`
`(12)
`
`Patenta m1
`Europfiisches
`European
`Patent Office
`Office e u ropéen
`
`des brevets (11)
`
`EP 2 757 254 A1
`
`EUROPEAN PATENT APPLICATION
`
`(43) Date of publication:
`23.07.2014 Bulletin 2014/30
`
`(51)
`
`Int CL:
`F030 71020005101)
`
`F030 1106(2006-01)
`
`(21) Application number: 133820225
`
`(22) Date of filing: 21.01.2013
`
`
`(84) Designated Contracting States:
`AL AT BE BG CH CY CZ DE DK EE ES FI FR GB
`GR HR HU IE IS IT LI LT LU LV MC MK MT NL NO
`PL PT RO RS SE SI SK SM TR
`
`Designated Extension States:
`BA ME
`
`(72)
`
`Inventor: Betran, Jaume
`08172 SANT CUGAT DEL VALLES (ES)
`
`(74) Representative: ZBM Patents - Zea, Barlocci &
`Markvardsen
`
`Plaza Catalunya, 1
`08002 Barcelona (ES)
`
`(71) Applicant: Alstom Wind, S.L.U.
`08005 Barcelona (ES)
`
`
`(54) Wind turbine blade
`
`Wind turbine blade comprising at least one de-
`(57)
`formable trailing edge section having a plurality of actu-
`ators consecutively arranged substantially downstream
`from one another and a control system for controlling the
`actuators, wherein a downstream end of one actuator is
`connected by a substantially rigid link with an upstream
`
`end of the next actuator and the plurality of actuators
`comprises an upper actuator being mounted above a
`chord line ofthe blade section and a lower actuator being
`mounted below a chord line of the blade section. Wind
`
`turbines comprising such a blade and methods of con-
`trolling loads on a wind turbine blade are also described.
`
`
`
`
`
`24
`
`EP2757254A1
`
`
`
`Printed by Jouve, 75001 PARIS (FR)
`
`
`
`1
`
`EP 2 757 254 A1
`
`2
`
`Description
`
`[0001] The present application relates to wind turbine
`blades comprising at least one deformable trailing edge
`section and wind turbines comprising such blades. Itfur—
`ther relates to methods of controlling loads on such wind
`turbine blades.
`
`BACKGROUND ART
`
`[0002] Modern wind turbines are commonly used to
`supply electricity into the electrical grid. Wind turbines
`generally comprise a rotorwith a rotor hub and a plurality
`of blades. The rotor is set into rotation underthe influence
`ofthe wind on the blades. The rotation ofthe rotor shaft
`
`drives the generatorrotoreitherdirectly("directly driven")
`orthrough the use ofa gearbox. The gearbox (if present),
`the generator and other systems are usually mounted in
`a nacelle on top of a wind turbine tower.
`[0003]
`Pitch systems are normally employed foradapt—
`ing the position of the blades to varying wind conditions.
`In this respect, it is known to rotate the position of each
`blade along its longitudinal axis in such a way that lift and
`drag are changed to reduce torque. This way, even
`though the wind speed increases, the torque transmitted
`by the rotor to the generator remains substantially the
`same. Using pitch systems may be particularly suitable
`for adapting the wind turbine blade to a varying wind
`speed. However, the control ofthe pitch systems may be
`rather slow and may not be suitable to react to a sudden
`wind gust or any other high rate changing wind condi-
`tions.
`
`Some systems change the aerodynamics of a
`[0004]
`wind turbine blade by providing the blade with a trailing
`edgeflap hinged to a main body. However, deflecting the
`aerodynamic surface about a hinged point may lead to
`flow separation which may cause abrupt aerodynamic
`changes thus decreasing load alleviation and reducing
`efficiency of the wind turbine.
`[0005] DocumentW02004/088130describesthe con-
`trol of aerodynamic forces substantially instantaneously
`and locally along the blades of a wind turbine rotor by
`continuous variation ofthe airfoil geometry in the leading
`edge region and trailing edge region along part or the
`whole blade span. It further describes the use of smart
`materials or mechanical actuators integrated in a deform-
`able material changing the outer geometry in the leading
`and trailing edge region and thereby changing the blade
`section aerodynamic forces.
`
`SUMMARY
`
`It is an object of the present disclosure to pro-
`[0006]
`vide an improved blade allowing variation of airfoil ge-
`ometry.
`In afirstaspecta wind turbine blade is provided.
`[0007]
`The blade comprises at least one deformable trailing
`edge section having a plurality ofactuators consecutively
`
`arranged substantially downstream from one another
`and a control system for controlling the actuators, where-
`in a downstream end of one actuator is connected by a
`substantially rigid link with an upstream end of the next
`actuator; and the plurality of actuators com prises an up—
`per actuator being mounted above a chord line of the
`blade section and a lower actuator being mounted below
`a chord line of the blade section.
`
`[0008] According to this aspect, at least one upper ac—
`tuator and at least one lower actuator are provided inside
`the trailing edge section. This ensures at least two de-
`grees offreedom to the control system. Furthermore, the
`fact that two consecutive actuators are connected to each
`
`other by a rigid link ensures a leverage effect between
`them. The actuators may thus reinforce each other, or at
`least partially cancel one another’s effects. The blades
`trailing edge shape may thus be widely changed upon
`activation of the actuators. This modifies the aerodynam-
`ic surface of the blade so that it can be used to e.g. mit—
`igate the loads acting on the blades. All this may be
`achievedwithoutexcessively complicatingawindturbine
`blade structure.
`
`In some embodiments, at least one upper ac—
`[0009]
`tuator may be mounted close to an inner surface of a
`suction side of a skin of the blade trailing edge section
`and at least one lower actuator may be mounted close
`to an inner surface of a pressure side of a skin of the
`blade trailing edge section. Mounting the actuators close
`to opposite inner surfaces of the blade’ skin improves the
`shape ofthe deflected trailing edge and the leverage ac—
`tion between consecutive actuators can be increased. In
`
`some of these cases, the at leastone upperactuator may
`be mounted directly to the inner surface of the suction
`side ofthe blade skin and the at least one lower actuator
`
`may be mounted directly to the inner surface ofthe pres-
`sure side of the blade skin.
`
`In some embodiments, the rigid links connected
`[0010]
`to the upstream end of the actuators may be mounted
`substantially perpendicular to the blade skin. This way,
`the aerodynamic profile may be changed in a verysmooth
`manner, e.g. reducing or avoiding local bulging ofa pro—
`file.
`
`[0011] Another aspect provides a wind turbine com-
`prising at least one blade substantially as hereinbefore
`described.
`
`[0012] A further aspect provides a method of control-
`ling a wind turbine blade substantially as hereinbefore
`described, the method comprising activating at least one
`upperand/orat least one lower actuator such thata struc—
`tural shape of the blade trailing edge changes in at least
`two degrees offreedom, e.g. flap angle and chord length.
`[0013] Additional objects, advantages and features of
`embodiments of the present invention will become ap-
`parent tc those skilled in the art upon examination of the
`description, or may be learned by practice of the inven-
`tion.
`
`10
`
`15
`
`20
`
`25
`
`30
`
`35
`
`40
`
`45
`
`50
`
`55
`
`
`
`3
`
`EP 2 757 254 A1
`
`4
`
`BRIEF DESCRIPTION OF THE DRAWINGS
`
`Particular embodiments of the present inven-
`[0014]
`tion will be described in the following by way of non-lim-
`iting examples, with reference to the appended drawings,
`in which:
`
`Figure 1 shows a cross-sectional view of a wind tur-
`bine blade according to an embodiment;
`
`10
`
`Figures 23-2d show cross-sectional views of wind
`turbine blades according to other embodiments; and
`
`Figure 3 shows a cross-sectional view of a wind tur-
`bine blade according to yet another embodiment.
`
`15
`
`DETAILED DESCRIPTION OF EMBODIMENTS
`
`Figure 1 shows a cross—sectional view ofa wind
`[0015]
`turbine blade 10 having a skin 1 1 . The blade section may
`comprise a deformable trailing edge portion 12 and a
`substantially non-deformable portion 13. Figure 1 shows
`two states ofthe blade section: an initial shape indicated
`by dotted lines 12a where the trailing edge is non-de-
`formed and a deformed shape indicated by solid lines
`where the trailing edge portion 12 is deformed.
`[0016] The deformable trailing edge may extend on the
`total length of the blade or it may extend on at least one
`section ofthe blade, e.g. on substantially one third ofthe
`total length, in particular the portion closest to the tip of
`the blade. In other cases, a plurality ofdeformable trailing
`edge sections may also be provided.
`[0017] A spar box 14 may be arranged inside the sub-
`stantially non—deformable portion 13 of the blade in order
`to maintain the distance between an inner surface of a
`suction side 15 of the blade and an inner surface of a
`
`pressure side 16 ofthe blade. The spar box 14 may sup-
`port wind loads acting on the blades, and in particular
`the blade bending loads. A rigid structure 17 may further
`be arranged inside the substantially non-deformable por-
`tion 13 of the blade. Such a structure 17 may support at
`least in part the loads derived from the deformable trailing
`edge 12 and may have a substantially C-shaped cross-
`section, the upper and lower parts of the C supporting
`the blade skin.
`
`[0018] The embodiment shown in figure 1 may com-
`prise five piezoelectric actuators P1-P5 arranged inside
`the trailing edge portion 12. Actuators P1, P3 and P5 may
`be mounted below a chord line A—A of the blade cross—
`
`section thus being lower actuators and actuators P2 and
`P4 may be mounted above the chord line A-A ofthe blade
`thus being upper actuators. According to this embodi—
`ment, the lower actuators may be mounted substantially
`tangential to an inner surface of a pressure side 16 of
`the blade skin and the upper actuators may be mounted
`substantially tangential to an inner surface of a suction
`side 15 of the blade skin.
`
`20
`
`25
`
`30
`
`35
`
`40
`
`45
`
`50
`
`55
`
`connecting each actuator to the next consecutive actu—
`ator. It should be understood that the rigid links may be
`structural elements, e.g. beams, having a sufficient stiff-
`ness such as not to deform, in particular under the influ-
`ence of the actuators.
`
`in figure 1, rigid link 20 may connect a down-
`[0020]
`stream end (arrow D) of actuator P1 with an upstream
`end (arrow U) of actuator P2, rigid link 21 may connect
`a downstream end of actuator P2 with an upstream end
`of actuator P3, rigid link 22 may connect a downstream
`end of actuator P3 with an upstream end of actuator P4
`and rigid link 23 may connect a downstream end of ac—
`tuator P4 with an upstream end of actuator P5. Further-
`more, an upstream end of actuator P1 may be connected
`to the rigid structure 17 provided in the non-deformable
`portion 13 and a downstream end ofactuator P5 may be
`connected to the blade skin at the trailing edge end 18
`by a relatively rigid structure 24.
`[0021]
`In addition, skin areas 19 of the trailing edge
`portion 12 that are not supporting the actuators P1-P5,
`the rigid links 20-23 or the rigid structure 24 may be made
`ofa relativelyflexible material. This ensures deformablllty
`and smoothness of the blade surface upon actuation of
`any actuator. Elastic or elastomeric materials are exam-
`ple of materials conferring the needed flexibility so that
`cracks due to fatigue loads are reduced. The rest 191 of
`the blade skin may be made out of any known composite
`material typically used in wind turbine blades construc-
`tion in order to maintain blade’s high rigidity and resist-
`ance to fatigue and wear while not compromising its
`weight.
`In an alternative example, the skin areas sup-
`[0022]
`porting the rigid links may be made from the same rela-
`tively flexible material (see figure 2d), since the rigid links
`may give sufficient support by themselves.
`[0023] A control system for controlling the actuators
`may also be provided. In the example illustrated in figure
`1 the control system may apply an electrical field on the
`piezoelectric elements so as to generate a mechanical
`strain (deformation) on the surface (blade skin) on which
`the actuators are being mounted. Based on the reverse
`piezoelectric effect, each actuator converts the input sig-
`nal received from the control system into an internal me-
`chanical deformation of the piezoelectric element thus
`deforming the surface ofthe blade on which it is mounted.
`The rigid links ensure a combined effect between the
`actuators. Loads acting on the blade may thus be easily
`compensated by adapting the shape of the blade.
`[0024]
`In the example of figure 1, many combinations
`of piezoelectric activation may be possible: each of the
`piezoelectric elements may be deformed in an upwards
`manner, a downwards manner or may be maintained in
`the default neutral position. Using the plurality of actua-
`tors, a very large number of combinations of flap angle
`and/or chord length of the blade may be available to ad-
`just lift (and drag and pitch moment) to adaptto changing
`wind loads.
`
`[0019]
`
`Rigid links 20-23 may further be provided for
`
`[0025] As used herein the chord line is the imaginary
`
`
`
`5
`
`EP 2 757 254 A1
`
`6
`
`straight line defined between the leading and trailing
`edge when the flap angle is zero. Considering a sign
`convention in which a minus sign is used for deformation
`of the trailing edge towards the suction side and a plus
`sign is used for a deformation ofthe trailing edge towards
`the pressure side, the following cases are only some of
`several possible combinations available for the embod-
`iment of figure 1:
`
`Case 1: actuators P1, P3 and P5 may be deformed
`towards the pressure side and actuators P2 and P4
`may be deformed towards the suction side, then the
`flap angle may be substantially maintained but the
`chord length may be extended. The lift coefficient
`may thus be slightly modified with a larger chord
`length. This may provide higher lift.
`
`Case 2: actuators P1, P3 and P5 may be deformed
`towards the suction side and actuators P2 and P4
`
`may be deformed towards the pressure side, then
`the flap angle may be substantially maintained and
`the chord length may be reduced. The lift coefficient
`may thus be slightly modified with a shorter chord
`length. This may provide lower lift.
`
`Case 3: actuators P1, P3, P4 and P5 may be de-
`formed towards the suction side and actuator P2 may
`be deformed towards the pressure side, the flap an-
`gle may thus be reduced while the chord length may
`be only slightly modified. The lift may be lowered.
`
`Case 4: actuators P1, P3, P4 and P5 may be de-
`formed towards the pressure side and actuator P2
`may be deformed towards the suction side, the flap
`angle may thus be increased while the chord length
`may be only slightly modified. The lift may be in-
`creased.
`
`Case 5: only actuator P1 may be deformed. In this
`case, the deformable trailing edge may act substan-
`tially as a hinged flap.
`
`Case 6: all actuators may be deformed towards the
`pressure side.
`in this case, the chord length may
`remain substantially the same and the lift may be
`increased.
`
`[0026] Clearly, many other options are available.
`[0027]
`in general for blades having a positive angle of
`attack, actuating the trailing edge portion towards its pos-
`itive position (pressure side) increases the lift. The loads
`on a blade may thus be increased, but this may be ac—
`ceptable and/or desirable,
`in accordance with circum-
`stances (e.g. sudden temporary decrease in wind
`speed). The increase of the lift increases the aerodynam-
`ic torque of the rotor. Furthermore, actuating a trailing
`edge portion towards its negative position (suction side)
`decreases the lift. The decrease in lift reduces the aero-
`
`dynamic torque and the loads on the blade in general.
`Deforming the trailing edge towards suction side may
`thus be used to counteract e.g. temporary high loads on
`a blade (sudden wind gusts).
`[0028]
`Figures 2a—2d show alternative embodiments.
`The same reference numbers will be used for matching
`parts.
`[0029] The alternative illustrated in figure 2a differs
`from that of figure 1
`in that inner areas 30 of the blade
`trailing edge portion 12 may be filled with a material with
`a honeycomb structure. This kind of material may be rel-
`atively lightweight and display a desirable anisotropic be—
`havior: it may be relatively stiff in a direction substantially
`perpendicular to the chord line, i.e. it is stiff so as to main-
`tain the airfoil thickness and not deform under aerody-
`namic pressure. At the same time, it may be more flexible
`in a direction substantially parallel to the chord line, thus
`allowing proper movement of the actuators. in other im-
`plementations, instead of a honeycomb structure mate—
`rial, other kinds of lightweight materials having such an-
`isotropic properties so as to permit an internal structural
`behavior may also be used.
`[0030] The alternative illustrated in figure 2b differs
`from that of figure 2a in that the rigid links 20-23 may be
`mounted substantially perpendicular to the blade skin at
`their end 20u, 21 u, 22u and 23u connecting upstream
`ends U ofactuators P2—P5. By having the rigid links sub—
`stantially perpendicular to the skin of the blade, the aer-
`odynamic profile may be deformed in a smoother man-
`ner, e.g. local bulging may be avoided or reduced.
`[0031] The alternative illustrated in figure 20 differs
`from that of figure 1
`in that those inner areas 31 of the
`blade trailing edge portion 12which are immediately next
`to the flexible material used forskin areas 19 ofthe trailing
`edge portion may comprise a honeycomb structure ma-
`terial (or similar) lying over the flexible material. The skin
`surface may thus be particularly stiff to withstand aero-
`dynamic loads, but more easily allow deformation of the
`skin in a direction perpendicular to that. If e.g. the most
`upstream lower actuator is activated, the rigid link be-
`tween this actuator and the consecutive upper actuator
`will move axially. An anisotropic material such as the one
`described may be particularly suitable.
`[0032] The alternative illustrated in figure 2d differs
`from that of figure 2a in that actuators P2—P4 although
`being respectively upper or lower actuators as explained
`in connection with figure 1, are not mounted tangential
`to the blade skin but they may be horizontally mounted
`in between two rigid links,
`i.e. P2 may be mounted in
`between rigid links 20 and 21, P3 in between rigid links
`21 and 22 and P4 in between rigid links 22 and 23a. With
`this internal structure, a suction side 15 of the blade skin
`along almost the whole trailing edge 12 may be made of
`a substantially flexible material 19’ (with the exception of
`the trailing edge end 18 and the area on which structural
`element 24 rests) and a pressure side 16 of the blade
`skin along almost the whole trailing edge 12 (with the
`exception ofthe areas on which actuators P1 and P5 and
`
`10
`
`15
`
`20
`
`25
`
`30
`
`35
`
`40
`
`45
`
`50
`
`55
`
`
`
`7
`
`EP 2 757 254 A1
`
`8
`
`rigid link 20 rest) may also be made of a flexible material
`19". Furthermore, the alternative illustrated in figure 2d
`may comprise inner areas 30 of the blade trailing edge
`portion 12 that may be filled with a honeycomb structure
`material as explained above in connection with figure 2a.
`[0033] Contrary to previous examples, the rigid links
`are not supported by "normal" skin material
`i.e. any
`known composite material typically used in wind turbine
`blades construction. Because of the rigidity of the links,
`no stiff skin material is needed and thus manufacture of
`
`the blade may be simplified. Alternatively, the rigid links
`may be supported by normal skin material.
`[0034]
`Figure 3 shows a cross-sectional view ofa wind
`turbine blade 10’ according to another embodiment. The
`same reference numbers will be used for matching parts.
`[0035] The embodiment of figure 3 may comprise two
`piezoelectric actuators P1’ and P2’ that may be arranged
`respectively below (lower actuator) and above (upper ac-
`tuator) a chord line (not shown) of the blade section. In
`this case a substantially rigid element in the form of a
`rigid beam 17’ may emerge from the spar box 14 towards
`the trailing edge end 18. In order to arrange both actua-
`tors P1’ and P2’ substantially downstream from one an—
`other, the lower actuator P1' may be mounted in between
`such a rigid beam 17’ and a rigid link 20’ connecting a
`downstream end D1 of actuator P1’ with an upstream
`end U2 of actuator P2’ and a downstream end D2 of
`
`actuator P2’ may be connected to a further structural el-
`ement 24’ connected to the trailing edge end 18. In this
`case inner areas 30’ of the blade trailing edge portion 12
`may also be filled with a honeycomb structure material.
`Furthermore, the blade skin of almost the whole trailing
`edge portion 12 may be made of a flexible material 19‘"
`with the exception of the trailing edge end 18 and that
`area on which structural element 24’ rests.
`
`[0036] As explained above, the basic principle lies on
`having at
`least
`two actuators arranged substantially
`downstream from one another and connected to each
`
`other by a substantially rigid link conforming an internal
`structure arranged inside a trailing edge portion ofa blade
`section such that upon activation of any of the actuators
`a structural shape of the trailing edge portion changes.
`[0037] Although the actuators described are piezoe-
`lectric elements, it should be understood that other type
`ofactuators having a substantially instantaneously lineal
`behavior such as bistable elements or mechanical actu-
`
`ators such as pneumatic or hydraulic cylinders may also
`be foreseen. Furthermore, other combinations and/or
`quantity of actuators are also possible as long as there
`are at least two actuators, one being an upper actuator
`and the other being a lower actuator. This way, whenever
`three or more actuators are being used a substantially
`zig-zag shape can be defined.
`[0038] Although only a number of particular embodi-
`ments and examples of the invention have been dis-
`closed herein, itwill be understood by those skilled in the
`art that other alternative embodiments and/or uses of the
`
`thereofare possible. Furthermore, the present invention
`covers all possible combinations of the particular embod-
`iments described. Thus, the scope of the present inven-
`tion should not be limited by particular embodiments, but
`should be determined only by a fair reading of the claims
`that follow.
`
`Claims
`
`1. Wind turbine blade comprising at least one deform-
`able trailing edge section having
`a plurality of actuators consecutively arranged sub-
`stantially downstream from one another and a con-
`trol system for controlling the actuators,
`wherein a downstream end of one actuator is con—
`
`nected by a substantially rigid link with an upstream
`end ofthe next actuator and the plurality of actuators
`comprises an upper actuator being mounted above
`a chord line ofthe blade section and a lower actuator
`
`being mounted below a chord line of the blade sec-
`tion.
`
`2. Wind turbine blade according to claim 1, wherein the
`actuators are alternatingly upper and lower actua-
`tors.
`
`3. Wind turbine blade according to any of claims 1 or
`2, wherein the actuators are linked such that upon
`activation of at least one upper and/or at least one
`lower actuator a structural shape of the blade trailing
`edge section changes in at least two degrees offree-
`dom.
`
`4. Wind turbine blade according to claim 3, wherein the
`actuators are linked such that upon activation of at
`least one upper and/or at least one lower actuator
`at leastone of a flap angle and a chord length of the
`blade is changed.
`
`5. Wind turbine blade according to any of claims 1—4,
`wherein at leastone upper actuator is mounted close
`to an inner surface of a suction side of a skin of the
`
`blade trailing edge section and at least one lower
`actuator is mounted close to an inner surface of a
`
`pressure side of a skin of the blade trailing edge sec-
`tion.
`
`6. Wind turbine blade according to claim 5, wherein the
`actuators are mounted substantially parallel to the
`blade skin.
`
`7. Wind turbine blade according to any of claims 1-6,
`wherein the rigid links connected to the upstream
`end of the actuators are mounted substantially per-
`pendicular to the blade skin.
`
`10
`
`15
`
`20
`
`25
`
`30
`
`35
`
`40
`
`45
`
`50
`
`55
`
`invention and obvious modifications and equivalents
`
`8. Wind turbine blade according to any of claims 1-7,
`
`
`
`9
`
`EP 2 757 254 A1
`
`10
`
`10.
`
`11.
`
`12.
`
`13.
`
`14.
`
`15.
`
`16.
`
`wherein the actuators are selected among a group
`consisting of piezoelectric elements, bistable ele-
`ments and pneumatic or hydraulic actuators.
`
`Wind turbine blade according to any of claims 1—8,
`wherein the deformable trailing edge section ex-
`tends on one third of the total length of the blade,
`towards a tip of the blade.
`
`Wind turbine blade according to any of claims 1-9,
`wherein the deformable trailing edge section spans
`on a range between 30% and 40% of the chord line
`of the blade section.
`
`Wind turbine blade according to any of claims 1-10,
`wherein at least portions ofa skin ofthe blade trailing
`edge section, not supporting the actuators, nor the
`rigid links, are made ofa relatively flexible material.
`
`Wind turbine blade according to claim 11, wherein
`substantially the whole blade trailing edge section
`skin is made of a relatively flexible material.
`
`Wind turbine blade according to any of claims 11-12,
`wherein at least inner areas of the blade trailing edge
`section next to the flexible material are filled with an
`
`anisotropic material.
`
`10
`
`15
`
`20
`
`25
`
`Wind turbine blade according to claim 13, wherein
`the anisotropic material is a honeycomb structure.
`
`30
`
`Wind turbine comprising at leastone blade according
`to any of claims 1-14.
`
`Method of controlling loads on a wind turbine blade
`according to any of claims 1-14, wherein the method
`comprises activating at least one upper and/or at
`leastone lower actuator such that a structural shape
`of the blade trailing edge section changes in at least
`two degrees of freedom.
`
`35
`
`40
`
`45
`
`50
`
`55
`
`
`
`EP 2 757 254 A1
`
`
`
`
`
`EP 2 757 254 A1
`
`f}#53
`
`. P
`
` FIG.23
`
`
`
`EP 2 757 254 A1
`
`
`
`
`
`EP 2 757 254 A1
`
`
`
`FIG.20
`
`10
`
`
`
`EP 2 757 254 A1
`
`
`
`FIG.2d
`
`11
`
`
`
`EP 2 757 254 A1
`
`
`
`12
`
`
`
`EP 2 757 254 A1
`
`Europiisches
`Patent: mt
`European
`Patent offlre
`Office européen
`
`des brevets
`
`EU ROPEAN SEARCH REPORT
`
`Application Number
`EP 13 38 2022
`
`
`DOCUMENTS CONSIDERED TO BE RELEVANT
`
`Categon/
`
`of reievant assaes
`Citation of document with indication, where appropriate,
`
`toclaim
`Relevant
`
`APPLICATION UPC)
`CLASSIFICATION OF THE
`
`Y
`
`Y
`
`A
`
`A
`
`A
`
`
`
`N E
`
`POFORM15030382(P011001)
`
`10
`
`15
`
`20
`
`25
`
`30
`
`35
`
`40
`
`45
`
`50
`
`55
`
`us 2007/036653 A1 (BAK DAN c
`BAK DAN CHRISTIAN [DK] ET AL)
`15 February 2007 (2007-02-15)
`*
`* paragraphs [0057]
`-
`[0060]; figures 6-8
`
`[DK] ET AL
`
`(PEREZ JUAN [DE])
`US 2002/100842 Al
`1 August 2002 (2002-08-01)
`[0039],
`* paragraphs [0029],
`[0038],
`[0049],
`[0050]; figures 19,20 *
`
`US 2001/052287 A1 (PEREZ JUAN [DE] ET AL)
`20 December 2001 (2001-12-20)
`* paragraph [0056]; figures 12,13 *
`
`us 6 375 127 01 (APPA KARI
`23 Aprii 2002 (2002-04-23)
`* coiumn 6,
`line 8 - Tine 61; figures
`2,4,5 *
`
`[03])
`
`US 2010/247314 A1 (NARASIMALU SRIKANTH
`[50]) 30 September 2010 (2010-09-30)
`* paragraphs [0028]
`-
`[0030]; figures *
`-----
`
`
`
`1-6,8-16 INV.
`F03D7/02
`F03D1/06
`
`1-6,8-16
`
`1,16
`
`1,16
`
`1,16
`
`TECHNICALFIELIIILSC
`SEARCHED
`I
`F030
`B64C
`
`’
`
`
`
`The present search report has been drawn up for ail claims
`Place of Search
`Date of completion cf the search
`
`Examiner
`
`The Hague
`CATEGORY OF CITED DOCUMENTS
`X: particuiarly relevant iftaken alone
`V : particuiorly relevant if combined With another
`document of the same category
`A : technoiogical background
`0: non-written disclosure
`P : intermediate document
`
`Area] Caiama, A
`8 Juiy 2013
`T : theory or principle underlying the invention
`E: eariier patent document, but pubiished on, or
`after the filing date
`D ' document cited in the application
`L ' document cited for other reasons
`
`tit:nienrherofthesamerpatemiarriiiy,oorfispohding N
`document
`
`1
`
`1
`
`13
`
`
`
`EP2757254A1
`
`ANNEXTOTHEEUROPEANSEARCHREPORT
`ON EUROPEAN PATENT APPLICATION NO.
`
`EP 13 38 2022
`
`This annex lists the patent family members relating to the patent documents cited in the above-mentioned EJropean search report.
`The members are as contained in the European Patent Office EDP file on
`The European Patent Office is in no way liable for these particulars which are merely given for the purpose of information
`08-07-2013
`
`Patent document
`citedIn search report
`
`Publication
`date
`
`Patent family
`member(s)
`
`Publication
`date
`
`US 2007036653
`
`A1
`
`15- 02- 2007
`
`FORMP0459
`
`E For more details about this annex :see Official Journal ofthe European Patent Office, No 12/82
`
`14
`
`2004225883A
`2521045A
`1780983
`1613860
`2007036653
`2004088130
`
`286474
`10055961
`1205383
`2234749
`2002100842
`
`341716
`10009157
`1128072
`2270909
`2001052287
`
`CN
`CN
`EP
`US
`
`101865076
`201757024
`2233735
`2010247314
`
`14- 10- 2004
`14- 10- 2004
`31- 05- 2006
`11-01-2006
`15-02-2007
`14-10-2004
`
`15—01—2005
`23-05-2002
`15-05-2002
`01-07-2005
`01-08-2002
`
`15-10-2006
`13-09-2001
`29-08-2001
`16-04-2007
`20-12-2001
`
`20-10-2010
`09-03-2011
`29-09-2010
`
`30-09-2010
`
`10
`
`15
`
`20
`
`25
`
`30
`
`35
`
`40
`
`45
`
`50
`
`55
`
`
`
`REFERENCES CITED IN THE DESCRIPTION
`
`EP 2 757 254 A1
`
`This list of references cited by the applicant is for the reader’s convenience only. it does not form part of the European
`patent document. Even though great care has been taken in compiling the references, errors or omissions cannot be
`excluded and the EPO disclaims all liability in this regard.
`
`Patent documents cited in the description
`
`- WO 2004088130 A [0005]
`
`15
`
`
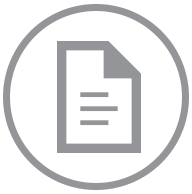
Accessing this document will incur an additional charge of $.
After purchase, you can access this document again without charge.
Accept $ ChargeStill Working On It
This document is taking longer than usual to download. This can happen if we need to contact the court directly to obtain the document and their servers are running slowly.
Give it another minute or two to complete, and then try the refresh button.
A few More Minutes ... Still Working
It can take up to 5 minutes for us to download a document if the court servers are running slowly.
Thank you for your continued patience.
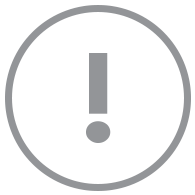
This document could not be displayed.
We could not find this document within its docket. Please go back to the docket page and check the link. If that does not work, go back to the docket and refresh it to pull the newest information.
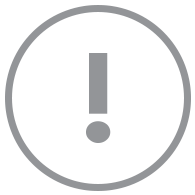
Your account does not support viewing this document.
You need a Paid Account to view this document. Click here to change your account type.
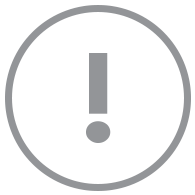
Your account does not support viewing this document.
Set your membership
status to view this document.
With a Docket Alarm membership, you'll
get a whole lot more, including:
- Up-to-date information for this case.
- Email alerts whenever there is an update.
- Full text search for other cases.
- Get email alerts whenever a new case matches your search.
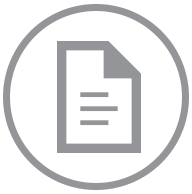
One Moment Please
The filing “” is large (MB) and is being downloaded.
Please refresh this page in a few minutes to see if the filing has been downloaded. The filing will also be emailed to you when the download completes.
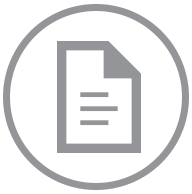
Your document is on its way!
If you do not receive the document in five minutes, contact support at support@docketalarm.com.
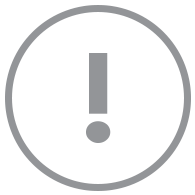
Sealed Document
We are unable to display this document, it may be under a court ordered seal.
If you have proper credentials to access the file, you may proceed directly to the court's system using your government issued username and password.
Access Government Site