`
`Intematlonal Bureau
`WORLD INTELLECTUAL PROPERTY ORGANIZATION
`
`
`
`(51) International Patent Classification 7 :
`
`H01L 31/068, 31/0352, 31/0224
`
`A1
`
`
`INTERNATIONAL APPLICATION PUBLISHED UNDER THE PATENT COOPERATION TREATY (PCT)
`WO 00/55923
`
`(11) InternationalPublication Number:
`(43) International Publication Date:
`
` 21 September 2000 (21.09.00)
`
`
`PCT/USOO/02609
`(81) Designated States: AE, AL, AM, AT, AU, AZ, BA, BB, BG,
`(21) International Application Number:
`
`BR, BY, CA, CH, CN, CU, CZ, DE, DK, EE, ES, FI, GB,
`GD, GE, GH, GM, HR, HU, ID, IL, IN, IS, JP, KE, KG,
`
`1 February 2000 (01.02.00)
` (22) International Filing Date:
`KP, KR, KZ, LC, LK, LR, LS, LT, LU, LV, MD, MG, MK,
`
`MN, MW, MX, NO, NZ, PL, PT, RO, RU, SD, SE, SG, SI,
`SK, SL, TJ, TM, TR, TT, UA, UG, UZ, VN, YU, ZA, ZW,
`
`(30) Priority Data:
`
`
`ARIPO patent (GH, GM, KE, LS, MW, SD, SL, SZ, TZ,
`17 March 1999 (17.03.99)
`US
`60/ 124,797
`
`
`UG, ZW), Eurasian patent (AM, AZ, BY, KG, KZ, MD,
`09/41 4,990
`7 October 1999 (07.10.99)
`US
`
`
`RU, TJ, TM), European patent (AT, BE, CH, CY, DE, DK,
`
`ES, FI, FR, GB, GR, IE, IT, LU, MC, NL, PT, SE), OAPI
`patent (BF, BJ, CF, CG, CI, CM, GA, GN, GW, ML, MR,
`(71) Applicant: EBARA SOLAR, INC.
`[US/US]; 811 Route 51
`
`NE, SN, TD, TG).
`South, Large, PA 15025 (US).
`
`(72) Inventors: MEIER, Daniel, L.; 264 Barclay Avenue, Pitts-
`
`
`burgh, PA 15221 (US). DAVIS, Hubelt, P.; 1141 Sper—
`ling Drive, Pittsburgh, PA 15221 (US). GARCIA, Ruth, A.;
`
`
`1910 Victoria Lane, Irwin, PA 15642 (US). SALAMI, Jalal;
`1121 Huston Drive, West Mifflin, PA 15122 (US).
`
`(74) Agents: SOCKOL, Marc, A. et 211.; Graham & James LLP, 600
`Hansen Way, Palo Alto, CA 94304—1043 (US).
`
`Published
`With international search report,
`Before the expiration of the time limit for amending the
`claims and to be republished in the event of the receipt of
`amendments.
`
`
`
`(54) Title: AN ALUMINUM ALLOY BACK JUNCTION SOLAR CELL AND A PROCESS FOR FABRICATIN THEREOF
`
`110
`
`
`
`(57) Abstract
`
`A process for fabricating a solar cell is described. The process includes: providing a base layer (118), and fabricating an emitter
`layer (120) Of p—type conductivity on a same side as the non—illuminated surface ( 128) of the base layer to provide a strongly doped p—type
`emitter layer and a p—n junction (124) between the n—type base layer (118) and the p—type emitter layer (120). The base layer of the present
`invention has n—type conductivity and is defined by an illuminated surface (126) and a non—illuminated surface (128) which is opposite to
`the illuminated surface.
`
`
`
`
`
`
`
`FOR THE PURPOSES OF INFORMATION ONLY
`
`Codes used to identify States party to the PCT on the front pages of pamphlets publishing international applications under the PCT.
`Slovenia
`SI
`Lesotho
`ES
`LS
`Albania
`SK
`Slovakia
`FI
`LT
`Lithuania
`Armenia
`SN
`LU
`FR
`Austria
`Senegal
`Luxembourg
`SZ
`Swaziland
`LV
`Latvia
`GA
`Australia
`TD
`Monaco
`Chad
`MC
`GB
`Azerbaijan
`TG
`MD
`GE
`Togo
`Republic of Moldova
`Bosnia and Herzegovina
`MG
`GH
`TJ
`Barbados
`Tajikistan
`Madagascar
`TM
`MK
`Turkmenistan
`GN
`The former Yugoslav
`Belgium
`TR
`GR
`Burkina Faso
`Turkey
`Republic of Macedonia
`TT
`Mali
`HU
`Trinidad and Tobago
`Bulgaria
`UA
`Ukraine
`IE
`Benin
`Mongolia
`UG
`IL
`Mauritania
`Brazil
`Uganda.
`United States of America
`US
`Malawi
`IS
`Belarus
`Uzbekistan
`UZ
`Mexico
`IT
`Canada
`Viet Nam
`VN
`JP
`Niger
`Central African Republic
`YU
`Netherlands
`KE
`Yugoslavia
`Congo
`Zimbabwe
`ZW
`Switzerland
`KG
`Norway
`New Zealand
`KP
`Céte d’Ivoire
`Poland
`Cameroon
`China
`Portugal
`Romania
`Cuba
`Russian Federation
`Czech Republic
`Sudan
`Germany
`Sweden
`Denmark
`Estonia
`Singapore
`
`
`ML
`MN
`MR
`MW
`MX
`NE
`NL
`NO
`NZ
`PL
`PT
`RO
`RU
`SD
`SE
`SG
`
`
`
`AL
`AM
`AT
`AU
`AZ
`BA
`BB
`BE
`BF
`BG
`8.]
`BR
`BY
`CA
`CF
`CG
`CH
`CI
`CM
`CN
`CU
`CZ
`DE
`DK
`EE
`
`Spain
`Finland
`France
`Gabon
`United Kingdom
`Georgia
`Ghana
`Guinea
`Greece
`Hungary
`Ireland
`Israel
`Iceland
`Italy
`Japan
`Kenya
`Kyrgyzstan
`Democratic People’s
`Republic of Korea
`Republic of Korea
`Kazakstan
`Saint Lucia
`Liechtenstein
`Sri Lanka
`Liberia
`
`KR
`KZ
`LC
`LI
`LK
`LR
`
`
`
`WO 00/55923
`
`PCT/USOO/02609
`
`AN ALUMINUM ALLOY BACK JUNCTION
`SOLAR CELL AND A PROCESS FOR
`
`FABRICATION THEREOF
`
`BACKGROUND OF THE INVENTION
`
`The present invention relates to an improved solar cell and a process for
`
`fabricating thereof. More particularly, the present invention relates to a solar
`
`cell including a p-n junction located near a non-illuminated surface of the
`
`solar cell and a process for fabricating thereof.
`
`Solar cells are widely used because they convert easily accessible energy
`
`from a light source, such as the sun, to electrical power to operate electrically
`
`driven devices, e.g., calculators, computers, and heaters used in homes. Figure
`
`1 shows a cross-sectional View of a layered stack that makes up a conventional
`
`silicon solar cell 10. Conventional silicon solar cell 10 typically includes a p-n
`
`junction 24 sandwiched between a p-type base layer 18 and an n—type layer 16,
`
`which is located near an illuminated (front) surface 11. The term “illuminated
`
`surface,” as used herein refers to the surface of a conventional solar cell that is
`
`exposed to light energy when the solar cell is active or under operation. Thus,
`
`the term “non- illuminated surface” refers to a surface that is opposite the
`
`illuminated surface. The basic structure of p—n junction 24 includes a
`
`heavily-doped (about 1020 cm'3) n—type emitter layer (11+) 16 at or near the
`
`illuminated surface 11 and disposed above a moderately-doped (about 1015 cm'
`
`
`
`WO 00/55923
`
`PCT/US00/02609
`
`3) p-type base layer (p) 18. Commercial embodiments of conventional solar
`
`cells typically include an optional anti-reflective coating 14 and a p+ layer 20
`
`that is formed between p-type base layer 18 and p—type silicon contact 22.
`
`A typical depth of p—n junction 24 from the top of the n+ emitter layer
`
`16 measures about.0.5um. A shallow front p—n junction 24 is desired in order
`
`to facilitate the collection of minority carriers that are created on both sides of
`
`p-n junction 24. Each photon of light that penetrates into p-type base layer 18
`
`and is absorbed by base layer 18 surrenders its energy to an electron in a
`
`bound state (covalent bond) and thereby frees it. This mobile electron, and
`
`the hole in the covalent bond it left behind (which hole is also mobile),
`
`comprise a potential element of electric current flowing from the solar cell. In
`
`order to contribute to this current, the electron and hole cannot recombine, but
`
`rather are separated by the electric field associated with p-n junction 24. If
`
`this happens, the electron will travel to n-type silicon contact 12 and the hole
`
`will travel to p-type silicon contact 22.
`
`In order to contribute to the solar cell current, photogenerated minority
`
`carriers (holes in the n+ emitter layer and electrons in the p-type base layer)
`
`should exist for a sufficiently long time so that they are able to travel by
`
`diffusion to p-n junction 24 where they are collected. The average distance
`
`over which minority carriers can travel without being lost by recombining
`
`2
`
`
`
`WO 00/55923
`
`PCT/USOO/02609
`
`with a majority carrier is called the minority carrier diffusion length. The
`
`minority carrier diffusion length generally depends on such factors as the
`
`concentration of defects in the silicon crystal (i.e. recombination centers) and
`
`the concentration of dopant atoms in the silicon. As the concentration of
`
`either defects or dopant atoms increases, the minority carrier diffusion length
`
`decreases. Thus, the diffusion length for holes in the heavily-doped n+
`
`emitter layer 16 is much less than the diffusion length for electrons in
`
`moderately-doped p—type base layer 18.
`
`Those skilled in the art will recognize that the n+ emitter layer 16 is
`
`nearly a “dead layer” in that few minority charge carriers created in emitter
`
`layer 16 are able to diffuse to p-n junction 24 without being lost by
`
`recombination. It is desirable to have n+ emitter layer 16 that is shallow or as
`
`close to surface of emitter layer 16 as possible for various reasons. By way of
`
`example, a shallow emitter layer allows relatively few photons to be absorbed
`
`in n+ emitter layer 16. Furthermore, the resulting photogenerated minority
`
`carriers created in n+ emitter layer 16 find themselves close enough to p-n
`
`junction 24 to have a reasonable chance of being collected (diffusion length 2
`
`junction depth).
`
`Unfortunately, in the conventional solar cell design, the depth of n+
`
`emitter layer is limited and cannot be as shallow as desired. Metal from
`
`3
`
`
`
`wo 00/55923
`
`PCT/USOO/02609
`
`emitter contacts 12, especially those formed by screen-printing and firing, can
`
`penetrate into p-n junction 24 and ruin or degrade it. The presence of metal in
`
`the p—n junction 24 “shorts” or “shunts” the junction. Therefore, although a
`
`shallow and lightly-doped n+ emitter layer 16 is desired in order to enhance
`
`the current produced by the cell, in practice, however, n+ emitter layer 16 is
`
`relatively deeper and more heavily-doped than desired to avoid shunting p-n
`
`junction 24. Consequently, in conventional solar cells, the deep location of
`
`n+ emitter layer 16 compromises the amount of current produced by the cell.
`
`What is needed is a structure and process for fabricating a silicon solar
`
`cell, which has a high minority carrier diffusion length, eliminates shunting of
`
`the p-n junction and does not compromise the amount of current produced.
`
`SUMMARY OF THE INVENTION
`
`In one aspect, the present invention provides a solar cell. The solar cell
`
`includes a base layer having dopant atoms of n—type conductivity and being
`
`defined by an illuminated surface and a non-illuminated surface. The
`
`illuminated surface has light energy impinging thereon when the solar cell
`
`is exposed to the light energy and the non-illuminated surface is opposite
`
`the illuminated surface. The solar cell further includes a back surface
`
`emitter layer that is made from an aluminum alloy to serve as a layer of p-
`
`
`
`wo 00/55923
`
`PCT/USOO/02609
`
`type conductivity. The solar cell further still includes a p—n junction layer
`
`disposed between the non—illuminated surface of the base layer and the
`
`back surface layer.
`
`In another aspect, the present invention provides a process for
`
`fabricating a solar cell. The process includes: (1) providing a base layer,
`
`(2) fabricating an emitter layer of p—type conductivity on a same side as
`
`the non-illuminated surface of the base layer to provide a strongly doped p-
`
`type emitter layer and a p-n junction between the n-type base layer and the
`
`p-type emitter layer. The base layer of the present invention has n—type
`
`conductivity and is defined by an illuminated surface and a non-
`
`illuminated surface. The illuminated surface has light energy impinging
`
`thereon when the solar cell is exposed to the light energy and the non-
`
`illuminated surface is opposite the illuminated surface.
`
`These and other features of the present invention will be described in
`
`more detail below in the detailed description of the invention and in
`
`conjunction with the following figures.
`
`
`
`WO 00/55923
`
`PCT/USOO/02609
`
`BRIEF DESCRIPTION OF THE DRAWINGS
`
`The present invention is illustrated by way of example, and not by way
`
`of limitation, in the figures of the accompanying drawings in which:
`
`Figure 1 shows a cross-sectional View of a conventional solar cell.
`
`Figure 2 shows a cross—sectional View of a solar cell, in accordance with
`
`an embodiment of the present invention.
`
`Figures 3A-3D show various stages of fabrication, according to one
`
`embodiment of the present invention, for the solar cell of Figure 2.
`
`Figure 4 shows a graph of a measured I—V curve of an aluminum alloy
`
`back junction dendritic web solar cell.
`
`Figure 5 shows a graph of internal quantum efficiency of an aluminum
`
`alloy back junction dendritic web solar cell.
`
`Figure 6 shows a cross-sectional view of a solar cell, in accordance with
`
`another embodiment of the present invention, with partial metal coverage on
`
`the back side of the solar cell.
`
`Figure 7 shows a cross-sectional View of a solar cell, in accordance with
`
`yet another embodiment of the present invention, whose contacts to the base
`
`layer are at the back of the cell in interdigitated fashion.
`
`6
`
`
`
`WO 00/55923
`
`PCT/USOO/02609
`
`DESCRIPTION OF THE PREFERRED EMBODIMENTS
`
`The present invention will now be described in detail with reference to
`
`the presently preferred embodiments as illustrated in accompanying drawings.
`
`In the following description, numerous specific details are set forth in order to
`
`provide a thorough understanding of the present invention. It will be
`
`apparent, however, to one skilled in the art, that the present invention may be
`
`practiced without some or all of these specific details. In other instances, well
`
`known process steps and/or structures have not been described in detail in
`
`order to not unnecessarily obscure the present invention.
`
`It is important to bear in mind that a minority carrier electron diffusion
`
`length (i.e. electrons in p-type silicon) is generally different from a minority
`
`carrier hole diffusion length (i.e. holes in n-type silicon) for a given doping
`
`concentration. This difference may depend on the nature of the crystalline
`
`defect, which may act as a recombination center. In dendritic web silicon, for
`
`example, the primary defects are precipitates of silicon oxide which nucleate
`
`on dislocation cores. The interface between the silicon oxide precipitate and
`
`the surrounding silicon carries a positive charge because of the mismatch of
`
`the atomic structure of the two materials. A negatively charged minority
`
`carrier electron is attracted to such a positively charged interface. Such a
`
`defect can capture and hold an electron until one of the numerous majority
`
`
`
`WO 00/55923
`
`PCT/USOO/02609
`
`carrier holes wanders by the defect whereupon the electron can fall into the
`
`hole in a recombination event.
`
`The present invention therefore recognizes that for a solar cell substrate
`
`layer, n-type doping may be desirable to achieve a higher minority carrier
`
`diffusion length than that obtained with p—type doping. A solar cell substrate
`
`having n-type conductivity requires an n-type base layer. A p—n junction was,
`
`therefore, fabricated employing the n-type base layer and an emitter layer at
`
`the illuminated side that includes boron, which is a practical choice for a
`
`p—type dopant.
`
`Unfortunately, it was found that boron diffusions frequently leave a
`
`stained silicon surface because of the formation of boron-silicon compounds.
`
`Such a stain seriously degrades the appearance of the surface of a solar cell.
`
`Boron stains may be removed at the expense of additional and unwanted
`
`processing steps such as thermal oxidation of the stained surface followed by
`
`chemically removing the thermal oxide. Thus, according to the findings of the
`
`present invention, for silicon materials in which n-type doping gives higher
`
`minority carrier diffusion length than does p-type doping, the desirability of a
`
`front p—n junction is offset by the presence of a boron stain for the p—type
`
`emitter layer.
`
`Referring back to Figure 1, commercial solar cells 10 have an n'i‘pp+
`
`8
`
`
`
`wo 00/55923
`
`PCT/USOO/02609
`
`structure. The n-type emitter layer 16 is commonly made using phosphorus
`
`diffusion (in which staining is not a problem), the silicon substrate is doped
`
`p—type, and back silicon surface 20 is typically doped p+ to promote ohmic
`
`contact with contact metal layer 22. An ohmic contact has a low resistance.
`
`The voltage developed across an ohmic contact has a linear relationship to the
`
`current flowing through the contact. In contrast, the voltage developed across
`
`a rectifying contact has a non-linear relationship to the current flowing
`
`through the contact. An aluminum—silicon alloy may be used to provide the
`
`p+ doping and the back metal contact. More importantly, the commercial
`
`solar cell 10 has p-n junction 24 located at the front of the cell. As explained
`
`above, therefore, n+ emitter layer 16 is forced to be deeper than desired to
`
`avoid shunting the front junction. If a silicon material with superior minority
`
`carrier diffusion length with n-type doping is to be used with a front p-n
`
`junction, p—type emitter layer is boron—doped to be practical. Boron doping, as
`
`explained above, gives a stained surface, which degrades cell appearance and
`
`which can only be removed with additional and unwanted processing.
`
`The present invention, therefore, provides a p—n junction located at the
`
`back end of the solar cell. Figure 2 shows a solar cell layer stack 110,
`
`according to one embodiment of the present invention, that has the p-n
`
`junction located at the back end (near the non-illuminated surface of the base
`
`
`
`WO 00/55923
`
`PCT/US00/02609
`
`layer), so it is impossible for the front metal contacts 1 12 to shunt the p—n
`
`junction. Since aluminum may be the choice of dopant in the silicon p+ layer,
`
`it is also impossible for the aluminum to shunt the junction.
`
`Solar cell layer stack 110 includes a base layer 1 18 of n-type
`
`conductivity, which is defined by an illuminated surface (front or top surface)
`
`126 and a non-illuminated surface (back or bottom surface) 128. A portion of
`
`base layer 118 near illuminated surface 126 is passivated by a shallow n+
`
`layer 1 16, which is typically formed by phosphorus diffilsion into a silicon
`
`layer. This embodiment, therefore, realizes the advantage of the conventional
`
`n+ layer and does not suffer from boron staining. An optional anti—reflective
`
`(AR) coating 1 14 is disposed atop n+ layer 116. If the coating is present as
`
`shown in Figure 2, silver contacts 1 12 fire through AR coating 1 14 to reach
`
`the surface of n+ silicon layer 1 16.
`
`A p-n junction 124 is formed at non-illuminated surface 128 or the
`
`interface between base layer 1 18 and an aluminum doped silicon layer 120,
`
`which functions as a p+ emitter layer in the solar cell layer stack of the present
`
`invention. An aluminum-silicon eutectic metal layer 122, which results when
`
`aluminum is alloyed with silicon, is disposed beneath p+ layer 120 and serves
`
`as a self-aligned contact to p+ emitter layer 120. It is noteworthy that boron
`
`10
`
`
`
`wo 00/55923
`
`PCT/USOO/02609
`
`doping is absent from the solar cell structure of Figure 2, so that there is no
`
`boron stain to compromise the appearance of the front surface.
`
`The placement of the p—n junction at the back side of cell 110 is a
`
`unique feature of solar cell 1 10 shown in Figure 2. It should be borne in mind
`
`that no other current silicon solar cell design employs such an aluminum alloy
`
`back junction. Furthermore, the depth of n+ layer 116 is of no real concern
`
`regarding shunting because p—n junction 124 is at the back of cell 110.
`
`In accordance with one embodiment, n—type base layer 1 18 is a
`
`dendritic web silicon crystal having a resistivity that is generally between
`
`about 5 Q-cm and about 100 Q—cm, and preferably about 20 Q-cm. The
`
`thickness of the dendritic web silicon substrate crystal is generally between
`
`about 30 um and about 200 um, and preferably about 100 um. In order for
`
`the cell 1 10 to operate at a practical energy conversion efficiency level, the
`
`hole diffusion length in n-type base layer 1 18 is, in one implementation of this
`
`embodiment, slightly less than the thickness of base layer 118. In a preferred
`
`implementation, however, the hole diffusion length is substantially equal to
`
`the thickness of base layer 118 and more preferably exceeds the thickness of
`
`base layer 1 18.
`
`Locating the p-n junction near the back of the cell instead of near the
`
`front of the cell is counterintuitive to one skilled in the art. It is normally
`
`1‘]
`
`
`
`WO 00/55923
`
`PCT/USOO/02609
`
`desirable to have the p-n junction near the front of the cell because the number
`
`of photons absorbed per unit depth decreases as one proceeds from the
`
`illuminated surface toward the back surface. For example, about 52% of the
`
`incident photons are absorbed within the first 5 um of the base layer from the
`
`illuminated surface, while about 10% are absorbed within the second 5 um
`
`slice of depth, and'about 6% are absorbed within the third 5 um slice. In fact,
`
`about 75% of the incident photons are absorbed within the top 30 um of the
`
`base layer.
`
`Since the absorption of photons results in the generation of
`
`electron-hole pairs, and since the minority carrier members of the pairs diffuse
`
`to the junction in order to be collected, placing the p—n junction near the
`
`illuminated surface is reasonable. As a rule of thumb, those minority carriers
`
`created beyond one diffusion length from the junction will not be collected
`
`and so will not contribute to the solar cell photocurrent.
`
`Figures 3A-3D show important intermediate solar cell structures formed
`
`at different stages of a fabrication process, according to one embodiment of
`
`the present invention. The illustrated embodiment of the inventive processes
`
`may begin when a single crystal silicon substrate of n~type conductivity is
`
`fabricated using well-known conventional techniques, e.g., Czochralski, Float—
`
`zone, Bridgman, edge defined film-fed growth (EFG), string ribbon growth,
`
`12
`
`
`
`wo 00/55923
`
`PCT/USOO/02609
`
`cast silicon crystallized by directional solidification, and dendritic web
`
`growth. In a preferred embodiment, however, the dendritic web growth
`
`technique may be implemented to produce an n-type single crystal substrate.
`
`Referring to'Figure 3A, the n-type single crystal serves as a base layer
`
`218, below which a p-n junction of the solar cell is subsequently formed. In a
`
`next step, a strongly doped n-type layer 216 (hereinafter referred to as an “n+
`
`layer”) may be formed atop base layer 218 using diffusion processes well
`
`known to those skilled in the semiconductor and solar cell fabrication art. In
`
`accordance with one embodiment of the present invention, a layer containing
`
`phosphorous is applied to the top surface of base layer 218 and the
`
`phosphorous atoms are driven into base layer 218 from any heat source. The
`
`phosphorous layer'is preferably from a screen printed paste or from a liquid
`
`dopant, and the heat source is a rapid thermal processing (RTP) unit or a belt
`
`fumace maintained at a temperature that is between about 750 °C and about
`
`1050 °C and preferably about 950 °C. At these temperatures, the diffusion
`
`time may generally be between about 30 seconds to about 30 minutes and
`
`preferably be about 5 minutes. As a result, there is formed a phosphorus—
`
`doped n+ passivating layer having a thickness that is generally between about
`
`0.1 um and about 1 um, preferably about 0.3 mm, with a sheet resistance of
`
`generally between about 10 9/square and about
`
`13
`
`
`
`WO 00/55923
`
`PCT/USOO/02609
`
`200 Q/square and preferably about 40 Q/square.
`
`Alternatively, in another embodiment, the top surface of base layer 218
`
`is subjected to phosphorous ion implantation and a portion near the top
`
`surface of base layer is transformed into n+ layer 216.
`
`In accordance with yet another embodiment, base layer 218 is
`
`passivated with a transparent dielectric layer which may have an appreciable
`
`positive or negative charge. In one implementation of this embodiment, the
`
`base layer is passivated with a layer of thermally grown silicon dioxide having
`
`a thickness of between about 50 A and about 500 A, and preferably about 150
`
`A. In this embodiment, the passivation of base layer 218 may be carried out
`
`in a rapid thermal processing unit at temperatures that are generally between
`
`about 800 °C and about 1050 °C and preferably about 1000 °C. Such
`
`temperature treatment is carried out for times that are generally between about
`
`30 seconds and about 30 minutes and preferably about 50 seconds.
`
`Regardless of how the n+ layer is passivated, or whether it is passivated those
`
`skilled in the art will recognize that at the conclusion of forming n+ layer 216,
`
`a high—low junction (n+n) is formed at the top of base layer 218.
`
`An anti-reflective coating 214 may then be deposited on top of n+ layer
`
`216, as shown in Figure 3B. By way of example, plasma-enhanced chemical
`
`14
`
`
`
`wo 00/55923
`
`PCT/USOO/02609
`
`vapor deposition (PECVD) of silicon nitride or atmospheric pressure chemical
`
`vapor deposition (APCVD) of titanium dioxide is carried out to form anti—
`
`reflective coating 214.
`
`'
`
`Next, conventional techniques may be employed to deposit an
`
`aluminum layer 222 on a bottom surface or non-illuminated surface of base
`
`layer 218. According to one embodiment of the present invention, aluminum
`
`is deposited by screen printing a pure aluminum paste onto bottom surface of
`
`base layer 218. In one implementation of this embodiment, aluminum layer
`
`222 is deposited by screen—printing over nearly the entire back of the cell to a
`
`thickness that is generally between about 5 um and about 30 um, and
`
`preferably about 15 um. The partially fabricated solar cell is then heated in a
`
`radiantly—heated belt furnace to a temperature comfortably above the
`
`aluminum-silicon eutectic temperature of about 577 °C, e.g., that may
`
`generally be between about 700 °C and about 1000 °C and preferably about
`
`800 °C, for a long enough duration, e.g., generally between about 0.1 minute
`
`and about 10 minutes and preferably about 2 minutes, to facilitate alloying of
`
`at least some aluminum from layer 222 with base layer 218. During the
`
`alloying process, the temperature treatment inside the belt furnace is high
`
`enough so that aluminum may effectively dissolve silicon. At such high
`
`temperatures, a portion of the base layer that measures approximately one—
`
`15
`
`
`
`WO 00/55923
`
`PCT/US00/02609
`
`third the thickness of the aluminum layer is effectively dissolved to create p+
`
`layer 220 shown in Figure 3C. By way of example, at about 800 °C, a 15 um
`
`thick aluminum layer 222 dissolves a 5 mm portion of a silicon base layer.
`
`Consequently, p+ layer 220 is silicon doped with aluminum and contact layer
`
`222 is an alloy that is about 88% aluminum by weight and about 12% silicon
`
`by weight the eutectic composition.
`
`The p+ emitter layer is created as described hereinafter. As the silicon
`
`cools, it continues to solidify or grow onto the underlying silicon, also
`
`incorporating a modest amount of the aluminum dopant, on the order of
`
`between about 1018 and about 1019 aluminum atoms per cubic centimeter. The
`
`concentration of aluminum atoms is significantly less than the concentration
`
`of silicon atoms, which is about 10,000 times larger at about 5x1022 atoms per
`
`cubic centimeter. As shown in Figure 3C, after cooling the layers, a portion of
`
`base layer 218 near the non—illuminated surface is transformed to a strongly
`
`doped p—type layer. 220 (hereinafter referred to as a “p+ layer”), by liquid
`
`phase epitaxy. Some of the silicon that was dissolved becomes part of the
`
`aluminum—silicon eutectic layer 222. The silicon that was not dissolved by the
`
`aluminum acts as a template for restructuring the silicon crystal as it is
`
`epitaxially regrown.
`
`The aluminum-silicon eutectic metal layer 222 is a good conductor (has
`
`16
`
`
`
`WO 00/55923
`
`PCT/USOO/02609
`
`a low electrical resistance), and serves as a self-aligned metal contact to the
`
`solar cell. The thickness of aluminum-silicon eutectic metal layer 222 is
`
`generally between about 1 um and about 30 um and preferably about 15 um.
`
`Figure 3D shows the structure resulting after depositing metal contacts
`
`and firing through the optional anti—reflective coating. By way of example, a
`
`silver layer is screen-printed onto the n+ layer 216, covering about 7% of the
`
`front surface in a grid pattern. Silver may be deposited by screen—printing to a
`
`thickness that is generally between about 5 um and about 20 um and
`
`preferably about 10 um. The resulting partially fabricated solar cell structure
`
`is then run through a belt furnace maintained at a temperature that is generally
`
`between about 700 °C and about 900 °C and preferably about 760 °C. The
`
`time for running the cell through the furnace is short in order to avoid
`
`allowing impurities in the silver paste from diffilsing into the silicon. In one
`
`embodiment of the present invention, the time for running the cell through the
`
`belt furnace is between about 0.1 minutes and about 10 minutes. In a
`
`preferred embodiment, however, the time is about 40 seconds. The thickness
`
`of silver ohmic contacts 212 to n+ layer 216 is generally between about 1 um
`
`and about 20 um and preferably about 10 um. If an optional anti-reflective
`
`coating is deposited, then the silver layer is fired through the coating. Both
`
`operations may (with or without anti-reflective coating) be performed in a
`
`17
`
`
`
`wo 00/55923
`
`PCT/USOO/02609
`
`radiantly-heated belt fumace. The fabrication steps of the present invention
`
`realize high-throughput and low-cost manufacturing.
`
`Figure 4 depicts an I-V curve, which shows a light energy to electrical
`
`energy conversion-efficiency of about 12.5% for an aluminum alloy back
`
`junction dendritic web silicon solar cell with full back metal coverage of the
`
`present invention. The solar cell employed to obtain the data shown in Figure
`
`4 has a nominal thickness of about 100 um and an area of about 25 cm2.
`
`Other parameters include a short—circuit current density of about 28.2
`
`mA/cmz, open-circuit voltage of about 0.595 V, and fill factor of about 0.747.
`
`The knee of the curve shows a maximum power point, where Vmp is about
`
`0.480V and Imp is about 0.653A.
`
`Figure 5 depicts measurements of spectral reflectivity (solid triangles)
`
`510, external quantum efficiency (open squares) 512, and internal quantum
`
`efficiency (solid squares) 514 for the solar cell of Figure 4. Measured
`
`reflectivity indicates that about 47% of the long wavelength (> 950 nm) light
`
`is reflected from the aluminum~silicon eutectic metal layer at the back surface.
`
`This reflected light then gets a second pass through the silicon and adds to the
`
`overall efficiency. Calculation of the internal quantum efficiency using the
`
`one—dimensional finite element model PClD indicates a hole diffusion length
`
`of about 200 pm in the base of this cell. This is double the cell thickness, as
`
`18
`
`
`
`WO 00/55923
`
`PCT/US00/02609
`
`required for good performance. The internal quantum efficiency curve has a
`
`positive slope over the range of about 500 nm to about 850 nm, indicating that
`
`the p-n junction is at the back of the cell, which is also noteworthy. In a
`
`conventional solar cell, the internal quantum efficiency curve would show a
`
`negative slope, indicating that the p-n junction is at the front of the cell.
`
`Figure 6 shows a solar cell layer stack 300, in accordance with another
`
`embodiment of the present invention, that is substantially similar to the solar
`
`cell 1 10 of Figure 2, except that solar cell 300 has only part of the back
`
`surface converted to a p—type layer and covered with metal. Thus, solar cell
`
`300 is referred to as having “partial” metal coverage on the back side as
`
`opposed to have “full” metal coverage, as shown in Figure 2 for solar cell 110,
`
`where the entire back surface is covered with metal. The partial metal
`
`coverage design of Figure 6 eliminates bowing of the thin cells, which results
`
`from a differential thermal contraction between the silicon and the
`
`aluminum-silicon eutectic metal layer upon cooling from the eutectic
`
`temperature of about 57 7 °C. It is important to bear in mind that such bowing
`
`sometimes occurs when full back metal coverage is used. The segmented
`
`metal also reducesthe cost of aluminum. The exposed n—type base layer
`
`surfaces 330 between metal islands at the back may be passivated in order to
`
`obtain respectable energy conversion efficiency. By way of example, the
`
`19
`
`
`
`WO 00/55923
`
`PCT/USOO/02609
`
`passivation step may be performed after the aluminum alloying step by
`
`growing a thermal oxide of about 115 A thickness in a rapid thermal
`
`processing unit at about 1000 °C for about 50 seconds. An anti—reflective
`
`coating may not be applied in this preliminary effort. Efficiencies up to about
`
`6.8% were obtained for 25 cm2 dendritic web silicon cells with screen-printed
`
`metals but without anit—reflective coating. The expected efficiency with an
`
`anti-reflective coating is about 9.9%.
`
`Figure 7 depicts a solar cell layer stack 400, according to yet another
`
`embodiment of the present invention, that is substantially similar to the solar
`
`cell 300 of Figure 6, except that solar cell 400 has n-type contacts 412 to the
`
`n-type base layer moved from the front of the cell to the back of the cell in an
`
`interdigitated fashion.
`
`This structure shown in Figure 7 has the added advantage of reducing to
`
`zero the shadowing of the front surface by contacts. Interconnecting cells in a
`
`module is also expected to be simpler with both contacts on the back side of
`
`the cell in that surface
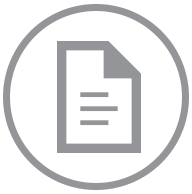
Accessing this document will incur an additional charge of $.
After purchase, you can access this document again without charge.
Accept $ ChargeStill Working On It
This document is taking longer than usual to download. This can happen if we need to contact the court directly to obtain the document and their servers are running slowly.
Give it another minute or two to complete, and then try the refresh button.
A few More Minutes ... Still Working
It can take up to 5 minutes for us to download a document if the court servers are running slowly.
Thank you for your continued patience.
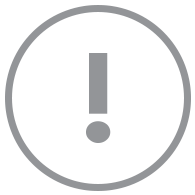
This document could not be displayed.
We could not find this document within its docket. Please go back to the docket page and check the link. If that does not work, go back to the docket and refresh it to pull the newest information.
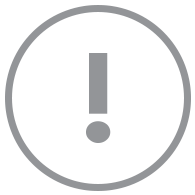
Your account does not support viewing this document.
You need a Paid Account to view this document. Click here to change your account type.
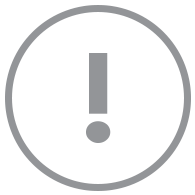
Your account does not support viewing this document.
Set your membership
status to view this document.
With a Docket Alarm membership, you'll
get a whole lot more, including:
- Up-to-date information for this case.
- Email alerts whenever there is an update.
- Full text search for other cases.
- Get email alerts whenever a new case matches your search.
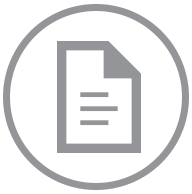
One Moment Please
The filing “” is large (MB) and is being downloaded.
Please refresh this page in a few minutes to see if the filing has been downloaded. The filing will also be emailed to you when the download completes.
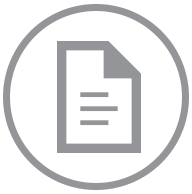
Your document is on its way!
If you do not receive the document in five minutes, contact support at support@docketalarm.com.
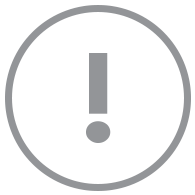
Sealed Document
We are unable to display this document, it may be under a court ordered seal.
If you have proper credentials to access the file, you may proceed directly to the court's system using your government issued username and password.
Access Government Site