`
`(I 9) World Intellectual Property Organization
`International Bureau
`
`(43) International Publication Date
`17 April 2003 (17.04.2003)
`
`
`
`(10) International Publication Number
`
`WO 03/031191 A2
`
`(51)
`
`International Patent Classification7:
`
`B41M 5/00
`
`(81)
`
`(21)
`
`International Application Number:
`
`PCT/US02/32452
`
`(22)
`
`International Filing Date: 9 October 2002 (09.10.2002)
`
`(25)
`
`Filing Language:
`
`(26)
`
`Publication Language:
`
`English
`
`English
`
`(84)
`
`(30)
`
`Priority Data:
`60/328,180
`
`9 October 2001 (09.10.2001)
`
`US
`
`(71)
`
`Applicant: KANZAKI SPECIALTY PAPERS INC.
`[ifUS]; 20 Cummings Street, Ware, MA 01082—2002
`(US).
`
`(72)
`
`Inventors: CUCH, Simon, R.; 15 Bent Tree Drive, East
`Longmeadow, MA 01028 (US). STEVENS, George, R.,
`Jr.; 28 Pomeroy Street, Wilbraham, MA 01095 (US).
`
`Designated States (national): AE, AG, AL, AM, AT, AU,
`AZ, BA, BB, BG, BR, BY, BZ, CA, CH, CN, CO, CR, CU,
`CZ, DE, DK, DM, DZ, EC, EE, ES, FI, GB, GD, GE, GH,
`GM, HR, HU, ID, IL, IN, IS, JP, KE, KG, KP, KR, KZ, LC,
`LK, LR, LS, LT, LU, LV, MA, MD, MG, MK, MN, MW,
`MX, MZ, NO, NZ, OM, PH, PL, PT, RO, RU, SD, SE, SG,
`SI, SK, SL, TJ, TM, TN, TR, TT, TZ, UA, UG, UZ, VN,
`YU, ZA, ZM, ZW.
`
`Designated States (regional): ARIPO patent (GH, GM,
`KE, LS, MW, MZ, SD, SL, SZ, TZ, UG, ZM, ZW),
`Eurasian patent (AM, AZ, BY, KG, KZ, MD, RU, TJ, TM),
`European patent (AT, BE, BG, CH, CY, CZ, DE, DK, EE,
`ES, FI, FR, GB, GR, IE, IT, LU, MC, NL, PT, SE, SK,
`TR), OAPI patent (BF, BJ, CF, CG, CI, CM, GA, GN, GQ,
`GW, ML, MR, NE, SN, TD, TG).
`
`Published:
`without international search report and to be republished
`upon receipt of that report
`
`(74)
`
`Agents: BONZAGNI, Mary, R. et al.; 171 Dwight Road,
`Suite 302, Longmeadow, MA 01106—1700 (US).
`
`For two-letter codes and other abbreviations, refer to the ”Guid-
`ance Notes on Codes andAbbreviations " appearing at the begin-
`ning ofeach regular issue ofthe PCT Gazette.
`
`(54) Title: AN INK JET RECORDING MATERIAL SUITABLE FOR USE IN WIDE FORMAT PRINTING APPLICATIONS
`
`03/031191A2
`
`(57) Abstract: An aqueous coating formulation for use in preparing ink jet recording materials is provided. The coating formula—
`tion, which employs porous pigments and/or metal oxide gels in combination with inorganic pigments (i.e., calcium carbonate and
`mixtures of calcium carbonate and alumina), has a relatively high binder—to—pigment dry weight ratio. An ink jet recording material
`0 prepared using such an aqueous coating formulation is also provided. The ink jet recording material demonstrates good printabil—
`ity and provides images having excellent water and humidity resistance and high image densities. In a preferred embodiment, the
`3
`inventive recording material further demonstrates good light or fade resistance.
`
`
`
`W0 03/031191
`
`PCT/US02/32452
`
`AN INK JET RECORDING MATERIAL SUITABLE FOR USE IN WIDE
`FORMAT PRINTING APPLICATIONS
`
`[0001]
`
`This application claims priority from US. Provisional Patent Application
`
`Serial No. 60/328,180, filed October 9, 2001.
`
`Related Application
`
`Field of the Invention
`
`[0002]
`
`The present invention generally relates to an aqueous coating formulation for
`
`use in preparing ink jet recording materials. The ink jet recording materials are suitable for
`
`use in wide format printing applications, demonstrate good printability and can provide
`
`images having excellent water and humidity resistance and high image densities.
`
`In a
`
`preferred embodiment, the inventive recording material further demonstrates good light or
`
`fade resistance.
`
`Background of the Invention
`
`[0003]
`
`Wide format ink jet recording materials are typically manufactured as wide
`
`rolls (i.e., greater than or equal to 24 inches in width), and are roll-fed into large printers for
`
`imaging. These materials are commonly used in commercial settings for applications
`
`including large advertisements, movie theater posters, outdoor signage and the like.
`
`[0004]
`
`Unlike narrow format ink jet recording materials, wide format materials,
`
`which are intended for long distance viewing, are required to meet more rigorous
`
`performance standards. For example, long distance viewing demands heightened acuity or
`
`sharpness in formed images and increased color gamut, background brightness and
`
`whiteness. In addition, wide format inkjet materials are ofien exposed to different use
`
`environments (e.g., outdoor use), which place additional demands on these materials in terms
`
`of color stability, resistance to light—induced fading, waterfastness, humidity resistance,
`
`abrasion resistance, and the like. It is further noted that wide format ink jet recording
`
`materials may encounter more ink per unit area when run through certain commercial printers
`
`and thus must effectively address problems with poor image quality, color bleed, smearing
`
`and cockle.
`
`[0005]
`
`Prior art attempts to meet these more rigorous performance requirements
`
`include the use of fluorescent whitening agents in ink jet coatings to increase the background
`
`brightness and whiteness of resulting recording materials. Fluorescent whitening agents,
`
`10
`
`15
`
`20
`
`25
`
`30
`
`
`
`W0 03/031191
`
`PCT/US02/32452
`
`however, degrade and, to a lesser extent, react with other coating components thereby
`
`contributing to the yellowing (i.e., poor light or fade resistance) of the resulting inkjet
`
`recording material.
`
`[0006]
`
`Efforts to minimize this effect include decreasing the level of fluorescent
`
`whitening agents in the inkjet coating. Unfortunately, the corresponding decrease in
`
`background brightness/whiteness renders such materials less suitable for use in wide format
`
`printing applications. Attempts to correct this deficiency by using superior or more
`
`expensive grades of exceptionally white and bright base paper, adversely impacts upon the
`
`economics of these materials.
`
`10
`
`[0007]
`
`US. Patent No. 6,129,785 to Schliesman et al. discloses a low pH aqueous
`
`suspension for application to optionally sized substrates, such as paper. The aqueous
`
`suspension comprises: absorptive silica pigment (e.g., a mixture ofz 75 % silica gel having a
`
`pore volume of 0.5 to 1.5 cc/g and 2 10 % alumina or alumina hydrate), a polyvinyl alcohol
`
`binder (e. g., low molecular weight, partially hydrolyzed polyvinyl alcohols) and a cationic
`
`fixing agent (e. g., polydiallyl dimethyl ammonium chloride), dispersed at low pH ranges of
`
`4.0 to 7.5. The acidic pH of the aqueous suspension is believed to enhance cationic function
`
`resulting in rapid dry times and improved ink hold out and color density.
`
`Recording materials prepared from low pH coating compositions, however,
`[0008]
`are less suitable for use in wide format printing applications where these materials tend to'be
`
`less stable and thus more susceptible to fading and yellowing. Moreover, images formed on
`
`the recording materials described in Schliesman er al. have image densities that are too low to
`
`render these materials suitable for use in wide format printing applications.
`
`[0009]
`
`In view of the above, a need exists for bright, white inkjet recording
`
`materials, which are not susceptible to fading or yellowing, and which provide images having
`
`high image densities.
`
`[0010]
`
`It is, therefore, an object of the present invention to provide such an ink jet
`
`recording material.
`
`[0011]
`
`It is a more particular object to provide an ink jet recording material suitable
`
`for use in wide format printing applications, which demonstrates good printability and which
`
`can provide images having excellent water and humidity resistance and high image densities.
`
`[0012]
`
`It is yet a more particular object of the present invention to provide an
`
`economical, bright, white inkjet recording material, which demonstrates good printability
`
`15
`
`20
`
`25
`
`30
`
`
`
`WO 03/031191
`
`PCT/US02/32452
`
`and good light or fade resistance, and which provides images having excellent water and
`
`humidity resistance and high image densities.
`
`SUMMARY OF THE INVENTION
`
`5
`
`[0013]
`
`The present invention therefore provides an aqueous coating formulation
`
`having a relatively high binder—to-pigment dry weight ratio, which comprises:
`
`10
`
`15
`
`(i)
`
`from about 45 to about 80 % by dry wt., based on the total dry
`
`weight of the coating formulation, of a pigment composition comprising from
`
`about 10 to about 90 % by dry wt., based on the total dry weight of the
`
`pigment composition, of a first pigment selected from the group of porous
`
`organic pigments, porous inorganic pigments, metal oxide gels and mixtures
`
`thereof, and from about 90 to about 10 % by dry wt., based on the total dry
`
`weight of the pigment composition, of a second pigment selected from the
`
`group of calcium carbonate and mixtures of calcium carbonate and alumina,
`
`wherein the sum of the pigment composition components total 100
`
`% by dry wt.;
`
`(ii)
`
`from about 10 to about 45 % by dry wt., based on the total dry
`
`weight of the coating formulation, of a water-soluble binder selected from the
`
`group of super, fully and partially hydrolyzed polyvinyl alcohols and mixtures
`
`20
`
`thereof and, optionally, one or more cationic acrylic resins;
`
`(iii)
`
`from about 1 to about 25 % by dry wt., based on the total dry
`
`weight of the coating formulation, of a cationic resin;
`
`(iv)
`
`an effective amount of an optionally fluorescent whitening agent; and
`
`(v)
`
`optionally, an effective amount of a blueing dye,
`
`25
`
`wherein, the sum of the coating formulation components total 100 % by dry
`
`wt.,
`
`wherein, the binder/pigment dry weight ratio in the coating formulation ranges
`
`from about 1:8 to about 1:1, and
`
`wherein, when an optionally fluorescent whitening agent and a blueing
`
`30
`
`dye are present
`
`in the coating formulation,
`
`the optionally fluorescent whitening
`
`agent/blueing dye dry weight ratio in the formulation ranges from about 1:1 to about
`
`1000:].
`
`[0014]
`
`The present invention also provides a method for preparing the aqueous
`
`coating formulation described above, which comprises:
`
`3
`
`
`
`W0 03/031191
`
`PCT/USOZ/32452
`
`(i)
`
`preparing an aqueous solution of the optionally fluorescent whitening
`
`agent; and then
`
`(ii)
`
`adding the remaining components in the following order of addition:
`
`cationic resin, first pigment, second pigment, remaining components.
`
`[0015]
`
`The present invention further provides an ink jet recording material, which
`
`comprises:
`
`(a)
`
`(b)
`
`a substrate;
`
`optionally, one or more undercoat layers located on the substrate,
`
`which is/are prepared using an aqueous coating formulation comprising:
`
`(i)
`
`(ii)
`
`(iii)
`
`(iv)
`
`one or more pigments;
`
`one or more binders;
`
`optionally, one or more dispersing agents; and
`
`an effective amount of an optionally fluorescent whitening
`
`agent
`
`wherein, the sum of the coating formulation components total 100 %
`
`by dry wt., and
`
`wherein, the pigment/binder dry weight ratio in the coating formulation
`
`ranges from about 1:1 to about 20:]; and
`
`(0)
`
`one or more ink jet receptive layers located on the optional undercoat
`
`layer(s) and/or on the substrate, which is/are prepared using the aqueous
`
`coating formulation described above.
`
`[0016]
`
`The foregoing and other features and advantages of the present invention will
`
`become more apparent from the following description.
`
`DETAILED DESCRIPTION OF THE INVENTION
`
`[0017]
`
`Although the present inventive inkjet recording material will be described
`
`herein mainly in reference to wide format printing applications, it is not so limited. The
`
`inventive material can be used in any application, including narrow format printing
`
`applications, where good printability and sharp, water and humidity resistant images, are
`
`10
`
`15
`
`20
`
`25
`
`30
`
`desired.
`
`[0018]
`
`As is well known to those skilled in the art, high binder-to-pigment ratios in
`
`inkjet coating formulations limit the machine coatability of such coating formulations and
`
`serve to reduce the maximum ink absorbency, interfere with the ink drying time and reduce
`
`the maximum coat weight of the resulting inkjet layer. By way of the present invention, it
`
`4
`
`
`
`W0 03/031191
`
`PCT/USOZ/32452
`
`has been discovered that coating formulations having relatively high binder-to-pigment dry
`
`weight ratios, which employ porous pigments and/or metal oxide gels in combination with
`
`inorganic pigments (i.e., calcium carbonate and mixtures of calcium carbonate and alumina)
`
`produce inkjet receptive layers which demonstrate good printability and which provide
`
`images having excellent water and humidity resistance and high image densities.
`
`[0019]
`
`Suitable porous organic pigments for use as the first pigment in the pigment
`
`composition of the coating formulation used to prepare the ink jet receptive layer of the
`
`present invention include acrylic resins such as polymethyl methacrylate, polymethylacrylate,
`
`polyacrylonitrile, poly(vinylpolypyrrolidone), styrene resins such as polystyrene,
`
`.
`
`polymethylstyrene and the like, as well as styrene-acrylic resins, urea-formaldehyde resins,
`
`polyvinyl chlorides, polycarbonates, etc. Suitable porous inorganic pigments include porous
`
`alumina, porous sodium aluminosilicate, porous calcium carbonate, porous clays, porous
`
`magnesium carbonate, porous synthetic amorphous silica and the like.
`
`[0020]
`
`The average diameter of pores in the porous organic and inorganic pigments is
`
`preferably from about 1 to about 800 nanometers, while the volume of pores in these
`
`pigments is preferably from about 0.4 to about 3.0 cubic centimeters per gram (cc/g).
`
`[0021]
`
`Metal oxide gels, suitable for use as the first pigment in the pigment
`
`composition of the subject coating formulation include alumina gels, silica gels, polymeric
`
`gels such as melamine formaldehyde (M-F) gels, phenol-furfiiral (P-F) gels, resorcinol-
`
`formaldehyde (R-F) gels, urea-formaldehyde (U-F) gels, titania gels and the like.
`
`[0022]
`
`In a preferred embodiment, the first pigment is a metal oxide gel.
`
`In yet a
`
`more preferred embodiment, the metal oxide gel is a silica gel having a surface area ranging
`
`from about 200 to about 800 square meters per gram (mZ/g), a pore volume ranging from
`
`about 0.4 to about 3.0 cc/g, an average particle size ranging from about 1 to about 17 [A and a
`
`pH ranging from about 2.5 to about 10.5.
`
`[0023]
`
`Specific preferred examples of silica gels having surface areas, pore volumes,
`
`average particle sizes and pHs falling within the ranges specified above, include SYLOID
`
`620 and 234 wax-free silica gels, SYLOID 7000 wax surface-treated silica gels and SYLOID
`
`74 (grade 4500, 5500 and 6500) silica gels, marketed by Grace Davison, W.R. Grace & Co.,
`
`7500 Grace Drive, Columbia, MD 21044 ("Grace Davison").
`
`[0024]
`
`The first pigment is present in the pigment composition in an amount ranging
`
`from about 10 to about 90 % by dry wt., preferably from about 20 to about 80 % by dry wt.,
`
`based on the total dry weight of the pigment composition. The present inventor has found
`
`that if the first pigment is employed in an amount which exceeds 90 % by dry wt., a decrease
`5
`
`10
`
`15
`
`20
`
`25
`
`30
`
`
`
`WO 03/031191
`
`PCT/US02/32452
`
`in optical or image densities will be observed, and if the first pigment is employed in an
`
`amount which falls below 10 % by dry wt., an increase in the degree of wicking or spread of
`
`water or ink will also be observed.
`
`[0025]
`
`The pigment composition of the coating formulation of the present invention
`
`also contains a porous or non-porous second pigment which appears to aid in the preservation
`
`or maintenance of an open structure in the ink jet receptive layer, upon drying, even at high
`
`binder-to—pigment dry weight ratios. The second pigment is selected from the group
`
`including calcium carbonate and mixtures of calcium carbonate and alumina.
`
`[0026]
`
`In a preferred embodiment, the second pigment is calcium carbonate and,
`
`more preferably, is a precipitated calcium carbonate (PCC) pigment possessing a surface area
`
`ranging from about 10 to about 300 square meters per gram (ml/g), a particle size ranging
`
`from about 0.1 to about 5 ,LL and rheology of a thixotropic nature thus facilitating application
`
`of the resulting coating formulation under high shear conditions such as air knife or blade
`coaters.
`
`[0027]
`
`Specific examples of PCCs possessing rheoiogy of a thixotropic nature are
`
`available from Minerals Technologies Inc., 35 Highland Avenue, Bethlehem, PA 18017,
`
`under the trade designation JETCOAT 30 precipitated calcium carbonate, and from Fitz
`
`Chem Corporation, 185 Industrial Drive, Elmhurst, IL 60126-1601, under the trade
`
`designation MAGNUM GLOSS precipitated calcium carbonate.
`
`[0028]
`
`In another preferred embodiment, the second pigment is a mixture comprising
`
`from about 60 to about 99 % by dry wt. (and more preferably from about 80 to about 95 % by
`
`dry wt.) of calcium carbonate and from about 40 to about 1 % by dry wt. (and more
`
`preferably from about 20 to about 5 % by dry wt.) of an alumina pigment.
`
`[0029]
`
`Anhydrous alumina and alumina hydrate pigments are preferred. As the
`
`an hydrous alumina there may be used any of the various crystalline alumina such as oc-
`
`alumina, B-alumina and y-alumina. As the alumina hydrate there may be used either alumina
`
`monohydrate or trihydrate. Examples of the alumina monohydrate include pseudoboehmite,
`
`boehmite and diaspore. Examples of the alumina trihydrate include gibbsite and bayerite.
`
`Preferred among these alumina pigments is alumina trihydrate.
`
`[0030]
`
`The average particle diameter of the alumina pigment to be used herein is
`
`preferably from about 0.1 to about 3.0 M, more preferably from about 0.4 to about 2.0 it. The
`
`alumina pigment to be used herein may or may not be porous but is preferably porous. The
`
`average diameter of pores in the particulate alumina pigment is preferably from about 0.5 to
`
`10
`
`15
`
`20
`
`25
`
`30
`
`
`
`W0 03/031191
`
`PCT/US02/‘32452
`
`about 300 nanometers. The volume of pores in the particulate alumina pigment is preferably
`
`from about 0.1 to about 2.1 cc/g.
`
`[0031]
`
`The second pigment is present in the pigment composition in an amount
`
`ranging from 90 to about 10 % by dry wt., preferably from about 80 to about 20 % by dry wt.,
`
`based on the total dry weight of the pigment composition. The present inventor has found
`
`that if the second pigment is employed in an amount below 10 % by dry wt., a decrease in
`
`optical or image densities will be observed, and if the second pigment is employed in an
`
`amount above 90 % by dry wt., an increase in the degree of wicking will also be observed.
`
`[0032]
`
`The subject pigment composition may contain additional components
`
`including, but not limited to, barium sulfate, clays, talc, titanium dioxide, zinc oxide and
`
`mixtures thereof.
`
`[0033]
`
`The pigment composition is present in the coating formulation in an amount
`
`ranging from about 45 to about 80 % by dry wt., preferably from about 50 to about 75 % by
`
`dry wt., based on the total dry weight of the coating formulation.
`
`[0034]
`
`The water—soluble binder ofthe coating formulation ofthe present invention is
`
`selected from the group consisting of super, fully and partially hydrolyzed polyvinyl alcohols
`
`and mixtures thereof and, optionally, one or more cationic acrylic resins.
`
`[0035]
`
`The term "super hydrolyzed," as used herein, is intended to refer to those
`
`polyvinyl alcohols having a % hydrolysis ranging from about 99 to about 100, while the term
`
`"fully hydrolyzed" refers to a % hydrolysis ranging from about 97 to about 99. The term
`
`"partially hydrolyzed," on the other hand, denotes a polyvinyl alcohol having a %hydrolysis
`
`of from about 70 to about 96.
`
`[0036]
`
`The super hydrolyzed polyvinyl alcohols of the present invention preferably
`
`have a % hydrolysis of from about 99.3 to about 99.6, while the fully hydrolyzed polyvinyl
`
`alcohols preferably have a % hydrolysis of from about 98 to about 98.8. The partially
`
`hydrolyzed polyvinyl alcohols preferably have a % hydrolysis of from about 84 to about 92.
`
`[0037]
`
`The super, fully and partially hydrolyzed polyvinyl alcohols of the water-
`
`soluble binder have medium-to-low molecular weights which range from about 5,000 to
`
`about 186,000 (preferably from about 13,000 to about 150,000) and may be modified by
`
`adding a cation thereto. More specifically, the polyvinyl alcohols may be modified by
`
`silanol, carboxy and/0r quaternary amine groups.
`
`[0038]
`
`Specific preferred examples of super, fully and partially hydrolyzed, medium-
`
`to-low molecular weight, polyvinyl alcohols are available from Air Products and Chemicals,
`
`Inc., 7201 Hamilton Blvd., Allentown, PA 18196-1501 ("Air Products") and are sold under
`
`7
`
`10
`
`15
`
`20
`
`25
`
`30
`
`
`
`WO 03/031191
`
`PCT/USO2/32452
`
`the trade designations AIRVOL 125 super hydrolyzed, medium molecular weight, polyvinyl
`
`alcohol, AIRVOL 325 fully hydrolyzed, medium molecular weight, polyvinyl alcohol,
`
`AIRVOL 523 partially hydrolyzed, medium molecular weight, polyvinyl alcohol and
`
`AIRVOL 205 partially hydrolyzed, low molecular weight, polyvinyl alcohol.
`
`[0039]
`
`The water-soluble binder may fiirther comprise from about 1 to about 50% by
`
`dry wt., based on the total dry weight of the water-soluble binder, of a cationic acrylic resin.
`
`The cationic acrylic resin serves to fix ink jet dyes and appears to enhance the color range or
`
`gamut of printed media. Suitable examples of such cationic acrylic resins include cationic
`
`styrene-acrylic resins, cationic styrene—acrylic copolymers, amide-modified cationic styrene-
`
`acrylic resins and cationic vinyl acrylic resins. Preferred cationic acrylic resins are cationic
`
`styrene-acrylic copolymers, which are available from Westvaco Corporation, Chemical
`
`Division, P.O. Box 70848, Charlestown Heights, SC 29415, and are sold under the trade
`
`designation TRUDOT P2605 cationic styrene-acrylic copolymers.
`
`[0040]
`
`The water-soluble binder may contain additional components (e. g., alginate,
`
`biocides, casein, cellulose derivatives, CMC, hydroxymethyl cellulose, hydroxypropyl
`
`cellulose, water soluble gums, latex, amphoteric latex, maleic anhydride resins, melamine
`
`resins, polyacrylamide resins, polyester resins, polyvinyl acetate, polyvinyl pyrrolidone,
`
`polyvinyl pyrrolidone vinyl acetate copolymers, modified starch, ethoxylated starch, cationic
`I starch, oxidized starch and blends thereof) provided any such additional components(s) dOes
`
`not adversely impact upon the desirable properties of the binder.
`
`[0041]
`
`In a more preferred embodiment, the water-soluble binder comprises:
`
`(a)
`
`from about 10 to about 90% by dry wt. (more preferably from about 20
`
`to about 80 % by dry wt.) of a super hydrolyzed, medium viscosity polyvinyl
`
`alcohol;
`
`(b)
`
`from about 10 to about 70% by dry wt. (more preferably from about 15
`
`to about 65 % by dry wt.) ofa partially hydrolyzed, medium viscosity
`
`polyvinyl alcohol; and
`
`(c)
`
`from about 0 to about 20% by dry wt. (more preferably from about 5 to
`
`about 15 % by dry wt.) ofa partially hydrolyzed, low viscosity polyvinyl
`
`alcohol.
`
`[0042]
`
`The water-soluble binder preferably has a medium—to—low Viscosity. More
`
`specifically, the binder has a preferred viscosity ranging from about 3 to about 40 centipoise
`
`10
`
`15
`
`20
`
`25
`
`30
`
`
`
`WO 03/031191
`
`PCT/USO2/32452
`
`(cps), as measured by a Brookfield Viscosimeter, model number DV-II+, using a 4 %
`
`polyvinyl alcohol aqueous solution at 20°C.
`
`[0043]
`
`The binder/pigment dry weight ratio in the coating formulation used to prepare
`
`the ink jet receptive layer of the present invention ranges from about 1:8 to about 1:],
`
`preferably ranges from about 1:6 to about 1:15, and more preferably ranges from about 1: 2.8
`
`to about 121.8.
`
`[0044]
`
`The present inventor has found that if the binder/pigment ratio exceeds 1:1
`
`(i.e., the binder is present in an amount which is greater than the amount of pigment), an
`
`increase in the degree of wicking and intercolor bleeding will be observed, while if the ratio
`
`falls below 1:8 (i. e., the binder is present in an amount which is less than 12.5 % ofthe
`
`amount of pigment), a decrease in optical or image densities will be observed.
`
`[0045]
`
`The water-soluble binder is present in the coating formulation in an amount
`
`ranging from about 10 to about 45 % by dry wt., preferably from about 15 to about 40 % by
`
`wt., based on the total dry weight of the coating formulation.
`
`[0046]
`
`The cationic resin of the coating formulation of the present invention serves as
`
`a fixing agent of ink and improves the fixing of recorded images and water resistance.
`
`[0047]
`
`Preferred cationic resins include polyvinyl benzyl trimethyl ammonium
`
`chloride, polydiallyl dimethyl ammonium chloride, polymethacryloxyethyl hydroxy
`
`ethyldiammonium chloride, quaternary acrylic copolymer latex, amidocpichlohydrin
`
`copolymer, dimethylaminoethylmethacrylate copolymer, vinyl pyrrolidone
`
`dimethylaminoethylmethacrylate copolymer, polyallylamine, polyvinylamine, Vinyl amine
`
`acrylonitrile copolymers, polyalkylene imine polymers, polyalkylene polyamine polymers,
`
`polyalkylene polyamide dicyandiamide copolymers, polyamide dicyandiamide copolymers,
`
`quaternary ammonium polymers and blends thereof. In a preferred embodiment, the cationic
`
`resin is a quaternary ammonium polymer and, more preferably, is polydiallyl dimethyl
`
`ammonium chloride marketed by Calgon Corporation, 2015 Christine Drive, Harleysville,
`
`PA 19438 under the trade designation CP-1030.
`
`[0048]
`
`The cationic resin is present in the coating formulation in an amount ranging
`
`from about 1 to about 25 % by dry wt., preferably from about 3 to about 15 % by dry wt.,
`
`based on the total dry weight of the coating formulation. If the cationic resin is present in an
`
`amount below 1 % by dry wt., the water resistance of the composition is very poor, and if the
`
`cationic resin is present in an amount above 25 % by dry wt., printed image quality is
`
`adversely affected.
`
`10
`
`15
`
`20
`
`25
`
`30
`
`
`
`WO 03/031191
`
`PCT/USO2/32452
`
`[0049]
`
`The optionally fluorescent whitening agent is added to the coating formulation
`
`of the present invention to increase the whiteness, brightness and bluish shade of the resulting
`
`inkjet recording material. Examples of such whitening agents include disulfonated,
`
`tetrasulfonated and hexasulfonated stilbene derivatives. In a preferred embodiment, the agent
`
`is a hexasulfonated stilbene derivative, which is available from Ciba Specialty Chemical
`
`Corp., 540 White Plains Road, Tarrytown, NY 10591 ("Ciba Specialty"), under the product
`
`designation TTNOPAL ABP—A, and is present in an amount ranging from about 0.01 to about
`
`1.5 % by dry wt., preferably from about 0.1 to about 0.8 % by dry wt., based on the total dry
`
`weight of the coating formulation.
`
`[0050]
`
`The whitening agent may employ a fluorescing agent, which absorbs energy in
`
`the UV region and emits light largely in the blue region.
`
`[0051]
`
`In a preferred embodiment, the coating formulation further comprises from
`
`about 0.001 to about 0.05 % by dry wt., preferably from about 0.002 to about 0.007 % by dry
`
`wt., based on the total dry weight of the coating formulation, of a blueing dye. The blueing
`
`dye serves to increase the whiteness of the ink jet recording material. Suitable examples of
`
`such dyes include cobalt blue, copper phthalocyanine, metal—free phthalocyanine, oxide
`
`cobalt phosphate, dye complex salts (i.e., dyes precipitated with phosphomolybdic,
`
`phosphotungstic, phospho-molybdotungstic acids), quinacridone pigments, ultramarine blue
`
`and mixtures thereof. Preferred blueing dyes have good lightfastness and are available from:
`
`Ciba Specialty, under the product designations IRGALITE BLUE RL PST copper
`
`phthalocyanine dyestuff dispersion and IRGALITE VIOLET RM and IRGALITE RED B-F L
`
`arylamide pigment dispersions; and Bayer Industrial Chemicals, under the product
`
`designations PONOLITI-I RED WC quinacridone pigment dispersion and PONOLITH BLUE
`
`RDC copper phthalocyanine pigment dispersion.
`
`[0052]
`
`It is noted that when both the optionally fluorescent whitening agent and the
`
`blueing dye are present in the coating formulation, the whitening agent/blueing dye weight
`
`ratio preferably ranges from about 1:1 to about 1000:], and more preferably ranges from
`
`about 2:1 to about 800:1. If the whitening agent/blueing dye ratio falls below 1:], the
`
`resulting inkjet recording material displays lower brightness and whiteness, and if the ratio
`
`exceeds 1000:] , the resulting recording materials demonstrates poor lightfastness.
`
`[0053]
`
`In addition to the above components, the coating formulation of the present
`
`invention can advantageously contain other additives such as antioxidants, antistatic agents,
`
`crosslinking agents, defoaming agents, dispersing agents, fragrances, mold inhibitors, slip
`
`10
`
`15
`
`20
`
`25
`
`30
`
`10
`
`
`
`WO 03/031191
`
`PCT/USO2/32452
`
`5
`
`10
`
`15
`
`20
`
`agents, UV absorbers and wetting agents. However, some such additives may adversely
`
`impact upon the desirable properties of the resulting ink jet receptive layer.
`
`[0054]
`
`In a most preferred embodiment, the coating formulation used to prepare the
`
`inkjet receptive layer of the present invention comprises:
`
`(1)
`
`from about 50 to about 75 % by dry wt. of a pigment composition
`
`comprising:
`
`(a)
`
`from about 20 to about 80 % by dry wt., based on the total
`
`dry weight of the pigment composition, of silica gel; and
`
`(b)
`
`from about 80 to about 20 % by dry wt., based on the total
`
`dry weight of the pigment composition, of precipitated calcium
`
`carbonate,
`
`(2)
`
`from about 15 to about 40 % by dry wt. of a water-soluble binder
`
`comprising:
`
`(a)
`
`from about 20 to about 70 % by dry wt., based on the total dry
`
`weight ofthe binder, ofa super and/or fully hydrolyzed, medium
`
`molecular weight polyvinyl alcohol;
`
`(b)
`
`from about 70 to about 25 % by dry wt., based on the total dry
`
`weight of the binder, of a partially hydrolyzed, medium-to—low
`
`molecular weight, polyvinyl alcohol; and
`
`(c)
`
`from about 5 to about 35 % by dry wt., based on the total dry
`
`weight of the binder, of a cationic styrene acrylic copolymer,
`
`(3)
`
`from about 3 to about 15 % by dry wt. ofpolydiallyl dimethyl
`
`ammonium chloride,
`
`(4)
`
`from about 0.01 to about 1.5 % by dry wt. of a hexasulfonated
`
`25
`
`stilbene derivative, and
`
`(5)
`
`from about 0.001 to about 0.05 % by dry wt. of a phthalocyanine dye
`
`stuff,
`
`wherein, the binder/pigment composition weight ratio ranges from about
`
`1:6 to about 1:15, and
`
`30
`
`wherein, the whitening agent/blueing dye weight ratio ranges from about
`
`2:1 to about 800:1.
`
`[0055]
`
`The inkjet receptive layer coating formulation is made by mixing the
`
`components with water so as to obtain an aqueous composition having a solids content
`
`ranging from about 15 to about 35 % (preferably from about 15 to about 20 %), based on the
`
`1 1
`
`
`
`WO 03/031191
`
`PCT/US02/32452
`
`total dry weight of the coating formulation. The pH of the aqueous composition is between 6
`
`and 10, and preferably is between 6.5 and 8.
`
`[0056]
`
`In a preferred embodiment, the coating formulation is made by first preparing
`
`an aqueous solution or emulsion of the optionally fluorescent Whitening agent and then by
`
`adding the remaining components in the following sequence: cationic resin (e.g., polydiallyl
`
`dimethyl ammonium chloride), first pigment (e.g., silica gel), second pigment (e.g., PCC),
`
`remaining ingredients or components. This sequence of addition is preferred where the
`
`cationic resin is somewhat incompatible with the optionally fluorescent whitening agent but
`
`aids in the dispersion ofthe first pigment.
`
`10
`
`15
`
`[0057]
`
`In order to avoid degradation in ink absorptivity caused by the use of
`
`excessive amounts of coating,
`
`it
`
`is preferred that the ink jet coating composition of the
`
`present invention be applied so as to achieve an average coat weight that ranges from about 2
`
`to about 14 g/m2, based on the total dry weight of the coating composition.
`
`[0058]
`
`Substrates useful in the present invention are coatable substrates, examples of
`
`which include, without limitation, paper, cardboard, corrugated board, plastic film, metal
`
`film, foil face stocks and label stocks.
`
`[0059]
`
`The substrate preferably has a thickness ranging from about 50 to about 300 a,
`
`a basis weight ranging from about 40 to about 240 grams per square meter (g/mz), a surface
`
`smoothness of from about 15 to about 150 Bekk seconds and a Cobb sizing of from about 25
`
`20
`
`to about 150 g/m2.
`
`25
`
`30
`
`[0060]
`
`The optional undercoat layer of the inkjet recording material of the present
`
`invention serves to reduce cockling and enhance or improve the whiteness, brightness,
`
`opacity, inkjet ink strike-through and lightfastness of the resulting inkjet recording material.
`
`[0061]
`
`When an undercoat layer is employed, the amount of optionally fluorescent
`
`whitening agent in the undercoat layer is greater than the amount of whitening agent in the
`
`ink receptive layer.
`
`[0062
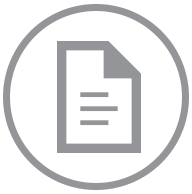
Accessing this document will incur an additional charge of $.
After purchase, you can access this document again without charge.
Accept $ ChargeStill Working On It
This document is taking longer than usual to download. This can happen if we need to contact the court directly to obtain the document and their servers are running slowly.
Give it another minute or two to complete, and then try the refresh button.
A few More Minutes ... Still Working
It can take up to 5 minutes for us to download a document if the court servers are running slowly.
Thank you for your continued patience.
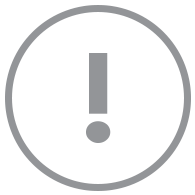
This document could not be displayed.
We could not find this document within its docket. Please go back to the docket page and check the link. If that does not work, go back to the docket and refresh it to pull the newest information.
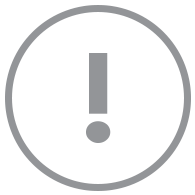
Your account does not support viewing this document.
You need a Paid Account to view this document. Click here to change your account type.
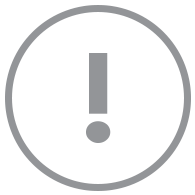
Your account does not support viewing this document.
Set your membership
status to view this document.
With a Docket Alarm membership, you'll
get a whole lot more, including:
- Up-to-date information for this case.
- Email alerts whenever there is an update.
- Full text search for other cases.
- Get email alerts whenever a new case matches your search.
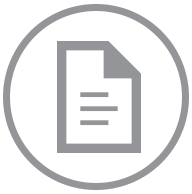
One Moment Please
The filing “” is large (MB) and is being downloaded.
Please refresh this page in a few minutes to see if the filing has been downloaded. The filing will also be emailed to you when the download completes.
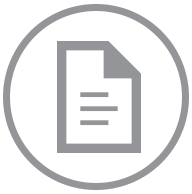
Your document is on its way!
If you do not receive the document in five minutes, contact support at support@docketalarm.com.
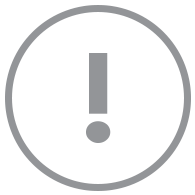
Sealed Document
We are unable to display this document, it may be under a court ordered seal.
If you have proper credentials to access the file, you may proceed directly to the court's system using your government issued username and password.
Access Government Site