`
`Office européen des brevets
`
`llllillllilliiilliilliiIlllllllllllllliiilllllilllllilllilllillliilll
`
`(11)
`
`EP 0 826 809 A1
`
`(12)
`
`EUROPEAN PATENT APPLICATION
`
`(43) Date of publication:
`04.03.1998 Bulletin 1998/10
`
`(51) int. CL5: D043 21/18
`
`(21) Application number: 97112691.?
`
`(22) Date of filing: 24.07.1997
`
`(84) Designated Contracting States:
`AT BE CH DE DK ES Fl FR GB GR iE IT LI LU MC
`NL PT SE
`Designated Extension States:
`AL LT LV no Si
`
`(30) Priority: 27.08.1996 IT UD960165
`
`(71) Applicant:
`Piave Industria Tessuti Elastici SpA
`32032 Feltre (BL) (lT)
`
`
`
`{72)
`
`Inventor: Antoniet'ti, Franco
`32032 Feltre (BL) (lT)
`
`(74) Representative:
`Petraz, Gilberto Luigi
`GLP S.r.l.
`
`Piazzale Cavedalis 6/2
`33100 Udine (ET)
`
`(54) Method to make etastic knitwear fabric and relative fabric
`
`,
`
`‘uu‘M.
`‘‘‘..:‘,
`
`
`
`Method to make elastic knitwear fabric from an
`(57)
`elastic or elastomeric thread (1 1a) and from at least one
`non elastic thread (1 lb). the method using a single-sec-
`tion run-proof knitting machine, or Raschel
`type
`machine, having a bar of needles (12) moving in alter-
`nation and at least a iciward bar and a rear bar of guide
`needles onto which the relative threads which have to
`
`be woven are threaded. the elastic thread (1la) being
`constituted by an elastic thread known commercially by
`the name of "Lycra", or material similar or comparable to
`it. with a count between 22 and 80 Dtex; the non elastic
`thread (11b) being constituted by a mutti—tilament nylon
`thread. or material similar or comparable to it, with a
`count of between 22 and 73 Dtex, where the ratio
`between the count expressed in Dtex and the filament
`count is the same or less than two; the weave of the non
`elastic thread (11b) having a basic pattern with a recur—
`rence equal to four rows (13) of the machine, in which at
`least three consecutive rows (13) work on separate nee-
`dles(12).
`fabric obtained by the method
`Elastic knitwear
`described above. using an elastic thread (11a) identifia-
`ble as "Lycra" with a count of 40 Dtex and a multi-fila-
`ment non elastic thread (11b) with a count of 44 Dtex
`and 28 filaments, with a maximum thickness of around
`0.54 mm and a minimum thickness of around 0.30 mm
`
`according to the type of basic weave used.
`
`EP0826809A1
`
`Printed by Xerox (UK) Business Servtoes
`21511534
`
`
`
`1
`
`EP0826 809 A1
`
`2
`
`Description
`
`This invention concerns a method to make elastic
`
`fabric for knitted goods, and also the fabric obtained by
`using the method, as set forth in the respective main
`claims.
`
`The invention, while using substantially traditional
`machines, makes it possible to obtain a product of very
`high quality in terms of modulus, elasticity, reduction in
`thickness, great permeability. a high level of transpira-
`tion and therefore a very low quotient of heat retained,
`and other qualities too.
`The invention also makes it possible to obtain a lab-
`ric with high non-run characteristics.
`The state of the art of knitted goods, for particular
`applications and particular products, covers the method
`of using an elastic thread, or elastomeric thread, inter-
`woven with a non elastic thread in order to obtain a lab—
`
`ric which has characteristics of elasticity, obtaining in
`any case a good feel quality which does not prejudice
`the contact effect with the skin of the wearer.
`
`Sometimes at least a third thread may be used in
`combination with the first two, usually of the non elastic
`type.
`in some cases, the fabric obtained from the knitting
`machine can be subjected to a process of teaseling fol-
`lowed by a process of shearing in order to improve the
`feel quality of the fabric.
`The knitting machines which make this kind of fab—
`ric normally have a movable bar of needles which
`moves in alternation, and at least two bars of guide nee-
`dies, that is, needles with a threading eye, defined as
`forward bar and rear bar, on each of which one of the
`threads which have to be woven is threaded.
`
`The bars of guide needles are movable in a way
`which is coordinated with the movement of the bar of
`
`needles to define the looping run of the thread around
`the needles themselves.
`
`ln traditional methods, it is preferred to put the elas-
`tic thread onto the rear bar, while the non elastic thread
`is put on the forward bar; however an inversion of this
`position of the threads is also found in the state of the
`art.
`
`The state oi the art also covers the fact that the non
`
`elastic component is woven to the elastic component
`with a slack length so that, when the fabric is removed
`from the machine, the elastic component contracts and
`consequently the slack lengths of the non elastic com-
`ponents are forced and are arranged as well as possible
`to be teaseled and sheared in such a way as to term a
`fabric which is characterised by a skin effect.
`ERIE-0.452.607 proposes to perform a simple
`inversion of the threading in the machine between the
`rear bar and the forward bar. that is the threading of the
`elastic thread in the forward bar and the threading of the
`non elastic thread in the rear bar. but this is obvious in
`itself, as the final effect obtained is specular.
`USA-2996906 describes a method to form a non-
`
`run fabric where both the threads, the elastic thread and
`the non-elastic thread, form the mesh in alternation, and
`not with every run of the machine.
`In this case the method obtains rows of mesh
`
`formed by elastic thread alternated with rows of mesh
`formed by non elastic thread, and therefore it does not
`provide a fabric wherein the elastic thread and the non
`elastic thread form the mesh at the same time on the
`same needle.
`USA-4044575 describes a method to form a fabric
`
`which does not have non<run properties. since only the
`non elastic thread forms the mesh whereas the elastic
`
`thread does not form the mesh, it is inserted as a sup-
`port or inlay.
`Moreover, the Atlas mesh binding is interrupted
`after three meshes and the total ratio is 6.
`
`EP—A-ot 19535 simply describes a method to form a
`fabric which to the technique of forming the mesh adds
`the insertion of a supplementary elastic thread in the
`direction of the well, thus giving extra elasticity in that
`direction.
`
`All these solutions, even if they are partially satis-
`factory, have shown characteristics which can still be
`improved on, at least in terms of elasticity and modulus
`of the final fabric thus obtained.
`
`is
`The present applicants have also found that it
`possible to obtain in the final fabric a reduced thickness
`even with the same qualities of elasticity and resistance.
`In order to improve the quality of a fabric obtained
`from an elastic component and a non elastic compo-
`nent, using substantially traditional knitting machines
`and threading methods, and to achieve further advan-
`tages, the present applicants have designed, tested and
`embodied this invention, which uses in a new combina-
`tion, which could never have been thought of before.
`basic components and specific weaves which were
`known to the state of the art.
`This invention is set forth and characterised in the
`
`10
`
`15
`
`20
`
`25
`
`30
`
`35
`
`4a
`
`respective main claims, while the dependent claims
`describe variants of the idea of the main embodiment.
`
`this invention is to achieve a
`The purpose of
`method to make a knitwear fabric which gives a final
`fabric of very high quality both manual and mechanical,
`of elasticity and resistence.
`A further purpose of the invention is to obtain a fab—
`ric which has a considerably reduced thickness com-
`pared with oonventional fabrics normally produced, with
`the same qualities of elasticity and resistance.
`A further purpose of the invention is to obtain a fab-
`ric with a high level of permeability and transpiration
`with a consequent very low quotient of heat retained
`which gives the fabric the characteristic of "cold" fabrics.
`A further purpose of the invention is to obtain a final
`fabric with high non-run characteristics.
`A further purpose of the invention is to obtain an
`elastic fabric particularly suitable, because of the above
`mentioned qualities, for underwear, corset articles and
`sportswear.
`
`55
`
`
`
`3
`
`EP 0 826 809 A1
`
`4
`
`The fabric according to the invention is obtained by
`weaving in the appropriate way a first thread with elastic
`or elastomeric characteristics with a second thread with
`non elastic characteristics.
`
`In one embodiment of the invention. the first elastic
`or elastomeric thread is constituted by a thread known
`commercially as "Lycra", or similar material, with a
`count of between 22 and 80 Dtex.
`The second thread with non elastic characteristics
`
`is constituted by a multi-filament nylon thread. or some
`comparable material, for example nylon 6. with a count
`of between 22 and 78 Dtex.
`
`According to a variant. the material which consti-
`tutes the filament is nylon 6.6.
`According to a further variant. the second thread
`with non elastic characteristics is made of polyester.
`According to the invention. the nylon thread is cho-
`sen with a number of filaments such that the ratio
`between the count emressed in Dtex and filaments is in
`any case less than 2. This principle defines the mini-
`mum number of filaments which must constitute a non
`
`elastic thread which can be adapted lor the invention.
`this minimum number being 11 in the case of thread
`with a count of 22 Dtex.
`
`The method according to the invention uses single
`section knitting machines of
`the non-run type. or
`Flaschel machines. substantially conventional with at
`least two bars of guide needles. one forward and one
`rear. cooperating with a bar of needles.
`The non—run guality of the fabric obtained with the
`method according to the invention is guaranteed.
`according to convention. by the fact that during weaving.
`the elastic thread and the non elastic thread work
`
`respectively in opposition.
`In this case, the thread with elastic characteristics is
`threaded on the rear bar of the machine. while the
`thread with non elastic characteristics is threaded on
`the tonrvard bar.
`
`All the guide needles of the bars. both forward and
`rear. are threaded with the relative thread. so that the
`machine presents a so-called full—bar threading.
`The weaves used to obtain the fabric according to
`the invention. starting from the threads as defined
`above, all have the common characteristic that the non
`elastic thread always recurs with every four machine
`rows.
`rows which constitute the weave
`In these four
`recurrence of the non elastic thread at least three con-
`secutive rows are made to work on three distinct nee-
`dlas.
`
`As the guide needle passes over the relative needle
`it may define. according to the case. an open mesh or a
`closed mesh.
`
`In all cases where the method according to the
`invention is applied. the thickness of the resulting fabric
`is in any case extremely reduced and variable according
`to the type of weave used.
`According to a variant a third thread is used, for
`
`example cotton. which is bound to the non elastic thread
`by the interposition of the elastic thread.
`The attached figures are given as a non-restrictive
`example and show some preferred embodiments of the
`invention as follows:-
`
`Fig.1
`
`Figta
`
`1'0
`
`Fig.2
`
`Fig.3
`
`15
`
`the
`
`shows the basic pattern of a first weave used
`in the method according to the invention;
`partially shows the development of
`weave in Fig.1;
`shows the basic pattern of a second weave
`used in the method according to the inven-
`tion;
`shows the basic pattern of a third weave
`used in the method according to the inven—
`tion.
`
`20
`
`25
`
`30
`
`35
`
`4o
`
`45
`
`55
`
`The reference number 10a in the attached figures
`denotes generally a basic length of mesh made by the
`rear bar of guide needles on which is threaded the elas-
`tic thread 1 1a. while the reference number 10b denotes
`generally the corresponding section of mesh made by
`the forward bar of guide needles on which is threaded
`the non elastic thread 11b.
`
`Each point 12 denotes the position of a needle of
`the bar with which the relative rear and forward bars of
`
`guide needles cooperate. while the spaces between the
`needles are denoted by the numbers underneath so as
`to define, according to convention. the run followed by
`the thread 11a. 11b guided by the guide needles
`between the needles 12.
`
`The number 13 denotes the lines which represent
`the various rows of the machine which are progressively
`covered by the weave made by the threads 11a and
`11b.
`
`in all three cases shown. the non elastic thread 11b
`always works in opposition to the elastic thread 11a.
`thus guaranteeing the non-run quality of the final fabric,
`Moreover.
`in all the cases shown. the non elastic
`thread 11b is looped with a recurrence of four rows 13
`of the machine.
`
`in the case of Fig. 1. the elastic thread 11a also
`recurs every four rows 13 of the machine. while in the
`case at Figs. 2 and 3 the elastic thread 11a recurs every
`two rows 13 of the machine.
`
`As can be seen from Figs. l. 2 and 3. inside the four
`rows 13 of the recurrence. the non elastic thread 11b is
`looped. for at least three consecutive rows 13. on dis-
`tinct needles 12.
`
`This type of weave causes the basic patterns
`shown in Figs.
`1 and 2 to be reproduced continuously.
`moving the non elastic thread 11b sideways from time to
`time by one needle 12. whereas in Fig. 3 the movement
`takes place for two consecutive rows on two needles
`and for the other two rows of the period on one needle.
`ln the weave shown in Fig.1 it can be seen how the
`two threads. the elastic 11a and the non elastic 11b. are
`moved on the respective bars of guide needles in a
`
`
`
`5
`
`EP0826 809 A1
`
`6
`
`specular way to each other.
`ln particular. the elastic thread ‘1 is threaded on the
`rear bar follows a run denoted by the notation 2-3. (in
`this pass a closed mesh around the relative needle 12 is
`achieved). 2-1 (an open mesh is achieved). 1-0 (a
`closed mesh is achieved) and 1-2 (an open mesh is
`achieved)
`in the same way. for the non elastic thread 11b
`threaded on the forward bar. the run. specular to the
`previous one. can be identified by the notation 1-0, 1-2.
`2—3. 2-1.
`With this type of weave the thread foilows a run in
`which with every successive row 13 the thread passes
`onto a distinct needle 12. moved sideways and adjacent
`to the preceeding one.
`Fig.1a shows a partial development of the basic
`pattern of Fig.1 in which several elastic threads 11a are:
`shown. while only one non elastic thrwd 11b is shown
`so as not to overload the drawing.
`This type of weave. together with the appropriate
`choice of the basic component materials. gives a con-
`siderable reduction in the thickness so as to obtain a
`
`thickness of the finished fabric in the region of 0.34 mm,
`using an elastic thread 1 1a made of "Lycra" with a count
`of 40 Dtex and a non elastic thread 11b made of nylon
`with a count of 44 Dtex and a number offilaments equal
`to 28.
`
`According to another embodiment. the non elastic
`thread 1 1b is made 01 polyester.
`in the weaves shown in Figs. 2 and 3. the elastic
`thread 11a is threaded on the rear bar according to a
`crossing run with a recurrence of two rows 13. identifia-
`ble by the notation 1-0. 1-2.
`Around the relative needles 12 closed meshes are
`achieved.
`For the non elastic thread 11b threaded on the for-
`
`ward bar, Fig.2 shows a basic pattern of weave which
`substantially reproduces in a specular way the weave of
`the non elastic thread 11b shown in Fig.1.
`In this case
`too there is a sequential run with a recurrence of tour
`machine rows 13. in which every consecutive row 13 is
`associated with a distinct needle 12. moved sideways
`and adjacent to the proceeding one.
`in correspondence with the pass 2-3 and the pass
`1-0 a closed mesh is achieved. whereas in corresponds
`ence with the pass 2-1 and 1-2 an open mesh is
`achieved.
`
`With this basic weave it is possible to obtain a final
`fabric with a thickness in the region of 0.43 mm using an
`elastic thread 11a made at "Lycra” with a count of 40
`Dtex and a non elastic nylon thread 11b with a count of
`44 Dtex and a number of filaments equal to 28.
`The weave in Fig.3 is different from the proceeding
`ones in that in passing trom the first to the second row
`13 and from the second to the third row 13 one needle
`
`12 is jumped. whereas in passing from the third to the
`fourth row 13 and from the fourth to the first row 13 of
`
`is looped onto the needle 12 immediately adjacent.
`With
`this weave closed meshes are always
`obtained around the respective needles 12, and thus a
`final fabric is obtained with a thickness of about 0.54
`
`mm using an elastic thread 11a made of "Lycra" with a
`count of 40 Dtex and a non elastic thread 111: made of
`
`nylon with a count 01 44 Dtex and a number of filaments
`equal to 28.
`
`10
`
`Claims
`
`1. Method to make elastic knitwear fabric starting from
`an elastic or elastomeric thread (11a) and at least
`one non elastic thread {1 1b). the method using a
`single-section.
`non-run
`knitting machine.
`or
`Fiaschel type machine. with a bar 01‘ needles (12)
`moving in alternation and at least one forward bar
`and one rear bar oi guide needles on which the rel-
`ative threads to be woven are threaded. the method
`being characterised in that:
`
`-
`
`-
`
`-
`
`the elastic thread (11a) is constituted by an
`elastic thread known commercially as "Lycra".
`or in similar or comparable material. with a
`count of between 22 and 80 Dtex;
`the non elastic thread (11b) is constituted by a
`multi filament thread made of nylon or other
`similar or comparable material. with a count of
`between 22 and 78 Dtex. where the ratio
`between the count expressed in Dtex and the
`number of the filaments is equal to or less than
`two:
`
`the weave of the non elastic thread (11b) has a
`basic pattern with a recurrence of tour machine
`rows (13), in which at least three consecutive
`rows (13) work on distinct needles (12).
`
`in which the non elastic
`2. Method as in Claim 1.
`thread (1 1b) is made of polyester.
`
`in which the elastic
`3. Method as in Claim 1 or 2.
`thread (11a) identifiable as "Lycra" has a count of
`4D Dtex.
`
`4. Method as in Claim 1 or 2. in which the non elastic
`multi-tilament thread (11b) made of nylon or of pol-
`yester has a count of 44 Dtex and a number of tile—
`merits equal to 28.
`
`51 Method as in Claim 1 or 2. in which the non elastic
`rmlti-tilament thread (11b) made of nylon or of pol-
`yester has a count of 44 Dtex and a number of file-
`ments equal to 36.
`
`6. Method as in any claim hereinbetore. in which the
`non elastic thread (11b) is made of type 6 nylon.
`
`15
`
`20
`
`25
`
`30
`
`35
`
`4a
`
`55
`
`the following period no needle 12 is jumped. the thread
`
`7. Method as in any claim from 1
`
`to 5 inclusive,
`
`in
`
`
`
`7
`
`EP 0 826 809 A1
`
`8
`
`17.
`
`18.
`
`19.
`
`20.
`
`Method as in Claim 16, in which in all the passes of
`the basic pattern the thread (11b) achieves a
`closed mesh around the relative needle (12).
`
`Method as in Claims 12 or 15, in which the basic
`pattern of weave of the elastic thread (He) has a
`recurrence of two rows (13) on two adjacent nee—
`dies (12) identifiable with the conventional notation
`1-0. 12.
`
`Method as in Claims 12 or 15, in which the basic
`pattern of weave of the elastic thread (He) has a
`recurrence equal to four rows (13) with the conven-
`tional notation 2-3, 2-1. ‘t-O, 1-2.
`
`Etastic fabric for knitwear obtained by means of the
`method of any claim hereinbetore. characterised in
`that by using an elastic thread (1 ta) identifiable as
`"Lycra" with a count of 40 Dtex and a non elastic
`multi-tilament thread (1 tb) with a count of 44 Dtex
`and 28 titaments, the elastic fabric for knitwear has
`a maximum thickness in the region of 0.54 mm and
`a minimum thickness in the region of 0.30 mm
`according to the type of basic weave used.
`
`which the non elastic thread (1 to) is made of type
`6.6 nylon.
`
`Method as in any claim hereinbefore, in which the
`weave of the non elastic thread (1 tb) has a basic
`pattern in which for every successive row (13) the
`thread (11b) in its run works with a needle (12)
`moved sideways and immediately adjacent to the
`preceeding needle (12).
`
`in
`to 7 inclusive,
`Method as in any claim from 1
`which the weave of the non elastic thread (11b) has
`a basic pattern in which for every successive row
`(13) the thread (the) is moved in its run for two con-
`secutive rows (13) on two needles (12) and for the
`other two rows (13) of the period on one needle
`(12).
`
`Method as in Claims 8 or 9, in which the weave of
`the non elastic thread (11b) is identifiabte with the
`conventional notation 1—0. 1-2, 2-3. 2—1 (Fig.1).
`
`in which in the passes 1—0
`Method as in Claim 10,
`and 2-3 the non elastic thread (11b) achieves a
`closed mesh around the relative needle (12),
`whereas in the passes 1-2 and 2-1 the non elastic
`thread (11b) achieves an open mesh around the
`relative needle (12).
`
`Method as in Claims 8 or 9, in which the weave of
`the non elastic thread (11b) is identifiable with the
`conventional notation 2-3, 2-1. 1-0, 1-2 (Fig. 2).
`
`in which in the passes 2-3
`Method as in Claim 12.
`and 1—0 the non elastic thread (11b) achieves a
`closed mesh around the relative needle (12).
`whereas in the passes 2-1 and 1-2 the non elastic
`thread (11b) achieves an open mesh around the
`relative needle (12).
`
`Method as in Claims 8 or 9, in which the basic pat-
`tern ot weave of the elastic thread (1 1a) is specular
`with that of the non elastic thread (11b).
`
`in
`to 7 inclusive,
`Method as in any claim from 1
`which the weave of the non elastic thread (11b) has
`a basic pattern in which for every pass from the first
`to the second row (13) and from the second to the
`third row(13) the thread (1 1b) in its run moves side-
`ways jumoing at least an intermediate needle (12).
`whereas in the pass from the third to the fourth row
`(13) and from the fourth to the first row (13) of the
`next period the thread (11b) moves sideways from
`one needle (12) to the adjacent one.
`
`10.
`
`11.
`
`12.
`
`13.
`
`14.
`
`15.
`
`16.
`
`Method as in Claim 15, in which the weave of the
`non elastic thread (11b) is identifiable with the con—
`ventional notation 2-3, 1-0. 2-3, 2-1 (Fig.3).
`
`1'0
`
`15
`
`20
`
`25
`
`30
`
`35
`
`4o
`
`45
`
`55
`
`
`
`EP 0 826 809 A1
`
`«first.
`
`NF
`/.
`
`m,
`
`2.9
`
`gig
`
`“ggfimx
`
`lfimfi)‘
`lflnfivmvmwiii
`
`n.5,:\..EW\_.
`Bir,n...r..{a
`a...vm;
`
`
`
`
`EP 0 826 809 A1
`
`
`
`
`
`EP 0 826 809 A1
`
`0’) EuropeanPatent
`
`Office
`
`EUROPEAN SEARCH REPORT
`
`ApplicationNumber
`
`EP 97 11 2691
`
`
`
`
`Calegory
`
`
`CLASSIFICATION OF THE
`Relevant
`C:iralion cf domlmem with inclrcalion. where aprjmpriate.
`
`
`to claim
`APPLICATION (Int.Cl.6)
`r
`of relevant nassa
`
`
`
`§004821/18
`
`US 2 996 906 A (ICHIBE)
`* column 1,
`line 21 ~ column 2,
`figure 1 *
`
`line 40;
`
`
`
`US 4 044 575 A (KRUG)
`
`E? 0 119 535 A (BAYER AG)
`
`E? 0 452 607 A (EUROJERSEY S.P.A.)
`
`TECHNICAL FIELDS
`
`llnLClj)
`SEARCHED
`
`
`
` Place at search
`
`The aresanl search report has been drawn up for all claims
`Dale al complelloncl flue search
`Examiner
`
`THE HAGUE
`CATEGORY OF Cl TED DOCUMENTS
`
`X '. particularly ralevanl 'rl taken alone
`Y I particularly relevant 'rl combined wllh another
`document or the Slam-5 category
`A : rschnological background
`O : non—written drsclasura
`P : Intermedlate dccumenl
`
`
`
`EPOFORM150803.82117’04601I
`
`Van Gelder‘, P
`19 December 1997
`T theory erpnncipla under-fling the Invention
`E : earlier parent document, but punlishea on; ur
`after the filing dam
`D ‘ documenl cirad in the application
`l. : document cited for ulnar reasons
`3. : mamfier ol the same palent lamityfi corresponding
`documen:
`
`
`
`
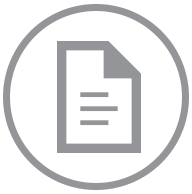
Accessing this document will incur an additional charge of $.
After purchase, you can access this document again without charge.
Accept $ ChargeStill Working On It
This document is taking longer than usual to download. This can happen if we need to contact the court directly to obtain the document and their servers are running slowly.
Give it another minute or two to complete, and then try the refresh button.
A few More Minutes ... Still Working
It can take up to 5 minutes for us to download a document if the court servers are running slowly.
Thank you for your continued patience.
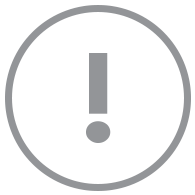
This document could not be displayed.
We could not find this document within its docket. Please go back to the docket page and check the link. If that does not work, go back to the docket and refresh it to pull the newest information.
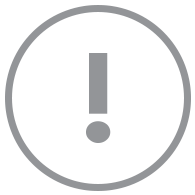
Your account does not support viewing this document.
You need a Paid Account to view this document. Click here to change your account type.
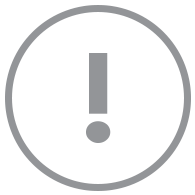
Your account does not support viewing this document.
Set your membership
status to view this document.
With a Docket Alarm membership, you'll
get a whole lot more, including:
- Up-to-date information for this case.
- Email alerts whenever there is an update.
- Full text search for other cases.
- Get email alerts whenever a new case matches your search.
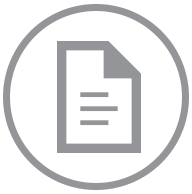
One Moment Please
The filing “” is large (MB) and is being downloaded.
Please refresh this page in a few minutes to see if the filing has been downloaded. The filing will also be emailed to you when the download completes.
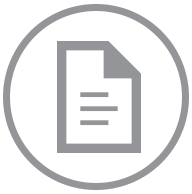
Your document is on its way!
If you do not receive the document in five minutes, contact support at support@docketalarm.com.
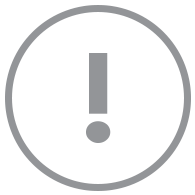
Sealed Document
We are unable to display this document, it may be under a court ordered seal.
If you have proper credentials to access the file, you may proceed directly to the court's system using your government issued username and password.
Access Government Site