`
`;
`
` FOREIGN PATENT DOCUMENTS
`US 2011/0282482 Al——Nov. 17, 2011
`EP
`1262305
`/2006
`JP
`2001-270096
`10/2001
`OTHER PUBLICATIONS
`
`65
`
`51)
`
`Prior Publication Data
`
`(2006.01)
`(2006.01)
`(2006.01)
`(2006.01)
`
`
`
`US 9,156,204 B2
`(10) Patent No:
`a2) United States Patent
`Knighton
`(45) Date of Patent:
`Oct. 13, 2015
`
`
`US009156204B2
`
`54) HYBRID SCANNER FABRICATOR
`
`75)
`
`73)
`
`a
`
`:
`.
`Inventor: Mark S. Knighton, Santa Monica, CA
`(US)
`
`Assignee: Synerdyne Corporation, Santa Monica,
`CA (US)
`“
`:
`:
`‘
`Subject to any disclaimer, the term ofthis
`patent is extended or adjusted under 35
`USS.C. 154(b) by 249 days.
`
`eos
`Notice:
`
`3/1995 Batchelderetal.
`5,402,351 A
`5/1996 Burns
`5,514,232 A
`11/1997 Hollarset al.
`5,683,561 A
`12/1997 Masters et al.
`5694324 A
`3/1998 Mattes et al.
`5,730,925 A
`4/1998 Sandersetal.
`5,740,051 A
`3/1999 Burnset al.
`5,879,489 A
`5,993,554 A * 11/1999 Keicher etal. oc. 118/641
`6,309,581 Bl
`10/2001 Gervasi
`6,391,251 BL*
`5/2002 Keicher et al. oe 419/7
`6,405,095 BL*
`6/2002 Janget al. vaccscssesien 700/118
`6,575,218 Bl
`6/2003 Burnset al.
`6,627,835 BL
`9/2003 Chunget al.
`6,629,011 BL*
`9/2003 Calderon et al. ou... 700/119
`6,764,636 BL
`7/2004 Allanic et al.
`.
`6,841,116 B2
`dipel Nex T2832
`aL)
`1/2005. Schmidt
`
`¢ 5/2005 Kuboetal.6,896,839 B2
`
`22)
`Filed:
`May 17, 2010
`> Auboera
`(Continued)
`
`Int. Cl.
`BOSC 19/00
`BOSB 7/06
`BOSC LIAO
`B29C 67/00
`(52) U.S.CL
`CPG: saves sees semererrensas B29C 67/0055 (2013.01)
`(58) Field of Classification Search
`USPC onsen 118/308, 309, 313-315, 666, 667, 712,
`118/713, 665, 697, 698; 425/375, 135, 145,
`425/162, 166, 150, 131.1, 60
`See applicationfile for complete search history.
`References Cited
`
`
`Synerdyne Corporation, PCT Search Report and Written Opinion
`mailed Feb. 8, 2012; PCT/US201 1/035260.
`(Continued)
`
`Primary Examiner — Yewebdar Tadesse
`(74) Attorney, Agent, or Firm — Blakely Sokoloff Taylor &
`Zafman LLP
`
`ABSTRACT
`(57)
`A system and methodto fabricate three dimensional objects.
`A set of fabricationtools includeat least a coarse deposition
`head and a fine additive head, a fine subtractive head or both
`employed concurrently within a single housing. A scanner
`may also be used within the housing to perform interleaved
`scanning ofthepartial fabrication during the fabrication. The
`process may be adjusted based on the scanresults.
`
`7 Claims, 4 Drawing Sheets
`
`(56)
`
`U.S. PATENT DOCUMENTS
`
`3,013,925 A
`4,589,830 A
`4,752,352 A
`5,260,009 A
`5,303,141 A
`5,398,193 A *
`
`12/1961
`5/1986
`6/1988
`LL/1993
`4/1994
`3/1995
`
`Larsen
`Clawson
`Feygin
`Penn
`Batchelderetal.
`deAngelis oo... 700/119
`
`
`
`
`COARSE
`SUBTRACTIVE
`HEAD
`NOZZLE
`
`
`
`
`
`
`
`30
`SCANNER
`
`XYZ SERVO TABLE
`
`
`
`1
`
`Shenzhen Tuozhu 1005
`
`1
`
`Shenzhen Tuozhu 1005
`
`
`
`US 9,156,204 B2
`
`Page 2
`
`(56)
`
`References Cited
`
`
`U.S. PATENT DOCUMENTS
`
`7,004,222 B2
`7,033,160 B2
`7.037.382 B2
`7,125,512 B2
`7,168,935 Bl
`7,291,002 B2
`Pees eS
`7,879,393 B2
`8,246,888 B2
`2001/0017085 A
`2001/0019340 A
`2001/0050448 A
`2002/0029094 A
`SOONG AT
`2
`2004/0170765 A
`2004/0175451 A
`2005/0001356 A
`2005/0167038 A
`2006/0105102 A
`2006/0225834 A
`2007/0077323 A
`2007/0126157 A
`2009/0020901 A
`2009/0177309 A
`2010/0127433 A
`
`
`
`
`
`Edereret al.
`2/2006
`Fong
`/2006
`19006 Davidson
`10/2006 Crumpetal.
`1/2007 Tamingeretal.
`11/2007 Russelletal.
`teontG aessky ehials
`2/2011 Ederer et al.
`/2012 Hopkinsetal.
`2001 Kuboetal.
`/2001 Kubo et al. cece 347/1
`
`12/2001 Kubo etal.
`.
`312002 KOEIesses serene f 90/ 197
`Bbhnd Sai aespa 264'40.1
`/
`Mulhaupt
`et al.
`9/2004
`Edereretal.
`9/2004 Maekawa etal.
`............. 425/144
`1/2005 Tochimoto et al.
`2005 Torris et al.
`5/2006 Hochsmann etal.
`10/2006 Medinaetal.
`/2007 Stonesmith etal.
`(2007 Bredt
`1/2009 Schillen et al.
`/2009 Kozlak
`(2010 Medinaet al.
`
`6/2010 Kritchman et al.
`2010/0140852 Al
`6/2010 Blake
`2010/0161105 Al
`§/2011 Yasukochi
`2011/0101569 Al
`11/2012 White etal.
`2012/0281239 Al
`12/2013 Jamar et al.
`2013/0334740 A9
`1/2014 Costabeber
`2014/0027953 Al
`2/2014 Crumpetal.
`2014/0048981 Al
`7/2014 Elsey
`2014/0191442 Al
`OTHER PUBLICATIONS
`Synerdyne Corporation, et al., PCT Search Report mailed Apr. 9,
`2012; PCT/US2011/051835.
`Synerdyne Corporation, et al., PCT Search Report mailed Apr. 9,
`2012; PCT/US2011/051838.
`Synerdyne Corporation, et al., PCT Search Report mailed Apr. 9.
`2012; PCT/US2011/051839.
`Synerdyne Corporation, International Preliminary Report on Patent-
`ability, International Appln No. PCT/US2011/051835 mailed Mar.
`4
`a
`= 2013.
`.
`.
`a
`ynerdyne Corporation, International Preliminary Report on Patent-
`ability, International Appin No. PCT/US2011/05 1838, mailed Mar.
`28, 2013.
`Synerdyne Corporation, International Preliminary Report on Patent-
`ability, International Appin No. PCT/US2011/05 1839, mailed Mar.
`28, 2013.
`Notice ofAllowance, U.S. Appl. No. 12/884,982, dated Jul. 30, 2014.
`9 pages.
`
`
`
`
`
`* cited by examiner
`
`2
`
`
`
`US. Patent
`
`Oct. 13, 2015
`
`Sheet 1 of 4
`
`US 9,156,204 B2
`
`
`
`SALLOVYLENS
`
`de
`
`
`
`S1aVLiOANASZAK
`
`YANNVOS
`
`3
`
`
`
`US. Patent
`
`Oct. 13, 2015
`
`Sheet 2 of 4
`
`US 9,156,204 B2
`
`YOLOW
`
`VIHA
`
`ASHVOO
`
`QVWSH
`
`NVOSGe
`
`QVSH
`
`vO0Z
`
`002c0¢
`
`
`
`YaTIONLNOOAYVMLIOS
`
`ONISOLINOW
`
`SYSAIG
`
`JINGOW
`
`802
`
`vec
`
`oCE
`
`0ZZ8b2912vieoLeOLZ
`
`avVaH
`
`
`
`
`
`
`
`ANIsYOLOWS8YOLOWHwOLONZUYOLOWAYOLOWX
`
`
`
`
`
`4
`
`
`
`
`U.S. Patent
`
`Oct. 13,2015
`
`Sheet 3 of 4
`
`US 9,156,204 B2
`
`START
`
`ORIENT COARSE NOZZLE
`FOR DEPOSITION
`
`2
`
`2
`
`304
` DEPOSIT MATERIAL
`
`FROM COURSE NOZZLE
`
` INTERLEAVE
`
`
`SCAN?
`
`SCAN
`OBJECT
`
`308
`
`
`
`310
`
`
`
`
` DETAILING
`REQUIRED?
`
`ANALYZE
`SCAN
`
`SUBTRACTIVE HEAD
`
`314
`
`
`
`DETAILING
`CAN BE
`
`
`DEFERRED?
`
`
`YES
`
`
`NO
`
`DETAIL OBJECT WITH FINE
`RESOLUTION ADDITIVE OR
`
`316
`4
`
`NO
`
`318 FABRICATION
`
`
`COMPLETE?
`
`
`YES
`END
`
`FIG. 3
`
`5
`
`
`
`DEPOSITION ZONE
`
`safesyesaepson
`
`Yi
`
`FIG. 4
`
`6
`
`
`
`US 9,156,204 B2
`
`1
`HYBRID SCANNER FABRICATOR
`
`FIELD
`
`The invention relates to a method and apparatusfor fabri-
`cating three dimensional objects. More specifically, embodi-
`ments of the invention relate to a hybrid applicator having
`coarse and fine fabrication capabilities and, in some cases,
`interleaved scanning.
`
`BACKGROUND
`
`Various three dimensionalprinters exist which can be used
`to fabricate a three dimensional object from a digital model.
`Typically, such printers spray downa seriesoffine dots of a
`plastic material perpendicularly to a build surface. The dot
`size is selected to permit creation ofthe minimumfeature size
`desired. As a result, when larger than the minimum feature
`size is desired, many more dots must be accumulatedto create
`the feature. Additionally, a sacrificial material must be used to
`support anyfeatures that are not perpendicularly supported
`by the build surface. As a result, the build process tends to be
`quite slow.
`fabrication systems
`Other existing three dimensional
`employa gel, which is extruded and cured to form a three
`dimensional object. However, this system has manyofissues
`described above and additionally suffers from sagging and
`deformation during cure.
`Additionally, anomalies or inconsistencies within the build
`process camnotbe identified, while the process is occurring.
`Thus, it is only after the time is consumedfor the complete
`fabrication that the finished product may reveal the build was
`unsuccessful. Thus, an entire additional build process must be
`undertaken to create a new object. A morereliable and faster
`apparatus and system for forming three dimensional objects
`from a digital representation is desirable.
`
`BRIEF DESCRIPTION OF THE DRAWINGS
`
`
`
`The embodimentsofthe invention areillustrated by way of
`example and not by wayof limitation
`in the figures of the
`accompanying drawings in which like references indicate
`similar elements. It should be noted that references to an
`embodimentof the invention in this disclosure are not neces-
`sarily to the same embodiment, and they mean at least one.
`FIG. 1 is a schematic diagram of a system of one embodi-
`ment ofthe invention.
`
`FIG.2 is a schematic diagram of a control subsystem for
`one embodimentofthe invention.
`FIG. 3 is a flow diagram of operation according to one
`embodimentof the invention.
`FIG.41s a schematic diagram showing oriented deposition
`according to one embodimentofthe invention.
`
`DETAILED DESCRIPTION
`
`FIG. 1 is a schematic diagram of a system of one embodi-
`mentof the invention. Within the housing 100, a plurality of
`fabrication tools 108 is disposed. Fabrication tools 108 may
`be disposed as a single head or individual independently
`moveable heads. In one embodiment, a coarse print nozzle
`1021s provided to deposit a fabrication material within a work
`space 110 at a granularity of greater than 0.030 square inches
`per deposition. As used herein, granularity greater than x
`meansthat each deposition occupiesan area greater than x.A
`work surface (also referred to as a build surface) 112 provides
`a support for the fabrication of a three dimensional target
`
`2
`object 114. In one embodiment,a plurality of servos move the
`work surface 112 relative to the fabrication tools 108 in x,y.
`z androtational directions responsive to computercontrol.
`In some embodiments, because the coarse nozzle 102 may
`deposit volumes ofmaterial that will not cool quickly enough
`under ambientconditions, an active cooling arm 120 may be
`used to provide active localized cooling to material deposit by
`coarse nozzle 102. In some embodiments, coarse nozzle 102
`mayalso be oriented to a different angular orientations 122
`relative to the work surface 112. This is discussed in more
`detail with reference to FIG. 4 below. In some embodiments
`the cross section of the nozzle 102 may also be changed so
`that a single deposition may have a different shape than a
`subsequentorprior deposition.
`Insome embodiments, also included within the fabrication
`tools 108 is a fine nozzle 104 to deposit smaller amounts of
`material than the coarse nozzle. This permits detailing of an
`object created by the coarse nozzle 102 so that large features
`can be rapidly built with the coarse nozzle 102 and small
`features added with the fine nozzle 104. In one embodiment.
`fine nozzle 104 deposits material with granularity less than
`0.015 square inches per deposition. As used herein, a granu-
`larity of less than x meansa deposited spot occupies an area
`less than x. Also included within the fabrication tools 108, in
`one embodimentofthe invention, is a subtractive head 106.
`which can subtractivelydetail the object 114. In one embodi-
`ment, subtractive head 106 is a computer controlled milling
`bit. In some embodiments, performing the subtractive detail-
`ing before addition of a subsequent layer, access to detail
`desired features can be assured.
`In one embodimentofthe invention, a three dimensional
`scanner 130 is provided within the housing 100 to scan the
`object 114 during fabrication. This permits the fabrication
`processto be adjusted responsiveto identification ofvariance
`in the fabricated object 114 from the intended object as
`reflected in the digital model sourcing the data for the fabri-
`cation. In some embodiments, a scanner 130 mayuse laser
`ranging to create the three dimensional modelofthe work in
`process 114, Other scanning methods are also within the
`scope and contemplation ofthe invention.
`In some embodiments, the intermediate scanned model
`may be analyzed to determine whethercorrective measures
`may be deferred until later in the fabrication process where
`such deferral would improvetheefficiency ofthe fabrication.
`For example,ifdetailing with fine nozzle 104 may bedeferred
`because it will still be possible to create that detail at a later
`point, then the analysis from the intermediate scan may cause
`the deferral ofthat detailing. However, where that aspect may
`or will no longer be accessible after further fabricationsteps,
`the corrective action or detailing action must be taken before
`such subsequent fabrication actions obscure the area to be
`detailed.
`In some embodiments, such as shownin FIG.1. the fabri-
`cation tools 108 and scanner 130 remain fixed and the work
`surface 112 is movedto effect the relative motion between the
`point object and the tool 108 and scanner 130. In other
`embodiments, the tools 108 and scanning 130 move more
`while the target object remainsfixed. Additionally, while and
`embodiment with a coarse nozzle and a fine nozzle is
`
`described and shown, a system employing a range ofmultiple
`nozzles is within the contemplation of the invention.
`FIG. 2 is a schematic diagram of a control subsystem for
`one embodimentof the invention. A controller 200 interacts
`
`witha pluralityof drivers 208, a three dimensional scan head
`204, and monitoring software 202. Controller 200 uses a
`digital model of an object to be fabricated to instruct the
`drivers 208.
`
`20
`
`25
`
`30
`
`35
`
`40
`
`45
`
`50
`
`60
`
`65
`
`7
`
`
`
`US 9,156,204 B2
`
`3
`During fabrication controller 200 mayperiodically initiate
`ascan ofthe partial object using scan head 204, The resulting
`scan data may beprovided to the monitoring software module
`202, which may conduct an analysis. For example, monitor-
`ing software module 202 may perform comparisonofexisting
`source model relative to what has been built in the partial
`object. The comparison mayreflect a need to modify one or
`more aspects of the build, or do additional additive or sub-
`tractive detailing. An evaluation mayalso be undertakento
`determine whethersuch additional detailing maybe deferred.
`The deferral ofthe detailing should be undertaken where such
`deferral makes where such deferral makes the overall fabri-
`
`cation moreefficient. For example, where deferral of detail-
`ing reduces the number of movements the object must
`ndergo in the process. Deferral should generally not be
`ndertaken whenthereis no efficiency gain or where it mayor
`will not be possible to perform detailingat a later point during
`the process. Drivers 208 include servo driversto drive notions
`210, 212, 214, and 216 to drive therelative motion between
`he work surface (112 in FIG.1) andthe fabricationtools (108
`in FIG. 1). As shown, motor 210 controls x motor, motor 212
`controls y motion, motor 214 controls z motor and motor 216
`controls rotation. An additional driver drives motor 218,
`which controls the orientation and cross section ofthe coarse
`
`oot
`
`nozzle. Additionally drivers 208 to include drivers to drive
`fine head deposition 220 coarse deposition 222 and the mill
`motor 224.
`
`FIG. 3 is a flow diagram of operation according to one
`embodimentofthe invention. At block 302, the coarse nozzle
`is oriented for desired angular deposition relative to the
`underlying material. In some cases, the model nozzle may
`deposit perpendicularly achieving a flat deposition zone 302
`as shown in FIG.4. In othercases, the nozzle maybe oriented
`to deposit an angle6 relative to the perpendicular to achieve
`an angular deposition zone 404 in FIG. 4.
`At block 304, the systemdrives the coarse nozzle to deposit
`material in the orientation selected at block 302. At decision
`block 306, a determination is made whether a scan should be
`interleaved at this point in the fabrication process. If a scan
`shouldbeinterleaved the object is scanned at block 308 and
`the three dimensional model ofthe partial objectis created. At
`block 310, the scan ofthe partial object is analyzedrelativeto,
`for example, the model on which the fabrication is based to
`evaluate if changes should be madeto the fabrication process
`concurrently.
`For example, variations between the intended design
`reflected in the source model and what has actually been
`created maynecessitate additional detailing or changes in the
`calibration ofthe system. Additionally, determinationscan be
`made whetherdetailing can be deferredto the extent that such
`deferral will improve the efficiency ofthe fabrication process
`by, for example, reducing the numberof the relative move-
`mentof the fabrication headsandthe object.
`A determination is made at decision block 312 whether
`
`detailing is required. f detailing is required at decision block
`314, a determination is made whether to what extent the
`detailing can be deferred. If the detailing is required and
`cannotbe deferred, the object detailed with the fine resolution
`additive or subtractive head at block 316. If no detailing is
`required or after the detailing is complete at block 316, the
`decision is made at decision block 318 wherethe fabrication
`
`is complete. If the fabrication is not complete, the system
`returns for further deposition. Otherwisethe process ends.
`While embodiments ofthe invention are discussed above in
`
`the context of flow diagrams reflecting a particular linear
`order, this is for convenience only. In some cases, various
`operations may be performed in a different order than shown
`
`4
`or various operations may occur in parallel. It should also be
`recognized that some operations described with respect to
`one embodiment may be advantageously incorporated into
`another embodiment. Such incorporation is expressly con-
`templated.
`It should be appreciated that reference throughout this
`specification to “one embodiment” or “an embodiment”
`means that a particular feature, structure or characteristic
`described in connection with the embodimentis includedin at
`
`least one embodimentofthe present invention.Therefore,itis
`emphasized and should be appreciated that two or moreref-
`erences to “an embodiment” or “one embodiment” or “an
`
`alternative embodiment” in various portions of this specifi-
`cation are not necessarilyall referring to the same embodi-
`ment. Furthermore, the particular features, structures or char-
`acteristics may be combined as suitable in one or more
`embodiments ofthe invention.
`
`the invention has been
`In the foregoing specification,
`described with referenceto the specific embodimentsthereof.
`Tt will, however, be evident that various modifications and
`changes can be made thereto without departing from the
`broader spirit and scope of the invention asset forth in the
`appendedclaims. The specification and drawingsare, accord-
`ingly, to be regardedin an illustrative rather than a restrictive
`sense.
`Whatis claimedis:
`
`1. A three dimensional printing apparatus comprising:
`a structure defining a work area;
`an interface to receive digital data defining a geometryfor
`a three-dimensional object to be fabricated;
`at least two different additive nozzlesthat deposit different
`volumes ofmaterial per unit oftime at each nozzle’s spot
`of deposition, one nozzle depositing at least twice as
`muchastheother, the two nozzles including:
`a coarse additive nozzle that deposits a larger volume of
`material per unit of time within the workarea;
`a fine additive nozzle that deposits a smaller volume of
`material per unit of time at a spot within the work area;
`and
`a controller configured to select between the coarse addi-
`tive nozzle and the fine additive nozzle during a build
`process based onthedigital data defining the geometry,
`to cause large features internal to the three-dimensional
`object to be built with the coarse additive nozzle more
`rapidlythan is possible with the fine additive nozzle.
`2. The three dimensional printing apparatus of claim 1
`whereinthe fine additive nozzle comprises a nozzle having a
`spot deposit granularity less than 0.015 square inches at a
`point of deposition.
`3. The three dimensional printing apparatus of claim 1
`whereinthe coarse additive nozzle has a spot deposit granu-
`larity greater than 0.030 square inchesat a point ofdeposition.
`4. The three dimensional printing apparatus of claim 1
`further comprising:
`temperature control subsystemto actively cool a portion of
`the deposit of material more rapidly than an intrinsic
`cooling rate of the material.
`5. The three dimensional printing apparatus of claim 1
`further comprising:
`a three dimensional scanner coupled to the structure to
`capture three dimensional data about the three-dimen-
`sional object being fabricated; and
`a control subsystem that monitors scan head data and con-
`trols the coarse additive fine additive nozzles to adjust a
`fabrication process to improve at least one of the speed
`or accuracy of a fabrication of the three-dimensional
`object.
`
`
`
`20
`
`25
`
`30
`
`35
`
`40
`
`45
`
`50
`
`55
`
`60
`
`65
`
`8
`
`
`
`US 9,156,204 B2
`
`5
`6. A three dimensionalprinting apparatus comprising:
`a structure defining a work area;
`an interface to receive digital data defining a geometry for
`a three-dimensional object to be fabricated;
`a coarse nozzle to deposit material at a coarse granularity 5
`within the work area; and
`at least one of a fine granularity additive nozzle or a fine
`granularity subtractive headto detail the material depos-
`ited bythe coarse nozzle; and
`a control subsystem that includes a software module con-
`figured to determine whether access to detail will be
`possible after a subsequent layer of material is depos-
`ited, and whether the fabrication of the three-dimen-
`sional object will be moreefficient per unit oftime when
`the detailing is deferred to a point of later time in the 15
`fabrication.
`
`10
`
`7. The three dimensional printing apparatus of claim 6
`wherein the subtractive mechanism comprises:
`a computer-controlled milling bit.
`RR ROR
`
`20
`
`9
`
`
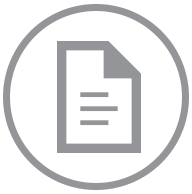
Accessing this document will incur an additional charge of $.
After purchase, you can access this document again without charge.
Accept $ ChargeStill Working On It
This document is taking longer than usual to download. This can happen if we need to contact the court directly to obtain the document and their servers are running slowly.
Give it another minute or two to complete, and then try the refresh button.
A few More Minutes ... Still Working
It can take up to 5 minutes for us to download a document if the court servers are running slowly.
Thank you for your continued patience.
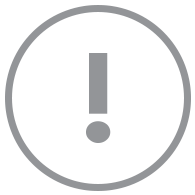
This document could not be displayed.
We could not find this document within its docket. Please go back to the docket page and check the link. If that does not work, go back to the docket and refresh it to pull the newest information.
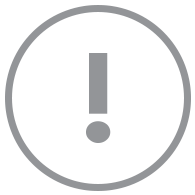
Your account does not support viewing this document.
You need a Paid Account to view this document. Click here to change your account type.
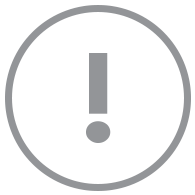
Your account does not support viewing this document.
Set your membership
status to view this document.
With a Docket Alarm membership, you'll
get a whole lot more, including:
- Up-to-date information for this case.
- Email alerts whenever there is an update.
- Full text search for other cases.
- Get email alerts whenever a new case matches your search.
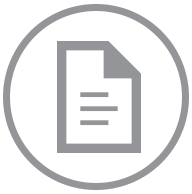
One Moment Please
The filing “” is large (MB) and is being downloaded.
Please refresh this page in a few minutes to see if the filing has been downloaded. The filing will also be emailed to you when the download completes.
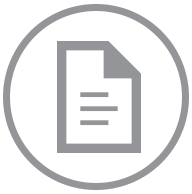
Your document is on its way!
If you do not receive the document in five minutes, contact support at support@docketalarm.com.
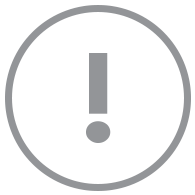
Sealed Document
We are unable to display this document, it may be under a court ordered seal.
If you have proper credentials to access the file, you may proceed directly to the court's system using your government issued username and password.
Access Government Site