`
`TECHNICAL FIELD
`
`5
`
`10
`
`15
`
`20
`
`25
`
`30
`
`The present invention relates to surgical instruments, and more particularly, to surgical
`
`instruments that may be manually operated to perform laparoscopic operations or various
`
`surgical operations.
`
`BACKGROUND ART
`
`A surgical operation is an operation for curing a disease by cutting,
`
`incising, and
`
`processing skin, membranes, or other tissues by using medical instruments. However, open
`
`surgery, which cuts and opens the skin of a surgical region and cures, shapes, or removes an
`
`organ therein, may cause bleeding, side effects, pain, scars, or the like. Therefore, a surgical
`
`operation, which is performed by forming a hole through the skin and inserting a medical
`
`instrument, for example, a laparoscope, a surgical instrument, or a surgical microscope thereinto,
`
`or a robotic surgical operation have recently become popular alternatives.
`
`The surgical instrument is an instrument for performing, by a surgeon, an operation on a
`
`surgical region by operating an end tool, which is installed at one end of a shaft inserted into a
`
`hole formed through the skin, by using an operator or by using a robotic arm. The end tool
`
`provided in the surgical instrument performs a rotating operation, a gripping operation, a cutting
`
`operation, or the like through a predetermined structure.
`
`However, since a conventional surgical instrument uses an unbendable end tool, it is not
`
`suitable for accessing a surgical region and performing various surgical operations. In order to
`
`solve this problem, a surgical instrument having a bendable end tool has been developed.
`
`However, an operation of an operator for bending the end tool to perform a surgical operation is
`
`not intuitively identical to an actual bending operation of the end tool for performing the surgical
`
`operation. Therefore, for surgical operators, it is difficult to perform an intuitive operation, and it
`
`takes a long time to learn how to use the surgical instrument.
`
`Information disclosed in this Background section was already known to the inventors
`
`before achieving the present invention or is technical information acquired in the process of
`
`
`
`achieving the present invention. Therefore, it may contain information that does not form the
`
`prior art that is already known to the public in this country.
`
`DETAILED DESCRIPTION OF THE INVENTION
`
`TECHNICAL PROBLEM
`
`The present invention provides a surgical instrument that is configured to intuitively
`
`match an actual operation of bending an end tool or performing a surgical operation with a
`
`corresponding operation of an operator. More particularly, to this end, the present invention
`
`provides an end tool having various degrees of freedom, an operator configured to intuitively
`
`control an operation of the end tool, and an operating force transmitter configured to transmit an
`
`operating force of the operator so that the end tool may operate in accordance with an operation
`
`of the operator.
`
`TECHNICAL SOLUTION
`
`According to an embodiment of the present invention, a surgical instrument includes: an
`
`end tool including a first jaw and a second jaw configured to rotate independently; an operator
`
`including a pitch operator controlling a pitch motion of the end tool, a yaw operator controlling a
`
`yaw motion of the end tool, and an actuation operator controlling an actuation motion of the end
`
`tool; an operating force transmitter including a first jaw wire connected with the first jaw to
`
`transmit an operation of the operator to the first jaw, a second jaw wire connected with the
`
`second jaw to transmit an operation of the operator to the second jaw, and one or more
`
`differential members transmitting a rotation of the yaw operator or the actuation operator to the
`
`first jaw or the second jaw via the first jaw wire or the second jaw wire; and a connector
`
`configured to extend in a first direction (X axis) and having one end portion coupled to the end
`
`tool and the other end portion coupled to the operator to connect the operator and the end tool,
`
`wherein the pitch operator
`
`is configured to rotate around a second direction (Y axis)
`
`perpendicular to the first direction; and at least a portion of the operator is configured to be more
`
`adjacent to the end tool than a rotating axis of the operator in at least any one operation state of
`
`the operator.
`
`10
`
`15
`
`20
`
`25
`
`30
`
`
`
`According to another embodiment of the present invention, an end tool includes: a first
`
`jaw and a second jaw configured to rotate independently of each other; a J ll pulley coupled with
`
`the first jaw and configured to rotate around a first axis formed at an end tool hub; a J 16 pulley
`
`formed at one side of the J ll pulley and configured to rotate around a second axis formed at one
`
`side of the first axis; a J 12 pulley and a J 14 pulley formed at one side of the J 16 pulley, and
`
`configured to rotate around a third axis formed at a predetermined angle with the first axis, and
`
`formed at one side of the end tool hub; a J2l pulley coupled with the second jaw and configured
`
`to rotate around an axis that is substantially identical to or parallel to the first axis; a J26 pulley
`
`formed at one side of the J21 pulley and configured to rotate around an axis that is substantially
`
`identical to or parallel to the second axis; and a J22 pulley and a J24 pulley formed at one side of
`
`the J26 pulley and configured to rotate around an axis that is substantially identical to or parallel
`
`to the third axis, wherein a first jaw wire is configured to at least partially contact the J 12 pulley,
`
`the J ll pulley, the J 16 pulley, and the J 14 pulley; and a second jaw wire is configured to at least
`
`partially contact the J22 pulley, the J21 pulley, the J26 pulley, and the J24 pulley.
`
`These and/or other aspects will become apparent and more readily appreciated from the
`
`following description of the invention, taken in conjunction with the accompanying drawings.
`
`ADVANTAGEOUS EFFECTS OF THE INVENTION
`
`According to the present invention, since an operation direction of the operator by a
`
`surgical operator and an operation direction of the end tool are intuitively identical to each other,
`
`the convenience of the surgical operator may be improved, and the accuracy, reliability, and the
`
`quickness of a surgical operation may be improved.
`
`DESCRIPTION OF THE DRAWINGS
`
`FIG. 1A is a schematic diagram illustrating a pitch operation of a conventional surgical
`
`instrument, and FIG. 1B is a schematic diagram illustrating a yaw operation thereof.
`
`FIG. 1C is a schematic diagram illustrating a pitch operation of another conventional
`
`surgical instrument, and FIG. 1D is a schematic diagram illustrating a yaw operation thereof.
`
`10
`
`15
`
`20
`
`25
`
`30
`
`
`
`FIG. IE is a schematic diagram illustrating a pitch operation of a surgical instrument
`
`according to the present invention, and FIG.
`
`lF is a schematic diagram illustrating a yaw
`
`operation thereof.
`
`FIG. 2 is a perspective view of a surgical instrument according to a first embodiment of
`
`the present invention.
`
`FIG. 3 is an internal perspective view of the surgical instrument of FIG. 2.
`
`FIG. 4 is a side view of the surgical instrument of FIG. 3.
`
`FIG. 5 is a perspective view illustrating an upper portion of an operator of the surgical
`
`instrument of FIG. 3.
`
`FIG. 6 is a perspective view illustrating a lower portion of the operator of the surgical
`
`instrument of FIG. 3.
`
`FIGS. 7 and 8 are perspective views illustrating an end tool of the surgical instrument of
`
`FIG. 3.
`
`FIG. 3.
`
`FIG. 3.
`
`FIG. 3.
`
`FIG. 9A is a plan view illustrating an end tool of the surgical instrument of FIG. 3.
`
`FIG. 9B is a plan view illustrating an end tool of a conventional surgical instrument.
`
`FIG. 10 is a schematic view illustrating a pitch operation of the surgical instrument of
`
`FIG. ll is a perspective view illustrating a pitch operation of the surgical instrument of
`
`FIGS. 12 and 13 are views illustrating a yaw operation of the surgical instrument of FIG.
`
`FIGS. 14 and 15 are views illustrating an actuation operation of the surgical instrument of
`
`10
`
`15
`
`20
`
`FIG. 16 is a perspective view of a surgical instrument according to a second embodiment
`
`25
`
`of the present invention.
`
`FIG. 17 is a plan view of the surgical instrument of FIG. 16.
`
`FIG. 18 is a perspective view illustrating an operator of the surgical instrument of FIG.
`
`16.
`
`30
`
`FIG. 19 is a view illustrating a yaw operation of the surgical instrument of FIG. 16.
`
`FIGS. 20 and 21 are views illustrating an actuation operation of the surgical instrument of
`
`FIG. 16.
`
`
`
`BEST MODE
`
`The present
`
`invention may include various embodiments and modifications, and
`
`particular embodiments thereof are illustrated in the drawings and will be described herein in
`
`detail. However,
`
`it will be understood that
`
`the present
`
`invention is not
`
`limited to the
`
`embodiments and includes all modifications, equivalents and substitutions falling within the
`
`spirit and scope of the present invention. In the following description, detailed descriptions of
`
`well—known functions or configurations will be omitted since they would unnecessarily obscure
`
`the subject matters of the present invention.
`
`Although terms such as "first" and "second" may be used herein to describe various
`
`elements or components, these elements or components should not be limited by these terms.
`
`These terms are only used to distinguish one element or component from another element or
`
`component.
`
`The terminology used herein is for the purpose of describing particular embodiments only
`
`and is not intended to limit the present invention. As used herein, the singular forms "a", "an",
`
`and "the" are intended to include the plural forms as well, unless the context clearly indicates
`
`otherwise. It will be understood that terms such as "comprise", "include", and "have", when used
`
`herein, specify the presence of stated features, integers, steps, operations, elements, components,
`
`or combinations thereof, but do not preclude the presence or addition of one or more other
`
`features, integers, steps, operations, elements, components, or combinations thereof.
`
`Hereinafter, embodiments of the present
`
`invention will be described in detail with
`
`reference to the accompanying drawings. In the following description, like reference numerals
`
`denote like elements, and redundant descriptions thereof will be omitted.
`
`Also, it will be understood that various embodiments of the present invention may be
`
`interpreted or implemented in combination, and technical features of each embodiment may be
`
`interpreted or implemented in combination with technical features of other embodiments.
`
`<First Embodiment of Surgical Instrument>
`
`A surgical instrument according to the present invention is characterized in that, for at
`
`least any one of the pitch, yaw, and actuation operations, when an operator is rotated in any one
`
`10
`
`15
`
`20
`
`25
`
`30
`
`
`
`direction, an end tool rotates in a direction that is intuitively identical to an operation direction of
`
`the operator.
`
`FIG. 1A is a schematic diagram illustrating a pitch operation of a conventional surgical
`
`instrument, and FIG. 1B is a schematic diagram illustrating a yaw operation thereof.
`
`Referring to FIG. 1A, in order to perform a pitch operation of a conventional surgical
`
`instrument, in a state where an end tool 120a is formed in front of an end tool rotation center
`
`121a and an operator llOa is formed in back of an operator rotation center llla, when the
`
`operator llOa is rotated in a clockwise direction, the end tool 120a also rotates in the clockwise
`
`direction, and when the operator llOa is rotated in a counterclockwise direction, the end tool
`
`120a also rotates in the counterclockwise direction. Referring to FIG. 1B, in order to perform a
`
`yaw operation of a conventional surgical instrument, in a state where an end tool 120a is formed
`
`in front of an end tool rotation center 121a and an operator llOa is formed in back of an operator
`
`rotation center llla, when the operator llOa is rotated in a clockwise direction, the end tool
`
`120a also rotates in the clockwise direction, and when the operator
`
`llOa is rotated in a
`
`counterclockwise direction, the end tool 120a also rotates in the counterclockwise direction. In
`
`this case, from the viewpoint of a horizontal direction of a user, when the user moves the
`
`operator llOa to the left, the end tool 120a moves to the right, and when the user moves the
`
`operator llOa to the right, the end tool 120a moves to the left. Consequently, since the operation
`
`direction of the user and the operation direction of the end tool are opposite to each other, the
`
`user may make an error and the operation of the user may not be easy.
`
`FIG. 1C is a schematic diagram illustrating a pitch operation of another conventional
`
`surgical instrument, and FIG. 1D is a schematic diagram illustrating a yaw operation thereof.
`
`Referring to FIG. 1C,
`
`in order for another conventional surgical
`
`instrument
`
`to be
`
`mirror—symmetrically formed to perform a pitch operation, in a state where an end tool 120b is
`
`formed in front of an end tool rotation center 121b and an operator llOb is formed in back of an
`
`operator rotation center lllb, when the operator llOb is rotated in the clockwise direction, the
`
`end tool 120b rotates in the counterclockwise direction, and when the operator llOb is rotated in
`
`the counterclockwise direction, the end tool 120b rotates in the clockwise direction. In this case,
`
`from the viewpoint of the rotation direction of the operator and the end tool,
`
`the rotation
`
`direction of the operator llOb by the user and the corresponding rotation direction of the end tool
`
`120b are opposite to each other. Consequently, the user may confuse the operation direction, the
`
`10
`
`15
`
`20
`
`25
`
`30
`
`
`
`operation of a joint may not be intuitive, and an error may be caused accordingly. Also, referring
`
`to FIG. 1D, in order to perform a yaw operation, in a state where an end tool 120b is formed in
`
`front of an end tool rotation center 121b and an operator 110b is formed in back of an operator
`
`rotation center 111b, when the operator 110b is rotated in the clockwise direction, the end tool
`
`120b rotates in the counterclockwise direction, and when the operator 110b is rotated in the
`
`counterclockwise direction, the end tool 120b rotates in the clockwise direction. In this case,
`
`from the viewpoint of the rotation direction of the operator and the end tool,
`
`the rotation
`
`direction of the operator 110b by the user and the corresponding rotation direction of the end tool
`
`120b are opposite to each other. Consequently, the user may confuse the operation direction, the
`
`operation of a joint may not be intuitive, and an error may be caused accordingly.
`
`In order to solve this problem, a surgical instrument according to an embodiment of the
`
`present invention illustrated in FIGS. 1E and IF is characterized in that an end tool 120C is
`
`formed in front of an end tool rotation center 121c and an operator 110c is also formed in front
`
`of an operator rotation center 111c, so that the operations of the operator 110c and the end tool
`
`120C are intuitively identical to each other.
`
`In other words, unlike a conventional example of the configuration in which the operator
`
`becomes adjacent to the user (i.e., becomes distant from the end tool) with respect to its own
`
`joint as illustrated in FIGS. 1A, 1B, 1C, and 1D,
`
`the surgical instrument according to an
`
`embodiment of the present invention illustrated in FIGS. 1E and IF is formed such that at least a
`
`portion of the operator may become more adjacent to the end tool with respect to its own joint
`
`(i.e., than its own joint).
`
`In other words, in the case of the conventional surgical instrument illustrated in FIGS. 1A,
`
`1B, 1C, and 1D, since the end tool is located in front of its own rotation center but the operator is
`
`formed in back of its own rotation center and thus the end tool moving the front with the rear
`
`fixed is moved by the operation of the operator moving the rear with the front fixed, they are not
`
`structurally intuitively identical to each other. Consequently, in the operation of the operator and
`
`the operation of the end tool, from the viewpoint of the horizontal direction or the viewpoint of
`
`the rotation direction, a mismatch may occur, the user may be confused, the operation of the
`
`operator may be difficult to perform intuitively rapidly, and an error may be caused accordingly.
`
`On the other hand, in the case of the surgical instrument according to an embodiment of the
`
`present invention, since both the end tool and the operator move with respect to the rotation
`
`10
`
`15
`
`20
`
`25
`
`30
`
`
`
`center formed at the rear, the operations may be structurally intuitively identical to each other.
`
`Consequently, the user may intuitively rapidly control the end tool direction, and the possibility
`
`of causing an error may be significantly reduced. A specific mechanism enabling this function
`
`will be described below.
`
`FIG. 2 is a perspective view of a surgical instrument according to a first embodiment of
`
`the present invention, FIG. 3 is an internal perspective view of the surgical instrument of FIG. 2,
`
`and FIG. 4 is a side view of the surgical instrument of FIG. 3.
`
`Referring to FIGS. 2, 3, and 4, a surgical instrument 100 according to a first embodiment
`
`of the present invention includes an operator 110, an end tool 120, an operating force transmitter
`
`130, and a connector 140. Herein, the connector 140 may be formed to have the shape of a
`
`hollow shaft, so that one or more wires (which will be described later) may be accommodated
`
`therein. The operator 110 may be coupled to one end portion of the connector 140, and the end
`
`tool 120 may be coupled to the other end portion of the connector 140, so that the connector 140
`
`may connect the operator 110 and the end tool 120.
`
`In detail, the operator 110 is formed at one end portion of the connector 140, and is
`
`provided as an interface having, for example, a tweezer shape, a stick shape, or a lever shape,
`
`which may be directly operated by a surgical operator. When a surgical operator operates the
`
`operator 110, the end tool 120, which is connected to the interface and is inserted into the body
`
`of a surgical patient, performs an operation, thereby performing a surgical operation. Although
`
`FIG. 2 illustrates that the operator 110 is formed to have the shape of a handle that may be
`
`rotated with a finger inserted thereinto, the inventive concept is not limited thereto, and the
`
`operator 110 may have various shapes that may be connected with the end tool 120 to operate the
`
`end tool 120.
`
`The end tool 120 is formed at the other end portion of the connector 140 and is inserted
`
`into a surgical region to perform a necessary surgical operation. As an example of the end tool
`
`120, a pair of jaws, namely, first and second jaws 121 and 122, may be used to perform a grip
`
`operation as illustrated in FIG. 2. However, the inventive concept is not limited thereto, and
`
`various surgical devices may be used as the end tool 120. For example, a one—armed cautery may
`
`be used as the end tool 120. The end tool 120 is connected with the operator 110 by the operating
`
`force transmitter 130 to receive an operating force of the operator 110 through the operating
`
`10
`
`15
`
`20
`
`25
`
`30
`
`
`
`force transmitter 130, thereby performing a necessary surgical operation such as a grip, cutting,
`
`or suturing.
`
`Herein, the end tool 120 of the surgical instrument 100 according to the first embodiment
`
`of the present invention is formed to rotate in two or more directions. For example, the end tool
`
`120 may be formed to perform a pitch motion around a Y axis of FIG. 2 and also perform a yaw
`
`motion and an actuation motion around a Z axis of FIG. 2. This will be described later in detail.
`
`The operating force transmitter 130 connects the operator 110 and the end tool 120 to
`
`transmit an operating force of the operator 110 to the end tool 120, and may include a plurality of
`
`wires, pulleys, links, nodes, and gears.
`
`Hereinafter, the operator 110, the end tool 120, and the operating force transmitter 130 of
`
`the surgical instrument 100 of FIG. 2 will be described in more detail.
`
`(Operator)
`
`FIG. 5 is a perspective view illustrating an upper portion of the operator of the surgical
`
`instrument of FIG. 3, and FIG. 6 is a perspective view illustrating a lower portion of the operator
`
`of the surgical instrument of FIG. 3.
`
`Referring to FIGS. 2 to 6, the operator 110 of the surgical instrument 100 according to
`
`the first embodiment of the present invention includes a pitch operator lll controlling a pitch
`
`motion of the end tool 120, a yaw operator ll2 controlling a yaw motion of the end tool 120, and
`
`an actuation operator ll3 controlling an actuation motion of the end tool 120.
`
`First, as an example of the use state of the surgical instrument 100 of FIG. 2, the user
`
`may grip a pitch operating handle (or bar) 1112 of the pitch operator 111 with the palm and
`
`rotate the pitch operating handle 1112 to perform a pitch motion, may insert the index finger into
`
`the yaw operator 112 and rotate the yaw operator 112 to perform a yaw motion, and may insert
`
`the big finger into the actuation operator 113 and rotate the actuation operator 113 to perform an
`
`10
`
`15
`
`20
`
`25
`
`actuation motion.
`
`A pitch operation, a yaw operation, and an actuation operation used in the present
`
`invention are summarized as follows:
`
`First, the pitch operation refers to an operation of rotating the end tool 120 in the vertical
`
`direction with respect to the connector 140, that is, an operation of rotating around the Y axis of
`
`30
`
`FIG. 2. In other words, the pitch operation refers to a vertical rotation of the end tool 120, which
`
`is formed to extend in the extension direction (the X—axis direction of FIG. 2) of the connector
`
`
`
`140, around the Y axis with respect to the connector 140. The yaw operation refers to an
`
`operation of rotating the end tool 120 in the horizontal direction with respect to the connector
`
`140, that is, an operation of rotating around the Z axis of FIG. 2. In other words, the yaw
`
`operation refers to a horizontal rotation of the end tool 120, which is formed to extend in the
`
`extension direction (the X—axis direction of FIG. 2) of the connector 140, around the Z axis with
`
`respect to the connector 140. The actuation operation refers a folding or unfolding operation of
`
`the jaws 121 and 122 when the jaws 121 and 122 rotate in opposite directions while rotating
`
`around the same rotating axis as the yaw operation. That is, the actuation operation refers to
`
`rotations of the jaws 121 and 122, which is formed at the end tool 120, in opposite directions
`
`10
`
`around the Z axis.
`
`15
`
`20
`
`Herein, when the operator 110 of the surgical instrument 100 is rotated in one direction
`
`with respect to the connector 140, the end tool 120 rotates with respect to the connector 140 in a
`
`direction that is intuitively identical to an operation direction of the operator 110. In other words,
`
`when the pitch operator 111 of the operator llO rotates in one direction, the end tool 120 rotates
`
`in a direction intuitively identical to the one direction to perform a pitch operation, and when the
`
`yaw operator 112 of the operator llO rotates in one direction, the end tool 120 rotates in a
`
`direction intuitively identical to the one direction to perform a yaw operation. Herein, it may be
`
`said that the intuitively identical direction refers to a case where a movement direction of the
`
`index finger of the user gripping the operator 110 is substantially identical to a movement
`
`direction of the end portion of the end tool 120. In addition, the identical direction may not be an
`
`exactly identical direction on a three—dimensional coordinate system. For example, the identical
`
`direction may refer to a case where when the index finger of the user moves to the left, the end
`
`portion of the end tool 120 also moves to the left, and when the index finger of the user moves to
`
`the right, the end portion of the end tool 120 also moves to the right, in order to maintain
`
`25
`
`intuition.
`
`To this end, in the surgical instrument 100, the operator 110 and the end tool 120 are
`
`formed in the same direction with respect to a plane perpendicular to the extension axis (X axis)
`
`of the connector 140. That is, in view of a YZ plane of FIG. 2, the operator 110 is formed to
`
`extend in a +X—axis direction, and the end tool 120 is also formed to extend in the +X—axis
`
`30
`
`direction. In other words, it may be said that a formation direction of the end tool 120 at one end
`
`portion of the connector 140 may be identical to a formation direction of the operator 110 at the
`
`10
`
`
`
`other end portion of the connector 140 in view of the YZ plane. In other words, it may be said
`
`that the operator 110 is formed to extend away from the body of the user gripping the operator
`
`110, that is, the operator 110 is formed to extend toward the end tool 120.
`
`In detail, in the case of a related art surgical instrument, an operation direction of an
`
`operator by a user is different from and is not intuitively identical to an actual operation direction
`
`of an end tool. Therefore, a surgical operator has difficulty in performing an intuitive operation,
`
`and it takes a long time to skillfully move the end tool in a desired direction. Also, in some cases,
`
`a faulty operation may occur, thus damaging a surgical patient.
`
`In order to solve such problems,
`
`the surgical
`
`instrument 100 according to the first
`
`embodiment of the present invention is configured such that an operation direction of the
`
`operator 110 is intuitively identical to an operation direction of the end tool 120. To this end, the
`
`operator 110 and the end tool 120 are formed on the same side in view of the YZ plane including
`
`a pitch operating axis 1111. This will be described below in more detail.
`
`The pitch operator 111 includes a pitch operating axis 1111 and a pitch operating handle
`
`1112. Herein, the pitch operating axis 1111 may be formed in the direction parallel to the Y axis,
`
`and the pitch operating handle 1112 may be connected with the pitch operating axis 1111 to
`
`rotate along with the pitch operating axis 1111. For example, when the user grips and rotates the
`
`pitch operating handle 1112, the pitch operating handle 1112 rotates around the pitch operating
`
`axis 1111. Then, the resulting rotating force is transmitted to the end tool 120 through the
`
`operating force transmitter 130, an operator control member 115, and an end tool control
`
`member 123, so that the end tool 120 rotates in the same direction as the rotation direction of the
`
`pitch operator 111. That is, when the pitch operator 111 rotates in the clockwise direction around
`
`the pitch operating axis 1111, the end tool 120 also rotates in the clockwise direction around an
`
`axis parallel to the pitch operating axis 1111, and when the pitch operator 111 rotates in the
`
`counterclockwise direction around the pitch operating axis 1111, the end tool 120 also rotates in
`
`the counterclockwise direction around the axis parallel to the pitch operating axis 1111.
`
`The yaw operator 112 and the actuation operator 113 are formed on one end portion of
`
`the pitch operating handle 1112 of the pitch operator 111. Thus, when the pitch operator 111
`
`rotates around the pitch operating axis 1111, the yaw operator 112 and the actuation operator 113
`
`also rotate along with the pitch operator 111. FIG. 2 illustrates a state in which the pitch
`
`operating handle 1112 of the pitch operator 111 is perpendicular to the connector 140, while FIG.
`
`10
`
`15
`
`20
`
`25
`
`30
`
`11
`
`
`
`11 illustrates a state in which the pitch operating handle 1112 of the pitch operator 111 is at an
`
`angle to the connector 140 by rotating around the pitch operating axis 1111 by some degree.
`
`Therefore, a coordinate system of the yaw operator 112 and the actuation operator 113 is
`
`not fixed, but relatively changes according to the rotation of the pitch operator 111. That is, FIG.
`
`2 illustrates that a yaw operating axis 1121 of the yaw operator 112 is parallel to the Z axis and
`
`an actuation operating axis 1131 of the actuation operator 113 is parallel to the Y axis. However,
`
`when the pitch operator 111 is rotated, the yaw operating axis 1121 of the yaw operator 112 is
`
`not parallel to the Z axis. That is,
`
`the coordinate system of the yaw operator 112 and the
`
`actuation operator 113 change according to the rotation of the pitch operator 111. However, for
`
`convenience of description, the coordinate system of the yaw operator 112 and the actuation
`
`operator 113 will be described on the assumption that the pitch operating handle 1112 is
`
`perpendicular to the connector 140 as illustrated in FIG. 2.
`
`The yaw operator 112 includes a yaw operating axis 1121 and a yaw operating member
`
`1122. Herein, the yaw operating axis 1121 may be formed to be at a predetermined angle to an
`
`XY plane where the connector 140 is formed. For example, the yaw operating axis 1121 may be
`
`formed in a direction parallel to the Z axis as illustrated in FIG. 3, and when the pitch operator
`
`111 rotates, the coordinate system of the yaw operator 112 may relatively change as described
`
`above. However, the inventive concept is not limited thereto, and the yaw operating axis 1121
`
`may be formed in various directions by ergonomic design according to the structure of the hand
`
`of the user gripping the yaw operator 112.
`
`The yaw operating member 1122 is formed to rotate around the yaw operating axis 1121.
`
`For example, when the user holds and rotates the yaw operating member 1122 by the index
`
`finger, the yaw operating member 1122 rotates around the yaw operating axis 1121. Then, the
`
`resulting rotating force is transmitted to the end tool 120 through the operating force transmitter
`
`130, so that the jaws 121 and 122 of the end tool 120 horizontally rotate in the same direction as
`
`the rotation direction of the yaw operating member 1122. To this end, a pulley 1121a may be
`
`formed at the yaw operating axis 1121. Also, a yaw wire 130Y may be connected to the pulley
`
`1121a, and the rotating force may be transmitted to the end tool 120 through the operating force
`
`transmitter 130 including the yaw wire 130Y, so that the jaws 121 and 122 of the end tool 120
`
`10
`
`15
`
`20
`
`25
`
`30
`
`may perform a yaw operation.
`
`12
`
`
`
`The actuation operator 113 includes an actuation operating axis 1131 and an actuation
`
`operating member 1132. Herein, the actuation operating axis 1131 may be formed to be at a
`
`predetermined angle to the X2 plane where the connector 140 is formed. For example, the
`
`actuation operating axis 1131 may be formed in a direction parallel to the Y axis as illustrated in
`
`FIG. 2, and when the pitch operator 111 rotates, the coordinate system of the actuation operator
`
`113 may relatively change as described above. However, the inventive concept is not limited
`
`thereto, and the actuation operating axis 1131 may be formed in various directions by ergonomic
`
`design according to the structure of the hand of the user gripping the actuation operator 113.
`
`The actuation operating member 1132 is formed to rotate around the actuation operating
`
`axis 1131. For example, when the user holds and rotates the actuation operating member 1132 by
`
`the big finger, the actuation operating member 1132 rotates around the actuation operating axis
`
`1131. Then, the resulting rotating force is transmitted to the end tool 120 through the operating
`
`force transmitter 130, so that the jaws 121 and 122 of the end tool 120 perform an actuation
`
`operation. Herein, as described above, the actuation operation refers to an operation of folding or
`
`unfolding the jaws 121 and 122 by rotating the jaws 121 and 122 in opposite directions. That is,
`
`when the actuation operator 113 is rotated in one direction, as the first jaw 121 rotates in the
`
`counterclockwise direction and the second jaw 122 rotates in the clockwise direction, the end
`
`tool 120 is folded; and when the actuation operator 113 is rotated in the opposite direction, as the
`
`first jaw 121 rotates in the clockwise direction and the second jaw 122 rotates in the
`
`counterclockwise direction, the end tool 120 is unfolded.
`
`A pulley 1131a may be formed at one end portion of the actuation operating axis 1131.
`
`An actuation wire 130A may be connected to the pulley 1131a.
`
`Referring to FIG. 3, the pitch operating axis 111 of the pitch operator 111 and the end
`
`tool 120 are formed on the same or parallel axis (X axis) in the surgical instrument 100
`
`according to the first embodiment of the present invention. That is, the pitch operating axis 1111
`
`of the pitch operator 111 is formed at on
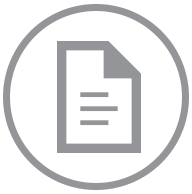
Accessing this document will incur an additional charge of $.
After purchase, you can access this document again without charge.
Accept $ ChargeStill Working On It
This document is taking longer than usual to download. This can happen if we need to contact the court directly to obtain the document and their servers are running slowly.
Give it another minute or two to complete, and then try the refresh button.
A few More Minutes ... Still Working
It can take up to 5 minutes for us to download a document if the court servers are running slowly.
Thank you for your continued patience.
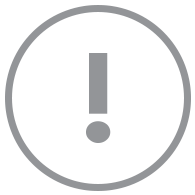
This document could not be displayed.
We could not find this document within its docket. Please go back to the docket page and check the link. If that does not work, go back to the docket and refresh it to pull the newest information.
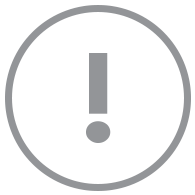
Your account does not support viewing this document.
You need a Paid Account to view this document. Click here to change your account type.
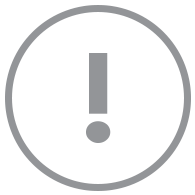
Your account does not support viewing this document.
Set your membership
status to view this document.
With a Docket Alarm membership, you'll
get a whole lot more, including:
- Up-to-date information for this case.
- Email alerts whenever there is an update.
- Full text search for other cases.
- Get email alerts whenever a new case matches your search.
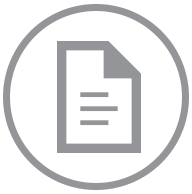
One Moment Please
The filing “” is large (MB) and is being downloaded.
Please refresh this page in a few minutes to see if the filing has been downloaded. The filing will also be emailed to you when the download completes.
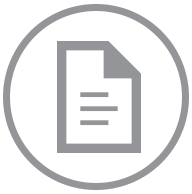
Your document is on its way!
If you do not receive the document in five minutes, contact support at support@docketalarm.com.
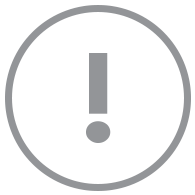
Sealed Document
We are unable to display this document, it may be under a court ordered seal.
If you have proper credentials to access the file, you may proceed directly to the court's system using your government issued username and password.
Access Government Site