself unintentionally.
`having the above recited elastic elonga-
`Tt is also an object of the invention to
`tion would create the proper “ give,” that
`provide a shoe lace which does not kink
`it would at the sametime comply with the
`20 and twist.
`ae Se
`severe
`requirements of knot-proofness, 85
`It is a further-object of the invention
`afford the desired hold of the foot with-
`to produce a shoe string which will com-
`out undue pressure on the instep in spite
`pensate imperfectly fitting shoe uppers,
`ofa scanty and ill-fitting shoe upper and
`which-will permit a proper closure of the
`that it would not twist or kink.
`-
`same-without undue compression of the
`- Thermoplastics, such as vinyl, vinyl. 90
`foot
`and therefore be
`a
`relief
`for
`chloride, vinylacetate, acryl and meth-
`persons who have pressure-sensitive foot
`acryl resins having admixed thereto about
`- ligaments. -
`-
`10 to 85 and preferably 20 to 32 per cent.
`It is also an object of the invention to
`plasticizers, such as butyl compounds,
`30 provide a shoe lace which is-water impreg-
`phialates such as for instance dioctyl- 95
`nable, therefore does not
`shrink in
`phtalate have been found to be of parti-
`contact -with water and does not become
`cular aptitude for the making of the shoe
`slippery in contradistinction to leather
`laces in conformity with the invention.
`and textile made shoe laces which under
`The ‘‘ give” of the shoe laces may be
`86 these conditions greatly lose in: knot-
`improved by making the cross section of 100
`proofness.
`--
`--
`- the strip-shaped , plastics
`substantially
`_
`It is a-further object of the invention
`circular, oval orelliptic. The application
`to produce a shoe lace which in itself hag
`of inner channels to the strips whereby
`sufficient body or stiffness to be directed
`tubular shoe laces result, further increase
`40 into the eyelet of the shoe upper, does not
`the knot-proofness.
`oe
`need to be reinforced and which does not
`The latter may also be improved by
`unravel,
`-
`roughening the surface of the bands -or
`It is an important object of the inven-
`‘applying to the same a slightly irregular
`,,
`tion-to create a shoe lace which can be
`surface configuration; this object may be
`45 easily manufactured and colored, which
`accomplished by mechanical-processes 110
`is colorproof and has.a great beauty
`such as sand-blasting or metallization:
`appeal.
`Oe
`-
`fine powders. such as powdered fine siliea
`A. shoe lace which, answersthese objects
`or clay may be blasted onto the same; the
`will be termed a shoe lace having a proper
`same purpose may be achieved by appli-
`50 “give” because-its main requirements
`cation of slight surface grooves, buckles 115
`are met by mechanical characteristics of
`or lumps; chemical methods may be used
`the material used for their manufacture.
`for the same purpose, such as the creation
`With the above
`recited and other
`of fitie surface Precipitates; for this pur-
`objects
`in view which will
`become
`pose a solution of barium chloride may be —
`55 apparent as this specification proceeds,
`added to the plastic compoundprior to its 120
`the invention consists in the use of
`extrusion into a strip and the extruded
`plasties and particularly of continuous
`strip may be immediately passed through
`bands ofplastics for the manufacture of
`diluted sulphuric acid whereby a strongly
`shoe laces; the thus produced shoe laces
`adherent fine precipitate of barium sul- —
`80 are knotproof, water impreenable, do not
`phate is produced onits surface.
`125
`twist or kink, can be easily colored and
`_ Thesurface dullness which is a clear
`are colorproof.
`-The plastic bands or
`indicator for the: desired toughening of
`strips used in accordance with the inven-
`the surface of the plastic band may also
`.
`tion for the manufacture of
`the laces
`be-obtained if the extrusion is-effected at
`65 should preferably have a certain critical
`a possibly low temperature.
`
`
`
`AYS02
`
`10
`
`Jb
`
`20
`
`25
`
`Another means to accomplish effects of
`the above described type consists in the
`applicationof coatings, for instance pare-
`rubber, laequer and varnish coatings to
`the <trips upon theif exit
`from the
`extrusion press, whereby adjustments may
`be obtained of the elongation and Imoet-
`proofness.
`The same purpose may be obtained by
`applying cores or inserts to the plastic
`hands of a material which has a different
`and preferably a lesser elongation. than
`the plastie band. Cores-or inserts made
`of
`textiles will successfully serve this
`purpose. These cores may be applied. te
`the plastie band duringits extrusion irom
`in extrusion press.
`:
`oe
`However,
`it may also he possible te
`superpose two thin plastic sheets and an
`intermediary textile layer
`to unite the
`three superposed layers. for instance by
`heat to form.a compensate sheet. and to
`separate this. sheet
`into a plurality of
`strips from which the laces are severed.
`‘A. shoe lace made of plasties in. accord-
`ance with the just explained principles is
`by way of example illustrated.
`in
`the
`secompanying drawing. in which.
`.
`Fig. 1
`is a-plan of one embodiment.
`. Fig. 4 is a plan of the end portion of a
`second embodiment,
`.
`.
`~ Figs. 2. 3, Sand 6-are cross sections of
`different laces.
`.
`.
`.
`.
`For the manufacture of a shoe laee as
`exemplified in the drawings a. thermo:
`plastic material such as for instance a
`vinyl resin containing 23 per cent... of .a
`butyl compound plasticizer is estruded
`from an extrusion press at a temperature
`which is sufficiently low to just permit
`the extrusion into a-strip having o cross
`section of approximately one hundred-
`thirtieth, square inch.
`Le
`Tf laces are used having a
`circular.
`elliptical, aval ar tubular cross section as
`shown in Figs. 2. 3, 5 and 6, a very satis-
`factory knot-proofness is obtained.
`Tn order to apply surface irregulations
`to, the plastie strips, such as grooves or
`ribs by mechanieal means. the extrusion
`nozzles of the press may. be correspond-
`ingly shaped or accordingly surfaced
`rollers may he used,
`.
`‘The laces are tapered at both ends and
`the ends do not require reinforcement:
`the ends do not unravel. A great advan-
`tage of the specific plastics used in the
`realization of the inyention is that they
`do not twist and kink during the tying
`procedure. 0
`he above given elastic elongation will,
`. of course. undergo a corresponding modi-
`fication if the cross section of the band is
`vuried or a different load is applied; how-
`65 ever, it is understood that any strip of a
`
`30
`
`35
`
`40
`
`45
`
`50
`
`65
`
`60
`
`plastic material is embraced by the inven-
`fon which has: the ubove recited elastic
`elongation.
`OO
`;
`"Havingnowparticularly deseribed and
`“nscertained the nature of my said inven- 70
`Hon and in. what manner the same is to —
`he performed, T declare that what T claim
`is:—
`1. A knot-proof
`lace for
`tying pur-
`poses, characterized therein that it con- J
`sists of a section severed from a continuous
`band made of a thermoplastic material.
`2. A knot-proof lace accordingto claim
`1, characterized therein that the thermo-
`plustie band has an elastie elongation of
`between about 5 to 174 per cent. when
`subjected to a load of about ten pounds.
`3. -.A knot-proof lace far tying purposes
`areording te claim 1, cha racterised there-
`in that the thermoplastie band has an
`elastic elongation of between about 10 to
`150 per cent. when subjected to a load of
`‘ahout ten pounds.
`-4, A knot-proof lace according to claim
`1. characterized therein that the thermo-
`plastic hand has an. elastic elongation of
`hetween about 10 to 100 per cent. when
`subjected to aload of aboutten pounds.
`_ 5, A knot-proof Jace according to claim
`j. characterized therein that the ends of
`the band-section are tapered.
`_ 6. A knot-proof lace according to claim
`1, characterized therein that
`fhe con-
`Hnnous-band of a thermoplastic material
`has an elliptical or oval or eireular or
`tubular cross: section.
`_ ¥. A knot-proof lace according to claim
`1, characterized therein that it
`is pro-
`vided with a ranghened surface configura-
`tion.
`-
`8. A knot-proof lace according to claim
`6, characterized therein that it is provided
`with a coating.to. control the elastic elon-
`aation ofthe thermoplastic band.
`9.. A knot-proof lace according to claim
`§. characterized therein that it is provided
`with 2 core to contro] the elastic elonga-
`toneof the plastic band.
`aceording to
`10. A knot-proof
`lace
`claim 1..characterized therein that it con-
`tains a core or insert of a textile material.
`11. A method of producing knot-provf
`shoe lace accordingto claim1, character-
`ized in shaping a-thermoplastic material
`having an elastic elongation of between 5
`to 175 per cent. into a continuous band
`and severing said band into sections of
`shoe lace length.
`.
`12. A method aceording to claim 11.
`characterized therein that a core or insert
`is applied to the thermoplastic band to
`control its elastic elongation.
`18. .4 method according to claim 11,
`characterized therein that a core or insert
`at a.textile material
`is applied to the
`
`80
`
`eh
`
`100
`
`106
`
`110
`
`115
`
`125
`
`130
`
`
`
`. 596,562
`
`5
`
`10
`
`thermoplastic band during its extrusion
`into a continuous band having an ellip-
`from an extrusion press.
`tical or quadrangular or oval or circular 25
`14. A method according to claim 11,
`or tubular cross section and an elastic
`characterized therein that sheets of
`a
`elongation of between 5 to 175 per cent.,
`5 thermoplastic material and a textile sheet
`severing said band into sections of shoe
`serving as an insert are superposed and
`lace length and tapering the ends of said
`sections.
`«80
`united and that the united sheet is severed
`into strips and the strips are cut into shoe
`17. A method of producing knot-proof
`lace length.
`shoe laces according io claim 15, charac-
`15. A method of producing knot-proof
`terized in imparting to the thermoplastic
`shoe laces according to claim 11, charac-
`band a roughened surface configuration.
`terized in extruding a
`thermoplastic
`18. A method of producing knot-proof 365
`material having about 10 to 85 per cent.
`shoe laces according to claim 15, charac-
`of a plasticizer admixed thereto into a
`terized in applying to the extensible
`45 continuous band having an elastie elon-
`thermoplastic band a coating to control
`gation of between 5 to 175 per cent., sever-
`its degree of elastic elongation.
`ing said band into sections of shoe lace
`Dated the 18th day of December, 1946.
`length and tapering the ends of the said
`ELKINGTON & FIFE,
`sections.
`Consulting Chemists and Chartered
`16. A method of producing knot-proof
`Patent Agents,
`shoe laces comprising extruding a thermo-
`Bank Chambers,
`plastic material having about 10 to 35
`329, High Holborn, London, W.C.1,
`per cent. of a plasticizer admixed thereto
`Agents for the Applicant.
`
`Leamington Spa: Printed for His Majesty’s Stationery Office, by the Courier Press—1948.
`Published at The Patent Office, 25, Southampton Buildings, London, W.C.2, from which
`copies, price 1s. 0d. each (inland) 1s. 1d. (abroad> may be obtained.
`
`
`
`596,562 COMPLETE SPECIFICATION
`
`
`
`1 SHEET
`
`[ThisDrawingisareproductionoftheOriginalonareducedscate]
`
`
`
`
`
`
`
`H.M.S.Q.(Ty. P.)
`
`
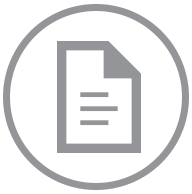
Accessing this document will incur an additional charge of $.
After purchase, you can access this document again without charge.
Accept $ ChargeStill Working On It
This document is taking longer than usual to download. This can happen if we need to contact the court directly to obtain the document and their servers are running slowly.
Give it another minute or two to complete, and then try the refresh button.
A few More Minutes ... Still Working
It can take up to 5 minutes for us to download a document if the court servers are running slowly.
Thank you for your continued patience.
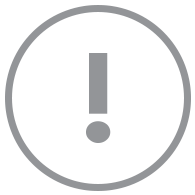
This document could not be displayed.
We could not find this document within its docket. Please go back to the docket page and check the link. If that does not work, go back to the docket and refresh it to pull the newest information.
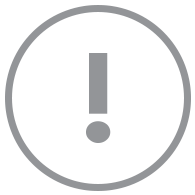
Your account does not support viewing this document.
You need a Paid Account to view this document. Click here to change your account type.
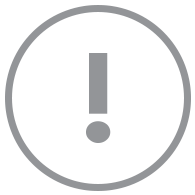
Your account does not support viewing this document.
Set your membership
status to view this document.
With a Docket Alarm membership, you'll
get a whole lot more, including:
- Up-to-date information for this case.
- Email alerts whenever there is an update.
- Full text search for other cases.
- Get email alerts whenever a new case matches your search.
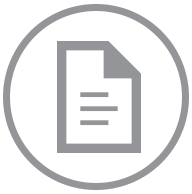
One Moment Please
The filing “” is large (MB) and is being downloaded.
Please refresh this page in a few minutes to see if the filing has been downloaded. The filing will also be emailed to you when the download completes.
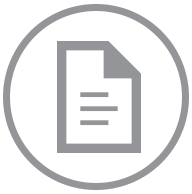
Your document is on its way!
If you do not receive the document in five minutes, contact support at support@docketalarm.com.
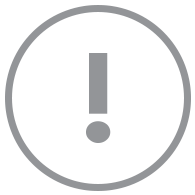
Sealed Document
We are unable to display this document, it may be under a court ordered seal.
If you have proper credentials to access the file, you may proceed directly to the court's system using your government issued username and password.
Access Government Site