`
`(19) p)
`
`Eu ropfiisches Patentamt
`
`European Patent Office
`
`Office européen des brevets
`
`(11)
`
`EP 1 403 341 A1
`
`(12)
`
`EUROPEAN PATENT APPLICATION
`
`(43) Date of publication:
`31.03.2004 Bulletin 2004/14
`
`(21) Application number: 03077891.4
`
`(22) Date of filing: 15.09.2003
`
`(84) Designated Contracting States:
`AT BE BG CH CY CZ DE DK EE ES FI FR GB GR
`HU IE IT LI LU MC NL PT RO SE SI SK TR
`
`Designated Extension States:
`AL LT LV MK
`
`(30) Priority: 27.09.2002 US 256822
`
`(71) Applicant: EASTMAN KODAK COMPANY
`Rochester, New York 14650 (US)
`
`(72) Inventors:
`- Chen, Huijuan D., clo Eastman Kodak Company
`Rochester, New York 14650-2201 (US)
`
`
`
`(51) lntCl.7: C09D 11/00, B41J 2/42,
`B41 M 5/00
`
`0 Wang, Xiaoru, c/o Eastman Kodak Company
`Rochester, New York 14650-2201 (US)
`- Frazier, Ricky G., c/o Eastman Kodak Company
`Rochester, New York 14650-2201 (US)
`
`(74) Representative: Weber, Etienne Nicolas et al
`Kodak Industrie,
`Département Brevets,
`CRT,
`Zone Industrielle
`
`71102 Chalon sur Saone Cedex (FR)
`
`(54)
`
`lnkjet printing method and inkjet ink composition
`
`An inkjet printing method, comprising the steps
`(57)
`of A) providing an ink jet printer that is responsive to
`digital data signals; B) loading the printerwith an inkjet
`recording element; C) loading the printer with an inkjet
`ink composition comprising an aqueous inkjet ink com—
`position comprising: a pigment, a polymer latex contain-
`
`ing at least one halogenated vinyl monomer, at least one
`surfactant, and a humectant; and D) printing on the ink
`jet recording element accompanied by a heating step
`using the inkjet inkcomposition in responseto the digital
`data signals.
`
`EP1403341A1
`
`Printed by Jouve, 75001 PARIS (FR)
`
`
`
`EP 1 403 341 A1
`
`Description
`
`FIELD OF THE INVENTION
`
`[0001] The present invention relates to an inkjet printing method using an aqueous inkjet ink composition comprising
`pigment and a polymer latex. The polymer latex is prepared from at least one halogenated vinyl monomer composition.
`
`BACKGROUND OF THE INVENTION
`
`lnkjet printing is a non-impact method for producing images by the deposition of ink droplets on a substrate
`[0002]
`(paper, transparentfilm, fabric, etc.) in response to digital signals. lnkjet printers have found broad applications across
`markets ranging from industrial labeling to short run printingto desktop document and pictorial imaging and large format
`printing for outdoor applications such as banners, signages, displays, posters, billboard and buswraps.
`[0003] This technique of printing is well suited for printing on a variety of surfaces (receivers) including porous and
`non-porous surfaces. Porous inkjet receivers have the advantage of large fluid intake and this provides fast printing
`speed. However, in some applications, such as banners, signages, displays, posters, billboard and buswraps, these
`porous receivers suffer from durability issues such as lightfastness, waterfastness, abrasion resistance and weather
`resistance. In order to overcome these problems, the prints are usually post treated by methods such as lamination,
`which adds to the cost considerably. Historically, in orderto overcome these problems, solvent based inks or UV curable
`inks were developed to be printed on non-absorbing substrates such as vinyl to achieve the desired durability. US
`patent 4,106,027 describes such a solvent based ink that is suitable for printing images on non-absorbing receivers
`with improved adhesion and durability. EP 0 882 104 B1 describes a UV curable inkjet ink composition for better
`durability of the print on non—absorbing substrate. A significant environmental, health and safety concern with both of
`these types of ink is the evaporation of solvent or UV monomer during printing.
`[0004] US Patent 8,087,416 describes the use of an aqueous based pigment ink for printing on non—absorbing vinyl
`substrate. That ink contains a grafted copolymer binder that is soluble in the aqueous vehicle but insoluble in water.
`However, the problem with the ink is that, due to the soluble nature of the binder in the ink vehicle, the ink viscosity is
`high and the printing reliability is poor. In addition, the printed images are not durable to solvent.
`[0005] US Patent 4,762,875 described a printing inks containing pigment and polymer additives forplastics and metal
`surfaces, however, there is a problem with this invention that the solid content for this ink is high, therefore the viscosity
`of the ink is too high for inkjet ink applications; in addition, the additives used in this invention is hydrophilic in nature
`therefore the resulted coatings has poor water resistance.
`[0006] Therefore, there is a need for an aqueous based inkjet ink that provides good waterfastness, lightfastness,
`abrasion resistance, good adhesion to non-absorbing substrates including untreated vinyl, and that can be printed
`reliably through a piezo or thermal printhead.
`
`SUMMARY OF THE INVENTION
`
`[0007] This and other objects are achieved in accordance with the present invention which comprises an ink jet
`printing method, comprising the steps of:
`
`A) providing an inkjet printer that is responsive to digital data signals;
`B) loading said printer with an inkjet recording element;
`C) loading said printer with an inkjet ink composition comprising an aqueous inkjet ink composition comprising:
`
`- -
`- -
`- -
`- -
`
`a pigment;
`a polymer latex containing at least one halogenated vinyl monomer;
`at least one surfactant; and
`a humectant; and
`
`D) printing on said inkjet recording element accompanied by a heating step using said ink jet ink composition in
`response to said digital data signals.
`
`ltwas found that the colloid stability, stain resistance and abrasion resistance of an inkjet image was improved
`[0008]
`using the composition described herein.
`
`10
`
`15
`
`20
`
`25
`
`30
`
`35
`
`4o
`
`45
`
`50
`
`55
`
`
`
`DETAILED DESCRIPTION OF THE INVENTION
`
`EP 1 403 341 A1
`
`[0009] The method of the present invention is suited for printing on a variety of substrates, especially on non-ab-
`sorbing substrates. The non-absorbing substrates that may be used in the present invention include any substrate that
`is essentially non-porous. They are usually not specially treated for additional liquid absorption. Therefore, these ma-
`terials have very low or no liquid absorbing capacity. Examples of such non-absorbing substrates are metals such as
`aluminum, copper, stainless steel and alloy etc.; plastics such as vinyl, polycarbonate, polytetrafluoroethylene (PTFE),
`polyethylene, polypropylene, polystyrene, cellulose; and other substrates such as ceramics, glass.
`[0010]
`In orderto achieve good image durability when printing aqueous based inks onto a non-absorbing substrate,
`the polymeric binder in the ink composition needs to be essentially hydrophobic, capable of providing good adhesion
`strength to the non—absorbing substrate, and also not be easily re—dispersible in water after drying . In addition, in order
`to provide good ink storage stability and prevent potential nozzle clogging, the hydrophobic polymer binder also needs
`to be sufficiently stable as a dispersion and compatible with other ink components, such as surfactant, colorants and
`humectants. Therefore, the polymer binders need to be dispersible in aqueous ink environment but not soluble to
`achieve low ink viscosity and print durability to both water and solvents. Furthermore, the ink should have sufficiently
`low surface tension to have good wettability to the non-absorbing substrate.
`[0011] The pigment used in the present invention can be either self-dispersible such as those described in US patent
`5,630,868, encapsulated as those described in the pending US patent application Serial No. 09/822,723, filed March
`30, 2001, or can be stabilized by a dispersant. The process of preparing inks from pigments commonly involves two
`steps: (a) a dispersing or milling step to break up the pigment to the primary particle, and (b) dilution step in which the
`dispersed pigment concentrate is diluted with a carrier and other addenda to a working strength ink. In the milling step,
`the pigment is usually suspended in a carrier (typically the same carrier as that in the finished ink) along with rigid,
`inert milling media. Mechanical energy is supplied to this pigment dispersion, and the collisions between the milling
`media and the pigment cause the pigment to deaggregate into its primary particles. A dispersant or stabilizer, or both,
`is commonly added to the pigment dispersion to facilitate the deaggregation of the raw pigment, to maintain colloidal
`particle stability, and to retard particle reagglomeration and settling.
`[0012] There are many different types of materials which may be used as milling media, such as glasses, ceramics,
`metals, and plastics. In a preferred embodiment, the grinding media can comprise particles, preferably substantially
`spherical in shape, e.g., beads, consisting essentially of a polymeric resin. In general, polymeric resins suitablefor use
`as milling media are chemically and physically inert, substantially free of metals, solvent and monomers, and of sufficient
`hardness and firability to enable them to avoid being chipped or crushed during milling. Suitable polymeric resins
`include crosslinked polystyrenes, such as polystyrene crosslinked with divinylbenzene, styrene copolymers, polyacr-
`ylates such as poly(methyl methylacrylate), olycarbonates, polyacetals, such as DerlinT'V', vinyl chloride polymers and
`copolymers, polyurethanes, polyamides, poly(tetrafluoroethylenes), e.g., TeflonT'V', and otherfluoropolymers, high den-
`sity polyethylenes, polypropylenes, cellulose ethers and esters such as cellulose acetate, poly(hydroxyethylmethacr—
`ylate), poly(hydroxyethylacrylate), silicone containing polymers such as polysiloxanes and the like. The polymer can
`be biodegradable. Exemplary biodegradable polymers include poly(lactides), poly(glycolids) copolymers of lactides
`and glycolide, polyanhydrides, poly(imino carbonates), poly(N-acy|hydroxyproline) esters, poly(N-palmitoyl hydroxy-
`prolino) esters, ethylene-vinyl acetate copolymers, poly(orthoesters), poly(caprolactones), and poly(phosphazenes).
`The polymeric resin can have a density from 0.9 to 3.0 g/cm3. Higher density resins are preferred inasmuch as it is
`believed that these provide more efficient particle size reduction. Most preferred are crosslinked or uncrosslinked pol-
`ymeric media based on styrene.
`[0013] Milling can take place in any suitable grinding mill. Suitable mills include an airjet mill, a roller mill, a ball mill,
`an attritor mill and a bead mill. A high speed mill is preferred. By high speed mill we mean milling devices capable of
`accelerating milling media to velocities greater than about 5 meters per second. Sufficient milling media velocity is
`achieved, for example, in Cowles-type saw tooth impeller having a diameter of 40 mm when operated at 9,000 rpm.
`The preferred proportions of the milling media, the pigment, the liquid dispersion medium and dispersant can vary
`within wide limits and depends, for example, up on the particular material selected and the size and density of the
`milling media etc. After milling is complete, the dispersion of active material is separated from the grinding media by
`simple sieving or filtration. With either of the above modes the preferred amounts and ratios of the ingredients of the
`mill grind will vary widely depending upon the specific materials and the intended applications. The contents of the
`milling mixture comprise the mill grind and the milling media. The mill grind comprises pigment, dispersant and a liquid
`carrier such as water. For aqueous inkjet inks, the pigment is usually present in the mill grind at 1 to 50 weight %,
`excluding the milling media. The weight ratio of pigment to dispersant is 20:1 to 1:2. The high speed mill
`is a high
`agitation device, such as those manufactured by Morehouse-Cowles, Hockmeyer et al.
`[0014] The dispersant is another ingredient in the mill grind. It can be either a small molecule or a polymer. Preferred
`dispersants used in the present invention include sodium dodecyl sulfate, acrylic and styrene-acrylic copolymers, such
`as those disclosed in U. 8. Pat. Nos. 5,085,698 and 5,172,133, and sulfonated polyesters and styrenics, such as those
`
`10
`
`15
`
`20
`
`25
`
`30
`
`35
`
`4o
`
`45
`
`50
`
`55
`
`
`
`EP 1 403 341 A1
`
`disclosed in U.S. Pat. No. 4,597,794. Other patents referred to above in connection with pigment availability also
`disclose a wide variety of dispersants. The dispersant used in the examples is potassium N-methyl-N-oleoyl taurate
`(K-OMT).
`[0015] The milling time can vary widely and depends upon the pigment, mechanical means and residence conditions
`selected, the initial and desired final particle size, etc. For aqueous mill grinds usingthe preferred pigments, dispersants,
`and milling media described above, milling times will typically rangefrom 1 to 100 hours. The milled pigment concentrate
`is preferably separated from the milling media by filtration.
`[0016] The pigment particles useful in the invention may have any particle sizes which can bejetted through a print
`head. Preferably, the pigment particles have a mean particle size of less than about 0.5 micron, more preferably less
`than about 0.2 micron.
`
`[0017] A wide variety of organic and inorganic pigments, alone or in combination, may be selected for use in the
`present invention. Colorant particles which may be used in the invention include pigments as disclosed, for example
`in U.S. Patents 5,026,427; 5,086,698; 5,141,556; 5,160,370; and 5,169,436. The exact choice of pigments will depend
`upon the specific application and performance requirements such as color reproduction and image stability. Pigments
`suitable for use in the present invention include, for example, azo pigments, monoazo pigments, disazo pigments, azo
`pigment lakes, [3-Naphthol pigments, Naphthol AS pigments, benzimidazolone pigments, disazo condensation pig-
`ments, metal complex pigments,
`isoindolinone and isoindoline pigments, polycyclic pigments, phthalocyanine pig-
`ments, quinacridone pigments, perylene and perinone pigments, thioindigo pigments, anthrapyrimidone pigments, fl-
`avanthrone pigments, anthanthrone pigments, dioxazine pigments, triarylcarbonium pigments, quinophthalone pig-
`ments, diketopyrrolo pyrrole pigments, titanium oxide,
`iron oxide, and carbon black. Typical examples of pigments
`which may be used include Color Index (C.
`l.) Pigment Yellow 1, 2, 3, 5, 6, 10, 12, 13,14, 16, 17, 62, 65, 73, 74, 75,
`81, 83, 87, 90, 93, 94, 95, 97, 98, 99, 100, 101, 104, 106, 108, 109, 110, 111, 113, 114, 116, 117, 120, 121, 123, 124,
`126,127,128,129,130,133,136,138,139,147,148,150,151,152,153,154,155,165,166,167,168,169,170,
`171,172,173,174,175,176,177,179,180,181,182,183,184,185,187,188,190,191,192,193,194;C.I.Pigment
`Orange1, 2, 5, 6, 13, 15, 16, 17, 17:1, 19, 22, 24, 31, 34, 36, 38, 40, 43, 44, 46, 48, 49, 51, 59, 60, 61, 62, 64, 65, 66,
`67, 68, 69; C.
`l. Pigment Red 1, 2, 3, 4, 5, 6, 7, 8, 9, 10, 11, 12, 13, 14, 15, 16, 17, 18, 21,22, 23, 31 , 32, 38, 48:1,48:
`2, 48:3, 48:4, 49:1 , 49:2, 49:3, 50:1, 51, 52:1 , 52:2, 53:1, 57:1, 60:1, 63:1, 66, 67, 68, 81, 95, 112, 114, 119, 122, 136,
`144,146,147,148,149,150,151,164,166,168,169,170,171,172,175,176,177,178,179,181,184,185,187,
`188, 190, 192, 194,200,202,204,206,207,210,211,212,213,214,216,220,222,237,238, 239,240,242,243,245,247,248,
`251 ,252,253,254,255,256,258,261 ,264; C.l. Pigment Violet 1, 2, 3, 5:1, 13, 19, 23, 25, 27, 29, 31, 32, 37, 39, 42, 44,
`50; 0|. Pigment Blue1, 2, 9, 10, 14, 15:1, 15:2, 15:3, 15:4, 15:6, 15, 16, 18, 19, 24:1, 25, 56, 60, 61, 62, 63, 64, 66;
`C.l. Pigment Green 1, 2, 4, 7, 8, 10, 36, 45; C.l. Pigment Black 1, 7, 20, 31, 32, and C.|. Pigment Brown 1,5, 22, 23,
`25, 38, 41, 42. In a preferred embodiment of the invention, the pigment is C.l. Pigment Blue 15:3, C.|. Pigment Red
`122, C.l. Pigment Yellow 155, C.l. Pigment Yellow 74, C.|. Pigment Black7 or bis(phthalocyanylalumino)tetraphenyld-
`isiloxane as described in U.S. Pat. No. 4,311,775.
`[0018]
`In the case of organic pigments, the ink may contain up to approximately 20% pigment by weight, but will
`generally be in the range of approximately 0.1 to 10%, preferably approximately 0.1 to 5%, by weight of the total ink
`composition for most inkjet printing applications. If an inorganic pigment is selected, the ink will tend to contain higher
`weight percentages of pigment than with comparable inks employing organic pigments.
`[0019]
`Instead of pigment, a dye can also be used in the current invention. Preferably, the dye is a water insoluble
`dye. To make the ink, the water insoluble dye can be dispersed or encapsulated into water dispersible particles as
`disclosed in U. S. Serial No. 10/020,694, filed December 14, 2001 . A broad range of water-insoluble dyes may be used
`in the invention such as an oil dye, a disperse dye, or a solvent dye, such as Ciba-Geigy Orasol Red G, Ciba-Geigy
`Orasol Blue GN, Ciba-Geigy Orasol Pink, and Ciba-Geigy Orasol Yellow. Preferred water-insoluble dyes can be xan-
`thene dyes, methine dyes, polymethine dyes, anthroquinone dyes, merocyanine dyes, azamethine dyes, azine dyes,
`quinophthalone dyes, thiazine dyes, oxazine dyes, phthalocyanine dyes, mono or poly azo dyes, and metal complex
`dyes. More preferably, the water insoluble dyes can be an azo dye such as a water insoluble analog of the pyrazolea—
`zoindole dye disclosed in U.S. Patent No. 6,468,338, and the arylazoisothiazole dye disclosed in U. 8. Patent 4,698,651,
`or a metal-complex dye, such as the water-insoluble analogues of the dyes described in U.S. Patents 5,997,622 and
`6,001,161, Le, a transition metal complex of an 8-heterocyclylazo-5-hydroxyquinoline. The solubility of the water in-
`soluble dye used in the present invention should be less than 1 g/L in water, and more preferably less than 0.5 g/L in
`water.
`
`[0020] The water insoluble dye can be present in any effective amount in the ink of the present invention, usually up
`to about 20% by weight of an ink jet ink composition, and preferably from about 0.05 to 15 wt. %.
`[0021] The polymer latex used in this invention can be homopolymer or copolymer or cross-linked polymer prepared
`with at least one halogenated vinyl monomer, and optionally other ethylenically-unsaturated monomers such that the
`latex can be stabilized in a water-based medium. The polymer latex contains an ethylenically-unsaturated monomer
`capable of addition polymerization. The ethylenically-unsaturated monomers which can be used in the invention in-
`
`10
`
`15
`
`20
`
`25
`
`30
`
`35
`
`4o
`
`45
`
`50
`
`55
`
`
`
`EP 1 403 341 A1
`
`clude, for example, the following monomers and their mixtures: acrylic acid, methacrylic acid, ethacrylic acid, methyl
`acrylate, ethyl acrylate, ethyl methacrylate, benzyl acrylate, benzyl methacrylate, propyl acrylate, propyl methacrylate,
`iso-propyl acrylate, iso-propyl methacrylate, butyl acrylate, butyl methacrylate, hexyl acrylate, hexyl methacrylate, oc-
`tadecyl methacrylate, octadecyl acrylate, lauryl methacrylate, lauryl acrylate, hydroxyethyl acrylate, hydroxyethyl meth-
`acrylate, hydroxyhexyl acrylate, hydroxyhexyl methacrylate, hydroxyoctadecyl acrylate, hydroxyoctadecyl methacr-
`ylate, hydroxylauryl methacrylate, hydroxylauryl acrylate, phenethylacrylate, phenethyl methacrylate, 6-phenylhexyl
`acrylate, 6-phenylhexyl methacrylate, phenyllauryl acrylate, phenyllaurylmethacrylate, 3-nitrophenyl-6-hexyl methacr-
`ylate, 3-nitrophenyl-18-octadecyl acrylate, ethyleneglycol dicyclopentyl ether acrylate, vinyl ethyl ketone, vinyl propyl
`ketone, vinyl hexyl ketone, vinyl octyl ketone, vinyl butyl ketone, cyclohexyl acrylate,3-methacryloxypropyl-dimethyl-
`methoxysilane, 3-methacryloxypropylmethyldimethoxysilane, S-methacryloxypropyl-pentamethyldisiloxane, 3-meth-
`acryloxypropyltris—(trimethylsiloxy)silane, 3—acryloxypropyldimethylmethoxysilane, acryloxypropylmethyldimethoxysi—
`lane, trifluoromethyl styrene, trifluoromethyl acrylate, trifluoromethyl methacrylate, tetrafluoropropyl acrylate, tetrafluor—
`opropyl methacrylate, heptafluorobutyl methacrylate,
`isobutyl acrylate, isobutyl methacrylate, 2—ethylhexyl acrylate,
`2-ethylhexyl methacrylate, isooctyl acrylate, isooctyl methacrylate, N,N-dihexyl acrylamide, N,N-dioctyl acrylamide, N,
`N-dimethylaminoethyl acrylate, N,N-dimethylaminoethyl methacrylate, N,N-diethylaminoethyl acrylate, N,N-diethyl-
`aminoethyl methacrylate, piperidino-N-ethyl acrylate, vinyl propionate, vinyl acetate, vinyl butyrate, vinyl butyl ether,
`and vinyl propyl ether ethylene, styrene, vinyl carbazole, vinyl naphthalene, vinyl anthracene, vinyl pyrene, methyl
`methacrylate, methyl acrylate, alpha-methylstyrene, dimethylstyrene, methylstyrene, Vinylbiphenyl, glycidyl acrylate,
`glycidyl methacrylate, glycidyl propylene, 2-methyl-2-vinyl oxirane, vinyl pyridine, aminoethyl methacrylate, aminoethyl-
`phenyl acrylate, maleimide, N-phenyl maleimide, N-hexyl maleimide, N-vinyl-phthalimide, and N-vinyl maleimide poly
`(ethylene glycol) methyl ether acrylate, polyvinyl alcohol, vinyl pyrrolidone, vinyl 4-methylpyrrolidone, vinyl 4-phenylpyr-
`rolidone, vinyl imidazole, vinyl 4-methylimidazole, vinyl 4-phenylimidazole, acrylamide, methacrylamide, N,N-dimethyl
`acrylamide, N—methyl acrylamide, N—methyl methacrylamide, aryloxy dimethyl acrylamide, N—methyl acrylamide, N—
`methyl methacrylamide, aryloxy piperidine, and N,N—dimethyl acrylamide acrylic acid, methacrylic acid, chlorometh—
`acrylic acid, maleic acid, allylamine, N,N—diethylallylamine, vinyl sulfonamide, sodium acrylate, sodium methacrylate,
`ammonium acrylate, ammonium methacrylate, acrylamidopropanetriethylammonium chloride, methacrylamidopropan-
`etriethylammonium chloride, vinyl-pyridine hydrochloride, sodium vinyl phosphonate and sodium 1-methylvinylphos-
`phonate, sodium vinyl sulfonate, sodium 1-methylvinyl-sulfonate, sodium styrenesulfonate, sodium acrylamidopro-
`panesulfonate, sodium methacrylamidopropanesulfonate, and sodium vinyl morpholine sulfonate, allyl methacrylate,
`allyl acrylate, butenyl acrylate, undecenyl acrylate, undecenyl methacrylate, vinyl acrylate, and vinyl methacrylate,
`dienes such as butadiene and isoprene; esters of saturated glycols or diols with unsaturated monocarboxylic acids
`such as, ethylene glycol diacrylate, ethylene glycol dimethacrylate, triethylene glycol dimethacrylate, 1,4-butanediol
`dimethacrylate, 1,3-butanediol dimethacrylate, pentaerythritol tetraacrylate, trimethylol propane trimethacrylate and
`polyfunctuional aromatic compounds such as divinylbenzene.
`[0022] The halogenated vinyl monomer used in the present invention can be vinyl chloride, vinylidene chloride, vinyl
`fluoride, vinylidene fluoride, vinyl bromide and vinylidene bromide, chloromethacrylic acid and the like.
`[0023]
`Surfactants that can be used in the present invention to synthesize the polymers include, for example, a
`sulfate, a sulfonate, a cationic compound, a reactive surfactant, an amphoteric compound, and a polymeric protective
`colloid. Specific examples are described in "McCutcheon's Emulsifiers and Detergents: 1995, North American Editor"
`and will be known to those skilled in the art.
`
`[0024] Depending on the types of initiators used, the reaction temperature can vary from about 30°C to about 90°C.
`Preferablythe reaction temperature is at least 40°C, and most preferably at least 50°C. To ensure that no free monomer
`is present, usually the reaction is continued for a time after the monomer addition. Also, more initiator may need to be
`added as a scavenger during the final stage of the reaction to increase the reaction conversion.
`[0025] Addition polymerization initiators useful in the practice of the invention include, for example, azo and diazo
`compounds, such as 2,2'-azobisisobutyronitrile, 2,2'-azobis(2,4-dimethyl valeronitrile), 2,2'-azobis(2,3-dimethyl buty-
`ronitrile), 2,2'—azobis(2—methyl butyronitrile), 2,2'—azobis(2,3,3—trimethyl butyronitrile), 2,2'—azobis(2—isopropyl butyroni—
`trile), 1,1'—azobis(cyc|ohexane—1—carbonitrile), 2, 2'—azobis(4—methoxyl—2,4—dimethyl valeronitrile), 2—(carbamoylazo)
`isobutyronitrile, 4,4'-azobis(4-cyanovaleric acid), and dimethyl -2,2'azobis isobutyrate, or peroxide compounds, such
`as butyl peroxide, propyl peroxide, butyryl peroxide, benzoyl isobutyryl peroxide, and benzoyl peroxide, orwater soluble
`initiators, for example, sodium persulfate, and potassium persulfate, or any redox initiators. Preferred initiators are the
`oil soluble initiators. Examples of particularly suitable initiators are azo, peroxide, persulfate, and redox initiators. The
`initiators may be used in an amount varying from about 0.2 to 4 weight percent or higher by weight of thetotal monomers.
`A chain transfer agent such as butyl mercaptan, may also be used to control the properties of the polymer formed.
`[0026] The polymers can be made via emulsion polymerization, dispersion polymerization, suspension polymeriza-
`tion, grand milling, or solution/bulk polymerization and then post-emulsification. Detailed information about the process
`and the stabilizers can be found in ”Emulsion Polymerization and Emulsion Polymers " (P. A. Lovell, M. S. El-Aasser,
`John Wiley & Sons Ltd., England, 1997).
`
`10
`
`15
`
`20
`
`25
`
`30
`
`35
`
`4o
`
`45
`
`50
`
`55
`
`
`
`EP 1 403 341 A1
`
`[0027] The polymer latex employed in the invention in general has a Tg of —50 to 150 °C, preferably 5 to 100 °C,
`most preferably 10 to 80 °C.
`[0028] The polymer latex employed in the invention in general have an average particle size of less than 2 pm,
`preferably less than 0.5 pm, more preferably less than 0.25 pm.
`[0029] The polymer latex used in the invention is present in the ink jet ink generally from 0.1% to 20% by weight,
`preferably from 0.5% to 10% by weight.
`[0030]
`All monomer units in the polymer latex used in the invention may be hydrophobic. Alternatively, the polymer
`latex may contain at least one hydrophilic monomer unit. The content of hydrophilic monomer unit is less than 50 mole
`% of the total monomer units in the polymer latex, preferably less than 20 mole % of the total monomer units in the
`polymer latex, most preferably less than 5 mole % of the total monomer units in the polymer latex.
`[0031] The hydrophilic monomer unit in the polymer latex may be selected from the group consisting of acrylic acid,
`methacrylic acid, chloromethacrylic acid, maleic acid, allylamine, N,N—diethylallylamine, vinyl sulfonamide, sodium acr—
`ylate, sodium methacrylate, ammonium acrylate, ammonium methacrylate, acrylamidopropane—triethylammonium
`chloride, methacrylamidopropanetriethylammonium chloride, vinyl-pyridine hydrochloride, sodium vinyl phosphonate
`and sodium 1-methylvinylphosphonate, sodium vinyl sulfonate, sodium 1-methylvinyl-sulfonate and sodium styrenesul-
`fonate. The hydrophilic monomers can also be non-ionic, such as ethyoxytriethylene glycol methacrylate, methoxypol-
`yethylene oxide methacrylate, methoxypropylene oxide acrylate, polyethyleneoxide methacrylate, polyethylenoxide
`acrylate, N-vinyl pyrrolidone and the like.
`[0032] The aqueous carrier medium for the ink composition is water or a mixture of water and at least one water
`miscible co-solvent. Selection of a suitable mixture depends on requirements of the specific application, such as desired
`surface tension and viscosity, the selected pigment, drying time of the pigmented inkjet ink, and the type of paper onto
`which the ink will be printed. Representative examples of water-miscible co-solvents that may be selected include (1)
`alcohols, such as methyl alcohol, ethyl alcohol, n—propyl alcohol, isopropyl alcohol, n—butyl alcohol, sec—butyl alcohol,
`t—butyl alcohol, iso—butyl alcohol, furfuryl alcohol, and tetrahydrofurfuryl alcohol; (2) ketones or ketoalcohols such as
`acetone, methyl ethyl ketone and diacetone alcohol; (3) ethers, such as tetrahydrofuran and dioxane; (4) esters, such
`as ethyl acetate, ethyl lactate, ethylene carbonate and propylene carbonate; (5) polyhydric alcohols, such as ethylene
`glycol, diethylene glycol, triethylene glycol, tetraethylene glycol, propylene glycol, polyethylene glycol, glycerol, 2-me-
`thyl-2,4-pentanediol 1,2,6—hexanetriol and thioglycol; (6) lower alkyl mono- or di-ethers derived from alkylene glycols,
`such as ethylene glycol mono-methyl (or -ethyl) ether, diethylene glycol mono-methyl (or -ethyl) ether, diethylene glycol
`mono-butyl (or-ethyl) ether, propylene glycol mono-methyl (or-ethyl) ether, poly(ethylene glycol) butyl ether, triethylene
`glycol mono-methyl (or -ethyl) ether and diethylene glycol dimethyl (or -ethyl) ether; (7) nitrogen containing cyclic
`compounds, such as pyrrolidone, N-methyl-2-pyrrolidone, and 1,3-dimethyl-2-imidazolidinone; and (8) sulfur-contain-
`ing compounds such as dimethyl sulfoxide, 2,2'-thiodiethanol, and tetramethylene sulfone.
`[0033] The amount of aqueous carrier medium is in the range of approximately 70 to 99 weight %, preferably ap-
`proximately 90 to 98 weight %, based on the total weight of the ink. A mixture of water and a polyhydric alcohol, such
`as diethylene glycol, is useful as the aqueous carrier medium. In a preferred embodiment, the inks contain from about
`5 to about 60 weight % of water miscible organic solvent based on the total weight of the aqueous carrier medium.
`[0034]
`Jet velocity, separation length ofthe droplets, drop size and stream stability are greatly affected bythe surface
`tension and the viscosity of the ink. Pigmented inkjet inks suitable for use with inkjet printing systems should have a
`surface tension in the range of about 20 dynes/cm to about 80 dynes/cm and, more preferably, in the range 30 dynes/
`cm to about 50 dynes/cm. Control of surface tensions in aqueous inks is accomplished by additions of small amounts
`of surfactants. The level of surfactants to be used can be determined through simple trial and error experiments, usually
`about 0.1% to about 6%, preferably, 0.5% to about 4% by weight of the total ink composition. Anionic, cationic and
`nonionic surfactants may be selected from those disclosed in U. 8. Patents 5,324,349; 4,156,616 and 5,279,654 as
`well as many other surfactants known in the ink jet ink art. Commercial surfactants include the Surfynols® from Air
`Products; the Zonyls® from DuPont and the Fluorads® from 3M. Preferred surfactants can be silicon surfactants or
`fluorinated surfactants. Preferred silicon surfactants are available from BYK—Chemie as BYK surfactants, and from
`Crompton Corp, as Silwet® surfactants. Commercially available fluorinated surfactants can be the 20 nyls® from Du—
`Pont and the Fluorads® from 3M, they can be used alone or in combination with other surfactants.
`[0035] A humectant is added to the composition employed in the process of the invention to help prevent the ink
`from drying out or crusting in the orifices of the inkjet printhead. Polyhydric alcohols useful in the composition employed
`in the invention for this purpose include, for example, ethylene glycol, diethylene glycol, triethylene glycol, propylene
`glycol, tetraethylene glycol, polyethylene glycol, glycerol, 2-methyl-2,4-pentanediol, 1,2,6-hexanetriol and thioglycol.
`The humectant may be employed in a concentration of from about 10 to about 50 % by weight of the entire ink com-
`position.
`In a preferred embodiment, diethylene glycol or a mixture of glycerol and diethylene glycol is employed a
`concentration of between 10 and 20 % by weight of the entire ink composition.
`[0036] The ink has physical properties compatible with a wide range of ejecting conditions, i.e., driving voltages and
`pulse widths for thermal inkjet printing devices, driving frequencies of the piezo element for either a drop-on-demand
`
`10
`
`15
`
`20
`
`25
`
`30
`
`35
`
`4o
`
`45
`
`50
`
`55
`
`
`
`EP 1 403 341 A1
`
`device or a continuous device, and the shape and size of the nozzle.
`[0037] A penetrant (0-10% by weight) may also be added to the ink composition employed in the process of the
`invention to help the ink penetrate the receiving substrate, especially when the substrate is a highly sized paper. A
`preferred penetrant for the inks employed in the present invention is n-propanol at a final concentration of 1-6 % by
`weight.
`[0038] A biocide (0.01-1.0% by weight) may also be added to prevent unwanted microbial growth which may occur
`in the ink over time. A preferred biocide forthe inks employed in the present invention is Proxel® GXL (Zeneca Colours
`Co.) at a concentration of 0.05-0.5 °/o by weight. Additional additives which may optionally be present in ink jet inks
`include thickeners, conductivity enhancing agents, anti-kogation agents, pH buffering agents, drying agents, and de-
`foamers.
`
`lnkjet inks made using water—dispersible polymers employed in this invention are employed in inkjet printing
`[0039]
`wherein liquid ink drops are applied in a cont
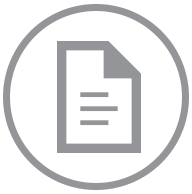
Accessing this document will incur an additional charge of $.
After purchase, you can access this document again without charge.
Accept $ ChargeStill Working On It
This document is taking longer than usual to download. This can happen if we need to contact the court directly to obtain the document and their servers are running slowly.
Give it another minute or two to complete, and then try the refresh button.
A few More Minutes ... Still Working
It can take up to 5 minutes for us to download a document if the court servers are running slowly.
Thank you for your continued patience.
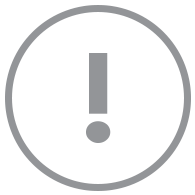
This document could not be displayed.
We could not find this document within its docket. Please go back to the docket page and check the link. If that does not work, go back to the docket and refresh it to pull the newest information.
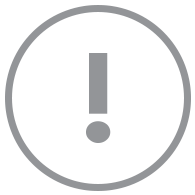
Your account does not support viewing this document.
You need a Paid Account to view this document. Click here to change your account type.
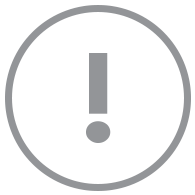
Your account does not support viewing this document.
Set your membership
status to view this document.
With a Docket Alarm membership, you'll
get a whole lot more, including:
- Up-to-date information for this case.
- Email alerts whenever there is an update.
- Full text search for other cases.
- Get email alerts whenever a new case matches your search.
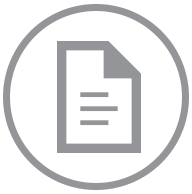
One Moment Please
The filing “” is large (MB) and is being downloaded.
Please refresh this page in a few minutes to see if the filing has been downloaded. The filing will also be emailed to you when the download completes.
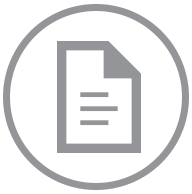
Your document is on its way!
If you do not receive the document in five minutes, contact support at support@docketalarm.com.
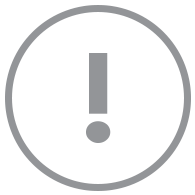
Sealed Document
We are unable to display this document, it may be under a court ordered seal.
If you have proper credentials to access the file, you may proceed directly to the court's system using your government issued username and password.
Access Government Site