`US 6,611,617 B1
`(10) Patent No.:
`
`Crampton Aug. 26, 2003 (45) Date of Patent:
`
`
`US006611617B1
`
`(54) SCANNING APPARATUS AND METHOD
`
`(76)
`
`Inventor: Stephen James Crampton, 9
`Broadfields, Goffs Oak, Waltham Cross,
`Herts EN7 5JU (GB)
`
`*)
`
`otice:
`Noti
`
`this
`disclaimer, the term of
`ubject to any
`f thi
`y disclai
`h
`Subj
`patent is extended or adjusted under 35
`U.S.C. 154(b) by 0 days.
`
`(21) Appl. No.:
`
`09/000,215
`
`(22) PCT Filed:
`
`Jul. 25, 1996
`
`(86) PCT No.:
`
`PCT/GB96/01868
`
`§ 371 (<)Q),
`(2), (4) Date: May 26, 1998
`
`(87) PCT Pub. No.: WO97/05449
`
`PCT Pub. Date: Feb. 13, 1997
`
`(30)
`
`Foreign Application Priority Data
`
`FOREIGN PATENT DOCUMENTS
`
`DE
`DE
`EP
`FR
`GB
`GB
`GB
`WoO
`WO
`
`3938714 Al
`PCT/AT91/00115
`0159187 Al
`PCT/FR90/00090
`2264601 A
`2264602 A
`PCT/GB95/01994
`PCT/US91/07511
`WO 96/10205
`
`$/1991
`5/1992
`10/1985
`9/1990
`9/1993
`9/1993
`2/1996
`4/1992
`4/1996
`
`OTHER PUBLICATIONS
`
`Sakaguchiet al., “Acquisition of Entire Surface Data Based
`on Fusion of Range Data,” IEICE Transactions, vol. E 74,
`No. 10 (1991).
`Fisher et al., “A Hand-held Optical Surface Scanner for
`Environmental Modeling and Virtual Reality,” Department
`of Artificial Intelligence, University of Edinburgh.
`Besl, PJ. and N.D. McKay, “A Method for Registration of
`3-D Shapes”, JEEF Transactions on Pattern Analysis and
`Machine Intelligence, vol. 4, No. 2, pp. 239-256, Feb. 1992.
`
`Jul. 26,1995
`
`(GB) ooeeeeec cece cece cee ceeneeeeenes 9515311
`
`* cited by examiner
`
`Int. C1? vee G06K 9/00; GO1D 11/14
`(51)
`(52) US. Ch. eens 382/154; 382/153; 356/614
`(58) Field of Search 0.0...ee 382/154, 153,
`382/100, 118, 232, 260, 199, 203, 266,
`312; 345/421, 425, 430, 422, 514, 516,
`427, 627, 589; 356/614, 3.14, 141.4
`
`(56)
`
`References Cited
`U.S. PATENT DOCUMENTS
`
`......... 702/153
`3/1987 Krouglicof et al.
`4,649,504 A *
`4/1989 Merz ou. eee eee 345/589
`4,825,391 A *
`1/1991 Inoue et al.
`............ 250/559.22
`4,982,102 A
`2/1991 Inoue etal. wo... 356/607
`4,993,835 A
`2/1992 Donaldson ..
`... 356/376
`5,090,811 A
`12/1992 Field, Jr.
`....
`.. 382/103
`5,168,528 A
`3/1993 Quick etal. .
`.. 345/427
`5,191,642 A *
`3/1993 Schulz ...........
`... 356/614
`5,198,877 A *
`
`.
`. 345/564
`5,251,296 A * 10/1993 Rhoden et al.
`TOM993 Boyles wvvccessenervossenvossee 348/95
`5,255,096 A
`5,264,578 A
`11/1993 Powell etal. .......... 219/130.01
`5,268,996 A * 12/1993 Steiner et al... 257/586
`
`.. 345/627
`5,357,599 A * 10/1994 Luken ............
`5,886,703 A *
`3/1999 Mauldin ....... 345/423
`
`
`
`Primary Examiner—Andrew W. Johns
`Assistant Examiner—Duy M. Dang
`(74) Attorney, Agent, or Firm—Christensen O’Connor
`Johnson Kindness PLLC
`
`(57)
`
`ABSTRACT
`
`A scanning apparatus and method for generating computer
`models of three-dimensional objects comprising, means for
`scanning the object to capture data from a plurality of points
`on the surface of the object so that the scanning may capture
`data from two or more points simultaneously, sensing the
`position of the scanning means, generating intermediate data
`structures from the data, combining intermediate data struc-
`tures to provide the model; display, and manually operating
`the scanning apparatus. The signal generated is structured
`light in the form of a stripe or an area from illumination
`sources such as a laser diode or bulbs which enable data for
`the position and color of the surface to be determined. The
`object may be on a turnable and may be viewedin real time
`as rendered polygons on a monitor as the object is scanned.
`
`11 Claims, 23 Drawing Sheets
`
`
`
`Shenzhen Tuozhu 1009
`
`1
`
`Shenzhen Tuozhu 1009
`
`
`
`U.S. Patent
`
`Aug.26, 2003
`
`Sheet 1 of 23
`
`US 6,611,617 B1
`
`Figure |
`
`
`
`Figure 2
`
`261
`
`3
`
`7
`
`13
`
`S1
`
`260
`
`261
`
`262
`
`2
`
`
`
`U.S. Patent
`
`Aug.26, 2003
`
`Sheet 2 of 23
`
`US 6,611,617 B1
`
`Figure 3(a)
`
`Figure 3(b)
`
`Figure 3(c)
`
`|
`
`.
`
`28'
`
`31
`
`Figure 3(d)
`I
`
`Al
`
`A2
`
`3
`
`
`
`U.S. Patent
`
`Aug.26, 2003
`
`Sheet 3 of 23
`
`US 6,611,617 B1
`
`Figure 4
`
`
`
`4
`
`
`
`U.S. Patent
`
`Aug.26, 2003
`
`Sheet 4 of 23
`
`US 6,611,617 B1
`
`Figure 5(d)
`
`Figure 5(b)
`
`NON-COPLANARITY
`164
`
`163a
`
`165
`
`(CxCy)
`
`Figure 5(c)
`COPLANARITY
`
`165
`
`a
`
`5
`
`
`
`U.S. Patent
`
`Aug.26, 2003
`
`Sheet 5 of 23
`
`US 6,611,617 B1
`
`Figure 6
`
`60
`
`61
`
`35
`
`29
`
`63
`
`64
`
`62
`
`65
`
`22
`
`6
`
`
`
`U.S. Patent
`
`Aug.26, 2003
`
`Sheet 6 of 23
`
`US 6,611,617 B1
`
`Figure 7
`
`HIGH
`
`LOW
`ON
`
`OFF
`OPEN
`
`SHUT.
`OPEN
`
`SHUT
`
`61
`
`SYN
`
`-
`
`C
`
`M
`
`'
`
`:
`
`0
`
`20 MSECS
`
`7
`
`
`
`U.S. Patent
`
`Aug. 26, 2003
`
`Sheet 7 of 23
`
`US 6,611,617 BI
`
`Figure 8
`
`wwweweweeewewowewe
`
`waleeo
`
`ae
`eee ew wee me ee ee ee
`
`31
`
`50
`
`52
`
`ee ee we we ee em
`
`50
`
`8
`
`
`
`
`
`
`U.S. Patent
`
`Aug.26, 2003
`
`Sheet 8 of 23
`
`US 6,611,617 B1
`
`Figure 9
`212 216
`
`Figure 10
`1
`
`210
`
`9
`
`
`
`U.S. Patent
`
`Aug.26, 2003
`
`Sheet 9 of 23
`
`US 6,611,617 B1
`
`Figure 11
`
`
`
`221
`
`222
`
`10
`
`
`
`U.S. Patent
`
`Aug.26, 2003
`
`Sheet 10 of 23
`
`US 6,611,617 B1
`
`Figure 12
`
`231
`
`230
`
`233
`
`932
`
`11
`
`
`
`U.S. Patent
`
`Aug. 26, 2003
`
`Sheet 11 of 23
`
`US 6,611,617 BI
`
`Figure 13
`
`Figure 14(a)
`
`Figure 14(b)
`
`12
`
`12
`
`
`
`
`
`
`U.S. Patent
`
`Aug. 26, 2003
`
`Sheet 12 of 23
`
`US 6,611,617 BI
`
`Figure 15
`
`Figure 16
`
`NEGATIVEPOINT
`
`113. 114
`
`115
`
`Mi
`
`1l5a
`
`13a
`
`13
`
`13
`
`
`
`
`
`U.S. Patent
`
`Aug.26, 2003
`
`Sheet 13 of 23
`
`US 6,611,617 B1
`
`Figure 17
`
`BYTES
`
`10
`
`N - NORMAL
`
`I - INTENSITY
`
`Z - DEPTH VALUE
`
`14
`
`
`
`U.S. Patent
`
`Aug.26, 2003
`
`Sheet 14 of 23
`
`US 6,611,617 B1
`
`Figure 18
`
`Z
`
`(\
`
`oeSEG
`
`9
`
`\
`
`15
`
`
`
`U.S. Patent
`
`Aug.26, 2003
`
`Sheet 15 of 23
`
`US 6,611,617 B1
`
`Figure 19
`
`Z
`
`Y
`
`12
`
`x
`
`121
`
`123
`
`120
`
`16
`
`16
`
`
`
`U.S. Patent
`
`Aug.26, 2003
`
`Sheet 16 of 23
`
`US 6,611,617 B1
`
`Figure 20(a)
`
`282
`Consotopga
`
`bC
`
`c d®
`
`°e
`
`es
`e-
`
`e&%e@
`
`Dag
`
`281
`
`Figure 20(b)
`
`Figure 20(c)
`302 —~ °-2
`
`Figure 20(e)
`307 Ln @a
`e-b
`
`Figure 20(f)
`308
`307a
`“* 307b
`
`Figure 20(g)
`
`303!
`
`17
`
`Figure 20(d)
`302a
`302b
`
`303.
`
`gonho
`
`-
`
`302c
`302d
`304g
`302h
`302i
`302)
`302)
`305
`302k
`
`3021
`
`:
`
`vs
`
`309
`
`17
`
`
`
`U.S. Patent
`
`Aug.26, 2003
`
`Sheet 17 of 23
`
`US 6,611,617 B1
`
`Figure 21
`
`272
`
`Figure 22
`
`321<ay
`
`320a
`
`323b
`
`323a
`
`320b
`
`18
`
`
`
`U.S. Patent
`
`Aug. 26, 2003
`
`Sheet 18 of 23
`
`US 6,611,617 BI
`
`Figure 23
`
`wewewwwrwewewewem==
`weeeewewwwe——eo
`
`time
`
`Figure 24
`
`240
`
`24
`
`25
`
`241
`
`242
`
`19
`
`19
`
`
`
`U.S. Patent
`
`Aug.26, 2003
`
`Sheet 19 of 23
`
`US 6,611,617 B1
`
`Figure 25
`
`4
`
`131
`
`xX
`
`130
`
`132
`
`133
`
`20
`
`20
`
`
`
`U.S. Patent
`
`Aug.26, 2003
`
`Sheet 20 of 23
`
`US 6,611,617 B1
`
`Figure 26(a)
`
`Figure 26(b)
`
`3
`
`333 “NL
`
`LY“™ 333
`
`331 7
`
`3
`
`21
`
`21
`
`
`
`U.S. Patent
`
`Aug.26, 2003
`
`Sheet 21 of 23
`
`US 6,611,617 B1
`
`Figure 27
`
`
`
`i44
`
`142
`
`22
`
`22
`
`
`
`U.S. Patent
`
`Aug. 26, 2003
`
`Sheet 22 of 23
`
`US 6,611,617 BI
`
`Figure 28(a)
`
`Figure 28(b)
`
`Figure 28(c)
`
`23
`
`23
`
`
`
`
`
`U.S. Patent
`
`Aug.26, 2003
`
`Sheet 23 of 23
`
`US 6,611,617 B1
`
`Figure 29(a)
`
`360
`
`Figure 29(b)
`
`362
`
`365
`
`360
`
`24
`
`24
`
`
`
`US 6,611,617 Bl
`
`1
`SCANNING APPARATUS AND METHOD
`
`CROSS-REFERENCE TO RELATED
`APPLICATIONS
`
`This is a United States national application corresponding
`to copending international application PCT/GB96/01868,
`filed July 25, 1996, which designates the United States, the
`benefit of the filing date of which is hereby claimed under 35
`U.S.C. §371, which in turn claims the benefit of British
`Application No. 9515311.0, filed July 26, 1995, the benefit
`of thefiling date of which is hereby claimed under 35 U.S.C.
`119.
`
`FIELD OF THE INVENTION
`
`This invention relates to an apparatus and method for
`scanning a three dimensional object.
`
`BACKGROUND OF THE INVENTION
`
`Real-world, three-dimensional objects whether with natu-
`ral form (e.g. geographical, plant, human or animal-like) or
`man-imagined form (e.g. sculptures, reliefs, cars, boats,
`planes or consumer products) are difficult to scan. This is
`because of features such as rapidly varying surface normals
`and surfaces for which a line of sight is difficult because it
`is partially obscured by other parts of the object.
`Scanning machines—also known as digitizing
`machines—for scanning objects or parts of objects can be
`categorised into two types: computer numerically controlled
`(CNC) and manually operated. Ascanning machine includes
`a unit that contains a sensing means commonlyreferred to
`as a probe.
`Objects or parts of objects can be scanned on CNC
`scanning machines with a number of computer numerically
`controlled (CNC) linear and rotating motor-driven axes.
`Different CNC machines can move/reorient the probe or the
`object—or both—by a combination of translation and rota-
`tion about these axes. Different machine designs are suited
`to different classes of objects. Probes can be temporarily or
`permanently attached to most types of CNC machine tool or
`CNCcoordinate measuring machine which can then be used
`for scanning. As examples, small and simple 3-axis CNC
`milling machines may be used or large, complex 5-axis
`machines may be used. The points captured by CNC
`machines are usually on a regular grid and the rate varies
`from around 1 point per second up to around 20,000 points
`per second depending on the technology being used and the
`object being scanned. The points from these scanning
`machines are accurate to the order of 0.05 mm. CNC
`machines with probes scan by executing one or more
`programs that move the axes of the machine such that there
`is relative motion between the probe and the object.
`CNC machines are expensive, partly because of the
`incorporation of motors and the associated equipment for
`assuring rejection motion such as linear guides and drive
`screws. Few CNC machinesare flexible enough so that the
`probe can be oriented in six degrees of freedomso as to scan
`the complete surface of a complex object. Even when a CNC
`machine has six degrees of freedom, it is often not suffi-
`ciently flexible so as to position the probe to scan the
`complete surface of the object without colliding with the
`object. When the object is a person or expensive, the risk of
`using a CNC machine may be unacceptable and there would
`be a necessity to make a machine to meet both the safety and
`scanning requirements of the application. The programming
`of a CNC machine so that
`the surface of the object is
`
`10
`
`5
`
`20
`
`30
`
`35
`
`40
`
`45
`
`50
`
`55
`
`60
`
`65
`
`2
`completely scanned without a collision of the probe or
`machine with the object is often highly complex. Usually the
`design of the machine and the degrees of freedom inherent
`in the design and limitations in the probe design such as the
`standoff distance during scanning between the probe and the
`object, meanthatit is impossible to come up with a scanning
`strategy that will scan the complete surface of the object. It
`is commonthat the object has to be manually picked up and
`replaced in a different position and or orientation one or
`more times during scanning. Each time that this occurs, the
`object has to be registered to a uniform coordinate system
`such that the data from the different scans can be accurately
`combined.
`
`Manually operated scanning machines can be categorised
`into three types: horizontal arm machines, multiply jointed
`arms and devices based on remote position sensing means.
`Manoually driven, horizontal arm measuring machines
`usually have three orthogonal axes and are usually based on
`a travelling column design. These machinesare usually quite
`large with the bed being at floor level so large items such as
`cars can easily be moved onto and off them. Often motors
`can be engaged on one or more axes to aid the manual
`movementof the machine. The probe is normally mounted
`at a fixed orientation on the end of the horizontal arm. This
`orientation may be changed and various devices may be
`attached betweenthe end of the horizontal arm and the probe
`to aid the changing of the orientation, most of these devices
`having two axes. Horizontal arm machines have the disad-
`vantage of not being able to easily orient the probe in six
`degrees of freedom. The limited flexibility in the design of
`a horizontal arm machine makes mostofthe far side of the
`object unscannable.
`Multiply jointed arms commonly comprise multiple link-
`ages and are available for scanning complex objects. A
`multiply jointed arm typically has 6 joint axes but may have
`more or less joint axes. At the end of the multiply jointed
`arm there is usually a tip reference point—such as a sphere
`whose centre is the reference point or a cone ending in a
`point. Scanningis carried out by bringing the point or sphere
`into contact with the object being scanned. The computer
`monitoring the multiply joined arm then measures the angles
`at all the joints of the multiply jointed arm and calculates the
`position of that reference point in space. ‘Ihe direction of the
`last
`link in the multiply jointed arm is also calculated.
`Positions can typically be output continuously at a rate of
`around 100 points per second, but the rate can be much more
`or much less. The accuracy is of the order of 0.1 to 0.5 mm.
`Thepoints from the arm are usually sparse and unorganised.
`The sparseness and lack of organisation of the points makes
`it difficult to provide enough information for constructing a
`computer modelof the object that is of acceptable quality. A
`multiply jointed arm with multiple linkages has a limited
`working volume. In general, if a larger working volumeis
`required, the arms become very expensive, less accurate and
`tiring, difficult to operate. The limited working volume can
`be increased by leapfrogging in which the whole arm/baseis
`moved to access another volume, but this requires a time
`consuming, systemof registering at least 3 points each time
`the arm is moved and recombining the data sets from each
`arm position. Manufacturer’s of multiplying jointed arms
`provided pre-calibrated arms and test methodsthat the user
`may employ to make sure that the arm is still calibrated to
`an acceptable accuracy. Such test methods use for example
`the standard tip reference point at the end of the arm and a
`reference sphere or a ball-bar which is a rod with two
`cylindrical cups that has a precise knowndistance between
`a homeball and a end of arm ball. As the arm tip at the end
`
`25
`
`25
`
`
`
`US 6,611,617 Bl
`
`3
`of the ball bar is moved on the surface of spherical domain
`the arm records positions which are later compared to a
`perfect sphere and error estimates for the arm are output.
`Remote position sensing devices include hand-held
`devices that transmit or receive position information in a
`calibrated reference volume using different physical meth-
`ods including electromagnetic pulses and sound waves. A
`hand-held device may be connected to the rest of the system
`by means of a cable. These devices are prone to generating
`scanned points with very large errors and some devices
`cannot work when the object being scanned has metallic
`components. They are less accurate than multiply jointed
`arms with accuracies of the order of 0.5 um upwards.
`There are three broad categories of scanning probe that
`could be mounted on the end of a multiply jointed scanning
`machine: point, stripe and area probes. Point probes measure
`a single point at a time and technologies include mechanical
`contact methodsand optical distance measurement methods.
`Stripe probes measure a number of points in a line either
`simultaneously or rapidly in a scanned sequence; the most
`commonstripe technology islaser stripe triangulation. Area
`probes measure a two-dimensional array of points on a
`surface either simultaneously or in a scanned sequence; the
`most commontechnologics are interference fringe and mul-
`tiple stripe projection. Some area methodsrequire the device
`to be heldstill for a few seconds during data capture. Stripe
`and area methods have an in-built speed advantage over
`point methodsas there are less motion of the proberelative
`to the object. There are differences between the methods in
`terms of accuracy and cost but these do not generalise with
`category, for example a particular area technology may be
`cheaper and more accurate than another point technology.
`Meansof capturing independent reference/feature points
`by contact are well known and efficient. Structured light
`using stripe or area methods is not good at capturing
`independent feature points because there is no way for the
`operator to align a known point on the object with a point on
`the stripe or in the area.
`Geometrical errors in the scanning process stem from
`many sources. CCD cameras can typically capture video at
`25 frames per second. One major disadvantage in normal use
`is that from any given demand for a frame there is a
`variability of 40 msecs until the start of capture of that
`frame. If the probe is being moved at for example 100
`mm/sec, this can lead to a geometrical error of 4 mm in the
`probe’s data. The duration of frame capture depends upon
`the shutter speed e.g. “oo sec is 10 msecs. One major
`disadvantage in normal use is that if the probe is being
`moved with a slow shutter speed, an additional geometrical
`error is created. An arm is typically connected to a computer
`by aserial cable with arms typically generating positions at
`125 posilions per second as they move;at this rate there is
`a variability of 8 msecs between when a position is needed
`at the computer and whenit arrives. This can also introduce
`a geometrical error when the probe is moving. The total
`variabilities of the CCD camera and the arm can cause large
`ageregate errors.
`There is a wide range of formats for 3D information in
`current use. These include the general categories: point
`formats, polygon formats and complex surface formats.
`Point formats include: independent points, lines of points
`where a plane intersects with a surface, 2.5D areas of points
`which are commonly known as range images which are
`single valued in Z and 3D point arrays which are often
`generated by medical scanners. The point formats have
`many standard representations including the Range Image
`
`5
`
`20
`
`40
`
`45
`
`50
`
`55
`
`60
`
`4
`resulting from the European ESPRIT
`Standard (RIS)
`Research & Development Project 6911, IGES and DXF
`published by AutoDesk Inc in the USA.
`Polygon formats include polygonsof different geometri-
`cal form. Polygons maybe 3 or more sided and formats may
`include mixed numbers of sides or always the same number
`of sides. Special cases such as Delaunay triangulation can
`specify the positioning of vertices and the relative lengths of
`sides of polygons. Standard representations of polygon
`formats include STL published by 3D Systems Inc in the
`USA, IGES, OBJ published by Wavefront Inc in the USA
`and DXF.
`
`Complex surface formats include Bezier, NURBS, and
`COONSpatches. Standard representations of complex stan-
`dards formats include IGES, VDA-FS, SET, STEP and DXF.
`The objective of scanning can be simply to gather a
`number of three-dimensional points on the surface of the
`object, or it may be to create a computer modelin a format
`that is fuseful for the application in which the model is to be
`used. It is generally true that a cloud of points alone is not
`much use in many applications and that more structure is
`needed to make a computer modelefficient to manipulate in
`typical applications such as visualisation, animation, mor-
`phing and surface or solid modeling.
`There are often benefits to be gained from reducing the
`size of the files associated with the model formats. Anyfile,
`whatever its format can be compressed using standard
`reversible utilities such as PKZIP/PKUNZIP from PKWare
`in the USA. With 3D point arrays, an octet format can be
`used to reduce the size of the arrays that represent a surface;
`an octet format splits a cubic volume into eight, smaller
`cubes and only further subdivides cubes by eight if they
`contain information; an octet format is reversible. Moving
`from unstructured point representation to polygon or com-
`plex surface formats often produces large compressions but
`relies on approximations so the process is nearly always
`irreversible and it is also difficult to automate so as to give
`good enoughresults. Chordal tolerancing is a commonly
`used method of reducing the quantity of discrete points in a
`2D or 3D polyline. As an intermediate data structure it has
`disadvantages in that: the intermediate data structure does
`not record the oricntation of cach stripe, it docs not record
`breaks in the data but assumes that all
`the points are
`connected by a surface and it does not record jumps in the
`data such as those caused by occlusions.
`Most scans today are carried out using a multiply jointed
`arm with a tip reference point. It is usual to firsf mark the
`object to be scanned with a permanent or temporary marking
`device such as an ink pen or scribe to create a polygonal
`network of splines. A single point is then scanned at each
`network intersection. On the computer, the points are linked
`together into a polygonal structure. The overall process
`(marking, scanning and linking) of creating a 3D polygonal
`modelis at a typical rate of 1 point (or vertex on the modcl)
`every 3 seconds. In some implementations, the network is
`not marked on, but appears on a computer display as each
`point is scanned; with this implementation, the network is
`built up interactively. This method is suitable for models
`with a relatively small number of vertices i.e. hundreds and
`thousands. The method is very slow, requires skill, patience
`and concentration, is expensive in human time particularly
`for large, detailed objects that can take 3 weeks to scan.
`An alternative method of scanning with a multiply jointed
`arm and contact tip reference point has often been tried in
`which independent points are rapidly captured without the
`aid of network. The points are then input into a surfacing
`
`26
`
`26
`
`
`
`US 6,611,617 Bl
`
`5
`software package which then constructs a polygonal net-
`work between the points. However, the ‘polygonisation’ of
`unorganised data points is usually very slow and speed
`decreases significantly as the number of points increases.
`‘The results are usually so poor as to be unacceptable. ‘here
`is usually a significant amount of hand editing of the data
`required.
`Where a CNC scanning machineis used, the intermediate
`data structures are usually range images. A number of
`unregistered range images may be registered, polygonised
`and integrated together. The raw data is a numberof range
`images of an object: typically from 5 to 20 in number, with
`each one either being a cylindrical or a linear range image.
`The process is not automatic and requires a combination of
`operator guidance and automated execution of algorithms.
`The operator first
`tries to align (ie. register) the range
`images to each other on the computer using a graphics
`display. This process is not accurate and is followed by an
`automatic least squaresfitting process that attempts to adjust
`the position and orientation of each range image such that
`they fit together as well as possible; this process is lengthy
`often taking hours on a powerful computer. Each range
`image is then independently polygonised into a network of
`2.5D triangular polygons. Finally, the networksof triangular
`polygons are integrated together. The output is a single, 3D
`polygon dataset. The process is expensive both in terms of
`capital equipmentcost and people time. It can take up to two
`years to becomeskilled enough to scan objects to produce
`good enough models. It can work and produce good results
`for detailed objects.
`For smooth objects, where the objective is to create
`complex surface formats, a coordinate measuring machine
`with a contact tip reference point is commonly used. It is
`usual to mark up the object with the desired surface patch
`boundaries by using a marking device such as a pen or a
`scribe. ‘These patch boundaries are then hand digitised with
`the contact point probe. The software package then gener-
`ates a CNC scanning program that automatically takes more
`points along the boundaries and inside the patches. The
`software then automatically generates a first attempt at the
`surface model. This method is used becauseit is quicker and
`easier for the operator to define patch boundaries that will
`lead to a surface model with the desired structure before
`scanning than to define the patch boundaries after scanning
`using a software package on a computer with a display
`showing the scanned points. It can take several days and
`often weeks to create patch boundaries which are usually
`splines and then create the patches and then trim the patches
`to form a surface model by using only the scanned points
`and a computer.
`Scanned data points have been displayed in real-time. The
`display of points has the disadvantages of easily becoming
`confusing to interpret and also that the observer does not
`know whenparts of the object’s surface have been missed
`during scanning.
`SUMMARY OF THE INVENTION
`
`According, to the present invention, there is provided a
`scanning apparatus for scanning an object
`to provide a
`computer model thereof, comprising means for scanning the
`object to capture data from a plurality of points on the
`surface of the object where the scanning meanscaptures data
`from two or more points simultaneously; means for gener-
`ating intermediate data structures therefrom; means for
`combining the intermediate data structures to provide the
`model; means for display and means for manually operating
`the scanning apparatus.
`
`10
`
`5
`
`20
`
`30
`
`35
`
`40
`
`45
`
`50
`
`55
`
`60
`
`65
`
`6
`The apparatus is mostefficient in the quest to reduce the
`time and cost of generating a computer model from a real
`world object by means of scanning with both time and cost
`reductions of an order of magnitude achieved over conven-
`tional
`techniques. The model
`is generated automatically
`from the intermediate data in a form that may be immedi-
`ately usable in a wide range of applications.
`The scanning means may usestructured light to more
`quickly scan the surface of the object. The scanning means
`may also be operable to sense the colour of the surface of the
`object, resulting in a model morelike the real world object.
`Preferably the scanning means therein comprises means
`for generating a signal for scanning the object, signal
`detection means for detecting the signal reflected from the
`object and means operable in response to the detected signal
`to provide the data for the intermediate data structure.
`The structured light is preferably projected as a plane of
`light such that a stripe is formed on a viewing plane that is
`situated normal to the projection axis of the signal generat-
`ing meansandsituated at the average stand-off distance from
`the signal generating means.
`Alternatively the structured light may be projected such
`that a pattern is formed on an area of a viewing plane that
`is situated normal
`to the projection axis of the signal
`generating means and situated at
`the average stand-off
`distance from the signal generating means.
`The signal generating means may be an illumination
`source such as a laser diode or one or more bulbs.
`
`During scanning, the operator may see the surface he has
`scanned appearing in real-time as rendered polygons on the
`display such that he may more easily scan the object. The
`operator may mount the object on a turntable and then he
`may scan from a seated position rather than walking around
`the object. The scanning means can be mounted on many
`different types of manual machines, giving enhanced flex-
`ibility for objects ranging in size from small to very large.
`The scanning means can be mounted on a multiply jointed
`arm for accurate scanning. The scanning mcans may be a
`self-contained unit that contains a remote position sensor
`and incorporates a display to give the most flexibility in
`scanning.
`According to the invention there is also provided a
`method for scanning an object to provide a computer model
`thereof, comprising the following steps:
`manually scanning the object with a signal by manual
`operation of a signal generating means:
`detecting the reflected signal
`generating intermediate data structures for the points;
`combining the intermediate data structures to provide the
`model; and
`displaying the data, wherein the data is captured from a
`plurality of points on the surface of the object simul-
`taneously.
`According to a further aspect of this method of the
`invention the colour datais also captured from the object and
`then mapped on to the model.
`Preferably the data is displayed simultaneously as a
`plurality of display polygons.
`The invention will now be described, by way of example
`only, with reference to the accompanying Figures, of which:
`BRIEF DESCRIPTION OF THE DRAWINGS
`
`FIG. 1 is a schematic representation of a scanning appa-
`ratus according to the invention;
`FIG. 2 is a schematic perspective drawing of a probe;
`
`27
`
`27
`
`
`
`US 6,611,617 Bl
`
`7
`FIG. 3a illustrates a first embodimentof the configuration
`of the optical elements housed in a probe;
`FIG. 30 illustrates a lamp configuration;
`FIG. 3c illustrates an alternative to the lamp configuration
`of FIG. 3b;
`FIG. 3d is a graphillustrating intensity as a function of
`distance along the line Al—A2 of FIG. 3a;
`FIG. 4 illustrates a second embodiment of the configura-
`tion of the optical elements housed in a probe;
`FIGS. 5a to 5d illustrate a method of calibrating the
`colour of the scanning apparatus of FIG. 1;
`FIG. 6 is a schematic block diagram illustrating the
`capture of colour and position data;
`FIG. 7 is a schematic representation illustrating how the
`detection of the colour and position data is synchronised;
`TIG. 8 is a schematic representation of the end of the
`multiply jointed arm of the apparatus of FIG. 1;
`FIG. 9 is a schematic illustration of the turntable and
`
`the
`
`the
`
`multiply jointed arm of the apparatus of FIG. 1;
`FIG. 10 illustrates the mounting of the probe on
`multiply jointed arm;
`FIG. 11 illustrates the alignment of the mount on the
`multiply jointed arm;
`FIG. 12 illustrates the alignment of the probe on
`multiply jointed arm;
`FIG. 13 illustrates a linear range image;
`FIGS. 14a, 145 illustrates cylindrical range images;
`FIG. 15 illustrates the range image placing method;
`FIG. 16 illustrates the surface normal extension method;
`FIG. 17 represents the structure of a single point in a range
`image;
`FIG. 18 illustrates the representation of an object by three
`range images;
`FIG. 19 illustrates the range image updating method;
`FIGS. 20a and 20b illustrate first and second stripes
`captured on a CCD array;
`FIGS. 20c, 20d, 20e and 20f illustrate the respective
`captured data points and strings of data points from the first
`and second stripes of FIGS. 20a and 20b;
`FIG. 20g illustrates polygons generated from these
`strings;
`FIG. 21 illustrates a probe mounted on a head and a
`head-up display;
`FIG. 22 illustrates colour image mapping;
`FIG. 23 illustrates the timing for position interpolation;
`FIG. 24 illustrates the triggering of the arm position
`measurement;
`FIG. 25 illustrates an object with markedlines thereon;
`FIG. 26a illustrates a probe mounted on a multiply jointed
`arm which is mounted on a horizontal arm machine;
`FIG. 265 illustrates two opposing horizontal arm
`machines;
`FIG. 27 illustrates a human foot being scanned;
`FIG. 28a illustrates stripe sections of a pipe network and
`panel;
`FIG. 28b illustrates partial polygon models of a pipe
`network and panel;
`FIG. 28c illustrates extrapolated polygon modelof a pipe
`network;
`FIG. 29a illustrates stripe scanning;
`FIG. 296 illustrates area scanning;
`
`8
`DETAILED DESCRIPTION OF EMBODIMENTS
`
`Referring now to FIG. 1, a scanning apparatus 100
`comprises a multiply jointed arm 1 with an arm control unit
`2 and a probe 3. The control unit 2, which includes a
`processing unit 10 is coupled to a computer or processing
`unit 4 and colour monitor 7. The probe 3 is also coupled to
`a probe control unit 5 that
`is likewise coupled to the
`computer 4, The intermediate data is displayed on the colour
`monitor 7 as rendered polygons 13. The probe 3 provides a
`stripe 8, which is projected onto an object 9 positioned on a
`turntable 14. The stripe 8 is in the form of a plane of light.
`Buttons 6 are also provided to control data capture. A colour
`frame grabber 11 in the computer 4 is mounted on a standard
`bus 12 and coupled to the probe 3.
`The computer 4, probe control unit 5, arm control unit 2,
`buttons 6, colour frame grabber 11 and monitor 7 are
`provided separately, for example, the computer 4 and moni-
`tor 7 may be a personal computer and VDU,although, for
`certain applications, it may be more convenient for one or all
`of them to be provided on the probe 3.
`The multiply jointed arm 1 and the probe 3 are coupled to
`the computer 4 by meansofthe control units 2, 5 discussed
`above. The computer 4 receives information from the scan-
`ning stripe 8, the position/orientation of the arm 1 in terms
`of X, Y, Z coordinates, with the coordinates I,J,K of the
`surface normal of the probe 3 and colour data if required.
`Referring now to FIG. 2, an embodiment of the probe 3
`for use with remote position sensor 261 is shown. The probe
`3 is lightweight and resilient so as to withstand being
`knocked without losing its calibration.
`Referring now to FIG. 29a, the structured light is preter-
`ably projected as a plane of light 364 such that a stri
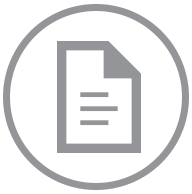
Accessing this document will incur an additional charge of $.
After purchase, you can access this document again without charge.
Accept $ ChargeStill Working On It
This document is taking longer than usual to download. This can happen if we need to contact the court directly to obtain the document and their servers are running slowly.
Give it another minute or two to complete, and then try the refresh button.
A few More Minutes ... Still Working
It can take up to 5 minutes for us to download a document if the court servers are running slowly.
Thank you for your continued patience.
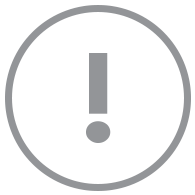
This document could not be displayed.
We could not find this document within its docket. Please go back to the docket page and check the link. If that does not work, go back to the docket and refresh it to pull the newest information.
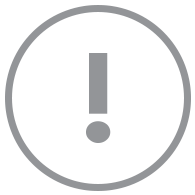
Your account does not support viewing this document.
You need a Paid Account to view this document. Click here to change your account type.
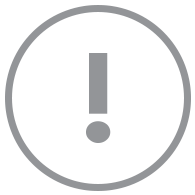
Your account does not support viewing this document.
Set your membership
status to view this document.
With a Docket Alarm membership, you'll
get a whole lot more, including:
- Up-to-date information for this case.
- Email alerts whenever there is an update.
- Full text search for other cases.
- Get email alerts whenever a new case matches your search.
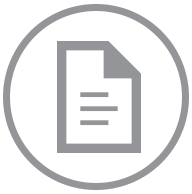
One Moment Please
The filing “” is large (MB) and is being downloaded.
Please refresh this page in a few minutes to see if the filing has been downloaded. The filing will also be emailed to you when the download completes.
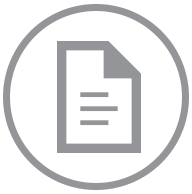
Your document is on its way!
If you do not receive the document in five minutes, contact support at support@docketalarm.com.
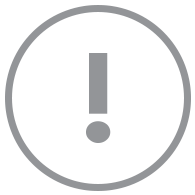
Sealed Document
We are unable to display this document, it may be under a court ordered seal.
If you have proper credentials to access the file, you may proceed directly to the court's system using your government issued username and password.
Access Government Site