`
`CROSS-REFERENCE TO RELATED APPLICATIONS
`
`[0001]
`
`This application is a continuation of US. Patent Application No. 14/810,314,
`
`entitled “LITHIUM-ION BATTERY” filed July 27, 2015, which claimed priority to and
`
`benefits of Chinese Patent Application Serial No. 2014105000741, entitled “LITHIUM-ION
`
`BATTERY” filed with the State Intellectual Property Office of P. R. China on September 25,
`
`2014, all of which are incorporated herein by reference.
`
`TECHNICAL FIELD
`
`[0002]
`
`The present disclosure relates to the field of battery technology, and particularly
`
`relates to a lithium-ion battery.
`
`BACKGROUND
`
`[0003]
`
`Lithium-ion battery has become an ideal power source used in mobile devices for
`
`replacing the conventional power source, due to the advantages of high energy density, high
`
`working voltage, long service life, no memory effect, non—pollution and the like. With the
`
`intellectualization and the multi—functionalization of mobile devices, the power consumption
`
`increases sharply, making a higher requirement to the energy density of lithium—ion battery.
`
`[0004]
`
`Sony has developed lithium-ion battery of graphite type since 1991, and after 20
`
`years of development, the energy density approaches to the limit. While some key problems
`
`for the development of new chemical systems are to be resolved, such as the self-
`
`pulverization brought by the expansion after silicon-based negative active material cycling,
`
`poor high temperature cycling performance of the positive active material at high voltage,
`
`poor stability of electrolyte at high voltage, gas production by the reaction of positive active
`
`material with electrolyte and the like.
`
`[0005]
`
`The promotion of the energy density has run into the bottleneck. To improve user
`
`experience, the development of lithium-ion battery with fast charge at high rate can make up
`
`for the disadvantages of energy density. But when lithium-ion battery is charged quickly at
`
`high rate, the electrode polarization of lithium-ion battery is serious, and the current per unit
`
`area increases, and the negative electrode quickly reaches to the potential of the lithium
`
`precipitation. Plenty of lithium ions diffusing from the positive electrode to the negative
`
`electrode can’t be accepted by the negative in time. The precipitation of lithium on the
`
`024607-02-5014-US
`
`l
`
`
`
`negative electrode surface causes quick fade of the lithium-ion battery capacity. And the
`
`accumulation of lithium dendritic crystal on the electrode surface will impale the separator
`
`easly and pose a big threat to the safety performance of battery.
`
`SUMMARY
`
`[0006]
`
`In view of the problems mentioned in background, the present disclosure aims to
`
`provide a lithium—ion battery, which can be charged quickly at high rate, with excellent safety
`
`performance and cycle performance.
`
`[0007]
`
`In order to achieve above object, the present disclosure provides a lithium-ion
`
`battery, which includes:
`
`a positive electrode including a positive current collector and a positive conductive
`
`membrane which is formed on the surface of the positive current collector by coating, drying
`
`and compacting a positive mixture slurry containing a positive active material, a positive
`
`conductive additive and a positive binder; a negative electrode including a negative current
`
`collector and a negative conductive membrane which is formed on the surface of the negative
`
`current collector by coating, drying and compacting a negative mixture slurry containing a
`
`negative active material, a negative conductive additive and a negative binder; a separator; an
`
`electrolyte; and a packaging foil. The compacted density of the positive conductive
`
`membrane is at a range from 3.9g/cm3 to 4.4g/cm3; the compacted density of negative
`
`conductive membrane is at a range from 1.55g/cm3 to 1.8g/cm3; the ratio of the capacity of
`
`the negative active material to the capacity of the positive active material is at a range from 1
`
`to 1.4, the charging rate of said lithium-ion battery is at a range from 1.3C to SC, in which the
`
`capacity of negative active material / the capacity of positive active material = (negative
`
`coating weight per unit areaX the weight ratio of negative active materials X the capacity per
`
`gram of negative active material)/(positive coating weight per unit area X the weight ratio of
`
`positive active materials X the capacity per gram of positive active material).
`
`[0008]
`
`The benefits of the present disclosure include:
`
`The lithium-ion battery of the present disclosure can be charged quickly at high rate.
`
`[0009]
`
`The lithium-ion battery of the present disclosure has excellent safety performance
`
`and cycle performance.
`
`DETAILED DESCRIPTION OF EMBODIMENTS
`
`[0010]
`
`The lithium—ion battery of the present disclosure is illustrated in details, referring
`
`024607-02-5014-US
`
`2
`
`
`
`to Examples, Comparative Examples and Testing results,
`
`[0011]
`
`First of all, the lithium-ion battery of the present disclosure includes: a positive
`
`electrode including a positive current collector and a positive conductive membrane which is
`
`formed on the surface of the positive current collector by coating, drying and compacting a
`
`positive mixture slurry containing a positive active material, a positive conductive additive
`
`and a positive binder; a negative electrode including a negative current collector and a
`
`negative conductive membrane which is formed on the surface of the negative current
`
`collector by coating, drying and compacting a negative mixture slurry containing a negative
`
`active material, a negative conductive additive and a negative binder; a separator; an
`
`electrolyte, and a packaging foil. The compacted density of the positive conductive
`
`membrane is at a range from 3.9g/cm3 to 4.4g/cm3; the compacted density of negative
`
`conductive membrane is at a range from 1.55g/cm3 to 1.8g/cm3, the ratio of the capacity of
`
`the negative active material to the capacity of the positive active material is at a range from 1
`
`to 1.4.
`
`[0012]
`
`In said lithium—ion battery of the present disclosure, on the one hand the lithium
`
`ion diffusion in negative electrode is accelerated by reducing the negative electrode
`
`polarization, on the other hand the diffusion velocity of lithium ion in positive electrode is
`
`slowed down by increasing the positive electrode polarization. Thus the charging process
`
`transforms quickly from charging with a constant current to charging with a constant voltage.
`
`The electrical current decreases gradually, and the amount of lithium ion diffusing from the
`
`positive electrode to the negative electrode per unit time is decreased. So the formation of
`
`lithium dendrite on the negative electrode surface can be effectively avoided, and the lithium-
`
`ion battery has excellent safety performance and cycle performance.
`
`[0013]
`
`To reduce the negative electrode polarization, (1) at coating process, the ratio
`
`(CB) of the capacity of the negative active material to the capacity of the positive active
`
`material is adjusted as large as possible. Because at the same SOC, if the CB of the all-battery
`
`is smaller, the lithium intercalation of the negative electrode is more sufficient, and the
`
`negative electrode potential is lower. In the charging process, it is shown as that the negative
`
`electrode reaches the precipitation potential of lithium quickly, making the precipitation of
`
`lithium easier. When the CB increases, the negative electrode potential is improved, and the
`
`lithium precipitation on the negative electrode surface can be effectively avoided, and the fast
`
`charging capability of lithium-ion battery at high rate can be improved. Meanwhile a higher
`
`CB easily leads to a lower energy density of lithium—ion battery, so the CB of the present
`
`024607-02-5014-US
`
`9)
`
`
`
`disclosure is at a range from 1 to 1.4, (2) at cold compacting step, the porosity of the negative
`
`conductive membrane can be increased by decreasing the compacted density of negative
`
`conductive membrane. And then the polarization on negative electrode surface is decreased,
`
`making the current distribution more uniform along the thickness direction. More negative
`
`active materials accept Li+ simultaneously in fast charge at high rate to avoid the lithium
`
`precipitation on the negative electrode surface. But a lower compacted density of negative
`
`conductive membrane makes the porosity of negative conductive membrane too high and the
`
`energy density of lithium-ion battery too low. So in the present disclosure, the compacted
`
`density of negative conductive membrane is at a range from 1.55g/cm3 to 1.8g/cm3.
`
`[0014]
`
`To increase the positive electrode polarization, at cold compacting step, increase
`
`in the compacted density of positive conductive membrane and decrease in the channel for
`
`lithium ion diffusion make the charging quickly transform to a constant voltage charging and
`
`the current decrease. Thus the lithium precipitation on the negative electrode sulface can be
`
`effectively avoided. But a too high compacted density of positive conductive membrane
`
`easily leads to the fracture of positive electrode, which is harmful for the safety performance
`
`and cycle performance of lithium—ion battery. So in the present disclosure, the compacted
`
`density of positive conductive membrane is at a range from 3.9g/cm3 to 4.4g/cm3.
`
`[0015]
`
`In said lithium-ion battery of the present disclosure, the compacted density of said
`
`positive conductive membrane is at a range from 3.95g/cm3 to 4.35g/cm3.
`
`[0016]
`
`In said lithium-ion battery of the present disclosure, the compacted density of said
`
`negative conductive membrane is at a range from 1.55g/cm3 to 1.75g/cm3.
`
`[0017]
`
`In said lithium-ion battery of the present disclosure, the ratio (CB) of the capacity
`
`of the negative active material to the capacity of the positive active material is at a range from
`
`1.03 to 1.2.
`
`[0018]
`
`In said lithium—ion battery of the present disclosure, the charging rate of said
`
`lithium-ion battery is at a range from 1.3C to SC.
`
`[0019]
`
`In said lithium-ion battery of the present disclosure, in formation of the negative
`
`conductive membrane, the coating weight of solid components in the negative mixture slurry
`
`on the surface of the negative current collector is at a range from 120mg/154O.25mm2 to
`
`190mg/1540.25mm2, in formation of the positive conductive membrane, the coating weight
`
`of solid components in the positive mixture slurry on the surface of the positive current
`
`collector is at a range from 230mg/1540.25mm2 to 380mg/1540.25mm2. The coating weight
`
`of solid components in conductive membrane can be reduced in the design of lithium—ion
`
`024607-02-5014-US
`
`4
`
`
`
`battery, because when the coating weight of solid components in conductive membrane is
`
`reduced, the current per unit area is decreased, and the concentration polarization along the
`
`thickness direction of electrode is alleviated. Thus the precipitation of lithium on the negative
`
`electrode surface in fast charging can be effectively avoided.
`
`[0020]
`
`In said lithium-ion battery of the present disclosure, said positive active material is
`
`at least one selected from the group consisting of cobalt acid lithium (LiCoOz), manganic
`
`acid lithium (LiMn204), lithium iron phosphate (LiFePO4) and ternary compound (NCM).
`
`Wherein, the ternary compound is at least one selected from the group consisting of the
`
`lithium nickel manganese cobalt oxides.
`
`[0021]
`
`In said lithium-ion battery of the present disclosure, said negative active material
`
`is carbon material which is at least one selected from the group consisting of soft carbon,
`
`hard carbon, artificial graphite, natural graphite and mesocarbon microbead.
`
`[0022]
`
`In said lithium-ion battery of the present disclosure, said separator is at least one
`
`selected from the group consisting of polyethylene (PE) membrane and polypropylene (PP)
`
`membrane. The thickness of said separator is from Sum to 30um.
`
`[0023]
`
`In said lithium—ion battery of the present disclosure, said electrolyte is a non—water
`
`electrolyte containing a non-water organic solvent and a lithium salt.
`
`[0024]
`
`In said lithium-ion battery of the present disclosure, said non-water organic
`
`solvent is a mixture of chain ester and cyclic ester, said chain ester is at least one selected
`
`from the group consisting of dimethyl carbonate DMC, diethyl carbonate DEC, ethyl methyl
`
`carbonate EMC, methyl propyl carbonate MPC, dipropyl carbonate DPC, fluorine-containing
`
`chain ester, sulphur-containing chain ester and unsaturated carbon-carbon bond-containing
`
`chain ester; said cyclic ester is at least one selected from the group consisting of ethylene
`
`carbonate EC, propylene carbonate PC, vinylene carbonate VC, y—butyrolactone y—BL,
`
`trimethylene sulf1te, fluorine—containing cyclic ester, other sulphur—containing cyclic ester and
`
`other unsaturated carbon-carbon bond-containing cyclic ester.
`
`[0025]
`
`In said lithium-ion battery of the present disclosure, said lithium salt is at least one
`
`selected from the group consisting of LiPFs, LiBF4, LiClO4, LiCF3SO3, LiN(SOzCF3)2 and
`
`LiN(SOzC2F5)2. Preferably, the lithium salt is LiPFs.
`
`[0026]
`
`The Examples using the lithium-ion battery and the electrolyte of the present
`
`disclosure are shown below.
`
`[0027]
`
`(1) Preparation of positive electrode
`
`024607-02-5014-US
`
`5
`
`Example 1
`
`
`
`N—methyl pyrrolidone (NMP) was used as a solvent to dissolve the positive binder
`
`polyvinylidene fluoride (PVDF). And a binder solution with mass fraction of 8% was
`
`obtained. Then LiCoOz (capacity per gram was 160mAh/g) used as a positive active material
`
`and carbon black used as positive conductive additive were added into the binder solution
`
`under stirring. The homogeneous positive mixture slurry was obtained by further stirring. In
`
`the positive mixture slurry, the weight ratio of LiCoOz, PVDF and carbon black was
`
`97: 1.5: 1.5. Then the positive mixture slurry was coated evenly on the aluminum foil used as
`
`the positive current collector and the coating weight was 334mg/1540.25mm2. After drying at
`
`120°C, the positive conductive membrane was obtained. The positive conductive membrane
`
`was cold compacted and adjusted the thickness, making its compacted density become
`
`3.95g/cm3. After being cut, the positive electrode of 72mm>< 1024mm was obtained.
`
`[0028]
`
`(2) Preparation of the negative electrode
`
`Artificial graphite (capacity per gram was 360mAh/g) used as negative active materials,
`
`sodium carboxymethyl cellulose (CMC) used as thickener, styrene butadiene rubber (SBR)
`
`used as positive binder and carbon black used as positive conductive additive were mixed
`
`with the solvent deionized water according to the weight ratio of 96: 1.5: 1.5: 1, and then the
`
`homogeneous negative mixture slurry was obtained by stirring. Then the negative mixture
`
`slurry was coated evenly on the copper foil used as the negative current collector and the
`
`coating weight was 155mg/154O25mm2. After drying at 90°C, the negative conductive
`
`membrane was obtained. Then the negative conductive membrane was cold compacted and
`
`adjusted the thickness, making its compacted density become 1.75g/cm3. After being cut, the
`
`negative electrode of 73.5mmX 1036mm was obtained.
`
`[0029]
`
`(3) Preparation of the electrolyte
`
`In electrolyte, LiPFc was used as lithium salt with the concentration of 1mol/L. A mixture of
`
`ethylene carbonate (EC) and dimethyl carbonate (DMC) (the mass ratio was 1:1) was used as
`
`a non-water organic solvent.
`
`[0030]
`
`(4) Preparation of the lithium-ion battery
`
`The positive electrode, the negative electrode and PE separator with l6um thickness were
`
`coiled to form a square naked-cell. Then the naked-cell was put into aluminum-plastic outer
`
`packing film. After being filled with electrolyte, being sealed and formation, the lithium-ion
`
`battery with a CB of 1.03 was obtained.
`
`Specifically:
`
`CB= the capacity of negative active material / the capacity of positive active material
`
`024607-02-5014-US
`
`6
`
`
`
`=(negative coating weight per unit areaX the weight ratio of negative active materials >< the
`
`capacity per gram of negative active material)/(positive coating weight per unit area X the
`
`weight ratio of positive active materials X the capacity per gram of positive active
`
`material).
`
`Example 2
`
`[0031]
`
`The lithium—ion battery was prepared using the method same as Example 1, except
`
`the differences as follows:
`
`[0032]
`
`(1) In formation of the positive conductive membrane, the coating weight of solid
`
`components in the positive mixture slurry on the surface of the positive current collector was
`
`314mg/154O.25mm2,
`
`(4) The CB was 1.1.
`
`Example 3
`
`[0033]
`
`The lithium-ion battery was prepared using the method same as Example 1, except
`
`the differences as follows:
`
`[0034]
`
`(1) In formation of the positive conductive membrane, the coating weight of solid
`
`components in the positive mixture slurry on the surface of the positive current collector was
`
`288mg/1540.25mm2;
`
`(4) The CB was 1.2.
`
`Example 4
`
`[0035]
`
`The lithium-ion battery was prepared using the method same as Example 1, except
`
`the differences as follows:
`
`[0036]
`
`(1) In formation of the positive conductive membrane, the coating weight of solid
`
`components in the positive mixture slurry on the surface of the positive current collector was
`
`265mg/1540.25mm2;
`
`[0037]
`
`(4) The CB was 1.3.
`
`Example 5
`
`[0038]
`
`The lithium-ion battery was prepared using the method same as Example 1, except
`
`the differences as follows:
`
`[0039]
`
`(1) In formation of the positive conductive membrane, the coating weight of solid
`
`components in the positive mixture slurry on the surface of the positive current collector was
`
`325mg/1540.25mm2, the compacted density of positive conductive membrane was 4g/cm3,
`
`[0040]
`
`(4) The CB was 1.06.
`
`Example 6
`
`024607-02-5014-US
`
`7
`
`
`
`[0041]
`
`The lithium-ion battery was prepared using the method same as Example 5, except
`
`the difference as follows:
`
`[0042]
`
`(2) The compacted density of negative conductive membrane was 1.65g/cm3.
`
`Example 7
`
`[0043]
`
`The lithium-ion battery was prepared using the method same as Example 5, except
`
`the difference as follows:
`
`[0044]
`
`(2) The compacted density of negative conductive membrane was 1.55g/cm3.
`
`Example 8
`
`[0045]
`
`The lithium-ion battery was prepared using the method same as Example 1, except
`
`the differences as follows:
`
`[0046]
`
`(1) In formation of the positive conductive membrane, the coating weight of solid
`
`components in the positive mixture slurry on the surface of the positive current collector was
`
`3OOmg/1540.25mm2, the compacted density of positive conductive membrane was
`
`3.95 g/cm3;
`
`[0047]
`
`(2) The compacted density of negative conductive membrane was 1.6g/cm3;
`
`[0048]
`
`(4) The CB was 1.15.
`
`Example 9
`
`[0049]
`
`The lithium-ion battery was prepared using the method same as Example 8, except
`
`the difference as follows:
`
`[0050]
`
`(1) The compacted density of positive conductive membrane was 4.1 g/cm3 .
`
`Example 10
`
`[0051]
`
`The lithium-ion battery was prepared using the method same as Example 8, except
`
`the difference as follows:
`
`[0052]
`
`(1) The compacted density of positive conductive membrane was 4.25 g/cm3.
`
`Example 11
`
`[0053]
`
`The lithium-ion battery was prepared using the method same as Example 8, except
`
`the difference as follows:
`
`[0054]
`
`(l) The compacted density of positive conductive membrane was 4.3 5g/cm3.
`
`Example 12
`
`[0055]
`
`The lithium-ion battery was prepared using the method same as Example 1, except
`
`the differences as follows:
`
`[0056]
`
`(1) In formation of the positive conductive membrane, the coating weight of solid
`
`components in the positive mixture slurry on the surface of the positive current collector was
`
`024607-02-5014-US
`
`8
`
`
`
`380mg/154O25mm2, the compacted density of positive conductive membrane was 4.1g/cm3,
`
`[0057]
`
`(2) In formation of the negative conductive membrane, the coating weight of solid
`
`components in negative mixture slurry on the squace of the negative current collector was
`
`185mg/154025mm2, the compacted density of negative conductive membrane was
`
`1.65 g/cm3;
`
`[0058]
`
`(4) The CB was 1.08.
`
`Example 13
`
`[0059]
`
`The lithium-ion battery was prepared using the method same as Example 12,
`
`except the differences as follows:
`
`[0060]
`
`(1) In formation of the positive conductive membrane, the coating weight of solid
`
`components in the positive mixture slurry on the surface of the positive current collector was
`
`340mg/154025mm2,
`
`[0061]
`
`(2) In formation of the negative conductive membrane, the coating weight of solid
`
`components in negative mixture slurry on the surface of the negative current collector was
`
`l65mg/154O25mm2.
`
`Example 14
`
`[0062]
`
`The lithium-ion battery was prepared using the method same as Example 12,
`
`except the differences as follows:
`
`[0063]
`
`(1) In formation of the positive conductive membrane, the coating weight of solid
`
`components in the positive mixture slurry on the surface of the positive current collector was
`
`290mg/154025mm2,
`
`[0064]
`
`(2) In formation of the negative conductive membrane, the coating weight of solid
`
`components in negative mixture slurry on the surface of the negative current collector was
`
`l4lmg/154O25mm2.
`
`Example 15
`
`[0065]
`
`The lithium-ion battery was prepared using the method same as Example 12,
`
`except the differences as follows:
`
`[0066]
`
`(1) In formation of the positive conductive membrane, the coating weight of solid
`
`components in the positive mixture slurry on the surface of the positive current collector was
`
`250mg/154025mm2,
`
`[0067]
`
`(2) In formation of the negative conductive membrane, the coating weight of solid
`
`components in negative mixture slurry on the surface of the negative current collector was
`
`024607-02-5014-US
`
`9
`
`
`
`l2lmg/1540.25mm2.
`
`[0068]
`
`The testing method and testing results of the lithium-ion batteries provided in the
`
`present disclosure are shown below.
`
`[0069]
`
`(1) Cycle performance test of the lithium-ion battery
`
`At 25°C, the battery was charged with constant current of 2.5C until the voltage reached
`
`4.35V, and then the battery was charged with constant voltage of 4.35V until the current
`
`reached the cut—off current of 0.05C, and then the battery was discharged with constant
`
`current of 1C until the voltage reached the cut-off voltage of 3V, which was a
`
`charge/discharge cycle. The charge/discharge cycle was repeated 350 times.
`
`[007 0]
`
`The capacity retention after 350 cycles (%) = the discharge capacity of the 350th
`
`cycle / the discharge capacity of initial cycle>< 100%.
`
`[0071]
`
`(2) Test for lithium precipitation of negative electrode
`
`At 25°C, the battery was charged with constant current of 2.5C until the voltage reached
`
`4.35V, and then the battery was charged with constant voltage of 4.35V until the current
`
`reached the cut—off current of 0.05C, and then the battery was discharged with constant
`
`current of 1C until the voltage reached the cut—off voltage of 3V, which was a
`
`charge/discharge cycle. The charge/discharge cycle was repeated 10 times. After cycles, the
`
`lithium-ion battery was full charged and took apart, and lithium precipitation on the surface
`
`of negative electrode was observed. Therein, the degree of lithium precipitation was graded
`
`into no lithium precipitation, slight lithium precipitation, medium lithium precipitation and
`
`serious lithium precipitation. No lithium precipitation meant that the area ratio of lithium
`
`precipitation region on the surface of negative electrode was 0%. Slight lithium precipitation
`
`meant that the area ratio of lithium precipitation region on the surface of negative electrode
`
`was less than 20%. Medium lithium precipitation meant that the area ratio of lithium
`
`precipitation region on the surface of negative electrode was at a range from 20% to 70%.
`
`Serious lithium precipitation meant that the area ratio of lithium precipitation region on the
`
`surface of negative electrode was more than 70%. Table 1 showed the parameters and results
`
`of performance test from Example 1 to Example 15.
`
`Table 1 The parameters and results of performance from Example 1 to Example 15
`
`Positive electrode
`
`Negative electrode
`
`Lithium
`
`Capacity
`
`Compacted
`
`.
`.
`Coating weight
`
`compacted
`
`.
`.
`Coating weight
`
`cycles
`
`density
`
`g/cm3
`
`mg/1540.25mm2
`
`density
`
`g/crn3
`
`024607-02-5014-US
`
`10
`
`mg/1540.25mm2
`
`precipitation
`,
`of negative
`
`retention
`
`after 3 50
`
`electrode
`
`
`
`Example 1
`
`1.03
`
`3.95
`
`334
`
`1.75
`
`155
`
`serious
`
`lithium
`
`50%
`
`70%
`
`82%
`
`93%
`
`precipitation
`medium
`
`
`
`lithium
`
`precipitation
`
`slight lithium
`.
`.
`.
`preClpltatlon
`no lithium
`.
`.
`.
`preClpltatlon
`serious
`
`Example 2
`
`1.1
`
`3 .95
`
`314
`
`Example 3
`
`1.2
`
`3.95
`
`288
`
`1.75
`
`1.75
`
`155
`
`155
`
`Example 4
`
`1.3
`
`Exalnple 5
`
`1.06
`
`265
`
`325
`
`155
`
`155
`
`
`
`lithium
`
`56%
`
`precipitation
`medium
`
`Example 6
`
`1.06
`
`4
`
`325
`
`1.65
`
`155
`
`lithium
`
`72%
`
`Example 7
`
`1.06
`
`4
`
`325
`
`300
`
`1.55
`
`1.6
`
`155
`
`155
`
`slight lithium
`.
`.
`.
`preClpltatlon
`medium
`
`83%
`
`lithillm
`
`73%
`
`precipitation
`
`
`
`Example 8
`
`1.15
`
`3.95
`
`Example 9
`
`1.15
`
`4.1
`
`Example 10
`
`1.15
`
`4.25
`
`Example 11
`
`1.15
`
`4.35
`
`Example 12
`
`1.08
`
`4.1
`
`300
`
`300
`
`300
`
`380
`
`1.6
`
`1.6
`
`1.6
`
`1.65
`
`155
`
`155
`
`155
`
`185
`
`Example 13
`
`1.08
`
`4.1
`
`340
`
`1.65
`
`165
`
`Example 14
`
`1.08
`
`4.1
`
`290
`
`1.65
`
`141
`
`
`
`precipitation
`
`slight lithium
`'
`'
`'
`prCClpltatlon
`no lithium
`.
`.
`.
`preClpltatlon
`no lithium
`'
`'
`'
`preClpltatlon
`serious
`
`lithillm
`
`precipitation
`medium
`
`
`
`lithium
`
`precipitation
`
`slight lithium
`'
`'
`'
`preClpltatlon
`no lithium
`
`84%
`
`93%
`
`96%
`
`55%
`
`71%
`
`84%
`
`95%
`121
`1.65
`250
`4.1
`1.08
`Example 15
`
`precipitation
`
`[0072]
`
`By the contrast from Example 1 to Example 4, it was observed that the lithium
`
`precipitation on the surface of negative electrode was improved significantly and the capacity
`
`retention of the lithium-ion battery increased after 350 cycles, with the decrease of the
`
`coating weight of solid components in the positive conductive membrane and the increase of
`
`024607-02-5014-US
`
`11
`
`
`
`the CB. When the CB was too small, the capacity retention after 350 cycles was low.
`
`[0073]
`
`By the contrast from Example 5 to Example 7, it was observed that the lithium
`
`precipitation on the surface of negative electrode was improved significantly and the capacity
`
`retention of the lithium-ion battery increased after 350 cycles, with the decrease of the
`
`compacted density of negative conductive membrane. When the compacted density of
`
`negative conductive membrane was too high, the capacity retention after 350 cycles was low.
`
`[007 4]
`
`By the contrast from example 8 to example 11, it was observed that the lithium
`
`precipitation on the surface of negative electrode was improved significantly and the capacity
`
`retention of the lithium-ion battery increased after 350 cycles, with the increase of the
`
`compacted density of positive conductive membrane. When the compacted density of
`
`positive conductive membrane was too small, the capacity retention after 350 cycles was low.
`
`[0075]
`
`By the contrast from example 12 to example 15, it was observed that the lithium
`
`precipitation on the surface of negative electrode was improved significantly and the capacity
`
`retention of the lithium-ion battery increased after 350 cycles, with the simultaneous decrease
`
`of the coating weights of solid components in the positive conductive membrane and in the
`
`negative conductive membrane. When the coating weights of solid components in the
`
`positive conductive membrane and in the negative conductive membrane were too high, the
`
`capacity retention after 350 cycles was low.
`
`024607-02-5014-US
`
`12
`
`
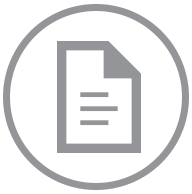
Accessing this document will incur an additional charge of $.
After purchase, you can access this document again without charge.
Accept $ ChargeStill Working On It
This document is taking longer than usual to download. This can happen if we need to contact the court directly to obtain the document and their servers are running slowly.
Give it another minute or two to complete, and then try the refresh button.
A few More Minutes ... Still Working
It can take up to 5 minutes for us to download a document if the court servers are running slowly.
Thank you for your continued patience.
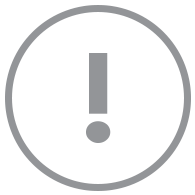
This document could not be displayed.
We could not find this document within its docket. Please go back to the docket page and check the link. If that does not work, go back to the docket and refresh it to pull the newest information.
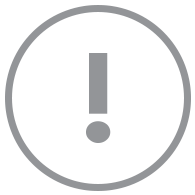
Your account does not support viewing this document.
You need a Paid Account to view this document. Click here to change your account type.
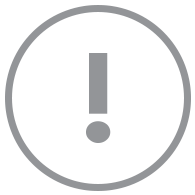
Your account does not support viewing this document.
Set your membership
status to view this document.
With a Docket Alarm membership, you'll
get a whole lot more, including:
- Up-to-date information for this case.
- Email alerts whenever there is an update.
- Full text search for other cases.
- Get email alerts whenever a new case matches your search.
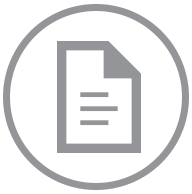
One Moment Please
The filing “” is large (MB) and is being downloaded.
Please refresh this page in a few minutes to see if the filing has been downloaded. The filing will also be emailed to you when the download completes.
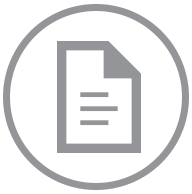
Your document is on its way!
If you do not receive the document in five minutes, contact support at support@docketalarm.com.
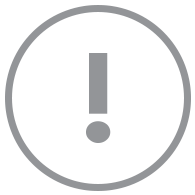
Sealed Document
We are unable to display this document, it may be under a court ordered seal.
If you have proper credentials to access the file, you may proceed directly to the court's system using your government issued username and password.
Access Government Site