`
`US 20060160250A1
`
`as) United States
`a2) Patent Application Publication (1) Pub. No.: US 2006/0160250 Al
`Bonassaret al.
`(43) Pub. Date:
`Jul. 20, 2006
`
`(54) MODULAR FABRICATION SYSTEMS AND
`METHODS
`
`Related U.S. Application Data
`
`(75)
`
`Inventors: Lawrence Bonassar, Ithaca, NY (US):
`Hod Lipson, Ithaca, NY (US); Daniel
`L. Cohen, Ithaca, NY (US); Evan
`Malone, Ithaca, NY (US)
`
`Coiiaapoaians Wadia!
`Michael L. Goldman
`Nixon Peabody LLP
`1300 Clinton Square
`P.O. Box 31051
`Rochester, NY 14603 (US)
`:
`(73) Assignee: Cornell Research Foundation,Inc., Ith-
`aca, NY
`
`(21) Appl. No.:
`
`11/201,057
`
`(22)
`
`Filed:
`
`Aug. 10, 2005
`
`(60)
`
`Provisional application No. 60/600,529,filed on Aug.
`11, 2004. Provisional application No. 60/704,299,
`filed on Aug. 1, 2005.
`Publication Claisification
`
`(51)
`
`Int. Cl.
`HOIL 21/00
`(2006.01)
`(92) WiSeCk semercientaanvanniiens 438/1; 438/5
`(57)
`ABSTRACT
`.
`.
`.
`Thepresent inventionrelates to an article fabrication system
`having a plurality of material deposition tools containing
`one or more materials useful in fabricating the article, and a
`material deposition device havinga tool interface for receiv-
`ing one of the material deposition tools. A system controller
`is operably connected to the material deposition device to
`control operation of the material deposition device. Also
`disclosed is a method of fabricating an article using the
`systemofthe invention and a method of fabricating a living
`three-dimensional structure.
`
`~~ 104 106
`
`
`124A
`
`
`
`
`
`1
`
`Shenzhen Tuozhu 1010
`
`1
`
`Shenzhen Tuozhu 1010
`
`
`
`Patent Application Publication Jul. 20,2006 Sheet 1 of 25
`
`US 2006/0160250 Al
`
`
`
`2
`
`
`
`Patent Application Publication Jul. 20,2006 Sheet 2 of 25
`
`US 2006/0160250 Al
`
`3
`
`
`
`Patent Application Publication Jul. 20,2006 Sheet 3 of 25
`
`US 2006/0160250 Al
`
`
`
`4
`
`
`
`Patent Application Publication Jul. 20,2006 Sheet 4 of 25
`
`US 2006/0160250 Al
`
`
`
`FIG. 4
`
`5
`
`
`
`Patent Application Publication Jul. 20,2006 Sheet 5 of 25
`
`US 2006/0160250 Al
`
`FIG. 2
`
`6
`
`
`
`Patent Application Publication Jul. 20,2006 Sheet 6 of 25
`
`US 2006/0160250 Al
`
`
`
`7
`
`
`
`Patent Application Publication Jul. 20,2006 Sheet 7 of 25
`
`US 2006/0160250 Al
`
`8
`
`
`
`Patent Application Publication Jul. 20,2006 Sheet 8 of 25
`
`US 2006/0160250 Al
`
`9
`
`
`
`Patent Application Publication Jul. 20,2006 Sheet 9 of 25
`
`US 2006/0160250 Al
`
`FIG.Q
`
`10
`
`10
`
`
`
`Patent Application Publication Jul. 20,2006 Sheet 10 of 25
`
`US 2006/0160250 Al
`
`11
`
`
`
`Patent Application Publication Jul. 20,2006 Sheet 11 of 25
`
`US 2006/0160250 Al
`
`12
`
`
`
`Patent Application Publication Jul. 20,2006 Sheet 12 of 25
`
`US 2006/0160250 Al
`
`
`
`FIG. 12
`
`13
`
`13
`
`
`
`Patent Application Publication Jul. 20,2006 Sheet 13 of 25
`
`US 2006/0160250 Al
`
`
`
`14
`
`
`
`Patent Application Publication Jul. 20,2006 Sheet 14 of 25
`
`US 2006/0160250 Al
`
`eI
`
`Co
`
`a
`
`Sj
`
`308
`
`308 —
`co
`
`C4
`
`co
`
`cI
`
`Co
`
`C4)
`Sj
`
`308
`
`
`
`co ea|
`
` 302
`
`x08 ( 310
`
`312
`
`Co
`
`co
`
`312
`
`co
`
`co
`
`310
`
`15
`
`15
`
`
`
`Patent Application Publication Jul. 20,2006 Sheet 15 of 25
`
`US 2006/0160250 Al
`
`
`
`FIG. 19
`
`16
`
`
`
`Patent Application Publication Jul. 20,2006 Sheet 16 of 25
`
`US 2006/0160250 Al
`
`
`
`FIG. 16
`
`17
`
`17
`
`
`
`Patent Application Publication Jul. 20,2006 Sheet 17 of 25
`
`US 2006/0160250 Al
`
`+©wy)
`
`518
`
`°i)x)
`
`18
`
`18
`
`
`
`
`Patent Application Publication Jul. 20,2006 Sheet 18 of 25
`
`US 2006/0160250 Al
`
`FIG. 18
`
`19
`
`
`
`Patent Application Publication Jul. 20,2006 Sheet 19 of 25
`
`US 2006/0160250 Al
`
`FIG. 19
`
`20
`
`20
`
`
`
`Patent Application Publication
`
`Jul. 20,2006 Sheet 20 of 25
`
`US 2006/0160250 Al
`
`
`
`FIG. 21
`
`21
`
`21
`
`
`
`Patent Application Publication
`
`Jul. 20,2006 Sheet 21 of 25
`
`US 2006/0160250 Al
`
`
`
`FIG. 23
`
`22
`
`22
`
`
`
`Patent Application Publication
`
`Jul. 20,2006 Sheet 22 of 25
`
`US 2006/0160250 Al
`
`23
`
`
`
`Patent Application Publication
`
`Jul. 20,2006 Sheet 23 of 25
`
`US 2006/0160250 Al
`
`FIG. 25
`
`24
`
`24
`
`
`
`Patent Application Publication
`
`Jul. 20,2006 Sheet 24 of 25
`
`US 2006/0160250 Al
`
`
`
`FIG. 26
`
`25
`
`25
`
`
`
`Patent Application Publication
`
`Jul. 20,2006 Sheet 25 of 25
`
`US 2006/0160250
`
`Al
`
`Peay”
`
`‘j
`
`i
`
`FIG.
`
`2/7
`
`26
`
`26
`
`
`
`US 2006/0160250 Al
`
`Jul. 20, 2006
`
`MODULAR FABRICATION SYSTEMS AND
`METHODS
`
`{0001] This application claims thepriority benefit of the
`provisional patent application entitled, “Modular Fabrica-
`tion Systems and Methods,”filed Aug. 1, 2005, with express
`mail certificate number EV652971121US and U.S. Provi-
`sional Patent Application Ser. No. 60/600,529,filed Aug.11,
`2004, which are hereby incorporated by reference in their
`entirety.
`
`FIELD OF THE INVENTION
`
`[0002] The present invention relates generally to anarticle
`fabrication system, a method of fabricating an article, and a
`method of fabricating a living three-dimensional structure.
`
`BACKGROUND OF THE INVENTION
`
`{0003] Solid freeform fabrication (“SFF”) is the name
`given to a class of manufacturing methods which allow the
`fabrication of three-dimensional structures directly from
`computer-aided design (“CAD”) data. SFF processes are
`generally additive, in that material is selectively deposited to
`construct the product rather than removed from a block or
`billet. Most SFF processes are also layered, meaningthat a
`geometrical description ofthe product to be produced is cut
`by a set ofparallel surfaces (planar or curved), and the
`intersections ofthe product and each surlace referred to as
`slices or layers—are fabricated sequentially. Together, these
`two properties mean that SFP processes are subject to very
`different constraints than traditional material removal-based
`
`manufacturing. Nearly arbitrary product geometries are
`achievable, no tooling is required, mating parts and fully
`assembled mechanisms can be fabricated in a single step,
`and multiple materials can be combined, allowing function-
`ally graded material properties. New features, parts, and
`even assembled components can be “grown” directly on
`already completed objects, suggesting the possibility of
`using SFFfor the repair and physical adaptation of existing
`products. On the other hand, a deposition process must be
`developed and tuned for each material, geometry is limited
`by the ability of the deposited material to support itself and
`by the (often poor) resolution and accuracy ofthe process,
`and multiple material and process interactions must be
`understood.
`
`[0004] SFF has traditionally focused on printing passive
`mechanical parts or products in a single material. and the
`emphasis of research has been on developing new deposition
`processes (U.S. Pat. No. 5,121,329 to Crump; U.S. Pat. No.
`5,134,569 to Masters; U.S. Pat. No, 5,204,055 to Sachs et.
`al.; and U.S. Pat. No. 5,126,529 to Weiss et. al.), on
`improving the quality, resolution, and surface finish of
`fabricated products, and on broadening the range ofsingle
`materials which can be employed by a given SFF process,
`including biocompatible polymers and other biomaterials
`(Pfister et al., “Biofunctional Rapid Prototyping for Tissue-
`engineering Applications: 3D Bioplotting Versus 3D Print-
`ing,’Journal ofpolymer Science Part A: Polymer Chemistry
`42:624-638 (2004); Landers et al., “Desktop Manufacturing
`of Complex Objects, Prototypes and Biomedical Scaffolds
`by Means of Computer-assisted Design Combined with
`Computer-guided 3D Plotting of Polymers and Reactive
`Oligomers,”Macromolecular Materials and Engineering
`282:17-21 (2000)), and living cells (Roth et al., “Inkjet
`
`Printing for High-throughput Cell Patterning, Biomaterials
`25:3707-3715 (2004)). These improvements have allowed
`freeform fabrication to become a viable means of manutfac-
`turing finished functional parts, rather than only prototypes.
`
`[0005] More recently, the greater utility of freeform fab-
`ricated products having multiple materials has been recog-
`nized, prompting reexamination and novel research into
`processes which can fabricate using multiple materials (U.S.
`Pat, No. 5,260,009 to Penn), and which can thereby produce
`complex articles with a variety of functionality, including
`functionally graded materials (Ouyang et al., “Rapid Proto-
`typing and Characterization of a WC—(NiSiB Alloy) Cer-
`amet/Tool Steel Functionally Graded Material (FGM) Syn-
`thesized by Laser Cladding,” Columbus, Ohio, USA:
`TMS—Miner. Metals & Mater. Soc. (2002); Smurov etal.
`“Laser-assisted Direct Manufacturing of Functionally
`Graded 3D Objects by Coaxial Powder Injection,”*Praceed-
`ings of the SPIE—The International Society for Optical
`Engineering 5399:27 (2004)), electronics, MEMS(Fuller et
`al., “Ink-jet Printed Nanoparticle Microelectromechanical
`Systems,Journal of Microelectromechanical Systems
`11:54-60 (2002). living tissue constructs (Mironov etal.,
`“Organ Printing: Computer-aided Jet-based 3D Tissue Engi-
`neering.” Trends in Biotechnology 21:157-161 (2003)), and
`compositions of living and nonliving materials (Sun et al.,
`“Multinozzle Biopolymer Deposition for Tissue Engineer-
`ing Application.” 6'* International Conference on Tissue
`Engineering, Orlando, Fla. (Oct. 10-13, 2003); International
`Patent Application No. PCT/US2004/015316 to Sunetal.;
`and U.S. Pat. No, 6,905,738 to Ringeisenet al.), All of these
`systems still depend upon a small fixed set of deposition
`process technologies, and are therefore limited to the mate-
`rials which can be adaptedto those processes, by the effects
`ofthose particular processes on the materials, and by the
`fabrication rates and resolutions of those processes.
`In
`particular,
`the system of U.S. Pat. No. 6,905,738 to
`Ringeisen et al., requires that
`for every material
`to be
`deposited, a two material system be developed comprising
`the material
`to be transferred, and a compatible matrix
`material which is vaporized by the laser in order to propel
`the transfer material to the substrate. In addition,this system
`has only demonstrated fabrication of thin films of materi-
`als—its ability to deposit many layers of materials is not
`well established. The system and method of Sun et al.,
`“Multinozzle Biopolymer Deposition for Tissue Engineer-
`ing Application,” 6" International Conference on Tissue
`Engineering, Orlando, Fla. (Oct. 10-13, 2003) and Interna-
`tional Patent Application No. PCT/US2004/015316 to Sun
`et al.,
`is limited to a fixed set of four deposition processes
`and requires that the alginate materials be deposited into a
`bath ofliquid crosslinking agent—alimitationit shares with
`the work ofPfister et al., “Biofunctional Rapid Prototyping
`for Tissue-engineering Applications: 3D Bioplotting Versus
`3DPrinting, Journal ofPolymer Science Part A: Polymer
`Chemistry 42:624-638 (2004) and Landerset al., “Desktop
`Manufacturing of Complex Objects, Prototypes and Bio-
`medical Scaffolds by Means of Computer-assisted Design
`Combined with Computer-guided 3D Plotting of Polymers
`and Reactive Oligomers,”Macromolecular Materials and
`Engineering 282:17-21 (2000). In addition, none of these
`systems explicitly measures the properties of, and monitors
`and controls the conditions experienced by the fabrication
`materials,
`the fabrication substrate, and the article under
`construction before, during. and/or afier fabrication as an
`
`27
`
`27
`
`
`
`US 2006/0160250 Al
`
`Jul. 20, 2006
`
`intrinsic part of the fabrication process and manufacturing
`plan. The fabrication process is thus limited to the spatial
`control of material placement onrelatively simple, passive
`substrates. Temporal control of the evolution of material
`properties is therefore not possible, and complex substrates
`whose state must be controlled and monitored continuously
`are not readily accommodated. Fabricating into or onto
`substrates, such as living organisms or devices which must
`remain in operation continuously, is problematic.
`
`[0006] A major challenge in orthopaedic tissue engineer-
`ing is the generation of seeded implants with structures that
`mimic native tissue, both in terms of anatomic geometries
`and intratissue cell distributions, Previous studies have
`demonstrated that
`techniques such as injection molding
`(Chang etal., “Injection Molding of Chondrocyte/Alginate
`Constructs in the Shape of Facial Implants,"J. Biomed. Mat.
`Res, 55:503-511 (2001)) and casting (Hung et al., “Ana-
`tomically Shaped Osteochondral Constructs for Articular
`Cartilage Repair’J. Biomech. 36:1853-1864 (2003)) of
`hydrogels can generate cartilage tissue in complex geom-
`etries. Other studies have investigated methods to reproduce
`regionalvariationsinarticular cartilage constructs by depos-
`iting multiple layers of chondrocytes (Klein et al., “Tissue
`Engineering ofStratified Articular Cartilage from Chondro-
`cyte Subpopulations,”Osteoarthritis Cartilage 11:595-602
`(2003)) or chondrocyte-seeded gels (Kim et al., “Experi-
`mental Model for Cartilage Tissue Engineering to Regener-
`ate the Zonal Organization of Articular Cartilage,”Osteoar-
`thritis Cartilage 11:653-664 (2003)). However,
`there
`remains no viable strategy for rapidly producing implants
`with correct anatomic geometries and cell distributions.
`Recently, advances in SFF techniques have enabled the
`deposition of multilayered structures composed of multiple
`chemically active materials (Malone etal., “Freeform Fab-
`rication of 3D Zine-Air Batteries and Functional Electro-
`Mechanical Assemblies,”Rapid Prototyping Journal 10:58-
`69 (2004)). Applicants believe that this technology has the
`potential to be adapted to the fabrication ofliving tissue
`under conditions that preserve cell viability.
`
`[0007] The present invention is directed at overcoming
`disadvantages ofprior art approaches and satisfying the need
`to establish a robust and reliable SFP system and method.
`
`SUMMARY OF THE INVENTION
`
`[0008] One aspect of the present invention relates to an
`article fabrication system. The system has a plurality of
`material deposition tools containing one or more materials
`useful in fabricating the article. The system has a material
`deposition device having a tool interface for receiving the
`material deposition tools, the tool interface of the material
`deposition device being movable relative to a substrate to
`dispense material from the material deposition tool to the
`substrate. A system controller is operably connected to the
`material deposition device to control operation ofthe mate-
`rial deposition device.
`
`[0009] Another aspect ofthe present inventionrelates to a
`method of fabricating an article. This method involves
`providing the above-described article fabrication system.
`Material
`is dispensed from the material deposition tools,
`when mounted on the tool interface of the material deposi-
`tion device, in amounts andat positions on the substrate in
`response to instructions fromthe system controller, whereby
`an article is fabricated on the substrate.
`
`[0010] A further aspect of the present invention relates to
`a methodoffabricating a living three-dimensional structure.
`This method involves providing a data set representing a
`living three-dimensional structure to be fabricated. One or
`more compositions including a composition having a hydro-
`gel with seeded cells is provided, The one or more compo-
`sitions are dispensed in a pattern in accordance withthe data
`set suitable to fabricate the living three-dimensional struc-
`ture.
`
`[0011] Yet another aspect ofthe present invention relates
`to an article fabrication system. The system has a material
`deposition too] containing one or more materials useful in
`fabricating the article. The system has a material deposition
`device having a tool
`interface for receiving the material
`deposition tool, the tool interface of the material deposition
`device being movable relative to a substrate to dispense
`material from the material deposition tool to the substrate.
`The system has an enclosure defining a receptacle for
`enclosing the substrate in a confined environment segregated
`from other components ofthe system and capable of receiv-
`ing material dispensed from the material deposition tool. A
`system controller is operably connected to the material
`deposition device to control operation of the material depo-
`sition device.
`
`(0012] Yeta further aspect of the present invention relates
`to anarticle fabrication system. The system has a material
`deposition tool containing one or more materials useful in
`fabricating the article. The system has a material deposition
`device having a tool
`interface for receiving said material
`deposition tool, the tool interface of the material deposition
`device being movable relative to a substrate to dispense
`material from the material deposition tool to the substrate.
`The system has one or more sensors positioned to detect
`non-geometric properties of material dispensed to the sub-
`strate. A system controller is operably connected to the
`sensors to control detection of material properties and to the
`material deposition device to control the material deposition
`device.
`
`(0013] The present invention relates to an article fabrica-
`tion system having multiple interchangeable material depo-
`sition tools and one or more modules capable of receiving
`material dispensed from material deposition tools. The
`deposition tools may contain interchangeable cartridges
`containing, materials useful
`in fabricating the article. The
`tools and/or the cartridges may also contain apparatus for
`monitoring and conditioning the material for deposition. The
`substrate modules are useful in fabricating the article, and
`mayalso contain apparatus for monitoring and conditioning
`the deposited materials,
`
`[0014] The system may also have a device to automati-
`cally switch tools andtheir cartridges and substrate modules,
`or these may be fixed in the system. A system controlleris
`operably connected to the material tools, cartridges, sub-
`strate modules, transfer devices, and positioning systems.
`The system has provision for monitoring and controlling the
`environmental conditions under which fabrication takes
`place, for monitoring and correcting fabrication errors dur-
`ing the course of fabrication, and for monitoring and con-
`trolling the properties of the article being fabricated during
`the course of fabrication. The combined capabilities ofthe
`system,
`the deposition tools, and the substrate modules
`allow monitoring and control of the conditions experienced
`
`28
`
`28
`
`
`
`US 2006/0160250 Al
`
`Jul. 20, 2006
`
`by all of the materials and by the article being fabricated,
`before. during, and/or after the fabrication process. This
`extends the freeform fabrication process to include con-
`trolled evolution of material properties as well as controlled
`deposition of multiple materials, allowing not just geomet-
`ric, but spatio-temporal control over the properties ofthe
`composite article being fabricated. These extended capabili-
`ties are especially important when fabricating integrated
`systems comprising multiple active materials, such as elec-
`trochemical devices and living tissue constructs. This is also
`the case when depositing constructsinto sensitive substrates,
`such as living organisms or sensing devices, the health and
`function of which must be maintained throughout the fab-
`rication process.
`
`[0015] The present invention’s modular system architec-
`ture and multi-level control scheme give it distinct advan-
`tages over other systems. The modular systemarchitecture
`enables the system ofthe present invention to adapt to high
`throughput applications,
`in which material changes and
`substrate changes must be eflicient and, in some cases, in
`which automation would be beneficial. The modular design
`also enables the system to adapt
`to a broad range of
`applications. For example, the same general system design
`could be used for in vitro as well as in vivo fabrication.
`
`[0016] The multi-level sensing, actuation, control, and
`intelligence enables the system to log and/or control the
`spatio-temporal state of numerous properties ofboth mate-
`rials and articles being fabricated prior, during, and after
`fabrication (for example, from the start of the fabrication
`process through incubation). These material and article
`properties include but are notlimited to temperature, humid-
`ity, light, vibration, pressure, mechanical loading. and shape.
`Spatio-temporal control of numerous properties is important
`when fabricating integrated systems with active materials
`such as electromechanical devices, self-assembling struc-
`tures, and living tissue constructs.
`
`BRIEF DESCRIPTION OF THE DRAWINGS
`
`FIG.1 isa perspective view ofa fabrication system
`[0017]
`in accordance with the present invention.
`
`[0018] FIG. 2 is a perspective view of a material deposi-
`tion device and the tool rack of the system in accordance
`with the present invention in which the tool rack is con-
`nected to the material deposition device.
`
`(0019] FIG. 3 is a front view of a material deposition
`device of a system in accordance with the present invention
`without a material deposition tool attached at
`the tool
`interface.
`
`[0020] FIG. 4 is a front view ofa material deposition tool
`in accordance with the present invention, which is a car-
`tridge holding tool capable of receiving a modular material
`cartridge.
`
`[0021] FIG. 5 is a front view of a material deposition
`device in accordance with the present invention fitted at a
`tool
`interface with a cartridge holding tool capable of
`receiving a modular material cartridge.
`
`FIG.6 is a front view ofa cartridge holding tool in
`[0022]
`which a modular material cartridge carrying a syringe is
`positioned in the cartridge chamber.
`
`[0023] FIG. 7 is a front view of a material deposition
`device of a system in accordance with the present invention
`fitted at the tool interface with a cartridge holding tool in
`which a modular material cartridge carrying a syringe is
`positioned in the cartridge chamber.
`[0024] FIGS, 8A-D are perspective views of a cartridge
`holding tool and material modular syringe cartridge that fits
`into the cartridge holding tool. FIGS. 8A-B illustrate per-
`spective, exploded views ofthe parts of a syringe which fit
`into the syringe cartridge. FIG, 8C illustrates a perspective,
`exploded view of how the syringe fits into the syringe
`cartridge. FIG. 8D illustrates a perspective view of the
`cartridge holding tool fitted with the syringe cartridge.
`
`FIG.9 is a perspective view of a transfer device in
`[0025]
`accordance with the present invention.
`
`[0026] FIG. 10 is a perspective view ofa fabrication
`system in accordance with the present invention in which the
`transfer device is in contact with a material deposition tool
`located on a tool rack. Also shown is the electronic wiring
`of a fabrication system that connects to an external com-
`puter.
`
`[0027] FIG. 11 is a perspective view of a fabrication
`system in accordance with the present invention in which a
`transfer device is replacing a material cartridge in a cartridge
`socket of a material deposition tool connected to a tool
`interlace.
`
`(0028] FIG. 12 is a back view of a material deposition
`device in accordance with the present invention showing a
`sensor attached to the back ofthe tool interface. The sensor
`detects properties of the substrate, of the article being
`fabricated, and of the materials being deposited,
`[0029] FIG. 13 is a perspective view ofa tip calibration
`sensor positioned on a substrate of a material deposition
`device. The tip calibration sensor enables the system con-
`troller to be awareofthe precise location ofa reference point
`onthe tool or tools attached to the tool interface relative to
`the tool interface.
`
`[0030] FIG. 14A isa front view ofa module in accordance
`with the present invention which is attachable to the sub-
`strate. A plan view (FIG, 14B) and a side view (FIG. 14C)
`of the substrate module are also shown.
`
`[0031] FIG. 15 is a perspective view of a module in
`accordance with the presentinvention depictinga receptacle
`into which material from a material deposition device is
`dispensed and examples offixture points, interfaces, and
`sensing and actuation ports which may be included in the
`module.
`
`[0032] FIG. 16 is a perspective view of a module in
`accordance with the present invention in which a receptacle
`is enclosed,
`
`[0033] FIG. 17 is an exploded perspective view of a
`module in accordance with the present invention.
`[0034] FIG. 18 is a perspective view of a fabrication
`system in accordance with the present invention in which a
`module is attached to a substrate.
`
`[0035] FIG. 19 is a perspective view of a fabrication
`system in accordance with the present inventionin whicha
`module having an enclosed receptacle is attached to a
`substrate.
`
`29
`
`29
`
`
`
`US 2006/0160250 Al
`
`Jul. 20, 2006
`
`FIGS. 20A-B are photographs showingthe results
`[0036]
`of viability tests in which both live (FIG. 20A) and dead
`(FIG. 20B) cells were detected in printed gels.
`
`[0037] FIG. 21Ais a stereolithography (“STL”) image of
`a bovine meniscus generated by a CT scan. FIG. 21B is a
`photograph ofthe printed meniscus-shaped gel using the
`fabrication system and method of the present invention.
`
`[0038] FIG. 22 is a photograph ofa 1-millimeter thick,
`autoclavable, clear plastic bag used to enclose the substrate
`in a sterile environment.
`
`[0039] FIG. 23 is a photograph of a plastic bag containing
`a printed sample which has been transferred to a sterilized
`hood for removal of a fabricated article.
`
`FIGS. 24.4-L are photographsofprinted gels using
`[0040]
`the fabrication system method of the present
`invention
`compared to images generated by CT scans.
`
`[0041] FIG. 25A-B are photographs of microscope views
`during viability tests using fluorescence microscopyfiltered
`to illuminate living cells (FIG. 25A) andfiltered to illumi-
`nate dead cells (FIG. 25B).
`
`[0042] FIG. 26A is a CAD model image generated from
`a CT sean of a meniscus-shaped pieceof cartilage used in
`fabricating the article shown in FIG, 26B. FIG, 26B is a
`photographofa fabricated article produced by a fabrication
`system in accordance with the present invention.
`
`[0043] FIG. 27A is a CAD model image generated from
`a CT scan of a meniscus-shaped piece of cartilage used in
`fabricating the article shown in FIG, 27B. FIG. 27B is a
`photograph of a fabricated article produced by a fabrication
`system in accordance with the present invention.
`
`DETAILED DESCRIPTION OF THE
`INVENTION
`
`[0044] One aspect of the present invention relates to an
`article fabrication system. The system has a plurality of
`material deposition tools containing one or more materials
`useful in fabricating the article. The system has a material
`deposition device having a tool interface for receiving the
`material deposition tools, the tool interface ofthe material
`deposition device being movable relative to a substrate to
`dispense material from the material deposition tool to the
`substrate. A system controller is operably connected to the
`material deposition device to control operation of the mate-
`rial deposition device.
`
`[0045] Another aspect of the present invention relates to
`an article fabrication system. The system has a material
`deposition tool containing one or more materials useful in
`fabricating the article. The system has a material deposition
`device having a tool interface for receiving the material
`depositiontool, the tool interface of the material deposition
`device being movable relative to a substrate to dispense
`material from the material deposition tool to the substrate.
`The system has an enclosure defining a receptacle for
`enclosing the substrate in a confined environment segregated
`from other components ofthe system and capableof receiv-
`ing material dispensed from the material deposition tool. A
`system controller is operably connected to the material
`deposition device to control operation of the material depo-
`sition device.
`
`[0046] A further aspect of the present invention relates to
`an article fabrication system. The system has a material
`deposition too] containing one or more materials useful in
`fabricating the article. The system has a material deposition
`device having a tool interface for receiving said material
`deposition tool, the tool interface of the material deposition
`device being movable relative to a substrate to dispense
`material from the material deposition tool to the substrate.
`The system has one or more sensors positioned to detect
`non-geometric properties of material dispensed to the sub-
`strate. A system controller is operably connected to the
`sensors to control detection of material properties and to the
`material deposition device to control the material deposition
`device.
`
`FIG.1 is a perspective view ofone embodimentof
`(0047]
`the systemofthe present invention. In the particular embodi-
`ment shown in FIG,1, tool rack 4 is connected to material
`deposition device 2. Located near material deposition device
`2 and tool rack 4 is transfer device 100, which is capable of
`making contact with material deposition tool 18 and moving
`material deposition tools 18 between material deposition
`device 2 and tool rack 4.
`
`(0048] Material deposition device 2 and tool rack 4 are
`again illustrated in perspective in FIG, 2, As shown,
`machine base 6 is the general supporting structure of mate-
`rial deposition device 2, Machine base 6 preferably has
`horizontal surface 90 which mayrest on the ground or on a
`flat surface, such as the top of a bench or a table, and two
`vertical surfaces 92-B connected to horizontal surface 90.
`
`In a preferred embodiment, machine base 6 is a large,
`precision granite structure, although other materials may be
`used in the construction of machine base 6 so long as the
`material is capable of dissipating vibration from the high
`acceleration motions that material deposition device 2 is
`capableof.
`
`[0049] Positioning system 8 is preferably a machine
`driven X-Y coordinate gantry supported by machine base 6.
`Positioning system 8 has two X-axis stages, includingfirst
`X-axis stage 10.4 and second X-axis stage 10B, preferably
`constructed of commercially available ballscrew stages.
`X-axis stages 10A-B rest on, and are attached to, vertical
`walls 92A-B of machine base 6. Positioning system 8 is
`preferably
`constructed of
`a
`commercially
`available
`ballscrew stage identical to X-axis stages 10A-B. Y-axis
`stage 12 is fixed, at opposite ends and perpendicular to,first
`X-axis stage LOA and second X-axis stage 10B and spans
`horizontal surface 90.
`
`[0050] Movementat positioning system 8 occurs as Y-axis
`stage 12 moves back and forth along X-axis stages 10A-B.
`This movement
`is driven by motors 404-B which,
`in a
`preferred embodiment, are high-performance brushless DC
`motors with optical encoders for displacement feedback.
`However, any motor which is capable of producing rela-
`tively high acceleration, good velocity regulation, and posi-
`tioning accuracy may be used to operate the movement of
`positioning system 8. In operation, motor 40A drives one
`end of Y-axis stage 12 along X-axis stage 10A while motor
`40B simultaneouslydrives the other end ofy-axis stage 12
`along X-axis stage 10B.
`
`(0051] Another moving componentofpositioning system
`8 is tool interface 20, which resides on Y-axis stage 12 and
`moves back and forth along Y-axis stage 12. Tool interface
`
`30
`
`30
`
`
`
`US 2006/0160250 Al
`
`Jul. 20, 2006
`
`20 is capable ofreceiving a material deposition tool, such as
`material deposition tool 18 illustrated in FIG. 2. As dis-
`cussed in greater detail below, material deposition tool 18
`may receive material cartridges, such as material cartridge
`26. Movement of tool interface 20 along Y-axis stage 12 is
`driven by motor 42, which is preferably a motor similarto,
`or identical to, motors 40A-B. With tool interface 20 being
`capable of moving back and forth along Y-axis stage 12 and
`Y-axis stage 12 being capable of moving back and forth
`along X-axis stages 10A-B, positioning system8 is capable
`of moving tool interface 20 in virtually any direction on a
`horizontal plane above horizontal surface 90.
`
`[0052] Abovehorizontal surface 90 of machine base 6 and
`below positioning system 8 is substrate 16, Substrate 16 is
`a build surface upon which material from material deposi-
`tion tool 18 is deposited. In a preferred embodiment, sub-
`strate 16 is equipped with calibration device 44, which may
`be fixed anywhere onsubstrate 16, but is preferably fixed to
`an outer edge or corner of substrate 16. Calibration device
`44 is described in greater detail below. Substrate 16 is
`preferably constructed of a precision-ground aluminum
`plate, but may be constructed of any material capable of
`ensuring planarity. Substrate 16 rests on support structure
`34, which holds substrate 16 in a horizontal position or,
`alternatively, may be adjusted to change the orientation(i.e.
`angle) of the surface plane of substrate 16 relative to
`positioning system 8. Support structure 34 is preferably of
`rigid construction.
`
`In the particular embodimentillustrated in FIG.2,
`[0053]
`support structure 34 is connected to Z-axis stage 14. Z-axis
`stage 14 is preferably a commercially available ballscrew
`stage, identical to X-axis stag
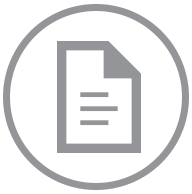
Accessing this document will incur an additional charge of $.
After purchase, you can access this document again without charge.
Accept $ ChargeStill Working On It
This document is taking longer than usual to download. This can happen if we need to contact the court directly to obtain the document and their servers are running slowly.
Give it another minute or two to complete, and then try the refresh button.
A few More Minutes ... Still Working
It can take up to 5 minutes for us to download a document if the court servers are running slowly.
Thank you for your continued patience.
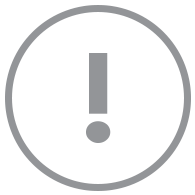
This document could not be displayed.
We could not find this document within its docket. Please go back to the docket page and check the link. If that does not work, go back to the docket and refresh it to pull the newest information.
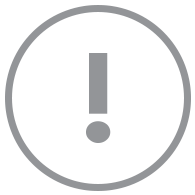
Your account does not support viewing this document.
You need a Paid Account to view this document. Click here to change your account type.
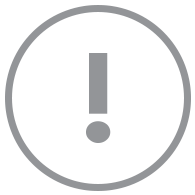
Your account does not support viewing this document.
Set your membership
status to view this document.
With a Docket Alarm membership, you'll
get a whole lot more, including:
- Up-to-date information for this case.
- Email alerts whenever there is an update.
- Full text search for other cases.
- Get email alerts whenever a new case matches your search.
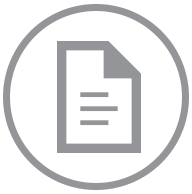
One Moment Please
The filing “” is large (MB) and is being downloaded.
Please refresh this page in a few minutes to see if the filing has been downloaded. The filing will also be emailed to you when the download completes.
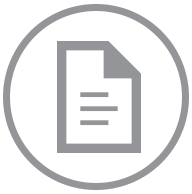
Your document is on its way!
If you do not receive the document in five minutes, contact support at support@docketalarm.com.
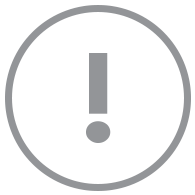
Sealed Document
We are unable to display this document, it may be under a court ordered seal.
If you have proper credentials to access the file, you may proceed directly to the court's system using your government issued username and password.
Access Government Site