`
`(19) World Intellectual Property Organization f
`International Bureau
`
`= ANDAA
`
`
`
`(43) International Publication Date
`28 August 2008 (28.08.2008)
`
`International Patent Classification:
`HOLL 23/34 (2006.01)
`
`(10) International Publication Number
`WO 2008/102266 A2
`
`(74)
`
`INFERMATA SYSTEMS
`Common Representative:
`LTD. Mishli, Oz, P.O.B. 13068, Kochay Yair, 44864
`Kochav Yair (IL).
`
`(51)
`
`(21)
`
`(22)
`
`International Application Number:
`PCT/TB2008/000830
`
`(81)
`
`International Filing Date:
`25 February 2008 (25.02.2008)
`
`Designated States (unless otherwise indicated, for every
`kind of national protection available): AE, AG, AL, AM,
`AO, AT, AU, AZ, BA, BB, BG, BH, BR, BW, BY, BZ, CA,
`CH, CN, CO, CR, CU, CZ, DE, DK, DM, DO, DZ, EC, EE,
`EG, ES, FI, GB, GD, GE, GH, GM, GT, HN, HR, HU, ID,
`IL, IN, IS, JP, KE, KG, KM, KN, KP, KR, KZ, LA, LC,
`LK, LR, LS, LT, LU, LY, MA, MD, ME, MG, MK, MN,
`MW, MX, MY, MZ, NA, NG, NI, NO, NZ, OM, PG, PH,
`PL, PT, RO, RS, RU, SC, SD, SE, SG, SK, SL, SM, SV,
`SY, TJ, TM, TN, TR, TT, TZ, UA, UG, US, UZ, VC, VN,
`ZA, ZM, ZW.
`
`(84)
`
`Designated States (unless otherwise indicated, for every
`kind of regional protection available): ARIPO (BW, GH,
`iM, KE, LS, MW, MZ, NA, SD, SL, SZ, TZ, UG, ZM,
`ZW), Eurasian (AM, AZ, BY, KG, KZ, MD, RU, TJ, TM),
`European (AT, BE, BG, CH, CY, CZ, DE, DK, EE, ES, FI,
`FR, GB, GR, HR, HU, IE, IS, IT, LT, LU, LV, MC, MT, NL,
`NO, PL, PT, RO, SE. SI. SK, TR), OAPI (BF, BJ, CF, CG,
`CI, CM, GA, GN, GQ, GW, ML, MR, NE, SN, TD, TG).
`Published:
`without international search report and to be republished
`uponreceipt of that report
`
`(25)
`
`Filing Language:
`
`(26)
`
`Publication Language:
`
`English
`
`English
`
`(30)
`
`(71)
`
`(72)
`(75)
`
`Priority Data:
`60/902,972
`60/972,657
`60/997,807
`
`23 February 2007 (23.02.2007)
`14 September 2007 (14.09.2007)
`5 October 2007 (05.10.2007)
`
`US
`US
`US
`
`Applicant (for all designated States except US): INFER-
`MATA SYSTEMS LTD. [IL/L]; 78 Ha‘ilanot Street,
`Kochav Yair (IL).
`
`Inventors; and
`Inventors/Applicants (for US only): BITON, Kfir
`{IL/IL]; 56 Belinson St., Halfa (IL). DOLLBERG, Yosh
`[IL/TLJ; 3 Hess St., Raanana(IL).
`
`
`
`008/102266A2IMNTININNININUNMINIONHHIATAA
`
`(54) Titles METHOD AND APPARATUS FOR RAPID FABRICATION OF FUNCTIONAL PRINTED CIRCUIT BOARD
`
`5108
`
`
`
`Figure 5
`
`570
`
`540
`
`400
`
`It is intended that the systems
`(57) Abstract: Systems and methods are provided for producing functional printed circuit boards.
`@¥ and methods described herein will allow the production of functional PCBs in a more efficient and less labor- and equipment-inten-
`
`wo sive manner than may be obtained using conventional production methods. The produced functional PCB would have the required
`
`mechanical, thermal, electrical, etc., characteristics enabling it to function in a manner corresponding to a design characteristics of
`a conventional PCB.
`
`Shenzhen Tuozhu 1008
`
`1
`
`Shenzhen Tuozhu 1008
`
`
`
`WO 2008/102266
`
`PCT/IB2008/000830
`
`METHOD AND APPARATUS FOR RAPID FABRICATION OF FUNCTIONAL
`
`PRINTED CIRCUIT BOARD
`
`CROSS-REFERENCE TO RELATED APPLICATIONS
`
`[0001]
`
`This Applicationis a continuation of and claimspriority from U.S. Application,
`
`Serial Number60/902,972, filed February 23, 2007; U.S. Application, Serial Number 60/972,657,
`
`filed September 14, 2007; and U.S. Application, Serial Number 60/997,807, filed October5,
`
`2007; the disclosureofall of which is incorporated herein by referencein its entirety.
`
`BACKGROUND
`
`1.
`
`Field of the Invention
`
`[0002]
`
`The generalfield of the invention relates to the field of the manufacture of printed
`
`circuit boards. More specifically, the present application relates to systems and methods for
`
`producing functional printed circuit boards, including functional prototype circuit boards, in a
`
`quick, safe, clean, waterless, efficient and compact manner.
`
`2.
`
`Related Arts
`
`[0003]
`
`Printed circuit boards (PCBs) are used to mechanically support and electrically
`
`connect electronic components using conductive pathways,or traces. In conventional PCB
`
`manufacture, such conductive pathwaysor traces are etched or milled from coppersheets
`
`laminated onto a non-conductive substrate. Such a processis relatively time consuming and
`
`utilizes harmful materials and solvents. Additionally, these processes generate waste material
`
`that needs to be disposed ofin a safe and environmentally sound manner. PCBs maybe used in
`
`any ofa variety of applications, including computers, cell phones, and otherelectronics
`
`applications.
`
`[0004]
`
`Oneissue associated with conventional PCB manufactureis that the production of
`
`the PCBsis a relatively complicated and time-consuming process. For example, to produce a
`
`single prototype PCB using conventional manufacturing methods, it may require, typically,
`
`]
`
`2
`
`
`
`WO 2008/102266
`
`PCT/1B2008/000830
`
`between 5 and 30 working days (including electronic component assembly and shipmenttimes),
`
`mainly depending on complexity of the fabricated board. Additionally, because various stages of
`
`the production are typically performed usinga variety of different equipment, which may be
`
`located in different locations, the production of conventional PCBsrequirelogistical
`
`coordination which maylead to further delays. Consequently, conventional fabrication
`
`techniques introducesignificant time delays, especially in prototype fabrication and design of
`
`new devices utilizing PCBs.
`
`[0005]
`
`Anotherissue associated with conventional PCB manufacture is the intensive use
`
`of fabrication tools, such as masks and stencils throughout most process phases, thus requiring
`
`production of new tools and patterns for each design fabricated. Asthis is a fair overhead for
`
`mass production runs, small quantity production runs (such as New Product Introduction — NPI,
`
`and prototyping in particular) suffer enormous overhead of time, costs, handling and materials.
`
`The conventional use of masks also necessitates the use of hazardous materials and solvents,
`
`thereby requiring certain steps of the manufacturingto be carried out in specially designed
`
`facilities, which increase the manufacturing costs.
`
`[0006]
`
`Recent trends in the industry lead to higher complexity PCB fabrication due to
`
`use of more complex technologies and higher demandsin fabrication. Some examplesare:
`
`higher clock frequencies, higher demands on controlled impedance, miniaturization which
`
`derives requirements for smaller traces, smaller pads and vias diameter and more layers. The
`
`smaller the features are, the harder it will be for conventional technology to handle them due to
`
`fundamental limitations of the traditional fabrication process. For instance, registration (i.e.
`
`lamination of separate board layers) is a problematic phase in terms of accuracy, which is driving
`
`conventional PCB fabrication downin termsofyield and accuracy.
`
`[0007]
`
`The requirements on the registration betweenlayers oftraditional PCB
`
`manufacture increase with advanced technologies. Furthermore, registration is one ofthe
`
`bottlenecks in the process, requiring heavy and expensive equipment, and, most importantly, is a
`
`challenge in terms of accuracy and yield (as layers are fabricated individually, suffering
`
`individual, non-linear stretching, and then should be aligned and laminated in accuracies of tens
`
`of microns). Another bottleneck in conventional manufacturing processis the drilling. A typical
`
`2
`
`3
`
`
`
`WO 2008/102266
`
`PCT/1B2008/000830
`
`PCBcontains hundredsto tens of thousands holes in various diameters, which require a set of
`
`drilling machines (e.g. mechanical and laser drilling machines), working in sequential order
`
`possibly with every lamination of every new layerto form the different via types (e.g. buried via).
`
`It is a costly chain in the process, both in time and money(e.g., due to the rapid wear out of
`
`small-diameter drillers), and can cost up to 30%of overall fabrication costs.
`
`[0008]
`
`As is well known, conventional PCBs comprise conductive andinsulative layers
`
`formed over a substrate. The conductive layers form conductive circuitry according to the
`
`desired design. The conductive circuitry is fabricated using masks, e.g., photoresist masks, to
`
`delineate the designed conductive circuitry to be formed on the substrate. Once the mask has
`
`been developed, techniques such as metal electroplating are utilized to deposit conductive
`
`material, e.g., copper, onto the unmasked areas of the substrate. In some designs the maskis
`
`then removed, while in others the mask remains on the PCB. Electroplating or electroless
`
`plating is also used for the interconnect fabrication, to provide electrical connection between the
`
`metal layers. For further discussionrelating to this technology, specifically utilizing SU-8 as the
`
`resin for the photoresist, the readeris directed to U.S. patent 4,882,245, the content of which is
`
`incorporated herein by reference.
`
`[0009]
`
`SU-8 is an octafunctional epoxidized novolac commercially available from
`
`Celanese Corporation of Dallas, Texas. As explained in the above cited ‘245 patent, when
`
`properly mixed with a photoinitiator and other components, SU-8 may be cured using exposure
`
`to radiation, e.g., selective UV illumination, to thereby delineate the circuitry over the substrate.
`
`The ‘245 patent recommendsthe use of UVE 1014, available from General Electric, of Fairfield,
`
`CT,as the photoinitiator, but other materials, e.g., triarylsulfonium salts, may be used.
`
`[0010]
`
`Rapid prototyping is the automatic construction of physical objects or models
`
`using, e.g., solid freeform fabrication or direct writing. solid freeform fabrication (SFF) is a
`
`technique for manufacturing solid objects by the sequential delivery of energy and/or material to
`
`specified points in space to producethat solid. Rapid prototyping takes virtual designs from
`
`computer aided design (CAD) or animation modeling software, transforms them into thin,virtual,
`
`horizontal cross-sections and then creates each cross-section in physical space, one after the next
`
`until the modelis finished. With additive fabrication, the machine reads in data from a CAD
`
`3
`
`4
`
`
`
`WO 2008/102266
`
`PCT/1B2008/000830
`
`drawing and lays down successivelayers of liquid, powder, or sheet material, and in this way
`
`builds up the model fromaseries of cross sections. These layers, which correspondto the virtual
`
`cross section from the CAD model, are joined together or fused automatically to create the final
`
`shape. The primary advantage to additive fabricationis its ability to create rapidly almost any
`
`two or three-dimensional shape or geometric feature. Therefore, rapid prototyping is generally
`
`used to provide a physical model, but not necessarily a working model, of a designedpart.
`
`[0011]
`
`As PCBsare developed for a new product, it is commonto first design a PCB and
`
`then produce a prototype of the PCB, which requires considerable time, effort and expense. The
`
`PCBprototype is then assembled with electronic components and then tested. Mostoften, the
`
`test results reveal either functional or performancedeficiencies, so that the process is repeated
`
`until the last PCB prototype version is validated as correct and ready for mass production.
`
`[0012]
`
`Currently, the absolute majority of PCB prototypes are producedin the same
`
`process and equipment and are made of the same materials as mass production PCB. This
`
`manufacturing processis very labor intensive and inefficient for prototype and low-quantity
`
`production, resulting in considerable waste of time, efforts and expense.
`
`[0013]
`
`Therefore, there continues to be a long existing needin the life cycle of PCBs for
`
`the capability to rapidly and reliably move from the design stage through the prototype stage, to
`
`mass-production. Particularly, it is required to go directly from computer PCBdesigns to
`
`immediate prototypes economically and automatically.
`
`[0014]
`
`PCBprototypes are of very high importance in the PCB developmentprocess, as
`
`they constitute the ultimate means and measurefortesting the developed design, and are
`
`virtually the most important factor in taking the go-to-mass-production decision. Taking a risky
`
`go-to-mass-production decision which is based on PCBprototype whichis not correlated in
`
`testing results to the mass-production fabricated PCB mayresult in failure of mass-production
`
`series produced, thereby causing significant loss of time and money.
`
`[0015]
`
`Various technologies are currently used in the general art of rapid prototyping,
`
`including selective laser sintering (SLS), fused deposition modeling (FDM), stereolithography
`
`(SLA), laminated object manufacturing (LOM), electron beam melting (EBM), and 3D printing
`
`5
`
`
`
`WO 2008/102266
`
`PCT/1B2008/000830
`
`(3DP). In general, the art of rapid prototyping provides a physical, rather than functional,
`
`validation of the designed product.
`
`[0016]
`
`Several attempts have been previously madeto provide rapid PCB prototyping
`
`and manufacturing systems. Some of them also proposed that mechanical rapid prototyping or
`
`similar techniques may be used for PCB fabrication. For example,it has been proposedto utilize
`
`extrusion to form metal traces over conventional PCB substrate. According to another proposal,
`
`UV laseris used to partially cure a resin, so as to form a partially cross-linked substrate. Metal
`
`traces are then deposited over the substrate in a conventional manner. The substrate is then
`
`placed in a mold to changeits shape to a 3D shape, and is then completely cured to result in a 3D
`
`PCB. According to yet another proposal, 3D printing may be used for fabricating PCBs, using a
`
`printer head for dispensing conductive material and another printer head for dispensing insulative
`
`material. For further information about such techniques, the reader is directed to: WO0052976,
`
`US5,172,472, US5,099,090, US5,156,772, US6,169,605, US5,838,567, US5,264,061, and U.S.
`
`published application Nos. 2004/0077112.
`
`[0017]
`
`All of these attempts have indeed proposed alternative rapid methods for PCB
`
`production, compared to the conventional PCB manufacture method. Conventional PCB
`
`manufacturing processes, systems and materials were tightly adapted, for over 60 years, to the
`
`desired functionality of the produced PCB (which dependsonits use and target application).
`
`Therefore alternative manufacturing methods, which are different compared to conventional
`
`PCB manufacture methods, should be adapted to fit target PCB functionality criteria. Otherwise,
`
`the fabricated prototype PCB will be merely a mechanical, limited-functionality model, and not a
`
`fully functional electro-mechanical structure, as it is designated to be. To date, prior art attempts
`
`have failed to consider the functional value of the fabricated PCB, or provide meansto control
`
`the functionality and adaptit to desired functionality criterions.
`
`[0018]
`
`Generally, testing results depend on functional behavior of the PCB under
`
`different conditions. This behavior depends further on numerous properties, whicharestrictly
`
`defined in published PCB industry standards.
`
`[0019]
`
`Yet, in spite ofall efforts and available technology, rapid fabrication of PCB
`
`remains an elusive goal and to this day, PCB fabrication is made using decades-old techniques of
`5
`
`6
`
`
`
`WO 2008/102266
`
`PCT/1B2008/000830
`
`patterning, laminating, drilling conductorplating, solder resist, and screen printing. This
`
`protracted process causes delays and cost increases in both the design and manufacturing phases
`
`of any productutilizing a PCB. Accordingly, there is a need in the art for a revolutionary
`
`technology that would drastically reduce the fabrication time and manufacturing complexity.
`
`Additionally, there is a need in the art for a technique that would avoid or minimize the intensive
`
`use of toxic and/or hazardous materials of conventional fabrication methods. These methodsare
`
`also extremely wasteful, as it is estimated that only about 7%of the materials used in the
`
`production process end up in the PCB. The remaining 93% are mainly disposedoff as toxic
`
`waste, thereby causing significant environmental damage.
`
`SUMMARY
`
`[0020]
`
`The following summary ofthe inventionis described in order to provide a basic
`
`understanding of some aspects and features of the invention. This summary is not an extensive
`
`overview ofthe invention, and as suchit is not intended to particularly identify key orcritical
`
`elements of the invention, or to delineate the scope of the invention.
`
`Its sole purposeis to
`
`present some concepts of the invention in a simplified form as a prelude to the more detailed
`
`description that is presented below.
`
`[0021]
`
`According to an aspect ofthe present invention, methods and apparatus for the
`
`quick andefficient production of functional PCBs and functional PCBprototypes, directly from
`
`computer designs, are provided.
`
`[0022]
`
`A feature of the present invention is that the PCB fabricated, although produced
`
`of different materials and by different processes and machinery, compared to conventional
`
`manufacture methods (which are used in mass production), would yield testing results which
`
`highly correlate to the testing results of the same design when produced in conventional mass
`
`production methods.
`
`[0023]
`
`It is another aspect ofthe present invention that the method and apparatus
`
`provided herein produce PCBsin correlation to important properties and specifications defined
`
`in prominent industry standards, as will be described in detail in the description. Furthermore,
`
`the present invention includes predetermined means for complying with current and future
`
`7
`
`
`
`WO 2008/102266
`
`PCT/1B2008/000830
`
`standardsin a structured manner, thus enabling flexibility in preparation to production of PCBs
`
`which comply with applicable industry standard, as specified for the required target application.
`
`[0024]
`
`According to the various exemplary embodiments described in the present
`
`application, systems and/or methods are provided for producing functional printed circuit boards.
`
`It is intended that the systems and methods described herein will allow the production of
`
`functional PCBsin a moreefficient and less labor- and equipment-intensive manner than may be
`
`obtained using conventional production methods. The produced functional PCB would have the
`
`required mechanical, thermal, electrical, etc., characteristics enabling it to function in a manner
`
`corresponding to design characteristics of a conventional PCB.
`
`[0025]
`
`The invented equipmentfor fabricating PCBsis “office friendly” and suitable for
`
`use in clean operations, such as research and developmentfacilities. Further, the systems and
`
`methodsfor fabricating the PCBs mayresult in the elimination (or tremendous reduction) of
`
`fabrication tools (e.g. masks and stencils) usage in this equipment, thus the fabrication processis
`
`easy to handle and very efficient for short production runs. Materials are selected for the various
`
`components of the PCBsthat possess suitable electronic, electrical, electromagnetic, thermal and
`
`mechanical characteristics, as will be described in greater detail below.
`
`[0026]
`
`According to an exemplary embodiment, rapid prototyping equipment is used to
`
`allow the production of functional PCBsin a shortened duration as compared to conventional
`
`methods(e.g., in as little as a several hours according to one exemplary embodiment). Such time
`
`savings may be achieved by changing not only the process phases involved in the manufacture of
`
`the PCBs, but also the equipment and materials used. Conventional PCB manufacturing requires
`
`tens to hundredsof skilled employees, very high investment in equipmentand inventory, and
`
`large manufacturing facility. On the other hand, according to a particular exemplary
`
`embodiment, a PCB may be manufactured by a single operator using a single system that
`
`integrates various components that previously were part of multiple different machines. The
`
`processis fully automated and the single employee is merely responsible for replacing cartridges,
`
`load the system with fabrication data, simple system calibration etc. Optionally, electronic
`
`component assemblyis integrated into the process so that a full turn-key system is provided.
`
`8
`
`
`
`WO 2008/102266
`
`PCT/1B2008/000830
`
`[0027]
`
`Accordingto an aspect of the invention, a PCBis fabricated without the use of a
`
`substrate or the conventional copper clad laminate (CCL). Rather, additive technologies, such as
`
`SFF techniques and/or electronic printing techniques,are utilized to fabricate a PCB from scratch,
`
`i.c., without a starting substrate. In one specific example, a radiation-curable liquid composition
`
`is deposited onto a tray. Then, the radiation-curable liquid composition is radiated to delineate
`
`the shape and the boundaries of the PCB,so as to provide a cured insulating layer. That is, the
`
`radiation can be provided selectively so as to cure the liquid to any size and shape PCB,
`
`including geometric forms withinit (e.g. via holes). This first step generates an insulatorthatin
`
`essence replaces the conventional substrate that previously needed to be drilled and cut to the
`
`propersize and shape. After the insulating layer is cured, a conductive trace is deposited in an
`
`additive and maskless manneronthe curedinsulating layer using, e.g., ink jet, or other
`
`technology. Thereafter, another insulating layer is deposited using the radiation-curable liquid
`
`composition, and so on and so forth, until all of the layers are completed. Via metallization is
`
`also performed using additive technology, such as SFF. The PCB maythen beflipped and
`
`another sequenceofinsulation and conductive layers provided on the other side, so as to generate
`
`a multi-layer, double-sided PCB. Various curing and baking steps maybe utilized during the
`
`fabrication of each conductive and/orinsulative layer. Amongits various advantages,the
`
`inventive method avoids the problemsof alignment and registration by performing registration
`
`for each layer while it is being fabricated, hence avoiding accumulation of inaccuracies.
`
`[0028]
`
`According to an aspect of the invention, a method for fabricating at least one
`
`functional printed circuit board (PCB) is provided, comprising, a. obtaining a PCB fabrication
`
`data file; b. performing data conversion to generate a modified fabricationfile corresponding to
`
`the fabrication data file; c. performing data transformation by modifying parameters specified in
`
`the modified fabrication file to account for variation in materials and processes utilized for
`
`fabricating the PCB,the data transformation generating a transformed fabricationfile; d.
`
`providing a tray; e. using the transformed fabricationfile to fabricate a dielectric layer by:i.
`
`depositing into the tray a liquid composition;ii. allowing the liquid composition to spread over
`
`the surface of the tray; and, iii. curing selected areas of the liquid composition to delineate the
`
`shape and the boundaries of the PCB to provide a cured insulating layer having a top and bottom
`
`surfaces; and, f. using the transformedfabrication file to fabricate a conductive layer by
`8
`
`9
`
`
`
`WO 2008/102266
`
`PCT/1B2008/000830
`
`depositing a conductive trace on at least one of the top and bottom surfaces of the cured
`
`insulating layer; to thereby provide a PCB having performancecharacteristics correlating to
`
`performance characteristics of a conventionally fabricated PCB usingthe fabrication data file.
`
`The method mayfurther comprise repeating steps e and fa plurality of times over one of the top
`
`and bottom surfaces of the dielectric layer so as to provide a multi-layer one-sided PCB. The
`
`method may further comprise flipping the one-sided PCBsothat the cured insulating layer
`
`becomestop layer on the tray, and repeating steps e and fa plurality of times on the otherofthe
`
`top and bottom surfaces of the dielectric layer so as to provide a multi-layered double-sided PCB.
`
`The method may further comprise repeating steps e and fa plurality of times over both of the top
`
`and bottom surfaces ofthe dielectric layer to provide a multi-layered double-sided PCB. The
`
`method mayfurther comprise depositing one or more of an insulative solder mask layer, a
`
`conductive pad coating and a legend on the double-sided PCBusing colored dielectric material.
`
`[0029]
`
`Curing selected areas may compriseirradiating selected areas.
`
`Irradiating
`
`selected area may comprise directing UV radiation onto selected areas. Curing selected areas
`
`may further comprise a curing enhancementstep following the irradiating the selected areas.
`
`The curing enhancement step may comprise a heating step. The heating step may comprise
`
`radiating the fabricated PCB with microwaveradiation. In the method, step d may further
`
`comprise providing a release agent over the tray. Providing a release agent may comprise one
`
`of: providing a fabric layer overthe tray or spreadinga liquid releasing agent overthe tray. The
`
`method may further comprise fabricating holes in the cured insulation layer by defining non-
`
`irradiated areas and cleaning the non-radiated areas after the curing step. The method may
`
`further comprise depositing conductive substance into selected holes to thereby fabricate
`
`conductive vias. Step e may comprise depositing into the tray a liquid composition comprising
`
`an octafunctional epoxidized novolac and photoinitiator. The liquid composition may further
`
`comprise nano-particles. Depositing a conductive trace may comprise using a deposition head to
`
`inject conductive substance onto the cured insulating layer. Each time step e is performed, sub-
`
`steps 1. 11. and ili. may be repeated a plurality oftimes so as to fabricate the dielectric layer by
`
`fabricating a plurality of sub-layers. After each repetition of sub-step iii. heat may be applied to
`
`the fabricated PCB. Each time sub-stepsi. ii. and iii. are performed, the method may further
`
`comprise fabricating holes in the sub-layer. Each time sub-stepsi. ii. and iii. are performed, the
`9
`
`10
`
`10
`
`
`
`WO 2008/102266
`
`PCT/1B2008/000830
`
`method may further comprise depositing conductive substance into selected holes. After a
`
`sequence of sub-stepsi. il. and lil. is performeda plurality of times, the method may further
`
`comprise depositing conductive substance into selected holes. At selected times wherein step e
`
`is performed, the method may further comprise fabricating curing enhancing tunnels in the
`
`fabricated dielectric layer. At selected times wherein step e is performed, the method may
`
`further comprise depositing soluble material to define voids in the fabricated dielectric layer.
`
`Eachtimestep e is performed, sub-stepsi. ii. and iii. may be repeated a plurality of times using
`
`at least two different dielectric materials, so as to fabricate the dielectric layer by fabricating a
`
`plurality of sub-layers having different dielectric insulation properties.
`
`[0030]
`
`In the method, step e may further comprise mixing into the dielectric materials at
`
`least one of ingredients that assist in conductors adherence, ingredients that mechanically
`
`stabilize the dielectric material, and ingredients that thermally stabilize the dielectric and
`
`material. Step e may further comprise mixing into the dielectric materials ingredients that
`
`modify the insulating properties of the dielectric material. Step e may further comprise
`
`depositing onto the dielectric layer an intermediate layer formed for improved conductive
`
`material adherence to the dielectric layer. At selected times wherein step e is performed, the
`
`method may further comprise generating trenches on at least one surface of the dielectric layer
`
`and wherein step f comprises depositingat least part of the conductive trace into the channels.
`
`Atselected times wherein step f is performed, the method may comprise depositing conductive
`
`traces of varying thickness as specified by the transformed fabrication file. At selected times
`
`wherein step f is performed, depositing conductive traces may comprise depositing a seed layer
`
`of conductive material and forming a main conductive layer over the seed layer. Forming a main
`
`conductive layer may comprise using electroplating. At selected times wherein step f is
`
`performed, the method may further comprise performing and least one of automated optical
`
`inspection of the formed conductive traces and electrical resistivity testing of the conductive
`
`traces.
`
`[0031]
`
`The method may further comprise performingelectrical testing at completion of
`
`fabrication of the PCB. A plurality of PCB boards may befabricated concurrently within the
`
`tray. Each of steps e and f may further comprise selecting fabrication parameters accordingto at
`
`10
`
`11
`
`11
`
`
`
`WO 2008/102266
`
`PCT/1B2008/000830
`
`least the desired insulation properties of the dielectric layer and resistivity properties of the
`
`conductive layer. Step e,ii, may further comprise planarizing a top surface ofthe liquid.
`
`[0032]
`
`According to an aspect of the invention, a method for fabricating at least one
`
`functional printed circuit board (PCB)is provided, comprising: uploading PCB fabrication data
`
`file onto a controller; utilizing the controller to control operation of a central handling station to
`
`load and unload a fabrication tray onto and from a plurality of tray positioning stations; utilizing
`
`the controller to control operation of a dielectric dispenserto dispense a dielectric substance onto
`
`the tray and to control operation of a curing mechanism to cure the dielectric substance to form a
`
`dielectric layer; utilizing the controller to control operation of a conductor dispenser to dispense
`
`a conductive substance onto the dielectric layer; and, utilizing the controller to control operation
`
`of a thermal station to thermally process at least one of the dielectric substance and the
`
`conductive substance. Thermally processing may comprise exposingat least one of the dielectric
`
`substance and the conductive substanceto at least one of: UV radiation, microwaveradiation,
`
`and heater radiation. Controlling operation ofthe dielectric dispenser may comprise operating a
`
`liquid dispenser to dispensea radiation curable liquid onto the tray, and wherein curing the
`
`dielectric substance comprisesradiating the liquid. Control operation of a dielectric dispenser
`
`may comprise operating a dispenser head to deposit dielectric substance according to layout
`
`design of the dielectric layer. The method may further compriseutilizing the controllerto
`
`control operation of a planarizing mechanism to planarize the dielectric layer. Controlling
`
`operation of the conductor dispenser may comprise operating a printer jet to dispense conductive
`
`trace material.
`
`[0033]
`
`The method may further comprise utilizing the controller to control operation of a
`
`flipping mechanismto flip a fabricated board so as to form conductive traces on both sides of the
`
`board. The method may further comprise fusing at least two fabricated boards together. The
`
`method may further comprise: operating the control console to generate a freeform fabrication
`
`file using at least the PCB fabrication data file; and, operating the control console to transform
`
`the freeform fabricationfile into a transformed fabrication file, wherein selected data of the
`
`freeform fabrication file is transformed so as to enable correlating performance characteristics of
`
`the PCB to performance characteristics of a conventionally fabricated PCB. Transforming into
`
`1]
`
`12
`
`12
`
`
`
`WO 2008/102266
`
`PCT/1B2008/000830
`
`transformed fabrication file may further comprise generating files to control the curing
`
`mechanism to delineate vias. Transforming into transformed fabrication file may further
`
`comprise generating files to control the curing mechanism to delineate vias having oblique, non-
`
`vertical sidewalls. Transforming into transformed fabrication file may further comprise
`
`generating files to fabricate mating structures on each fabricated board to ensure alignment
`
`during the step of fusing the fabricated boards.
`
`[0034]
`
`In the method,utilizing the controller to control operation of a conductor
`
`dispenser may comprise depositing conductive substance on both sides of the dielectric layer.
`
`The method may further comprise setting parameters of the curing mechanism to facilitate
`
`fabricating dielectric layer having properties corresponding to conventional PCB insulation layer
`
`fabricated according to the fabrication data file. The method may further comprisesetting
`
`parameters of the conductor dispenser and the thermal station to facilitate fabricating conductive
`
`layer having properties corresponding to conventional PCB conductive traces fabricated
`
`accordingto the fabrication data file. Transforming into transformed fabricationfile may further
`
`comprise changing a designed thickness of conducti
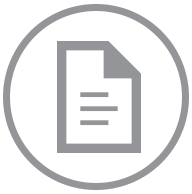
Accessing this document will incur an additional charge of $.
After purchase, you can access this document again without charge.
Accept $ ChargeStill Working On It
This document is taking longer than usual to download. This can happen if we need to contact the court directly to obtain the document and their servers are running slowly.
Give it another minute or two to complete, and then try the refresh button.
A few More Minutes ... Still Working
It can take up to 5 minutes for us to download a document if the court servers are running slowly.
Thank you for your continued patience.
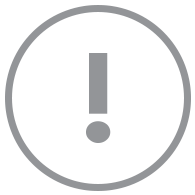
This document could not be displayed.
We could not find this document within its docket. Please go back to the docket page and check the link. If that does not work, go back to the docket and refresh it to pull the newest information.
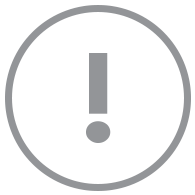
Your account does not support viewing this document.
You need a Paid Account to view this document. Click here to change your account type.
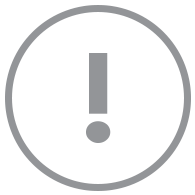
Your account does not support viewing this document.
Set your membership
status to view this document.
With a Docket Alarm membership, you'll
get a whole lot more, including:
- Up-to-date information for this case.
- Email alerts whenever there is an update.
- Full text search for other cases.
- Get email alerts whenever a new case matches your search.
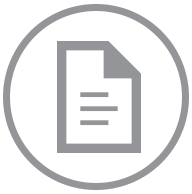
One Moment Please
The filing “” is large (MB) and is being downloaded.
Please refresh this page in a few minutes to see if the filing has been downloaded. The filing will also be emailed to you when the download completes.
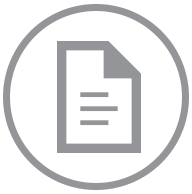
Your document is on its way!
If you do not receive the document in five minutes, contact support at support@docketalarm.com.
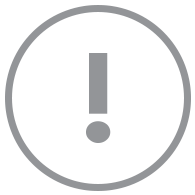
Sealed Document
We are unable to display this document, it may be under a court ordered seal.
If you have proper credentials to access the file, you may proceed directly to the court's system using your government issued username and password.
Access Government Site