`4.. Mn A-...|:,...-:,._ mug <n91 c ['71
`roux tram: “)0 ha» 1071
`
`(11) 1346 369
`A
`
`PATENTS ACT 1949
`
`SPECIFICATION NO 1346369
`
`The following corrections were allowed under Section 76 on 30 July 1974.
`
`Page 1.
`
`line 20, after processes insert
`
`,
`
`Page 1,
`
`line 54,
`
`for irridium read iridium
`
`Page 1,
`
`line 78, after series insert,
`
`Page 4,
`
`line 48,
`
`for zinc chromium read zinc-chromium
`
`Page 5,
`
`line 70, after resorted insert to
`
`Page 6,
`
`line 43, after solution delete ammonium carbonate
`
`Page 8,
`
`line 1, after per insert square
`
`Page 8,
`
`line 116, for as read are
`
`Page 9,
`
`line 43,
`
`for found read bound
`
`Page 9,
`
`line 92, after analogous delete,
`
`Page 11,
`
`line 56,
`
`for aluminate read aluminum
`
`Page 12,
`
`line 75,
`
`for feet read foot
`
`Page 13,
`
`line 27, after surface insert
`
`,
`
`Attention is also directed to the following printers errors:-
`
`Page 2,
`
`line 55, after a insert metal having a
`
`Page 3,
`
`line 53, after iron insert spinel
`
`Page 3,
`
`line 76, after vanadium— insert magnesium
`
`Page 4,
`
`line 111, for metal
`
`insert metals,
`
`Page 5,
`
`line 30,
`
`for ben read been
`
`Page 5,
`
`line 31, after to insert for
`
`Page 5,
`
`line 33
`
`for temperature read temperatures
`
`Page
`
`6,
`
`Page 9,
`Page 9,
`
`9.
`
`Page
`
`line 23, after oxalate insert solution
`
`line 79,
`
`for
`
`(BeRuoé) read (BeRuDB)
`
`line 79 fbr ruthenate read ruthenite
`
`line 88,
`
`for (MgRuO3) read (MgRuoé)
`
`Page 10,
`
`line 121,
`
`for such read Such
`
`Page 13,
`
`line 1,
`
`for whever read wherever
`
`Page 13,
`
`line 7,»f0r of read to
`
`Page 13,
`
`line 102,
`
`for comprising read comprises
`
`THE PATENT OFFICE
`23 August 1974
`
`,
`
`R 77160/3
`
`
`
`PATENT SPECIFICATION
`
`(11)
`
`1346 369
`
`1346369
`
`(22) Filed 29 Oct. 1971
`(21) Application No. 5 O3 15/71
`(32) Filed 2 Nov. 1970‘
`(31) Convention Application No. 86062
`(32) Filed 8 March 1971 in
`(31) Convention Application No. 121683
`(33) United States of America (US)
`(44) Complete Specification published 6 Feb. 1974
`(5 1) International Classification BOIK 3 /06//C22]? 13/00
`(52) Index at acceptance
`C7B AlC AZCZ AZD A9
`BZE 191 19X 19Y 203 ZOY 348 378 41X 41Y 498 568 62X
`62Y 638 679 708 768 778
`
`C7B 13
`
`
`
`(54) ELECTRODES
`
`We, PPG INDUSTRIES, INC., a
`(71)
`Corporation organised and existing under the
`laws of the Commonwealth of Pennsylvania,
`United States of America, of One Gateway
`Center, Pittsburgh, Commonwealth of Penn-
`sylvania, 15222, United States of America,
`(assignee
`of ALEKSANDRS MARTIN-
`SONS), do hereby declare the invention, for
`which we pray that a patent may be granted
`to us, and the method by which it is to be
`performed, to be particularly described in and
`by the following statement:—
`The present invention relates to electrodes
`suitable for use for electrolytic purposes, for
`example for the electrolysis of aqueous alkali
`metal chloride solutions.
`Chlorine and alkali metal hydroxides, such
`as lithium hydroxide, sodium hydroxide, and
`potassium hydroxide, are produced commer—
`cially by either of two electrolytic processes
`electrolysis in a dipahragm cell or electrolysis
`in a mercury cell. Alkali metal chlorates are
`made in a cell similar in structure to a dia-
`phragm cell but not having a diaphragm.
`The design and operation of mercury cells,
`diaphragm cells, and chlorate cells, are more
`fully treated in Mantel], Electrochemical
`Engineering, McGraw-Hill, New York, NY.
`(1960), and Sconce, Chlorine, Reinhold, New
`York, N.Y. (1962).
`Common to all three processes has been the
`use of carbon anodes. These carbon anodes
`are a constant source of difficulty. They are
`short lived and subject to uneven wear and
`erosion. In mercury cells, frequent adjustment
`is required in order to maintain a constant gap
`between the cathode and anode and thereby
`maintain a constant voltage drop across the
`electrolyte. In diaphragm cells and chlorate
`cells, no provision is made for varying the
`anode—cathode space, and, accordingly,
`the
`voltage
`increases with time. Additionally,
`organic solvents present in the graphite elec—
`trodes may plug the diaphragm, resulting in a
`further increase in voltage. Reaction of the
`anode products with the graphite anode result
`
`in halogenated hydrocarbons being present in
`the anode product.
`Many attempts have been made to remedy
`these problems. It has long been recognized
`that a superior anode would be one made of
`a solid precious metal, that is, a metal chosen
`from the
`group
`consisting
`of platinum,
`irridium, osmium,
`ruthenium,
`rhodium and
`palladium. However,
`this is neither econo-
`mical nor practical. The art
`shows many
`attempts to» obtain a lower cost electrode hav—
`ing the long life and low overvoltage of a
`solid precious metal electrode, as well as the
`low cost of a graphite electrode. These
`attempts have sought to provide a durable
`coating, usually of a platinum group metal
`or platinum group metal oxide, on an elec—
`tro—conductive base, which base usually is
`composed of a valve metal such as titanium.
`These electrodes are noticeably longer in
`life and operate at lower voltages than carbon
`electrodes. However, platinum group metals
`either as such or as their oxides are expensive.
`It has now been found that a particularly
`satisfactory anode for the electrolysis of brines
`may be provided by an electrode having an
`outer electroconductive surface comprising 2
`spinel
`on
`an
`electroconductive
`substrate
`wherein an intermediate layer comprising an
`oxycompound of a second transition series
`platinum group metal chosen from oxides of
`the second transition series platinum group
`metals, alkaline earth metal (as herein defined)
`oxides of the second transition series platinum
`group metals, and rare earth metal (as herein
`defined) oxides of the second transition series
`platinum group metals is placed between the
`substrate and outer surface. The platinum
`group metals of the second transition series
`consist of ruthenium, rhodium, and palladium.
`The oxycompound of the second transition
`series platinum group metals may be present
`in the substrate and, additionally, may also
`be dispersed through the spinel coating. When
`' the oxycompound is also dispersed through the
`spinel coating, it may be dispersed uniformly
`
`50
`
`55
`
`60
`
`65
`
`70
`
`75
`
`80
`
`85
`
`9Q
`
`10
`
`15
`
`20
`
`25
`
`30
`
`35
`
`40
`
`[Price 2513]
`
`SEE CORRECTIGE‘i
`
`SUP ATTACHED
`
`
`
`1,346,369
`
`or non-uniformly. The resulting anode appears
`to ofier economies of construction and opera-
`tion over an anode having a metallic platinum
`coating on an electroconductive substrate.
`As used herein, “ spinel ” means an oxy—
`compound of at
`least 2 types of ion of a
`metal or metals which oxycompound has the
`unique crystal structure and formula charac-
`teristic of spinels. The spinel may be applied
`with a suitable binding agent over a suitably-
`treated metal structural member or substrate.
`Such spinel itself comprises mainly the ions
`of the metal or metals and oxygen in chemical
`combination. However, amounts, usually minor
`amounts, of other materials such as other
`metal oxides, sulfides, fluorides, or even metals
`in the metallic state, may be entrapped in
`or associated with the spinel crystal structure
`without seriously impairing the desirable pro-
`perties of the spinel surface.
`A suitable electroconductive substrate is one
`that
`retains its electroconductive properties
`during the formation of
`the spinel surface
`thereon and in the course of using the result-
`ing electrode for its intended purpose. Such
`a substrate will be resistant to oxidation dur-
`ing fabrication and electrolysis, and will not
`be subject to attack by the gases liberated
`during electrolysis. Preferably,
`the substrate
`should be more electroconductive than the
`spinel itself.
`The resulting electrode is long lived in the
`electrolytic cell environment and has satis-
`factory overvoltage characteristics.
`In the accompanying drawings the sole
`Figure is an X—ray diffraction pattern of an
`electrode produced according to the procedure
`of Example I, below.
`Suitable electroconductive substrates hav-
`ing a spinel outer coating and an inter-
`mediate layer of an oxycompound of a second
`transition series platinum group metal
`(i.e.,
`ruthenium, rhodium, palladium) therebetween
`produce an anode that is dimensionally stable
`in an environment where chlorine is electro-
`lytically produced. Spinels are oxycompounds
`of the two or more types of ion of one or
`more metals characterized by a unique crystal
`structure, stoichiometric relationship, and X-
`ray diffraction pattern.
`Oxycompounds having the spinel structure
`may be represented by the empirical formula
`
`MIIMEIII()41
`
`represents a metal having a
`wherein MII
`valency of plus 2, and MIII
`represents a
`valency of plus 3. The metals may be the
`same metal as in CrHCrLFHO, or different
`metals as in NiCr204. Spinels are more pre—
`cisely represented by the empirical formula
`
`MII<MIIIILMII[1304'
`
`where MII represents a metal having a valency
`
`10
`
`15
`
`20
`
`25
`
`30
`
`35
`
`40
`
`45
`
`5O
`
`55
`
`60
`
`of plus 2, and Mum and MIIIb represent
`metals having a valency of plus 3. Mum and
`Mm" may either be the same metal or
`different metals, and one or both of them
`may represent the trivalent state of the metal
`present in the bivalent state, as
`
`Fen(CumFem)O,,
`
`ions may be ions of
`three metal
`or all
`different metals, as MgAlFeO4.
`and the
`The
`spinel
`crystal
`structure
`methods of identifying it by X-ray techniques
`are described in the literature. For example,
`the spinel structure is discussed in Wyckoff,
`Crystal Structure, Vol.
`3
`(2nd Edition),
`Wiley & Sons, New York (1963) at pages
`75 to 86;
`in Wells, Structural
`Inorganic
`Chemistry, Oxford University Press, New
`York (1950) at pages 379 to 388 ;
`in Evans,
`An Introduction to Crystal Chemistry (2nd
`Edition), Cambridge University Press, New
`York (1966) at pages 171 to 175; and in
`Bragg, Claring—Bull and Taylor, The Crystal-
`line State, Vol.
`4, Crystal Structures of
`Minerals, G. Bell & Sons Ltd., London (1965)
`at pages 102 to 106.
`the spinel
`According to those authorities,
`crystal
`structure may be characterized as
`comprising oxygen ions in an approximately
`cubic
`close-packed relations-hip, with the
`metal
`ions lying in holes of
`the packing.
`Crystal structures having close-packed atoms
`or ions may be conveniently considered, for
`purposes of illustration, as being arranged in
`layers. In the spinel lattice having metal ions
`and layers of close-packed oxygen ions,
`the
`metal ions are smaller than the oxygen ions
`and are found between the layers of oxygen
`ions. Therrelationship within the lattice may
`be shown by imagining that the layers of
`oxygen ions are taken apart,
`leaving asso-
`ciated with each layer of oxygen ions the
`metal
`ions immediately in contact with the
`upper surface of the layer of oxygen ions.
`In this way the spinel
`structure may be
`regarded as built up of two kinds of alter-
`nate layers which layers are superposed one
`on top of the other in an alternating manner.
`The spinel structure may be further charac-
`terized in that one-third of the metal
`ions
`have 4 oxygen neighbors which oxygen
`neighbors are arranged tetrahedrally to the
`metal ion, and that two-thirds of the metal
`ions have 6 oxygen neighbors which oxygen
`neighbors are arranged octahedrally to the
`metal ion.
`close—packed
`the layers of
`In each of
`oxygen ions are diagonal chains of metal
`ions having octahedral geometry. The octa-
`hedral metal
`ions are linked laterally above
`and below the layer of oxygen ions by the
`metal ions having tetrahedral geometry. The
`direction of the chains in any layer is normal
`to the direction of the chains in the adja—
`
`65
`
`70
`
`75
`
`80
`
`85
`
`90
`
`95
`
`100
`
`105
`
`110
`
`115
`
`120
`
`
`
`
`
`
`1,346,369
`
`cent layer. Four layers make up a unit cell.
`The unit cell referred to above is an arbitrary
`parallelopiped which is the smallest repetitive
`unit identifiable as the crystal. The unit cell
`generally, as a matter of convenience, con-
`forms to the symmetry of the system to which
`the crystal belongs. The unit cell is defined
`by the lengths of its edges, and the angles
`included between them. The edges of
`the
`unit cell are termed unit translations in the
`pattern. Starting from any point of origin in
`the lattice and going a distance equal to and
`parallel to: any cell edge, or by any combina—
`tion of such movements, we arrive at a point
`where the whole surrounding structure has
`the same form and orientation as at the point
`of origin. Because of the arbitrary nature of
`the definition of the unit cell, any one ion
`may be entirely within one cell or it may,
`alternatively be divided between two, four, or
`eight unit cells. Additionally,
`the neighbor
`of any one ion may be in the same unit cell
`or in an adjacent unit cell.
`The spinel unit cell contains eight “ formula
`weights”,
`i.e., eight MIIM211104 units. More
`particularly,
`the crystallographic unit cell of
`the spinel structure contains 32 oxygen ions.
`There are equivalent positions in this cell for
`8 metal
`ions surrounded tetrahedrally by 4
`oxygen ions, and for 16 metal
`ions sur-
`rounded octahedrally by 6 oxygen ions.
`Spinels may further be characterized on
`the basis of which metal ions occupy which
`positions
`in the crystal
`structure. Those
`spinels wherein the positions of tetrahedral
`coordination are occupied by the divalent
`metallic ions and the positions of octahedral
`coordination are occupied by the trivalent
`metal
`ions are “regular ”
`spinels. Those
`spinels reported in the literature as being
`“regular” spinels, and their stoichiometric
`formulae:
`include:
`the magnesium-vanadium
`spinel
`(MgV204);
`the zinc-vanadium spinel
`(va,o,); the magnesium-chromium spinel
`(MgCr204);
`the manganese-chromium spinel
`(MnCr204) ;
`the
`iron-chromium spinel
`(FeCr204);
`the
`cobalt—chromium spinel
`(CoCr204);
`the
`nickel-chromium spinel
`(NiCr204;)
`the
`copper-chromium spinel
`(CuCr20,)3
`the
`zinc
`chromium spinel
`(ZnCrgoi);
`the
`zinc—manganese
`spinel
`(ZnMnZOQ;
`the zinc-iron spinel (ZnFezor);
`the cadmium—iron (CdFe204);
`the copper—
`cobalt spinel (CuC0204); the zinc-cobalt spinel
`(ZnCogO4) 3
`the magnesium-rhodium spinel
`(Mth204) ;
`the
`zinc—rhodium
`spinel
`(ZnRh204);
`the magnesium-aluminum spinel
`(MgA1204);
`the manganese—aluminum spinel
`(MnA1204);
`the
`iron-aluminum spinel
`(FeA1204) ;
`the
`cobalt-aluminum spinel
`(C0A1204);
`the
`zinc-aluminum
`spinel
`(ZnA1204) ,
`the
`nickel-aluminum spinel
`(NiA1204); and the calcium-gallium spinel
`(CaGa204).
`Other spinels, wherein the tetrahedral posi—
`
`10
`
`15
`
`20
`
`25
`
`3O
`
`35
`
`40
`
`45
`
`50
`
`55
`
`60
`
`65
`
`tions are occupied by one-half of the trivalent
`metal
`ions and wherein the remaining one—
`half of the trivalent metal
`ions along with
`all of the divalent metal
`ions are in octa—
`hedral
`positions,
`are
`characterized
`as
`“inverse ” spinels. In “inverse” spinels the
`arrangement of octahedral divalent and octa—
`hedral
`trivalent positions
`is
`substantially
`random. Such spinels, and their
`stoichio—
`metric formulae,
`include:
`the titanium-mag-
`nesium spinel
`(Tng204);
`the vanadium—
`spinel (VMg204), the magnesium—iron spinel
`(MgFe204);
`the
`titanium—iron
`spinel
`(TiFe2.O,); the cobalt-iron spinel (CoFegO4);
`the nickel~iron spinel (NiFeZOQ; the copper—
`iron
`spinel
`(CuFeEOQ;
`the
`titanium-
`zinc
`spinel
`(TiZn204);
`the
`tin—cobalt
`spinel
`(SnC0204);
`the
`tin-zinc
`spinel
`($1an04);
`the magnesium—gallium spinel
`(MgGaZOQ;
`the magnesium-indium spinel
`(MgIn204);
`the manganese—indium spinel
`(MnIn204); the iron-indium spinel (Feln204);
`the coba1t~indium spinel (CoInEO4); and the
`nickel-indium spinel (NiIn204).
`In still other spinels,
`the distribution of
`metal ions is less regular, the spinels exhibit-
`ing both normal and inverse arrangement, as
`is discussed, for example in Bragg, Claring—
`bull, and Taylor, The Crystalline State, Vol.
`4; Crystal Structure of Minerals, G. Bell &
`Sons. Ltd, London (1965) at pages 105 and
`106.
`The spinel crystallographic unit gives a
`unique X-ray diffraction pattern correspond-
`ing to the spacings between the crystallo-
`graphic planes. Typically, the observation of
`this X—ray diffraction pattern involves sub-
`jecting spinel
`samples
`to X-rays from a
`copper target. Methods of accomplishing this
`are more particularly described in chapter 5
`of King and Alexander, X—ray Diffraction
`Procedures, John Wiley and Sons, Inc., New
`York (1954), at pages 235 to 318, and especi—
`ally at pages 270 to 318, and in Ncwfield,
`X-ray Diffraction Methods, john Wiley and
`Sons, Inc., New York, N.Y., (1966), at pages
`177 to 207. As described therein,
`these X-
`rays have a wave length of 1.5405 angstrom
`units. The X-rays diffracted by the sample
`are particularly intense at certain angles, 6,
`resulting in peaks on diffractometer print-
`outs as in the Figure or in lines on photo—
`graphic diffraction patterns. This high inten-
`sity is caused by the X»rays “ reflected ” from
`parallel planes in the crystal reinforcing each
`other. The wave length of the X—rays,
`the
`spacing of the planes in the crystal, and the
`angle, «6’, are related by Bragg’s Law. Bragg’s
`Law is
`
`2d sin 19:11)»
`
`where d is the distance between the planes
`of the crystal,
`:1 is an integer, A is the wave
`length of the X—rays, and 9 is the angle of
`
`7O
`
`75
`
`80
`
`85
`
`90
`
`95
`
`100
`
`105
`
`110
`
`115
`
`120
`
`125
`
`
`
`
`
` 1,346,369 4
`
`4|
`
`incidence of the X—rays, and also the angle
`of reflection of the X—rays.
`Typically,
`the X-ray diffraction data is
`obtained from a diflractometer that is direct
`reading in 20, wherein 180 degrees —26 is
`the angle between the incident ray and the
`reflected ray. One way of recording X-ray
`diffraction data is in the form of a graph
`of the intensity of the reflected ray versus
`26. X—ray diffraction data recorded in this
`way is shown in the Figure.
`The Figure is a graph of the intensity of
`the reflective ray versus two theta for an
`electrode prepared according to Example I
`and consisting of a titanium member having
`thereon an outer surface of a cobalt—aluminum
`bimetal spinel and silicon dioxide and an inter—
`mediate layer of palladium oxide between the
`cobalt-aluminum spinel, silicon dioxide outer
`surface and the titanium member. The peak
`at 33.92 degrees two theta is the charac-
`teristic PdO peak reported in the literature.
`Also to be noted are the characteristic cobalt—
`aluminum spinel peaks at (in numerical order)
`31.28 degrees two thetah 36.78 degrees two
`theta, 59.18 degrees two theta, and 64.98
`degrees two theta.
`results have been
`Good electrochemical
`obtained with all spinels which have been
`tested. Spinels,
`including normal and inverse
`spinels, as well as those exhibiting both the
`normal and inverse arrangement are con—
`templated:
`
`including
`The spinels of magnesium,
`titanium—magnesium spinel
`(Tng204),
`vanadium—magnesium spinel (VMgzO4), and
`tin—magnesium spinel (SnMggoé).
`including
`The
`spinels
`of
`vanadium,
`(MgV204),
`magnesium—vanadium spinel
`iron-vanadium spinel (FeV204), and zinc—
`vanadium spinel (ZnV204).
`The
`spinels
`of
`chromium including
`magnesium-chromium spinel
`(MgCr204),
`manganese-chromium spinel
`(MnCr204),
`iron-chromium spinel
`(FeCrgO4),
`cobalt—
`chromium spinel
`(COCT204),
`nickel—
`chromium spinel
`(NiCr204),
`copper—
`chromium spinel (CuCrgOi), zinc chromium
`spinel
`(ZnCrgoi),
`cadmium—chromium
`spinel
`(CdCr204),
`and the chromium—
`chromium spinel (CrHCrngQ.
`are
`results
`satisfactory
`Particularly
`including
`The spinels of manganese,
`spinel.
`the
`bimetal
`obtained
`with
`titanium-manganese spinel (TiMn2O4), and
`zinc—manganese spinel (ZnMn204), and the Bimetal spinels are those spinels having the
`manganese—manganese spinel
`formula MIIM211104 as described hereinabove
`where MII and MIII are ions of two different
`
`(ZnFe204), cadmium-iron
`zinc-iron spinel
`spinel
`(CdFeEOi),
`lead-iron
`spinel
`(PbFe20'4),
`and
`aluminum-iron
`spinel
`(FeAlFeOi).
`including mag—
`The spinels of cobalt
`nesium-cobalt spinel (MgC0204), titanium-
`cobalt
`spinel
`(TiConi),
`copper-cobalt
`spinel
`(CuCozoi),
`zinc-cobalt
`spinel
`(ch0204),
`tin-cobalt
`spinel
`(SnC0204),
`and cobalt-cobalt spinel
`(CoUCoJUOi).
`The spinels of nickel _including iron-
`nickel spinel (FeNigoé), and germanium-
`nickel spinel (GeNi204)
`The spinels of rhodium including mag—
`nesium-rho-dium spinel
`(MthgOQ,
`cad—
`mium—rhodium spinel
`(CdRhgoi), cobalt-
`rhodium spinel (CoRh204), copper—rhodium
`spinel
`(CuRh204), manganese-rhodium 80
`spinel
`(MnRhgoi), nickel—rhodium spinel
`(NiRhgoi),
`and
`zinc-rhodium spinel
`(ZnRhgoi).
`The zinc spinels including titanium—zinc
`spinel
`(Tianoi),
`and
`tin—zinc
`spinel
`(SnZn204).
`The aluminum spinels including mag—
`nesium-aluminum
`spinel
`(MgA1204),
`strontium-aluminum
`spinel
`(SrA1204),
`chromium-aluminum spinel
`(CrA1204),
`molybdenum—aluminum spinel
`(MoAIZOé),
`manganese-aluminum spinel
`(MnA1204),
`iron—aluminum spinel
`(FeAlgot),
`cobalt—
`aluminum spinel
`(CoA1204),
`nickel—
`aluminum spinel
`(NiA1204),
`copper— 95
`aluminum spinel
`(CuAlEO4),
`and zinc—
`aluminum spinel (ZnA1204).
`The
`gallium spinels
`including mag-
`nesium—gallium spinel
`(MgGagoa), zinc-
`gallium spinel
`(ZnGagoi), and calcium— 100
`gallium spinel (CaGa204).
`including mag-
`The
`indium spinels
`nesium—indium spinel (MgIngoé), calcium-
`indium spinel
`(CaIn204), manganese-
`indium spinel
`(Mnln204),
`iron—indium 105
`spinel
`(FeIn204),
`cobalt-indium spinel
`(CovInzoé), nickel-indium spinel (NiIn204),
`cadmium-indium spinel
`(CdIn204),
`and
`mercury—indium spinel (HgIngoi).
`three
`The spinels containing ions of
`metal
`such
`as magnesium-aluminum-
`iron
`spinel
`(MgFeAlOi),
`and
`nickel-
`aluminum-iron spinel (NiFeAlOQ.
`
`65
`
`70
`
`75
`
`85
`
`90
`
`110
`
`115
`
`(MnIIMngIIIO4).
`
`metals.
`Better electrolytic results are obtained with 120
`aluminate spinels, that is Where one or both
`The spinels of iron including magnetite
`of the ions present
`in the plus 3 valency
`(FeHFeJHOi), magnesium iron
`spinel
`state is aluminum, as in CuA1204, CoA1204,
`(MgFe20-4), titanium-iron spinel (TiFegoi),
`manganese—iron spinel (MnFegoé), cobalt— FeAlFeOi, and NiAlgoi.
`iron spinel
`(CoFegoi), nickel—iron spinel
`Best results are obtained with the heavy 125
`(Ntigoi), copper-iron spinel (CuFegoi), metal-aluminate spinels,
`that
`is where the
`
`m
`
`10
`
`15
`
`20
`
`25
`
`30
`
`35
`
`4O
`
`45
`
`50
`
`55
`
`60
`
`
`
`1,346,369
`
`metal ion present in the plus 2 valency state
`is iron, cobalt, or nickel, as in FeHAIFemO4,
`CoAlZO.” and NiA1204, and with the heavy
`metal ferrite spinels,
`that is, where iron is
`present
`in the plus 3 valency state, as in
`COF6204, MgFE’204, and NiF6204.
`Whenever FeAlFe04 is referred to herein,
`it is understood that this material may actu-
`ally be a mixture of FeHFezmoi, FeAlzor,
`and FeHAlFemOr. This material may be
`characterized by the presence of
`iron in
`both the plus 2 and plus 3 valency states,
`as well as the presence of aluminum in the
`plus
`3 valency state. Additionally, FeO,
`Fe203, and A1203 may also be present.
`Preferably,
`the spinel
`itself should have
`some
`appreciable
`electroconductivity when
`measured in bulk. While good results have
`been obtained with 2. spinel having an electro~
`conductivity as
`low as
`10""
`(ohm—centi—
`meters)‘ , generally the conductivity should
`be at
`least 10‘1 (ohm-centimeters)"1. More—
`over,
`the thin spinel coatings appear
`to
`exhibit greater conductivity as the electrodes
`are used as anodes in the electrolysis of
`aqueous sodium chloride to- produce chlorine
`and sodium hydroxide. Thus, some electro-
`catalytic effect may play a role in the elec—
`trolytic processes herein contemplated.
`The temperatures which have ben resorted
`the preparation
`of
`spinels,
`typically
`to
`ranging from 750°C.
`to 1350°C., are far
`
`above the temperature which decompose and
`volatilize various compounds of
`the oxida-
`tion inhibitors and the binding agents and,
`in a normal atmosphere oxidize the surface
`of the substrate. For this reason when the
`spinel
`is formed in contact with the sub-
`strate, as for example,
`from mixed oxides
`of the metals, the substrate or support mem-
`ber may suffer some degree of oxidation and,
`in such a case,
`the electrode may show a
`much higher voltage than is desirable. But
`when the spinel
`is formed prior to being
`applied to the substrate or support member,
`the highest temperature that the member is
`exposed to is the higher of either the decom-
`position temperature of the oxidation inhibitor,
`the liquid solvent, or of the binding agent
`compound, and the degree of oxidation of the
`member is negligible.
`the
`is desirable that
`For this reason,
`it
`spinel be formed prior to being applied to
`the support member. This can be accom—
`plished by oxidation of the mixed metals,
`or by mixing and subsequent heating of the
`mixed oxides, or by coprecipitation from
`solutions of compounds of
`the metals fol-
`lowed by heating or by thermal decomposi-
`tion of compounds of the mixed metals. The
`preferred compounds are those which decomh
`pose directly to the oxides on heating and
`do not leave a residue as carbonates, form-
`ates, nitrates, and oxalates, e. g.:
`
`A
`
`Coco,.+A1,(co_.)s —> CoO+A1203 +4c021~
`
`A
`
`The resulting product is an intimate mixture
`of the two oxides which can be heated to
`form the spinel.
`Various procedures may be resorted for the
`preparation of spinels to be used as elec—
`trode surfaces. For example, spinels may be
`prepared from the mixed oxides. Cobalt-
`aluminum spinel,
`copper—aluminum spinel,
`and nickel—aluminum spinel were prepared
`from the mixed oxides. The general pro—
`cedure was to grind stoichiometric amounts
`of the oxides to minus 200 mesh (U.S. Stan-
`dard Sieve Series), mix the ground oxides
`together, place the mixed, ground oxides in
`a crucible, and heat the mixed, ground oxides,
`thereby forming the spinel.
`Another mixed oxide procedure may be
`utilized for the iron—aluminum spinel having
`the stoichiometric formula FeH(FemAl)04.
`By this method the iron-aluminum spinel is
`prepared from the mixed oxides Fe203, FeO,
`and A1203, according to the following pro-
`cedure
`described
`in Blue
`and Claassen,
`Journal of
`the American Chemical Society,
`71, 3839 (1949) and Couglin, King and
`
`the American
`of
`Journal
`Bonnickson,
`Chemical Society, 73, 3891 (1951).
`According to this procedure, FeO was first
`prepared by heating metallic iron and FegOg
`in the presence of water vapor. The reactions
`believed to be taking place are:
`
`Fe+H20 ——>~ FeO+Hz
`
`Fe304+H2 —> 3Fe0 +H20
`
`The FeO prepared as described above,
`Page, and A120,, all ground to minus 200
`mesh (US. Standard Sieve Series) were
`mixed and heated under a vacuum overnight
`at
`a
`temperature of
`about 110°C. The
`material was then heated to 1200°C., under
`vacuum, for 24 hours. The resulting product
`was black, magnetic material exhibiting the
`X-ray diffraction pattern reported in the
`literature to be characteristic of the
`
`FeU(FeIIIA1)o.
`
`spinel.
`
`10
`
`15
`
`20
`
`25
`
`30
`
`65
`
`7O
`
`75
`
`80
`
`85
`
`90
`
`35
`
`40
`
`45
`
`50
`
`55
`
`60
`
`95
`
`100
`
`105
`
`110
`
`
`
`1,346,369
`
`Spinels may be prepared by precipitation
`from nitrate solution, followed by oxidation
`of the precipitate to yield the spinel. Copper~
`aluminum,
`copper-chromium,
`copper-iron,
`cobalt—aluminum,
`and
`cobalt—chromium
`spinels,
`inter alia, were prepared by pre-
`cipitation from the nitrate solutions. The
`general procedure was to: prepare an aqueous
`solution 0.5 molar in the nitrate salt of the
`divalent metal and 1.0 molar in the nitrate
`salt of
`the trivalent metal. This solution
`was evaporated to dryness by heating the
`solution to a temperature between 125°C.
`and 140°C. The dried product was then
`heated in an air—aspired furnace to drive off
`the nitrogen compounds, yielding thereby a
`mixed oxide. The mixed oxide was then
`ground to a powder which was then heated
`in a furnace to a temperature sufliciently
`high to form the spinel.
`,
`Spinels useful for electrode coatings may
`also be
`prepared. by precipitation from
`oxalate, and subsequent oxidation. A solution
`of MgSO, and FeSO4 in distilled water was
`prepared. The solution was then filtered. The
`filtered solution was heated to boiling and
`ammonium oxalate and oxalic acid were
`added to the solution with stirring. Boiling
`and stirring were continued until a precipit-
`ate appeared. The resulting precipitate was
`filtered and washed. The washed precipitate
`was then dried and the dried product was
`placed in a porcelain crucible and heated to
`a temperature of 500°C, held at
`the tem-
`perature of 500°C. for 10 minutes and then
`slowly cooled to room temperature. The
`resulting product was ground to minus 200
`mesh and then heated to 950°C. and held at
`950°C.
`for 7-;— hours,
`thereby yielding the
`spinel.
`Spinels may also be prepared by ammo-
`nium carbonate
`precipitation
`from the
`chloride
`solution
`ammonium carbonate.
`Nickel—chromium,
`nickel—aluminum,
`cobalt-
`aluminum,
`and
`copper—chromium spinels,
`inter alia, were prepared by precipitation
`from chloride solutions. The general pro-
`cedure was to prepare a solution containing
`the chloride salts of the di— and tri-valent
`metals. To- this solution was added ammo—
`nium carbonate. The
`solution was
`then
`stirred under a nitrogen blanket and the
`precipitate which formed was separated by
`centrifuging under a nitrogen atmosphere.
`The centrifugate was dried under a nitrogen
`atmosphere and the solid material ground
`and heated under vacuum for 72 hours, there—
`by yielding the spinel.
`Spincls may also be prepared by ammo-
`nium hydroxide
`precipitation
`from the
`chloride solution. In this prOCedure, a solu-
`tion was prepared from stoichiometric quan-
`tities of the two chlorides. To this solution
`was added a concentrated solution of ammo-
`nium hydroxide. The resulting mixture was
`
`10
`
`15
`
`20
`
`25
`
`30
`
`35
`
`40
`
`45
`
`50
`
`55
`
`60
`
`65
`
`stirred until a precipitate appeared. The
`resulting precipitate was separated and dried.
`The dried precipitate was ground to minus
`100 mesh (U.S. Standard Sieve Series) and
`placed in a covered crucible which was
`placed in a vacuum furnace under a vacuum
`of 10‘5 millimeters of mercury and heated
`to a temperature of 900°C. or greater and
`maintained thereat
`for 24 hours,
`thereby
`yielding the spinel.
`Depending on the method of forming the
`mixed oxide and the degree of comminution
`thereof,
`it is possible that all of the mixed
`oxide will not necessarily be converted to a
`spinel but
`that
`some will
`remain as
`the
`original oxide. This has no deleterious effect
`on the anode. The less soluble oxides, as
`A1203, will
`remain on the anode without
`deleterious effect, while the more soluble
`oxide, as COO or NiO, may be dissolved by
`the anolyte when the finished electrode is
`employed as an anode.
`reportedly have
`Also FeEO3 and A120,.
`structures which permit significant quantities
`of either or both to be present in the spinel
`lattice without deleterious effects, and with—
`out being readily detectable by X—ray diffrac—
`tion.
`The preferred spinel usually is applied
`together with a binding agent. These agents
`include organometallic compounds which, on
`heating, decompose to the metal or metal
`oxide and volatiles as well as more permanent
`binders.
`the
`Typically, regardless of the substrate,
`spinel must be made to adhere to the oxy—
`compound of
`the second transition series
`platinum group metal. This may be accom-
`plished by providing a lattice or network
`within the spinel, with a suitable permanent
`binding agent, whereby the adherence of the
`spinel to the intermediate layer of said oxy-
`compound is enhanced.
`A suitable permanent binding agent has
`to be impervious to the chlorine environ-
`ment of the electrolytic cell as for instance
`a metal compound, such as an oxide, sulfide,
`nitride, boride, or carbide of titanium,
`tan-
`talum, niobium, aluminum, bismuth, tungsten,
`molybdenum, zirconium, hafnium, vanadium,
`chromium, or silicon. It has been found that
`particularly good binding results are obtained
`by the formation,
`in sitzc with the spinel
`coating, of a metal oxide that is substantially
`non—reactive with the anolyte. The formation
`of this oxide, in situ, must, moreover,
`take
`place at a temperature below the temperature
`at which any appreciable oxidation of the
`structural member occurs or any adverse
`effect on the undercoat occurs. For
`this
`reason,
`the thermal
`decomposition
`of
`a
`readily decomposed compound having vola—
`tile decomposition products as, for instance,
`an oxalate, carbonate, hydroxide, hydrated
`oxide, or
`resinate of
`titanium,
`tantalum,
`
`7O
`
`75
`
`80
`
`90
`
`95
`
`100
`
`105
`
`110
`
`115
`
`120
`
`125
`
`130
`
`m
`
`
`
`
`
` 7 1,346,369 7
`
`
`
`5
`
`10
`
`20
`
`25
`
`30
`
`35
`
`40
`
`45
`
`is built up
`the spinel content
`formed until
`bismuth,
`aluminum,
`silicon, molybdenum,
`to the desired thickness, usually the process
`tungsten, niobium, or
`zirconium, hafnium,
`of brushing and heating being repeated by
`vanadium may be used. Generally the more
`permanent binders are inorganic. Titanium 7 to 20 times. It is to be understood that
`compounds are preferred. Whenever titanium satisfactory results may also be obtained
`dioxide is described as a binding agent, it without heating after every coat of spinel so
`will be understood that other binding agents
`long as the resinate is ultimately decomposed.
`as herein described may be used in lieu of The resulting surface, 200 to 400- micro—
`or in addition thereto.
`inches thick, has 0.02 to 0.04- gram of spinel
`the permanent
`Small
`concentrations of
`per square inch of spinel coated anode sur— 75
`binding
`agent
`are
`e
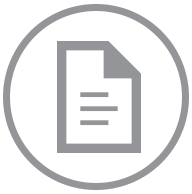
Accessing this document will incur an additional charge of $.
After purchase, you can access this document again without charge.
Accept $ ChargeStill Working On It
This document is taking longer than usual to download. This can happen if we need to contact the court directly to obtain the document and their servers are running slowly.
Give it another minute or two to complete, and then try the refresh button.
A few More Minutes ... Still Working
It can take up to 5 minutes for us to download a document if the court servers are running slowly.
Thank you for your continued patience.
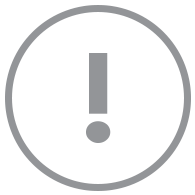
This document could not be displayed.
We could not find this document within its docket. Please go back to the docket page and check the link. If that does not work, go back to the docket and refresh it to pull the newest information.
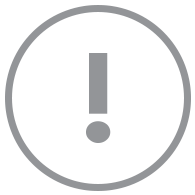
Your account does not support viewing this document.
You need a Paid Account to view this document. Click here to change your account type.
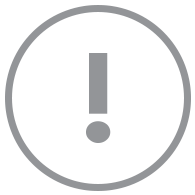
Your account does not support viewing this document.
Set your membership
status to view this document.
With a Docket Alarm membership, you'll
get a whole lot more, including:
- Up-to-date information for this case.
- Email alerts whenever there is an update.
- Full text search for other cases.
- Get email alerts whenever a new case matches your search.
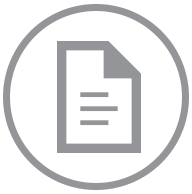
One Moment Please
The filing “” is large (MB) and is being downloaded.
Please refresh this page in a few minutes to see if the filing has been downloaded. The filing will also be emailed to you when the download completes.
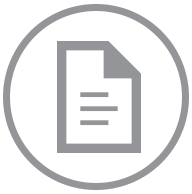
Your document is on its way!
If you do not receive the document in five minutes, contact support at support@docketalarm.com.
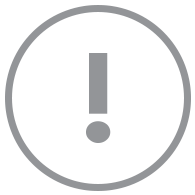
Sealed Document
We are unable to display this document, it may be under a court ordered seal.
If you have proper credentials to access the file, you may proceed directly to the court's system using your government issued username and password.
Access Government Site