`(19) World Intellectual Property
`Organization
`International Bureau
`
`(43) International Publication Date
`3 November 2016 (03.11.2016)
`
`WIPOI PCT
`
`\9
`
`(10) International Publication Number
`
`WO 2016/175738 A1
`
`(51)
`
`International Patent Classification:
`C09D 11/00 (2014.01)
`
`(21)
`
`International Application Number:
`
`PCT/US201 5/027743
`
`(22)
`
`International Filing Date:
`
`(25)
`
`(26)
`
`(71)
`
`(72)
`
`(74)
`
`(81)
`
`Filing Language:
`
`Publication Language:
`
`27 April 2015 (27.04.2015)
`
`English
`
`English
`
`Applicant: HEWLETT-PACKARD DEVELOPMENT
`COMPANY, LP. [US/US]; 11445 Compaq Center Drive
`W., Houston, Texas 77070 (US).
`
`Inventors: KASPERCHIK, Vladek; 1070 NE Circle
`Blvd., Corvallis, Oregon 97330-4239 (US). BUTLER,
`Thomas W.; 1070 NE Circle B1vd., Corvallis, Oregon
`97330—4239 (US). BRUINSMA, Paul Joseph; 16399 W.
`Bernardo Dr., San Diego, California 92127-1899 (US).
`
`Agents: FOUGERE, Jeffrey R. et al.; Hewlett-Packard
`Company, Intellectual Property Administration, 3404 E.
`Harmony Rd, Mail Stop 35, Fort Collins, Colorado 80528
`(US).
`
`Designated States (unless otherwise indicated, for every
`kind ofnational protection available): AE, AG, AL, AM,
`AO, AT, AU, AZ, BA, BB, BG, BH, BN, BR, BW, BY,
`
`BZ, CA, CH, CL, CN, CO, CR, CU, CZ, DE, DK, DM,
`DO, DZ, EC, EE, EG, ES, FI, GB, GD, GE, G11, GM, GT,
`HN, HR, HU, ID, IL, IN, 1R, IS, JP, KE, KG, KN, KP, KR,
`KZ, LA, LC, LK, LR, LS, LU, LY, MA, MD, ME, MG,
`MK, MN, MW, Mx, MY, MZ, NA, NG, N1, NO, NZ, OM,
`PA, PE, PG, PH, PL, PT, QA, Ro, RS, RU, RW, SA, SC,
`SD, SE, SG, SK, SL, SM, ST, sv, SY, TH, TJ, TM, TN,
`TR, TT, TZ, UA, UG, US, UZ, VC, VN, ZA, ZM, ZW.
`
`(84) Designated States (unless otherwise indicated, for every
`kind of regional protection available): ARIPO (BW, GH,
`GM, KE, LR, LS, MW, MZ, NA, RW, SD, SL, ST, SZ,
`TZ, UG, ZM, ZW), Eurasian (AM, AZ, BY, KG, KZ, RU,
`TJ, TM), European (AL, AT, BE, BG, CH, CY, CZ, DE,
`DK, EE, ES, FI, FR, GB, GR, HR, HU, IE, IS, IT, LT, LU,
`LV, MC, MK, MT, NL, NO, PL, PT, RO, RS, SE, SI, SK,
`SM, TR), OAPI (BF, BJ, CF, CG, CI, CM, GA, GN, GQ,
`GW, KM, ML, MR, NE, SN, TD, TG).
`Declarations under Rule 4.17:
`
`as to the identity ofthe inventor (Rule 4.1 7(i))
`
`as to applicant’s entitlement to applyfor and be granted a
`patent (Rule 4.1 7(ii))
`Published:
`
`with international search report (Art. 21(3))
`
`(54)
`
`Title: WHITE INKS
`
`
`
`(57) Abstract: The present disclosure provides a White ink including an aqueous ink vehicle, from 5 Wt% to 50 Wt% of a white metal
`oxide pigment having an average particulate size from 100 nm to 2,000 nm, from 0.1 wt% to 4 wt% of anionic oxide particulates
`having an average particulate size from 1 nm to 100 nm, from 2 Wt% to 30 Wt% of latex particulates having a glass transition temper—
`ature from 0 C to 130 C, and a non-ionic or predominantly non-ionic dispersant having an acid number not higher than 100mg
`KOH/g based on dry polymer weight. The White metal oxide pigment and anionic oxide particulates are present in the white ink at a
`weight ratio from 5:1 to 200: l.
`
`
`
`W02016/175738A1|||||||||||||||||||||||||||||||||||||||||||||||||||||||||||||||||||||||||||||||||||||||||||||||
`
`
`
`WO 2016/175738
`
`PCT/U82015/027743
`
`WHITE INKS
`
`BACKGROUND
`
`[0001]The use of ink—jet printing systems has grown dramatically in recent
`
`years. This growth may be attributed to substantial improvements in print
`
`resolution and overall print quality coupled with appreciable reduction in cost.
`
`Today's ink-jet printers offer acceptable print quality for many commercial,
`
`business, and household applications at lower costs than comparable products
`
`available just a few years ago. Notwithstanding their recent success, research
`
`and development efforts continue toward improving ink-jet print quality over a
`
`wide variety of different applications.
`
`[0002]An ink-jet image is formed when a precise pattern of dots is ejected
`
`from a drop-generating device known as a "printhead" onto a printing medium.
`
`Inks normally used in ink—jet recording are sometimes composed of water—soluble
`
`organic solvents, surfactants, and colorants in a predominantly aqueous fluid.
`
`Regarding the use of colorants, certain pigments can be more challenging than
`
`other in achieving certain desirable properties. For example, ink opacity,
`
`durability, and uniformity can be a challenge in certain circumstances.
`
`BRIEF DESCRIPTION OF THE DRAWINGS
`
`1O
`
`15
`
`20
`
`25
`
`[0003]Additional features and advantages of the disclosure will be
`
`apparent from the detailed description which follows, taken in conjunction with the
`
`accompanying drawings, which together illustrate, by way of example, features of
`
`30
`
`the technology; and, wherein:
`
`[0004] FIG. 1 depicts examples where a cationic polymer is digitally printed
`
`on a media substrate contemporaneously orjust before printing a white inkjet ink
`
`1
`
`
`
`WO 2016/175738
`
`PCT/U82015/027743
`
`thereon, and wherein the white inkjet ink is prepared in accordance with
`
`examples of the present disclosure;
`
`[0005] FIG. 2 depicts examples where a cationic polymer is applied to a
`
`media substrate prior to (either digital or by analog application) printing a white
`
`inkjet ink thereon, and wherein the white inkjet ink is prepared in accordance with
`
`examples of the present disclosure;
`
`[0006]F|G. 3 depicts examples of heat fusing an image printed as
`
`described in FIGS. 1 or 2 in accordance with examples of the present disclosure;
`
`[0007]F|G. 4 depicts a printed article, such as that shown in FIG. 3, after
`
`1O
`
`heat fusing on the media substrate;
`
`[0008]F|G. 5 is an image of a vertical drip test conducted using a Control
`
`lnk;and
`
`[0009]F|G. 6 is an image of a vertical drip test conducted using an ink
`
`prepared in accordance with examples of the present disclosure.
`
`[0010] Reference will now be made to the exemplary embodiments
`
`illustrated, and specific language will be used herein to describe the same. It will
`
`nevertheless be understood that no limitation of the scope of the disclosure is
`
`thereby intended.
`
`DETAILED DESCRIPTION
`
`[0011]The present disclosure is drawn to white inks, namely water-based
`
`white inkjet inks that can be jetted from various types of inkjet printheads, but are
`
`particularly friendly for use in thermal inkjet printheads. These inks, in some
`
`instances with the assistance of a fixer coating layer or fixer ink, can be printed
`
`not only on porous media, but also effectively on more challenging non-porous
`
`polymer media.
`
`[0012] In accordance with this, it has been realized that inks white metal
`
`oxide pigments (e.g., zinc oxide, titanium dioxide such as rutile or anatase,
`
`zirconium oxide, etc.) can be dispersed and effectivelyjetted from thermal inkjet
`
`printheads with non-ionic or predominantly non-ionic dispersants. Unfortunately,
`
`these inks also tend to produce coating of non-uniform thickness when dried on
`
`2
`
`15
`
`20
`
`25
`
`30
`
`
`
`WO 2016/175738
`
`PCT/U82015/027743
`
`non-porous substrates, which ultimately leads to poor quality prints. This problem
`
`can be solved by adding a relatively small amount (around 1-2 orders of
`
`magnitude less than the weight percentage of the white metal oxide pigment) of
`
`anionic oxide particulates (e.g., precipitated silica dispersion, fumed silica
`
`dispersion, anionically charged alumina-silicate particles dispersion, etc.). This, in
`
`combination with latex for added durability, and typically, fixer applied to the
`
`media substrate to temporarily fix the ink prior to heat fusion, can provide high
`
`print quality and highly durable prints can be generated on smooth polymer
`
`substrates. More specifically, the anionic oxide particulates of the white ink can
`
`act to cross-link with cationic polymer (e.g., usually delivered with a digitally
`
`printable or analog application fixer fluid) located at the surface of the media
`
`substrate. This interaction temporarily freezes the white metal oxide pigment on
`
`the print surface and prevents pigment shifting and print quality degradation
`
`during drying. Then, in some examples, the latex can be fused with the ink to
`
`provide durability to the printed image. Thus, by generating a more uniform print
`
`layer (avoiding the Marangoni effect and severe coalescence), uniform and
`
`adequate ink thickness can lend itself to greater uniformity and efficient opacity of
`
`the printed image. Additionally, non-ionic stabilization of the white metal oxide
`
`pigment provides for prevention of the formation of stable aggregates
`
`(coagulation) during ink drying. Printing a relatively thick ink layer on non-porous
`
`media surface in absence of strong cohesive forces between pigment particles
`
`can lead to uncontrolled ink spread outside printed area boundaries and poor
`
`edge definition. This can be avoided using the inks of the present disclosure. On
`
`another note, in some examples, color gamut can be improved if this white ink is
`
`used as part of a colored ink set, because these inks can also provide a method
`
`of generating an on-demand white background for colored, black, or off-white
`
`substrates.
`
`[0013] In accordance with examples of the present disclosure, the white
`
`ink formulations of the present disclosure can include an aqueous ink vehicle,
`
`latex particulates, and two separate and distinct types of oxide particulates. For
`
`example, the ink can include from 5 wt% to 50 wt% (or from 10 wt% to 35 wt%) of
`
`a white metal oxide pigment having an average particulate size from 100 nm to
`
`3
`
`10
`
`15
`
`20
`
`25
`
`30
`
`
`
`WO 2016/175738
`
`PCT/USZOlS/027743
`
`2000 nm. The ink can also include from 0.1 wt% to 4 wt% of anionic oxide
`
`particulates having an average particulate size from 1 nm to 100 nm. The white
`
`metal oxide pigment and anionic oxide particulates can be present in the white
`
`ink at a weight ratio from 5:1 to 200:1. As also mentioned, the white ink can also
`
`include from 2 wt% to 30 wt% of latex particulates having a glass transition
`
`temperature from 0 °C to 130°C. The ink can also included a non-ionic or
`
`predominantly non-ionic dispersant to disperse the pigment and other
`
`particulates. The non—ionic or predominantly non—ionic dispersant can be defined
`
`by having non—ionic to weak anionic character having an acid number, per dry
`
`polymer, of not higher than 100mg KOH/g, or not higher than 50mg KOH/g, or in
`
`some examples, not higher than 30mg KOH/g. The dispersant can likewise be
`
`non-ionic without an appreciable acid number.
`
`[0014] In another example, a method of making a white ink can include
`
`steps of milling a white metal oxide pigment in a water—based carrier (which can
`
`be a thick slurry or a thinner composition) with a non-ionic or predominantly non-
`
`ionic dispersing agent (i.e. predominantly non-ionic/weak anionic character
`
`having an acid number, per dry polymer, of not higher than 100mg KOH/g, or not
`
`higher than 50mg KOH/g, or in some examples, not higher than 30mg KOH/g) to
`
`form a white metal oxide pigment dispersion; and admixing water, organic co—
`
`solvent, anionic oxide particulates, and latex particulates with the white metal
`
`oxide pigment dispersion to form a white ink. The white ink can have a white
`
`metal oxide pigment to anionic oxide particulate weight ratio from 5:1 to 200:1.
`
`[0015] In another example, a white thermal inkjet ink can include an
`
`aqueous ink vehicle, Ti02 pigment, and anionic oxide particulates. The Ti02
`
`pigment can be present in the white thermal inkjet ink at from 10 wt% to 35 wt%,
`
`and can have an average particulate size from 150 nm to 500 nm. The TiOz
`
`pigment can be dispersed with a non-ionic or predominantly non-ionic dispersant
`
`having an acid number not higher than 30 mg KOH/g based on dry polymer
`
`weight. The anionic oxide particulates can be present in the white thermal inkjet
`
`ink at from 0.1 wt% to 4 wt%, and can have an average particulate size from 1
`
`nm to 50 nm. The white metal oxide pigment and anionic oxide particulates can
`
`be present in the white thermal inkjet ink at weight ratio from 5:1 to 200:1.
`
`4
`
`1O
`
`15
`
`20
`
`25
`
`30
`
`
`
`WO 2016/175738
`
`PCT/USZOlS/027743
`
`[0016]These white inks can be used in forming white images on various
`
`media substrate, including smooth polymer (non-porous) media substrate, and
`
`can be printed in combination with a fixer coated on the surface of the media. For
`
`example, a fixer with cationic polymer can be applied to the media substrate and
`
`can be formulated so that its cationic polymer interacts with the anionic oxide
`
`particulates to immobilize the white metal oxide pigment.
`
`[0017] In each of these examples, there are several advantages related to
`
`the inclusion of the anionic oxide particulates along with a more dominant
`
`concentration of the white metal oxide pigment. The addition of anionic oxide
`
`particulates provides a relatively strong to very strong electrostatic interaction
`
`with cationic polymer that may be present on the media substrate, or as part of a
`
`fixer fluid to be printed (digitally) or otherwise applied (analog application) on a
`
`media substrate. The negative charge, small size, and relative large number of
`
`these anionic oxide particulates provide a way of fixing relatively thick ink layer on
`
`a smooth polymer surface for drying and/or subsequent heat fusing. For example,
`
`these particulates have an opposite charge relative to that of the cationic polymer
`
`present in a fixer coating or fixer fluid applied to the media substrate. Thus, these
`
`inks can provide electrostatic cross-linking sites for cationic polymer molecules.
`
`Mixing of white ink containing these particulates with cationic fixer or a fixer
`
`coating can very quickly create a cross-linked network, trapping larger non-
`
`ionically—stabilized Ti02 pigment (or other white metal oxide pigment).
`
`[0018]F|G. 1 depicts an example where a digitally printed fixer is applied
`
`just prior to or essentially simultaneously with an inkjet ink of the present
`
`disclosure. FIG. 2 depicts an example where a fixer is applied to a media
`
`substrate prior to application of an inkjet ink. The fixer in this latter example can
`
`likewise be applied by digital printing, or alternatively, by analog application, e.g.,
`
`roller, curtain coating, blade coating, Meyer rod coating, or any other coating
`
`methodology suitable for producing thin layer of fixer on the printed substrate,
`
`etc. As shown in FIGS. 1 and 2, an inkjet printing device 30 is adapted to digitally
`
`print a white inkjet ink 10, and in some examples, a fixer composition 20, on a
`
`media substrate 40. The media substrate can be a smooth, non-porous polymer
`
`substrate that is othenNise difficult to print on with high image quality and high
`
`5
`
`1O
`
`15
`
`20
`
`25
`
`30
`
`
`
`WO 2016/175738
`
`PCT/USZOlS/027743
`
`durability. Specifically, FIG.
`
`1 shows the fixer composition being printed digitally
`
`from the printing device, and FIG. 2 shows the fixer composition being pre-
`
`applied to the media substrate, either digitally or by an analog coating method. In
`
`both examples, the white inkjet ink includes white metal oxide pigment 12,
`
`anionic oxide particulates 14, latex particulates 16, and an ink vehicle 18 which
`
`typically includes a non-ionic dispersant or dispersing agent. Water, organic
`
`solvent, and/or other ingredients can likewise be present in the ink vehicle. The
`
`fixer composition can include cationic polymer 22 that is interactive with the
`
`anionic oxide particles of the white ink, thereby providing some immobilization or
`
`freezing of the pigment and particles on the print media substrate.
`
`[0019] In another example, the image printed or otherwise generated in
`
`accordance with FIGS. 1 and 2 can be heat fused. More specifically, FIG. 3
`
`shows a heat fusing device 50 which is used to apply heat 52 to the printed
`
`article to form a heat fused printed article as shown in FIG. 4. Because of the
`
`presence of both the white metal oxide pigment 12 and the latex particulates
`
`16,16b appropriately spaced, there can be enhanced light scattering 60 and
`
`lower transmittance 62 than even more densely packed white metal oxide
`
`pigment, which thus provides enhanced opacity. This increased opacity can be
`
`achieved by optically spacing the white metal oxide pigment from one another.
`
`For example, drying of the inks without latex particulates such that all of the high
`
`refractive index particulates are in close contact leads to formation of a densely
`
`packed layer of the white metal oxide pigment, which reduces their light
`
`scattering ability and overall opacity. On the other hand, using the fusible latex
`
`particulates as shown, and typically applying heat to fuse the latex particulates,
`
`the low refractive index optical spacing can boost the opacity of the printed
`
`coating by from 0.1% to 25%, or more typically from 5% to 20% or from 5% to
`
`25%. In other words, the crowding effect of tightly-packed high refractive index
`
`(n) particulates with little or no voids decreases light scattering and increase
`
`transparency of the coating. By optically spacing the white metal oxide pigment
`
`with the low refractive index latex particulates (and typically heat fused after
`
`printing) an increase in opacity can be realized. As a further point, fusion can add
`
`enhanced durability to the printed article. In some cases the fusing of the latex
`
`6
`
`1O
`
`15
`
`2O
`
`25
`
`30
`
`
`
`WO 2016/175738
`
`PCT/USZOlS/027743
`
`particulates may help the latex polymer distribute more evenly between light
`
`scattering white metal oxide pigment and, hence, further improve opacity as well.
`
`[0020] In accordance with this, a printed article can include up to 75, or up
`
`to 50 gsm, of total fluids (white ink + fixer) applied to a media substrate. The term
`
`"up to 75 gsm" or "up to 100 gsm" is used because typical inkjet images include
`
`fully imaged areas as well as non-imaged and/or lower density areas. After water
`
`and solvent(s) evaporation and fusing, the gsm roughly translates into 15-50 wt%
`
`of the initial fluid dispersion flux density, i.e. thus less than 50 gsm. In one
`
`example, full density inked area may be at from 30 to 50 gsm ink/fixer film, but
`
`densities lower in the tone ramp will be lower than this, thus the use of the phrase
`
`“up to” 75 gsm or "up to" 50 gsm. That being stated, though some areas on a
`
`media substrate might be at 0 gsm under this definition (unprinted areas), there
`
`will be areas that are imaged that range from greater than 0 gsm up to 50 gsm
`
`(after drying or heat fusing). In a typical printed article, there is a portion of the
`
`media that can be printed at from 5 gsm to 50 gsm.
`
`[0021]Turning now to the various specific ingredients that are present in
`
`the white ink, there can be a white metal oxide pigment. The “white” pigment
`
`provides much of the white coloration to the ink, though without the other
`
`ingredients in the ink, the pigment may have some transparency or translucency.
`
`Examples of white metal oxide pigments that can be used include titanium
`
`dioxide particulates, zinc oxide particulates, zirconium oxide particulates,
`
`combinations thereof, or the like. Pigments with high light scatter capabilities,
`
`such as these, can be selected to enhance light scattering and lower
`
`transmittance, thus increasing opacity. White metal oxide pigments can have a
`
`particulate size from about 100 nm to about 2000 nm, and more typically, from
`
`about 125 nm to 700 nm, and in still another example, from about 150 nm to 500
`
`nm. The combination of these pigments within these size ranges, appropriately
`
`spaced from one another with ingredients such as latex, full opacity can be
`
`achieved at relatively thin thickness, e.g., 5 gsm to 50 gsm after removal of water
`
`and other solvent(s) from the printed ink and fixer film.
`
`[0022]The white metal oxide pigment, among other solids that may be
`
`present, can be dispersed using a non-ionic dispersing agent. Suitable non-ionic
`
`7
`
`10
`
`15
`
`20
`
`25
`
`30
`
`
`
`WO 2016/175738
`
`PCT/USZOlS/027743
`
`dispersing agents can allow for suitable dispersibility and stability in an aqueous
`
`ink environment, while having little to no impact on the viscosity of the liquid
`
`phase of the ink as well as retaining good printhead reliability in thermal inkjet
`
`printheads. Dispersants meeting these parameters are typically non-ionic or
`
`predominantly non-ionic (only weakly anionic) in character. For definitional
`
`purposes, these dispersants are referred to as non-ionic dispersants, provided
`
`they are non-ionic or predominantly non-ionic in nature, i.e. the acid number of
`
`the predominantly non—ionic/weak anionic dispersant, per dry polymer, is not
`
`higher than 100mg KOH/g, and is typically less than 50mg KOH/g, most typically
`
`less than 30mg KOH/g. That being state, in one example, non-ionic dispersing
`
`agent with no anionic properties can be used one example.
`
`[0023] Examples of non-ionic dispersants that are included in this definition
`
`are water-hydrolysable silane coupling agents (SCAs) with relatively short
`
`(oligomer length range of not longer than 50 units, not longer than 30 units, or not
`
`longer than 15 units, e.g., 10 to 15 units) polyether chain(s), which are also
`
`soluble in water. An example of such a dispersant includes Silquest® A1230
`
`polyethylene glycol methoxysilane available from Momentive Performance
`
`Materials. Other examples include soluble low-to-midrange M (e.g., usually
`
`molecular mass of the polymer less than 15,000 Da) branched co—polymers of
`
`comb-type structures with polyether pendant chains and acidic anchor groups
`
`attached to the backbone, such as Disperbyk®-190 and Disperbyk®-199
`
`available from BYK Chemie, as well as Dispersogen® PCE available from
`
`Clariant.
`
`[0024] In further detail regarding the dispersants that can be used, in one
`
`example, reactive hydrophilic alkoxysilane dispersants that can be present, and
`
`examples include, but are not limited to, hydrolysable alkoxysilanes with alkoxy
`
`group attached to water-soluble (hydrophilic) moieties, such as water-soluble
`
`polyether oligomer chains, phosphate groups, or carboxylic groups. In some
`
`examples, the dispersant used to disperse white metal oxide pigment can be a
`
`polyether alkoxysilane or polyether phosphate dispersant. Upon dissolution in
`
`water with the white metal oxide pigment, the alkoxysilane group of the
`
`dispersant often hydrolysis resulting in formation of silanol group. The silanol
`
`8
`
`1O
`
`15
`
`20
`
`25
`
`30
`
`
`
`WO 2016/175738
`
`PCT/U82015/027743
`
`group, in turn, may react or form hydrogen bonds with hydroxyl groups of metal
`
`oxide particulate surface, as well as with silanol groups of other dispersant
`
`molecules through hydrogen bonding. These reactions lead to bonding or
`
`preferential absorption of the dispersant molecules to the metal oxide particulate
`
`surfaces and also form bonds between dispersant molecules themselves. As a
`
`result, these interactions can form thick hydrophilic coatings of reactive
`
`dispersant molecules on surface of the white metal oxide pigment. This coating
`
`can increase the hydrodynamic radius of the particulates and thus reduce their
`
`effective density and settling rate. Furthermore, the dispersant coating prevents
`
`agglomeration of the white metal oxide pigment upon settling so that when
`
`sediment and settling does occur over time in the ink formulations, the settled
`
`white metal oxide pigment remain fluffy and thus are easy to re-disperse upon
`
`agitation. In still further detail, these dispersants have a relatively short chain
`
`length and do not contribute significantly to the ink viscosity, even with relatively
`
`high metal oxide particulate loads, e.g. over 30 wt% white metal oxide pigment in
`
`the ink.
`
`[0025]As mentioned, a suitable alkoxysilane dispersant can have an
`
`alkoxysilane group which can be easily hydrolyzed in aqueous environment and
`
`produce a silanol group, and a hydrophilic segment. The general structure of the
`
`alkoxysilane group is —Si(OR)3, where R most can be methyl, ethyl, n-propyl,
`
`isopropyl, or even a longer (branched or unbranched) alkane chain. It is noted
`
`that the longer the hydrocarbon (R), the slower hydrolysis rate and rate of
`
`interaction with dispersed metal oxide particulate surface. In a few highly practical
`
`examples, structures with —Si(OR)3 where R is methyl or ethyl can typically be
`
`used. The hydrophilic segment of the alkoxysilane dispersant can likewise be
`
`large enough (relative to the whole molecule size) in order to enable dispersant
`
`solubility in aqueous environment, as well as prevent agglomeration of the white
`
`metal oxide pigment. In one example, the hydrophilic segment can be a polyether
`
`chain, e.g., polyethylene glycol (PEG) or its co—polymer with polypropylene glycol
`
`(PPG). Polyether—based dispersant moieties have clean thermal decomposition,
`
`and thus, are good candidates for use. When heated above decomposition
`
`temperature, PEG and PPG-based molecules decompose into smaller molecular
`
`9
`
`1O
`
`15
`
`20
`
`25
`
`30
`
`
`
`WO 2016/175738
`
`PCT/U82015/027743
`
`fragments with high volatility or good water solubility. Thus, their decomposition
`
`usually does not form noticeable amounts of solid residue on surface of
`
`microscopic heaters used for driving thermal inkjet printheads (which can cause
`
`thermal inkjet printheads to fail over time or render them non—operational in some
`
`instances).
`
`[0026] In further detail, examples polyether alkoxysilane dispersants that
`
`may be used to disperse white metal oxide pigment can be represented by the
`
`following general Formula (I):
`
`(I)
`
`R1
`
`
`
`Rz—Sli
`
`R3
`
`(PE) — R4
`
`1O
`
`wherein:
`
`a) R1, R2 and R3 are hydroxy groups, or hydrolyzable linear or branched
`
`alkoxy groups. For hydrolyzable alkoxy groups, such groups can have 1 to 3
`
`carbon atoms; in one aspect, such groups can be —OCH3 and —OCH2CH3. In
`
`some examples, R1, R2 and R3 are linear alkoxy groups having from 1 to 5 carbon
`
`15
`
`atoms. In some other examples, R1, R2 and R3 groups are —OCH3 or —OCZH5.
`
`b) PE is a polyether oligomer chain segment of the structural formula
`
`[(CH2)n—CH(R)—O]m, attached to Si through Si—C bond, wherein n is an integer
`
`ranging from O to 3, wherein m is an integer superior or equal to 2 and wherein R
`
`is H or a chain alkyl group. R can also be a chain alkyl group having 1 to 3
`
`carbon atoms, such as CH3 or CzH5. In some examples, m is an integer ranging
`
`from 3 to 30 and, in some other examples, m is an integer ranging from 5 to 15.
`
`The polyether chain segment (PE) may include repeating units of polyethylene
`
`glycol (PEG) chain segment (—CH2CH2—O—), or polypropylene glycol (PPG)
`
`chain segment (—CH2—CH(CH3)—O—), or a mixture of both types. In some
`
`examples, the polyether chain segment (PE) contains PEG units (—CHZCH2—
`
`20
`
`25
`
`0—); and
`
`c) R4 is hydrogen, or a linear or a branched alkyl group. In some examples,
`
`R4 is an alkyl group having from 1 to 5 carbon atoms.
`
`10
`
`
`
`WO 2016/175738
`
`PCT/U82015/027743
`
`[0027] Other examples of dispersants used to disperse white metal oxide
`
`pigment can include polyether alkoxysilane dispersants having the following
`
`general Formula (II):
`
`OR’
`
`(11)
`
`OR”—Si — (PE)— R4
`
`OR!!!
`
`1O
`
`15
`
`20
`
`25
`
`wherein R’, R" and R'" are linear or branched alkyl groups. In some
`
`examples, R', R” and R'" are linear alkyl groups having from 1 to 3 carbon atoms
`
`in chain length. In some examples, R', R” and R"’—CH3 or —C2H5. R4 and PE are
`
`as described above for Formula (I); i.e. PE is a polyether oligomer chain segment
`
`of the structural formula: [(CH2) n—CH—R—O]m, wherein n is an integer ranging
`
`from O to 3, wherein m is an integer superior or equal to 2 and wherein R is H or
`
`a Chain alkyl group; and R4 is hydrogen, or a linear or a branched alkyl group. In
`
`some examples, R4 is CH3 or CzH5.
`
`[0028] In some examples, the white metal oxide pigment present in the ink
`
`composition are dispersed with polyether alkoxysilanes. Examples of suitable
`
`polyether alkoxysilanes include (CH30)3Si—(CH20HzO)n, H; (CH3CH20)3Si—
`
`(CHZCH20)n,H; (CH30)3Si—(CHZCHZO)n, CH3; (CH3CHZO)3Si—(CHZCHZO)n,
`
`CH3; (CH30)3Si—(CHZCH20)n, CH2CH3; (CH30H20)3Si—(CHZCHZO)n, CHchg;
`
`(CH30)3Si—(CHZCH(CH3)O)n, H; (CHgCHzO)3Si—(CH2CH(CH3) O)“, H;
`
`(CH30)3Si—(CHZCH(CH3) O)n, CH3; (CH3CH20)3Si—(CH20H(CH3) 0)”, CH3;
`
`wherein n' is an integer equal to 2 or greater. In some examples, n' is an integer
`
`ranging from 2 to 30 and, in some other examples, n’ is an integer ranging from 5
`
`to 15.
`
`[0029] Commercial examples of the polyether alkoxysilane dispersants
`
`include, but are not limited to, the aforementioned Silquest®A—1230
`
`manufactured by Momentive Performance Materials, and Dynasylan® 4144
`
`manufactured by Evonik/Degussa.
`
`[0030]The amount of dispersant used to disperse the white metal oxide
`
`pigment and other solids may vary from about 1% by weight to about 300% by
`
`weight of the white metal oxide pigment content. In some examples, the
`
`11
`
`
`
`WO 2016/175738
`
`PCT/USZOlS/027743
`
`dispersant content range is from about 2 to about 150% by weight of the white
`
`metal oxide pigment content. In some other examples, the dispersant content
`
`range is from about 5 to about 100% by weight of the white metal oxide pigment
`
`content.
`
`[0031]A dispersion of white metal oxide pigment suitable for forming the
`
`white inks of the present disclosure can be prepared via milling or dispersing
`
`metal oxide powder in water in the presence of suitable dispersants. For example,
`
`the metal oxide dispersion may be prepared by milling commercially available
`
`inorganic oxide pigment having large particulate size (in the micron range) in the
`
`presence of the dispersants described above until the desired particulate size is
`
`achieved. The starting dispersion to be milled can be an aqueous dispersion with
`
`solid content up to 65% by weight of the white metal oxide pigment or pigments.
`
`The milling equipment that can be used may be a bead mill, which is a wet
`
`grinding machine capable of using very fine beads having diameters of less than
`
`1.0 mm (and, generally, less than 0.5 mm) as the grinding medium, for example,
`
`Ultra-Apex Bead Mills from Kotobuki Industries Co. Ltd. The milling duration, rotor
`
`speed, and/or temperature may be adjusted to achieve the dispersion particulate
`
`size desired.
`
`[0032]The anionic oxide particulates that are also included in the white ink
`
`can be any of a variety of anionic oxide particles, such as anionic semi-metal
`
`oxide particles, e.g., anionic silica particulates. One example is an anionically-
`
`stabilized colloidal silica dispersion. Other examples include precipitated silica
`
`dispersions, anionically charged alumina silicate particle dispersion, anionically-
`
`stabilized fumed silica dispersions (such as Cab—O—Sperse® silica series
`
`available from Cabot Corporation). Typically, in many colloidal silica dispersions,
`
`particulates have a strong anionic (negative) charge at about pH >7, and thus,
`
`can instantly or very quickly react with cationic polymer applied to a media
`
`substrate, forming a loose cross-linked network. Generally, the higher is the
`
`number of particulates per volume of the ink, the stronger is their cross-
`
`linking/pigment immobilization effect upon mixing with the fixer layer or fluid on
`
`the media substrate. Thus, in some examples, there are advantages for using
`
`small anionically charged silica, e.g., the same weight percentage of anionic
`
`12
`
`1O
`
`15
`
`20
`
`25
`
`30
`
`
`
`WO 2016/175738
`
`PCT/U82015/027743
`
`oxide particulates in an ink formulation at 3 nm would have roughly 103 times
`
`more particulates than a dispersion having 30 nm particulates. Thus, the use of
`
`small particles, e.g., from 1 nm to 100 nm, or more typically from 1 nm to 50 nm,
`
`relative to the size of the white metal oxide pigments, e.g., 100 nm to 2000 nm,
`
`can provide some advantage with respect to fixing an ink with a fixer coating or
`
`composition.
`
`[0033]Anionic oxide particulates, such as anionic colloidal silica in
`
`dispersion form, are commercially available, and examples include Snowtex®
`
`Colloidal Silicas available from Nissan Chemical Corporation, e.g., Snowtex® ST—
`
`S (spherical particulates; median particulate size ~2—3nm); Snowtex® ST-3OLH
`
`(spherical particulates; median particulate size ~30nm); and Snowtex® ST-UP
`
`(elongated particulates (particulate dimensions ~9-15/40-100 nm). Other anionic
`
`oxide particulates include IDISIL® colloidal silica available from Evonik Industries
`
`(particulate size 5—50nm); Ludox® colloidal silicas available from W.R. Grace &
`
`Co. such as Ludox® HS-3O (particulate size ~12nm); Ludox AM, Ludox® SM-AS,
`
`Ludox® AS-30, Ludox® AS-40 (particulate size ~12nm), etc.; Bindzil® and
`
`Levasi|® grades of colloidal silica available from Akzo Nobel N.V.
`
`[0034] It is also notable that there are advantages to adding the latex
`
`particulates to the inks of the present disclosure. For example, by combining
`
`white metal oxide pigment with latex particulates, opacity can be increased, even
`
`though la
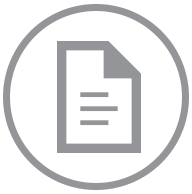
Accessing this document will incur an additional charge of $.
After purchase, you can access this document again without charge.
Accept $ ChargeStill Working On It
This document is taking longer than usual to download. This can happen if we need to contact the court directly to obtain the document and their servers are running slowly.
Give it another minute or two to complete, and then try the refresh button.
A few More Minutes ... Still Working
It can take up to 5 minutes for us to download a document if the court servers are running slowly.
Thank you for your continued patience.
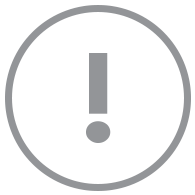
This document could not be displayed.
We could not find this document within its docket. Please go back to the docket page and check the link. If that does not work, go back to the docket and refresh it to pull the newest information.
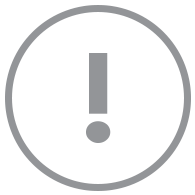
Your account does not support viewing this document.
You need a Paid Account to view this document. Click here to change your account type.
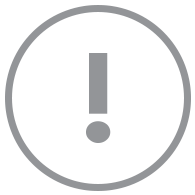
Your account does not support viewing this document.
Set your membership
status to view this document.
With a Docket Alarm membership, you'll
get a whole lot more, including:
- Up-to-date information for this case.
- Email alerts whenever there is an update.
- Full text search for other cases.
- Get email alerts whenever a new case matches your search.
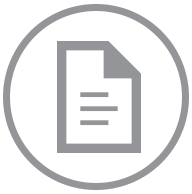
One Moment Please
The filing “” is large (MB) and is being downloaded.
Please refresh this page in a few minutes to see if the filing has been downloaded. The filing will also be emailed to you when the download completes.
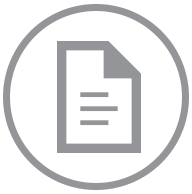
Your document is on its way!
If you do not receive the document in five minutes, contact support at support@docketalarm.com.
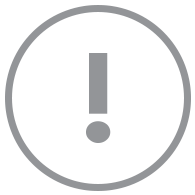
Sealed Document
We are unable to display this document, it may be under a court ordered seal.
If you have proper credentials to access the file, you may proceed directly to the court's system using your government issued username and password.
Access Government Site