`D'
`Igl a
`(DAS)
`
`_
`S
`66655 el‘Vlce
`
`WIPO
`
`WORLD
`INTELLECTUAL PROPERTY
`ORGANIZATION
`
`CERTIFICATE OF AVAILABILITY OF A CERTIFIED PATENT DOCUMENT IN A
`
`DIGITAL LIBRARY
`
`The International Bureau certifies that a copy of the patent application indicated
`below has been available to the WIPO Digital Access Service since the date of
`availability indicated, and that the patent application has been available to the
`indicated Office(s) as of the date specified following the relevant Office code:
`
`Document details:
`
`Country/Office: G B
`
`Filing date: 28 Jul 2016 (28.07.2016)
`
`Application number: 16130619
`
`Date of availability of document:
`
`08 Sep 2016 (08.09.2016)
`
`The following Offices can retrieve this document by using the access code:
`
`JP, US, SE, NZ, KR, GB, AU, ES, IB, EE, CN, MA, Fl
`
`Date of issue of this certificate:
`
`22 Jun 2017 (22.06.2017)
`
`34, ohemin des Colombettes
`
`
`
`
`
`Concept House
`Cardiff Road
`
`Newport
`South Wales
`
`NPlO 8QQ
`
`Certified Office Copy
`
`1, the undersigned, being an officer duly authorised in accordance with Section 74(1) and (4) of
`the Deregulation & Contracting Out Act 1994, to sign and issue certificates on behalf of the
`Comptroller—General, hereby certify that annexed hereto is a true copy of the documents as
`originally filed in connection with patent application GBl6l306l .9 on 28 July 2016 and as
`stored electronically on the Patents Electronic Case file System.
`
`The Patents Electronic Case—file System is compliant with British Standard BS10008 —
`Evidential weight and legal admissibility of information stored electronically and 1S015801 -
`Electronic imaging — information stored electronically, recommendations for trustworthiness and
`reliability.
`
`In accordance with the Patents (Companies Re-registration) Rules 1982, if a company named in
`this certificate and any accompanying documents has re-registered under the Companies Act
`1980 with the same name as that with which it was registered immediately before re-registration
`save for the substitution as, or inclusion as, the last part of the name of the words "public limited
`company" or their equivalents in Welsh, references to the name of the company in this certificate
`and any accompanying documents shall be treated as references to the name with which it is so
`re—registered.
`
`In accordance with the rules, the words "public limited company” may be replaced by p.l.c., plc,
`P.L.C. or PLC.
`
`Re-registration under the Companies Act does not constitute a new legal entity but merely
`subjects the company to certain additional company law rules.
`
`Signed A HAYES
`
`Dated 2 August 2016
`
`
`
`
`
` .fi,
`intellectual
`
`Property
`OffiCe
`
`Patents Form 1
`Patents Act 1977 (Rule 12)
`
`Request for grant of a patent
`
`.
`.
`Application number
`1. Your reference
`
`GB 1613061 _9
`
`2.
`
`Full name, address and postcode of the applicant or of
`each applicant
`
`1200203669
`1016017671 D01063
`28/07/2016 230.00 DepositAccount
`
`Concept House
`Cardiff Road
`Newport
`South Wales
`NP10 SQQ
`
`RL/PX215464GB
`
`CROWN PACKAGING TECHNOLOGY, INC.
`11535 South Central Avenue
`Alsip 60803-2599
`Illinois
`United States of America
`
`Patents ADP number (if you know it)
`
`3. Title of the invention
`RADIAL OFFSET MONITOR
`
`MARKS & CLERK LLP
`4. Name of your agent (ifyou have one)
`“Address for service" to which all correspondence should MARKS & CLERK LLP
`be sent. This may be in the European Economic area or
`Fletcher House (2nd Floor)
`Channel Islands (see warning note below)
`Heatley Road Oxford Science Park
`(including the postcode)
`Oxford OX4 4GE
`Oxfordshire
`
`United Kingdom
`
`Patents ADP number (if you know it)
`
`5. Priority declaration: Are you claiming priority from one or
`more earlier-filed patent applications? If so, please give
`details ofthe application(s)
`
`Country
`
`Application number
`
`Date of filing
`
`PDAS Access Code
`
`6. Divisionals etc: Is this application a divisional application,
`or being made following resolution of an entitlement
`dispute about an earlier application. If so, please give the
`application number and filing date ofthe earlier
`application
`
`7.
`
`lnventorship: (Inventors must be individuals not
`companies)
`
`Are all the applicants named above also inventors?
`
`8. Are you paying the application fee with this form?
`
`No
`
`Yes
`
`Number of earlier UK
`app'mat'on
`
`Date of filing
`(day/month Wear)
`
`(REV DEC07)
`Intellectual Property Office is an operating name ofthe Patent Office
`
`Patents Form 1(e)
`https://www.gov.uk/ipo
`
`
`
`Patents Form 1
`
`9. Accompanying documents: please enterthe number of
`pages of each item accompanying this form.
`
`Continuation sheets of this form
`
`Description:
`
`1 3
`
`Claim(s):
`
`Abstract:
`
`2
`
`1
`
`Drawing(s):
`
`14
`
`If you are n_ot filing a description, please give details of
`the previous application you are going to rely upon
`
`
`
`Application number Date of filingCountry PDAS Access Code
`
`
`
`
`
`10. If you are also filing any of the following, state how many
`against each item.
`
`Priority documents:
`
`0
`
`Statement of inventorship and right to grant of a patent
`(Patents Form 7):
`
`Request for search (Patents Form 9A):
`
`Request for a substantive examination (Patents Form 10):
`
`1
`
`1
`
`1
`
`Pre-conversion Archive
`Any other documents (please specify):
`
`PDAS Registration Form
`
`11. WVe request the grant of a patent on the basis of this application.
`
`Signature: Subject: Robert Lind 364; Issuer: European Date:
`Patent Office, European Patent Office CA
`GZ
`
`28 Jul 2016
`
`12. Name, e-mail address, telephone, fax and/or mobile
`number, if any, of a contact point for the applicant
`
`LIND, Dr Robert
`Email: oxford@marks-clerk.com
`Telephone: +44(0)1865 397900
`Fax: +44(0)1865 397919
`
`Warning
`After an application for a patent has been filed, the Comptroller will consider whether publication or communication of the
`invention should be prohibited or restricted under section 22 of the Patents Act 1977. You will be informed if it is necessary to
`prohibit or restrict your invention in this way. Furthermore, if you are resident in the United Kingdom and your application contains
`information which relates to military technology, or would be prejudicial to national security orthe safety of the public, section 23 of
`the Patents Act 1977 prohibits you from applying for a patent abroad without first getting written permission from the Office unless
`an application has been filed at least 6 weeks beforehand in the United Kingdom for a patent for the same invention and either no
`direction prohibiting publication or communication has been given, or any such direction has been revoked. Until such time or until
`the revocation of any direction, for any such application the address for service referred to at part 4 above must be in the United
`Kingdom.
`
`Although you may have an address for service in the Channel Islands, any agent instructed to act for you must reside or have a
`place of business in the European Economic Area or Isle of Man.
`
`(REV DECO7)
`
`Patents Form 1(e)
`
`
`
`M&C PX215464GB
`
`Technical Field
`
`RADIAL OFFSET MONITOR
`
`The present invention relates to a radial offset monitor, and in particular, though not
`
`necessarily, to a can bodymaker comprising a radial offset monitor. The invention also
`
`relates to a method of detecting a radial offset of a bodymaker ram and/or punch.
`
`1O
`
`Background
`
`15
`
`20
`
`25
`
`30
`
`In known bodymakers for the production of thin-walled metal can bodies by a “drawing
`
`and wall—ironing” (DWI) process, metal cups are fed to the bodymaker and carried by a
`
`punch on the end of a ram through a series of dies to produce a can body of the
`
`desired size and thickness. The series of dies may include a redraw die for reducing
`
`the diameter of the cup and lengthening its sidewall, and one or more ironing dies for
`
`wall-ironing the cup into a can body. The area or cradle of the bodymaker frame within
`
`which the dies are located is known as the “toolpack”. The can body carried on the
`
`punch may ultimately contact a bottom forming tool or “domer” so as to form a shape
`
`such as a dome on the base of the can. An exemplary bodymaker is described in
`W09934942.
`
`When setting up a can bodymaker, the ram and its drive components are typically fixed
`
`in place on the bodymaker frame. This aligns the axis of the ram with the main axis of
`
`the bodymaker. The other components, including for example the redraw and ironing
`
`dies and domer, are then aligned with the ram.
`
`Over time, frictional forces and general wear will cause the alignment of the ram to vary
`
`slightly.
`
`In addition, a high speed reciprocating ram is generally subject to at least
`
`some vibration, due to the impact of the ram on the can body and to the variable
`
`“droop” of the ram as it moves from and to its fully-extended position. When the ram
`
`carries the can body into contact with the domer, any misalignment can lead to the can
`
`body end splitting, particularly where the can body is aluminium.
`
`If the misalignment is
`
`slight, the split (sometimes known as a “smile”) may not be immediately visible to the
`
`33594726—1-SBRADLEY
`
`
`
`M&C PX215464GB
`
`2
`
`naked eye, and the split may lead to the can bursting once the can body has been
`
`filled. This may not occur until the filled can has been purchased.
`
`Alignment procedures for known bodymakers are complex and require significant skill
`
`to ensure that the machines can be operated safely and efficiently. A typical method of
`
`aligning the ram of a bodymaker comprises halting the production line and inserting two
`
`gauge rings comprising sensors into the bodymaker toolpack, preferably in
`
`the
`
`positions usually occupied by the first and third ironing dies. The gauges must be
`
`inserted in the correct orientation and must then be calibrated. Measurements may
`
`then be taken as the punch passes through the gauge ring on the forward stroke,
`
`backward stroke and during and after doming. This process is carried out
`
`in the
`
`absence of a can body to avoid the sensors detecting the can body rather than the
`
`punch.
`
`Alignment and re-alignment of known bodymakers is
`
`therefore a time consuming
`
`process which requires the can body production line to be halted. The high volume
`
`nature of the can industry means that
`
`lost production time can be very costly for
`
`producers.
`
`Summary of the Invention
`
`According to a first aspect there is provided a radial offset monitor comprising a body
`
`defining an internal bore and one or more eddy current sensors spaced around the
`
`bore. The bore may be cylindrical.
`
`The radial offset monitor may be configured to detect the misalignment of an object
`
`moving axially through the bore, relative to the axis, i.e. to detect offset along a radius.
`
`The radial offset monitor may be configured to be attached to a toolpack module of a
`
`can bodymaker, wherein said object is a ram and/or a punch, or a can body held on the
`
`punch.
`
`The radial offset monitor may comprise comprising four eddy current sensors
`
`equiangularly spaced around the bore.
`
`10
`
`15
`
`20
`
`25
`
`30
`
`35
`
`33594726—1-SBRADLEY
`
`
`
`M&C PX215464GB
`
`The eddy current sensors may be adjustable in a direction orthogonal to the axis.
`
`3
`
`According to a second aspect there is provided a can bodymaker comprising the radial
`
`offset monitor of the first aspect, wherein the object is a ram and/or a punch, or a can
`
`body held on the punch, of the can bodymaker.
`
`The body of the radial offset monitor may be co-located with, or integrated into, a
`
`stripper housing.
`
`The can bodymaker may comprise a controller having an input for receiving sensor
`
`data from the radial offset monitor; and a processor configured to compute one or more
`
`of ram position, ram trajectory, punch position, punch trajectory, can body presence,
`
`can body sidewall thickness.
`
`The can bodymaker may comprise an adjustment mechanism to automatically adjust
`
`one or more components of the bodymaker in response to detection by the radial offset
`
`monitor of a misalignment of the ram and/or punch and/or can body.
`
`The one or more components may be or may include the ram, the punch, a domer, and
`
`the adjustment may be an axial adjustment.
`
`According to a third aspect there is provided a can bodymaker toolpack comprising the
`
`radial offset monitor of the first aspect.
`
`According to a fourth aspect there is provided a method of detecting axial misalignment
`
`of an object subject to reciprocating motion along an axis,
`
`the method comprising
`
`obtaining electrical output signals from one or more eddy current sensors spaced
`
`around a bore extending through a body within which the sensor(s) is(are) located, as
`
`the object moves through the bore; and processing the signal(s) to detect any axial
`
`10
`
`15
`
`20
`
`25
`
`30
`
`misalignment.
`
`The method may be employed in a can bodymaker, wherein said object may be a ram
`
`and/or a punch, or a can body held on the punch, of the can bodymaker.
`
`33594726—1-SBRADLEY
`
`
`
`M&C PX215464GB
`
`4
`
`The method may comprise the radial offset monitor being co—located with, or integrated
`
`into, a stripper of the can bodymaker.
`
`The method may comprise processing the sensor data to compute one or more of ram
`
`position, ram trajectory, punch position, punch trajectory, can body presence, can body
`sidewall thickness.
`
`The method may comprise using an adjustment mechanism to automatically adjust one
`
`or more components of the bodymaker in order to correct the misalignment.
`
`The method may be carried out while the bodymaker is producing can bodies.
`
`Brief Description of the Drawings
`
`Figure 1 illustrates schematically a cross-section of a part of a known bodymaker;
`
`Figure 2a is a perspective view of a plurality of sensors integrated into a stripper
`
`housing;
`
`Figure 2b is a cross-sectional schematic view of a sensor within the stripper housing;
`
`Figure 3 is a cross-sectional view of the stripper housing of Figure 2 in position on a
`
`10
`
`15
`
`20
`
`bodymaker;
`
`Figure 4 is an enlarged cross—sectional view of the bodymaker of Figure 3;
`
`Figure 5a is a perspective cross-sectional view of the bodymaker of Figure 3;
`
`Figure 5b is an enlarged section of the view of Figure 5a;
`
`Figure 6a is a perspective view of a stripper housing comprising adjustable sensors
`
`and attached to a plastic stripper;
`
`Figure 6b is a perspective view of the stripper housing of Figure 6a in position on a
`
`bodymaker;
`
`Figure 7a is a perspective view of a stripper housing comprising adjustable sensors
`
`and attached to a steel stripper;
`
`Figure 7b is a cross-sectional view of the stripper housing of Figure 7a in position on a
`
`25
`
`30
`
`bodymaker;
`
`Figure 8 is a cross-sectional view of the stripper housing of Figure 7a;
`
`Figure 9 is a perspective view of a plurality of sensors integrated into a sensor housing;
`
`Figure 10 is a cross-sectional view of the sensor housing of Figure 9 in position on a
`
`35
`
`bodymaker;
`
`33594726—1-SBRADLEY
`
`
`
`M&C PX215464GB
`
`5
`
`Figure 11a is a perspective cross—sectional view of the bodymaker of Figure 10;
`
`Figure 11b is an enlarged section of the view of Figure 11a;
`
`Figure 12 is a graphical representation of sensor output;
`
`Figure 13 is an alternative graphical representation of sensor output; and
`
`Figure 14 is a further alternative graphical representation of sensor output.
`
`Detailed Description
`
`10
`
`15
`
`20
`
`25
`
`30
`
`35
`
`Figure 1
`
`illustrates schematically a cross-section of a known long-stroke bodymaker 1.
`
`The bodymaker 1 comprises a frame 2 and a ram 4 supported by a pair of hydrostatic
`
`bearings (not shown). The ram 4 is constructed using a metal or metal alloy and
`
`moves horizontally through a series of ironing dies 5. The dies 5 are clamped to a
`
`large block of metal or bolster plate 9. On the forward stroke, the ram 4 moves towards
`
`a bottom forming tool or domer 6 and on the return stroke the ram 4 moves away from
`
`the domer 6. A punch 7 is mounted on the end of the ram 4 nearest the domer 6. The
`
`punch 7 is constructed using a metal or metal alloy, such as steel. At the furthest
`
`extent of the ram’s 4 fonNard stroke, a base of a can body (not shown) held on the end
`
`of the punch 7 is brought into contact with the domer 6. At the furthest extent of the
`
`ram’s 4 backward stroke, the punch 7 will be located at a position to the right of a
`
`blankholder 3 of the bodymaker 1.
`
`In one complete cycle the ram 4 therefore moves
`
`from the blankholder 3 to the domer 6 and back again.
`
`Metal cups are fed into the bodymaker 1 one at a time to the left of the blankholder 3
`
`position. Each cup is carried by the punch 7 through the series of dies 5 as described
`
`above, as the ram 4 moves forwards. At the end of the forward stroke the resulting can
`
`body is brought into contact with the domer 6 and the base of the can body is formed.
`
`As the ram 4 begins its return stroke, the can body is removed from the punch 7 by a
`
`stripper 8. The stripper 8 may comprise a plastic or a steel ring. The stripper 8 in this
`
`example consists of stripping fingers (not shown here) mounted within an annular
`
`plastic stripper housing 13,
`
`located at one end of the die assembly 5. The radially
`
`inward ends of the stripping fingers extend into the bore of the die assembly 5 through
`
`which the punch 7 passes. On the forward stroke of the ram 4 the can body carried on
`
`the punch 7 deflects the stripping fingers as it moves along the bore of the die
`
`assembly 5. As the punch 7 moves on the return stroke, i.e. away from the domer 6,
`
`the stripping fingers prevent the can body from returning with the punch 7 and the can
`
`33594726—1-SBRADLEY
`
`
`
`M&C PX215464GB
`
`6
`
`body is stripped from the punch 7 and then removed from the bodymaker 1.
`
`In other
`
`embodiments not shown here, the can body may be removed from the bodymaker 1 by
`
`pressurised air (alternatively, pressurised air may be used to assist removal by a
`
`stripper).
`
`Figures 2, 3, 4 and 5 illustrate a first embodiment of a radial offset monitor or ram
`
`position sensor 10 comprising a plurality of sensors 11 housed within the outer
`
`circumference of a stripper housing 13, which takes the form of an annular ring.
`
`In
`
`Figure 2a, the stripper housing 13 is illustrated from the rear,
`
`i.e. as seen from the
`
`toolpack of the bodymaker, and without the stripper being present.
`
`In this example,
`
`there are four sensors 11 equally spaced around the stripper housing 13, although
`
`fewer, or additional sensors, may be used. The housing 13 may be a monolithic block
`
`machined from a single piece of metal, and comprises an internal bore configured to
`
`accommodate a can body of specific diameter, located on the punch 7.
`
`The sensors
`
`11
`
`are eddy current sensors,
`
`such as the eddyNCDTTM range
`
`manufactured by Micro-EpsilonT'V'.
`
`Unlike simple inductive sensors, eddy current
`
`sensors provide the ability to measure distances to conductive objects with an
`
`extremely high degree of precision (in the nanometre range). Advantageously, no
`
`contact with the object is required, such that measurement is wear-free.
`
`The eddy current sensors 11 each comprise a coil (not shown here) inside an outer
`
`casing. The coil
`
`is supplied with a high-frequency alternating current
`
`in order to
`
`produce an electromagnetic field.
`
`The coil’s electromagnetic field induces eddy
`
`currents in the conductive object. These eddy currents create an opposing magnetic
`
`field which resists the field produced by the coil. The interaction of magnetic fields
`
`produced by the coil and the conductive object depends upon the distance between
`
`them, and changes when the distance changes. The sensors 11 then produce a
`
`10
`
`15
`
`20
`
`25
`
`30
`
`voltage output proportional to the change in distance between the conductive object
`and the sensor 11.
`
`The electromagnetic field produced by a sensor 11 is capable of penetrating non-
`
`metallic objects. This means that eddy current sensors 11 can be used to produce
`
`measurements even where the (metallic) object has a non-conductive coating, such as
`
`33594726—1-SBRADLEY
`
`
`
`M&C PX215464GB
`
`7
`
`plastic, or where the metallic object is contaminated with dirt or oil. The sensors 11 are
`
`also substantially insensitive to temperature change.
`
`Each sensor 11 comprises a face 11a which is located within a circumference of the
`
`internal bore of the stripper housing 13 and which faces into the internal bore of the
`
`stripper housing 13. As illustrated in Figure 2b, each sensor 11 is housed within the
`
`stripper housing 13 such that the face 11a of the sensor 11 does not protrude from the
`
`stripper housing 13. The face 11a may be flush with an exterior of the housing 13, or
`
`the face 11a may be slightly recessed, as shown in Figure 2b. An air gap 16 is
`
`provided around the sensor face 11a, such that the sensor face 11a does not come
`
`into contact with the stripper housing 13. This avoids any interference from the stripper
`
`housing 13, which may be constructed from plastic or from metal.
`
`Figures 3, 4 and 5 illustrate the stripper housing 13 and integrated sensors 11 of Figure
`
`2 positioned within a bodymaker, such as the bodymaker of Figure 1.
`
`In these
`
`illustrated examples, a section of the bodymaker comprising the stripper 8, stripper
`
`housing 13, sensors 11 and bolster plate 9 is shown. This illustrated section of the
`
`bodymaker further comprises an adapter plate 14 and a retaining ring 15. The adaptor
`
`plate 14 enables the stripper 8 and stripper housing 13 to be attached to the
`
`bodymaker 1 and the retaining ring 15 holds the stripper 8 in place on the front of the
`
`stripper housing 13.
`
`In this illustrated example, the toolpack,
`
`identified by reference
`
`numeral 18, is shown without tools (i.e. the die assembly is not shown).
`
`An advantage of integrating the sensors 11 into an interior of the stripper housing 13 is
`
`that no additional space is required between the adapter plate 14 and the retaining ring
`
`15. Both the sensors 11 and stripper housing 13 may be accommodated within the
`
`space usually occupied by the stripper housing 13 alone, hence the overall longitudinal
`
`dimensions of the bodymaker 1 are unaffected by the inclusion of the sensors 11.
`
`Figure 4 illustrates the ram 4 on its forward stroke, passing through the internal bore of
`
`the stripper housing 13. Also illustrated is the can body unloader pocket 17, which
`
`forms part of the discharge turret and which transports the manufactured can body (not
`
`shown) away from the bodymaker.
`
`10
`
`15
`
`20
`
`25
`
`30
`
`33594726—1-SBRADLEY
`
`
`
`M&C PX215464GB
`
`8
`
`The eddy current sensors 11 continuously sense or monitor the position or radial offset
`
`of the ram 4 (i.e. measure the distance between themselves and the ram surface) as it
`
`passes through the stripper housing 13 and send this information to a bodymaker
`
`controller (not shown), comprising a PLC (programmable logic circuit). The sensors 11
`
`and the controller may be in wired or
`
`in wireless communication. The controller
`
`calculates the distance of the ram 4 from a longitudinal bodymaker axis, indicated in
`
`Figure 4 by line AA. The alignment of the ram may also be measured with respect to a
`
`vertical bodymaker axis indicated in Figure 4 by line BB. The information provided by
`
`the sensors is displayed on an external device (not shown here) comprising a display
`
`screen, as will be further discussed below.
`
`It will be appreciated that a bodymaker may need to be re—configured to produce can
`
`bodies of different diameters, by replacing the toolpack with a toolpack having dies of a
`
`different diameter and by replacing the ram with a ram having a different diameter. For
`
`example, to accommodate a larger can body, a ram having a 2 inch diameter might be
`
`replaced by a ram having a 3 inch diameter.
`
`In this case, the stripper will also need to
`
`be replaced in order to accommodate the ram and to remove the can body.
`
`Figures 6, 7 and 8 illustrate a second embodiment of radial offset monitor 20,
`
`in which
`
`the eddy current sensors 11 integrated into a stripper housing 113 are adjustable.
`
`Figures 6a and 6b illustrate a plastic stripper 8a attached to the stripper housing 113 by
`
`a retaining ring 15. Figures 7a, 7b and 8 illustrate the same stripper housing 113, to
`
`which a steel stripper comprising steel fingers 8b is attached using the retaining ring
`
`15. The plastic stripper 8a has a smaller internal bore than the steel stripper 8b, hence
`
`the steel stripper 8b can accommodate a ram, and a can body, of larger diameter. The
`
`stripper housing 113 has an internal bore configured to accommodate the largest
`
`diameter ram to be used with the bodymaker.
`
`In order to facilitate the exchange of
`
`strippers 8a, 8b, each stripper 8a, 8b is provided with a stripper adapter ring 19a, 19b.
`
`When changing from one type of stripper to another, only the stripper 8a, 8b and the
`
`stripper adapter ring 19a, 19b need be replaced.
`
`In both Figures 6 and 7, eddy current sensors 11 which are configured to be adjustable
`
`are integrated into the stripper housing 113, as will be discussed in more detail below.
`
`In these examples,
`
`four eddy current sensors 11 are equally spaced around the
`
`stripper housing 113, with sensor faces 11a facing into the bore of the stripper housing
`
`10
`
`15
`
`20
`
`25
`
`30
`
`35
`
`33594726—1-SBRADLEY
`
`
`
`M&C PX215464GB
`
`9
`
`113. An air gap (not shown here) is provided around each sensor face 11a, such that
`
`the sensor face 11a does not come into contact with the stripper housing 113.
`
`Figure 8 is a perspective cross-sectional view of the stripper housing 113 of Figure 7,
`
`shown attached to an adaptor plate 14. The steel stripper 8b is held in place on the
`
`stripper housing 113 by a retaining ring 15 and is provided with a stripper adapter ring
`
`19b. Although a steel stripper 8b is shown in this example, the plastic stripper 8a, or
`
`an alternative stripper, could also be used.
`
`The stripper housing 113 is configured to accommodate four adjustment mechanisms,
`
`one adjacent to each eddy current sensor 11. For example, the stripper housing 113
`
`may comprise cut outs of a suitable size and shape.
`
`In this example, each adjustment
`
`mechanism comprises a miniature high precision ball screw 21 and a guide mechanism
`
`22. The ball screw 21 converts rotary motion to linear motion.
`
`Each screw 21
`
`comprises a moveable collar 24 attached to the guide mechanism 22, which is in turn
`
`attached to the adjacent eddy current sensor 11 .
`
`Upon manual or automatic adjustment of
`
`the ball screw 21,
`
`the collar 24, guide
`
`mechanism 22 and hence the eddy current sensor 11 can be adjusted in a direction
`
`orthogonal to the inner face of the stripper housing 113.
`
`In other words, the eddy
`
`current sensor 11 can be adjusted, or screwed in or out, so that the face of the sensor
`
`11a either protrudes from, is flush with or is recessed into the inner face of the stripper
`
`housing 113.
`
`It will be appreciated that the position of the sensor face 11a can be
`
`adjusted depending upon the diameter of the ram which is to be used.
`
`Sensor
`
`recalibration may be required after adjustment.
`
`The adjustability of the sensors 11 allows the same stripper housing 113 to be used
`
`with a range of ram sizes. The ball screws 21 can be adjusted without removing the
`
`stripper housing 113 and so the sensors 11 can be easily and quickly configured to be
`
`used with a variety of ram sizes.
`
`A third embodiment of a radial offset monitor or ram position sensing gauge 30 is
`
`illustrated in Figures 9, 10 and 11.
`
`In this embodiment, a number of eddy current
`
`sensors 11 are housed in a separate sensor housing 12.
`
`In this illustrated example,
`
`there are four eddy current sensors 11 equally spaced around the annular sensor
`
`10
`
`15
`
`20
`
`25
`
`30
`
`35
`
`33594726—1-SBRADLEY
`
`
`
`M&C PX215464GB
`
`10
`
`housing 12. The housing 12 comprises an internal bore configured to accommodate a
`
`can body located on the punch 7.
`
`In use, the sensor housing 12 is located between a stripper housing 213 and the
`
`stripper 8, as will be discussed further below. The face 11a of each sensor 11 is
`
`located within a circumference of an internal bore of the sensor housing 12, such that
`
`the face 11a of the sensor 11 does not protrude from the sensor housing 12. As
`
`discussed with reference to Figure 2b above, each sensor face 11a is surrounded with
`
`an air gap to avoid any interference from the sensor housing 12.
`
`Figures 10 and 11 illustrate the sensor housing 12 of Figure 9 in position within a
`
`bodymaker, such as the bodymaker of Figure 1, shown with the toolpack removed.
`
`In
`
`this illustrated example, the sensors 11 are not integrated into the stripper housing 213,
`
`but are instead mounted equiangularly around a separate sensor housing 12, located
`
`behind the stripper 8, Le. between the stripper 8 and stripper housing 213.
`
`In this case,
`
`the stripper housing 213 is adapted with one or more recesses to provide space for the
`
`sensor housing 12.
`
`The embodiments described above may be retrofitted to existing bodymakers.
`
`Advantageously, the embodiment of Figures 9, 10 and 11, in which a separate sensor
`
`housing 12 is provided, can be moved from one bodymaker to another in order to carry
`
`out diagnostic testing on the alignment of the ram 4.
`
`In other words, the sensor
`
`housing 12 may be removed from its position between the stripper 8 and the stripper
`
`housing 213 without affecting the configuration or the operation of the bodymaker.
`
`Similarly, the sensor housing 12 may be re-fitted into the bodymaker where further
`
`diagnostic testing is
`
`required.
`
`The number of
`
`radial offset monitors required is
`
`therefore reduced.
`
`The eddy current sensors 11 provide precise, real-time information as to the ram 4
`
`position with respect to the bodymaker 1 axis or axes. Since the punch 7 is located on
`
`a distal end of the ram 4, the sensors 11 can also provide information regarding the
`
`position of the punch 7. Positional information can be provided by the sensors 11 both
`
`when the ram 4 is stationary and when the bodymaker 1
`
`is running,
`
`i.e. when the
`
`bodymaker is in normal operation and can bodies are being fed in. Since the radial
`
`offset monitor 10, 20, 30 either comprises a stripper housing 13, 113 or is mounted
`
`10
`
`15
`
`20
`
`25
`
`30
`
`35
`
`33594726—1-SBRADLEY
`
`
`
`M&C PX215464GB
`
`between the stripper housing 213 and the stripper 8,
`
`it is not necessary to remove any
`
`of the dies 5.
`
`11
`
`In addition to dynamically monitoring the radial offset of the ram 4 with respect to an
`
`axis of the bodymaker, the sensors 11 can also provide information regarding the ram’s
`
`4 trajectory i.e. the path the ram 4 will take after it passes through the stripper housing
`
`13, 113, 213 and/or the sensor housing 12. This can be provided by taking a series of
`
`measurements of the ram’s position as it passes by the sensors 11.
`
`The sensor data received can also be used to monitor the punch 7 trajectory and
`
`alignment, as well as measuring ram 4 vibration. The use of highly sensitive eddy
`
`current sensors 11 also means that
`
`it
`
`is possible to detect whether a can body is
`
`present on the punch 7 or not, and to measure a thickness of the can body. Since the
`
`sensitivity of the eddy current sensors eliminates interference from the can body, these
`
`measurements can be taken while the bodymaker
`
`1
`
`is
`
`idle and also when the
`
`bodymaker 1 is making can bodies.
`
`Detection of the presence and/or thickness of a can body on the punch 7 is useful as it
`
`can indicate whether a can body has been properly removed from the punch 7 by the
`
`stripper 8, and whether there are any defects in the can body, e.g. the sidewall of the
`
`can body is too thin or too thick, potentially indicating cracks or splits.
`
`The signal
`
`from the sensors 11
`
`is sent
`
`to the bodymaker controller where it
`
`is
`
`converted and presented on a human-machine interface (HMI), which may comprise a
`
`screen or digital display. The signal can be presented in several different ways. For
`
`example, the processed signal output may show the position of the punch 7 in relation
`
`to its fully-aligned target position; the position of the ram/punch in relation to the A
`
`and/or B axis of the bodymaker; the trajectory of the ram/punch as a 3D plot; a 3D
`
`ram/punch patch plot or A-B axis ram/punch patch plot; a plot of the position of the ram
`
`or punch in relation to an axis of the bodymaker 1.
`
`Figure 12 is a graphical representation of an exemplary signal output from the sensors
`
`11 of any of the embodiments of Figures 2 to 11, showing the position of a ram
`
`operating at 100 cycles per minute (equivalent to the drive shaft operating at a speed of
`
`100 rpm). The signal output
`
`is recorded over a single cycle of the ram i.e. one
`
`10
`
`15
`
`20
`
`25
`
`30
`
`35
`
`33594726—1-SBRADLEY
`
`
`
`M&C PX215464GB
`
`12
`
`complete ram stroke. The graph indicates the real—time radial deviation of the ram from
`
`its target or fully aligned position in millimetres. A deviation of 0.00 mm indicates that
`
`the ram is fully aligned and in its target position.
`
`The graph also illustrates any deviation of
`
`the ram from its target
`
`trajectory.
`
`A
`
`deviation of 0 degrees indicates th
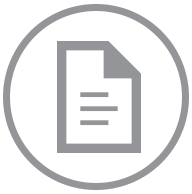
Accessing this document will incur an additional charge of $.
After purchase, you can access this document again without charge.
Accept $ ChargeStill Working On It
This document is taking longer than usual to download. This can happen if we need to contact the court directly to obtain the document and their servers are running slowly.
Give it another minute or two to complete, and then try the refresh button.
A few More Minutes ... Still Working
It can take up to 5 minutes for us to download a document if the court servers are running slowly.
Thank you for your continued patience.
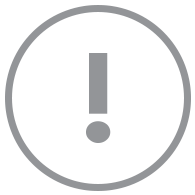
This document could not be displayed.
We could not find this document within its docket. Please go back to the docket page and check the link. If that does not work, go back to the docket and refresh it to pull the newest information.
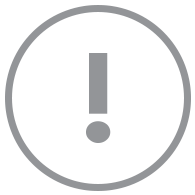
Your account does not support viewing this document.
You need a Paid Account to view this document. Click here to change your account type.
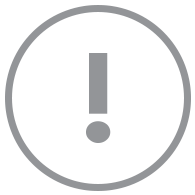
Your account does not support viewing this document.
Set your membership
status to view this document.
With a Docket Alarm membership, you'll
get a whole lot more, including:
- Up-to-date information for this case.
- Email alerts whenever there is an update.
- Full text search for other cases.
- Get email alerts whenever a new case matches your search.
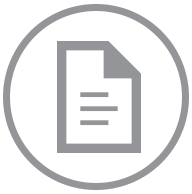
One Moment Please
The filing “” is large (MB) and is being downloaded.
Please refresh this page in a few minutes to see if the filing has been downloaded. The filing will also be emailed to you when the download completes.
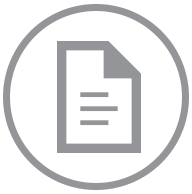
Your document is on its way!
If you do not receive the document in five minutes, contact support at support@docketalarm.com.
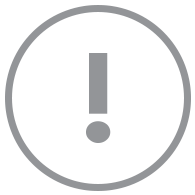
Sealed Document
We are unable to display this document, it may be under a court ordered seal.
If you have proper credentials to access the file, you may proceed directly to the court's system using your government issued username and password.
Access Government Site