`
`W02014109347
`
`Sign in
`
`Patenffi,
`
`English
`
`French
`
`Japanese
`
`.Wm“““l
`
`: Find prior art
`
`““‘W
`s this application E
`
`
`I}
`
`v
`
`Poly-l-lactlc aCld solidified and ext-rusmn-
`molded article, method for producmg same,
`-
`-
`in? use applications Of same
`sets 2034109347 A1
`
`ABSTRACT
`A poly-L-lact:c aCld (PLLA) solidified and extrusion~molded article which
`_
`comprises a resin material containing a PLLA haying a weight average
`molecular weight of 100,000 to 380,000, a melt ViscoSlty (temperature. 2407;,
`shear rate: 120 sec?) of 20 to 2,000 Pa‘s and an L—form content of 80 to 100%.
`
`and has a thickness or diameter of 10 to 500 mm and tensile strength of 5 to
`100 MPa at 66"C (wherein the article may additionaily contain a filler; in this
`
`Publication number
`Publication type
`Application number
`Publication date
`Filing date
`Priority date
`
`Also published as
`
`Inventors
`
`Applicant
`Export Citation
`
`“02014109347 A1
`Application
`PCTIJP2014/050184
`Jul 1.7. 2014
`Jan 9, 2014
`Jan 11. 2013
`
`oAzsarasom. cameras-ac
`CN'30493FGSOA. i)82015033541311
`
`tw‘lasayuki Okui'a, 3:1:‘5’ AESVE:
`
`‘lakeo Taltahashi Hiroyuiizl Sate. it;
`.
`Kureha Corporation, ~, =':'_
`
`BiBTex EndNote. RetMan
`
`
`_ Referenced by 54:: Classifications tel},
`Patent Citations i‘
`
`---’
`2-393; EVEN-3 ‘-
`L
`
`case the tensile strength of the article may be 5 to 200 MPa): a downhole tool
`member or ball sealer for well drilling use. which is formed by machining the
`solidified and extrusion—molded article; a sealing plug equipped With the
`downhole tool member; a method for producing a PLM solidified and extrusion~molded article, which comprises the steps of supplying a resin material containing a
`PLLA into an extruder. carrying out the solidification and extiu5lon molding of the resin material, pressurizing the resultant solidified and extruded product. and then
`drawing the pressurized product while applying a back pressure in the direction of a forming die to thereby prevent the expansion of the solidified and extruded
`product; and a wet: drilling method
`
`External Links: Patentscope Espacenet
`
`
`HIAGES
`
`Diz'thRiP'l‘iO?\
`
`l
`
`
`
`‘ J "r Japanese
`
`(ILAifViS £3?)
`
`tr
`
`
`
`ed from Japanese
`
`Poly ~t.~ lactic acid solidified extrudate and its manufacturing method and its
`application
`
`1. The weight average molecular weight of 100.000 to 380,000, a
`
`temperature of 240 "C and an :\ rate melt viscosity measured at 1205ec
`
`The present invention relates to poiylactic acid ~L- solidified extrudate and a
`method for producing the same and their applications. More particularly, cutting
`dl'iiiingi deSlred secondary molded product thickness which can be molded into
`or diameter of the polylactic acid -L- solidified extrudate shapes and a method
`of manufacturing by machining such as cutting, as well as, on the downhole tool
`member and well drilling method ball sealer or for well drilling for the weil drilling
`
`‘1 is 20 ~ 2,000Pa - s, and, L form proportion of 80-100% made of a resin
`material containing a polylactic acid -L- has a thickness or diameter of 10
`~ 500mm, a tensile strength of 5 ~ 100MPa at a temperature 66 "C’
`polylactic acid -l_— solidified extrudate.
`
`is formed from the poly «L— lactic acid solidified extrudate. Resin mottled product having a three-dimensional shape or complex shape. is
`
`generally molded by injection molding According to the injection moiding. it is
`possible to mass-produce a molded product having a destred shape However,
`in order to produce by ihiection molding a molded product that require high
`dimensmnal accuracy. it is necessary an expensive mold having a high
`
`P
`i
`dimenswnai accuracy Moreover. lflleCthii molding, since it is easny deformed
`by the shrinkage and resrdual stresses after the injection molding. and
`depending on the properties of the molded product of the shape and the reset
`material. it is necessary to preciseiy adjust the die shape. in injection molding.
`because of the high failure rate, often the product is costly. Further in the
`
`3_ The weight average molecular weight of 1001000 to 350‘000. a
`temperature of 240 of and shear rate melt viscosity measured at 1205ec
`‘1 is 20 ~ 2,000Pa s, and, L form proportion of 80-10095 with poly —L-
`add, :5 resin materiai containing 5 to 70 wt% of the filler in total amount
`(the total amount of the resin material is 100 wt%). and has a thickness
`or diameter of 10 ~ 500mm > poly lactic acid 4: solidified extrudate
`
`
`3:
`4. n
`f;
`
`'0. A,
`.
`a ‘.'m \«xax
`Try the new {mingle Patients with machinectasslt‘ssd (Boogie Schoiar results, and Japanese and South~ hereon patents.
`
`https:fl’www.google.com/patentstOZO14109347A1'25ci=en&dq=W02014109347&h1:en...
`
`10.51 U201 7
`
`
`
`Patent W02014109347A1 — Poly-l-lactic acid solidified and extrusion-molded article, met... Page 2 of 20
`
` :nn molding there is a shrinkage and residual stress. it is difficult to mold a
`large ...olded product thickness
`
`in order to obtain a molded article having a three-dimensional shape or a
`complicated shape, the resrn materiai is extruded, flat, round bar, pipe, a
`material for machining having various shapes such as atypical products
`5material?or cutting“ is referred to it have) were prepared, cut into the machine
`for processtng materiai, drilling a method of molding a secondary molded article
`having a desired shape is subjected to mechanical processing such as cutting,
`are known, The method of machining a materiai for machining, since it requires
`no expensrve molds can be produced to yield low molding at relatively low cost,
`it can cope with frequent changes in the specifications of the molding.
`dimensionai accuracy that a high molding was obtained, and has advantages
`such that it is possible to manufacture a molded product having a complicated
`shape and a large thickness which is not suitable for iniection molding
`
`However, in any plastic material or extrudate, it is not suitable for the material
`for machining, The material for machining. for example, it is excellent in
`mechanical workability in thickness the residual stress is small
`it does not
`
`cause deformation and distort-3: Lian overly heating to the frictional heat
`
`ng with high precision such that it can
`generated during machining, the mac
`have been required to satisw a high degree of required properties
`
`The machining of polymeric material, in general, most of the processmg
`methods used in the metallic material is used as is. Be formed by extruding,
`conventional film or sheet, iarge flexibility in thin such tubes are not suitable for
`mechanical processing such as cutting, Even extrudate having a shape, such
`as thickness or diameter is large flat or round bar. extrudate residual stress
`during extrusion is too large. easiiy deformed after the time of machining or
`machining, dimensional accuracy it is difficult to obtain a high secondary
`molding Restriual stress may be an extruded product with reduced. cutting,
`driil--ng which tends to generate cracks or cracks at the time of mechanicall
`processing such as cutting, not suitable material for machining.
`
`To obtain material for machining with characteristics suitable for machining by
`‘t of the resin material, a
` extrusion molding, i
`
` necessary to devote the se'
`
`contrivance such as the extrusion molding method Therefore, conventionaiiy.
`by usrng a resin material containing a generai~purpose resin. engineering
`plastics. for extrusion molding method for the production of extrudates suitable
`for material for machining. various proposals have been made,
`
`For example. Patent Document 1, polyetheretherketone, poiyetherimide,
`polyphenyiene sulfide, pclysuifone, polyether sulfone, and solidified extrusion—
`rnolding a resm composttion containing engineering plastic such as
`polycarbonate 3mm excess thickness or diameter Method for producing a
`material for machining withis \.is
`
`On. the other hand, as a friendly polymer materials environmentally degradable
`plastics have been focused, extrudates such as films and sheets. blow molded
`articles, such as bottles. application deployment have been made to such as
`injection molding. in recent years, it is also required increased for application to
`a biodegradable plastic of machining for the material.
`
`Poiylactic actd is known as a representative biodegradable plastic, because it
`has a moderate rate of degradation, depending on the application and the
`environment it is a biodegradable plastic which are preferably used. Furtherr
`
`poiylactic acid, greenhouse effect gas circulating Sir
`:t is a polymeric material
`obtained by polymerizing the lactic acid obtained by fermenting a sugar taken
`from the plantwderived raw materials such as maize, even when the combustion
`process in the enVironment it has a carbon offset property that does not
`increase the emissions of CO 2 :5
`
`By the way, from the growing interest in the resource constraints. oil (shale oil,
`etc.) -:‘in the present invention. may be sxrnply referred to as "Oil“.l Hydrocarbon
`
`rytheneii‘s oogleafiyategn33.??th rgachignnaoi asgait (300555331: olar
`.. e‘o
`rb nsfro.
`etc) hd
`as s e
`esofwurces 3 ch as
`
`f,{.i:’}:i':t}in any one c‘
`a :"C wedge Li-
`ruins and Japanese anddiwttblbammmemat:ne .
`
`
`
`t
`
`.n'
`
`t
`
`r
`
`,
`
`.
`
`in.-x!"x -
`
`e \ .‘\."\-—\ an"? .
`
`5 (‘x
`
`1
`
`r.-
`
`V
`
`‘?§F{‘\F\:‘.
`
`:
`
`a \ nnvx j"? in t
`
`1
`
`‘ net 1.14"}
`
`A1 “s
`
`{ft-3U
`o'irig to any
`
`at?- or more aspect ratio
`
`
`€39 ELZCOi'
`
`"(iii:
`
`
`
`rem rt.im
`
`
`
`
`
`15.
`therein: 14 w
`' gpiug acmrdirig
`to th:
`.
`
`who of the Outer diameter of the hoiiow portion
`
`hub;
`
`am one of t
`
`uh K‘-
`
`18.
`
`
`
`to ": ? havini‘\ po-n‘mi.‘
`
`
`
`
`
`
`
`Patent WO2014109347A1 - Poly—l-laotic acid solidified and extrusion—molded article, met... Page 3 of 20
`
`or the at toast one ax;
`
`a...“
`l"l'\
`’3
`
`sted their:
`
`'
`
`. the tapped pontion and at
`tciaim 24 which i.
`‘
`
`
`:.
`
`including the For downhole provided li’l order to perform well driiling for
`recovering hydrogen resources (holes provided for forming an underground
`welibore.
`weli or well. such as gas weiis). even higher depth of the
`enlargement progresses They are out. For example, in a horizontal welt bore.
`which is formed by embedding a substantially horizontally in the shale layer or
`the iike over the underground 1,000m. a method of performing hydraulic
`fracturing (the fracturing} has become widespread. Ball sealers and for sealing
`perforations of (fractures) formed by hydraulic fracturing. downhole tools for well
`di‘dili‘lQ that is installed downhole in order to carry out the hydraulic fracturing
`(hereinafter simply be referred to as "downhoie tool" a} a is Flack plug. bridge
`plug. packer. such as the sealing plug, such as a cement retainer is to stop eye
`the place that made the hydraulic fracturing before and place of the vicmity of
`the distal end of the down hole. new. or again by carrying out the hydrauilc
`fracturing, after forming a perforation (fractures). and is recovered or destroyed,
`
`Therefore,
`1 ball sealers. welt drilling for the downhole tool member provrded
`in the downhole tool such as the sealing plug (hereinafter sometimes referred to
`simply as "downhole tool member“). l bear in hydraulic fracturing and laying
`strength (eg. tensrle strength} and which has a cost. ease of recovery or
`destruction is sought.
`
`Flack plugs. bridge plugs. packers. cement retainer. etc. of the seating piug
`(hereinafter. simply referred to as "piug“.} ls rubber usually around a mandrel
`plug (sometimes referred to as "mandrel" ) It is of the structure in which
`mounting Say of sealing member. the sealing mechanism of the sealing plug.
`the tensile and f or compression of the core rod (mandrel). rubber express
`sealang action by deforming (Patent Documents 2 and 3). The SIZe of the plug
`core rod (mandrel) as the maximum inner diameter of the downhole. as long as
`it Is possible to attach a rubber-made sealing member around and formed into
`any predetermined outer diameter. often 70 it is ~ ‘lOOmm. Moreover. mandrel
`plug (mandrei). many in order to pass the mud has a hollow shape. the hollow
`
`has
`often 10 ~ 50mm. typically 19 1mm (0 75 inches} 25 4mm (‘- inch).
`and a 31.8mm (1.25 inch}. for example. the main portion of the piperiike shape
`of the length ofabout 1.000mm. at both ends and pulling the seed rod (mandrel)
`and r' or Jig for performing compression is a shape with the enlarged diameter
`portion so as to be able to engage the. in the tensile and i or compression of the
`plug core rod (mandrel). about 1500 ~ 5,000kgf (about 14.700 ~ 49.000N}. in
`many cases. about 2.000 ~ 4.500kgf (about 19 _, subjected high load of 600 ~
`44.100N) is the core bar (mandrel). in particular, the core rod (engaging portion
`Wlth the aforementioned diameter expansion portion (jig of the mandrel». 2—5
`times of stress Because the concentration is. it is necessary to select a material
`that has the strength to withstand these high loads.
`
`27.
`
`Foltowing steps 1 through 4;
`1) weight average molecular weight of 150,000 to 540,000, temperature
`
`240 °C and a shear rate of tZOSec ‘1 in the measured melt viscosity of 30
`~ 3.000Pa - s, and poly-L-body ratio is 80-100% The resin material
`containing -L- lactic acid, is fed to an extruder and melt-kneaded at a
`cylinder temperature of 195 ~ 260 °C extruder step 1.
`2) from the extrusrorl die of the extruder tip. a restn material which is
`melted by melt-kneading. a channel having a cross-sectional shape of
`the molten resin passage and communicating and extruded product of
`the extrusion die. the forming die and a cooling means step of extrusion
`into the flow channel 2;
`3) it is solidified by cooling the forming die flow path melt extrudate
`comprising a restn material. then step 3 is extruded solidified extrudate to
`the outside from the tip of the forming die; a and 4) solidifying the
`extrudate is pressurized Te. and receipt while applying back pressure in
`the forming die direction, that time. by suppressing the expansion in the
`thickness direction or radial direction of the solidified extrudate by
`pressure. the thickness or diameter obtain a solidified extrudate of 10 -~
`500mm Step 4;
`10 to have a thickness or diameter of 500mm. the production method of
`
`poly
`0 acid -L- solidified extrudate tensile strength at a temperature 66
`°C is 5 ~ 100MPa including the.
`
`28.
`
`Following steps 1 ’to 4;
`l
`') weight average molecular weight of 150.000 to 540.000, temperature
`
`After the implementation of the hydraulic fracturing IS, it can recover the sealing
`member. a method of or destroy the core rod (mandrel) for forming an opening
`is adopted. As the mandrel oi the plug (mandrel). conventionalty. since the
`metal of the cast iron or the like is used. it takes a high cost in recovery of the
`sealing plug. the difficulty in breaking of the metal core bar (mandrel: was a
`difference To the high cost. The plug core rod (mandrel). have come to be
`carried out the use of epoxy resin compostte material or the like. However. restn
`composite material such as an epoxy resin composite material. the strength is
`not sufficrent. it takes a high cost for the recovery of the sealing member :s the
`same resm and reinforcing material after breaking the core rod (mandrel)
`(carbon fiber. metai fiber. etc.) because it is non-degradable treatment or
`disposal i have a problem is virtually :mpossible.
`
`240 °C and a shear rate of tZOSec “ in the measured melt viscosity is 30
`~ 3.000Pa s and. is a Luisomer ratio is 80-“loo% with poly -L- acid. a
`resin material containing 5 to 70 wt% of the filler in total amount (the total
`amount of the resin material is 100 wt%.). was fed to an extruder.
`extruder cylinder temperature 195 is melt-kneaded at ~ 260 °C step t ‘;
`2) from the extrusion die of the extruder tip. a resin material which is
`melted by melt-Kneading. a channel having a cross-sectional shape of
`the molten resin passage and communicating and extruded product of
`the extrusion die, the forming die and a cooling means step of extrusion
`into the flow channel 2;
`3) it is solidified by cooling the forming die flow path melt extrudate
`comprising a resin material. then step 3 is extruded solidified extrudate to
`the outside from the tip of the forming die; a and 4) solidifying the
`extrudate is pressurized Te. and receipt while applying back pressure in
`the forming die direction. that time. by suppressing the expansion in the
`‘i’ry the new (Boogie Patents. wltn mashinwolassified (Beagle echoiar results, and Japa‘lflfiflééWflttoiPfifidfiFfiflé‘bfion of the solidified extrudate by
`
`Also, the ball sealers are aiso conventionally made of non-degradable material
`of the rubber~~coated nylon, or the like nonmdegradable plastics and aluminum.
`
`such as a phenolic. resm. for sealintd '
`*. if necessary. to compare that
`the diameter 16 - 32mm those target small has been used However. in recent
`years. with an increase in depth of the size of the downhole have larger
`diameter. for example a diameter of 25 ~ 100mm. or even a large diameter. a
`request for a bail sealer having a strength to withstand a high load is spread
`
`httpsz/i’www.googlc.cornipatcnts/WOZO14109347A1?cl===en&dq:WO2014109347&hl=en...
`
`10;"111’2017
`
`
`
`Downhoie too: member or ball sealers {hereinafter sometimes referred to as
`
`“downhole tool member. and the like" )AS, without recovering the ground -
`
`use. it can be disintegrated by keep leaving in the downhole S
`it is, the use
`of degradable plastics is expected. Specifically. it has a suffiCient strength
`(temperature environments in excess of 65 ”Cl environment that exceeds the
`underground 1.000rn, diverse together are capable of forming a downhole too:
` ‘= in step a so
`unified extrudate obtain
`as “M ..
`..
`members such as the desired shape and depth degradable plastic and a
`molded product such as a possible decomposition is adapted to be determined
`‘(0
`:2 oi m. whee“- lumen
`..
`.-:, -)
`‘ :. 5 ottne neat tieatment {em
`pinata-e. d1 (W133
`in the environment (ie various temperature environments).
`
`
`
`'~l‘“‘\.g ball sealer according to '
`-. part or all of the we .
`
`doomnposerj into alter the se
`um.“
`the walleye dn=ling
`
`'
`
`~
`
`Patent W02014109347A1 - Poly-l-lactic acid solidified and extrusion—molded article, met... Page 4 of 20
`
`pressure. the thickness or diameter obtain a solidified extrudate of 10 ~
`500mm Step 4;
`10 to have a thickness or diameter of 500mm, the production method of
`polylactic acid ~L— solidified extrudate tensile strength at a temperature 66
`"C is 5 ~ 200MPa including the.
`
`However. many of them with a degradable plastic is a crystalline resin iniection
`molding or compression molding, by a general purpose method of a resm
`molding, such as melt extrusion molding, and to produce a molded product,
`such as a downhole tool member. after shaping it { shrinkage and voids due to
`shrinkage accompanying the thermal contraction and crystallization after
`
`39'
`
`
`‘
`.
`.
`
`molding) occurs, the dimensional accuracy required is not obtained. Therefore,
`in order to obtain the downhole tool member such as a method in which the
`
`.51,
`
`thickness or diameter formed by the solidification extrusron molding from a
`degradable plastic machining such as cutting large solidified extrudate has
`attracted attention.
`
`
`
`Polylactic acid, a representative biodegradable plastic. it is known to use in a
`wellbore. such as on drilling Patent Document 4, weilbore treatment fluid
`vrscosrty containing polyiactic acid, together with the sand control screen or coating. mechanical devaces or components
` rhc dos-:1 :s disclosed as a mechanical device. the packer . bridge plug or
`thereof are arranged in iuchi pit formed poly-i
`cement retainer etc. are exemplified.
`
`\\\\\\\\\\\\\\\\\\\\\\\\\\\\\\\\\\\\\\\\\\\\\\\\\\\\\\\\\\\\\\\\\\\\\\\\\\\\\\\\\\\\\\\\\\\\\\\\\\\\\
`
`Patent Document 4. furthermore, from a crystalline poly -D- lactide (polylactic add). the bending strength of the rod-
`
`shaped body to be manufactured by :n when molding. it is in the range of 40 ~ l40MPa. and is solidified by extrusion rod-
`shaped body to be formed is described as having a flexural strength of up to ZOOMPaK refer to "Biomateriais 17 (March
`
`1996, 529—535)“ (Non—Patent Document l). Non-Patent Document 1.. as a "soli
`‘
`:19 improvement in mechanical
`properties of the polylactic acid by extrusmn". My {viscosity average molecular weight) of 160,000 rod from a poly-lactide
`»D- become solidified Circular cross section manufactured by extrusion of There are listed, the mechanical properties of
`yield bending strength, etc. of the solidified extrudates are disclosed specifically a round bar having a diameter of 4mm
`
`A round rod in a solidified extrudate diameter 4mm disclosed in Non—Patent Document 1. specrficaliy. the shape and see of
`the downhole required along with a high depth of the size of the recent dcwnhoie it is not possible to form a tool member.
`and the like. Then. the solidified extrudate rod-shaped body or the like formed from poly —D- lactide as disclosed in Patent
`Document 4 or Non~Patent Document 1. since the glass transition temperature of the polylactic aCld is a 55 ~ 60 "t“. it has
`sufficient strength (temperature environments in excess of 65 “Cl environment that exceeds the aforementioned
`underground 1,000m, whether those capable of forming a downhole tool members such as the desrred shape was
`unknown.
`
`Patent Publication No. 2005—226031 {US PatentAppllcation Publication No. 20081038517 Patent specification
`correspondence) US Patent Application Publication No. 2005/205265 US Patent Application Publication No. 33:}: 1/277989
`US Patent Application Publication No 20041231845
`
`" Enhancement of the mocha-meal Properties of Polylactzdes by sc=id state extrusion Biomaterials 1996. Vol 17, No.5
`(1996952). pp 529 ~ 535
`
`The object of the present invention has a setting, drilling. secondary molded article having a desired shape by mechanical
`
`. merits in excess of 65 “(i‘) environment
`processing such as cutting. in particular a sufficient strength (temperature envi
`that exceeds the underground 1.000m. The present invention is to provide a desired solidified extrudate of biodegradable
`plastics which can be formed downhole tool members such as the shape and manufacturing method. and its applications
`
`The present inventors have found. as a result of :ntensive studies to solve the above problems, by the ratio of L- lactic acid
`is to select a high poiylactic acid. in an enVironment (greater than 65 "t‘ temperature environment, etc.) that exceeds the
`underground '3 ,C-OOm . and it found that the solidified extrudate having excellent strength that can not be anticipated from
`the solidified extrudate formed from polylactic —D- acid disclosed in Patent Document 4 is obtained, and have completed
`the present invention.
`
`That is. according to the present invention, the weight average molecular weight of 100.000 to 380,000, the melt Viscosity
`
`measured at a temperature 240 *1: and a shear rate of izosec "' is 20 ~ 2‘000Pa ~ s, and, i. Body ratio made ofa resrn
`material containing 80~100% of the porylactic acid -l_- has a thickness or diameter of 10 ~ 500mm. poiylactic acid -L-
`solidified tensile strength at a temperature 66 ( as 5 ~ tOOMPa extrusion molded product is provrded.
`Try the new Googie Patients; with machine-classified Googia Scholar results, and Japanese and South Korean patents.
`
`httpscr'fwww. googlc.com/patentsr’W020 1 41 09347A] ?clficn&dq=W02014109347&h1:en...
`
`10.3’11/2017
`
`
`
`Patent W02014109347A1 - Poly-l-lactic acid solidified and extrusion-molded article, met... Page 5 of 20
`
`As aspects of the present invention, resin material. wherein the polylactic acrd ~L- solidified extrudate is poly -L— aCid
`
`composition some,
`j: b: to 70% by weight of filler based on the total quantity is provided .
`
`According to the invention the weight average molecular weight of 100,000 to 380000, the melt viscosity measured at a
`
`temperature 240 ”C and a shear rate of lzosec ‘7 is 20 ~ 2,000Pa > s, and. L body ratio of 80 and to 100% poly ~L— lactic
`acid (to a total volume of 100 mass% of the resin material.) The resin material containing 5 to 70 wt% of the filler in the
`total amount consists of, 10 ~ 500mm have a thickness or diameter of a tensile strength of 5 ~ ZOOMPa at a temperature
`of 66 '(i' poly wL_ lactic acid solidified extrudate is provided
`
`According to the present invention. as a mode of implementation the followrng (i) to polylactic and -L— solidified extrudate
`(is) is provrded.
`{ll filler. wherein the polylactic acid -L— solidified extrudate is fibrous fillers,
`(2) filter, said poly -L- lactic acid solidified extrudate having 100 or more of aspect ratio
`(:3) the resin material for the poly lactic acid —l.- 100 parts by weight, the weight average molecular weight of 100,000 to
`380.000,. the melt viscosdy measured at a temperature 240 ”t‘ and a shear rate of 120sec “l is 20 to a 2,000Pa s, and‘
`the poly --l_~ lactic acid solidified extrudate D body ratio contains poly ~Dv lactic aCid 40-200 parts by weight of 80-10096.
`(4} the poly~lactic add and poly -L- -D~ lactic acid, wherein the poiylactic acid ~L- solidified extrudates which form the
`stereocomplex
`(5} round rod wherein the polylactic acid -L- solidified extrudate havmg the shape of a hollow or a flat,
`
`(6) The poly ~L- lactic cost solic
`l extrudate which is a material for machining.
`
`Furthermore, according to the present invention, the poly ~L- acid solidified extrudate was machined to form the diameter
`of 20 ~ 200mm well drilling ball sealers or well drilling downhole for a material for machining tool member is provided;
`furthermore the sealing plug comprising a downhole tool member for \l\ Drilling is provided.
`
`Further. according to the present invention. sealing with a specific embodiment of the sealing plug with the wellbore drilling
`downhole tool member, the following; {i} well drilling downhole tool member ~ (Xiv) plug is provided.
`{5; the wellbore drilling downhcle tool member,
`a. Mandreit
`b. A pair of rings placed on the outer peripheral surface perpendicular to the axial direction of the mandrel, and:
`c An outer Circumferential surface perpendicular to the axral direction of the mandrel, said sealing plug is at least one
`selected from the group consisting of one or both of the slip or wedge placed in. position between the pair of rings.
`{iii mandrel. said sealing plug having a hollow portion along the axial direction.
`
`mandrel. said sealing plugs ratio of the outer diameter of the hollow portion to the diameter of the mandrel is 0.7 or
`less.
`
`{iv) the mandrel and, said sealing plug is a one ring of a pair of rings are formed integrally
`(V; a mandrel wherein the sealing plug radius of curvature of the working portion of the outer peripheral surface is 0.5mm
`or more.
`
`(\fi) the outer peripheral surface of the mandreil the eyes stop plug having a place that is protected by metal
`{viii on the outer peripheral surface of the mandrel, said of the sealing plug is not provided with the slip and wedge
`Ari outer circumferential surface perpendicular to the axial direction of (will mandrel was placed at a position between the
`pair of rings. said sealing plug comprismg a combination of at least one slip and wedge
`(ix) the slip and the said sealing plug comprising a pluraliiy of combination of the wedge,
`(X; a on the outer peripheral surface perpendicular to the axial direction of the mandrel, one placed at a position between
`the pair of rings, said sealing plug comprising a rubber member of the at least one expandable annular
`(Xi) expandable annular rubber member. the axial length of the mandrel, wherein the sealing plug 10 to 70% the length of
`the mandrel
`
`{Xlii mandrel. said of the sealing plug harm a fixmg portion fixed to remain in the compressed state of the expandable
`annular rubber member of the outer peripheral surface
`(Xsii) a fixed portion: a groove, stepped portions and said sealing plug is at least one selected from the group consisting of
`threads
`
`{Xiv'} expandable annular said of the sealing plug multiple equipped with a rubber member
`
`ln addition. according to the present invention, through the followsng steps 1 to 4.
`1} weight average molecular weight of 150,000 to 540000. temperature 240 “C and a shear rate of lzosec “ in the
`measured melt viscosity of 30 ~ 3.000Pa st and poly-L—body ratio is 80-100% The resin material containing -L~ lactic acid,
`is fed to an extruder and melt-kneaded at a cylinder temperature of 195 ~ 260 “C extruder step 1;
`2) from the extrusion die of the extruder tip, a resin material which is melted by melt-kneading. a channel having a cross—
`sectionai shape of the molten resin passage and communicating and extruded product of the extrusion die, the forming die
`and a cooling; means step of extrusion into the flow channel 32,
`3) i: is solidified by cooling the forming die flow path melt extrudate comprising a resin material then step 3 is extruded
`solidified extrudate to the outSide from the tip of the forming die; a and 4) solidifying the extrudate is pressurized Te, and
`
`receipt while applying back pressure in the forming rile dire: ‘
`a that time. by suppressmg the expansion in the thickness
`Tamer moanmnmmmesmaewnme snaimammmaatew-
`
`https:.r’/www.google.comfpatents/WOZO14109347A1?cl==en&dq==‘A-“02014109347&h1=en...
`
`10/1 1:20] 7
`
`
`
`Patent W02014109347A1 - Poly—l-lactic acid solidified and extrusion-molded article, met... Page 6 of 20
`
`to ~ 500mm Step 4;
`Have a thickness or diameter of 10 ~ 500mm. including a method of manufacturing a tensile strength is 5 ~ 100MPa
`polylactic and -L- solidified extrudate at a temperature 66 "C is provided
`
`Desrred by, according to the present invention, the following steps 1 ‘to 4;
`
`ii weight average molecular weight of 150.000 to 540,000, temperature 240 °C and a shear rate of lzosec “ in the
`1
`measured melt viscosrty is 30 ~ 3,000Pa - s and, is a L-isomer ratio is 80-10096 with poly -L- acid. a resin material
`containing 5 to 70 wt% of the fille.r in total amount (the total amount of the resin material is 1.00 wt%.). was fed to an
`extruder. extruder cylinder temperature 195 is melt-kneaded at ~ 260 °C; step 1 i
`2} from the extrusion die of the extruder tip. a resin material which is melted by melt-kneading. a channel having a cross-
`sectional shape of the molten resin passage and communicating and extruded product of the extrusron die. the forming die
`and a cooling means step of extrusion into the flow channel 2:
`3) it is solidified by cooling the forming die flow path melt extrudate cistersrising a resin material. then step 3 is extruded
`solidified extrudate to the outside from tile tip of the forming die; a and 4) solidifying the extrudate is pressurized Te, and
`receipt while applying back pressure in the forming die direction that time. by suppressing the expansron in the thickness
`direction or radial direction of the solidified extrudate by pressure. the thickness or diameter obtain a solidified extrudate of
`10 ~ 500mm Step 4;
`Have a thickness or diameter of 10 ~ 500mm. including a method of manufacturing a tensile strength is 5 ~ 200MPa
`
`polyiactic acrd
`solidifi.
`..e at a temperature 66 “C is providm,
`
`According to the present invention. poly -L- acid solidified extrudate obtained in step 4. the method of manufacturing
`further comprising is provided a process 5 for the heat treatment 3424 hours at a temperature of 90 ~ :90 “1'
`
`Additionally. according to the present invention, by usmg the wells drilled ball sealers. that some or all of the well drilling
`ba=l sealers are decomposed after performing a sealing treatment of the wellbore well dn‘ilsng wherein the, and, using a
`sealing plug prowded with the wellbore drilling downhole tool member, after carrying out the sealing treatment of the
`weilbore. the downhole tool for well drilling well drilling wherein the part of the members or the whole is decomposed is
`provrded.
`
`According to the present invention the weight average molecular weight of “30-0000 to 380.000. the melt viscosity
`measured at a temperature 240 ”C' and a shear rate of 1205ec "
`is 20 ~ 2.000% , s. and. L form proportion There made of
`a resin material containing 801.00% of the polylactic acid -L-, 10 to have a thickness or diameter of 500mm, a tensile
`strength of 5 ~ 100M Pa at a temperature 66 “if; the desired is 5 ~ ZOOMPa poly molding by being -l.~ lactic solidified
`extrudate. cutting. drilling, secondary molded article having a desired shape by mechanical processing such as cutting. in
`particular. the well drilling downhole tool members or the like provided in the sealing plug It is possible to have sufficient
`strength at (temperature environments in excess of 65 ”C‘) envtroriment that exceeds the underground 1.000rn. degradable
`plastic which is capable of forming a downhole tool members such as the desired shape effect tha
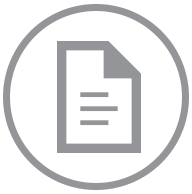
Accessing this document will incur an additional charge of $.
After purchase, you can access this document again without charge.
Accept $ ChargeStill Working On It
This document is taking longer than usual to download. This can happen if we need to contact the court directly to obtain the document and their servers are running slowly.
Give it another minute or two to complete, and then try the refresh button.
A few More Minutes ... Still Working
It can take up to 5 minutes for us to download a document if the court servers are running slowly.
Thank you for your continued patience.
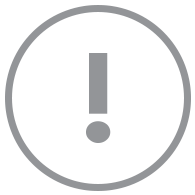
This document could not be displayed.
We could not find this document within its docket. Please go back to the docket page and check the link. If that does not work, go back to the docket and refresh it to pull the newest information.
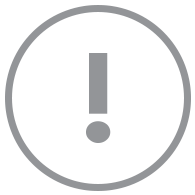
Your account does not support viewing this document.
You need a Paid Account to view this document. Click here to change your account type.
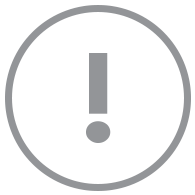
Your account does not support viewing this document.
Set your membership
status to view this document.
With a Docket Alarm membership, you'll
get a whole lot more, including:
- Up-to-date information for this case.
- Email alerts whenever there is an update.
- Full text search for other cases.
- Get email alerts whenever a new case matches your search.
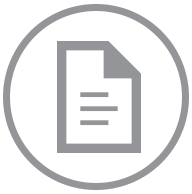
One Moment Please
The filing “” is large (MB) and is being downloaded.
Please refresh this page in a few minutes to see if the filing has been downloaded. The filing will also be emailed to you when the download completes.
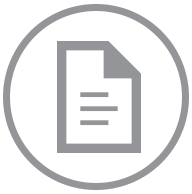
Your document is on its way!
If you do not receive the document in five minutes, contact support at support@docketalarm.com.
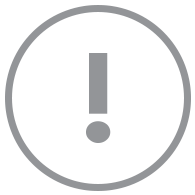
Sealed Document
We are unable to display this document, it may be under a court ordered seal.
If you have proper credentials to access the file, you may proceed directly to the court's system using your government issued username and password.
Access Government Site