`(KK-2332)
`
`CONTROL IVIECHANISM FOR STEPLESS TRANSMISSION
`
`Inventors:
`
`Jun MAT SUURA
`
`Nobuhisa KAMIKAWA
`
`Syouto YOSHIIVIOTO
`Koji IWAKI
`Masaru IIDA
`
`Toshifumi YASUDA
`
`CROSS-REFERENCE TO RELATED APPLICATIONS
`
`[0001]
`
`The present application claims priority to Japanese Patent Applications No.
`
`2014-161495, filed on August 7, 2014, and No. 20l4-l62729, filed on August 8, 2014. Further,
`
`the present application is a continuation-in-part application of US. patent application Ser. No.
`
`15/650,358, filed on July 14, 2017.
`
`BACKGROUND OF THE INVENTION
`
`Field of the Invention
`
`[0002]
`
`The present invention relates to a control mechanism for controlling the output rotary
`
`speed and direction of a hydrostatic transmission (hereinafter, “HST”). Especially, the control
`
`mechanism is a servomechanism including a servo unit that combines a telescopic (linearly
`
`movable) actuator and a valve.
`
`Related Art
`
`[0003]
`
`As disclosed by JP 2002-250437 A (hereinafter, “Dl”), JP HO6-lOO278 B (hereinafter,
`
`“D2”), and JP 2013-096449 A (hereinafter, “D3”), an HST used as a transmission for a tractor
`
`is usually disposed in a casing that also serves as a vehicle body frame (chassis) of the tractor.
`
`Also, as disclosed by D1, D2 and D3, it is well-known that a piston in a hydraulic cylinder
`
`serves as the actuator for controlling a position of a movable swash plate of the HST.
`
`In this
`
`regard, a trunnion shaft serving as a pivot of the movable swash plate is connected to the piston.
`
`Especially, each of the hydraulic cylinders disclosed by D2 and D3 is configured as a
`
`servomechanism.
`
`
`
`Atty. Docket No. 0666.5620004
`(xx—233.2)
`
`[0004]
`
`With regard to connection of the actuator to the trunnion shaft, in DI, the trunnion
`
`shaft has a tip projecting outward from the casing, and an arm is fixed on the tip of the trunnion
`
`shaft, and is connected via a link to a tip of a piston rod extended from the hydraulic cylinder
`
`disposed outside of the casing. Similarly, in D2, an arm is fixed on a tip of the trunnion shaft
`
`projecting outward from the casing. However, a tip of the arm is directly connected to the
`
`piston in the hydraulic cylinder without a link. In D3, a part of the casing serves as a housing
`
`of the hydraulic cylinder. The piston in the hydraulic cylinder formed in the casing is directly
`
`connected to the movable swash plate of the HST in the casing so that the HST and the
`
`hydraulic cylinder are assembled together in the casing.
`
`[0005]
`
`To achieve a simple and compact vehicle body frame, some tractor makers desire the
`
`HST to be minimized for its arrangement in the casing serving as the vehicle body frame, and
`
`the actuator to be separated from the HST so as to enable its external attachment on the outside
`
`of the casing. From this viewpoint, the structure disclosed by D3 does not meet these desires.
`
`[0006]
`
`If it is premised that the HST is disposed inside of the casing, and the actuator outside
`
`of the casing, it is desirable in assembility, maintenanceability, and reduction of parts count
`
`and costs that the actuator can be easily connected or disconnected to and from the tip of the
`
`trunnion shaft projecting outward from the casing. A space under the step of the tractor on a
`
`right or left side of the casing is suggested as one of appropriate spaces for arrangement of
`
`such an actuator. However, if the actuator is to be disposed under the step, the actuator must
`
`be disposed at a considerably low position so that a sufficient vertical gap between the actuator
`
`and the step above the actuator is ensured to facilitate works for connecting or disconnecting
`
`the actuator to and from the trunnion shaft, and to prevent the attached actuator from
`
`interfering with the step. Such a low position becomes considerably lower than the trunnion
`
`shaft. Therefore, as taught or suggested by D1 and D2, a link or an arm is needed to connect
`
`the trunnion shaft to the actuator.
`
`[0007]
`
`If the actuator is a telescopic actuator, such as a piston rod of a hydraulic cylinder, the
`
`movement of the actuator is linear while the movement of the arm that rotates centered on the
`
`trunnion shaft or the like is circular. Therefore, such a differential movement between the arm
`
`and the actuator should be considered when they are connected to each other. This differential
`
`movement becomes larger as the distance between the trunnion shaft and the actuator becomes
`
`larger.
`
`In other words, if a large vertical gap between the actuator and the trunnion shaft is
`
`-2-
`
`
`
`Atty. Docket No. 0666.5620004
`(KK-233.2)
`
`desired to ensure the facility in work for connecting and disconnecting the actuator to and from
`
`the trunnion shaft, there should be any configuration for absorbing the differential movement
`
`between the arm and the actuator that may become large because of the large vertical gap.
`
`[0008]
`
`In this regard, Dl discloses a structure that the cylinder serving as the actuator is
`
`pivotally connected at the tip of the piston rod thereof to the arm, and at a cylinder bottom
`
`thereof to a part of the vehicle (e.g., a frame). During the telescopic movement of the piston
`
`rod, the entire cylinder rotates centered on the pivot at the cylinder bottom according to
`
`rotation of the arm. D2 discloses a structure that a groove or a slot is provided in a portion of
`
`the piston of the servomechanism to the tip of the arm so as to absorb the rotation of the tip of
`
`the arm during the sliding movement of the piston.
`
`[0009]
`
`However, in the case of DI, the part of the vehicle pivotally supporting the cylinder
`
`bottom is weighed on or loaded eccentrically because it cantilevers the cylinder, so that it is
`
`liable to a twisting stress due to the rotation of the cylinder. If the actuator is assembled with a
`
`valve so as to constitute a servo unit, especially, if the valve is a large and heavy solenoid valve,
`
`the part pivoting the cylinder bottom further tends to be twisted. In the case of D2, the portion
`
`of the piston engaged with the tip of the arm is complicated in structure.
`
`It needs accurate
`
`dimensions to surely absorb the differential movement between the piston and the arm while
`
`ensuring a stable telescopic movement of the piston and a stable rotation of the arm. Further,
`
`the slot or groove has to be formed. As a result, the cost of the configuration of D2 becomes
`
`great. Moreover, in the case of D2, the actuator is a twin rod piston. While the piston engages
`
`with the tip of the arm, the actuator unit including the valve and the piston has to be supported
`
`by attaching both tips of the piston rods to the casing of the HST, thereby increasing the
`
`number of positions and processes for attaching or detaching the actuator unit.
`
`[0010]
`
`Moreover,
`
`it is desirable that the servo unit is minimized as much as possible.
`
`However,
`
`the actuator needs a biasing means that biases the actuator to a position
`
`corresponding to a neutral position of the movable swash plate, i.e., a neutral position of the
`
`HST. The existence of the biasing means hinders the servo unit from being minimized.
`
`
`
`Atty. Docket No. 0666.5620004
`(KK-233.2)
`
`SUlVllVlARY OF THE INVENTION
`
`[0011]
`
`An object of the invention is to downsize a servo unit and further to facilitate
`
`attachment and detachment of the servo unit, in the case where an HST control mechanism
`
`such as a servo mechanism to be provided separately from an HST includes the servo unit
`
`constituted by the combination of an actuator and valves.
`
`[0012]
`
`A control mechanism for stepless transmission according to the invention is a control
`
`mechanism connected to a manipulation lever in a stepless transmission and disposed outside
`
`a housing of the transmission, and includes: a) a piston rod connected to the manipulation
`
`lever; b) a piston provided on the piston rod coaXially with the piston rod, c) a cylinder case
`
`provided with a cylinder adapted to house the piston rod and the piston such that the piston rod
`
`and the piston are displaceable in an aXial direction, the piston and the cylinder forming a first
`
`fluid chamber to be supplied with a hydraulic fluid for withdrawing the piston rod from the
`
`cylinder and a second fluid chamber to be supplied with the hydraulic fluid for introducing the
`
`piston rod into the cylinder; d) a spring adapted to bias the manipulation lever in a neutral
`
`direction coaXially with the piston rod, e) a proportional pressure control valve adapted to
`
`selectively supply the hydraulic fluid to the first fluid chamber or the second fluid chamber,
`
`the proportional pressure control valves being mounted to the cylinder case, and f) a pivot
`
`shaft adapted to support the cylinder case oscillatably with respect to the housing.
`
`[0013]
`
`Thus, the servo unit is pivotally supported through the pivot shaft, which can ensure
`
`the integrity of the servo unit constituted by the combination of the actuator and the valves, can
`
`enhance the assemblability, and also can ensure easiness of attachment and detachment of the
`
`servo unit.
`
`[0014]
`
`Preferably,
`
`in the control mechanism for stepless transmission,
`
`the proportional
`
`pressure control valve is composed of a first valve configured to supply the hydraulic fluid to
`
`the first fluid chamber and a second valve adapted to supply the hydraulic fluid to the second
`
`fluid chamber,and an aXis center of the piston rod, an aXis center of displacement of a valve
`
`body of the first valve and an aXis center of displacement of a valve body of the second valve
`
`form a triangle shape, when viewed in the aXial direction of the piston rod.
`
`
`
`Atty. Docket No. 0666.5620004
`(xx—233.2)
`
`[0015]
`
`This can reduce the radial size of a portion of the servo unit where the actuator and the
`
`valves are disposed, which can downsize the hydraulic transmission control mechanism,
`
`thereby preventing it from interfering with obstructions existing around the housing.
`
`[0016]
`
`Further, preferably, in the control mechanism for stepless transmission, the spring is
`
`arranged in the axial direction such that a coil axis center of the spring and the axis center of
`
`the piston rod are substantially coincident with each other.
`
`[0017]
`
`This can reduce the radial size of a portion of the servo unit where the neutral spring is
`
`disposed, which can downsize the hydraulic transmission control mechanism,
`
`thereby
`
`preventing it from interfering with obstructions existing around the housing.
`
`[0018]
`
`Further, preferably, in the control mechanism for stepless transmission, the piston rod,
`
`the first valve, and the second valve are disposed such that the axial direction of the piston rod,
`
`a direction of displacement of a valve body of the first valve and a direction of displacement of
`
`a valve body of the second valve are parallel with each other, and the spring is disposed on one
`
`end of the cylinder case in the axial direction of the piston rod, and the first valve and the
`
`second valve are disposed on the other end of the cylinder case on an opposite side to the
`
`spring, in the axial direction of the piston rod.
`
`[0019]
`
`This can reduce the radial size of the servo unit constituted by the actuator, the valves
`
`and the neutral spring which are integrated, which can downsize the hydraulic transmission
`
`control mechanism.
`
`[0020]
`
`Further,
`
`in the control mechanism for stepless transmission further includes a
`
`mounting part having the pivot shaft such that the mounting part is oscillatable and is
`
`prevented from being disengaged from the housing, wherein the mounting part is detachably
`
`mounted to the cylinder case.
`
`[0021]
`
`This enables easily coping with changes of the specifications of the control mechanism
`
`for stepless transmission, through replacement of the mounting part.
`
`[0022]
`
`Further, preferably, in the control mechanism for stepless transmission, the cylinder
`
`case is mounted to the mounting part such that an axis line of the piston rod and an axis line of
`
`the oscillatable shaft portion are overlapped with each other in a plan view.
`
`[0023]
`
`This allows the cylinder case to smoothly oscillate during stretching and shrinking of
`
`the piston rod, thereby efficiently moving the manipulation lever.
`
`
`
`Atty. Docket No. 06665620004
`(KK-233.2)
`
`[0024]
`
`Further, preferably, in the control mechanism for stepless transmission, the piston rod
`
`is provided with a thread portion at a tip end portion, is secured, through screwing, to the
`
`manipulation lever connecting portion, and is provided with a flat portion in at least a portion
`
`of an outer peripheral surface.
`
`[0025]
`
`This enables changing the position of the manipulation lever connecting portion by
`
`rotating a tool fitted to the flat portion, thereby easily and accurately adjusting the neutral
`
`position.
`
`[0026]
`
`These and other objects, features and advantages of the invention will appear more
`
`fully from the following detailed description of the invention with reference to the attached
`
`drawings.
`
`BRIEF DESCRIPTION OF THE DRAWINGS
`
`[0027]
`
`Fig. l is a side view of a vehicle frame casing 11 to which a servo set 40 according to a
`
`first embodiment is attached.
`
`[0028]
`
`Fig. 2 is a sectional side view of vehicle frame casing 11 showing a structure of an HST
`
`[0029]
`
`[0030]
`
`[0031]
`
`[0032]
`
`[0033]
`
`[0034]
`
`[0035]
`
`[0036]
`
`[0037]
`
`[0038]
`
`[0039]
`
`[0040]
`
`l therein.
`
`Fig. 3 is a perspective view of a servo unit 60.
`
`Fig. 4 is a side view of servo unit 60.
`
`Fig. 5 is a cross sectional view taken along V-V line of Fig. 4.
`
`Fig. 6 is a cross sectional view taken along VI—VI line of Fig. 4.
`
`Fig. 7 is a cross sectional view taken along VII-VII line of Fig. 6.
`
`Fig. 8 is a cross sectional view taken along VIII-VIII line of Fig. 4.
`
`Fig. 9 is a cross sectional view taken along IX-IX line of Fig. 4.
`
`Fig. 10 is a cross sectional view taken along X-X line of Fig. 4.
`
`Fig. 11 is a cross sectional view taken along XI-XI line of Figs. 6 and 7.
`
`Fig. 12 is a sectional side view of a neutral returning unit 80.
`
`Fig. 13 is a hydraulic circuit diagram for supplying fluid to HST l and servo set 40.
`
`Fig. 14 is a sectional side view of HST l disposed in vehicle frame casing 11 to be
`
`provided with a servo unit 30 according to a second embodiment.
`
`
`
`Atty. Docket No. 0666.5620004
`(KK-233.2)
`
`[0041]
`
`Fig. 15 is a cross sectional view taken along XV-XV line of Fig. 14 as a sectional rear
`
`view of HST 1 provided with servo unit 30 according to the second embodiment.
`
`[0042]
`
`Fig. 16 is a sectional side view of a portion of servo unit 30 including a hydraulic
`
`cylinder 32.
`
`Fig. 17 is a hydraulic circuit diagram for supplying fluid to HST l and servo unit 30.
`
`Fig. 18 is a sectional rear view of a servo unit 30A.
`
`Fig. 19 is a sectional rear view of a servo unit 30B.
`
`Fig. 20 is a sectional rear view of a servo unit 30C.
`
`Fig. 21 is a sectional rear view of a servo unit 30D.
`
`Fig. 22 is a sectional rear view of a servo unit 30E.
`
`Fig. 23 is a sectional side view of servo unit 30E.
`
`Fig. 24 is a hydraulic circuit diagram for supplying fluid to HST l and a servo unit 90.
`
`Fig. 25 is a side view of servo set 200.
`
`Fig. 26 is a rear view of servo set 200.
`
`Fig. 27 is a front view of servo set 200.
`
`Fig. 28 is a perspective view of servo set 200.
`
`Fig. 29 is a cross-sectional view taken along A-A line of Fig. 25.
`
`Fig. 30 is a cross-sectional view taken along B-B line of Figs. 25 and 26.
`
`Fig. 31 is a cross-sectional view taken along C-C line of Fig. 26.
`
`Fig. 32 is a cross-sectional view taken along D-D line of Fig. 26.
`
`Fig. 33 is a side view illustrating a state of mounting of servo set 200 to vehicle frame
`
`[0043]
`
`[0044]
`
`[0045]
`
`[0046]
`
`[0047]
`
`[0048]
`
`[0049]
`
`[0050]
`
`[0051]
`
`[0052]
`
`[0053]
`
`[0054]
`
`[0055]
`
`[0056]
`
`[0057]
`
`[0058]
`
`[0059]
`
`casing 11.
`
`[0060]
`
`Fig. 34 is a perspective assembly view illustrating the state of mounting of servo set
`
`200 to vehicle frame casing 11.
`
`[0061]
`
`Fig. 35 is a front-portion cross-sectional view illustrating a portion for pivotally
`
`supporting servo set 200 on vehicle frame casing 11.
`
`[0062]
`
`Fig. 36 is a hydraulic circuit diagram for supplying fluid to HSTl and servo set 200.
`
`
`
`DETAILED DESCRIPTION OF THE INVENTION
`
`Atty. Docket No. 0666.5620004
`(xx—233.2)
`
`[0063]
`
`A first embodiment about an HST control mechanism (servomechanism) serving as an
`
`actuator device for controlling a movable swash plate of an HST (Hydro-Static-Transmission)
`
`shown as an example of a continuously variable transmission capable of switching forward
`
`and reverse will be described with reference to Fig. 1 to 13. Referring to Figs. 1 and 2, an HST
`
`1, a vehicle frame casing 11 and an axle casing 12 will be described. Vehicle frame casing 11
`
`is a casing formed to serve as a vehicle body frame (chassis). Vehicle frame casing 11
`
`incorporates HST 1 serving as a unit for changing a speed of a vehicle such as a tractor.
`
`Vehicle frame casing 11 has front and rear open ends. One of the front and rear end open ends
`
`of HST 1 (in this embodiment, the front open end) is an open end 11a, which is joined to an
`
`end portion (in this embodiment, a rear end portion) of an engine 10 (see Fig. 13). The other of
`
`the front and rear ends of HST 1 is an open end 11b, which is joined to an end portion (in this
`
`embodiment, a front end portion) of axle casing 12. Hereinafter, positions and directions of all
`
`component elements of the first embodiment and a later-discussed second embodiment are
`
`defined on the assumption that vehicle frame casing 11 has front open end 11a and rear open
`
`end 11b.
`
`[0064]
`
`Axle casing 12 journals an axle (not shown) and incorporates a transmission for
`
`driving the axle. This transmission transmits power outputted from HST 1 to the axles. The
`
`transmission may include a speed-changing mechanism (e.g., a gear transmission).
`
`In this
`
`case, HST 1 serves as a main speed-changing transmission, and the transmission in axle casing
`
`12 serves as a sub speed-changing transmission.
`
`[0065]
`
`Vehicle frame casing 11 and axle casing 12 joined to each other serve as a vehicle body
`
`frame, which is disposed at a laterally middle portion of a vehicle such as a tractor, for
`
`example. Referring to Fig. 1 (and Fig. 2 illustrating another embodiment), this vehicle body
`
`frame is fixedly provided on right and left ends thereof with left and right steps 13 and 14
`
`made of horizontal plates, which are used for an operator’s getting on and off the vehicle, and
`
`as a foot rest for an operator sitting on a seat. A servo set (servomechanism) 40 for controlling
`
`a later-discussed movable swash plate of HST 1 is disposed under one of steps 13 and 14 (in
`
`this embodiment, step 14. See Fig. 15 or others illustrating the second embodiment).
`
`
`
`Atty. Docket No. 06665620004
`(xx—233.2)
`
`[0066]
`
`HST 1 includes a hydraulic pump 2, a hydraulic motor 3, a center section 4, an HST
`
`housing 5, a charge pump 20 and others, which are assembled together into a unit defined as
`
`HST 1.
`
`In this embodiment, center section 4 is shaped as a vertical plate, which is fixed in
`
`vehicle frame casing 11 so as to cover rear open end 1 lb of vehicle frame casing 11. A vertical
`
`front surface of center section 4 is formed with a pump mounting surface and a motor
`
`mounting surface, which are vertically juxtaposed so that one is above the other.
`
`In this
`
`embodiment, the pump mounting surface is disposed above the motor mounting surface. A
`
`cylinder block 2a of hydraulic pump 2 is rotatably slidably mounted onto the pump mounting
`
`surface, and a cylinder block 3a of hydraulic motor 3 onto the motor mounting surface. A
`
`valve plate may be interposed between each cylinder block 2a or 3a and the pump or motor
`
`mounting surface. HST housing 5 is extended forward from center section 4 so as to cover
`
`hydraulic pump 2 and hydraulic motor 3 at upper, lower, right, left and front sides of hydraulic
`
`pump 2 and motor 3.
`
`[0067]
`
`Referring to Fig. 2, a front wall of HST housing 5 is disposed forward from hydraulic
`
`pump 2 and motor 3. A movable swash plate 6 of hydraulic pump 2 is disposed adjacent to an
`
`upper portion of the front wall of HST housing 5. Movable swash plate 6 is a trunnion-type
`
`movable swash plate having later-discussed lateral trunnion shafts pivoted by right and left
`
`side walls of HST housing 5, and abuts against heads (front ends) of plungers 2b projecting
`
`forward from cylinder block 2a. A later-discussed pump shaft 2c is extended forward from
`
`movable swash plate 6, is journalled by an upper portion of the front wall of HST housing 5,
`
`and is extended forward from HST housing 5 to as to be drivingly connected to a
`
`later-discussed flywheel lOb. On the other hand, a fixed swash plate 6 of hydraulic motor 3 is
`
`fixed to a lower portion of the front wall of HST housing 5 so as to abut against heads of
`
`plungers 3b projecting forward from cylinder block 3a.
`
`[0068]
`
`Movable swash plate 6 includes right and left trunnion shafts serving as a fulcrum axis
`
`for rotation of movable swash plate 6. Right and left trunnion shafts are journalled by right
`
`and left walls of HST housing 5. Of the trunnion shafts, one trunnion shaft 6b projects
`
`outward from HST housing 5, and has an end portion projecting outward from a right or left
`
`(in this embodiment, right) outer side surface llc of vehicle frame casing 11 just below step 14.
`
`A first arm 107 is fixed at a top portion thereof to the end portion of trunnion shaft 6b. First
`
`arm 107 is extended downward along the outer side surface of vehicle frame casing 11, and
`
`-9-
`
`
`
`Atty. Docket No. 0666.5620004
`(xx—233.2)
`
`has a lower end portion to which a rear end portion 82b of a rod 82 extended rearward from a
`
`cylindrical member 81 of a neutral returning unit 80.
`
`[0069]
`
`A second arm 109 is disposed rearward from first arm 107 outside of vehicle frame
`
`casing 11, and is extended along outer side surface 11c of vehicle frame casing 11. Second
`
`arm 109 has a pivot shaft 109a at a vertically intermediate portion thereof so as to be pivoted
`
`onto outer side surface 11c of vehicle frame casing 11 via pivot shaft 109a. Second arm 109 is
`
`pivotally connected at a top portion thereof to a vertically intermediate portion of first arm 107
`
`via a link 108. A tip (i.e., rear end) of a piston rod 33a extended rearward from a hydraulic
`
`cylinder 32 of a servo unit 60 is pivotally connected to a lower end portion of second arm 109.
`
`Servo unit 60 and a neutral returning unit 80 are assembled together so as to constitute a servo
`
`set (i.e., servomechanism) 40 for controlling movable swash plate 6 of hydraulic pump 2.
`
`In
`
`this regard, fist arm 107, link 108 and second arm 109 serve as a rotary member, to which a
`
`piston rod 33a of a piston 33 serving as a telescopic actuator of servo unit 60 and a rear end
`
`portion 82b of a rod 82 serving as a telescopic member of neutral returning unit 80 are
`
`pivotally connected. Neutral returning unit 80 includes a neutral biasing spring 83 (the neutral
`
`spring) serving as a biasing device. Neutral biasing spring 83 biases rod 82 toward its neutral
`
`position corresponding to a neutral position of movable swash plate 6.
`
`[0070]
`
`Due to a fore-and-aft telescopic movement of piston rod 33a of servo unit 60, second
`
`arm 109 rotates centered on pivot shaft 109a. Accordingly, first arm 107 connected to second
`
`arm 109 via link 108 rotates centered on an axis of trunnion shaft 6b, thereby rotating movable
`
`swash plate 6 of hydraulic pump 2, because trunnion shaft 6b of movable swash plate 6 is fixed
`
`to first arm 107. Further, due to the telescopic movement of piston rod 33a and the rotation of
`
`second arm 109, first arm 107 rotates so as to move rod 82 telescopically against the biasing
`
`force of neutral biasing spring 83.
`
`In servo unit 60, proportional pressure control valves 35
`
`and 36 can be controlled to apply an operation force to piston rod 33a. Once piston rod 33a is
`
`released from the operation force, rod 82 returns to the neutral position defined by the biasing
`
`force of neutral biasing spring 83, thereby returning first arm 107 and movable swash plate 6
`
`to their neutral positions. Due to the movement of first arm 107 to its neutral position, second
`
`arm 109 is rotated via link 108 so that piston rod 33a returns to a position in the telescopic
`
`movement direction (fore-and-aft direction) of piston rod 33a corresponding to the neutral
`
`position of movable swash plate 6 with trunnion shafts 6a.
`
`-10-
`
`
`
`Atty. Docket No. 0666.5620004
`(xx—233.2)
`
`[0071]
`
`Hydraulic pump 2 includes a fore-and-aft horizontal pump shaft 2c serving as a rotary
`
`axis of cylinder block 2a. Hydraulic motor 3 includes a fore-and-aft horizontal motor shaft 3c
`
`serving as a rotary axis of cylinder block 3a. Pump shaft 2c and motor shaft 3c are journalled
`
`by center section 4. Rear end portions of pump shaft 2c and motor shaft 3c project rearward
`
`from center section 4 into axle casing 12. In axle casing 12, a front end portion of a PTO shaft
`
`or a front end portion of a PTO transmission shaft 15 interlocking with the PTO shaft is
`
`connected via a coupling 15a to the rear end portion of pump shaft 2c. On the other hand, in
`
`axle casing 12, a front end portion of an input shaft 16 of the transmission in axle casing 12 is
`
`connected via a coupling 16a to the rear end portion of motor shaft 3c serving as an output
`
`shaft of HST 1.
`
`[0072]
`
`In vehicle frame casing 11, a gear casing 21 is fixed to a front end of HST housing 5. A
`
`front portion of pump shaft 2c projects forward from the front wall of HST housing 5 through
`
`gear casing 21. After engine 10 is joined to front open end 11a of vehicle frame casing 11, a
`
`fore-and-aft horizontal engine output shaft 10a of engine 10 is extended into vehicle frame
`
`casing 11 via front open end 11a, so that a flywheel 10b provided at a rear end portion of
`
`engine 10 is disposed in a front inside space in vehicle body frame 11. Pump shaft 2c serving
`
`as an input shaft of HST 1 projects forward from gear casing 21 as mentioned above, so that a
`
`front end portion of pump shaft 2c is connected to flywheel 10b via a damper 10c.
`
`[0073]
`
`In gear casing 21, pump shaft 2c is journalled at a fore-and-aft intermediate portion
`
`thereof, and a charge pump driving shaft 24 is extended parallel to pump shaft 2c and is
`
`journalled.
`
`In gear casing 21, a gear 22 is fixed on the fore-and-aft intermediate portion of
`
`pump shaft 2c, and a gear 23 is fixed on charge pump driving shaft 24. Gears 22 and 23 mesh
`
`with each other so as to constitute a gear train for transmitting power from pump shaft 2c to
`
`charge pump driving shaft 24. A pump housing 26 incorporating charge pump 20 is fixed to a
`
`front end of gear casing 21 so as to extend parallel to the front portion of pump shaft 2c
`
`projecting forward from gear casing 21. Charge pump driving shaft 24 projects forward from
`
`gear casing 21 into pump housing 25. In pump housing 25, a pump driven shaft 20c parallel to
`
`charge pump driving shaft 24 is journalled.
`
`In pump housing 25, a pump gear 20a fixed on
`
`charge pump driving shaft 24 and a pump gear 20b fixed on pump driven shaft 20c mesh with
`
`each other so as to constitute a gear pump serving as charge pump 20.
`
`-11-
`
`
`
`Atty. Docket No. 06665620004
`(KK-233.2)
`
`[0074]
`
`Referring to Figs. 2 and 13, a hydraulic fluid supply system for supplying fluid from
`
`charge pump 20 to HST 1 will be described. Charge pump 20 sucks fluid from a fluid sump in
`
`axle casing 12. In this regard, aXle casing 12 has a fluid discharge port P1. Fluid of the fluid
`
`sump in axle casing 12 is taken out of aXle casing 12 via fluid discharge port P1 and is sucked
`
`to a suction port of charge pump 20 disposed in vehicle frame casing 11 via a fluid passage L1.
`
`Fluid passage L1 may be formed within a wall of vehicle frame casing 11, or may be made of
`
`pipes disposed outside of casings 11 and 12, for example.
`
`[0075]
`
`Fluid delivered from a delivery port of charge pump 20 is taken out of vehicle frame
`
`casing 11 again, and is supplied into a charge fluid passage 4a formed in center section 4 via a
`
`line filter 26, a fluid passage L2 and a charge port P2.
`
`In the embodiment shown in Fig. 2,
`
`charge fluid passage 4a has an open end serving as charge port P2 at a rear end surface of
`
`center section 4, and fluid passage L2 is connected to charge port P2.
`
`[0076]
`
`A relief valve 28 is provided in center section 4 so as to adjust a hydraulic pressure of
`
`fluid in charge fluid passage 4a of center section 4. Fluid released from relief valve 28 is
`
`drained into a chamber in HST housing 5 forward from center section 4 via a drain fluid
`
`passage 4b formed in center section 4. Referring to Fig. 1, HST housing 5 has a drain port for
`
`draining fluid from the inside of HST housing 5. This drain port is normally plugged with a
`
`drain cap 29, as shown in Fig. 2. Fluid from the drain port is drained to the fluid sump in HST
`
`housing 5 or vehicle frame casing 11. This fluid sump may be fluidly connected to a fluid
`
`sump in aXle casing 12 via a fluid passage L5, as shown in Fig. 13.
`
`[0077]
`
`Referring to Fig. 13, center section 4 is formed therein with a pair of main fluid
`
`passages MLl and ML2 that are interposed between hydraulic pump 2 and hydraulic motor 3.
`
`Center section 4 is provided therein with a pair of charge valve units CV1 and CV2. The fluid
`
`in charge fluid passage 4a has a hydraulic pressure regulated by relief valve 28. When main
`
`fluid passage MLl is hydraulically depressed, a check valve 45 in charge valve unit CV1 is
`
`opened so that the fluid in charge fluid passage 4a is supplied to main fluid passage MLl via
`
`opened check valve 45 in charge valve unit CV1. When main fluid passage ML2 is
`
`hydraulically depressed, a check valve 45 in charge valve unit CV2 is opened so that the fluid
`
`in charge fluid passage 4a is supplied to main fluid passage ML2 via opened check valve 45 in
`
`charge valve unit CV2. Each of charge valve units CV1 and CV2 includes a relief valve 46
`
`-12-
`
`
`
`Atty. Docket No. 0666.5620004
`(xx—233.2)
`
`that bypasses corresponding check valve 45 so as to regulate the hydraulic pressure in
`
`corresponding main fluid passage ML1 or ML2.
`
`[0078]
`
`One of charge valve units CV1 and CV2 includes an orifice 47 bypassing
`
`corresponding check valve 45 so that orifice 47 functions to expand a neutral region of HST 1.
`
`If main fluid passage ML2 is designated to have a higher hydraulic pressure than that of main
`
`fluid passage MLl during backward traveling of the vehicle, preferably, charge valve unit
`
`CV2 for supplying fluid to main fluid passage ML2 has orifice 47.
`
`[0079]
`
`Referring to the hydraulic circuit diagram of Fig. 13, a general configuration of servo
`
`set 40 and a fluid supply system for supplying fluid from charge pump 20 to servo unit 60 of
`
`servo set 40. A delivery fluid passage from charge pump 20 passes line filter 26 and then is
`
`bifurcated into fluid passages L2 and L3. Fluid passage L2 is extended into HST 1. Fluid
`
`passage L3 is extended to servo unit 60. In this way, charge pump 20 supplies hydraulic fluid
`
`to both HST 1 and servo unit 60 for controlling movable swash plate 6 of HST 1.
`
`[0080]
`
`Servo unit 60 includes a hydraulic cylinder 32 and proportional pressure control valves
`
`35 and 36. Piston 33 serving as the actuator for controlling the position of movable swash
`
`plate 6 is slidably fitted in hydraulic cylinder 32. Opposite piston rods 33a and 33b are
`
`extended from piston 33 and project outward from opposite ends of hydraulic cylinder 32. The
`
`tip of piston rod 33a is pivotally connected to second arm 109 as mentioned above.
`
`[0081]
`
`Proportional pressure control valve 35 is adapted to supply or discharge fluid to and
`
`from a fluid chamber 32a formed in hydraulic cylinder 32 on one side of piston 33.
`
`Proportional pressure control valve 36 is adapted to supply or discharge fluid to and from a
`
`fluid chamber 32b formed in hydraulic cylinder 32 on the other side of piston 33. Proportional
`
`pressure control valves 35 and 36 are proportional solenoid valves provided with respective
`
`proportional solenoids 35a and 36a. Proportional pressure control valve 35 has a valve port
`
`35d fluidly connected to fluid chamber 32a in hydraulic cylinder 32 via a hydraulic fluid
`
`passage 43. Proportional pressure control valve 36 has a valve port 36d fluidly connected to
`
`fluid chamber 32b in hydraulic cylinder 32 via a hydraulic fluid passage 44. One of
`
`proportional pressure control valves 35 and 36 is designated so as to be excited during forward
`
`traveling of the vehicle, and the other of proportional pressure control valves 35 and 36 so as to
`
`be excited during backward traveling of the vehicle. Either proportional pressure control
`
`-13-
`
`
`
`Atty. Docket No. 0666.5620004
`(KK-233.2)
`
`valve 35 or 36, which is excited, supplies fluid from its valve port 35
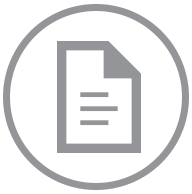
Accessing this document will incur an additional charge of $.
After purchase, you can access this document again without charge.
Accept $ ChargeStill Working On It
This document is taking longer than usual to download. This can happen if we need to contact the court directly to obtain the document and their servers are running slowly.
Give it another minute or two to complete, and then try the refresh button.
A few More Minutes ... Still Working
It can take up to 5 minutes for us to download a document if the court servers are running slowly.
Thank you for your continued patience.
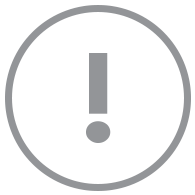
This document could not be displayed.
We could not find this document within its docket. Please go back to the docket page and check the link. If that does not work, go back to the docket and refresh it to pull the newest information.
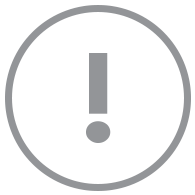
Your account does not support viewing this document.
You need a Paid Account to view this document. Click here to change your account type.
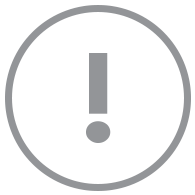
Your account does not support viewing this document.
Set your membership
status to view this document.
With a Docket Alarm membership, you'll
get a whole lot more, including:
- Up-to-date information for this case.
- Email alerts whenever there is an update.
- Full text search for other cases.
- Get email alerts whenever a new case matches your search.
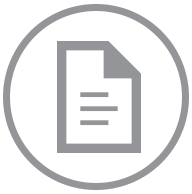
One Moment Please
The filing “” is large (MB) and is being downloaded.
Please refresh this page in a few minutes to see if the filing has been downloaded. The filing will also be emailed to you when the download completes.
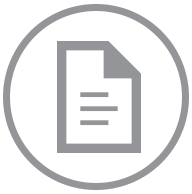
Your document is on its way!
If you do not receive the document in five minutes, contact support at support@docketalarm.com.
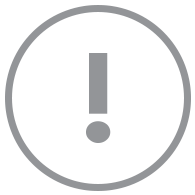
Sealed Document
We are unable to display this document, it may be under a court ordered seal.
If you have proper credentials to access the file, you may proceed directly to the court's system using your government issued username and password.
Access Government Site