`US 6,580,959 B1
`(10) Patent No.:
`Jun. 17, 2003
`(45) Date of Patent:
`Mazumder
`
`
`US006580959B 1
`
`(54) SYSTEM AND METHOD FOR REMOTE
`DIRECT MATERIAL DEPOSITION
`
`Jyoti Mazumder, Ann Arbor, MI (US)
`Inventor:
`(75)
`(73) Assignee: Precision Optical Manufacturing
`(POM), Plymouth, MI (US)
`
`(*) Notice:
`
`Subject to any disclaimer, the termofthis
`patent is extended or adjusted under 35
`US.C. 154(b) by 0 days.
`
`(21) Appl. No.: 09/575,857
`5
`Filed:
`
`May19, 2000
`
`(22)
`
`—
`Related U.S. Application Data
`(63) Continuation-in-part of application No. 09/522,671,filed on
`Mar. 10, 2000.
`(60)
`Provisional application No. 60/135,228, filed on May 21,
`1999, and provisional application No. 60/123,890,filed on
`Mar. 11, 1999.
`7,
`Int. Ch. cece seeseneeereneees GO06F 19/00
`9
`:
`.
`UWS. Ch eee 700/121; 700/166; 700/112
`Field of S
`h
`,
`700/121 166
`Field Ocriae.Tia.Ag.leo,en 119: 703/3.
`2
`206/46
`2
`2
`?
`?
`References Cited
`U.S. PATENT DOCUMENTS
`
`(51)
`(52)
`58)
`(58)
`
`(56)
`
`5,262,954 A
`* 11/1993 Fujino et al. oo... 700/112
`3/1994 Hutchins .......
`. 700/174
`5,291,416 A *
`
`6/1998 Meredith etal.
`... 118/665
`5,772,861 A *
`8/1998 Fiekiel ................0000008 702/122
`5,790,977 A
`
`
`
`3/1999 Moore oc. eee 345/835
`2/2000 Moukheibir
`.....
`33
`4/2000 Campbell etal. ...
`4/2000 Margery et al.
`............. 702/84
`
`5,877,961 A *
`6,021,404 A
`6,047,259 A
`6,055,487 A
`* cited by examiner
`.
`.
`.
`Primary Examiner—Leo Picard
`:
`Assistant Examiner—Kidest Bahta
`(74) Attorney, Agent, or Virm—Gifford, Krass, Groh,
`Sprinkle, Anderson & Citkowski, PC
`(57)
`ABSTRACT
`A system and method for remotely
`controlling the fabrica-
`y
`y
`iS
`tion of a product at a local manufacturing site. The product
`is fabricated by depositing successive material
`layers
`through a local
`laser-aided, feedback-controlled, direct
`material deposition system. The system is equipped with
`strain gages, optical sensors and acoustic sensors generating
`signals which are processed ina local computerto determine
`the temperature, strain and residual stress of the product
`during fabrication. A feedback controller interfaces with the
`local computer and with a numerical controller and operates
`to control the material deposition process. The local numeri-
`P
`Pp
`cal controller receives a file of a digitized description of the
`product from the remote computer, preferably via an Internet
`connection. The local computer sends temperature, strain
`and stress data to the remote computer, enabling a designer
`interfacing with the remote computer to monitor, control and
`modify the fabrication of the product in real time on line.
`The fabrication process is recorded by video or television
`camera and the shown in real-time on a screen display
`connected to the remote computer.
`
`21 Claims, 3 Drawing Sheets
`
`LOCALSITE
`
`205
`
`200
`
`
`REMOTESITE
`
` LAYER
`LASER-AIDED
`
`
`SUBSTRATE
`
`DMD SYSTEM
`
`
`
`
`
`COMPUTER
`
`
`
`
`
`
`
`
`
`
`
`FEEDBACK
`
`LOCAL
`CONTROLLER
`
`
`70
`
`
`
`
`
`1
`
`Shenzhen Tuozhu 1004
`
`1
`
`Shenzhen Tuozhu 1004
`
`
`
`U.S. Patent
`
`Jun. 17, 2003
`
`Sheet 1 of 3
`
`US 6,580,959 B1
`
`CadV-UASV'T
`
`
`
`WiALSASGING
`
`JNO
`
`MOVACAAA
`
`WATIOUWLINOO
`
`
`ALISTVOOT
`or|
`YVALAdIANOO
`TVIOOT
`UHAVT
`
`!ALVULSANSs
`
`
`
`ALISALOWWA
`
`00¢
`
`WVO/dVO
`
`ALOWRI|
`
`UTLAWO
`
`2
`
`
`
`
`
`
`
`
`U.S. Patent
`
`Jun. 17, 2003
`
`Sheet 2 of 3
`
`US 6,580,959 BL
`
`internet
`
`ETB
`|
`|
`
`| Decompression
`
`DMD
`System
`
`Compression and Encryption
`
`FIGURE 2
`
`3
`
`
`
`~ ©SS
`
`US 6,580,959 B1
`
`FIGURE3
`
`“a
`ws
`
`9 —
`
`U.S. Patent
`
`Jun. 17, 2003
`
`Sheet 3 of 3
`
`4
`
`
`
`US 6,580,959 B1
`
`1
`SYSTEM AND METHOD FOR REMOTE
`DIRECT MATERIAL DEPOSITION
`
`REFERENCE TO RELATED APPLICATIONS
`
`This application claimspriority of U.S. Provisional Patent
`Application Ser. No. 60/135,228, filed May 21, 1999, which
`is a continuation-in-part of U.S. Patent Application Ser. No.
`09/522,671, filed Mar. 10, 2000, which claims priority of
`U.S. provisional patent application Ser. No. 60/123,890,
`filed Mar. 11, 1999. The entire contents of these and the
`following U.S. Patent Applications are incorporated herein
`by reference: Ser. No. 09/107,912, filed Apr. 10, 1997; and
`Ser. No. 09/526,631, filed Mar. 16, 2000.
`
`FIELD OF THE INVENTION
`
`this invention relates to lascr-aided direct
`In general,
`material deposition processes and, more particularly, to a
`system and method of monitoring, controlling and modify-
`ing such processes, preferably in real time, from a remote
`location.
`
`BACKGROUND OF THE INVENTION
`
`Advances in modem telecommunication methods, includ-
`ing the Internet, as well as advances in data acquisition and
`manipulation, allow the transfer of large volumes of data
`between distant sites in a relatively short time. The use of
`web browsers enable users to view not only text, but also
`video, graphics and audio files.
`Large data files may be compressed before their transfer
`by a variety of methods to speed transmission time. Con-
`nections between sites may be effected by high-speed links
`in asynchronous transfer mode (ATM)or using Ethernet and
`Fast-Ethernet in a Local Access Network (LAN) or Wide
`Access Network (WAN) environment.
`Interactive image and data transmissionis currently under
`development for various applications including medical
`examination, diagnosis and treatment of disease, as
`described in U.S. Pat. No. 6,021,404 (Universal computer
`assisted diagnosis), U.S. Pat. No. 6,055,487 (Interactive
`remote sample analysis system) and U'S. Pat. No. 6,047,259
`(Interactive method and system for managing physical
`exams, diagnosis and treatment protocols in health care
`practice).
`Another remote control application is related to remote
`access and exchange of data between a remote host and an
`instrument, such as the vector modulation analyzer (WMA)
`with resident control and data acquisition software, as
`described in U.S. Pat. No. 5,790,977.
`The need remains, however, for a system and method
`enabling a design team at a remote site to monitor, control
`and modify the fabrication process of a product at a local
`manufacturing site. Such tele-control would be particularly
`advantageous when the manufacturing process involves
`specialized and delicately calibrated or expensive
`equipment, which is either too costly to duplicate at many
`plants or simply not available at the chosen or required site
`of production.
`SUMMARY OF THE INVENTION
`
`This invention utilizes advances in telecommunication
`and fast data transfer to control the fabrication of precisely
`dimensioned and intricatcly-detailed products through an
`automated, feedback-controlled, laser-aided direct material
`deposition (DMD) process, as described in co-owned and
`co-pending U.S. patent application Ser. No. 09/107,912,
`
`10
`
`5
`
`20
`
`30
`
`35
`
`45
`
`50
`
`55
`
`60
`
`65
`
`2
`filed Apr. 10, 1997, and in U.S. patent application Ser. No.
`09/522,671, filed Mar. 10, 2000.
`The geometry of the product is provided by a computer-
`aided design system (CAD). The deposition tool path is
`generated by a computer-aided manufacturing system
`(CAM) for CNC machining having post-processing soft-
`ware for deposition, instead of software for removal, as in
`conventional CNC machining. The CAM software inter-
`faces with a feedback controller. For in-situ control of the
`DMD manufacturing process,
`the computer holding the
`CAD/CAM software, the CNC and feedback controller and
`the laser equipmentare all located at the local manufacturing
`site.
`
`For remote control of the DMDprocess, a design team or
`an individual designer is located at the “remote” site and
`operates, through a user interface, their “remote” host com-
`puter. The remote computer stores the description of a
`product to be fabricated. The description is preferably pro-
`cessed by a commercial Computer-Aided Design and
`Computer-Aided Manufacturing (CAD/CAM) software
`package, also residing at the remote host computer. This
`software generates a CAM file from whichthe tool path file
`will be created.
`
`Because the CAM file of the product description is large,
`it is first compressed by an efficient compression algorithm
`to enable its fast transmission, e.g. over the Internet, to the
`manufacturing site. The remote host computer is preferably
`equipped with two monitors, one with a graphical user
`interface and the other for image and video observation of
`the laser-aided direct material deposition process. The dis-
`play preferably includes zoom androtation capabilities to
`enable detailed and accurate view from variousangles of the
`product undergoing fabrication.
`When the designer perceives a defect, an abnormality or
`some other undesirable characteristic affecting the final
`quality of the product, or whenit seemsdesirable to improve
`the design, the designer may pause or abort the fabrication
`process by sending a commandto the controller of the DMD
`system at
`the “local”, ie.
`the manufacturing, site. The
`designer then edits the CAD file and transmits over the
`Internet the modified and post-processed CAM file, either in
`its entirety, or only a block ofit containing the modification.
`Optical sensors at the manufacturing site continuously
`monitor the composition, temperature, and dimensions of
`the product. Acoustic emission sensors and strain gages at
`the manufacturing site monitor residual stress development
`in the product. Some or all of the information from the
`sensors is sent via a communications system to the remote
`computer at the designer site to determine the need for
`corrective measures. The signals from the sensors are also
`sent to the local computer control system at the manufac-
`turing site, where they are further processed to determine the
`independent parameters controlling the DMD process,e.g.
`the laser power, the beam diameter and the powderflowrate.
`The feedback controller uses this information to control the
`
`laser deposition process on command from the remote
`computer transmitted to the feedback controller through the
`local computer.
`BRIEF DESCRIPTION OF THE DRAWINGS
`
`FIG. 1 is a block diagram depicting important subsystems
`according, to the invention;
`FIG. 2 is a block diagram of information flow according
`to the invention with an emphasis on data type, sorting,
`compression and encryption; and
`FIG. 3 is an illustration of a NURBSinterpolation useful
`to the invention.
`
`5
`
`
`
`US 6,580,959 B1
`
`3
`DETAILED DESCRIPTION OF THE
`INVENTION
`
`FIG. 1 is a block diagram which shows important sub-
`systems according to the invention. A remote site 200
`communicates with a local site 205 via a communications
`
`system 75, preferably including the Internet. The design
`group and design equipment and software are located at the
`remote site 200, while the manufacturing team and manu-
`facturing equipment and software are locatedat the localsite
`205.
`
`The local site includes a laser-aided, computer-controlled
`direct material deposition system 10, which is used to
`fabricate, repair or modify three-dimensional products by
`applying sequentially layers of material 20 on a substrate 30.
`The laser-aided direct material deposition system (DMD) 10
`is equipped with a feedback controller 80 for monitoring and
`controlling the dimensions and overall geometry of the
`fabricated product. The feedback controller is connected
`with a computer numerical controller (CNC) 90 which
`guides the path of the laser beam incorporated in the DMD
`system 10. The details of the laser-aided, computer con-
`trolled direct material deposition system can be found in
`US. patent application Ser. No. 09/107,912 and are notall
`explicitly shown in FIG. 1.
`The manufacturing system at the local site includes a local
`computer 70 interfacing with the fecdback controller 80 and
`receiving input data from one or more sensors outputting
`information representative to fabrication progress. Such
`sensors may include strain gages 40, acoustic sensors 50,
`optical sensors 60 and video or television camera 65. One or
`more cameras may bespatially calibrated enabling dimen-
`sions to be remotely determined from the remote location.
`Contact and non-contact metrological instruments may also
`be used to perform accurate measurements to monitor the
`fabrication process. The local computer 70 communicates
`with a remote computer 95 via the communication system
`75 and receives the necessary computer files defining the
`deposition tool path for the numerical controller (CNC) 90.
`The remote site includes the remote computer 95, which
`receives input
`form a computer-aided design/computer-
`aided manufacturing (CAD/CAM) software program 105.
`The geometry of the product to be manufactured at the local
`site 205 is provided by a computer-aided design program
`(CAD)whichis part of CAD/CAM 105 software. The CAM
`part of the CAD/CAM 105software generates the deposition
`tool path. ‘lo accomplish this, the conventional CAM soft-
`ware is equipped with post-processing software for
`deposition, instead of post-processing software for removal,
`as is the case in conventional CNC machining. For in-situ
`DMD manufacturing, the CAM software interfaces directly
`with the feedback controller 80. For remote-control DMD
`
`manufacturing, the deposition tool-path files generated by
`the CAM software reside in the remote computer 95 and are
`sent via the communications system 75 to the local computer
`75 which interfaces with the feedback controller 80.
`
`FIG. 2 is a drawing which emphasizes type of data and
`information flow. CAD/CAM data and sensor updates are
`preferably delivered to a data sorter and from there, to a
`compression/encryption platform. The information is
`decompressed and applied to the DMD system, with updated
`sensor outputs and other data being preferably compressed
`and encrypted prior to being sent back to the remotesite.
`The factors that affect the dimensions of material depo-
`sition typically include laser power, beam diameter, tempo-
`ral and spatial distribution of the beam,interaction time, and
`powderflow rate. Adequate monitoring and control of laser
`
`4
`power, in particular, has a critical effect on the ability to
`fabricate completed parts and products with complex geo-
`metric features and within control tolerances. Accordingly,
`the feedback controller 80 of the direct material deposition
`system typically cooperates directly with the numerical
`controller (CNC) 90, which, itself, controls all functions of
`the direct material deposition system, including laser power.
`The laser source (not shown) of the DMD system is
`mounted above the substrate 30, and a layer of material 20
`is deposited according to the description of the product,
`whichis incorporated in the deposition tool path. The laser
`source has sufficient density to create a melt pool with the
`desired composition of substrate or previously deposited
`layer and cladding powder. The cladding powder, typically
`metallic, is sprayed on the substrate preferably through a
`laser spray nozzle with a concentric opening for the laser
`beam, as described in U.S. Pat. No. 4,724,299, so that the
`powderexits the nozzle coaxially with the beam.
`The numerical controller 90 preferably controls all oper-
`ating components of the DMD system of FIG. 1, including
`the operating conditions of the laser, receiving direction
`from the remote computer 95 through the communications
`system 75 and the local computer 70 for building the part or
`product. The commands received depend on the design
`(CAD)files of the product, which have beentranslated to
`deposition tool path files for deposition by the remote
`computer 95 before they were sent to the local computer.
`Thetool path files enable the numerical controller (CNC) 90
`to prescribe a path for the laser nozzle across the substrate
`for material deposition.
`The numerical controller 90 also receives feedback con-
`trol signals from the feedback controller 80 to adjust laser
`poweroutput, and further controls the relative position of the
`substrate and laser spray nozzle. All these functions are
`coordinated by the local computer 70, which sends feedback
`data to the remote computer 95 and receives instructions
`from the remote computer 95 to control
`the deposition
`process and,if necessary, to alter the entire laser source path
`or parts of it.
`For real-time, on-line control of the deposition process
`from the remotesite, it is important that fast communication
`connections are used. The tool path files, which are gener-
`ated by the CAM program in the remote computer 95, are
`preferably transferred in seconds, and on line editing is
`preferably done in milliseconds. The tool path files are
`typically files of the coordinates of many points along the
`tool path and,for a realistic part or product, have size of the
`order of 100 MB. This is because CAM software models
`
`into short chords (straight-line
`contours (curved lines)
`segments), sometimes shorter than 0.0001 inch.
`When a product demands precise contouring of intricate
`geometric features, many more and shorter chords are
`needed, and the tool path program becomes too long.
`Several commercial compression codes are available and
`can reduce the size of the files by compressing them before
`transmittal.
`In addition, some common sense rules and
`recent techniques have been developed to shortenthe size of
`the tool path files, especially for blocks of dense data near
`tightly curved geometric features. Such rules include:
`Eliminating non-essential characters, such as comments,
`especially since the design group at the remote com-
`puter will control the deposition process.
`Using the “tenths” rather than the decimal format, so that
`0.0003 is written as 3 in the language of the tool path
`code (G-code).
`Not repeating numerical control commands (G-code
`commands) on each line, since those commandsstay on
`until turned off.
`
`10
`
`5
`
`20
`
`30
`
`35
`
`40
`
`45
`
`50
`
`55
`
`65
`
`6
`
`
`
`US 6,580,959 B1
`
`5
`Recent techniques for reducing tool path file size include
`circular interpolation and NURBS. Circular interpolation
`simply fits circular arcs of various radii to the coordinate-
`point data. A substantial program-size reduction is achieved,
`because an arc can represent a larger portion of a curve than
`a straight-line segment with comparable accuracy. Tool path
`files that have been converted to circular are files are
`typically 60 to 90 percent smaller than the original point-
`to-point
`files, according to Tom Beard, “Machining in
`Circles”, published in Modern Machine Shop, July 1996. A
`commercial software code NWDesigns MetaCut has been
`developed by Northwood Designs, Inc., (Antwerp, N-Y.).
`NURBS(Non-Uniform Rational B-Splinc) is a type of
`curve interpolation that uses spline curves, which are much
`more versatile than circular arcs. Recent CAM software
`incorporates a NURBSspline command into the tool path
`file by a single G-code command “G6.2”. The result is a
`single line of tool path programming instead of a dense
`block of file for a complex, curving tool path. Norwood
`Designs, Inc., and Delcam International (Windsor, Ontario)
`offer CAM systems that produce NC tool paths incorporat-
`ing NURBSfrom CAD files. FIG. 3 shows the extent of a
`typical NURBSblock replacing the linearized segments 310
`of an original curved contour 300.
`To control the quality of the product, strain changes in the
`deposited layers are monitored through several sensor sys-
`tems during the deposition process. Returning to FIG. 1, a
`mechanical strain gage system 40 includes conventional
`high-temperature strain gages attached to the back surface of
`the substrate 30. The strain gages 40 measure strain in
`predetermined locations and directions,
`typically X, Y
`directions, along and across the deposition path. These gages
`are attached on the back of the substrate with high-
`temperature solder or other temperature-resistant means to
`avoid damage from laser heat or stray reflection from the
`laser beam.
`
`Additional, non-purely-mechanical, sensors systems are
`incorporated, preferably acoustic sensors 60 and optical
`sensors 50. The acoustic sensors operate on the principle that
`during material deposition strains and other physical
`changes, such as phase transformation changes, or crack/
`defect initiation produce sound waves which can be picked
`up by the acoustic sensors 60. ‘The acoustic sensors 60 are
`typically piezoelectric. Currently miniaturized acoustic sen-
`sors are used for micro electrical mechanical systems
`(MEMS). U.S. Pat. Nos. 4,783,821 and 4,816,125,
`for
`example, disclose a miniature diaphragm pressure trans-
`ducer.
`The acoustic sensors, whether miniaturized or not, are
`basically micro-microphones or microphones, respectively,
`which convert sound wavesto electrical signals. The optical
`sensors 50 include a variety of devices, such as those
`operating on photovoltaic, fiber optic, and interferometric
`principles. Using an optical detector and an interference
`measuring technique, small strains can be measured with
`high sensitivity. The acoustic sensors and optical sensors
`must be calibrated against independent (mechanical) strain-
`gage measurements. The acoustic sensors,
`in particular,
`require careful calibration to distinguish strain from other
`sources of acoustic emission from the product, such as crack
`initiation, defect formation, and phase transformation, dur-
`ing the fabrication of the product fabrication through laser-
`aided material deposition.
`The acoustic sensors 60, optical scnsors 50 and strain
`gages 40, send their strain measurements during the depo-
`sition process to the local computer 70 in the form of
`electrical signals. A rough estimate of stresses may be
`
`10
`
`5
`
`20
`
`30
`
`35
`
`40
`
`45
`
`50
`
`55
`
`60
`
`65
`
`6
`obtained through linear stress strain relations and elementary
`beam theory, but a complete residual stress history requires
`the incorporation of finite element codes, such as those
`commercially available for linear and nonlinear systems.
`The local computer 70 is programmed to offer both of these
`options: a rough calculation for experimental purposes dur-
`ing product design and development, and a full-fledged
`finite element analysis for more accurate prediction during
`actual production.
`The computer program comparesthe results of the stress-
`strain calculation with pre-determined failure criteria which
`incorporate a safety factor. The simplest criterion is to
`compare the maximum tensile stress with the yield stress
`and require the ratio not to exceed a given value. For ductile
`materials and multi-axial stresses, more sophisticated failure
`criteria may be incorporated in the stress analysis computer
`program, such as the von Mises or maximum strain energy
`criterion, or even crack initiation and propagation theories
`may be applied. Based on the results of the failure analysis,
`the local computer issues a warning/alarm signal for a
`humanoperatorat the local site, or sends an electronic signal
`to the remote computer for online control, or sends appro-
`priate commandsto a feedback controller 80, which inter-
`faces with the numerical controller 90.
`The numerical controller initiates corrective action, such
`as termination of the deposition process, adjustment of the
`deposition rate or laser power, and changes in the cooling
`conditions. ‘he data from the sensor systems 40, 50, 60 are
`processed by the local computer to produce real-time
`temperature, strain and stress data during the fabrication
`process. The sensor data are transmitted through the com-
`munications system 75 to the remote computer 95 for remote
`control of the process, or for modification of the product
`design, in its entirety or in part, and for replacement of the
`original CAM file with a new edited CAM file or CAM-file
`block to be transmitted back to the local computer 70.
`In addition to the sensor systems 40, 50, 60, a video or TV
`camera 65 records the laser-aided DMD process and trans-
`mits the images to the local computer 70, which then sends
`the images together with the associated temperature, strain
`and stress data to the remote computer 95 to be displayed
`preferably on a TV screen or shown on the remote computer
`monitor as streaming video (display screens not shownin
`FIG. 1).
`The temperature, strain and stress data, visual images or
`metrological information collected at the local manufactur-
`ing site 205 are all processed through the local computer 70,
`which communicates with the remote computer 95 and the
`numerical 70 and fecdback 80 controllers. All the data-
`
`processing is done locally at the manufacturing site 205 and
`only processed information of actual temperature, strain and
`stress, as well as physical dimensions, composition and
`appearance of the product
`is transmitted to the remote
`computer 95. Modification of CAD and CAM files, as well
`as generation and compression of the tool path files is done
`at the remote site 200 using the remote computer 95.
`In the preferred configuration, only the new or edited
`compressed tool path files are transmitted to the local
`computer 70. The reason for this is that, according to the
`invention, the control of the manufacturing process lies with
`the remote site 200 that houses the design team. If there is
`a need to transfer control to the local site 205, the CAD files
`are simply transmitted to the local computer 70, and a
`backup package, which is stored in the local computer and
`includes CAM software and post-processing software for
`generating tool path code, is used instead. This latter mode
`of operation is intermediate between in-situ and remote-
`control direct material deposition process.
`
`7
`
`
`
`US 6,580,959 B1
`
`7
`
`I claim:
`1. Aremote control manufacturing system, comprising:
`a remote computer system for generating and editing a
`design description of a product;
`a local manufacturing system for fabricating the product
`in accordance with the design description using a
`laser-aided direct material deposition (OMD) process
`interfaced to a numerical controller, the DMD process
`being characterized in that the laser is used to create a
`melt pool into which powder or other feed material is
`delivered to create three-dimensional objects; and
`a communicationslink facilitating the electronic transfer
`of design, manufacturing and control
`information
`between the remote computer system and the local
`manufacturing system,
`thereby enabling the remote
`computer to monitor, control and modify the fabrica-
`tion process at the local manufacturing system.
`2. The remote control manufacturing system of claim 1,
`wherein the manufacturing system interfaces with a feed-
`back controller.
`
`3. The remote control manufacturing system of claim 1,
`wherein the local manufacturing system includes one or
`more sensors to collect temperature, strain or stress data for
`transmission to the remote computer system.
`4. The remote control manufacturing system of claim 1,
`wherein the manufacturing information includes visual
`images of the product being fabricated.
`5. The remote control manufacturing system of claim 1,
`wherein the remote computer system includes software for
`generating a deposition tool path file from the description of
`the product.
`6. The remote control manufacturing system of claim 5,
`wherein the remote computer system includes software for
`minimizing the size of the deposition tool path file.
`7. The remote control manufacturing system of claim 1,
`wherein a uscr interfaces to the communications link
`
`through an Internet browser.
`8. A remote control manufacturing system, comprising:
`a laser-aided direct material deposition (DMD) system for
`fabricating a three-dimensional product by depositing
`successive material layers on a substrate, the material
`deposition system comprising:
`a plurality of sensors providing outputs;
`a local computer receiving and processing the sensor
`outputs to generate fabrication progress information;
`and
`
`a feedback controller interfaced to the local computer
`and a numerical controller, the feedback controller
`being operative to control the material deposition
`process; and
`a remote computer system, comprising:
`a computerized description of the product;
`a software package for creating a file of a deposition
`tool path for the fabrication of the product; and
`a communications system for sending the tool path file to
`and receiving the fabrication progress information from
`the local computer, so that the fabrication of the product
`can be monitored, controlled and modified from the
`remote computer system through the local computer in
`real time on line.
`
`10
`
`5
`
`20
`
`35
`
`40
`
`45
`
`50
`
`55
`
`60
`
`8
`9. The remote control manufacturing system of claim 8,
`wherein one of the sensors is an acoustic sensor.
`10. The remote control manufacturing system of claim 8,
`wherein one of the sensors is an optical sensor.
`11. The remote control manufacturing system of claim 8,
`wherein the fabrication progress information includes prod-
`uct temperature, stress or strain.
`12. The remote control manufacturing system of claim 8,
`wherein the fabrication progress information includes the
`height of the deposition layers.
`13. The remote control manufacturing system of claim 8,
`wherein the deposition tool path file is compressed to reduce
`its size at the remote computer system.
`14. The remote control manufacturing system of claim 8,
`further comprising a video or television camera recording
`the fabrication process and transmitting the images to be
`viewed on a screen display situated at the remote computer
`system.
`15. The remote control manufacturing system of claim8,
`wherein the communications system connecting the local
`and remote computers includes an Internet browser.
`16. A method associated with the remote-control fabrica-
`
`tion of a product, comprising the steps of:
`a) generating a file of a deposition tool path at a remote
`computer, and sending the file to a local computerat the
`manufacturing site;
`b) transferring the deposition tool path file to a numerical
`controller interfaced to a laser-aided, direct material
`deposition system to fabricate the product on a sub-
`strate by depositing successive layers having a height;
`c) collecting in the local computer real-time strain and
`temperature sensor data of the product during material
`deposition;
`d) sending the strain and temperature data to the remote
`computer via a communications system; and
`e) sending control commands from the remote computer
`to the local computer to control the material deposition
`process.
`17. The method of claim 16, further comprising the steps
`
`of:
`
`inputting the strain data into a finite-element program in
`the local computer to calculate residual stress data for
`the product; and
`sending the stress data to the remote computer via the
`communications system.
`18. The method of claim 16, wherein the file of the
`deposition tool path is compressed to reduceits size.
`19. The method of claim 16, wherein the direct material
`deposition system of step b) includes a feedback controller
`for controlling the height of each deposited layer.
`20. The method of claim 16, comprising the additional
`step of using a video or television camera to record the
`fabrication of the product and sending the images to a
`display connected to the remote computer.
`21. The method of claim 16, comprising the additional
`step of:
`editing the file of the deposition tool path in the remote
`computer and sending the edited file to the local
`computer.
`
`8
`
`
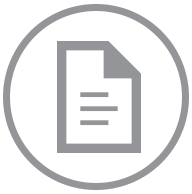
Accessing this document will incur an additional charge of $.
After purchase, you can access this document again without charge.
Accept $ ChargeStill Working On It
This document is taking longer than usual to download. This can happen if we need to contact the court directly to obtain the document and their servers are running slowly.
Give it another minute or two to complete, and then try the refresh button.
A few More Minutes ... Still Working
It can take up to 5 minutes for us to download a document if the court servers are running slowly.
Thank you for your continued patience.
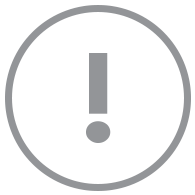
This document could not be displayed.
We could not find this document within its docket. Please go back to the docket page and check the link. If that does not work, go back to the docket and refresh it to pull the newest information.
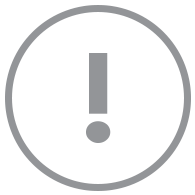
Your account does not support viewing this document.
You need a Paid Account to view this document. Click here to change your account type.
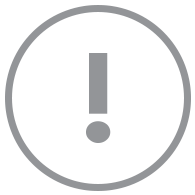
Your account does not support viewing this document.
Set your membership
status to view this document.
With a Docket Alarm membership, you'll
get a whole lot more, including:
- Up-to-date information for this case.
- Email alerts whenever there is an update.
- Full text search for other cases.
- Get email alerts whenever a new case matches your search.
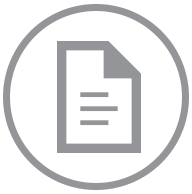
One Moment Please
The filing “” is large (MB) and is being downloaded.
Please refresh this page in a few minutes to see if the filing has been downloaded. The filing will also be emailed to you when the download completes.
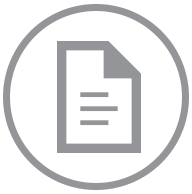
Your document is on its way!
If you do not receive the document in five minutes, contact support at support@docketalarm.com.
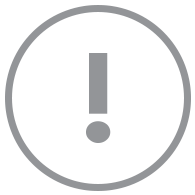
Sealed Document
We are unable to display this document, it may be under a court ordered seal.
If you have proper credentials to access the file, you may proceed directly to the court's system using your government issued username and password.
Access Government Site