`Liquid Cooled, Power Semi-Conductor Package
`
`Arthur H. Iversen
`Coriolis Corporation
`Campbell, California 95008
`
`and
`
`Stephen Whitaker
`Department of Chemical Engineering
`University of California
`Davis, California 95616
`
`Abstract - A new type of heat exchange process is described for use
`in semiconductor heat sinks. This involves the use of subcooled,
`nucleate boiling at concave curved surfaces where radial
`acceleration. v%, can be used to develop significant and beneficial
`buoyancy forces. This system provides a heat transfer surface with
`a uniform temperature, i.e.. the boiling point of the fluid, and
`requires no vapor-liquid separation process since all vapor bubbles
`are immediately condensed in the subcooled liquid. Use of low
`boiling point dielectric fluids, e.g. FC 72 (BP 56'C), establishes a
`uniform heat sink temperature that is independent of location or
`environment and does not require elaborate coolant and/or
`environmental conditioning. The low junction to fluid specific
`thermal resistance, 0jf-0.1' C/WcmZ, and high heat flux
`dissipation capability, -6,000 W/cm2, inherent in this design lends
`itself to a
`system design with high reliability and lower
`manufacturing costs. Failure rates are reduced and leakage currents
`are lowered by virtue of lower device operating temperatures, i.e.
`low boiling point coolants. Elimination of dry contacts and large
`mechanical forces, e.g. Disc Type Package, substantially reduces
`life shortening thermal stresses and lowers thermal resistance. The
`design lends itself to compact lightweight construction for high
`voltage series operation of devices and permits simplified parallel
`operation of high power devices.. Experimental studies at Coriolis
`Corporation have demonstrated a heat flux of 6300 watts/cm2 using
`FC77 with a pressure drop of only 2.70 pounds per square inch,
`over a one centimeter long heat transfer channel. In this paper we
`describe the design, construction, and operdtion of a liquid-cooled
`high power semi-conductor package and cooling technique for
`improved device reliability, simplified parallel operation of multiple
`devices, and efficient high voltage series construction.
`
`I. INTRODUCTION
`
`The performance of high power devices such as diodes,
`thyristors, GTO's, MOSFETS etc. is often limited by the heat
`removal capabilities of the thermal package. To achieve reasonable
`heat flux removal rates, device packages are often bulky and heavy,
`and this can complicate the packaging of these devices for series,
`parallel or series-parallel operation. For parallel operation, the need
`to maintain uniform junction temperatures is further complicated by
`those applications subject to surge-current overloads that can cause
`hot spots within a device.
`A common method for power device cooling is the use of high
`mechanical forces (up to 10 tons) to press the Disc Type package
`against the external heat sink which employs massive and bulky
`clamping springs and insulators. The sliding contacts resulting
`from this method have relatively high thermal resistance so the
`performance of the device in both steady state and surge is limited,
`and this construction additionally suffers from degradation of
`thermal fatique life (Glascock and Webster, 1983)[ 11.
`In this paper we propose a novel packaging and cooling scheme
`that addresses the shortcomings of conventional packaging and
`cooling techniques for high power devices, e.g. Disc Type Package.
`
`is pinned at the boiling temperature of the coolant thereby
`providing uniform device junction temperatures system wide,
`from cabinet to cabinet and room to mom;
`a) Simplifies parallel operation of devices.
`b) Thermal resistance change with transient or steady state
`operation should be minimal and confine substantially to
`that due to the silicon temperature rise by virtue of the
`elimination of mechanical pressure contacts and their
`associated degration of thermal fatigue life.
`c) Combined with (2) provides suppression of hot
`spots.
`d) Combined with (2) enables sustained surge current
`operation.
`4) Compact, light weight construction results from efficient
`heat transfer from the silicon chip substrate, e.g. negligible
`lateral heat transfer resulting in a heat transfer surface, i.e. the
`substrate, that is the same size as that of the chip. The dielectric
`coolant is an excellent insulator, e.g. 38 KV/O.l" for FC72 and
`therefore package size is principally dictated by external
`electrical breakdown characteristics of the housing. For
`example, 60 Thyristors (4500V/2000A) could be seriesed to
`provide 120KV/2000A.operation. It is estimated that package
`size might be about 3 0 long, 8" diameter and weigh about 50
`lbs. Curved surface cooling could increase device rating to
`8.009 A at the expense of the long term surge current safety
`margin.
`5 ) Cost effective design is provided on two levels; more
`efficient heat transfer permits higher device ratings, that is a
`53mm device can be substituted for a 77Mm or lOOmm device,
`e.g. a doubling or quadrupling of heat flux removal,
`alternatively or in combination, substantial perfomnce margin
`can be achieved to permit sustained operation under surge
`current conditions. Compact design reduces system space
`requirements and uniform junction temperatures simplifies
`fail-safe circuit design. Incorporating a large number of devices
`in a hermetically sealed housing eliminates the individual device
`packaging costs, e.g. ceramic housing and associated
`component and labor costs.
`
`11. CONSTRUCTION
`
`- HELIARC FLANQE
`
`,
`
`I
`
`I i
`
`A. Benefits Include;
`1) Operation of devices at higher ratings, e.g. substitution of
`53mm devices for 77mm or l0Omm devices with attendant cost
`savings.
`2) Longer device life by virtue of lower junction temperatures
`[24] and reduced leakage, as provided by low thermal
`resistance construction and low boiling point coolants.
`3) Improved system reliability as provided by subcooled
`nucleate boiling heat transfer wherein the heat exchange surface
`89<382792-0/89/0000-1340S01.00 0 1989 IEEE
`
`,- HELIARC FLAN=
`d
`
`Figure 1
`
`Authorized licensed use limited to: Robert Durham. Downloaded on November 08,2024 at 18:49:59 UTC from IEEE Xplore. Restrictions apply.
`
`LIBERTY EXHIBIT 1042, Page 1
`
`
`
`Figure 1 illustrates an insulating structure to house an assembly
`of power devices. The housing may be cast from a suitable epoxy
`such as is employed for HV insulators. Alternative insulating
`materials of construction include ceramic or glass. Flanges for
`heliarc welds are employed at both the positive and negative
`terminals to provide hermetic seals.
`
`/ HV ELECTRODE
`
`curved surface coolant channels. The coolant, being a dielectric,
`contributes to the electrical insulation of the package, e.g.
`38KV/O.1" for FC72 fluorocarbon. In addition to cooling the
`device, coolant channels may be provided to divert a predetermined
`coolant flow over the device electrical interconnects to remove
`resistive heat losses. For clarity of illustration of the curved surface
`cooling concept, single curved surface cooling is shown. For
`power devices of large dimensions, periodic curved surface cooling
`as described in U.S. Patent #4,712,609 [23] would be employed.
`
`m
`
`i
`
`+ ELECTRODE
`
`
`
`CHIP
`
`\- ELECTRODE
`
`FLOW DIVERTER
`
`SERIES CONNECTION
`
`QND ELECTRODE
`HELIARC FLANQE
`
`Figure 2 illustrates a preassembled stack of power devices
`shown for convenience as electrically connected in series.
`Alternative connections are parallel or a combination of
`series-parallel connections as might be employed for fail-safe
`ogartioa.
`
`Positive Terminal
`
`Housing
`
`Flow
`Diverter
`
`Curved
`Heat Transfer
`Substrate
`
`Chip
`
`Coolan i t Out/et
`
`,/'
`
`Coolant Inlet-
`Figure 3 illustrates an angled cross section view of the stack of
`power devices of Fig. 2 mounted in the housing of Fig. 1. Coolant
`flow is shown progressing up the input coolant conduit and then
`branching off at 90' to progressively feed, in parallel, each of the
`
`INPUT
`COOLANT
`CONDUIT
`
`Figure 4 illustrates a top-down, cross section view of the
`packaged devices to show input and discharge coolant channels and
`the method for alignment of the preassembled power device stack
`within the housing.
`b. Devicecooling
`Conventional high power device cooling, e.g. Disc Type
`Packages, are reputed to have maximum heat flux removal rates of
`about 150 W/cm2 and utilize massive and bulky clamping springs
`and insulators. Curved surface cooling has demonstrated 17
`KW/cm2 (Gambill 19 Greene, 1958)[2], 24 KW/ cm2 (Leslie et al
`1983)[3] and 6.3 KW/ cm2 (Iversen and Whitaker 1984)[4].
`Sub-cooled nucleate boiling heat transfer for flow over concave
`curved heat exchange surfaces offers substantial advantages.
`Curved surface sub-cooled nucleate boiling at the device heat
`exchange surface acts effectively as an infinite heat sink thereby
`maintaining a substantially constant heat sink temperature over a
`broad range of device heat fluxes from device to device and package
`to package independent of environment or location. Junction
`temperature is then the product of the heat flux and thermal
`resistance of a thin high thermal conductivity substrate, e.g.
`tungsten, plus the boiling point of the coolant, to which is added a
`superheat which depends upon the heat flux. Low boiling point
`fluorocarbon coolants, e.g. FC 87(32' C), or FC 72(56' C), enable
`high heat fluxes to be obtained while maintaining junction
`temperatures within acceptable limits. Thus, the heat transfer
`characteristics of the heat sink are no longer limited by mechanical
`contacts and thick heat sink members.
`Device junction-to-fluid thermal resistance, 06 is strongly
`influenced by the construction technique utilized. By employing
`diffusion bonded device construction, Glascock [ 11 demonstrated a
`substantial drop in junction -to -case thermal resistance, Ojc. over
`dry contact construction while still using Disc Type Package heat
`sinking. With liquid cooling, the dry sliding Disc Type Package
`heat sink contact is replaced with one of high compliance, negligible
`pressure and total contact for optimum performance. To simplify
`calculations and to provide a conservative design, the thermal
`resistance is calculated for single sided cooling. With double sided
`cooling. e.g. the use of structured copper, thermal resistance of
`about 60% of that for single sided cooling may be obtained. Using
`Nuegebauer's [13] junction to fluid specific thermal resistance Ojf of
`0.1' Wan* for bonded structures resulting in a thermal resistance
`of -0.002' W for a 77mm device and -.0012' c/w for a 100 mm
`device would provide a junction temperature rise AT of 15' C at the
`conventional maximum heat flux of 150 W/cm 2 . Using FC72 (BP
`56' C) as a coolant would result in a conservative junction
`temperature of 71' C (56' C + 15' C) plus superheat resulting in
`1341
`
`Authorized licensed use limited to: Robert Durham. Downloaded on November 08,2024 at 18:49:59 UTC from IEEE Xplore. Restrictions apply.
`
`LIBERTY EXHIBIT 1042, Page 2
`
`
`
`lower leakage currents and enhanced device life. With double sided
`cooling, the thermal resistance of the 77mm devices would reduce to
`about 0.0012' C/W, as contrasted to greater than 0.01' C/W for
`Digital Type Package construction. Thermal resistance change with
`transient or steady state operation should be minimal and confined
`substantially to that due to the silicon temperature rise by virtue of
`the elimination of mechanical pressure contacts. Direct liquid
`cooling eliminates Disc Type Package related thermal stress and
`associated device life degradation.
`B. Coolant ComDatibility
`
`With respect to coolant compatibility, the use of pure
`fluorocarbons, e.g. 3M, FC72 (BP 56' C) or FC87 (BP32.C)
`appears to present no difficulties for device cooling. In an ongoing
`experiment, 3M has been operating bare chip devices in FC72 for
`over 4 1/2 years with no difficulties[5]. The Cray 3 will employ 3M
`fluorocarbon bare chip cooling. Virtually all prior work reported
`with fluorocarbon cooling has been with the chloro-fluorocarbon
`R-113 (BP47.C). R113 has been reported as reactingwith
`aluminum, copper and other similar metals, Eriksson et a1[6]. The
`authors experience has been similar to the above with respect to
`copper and zinc in addition to experiencing corrosion of 400 series
`stainless steel. The pure fluorocarbons do not seem to present any
`difficulties for packaged or bare chip cooling nor do they appear to
`present a threat to the environment.
`C. Reliability
`A recent field study by the military provided a correlation
`between failure rate models and real life situations. From the data,
`device temperatures of 5@ 100' C are acceptable and 100-125'C are
`marginal [24]. Employing the temperature related failure rate table
`of Corman et al. [24] a comparison of relative failure rates for Disc
`Type Packages and curved surface cooling can be made. At a 110'C
`ju'nction temperature for Disc Type Packages, the failure rate would
`be 10 times higher for CMOS and 4 times higher for Bipolar as
`compared to a 71'C (FC72) junction temperature, i.e. 150 W/cm2,
`with curved surface cooling. At a 47'C (FC87) junction
`temperature, Disc Type Package failure rate would be 38 times
`higher for CMOS and 13 times higher for Bipolar as compared to
`curved surface cooling. At a junction temperature of 125'C, the Disc
`Type Package failure rate increases to 20X for CMOS and 6.4X for
`Bipolar over 71'C(FC72) curved surface cooling. Compared to
`47'C operation (FC87), it is 80X higher for CMOS and 20X for
`Bipolar. A further failure mode is caused by thermal stresses which
`arise from 1)the clamping forces employed in Disc Type Package
`heat sinking, and 2) the high temperature excursions that Disc Type
`Packages undergo. In the proposed design, (1 above) is eliminated
`and (2 above) is minimized.
`D. Extended Slarpe Current Tolerance
`By increasing the coolant velocity and using a lower boiling
`point coolant, e.g. FC87 (BP 32'C), high surge currents can be
`tolerated for extended periods. For example, using FC87 (BP
`32'C) and a 125'C max junction temperature, the permissible AT
`temperature rise is 93'C. Assuming 1O'C for super-heat. the
`junction to heat exchange surface AT is 83'C. Using the junction to
`heat exchange surface specific thermal resistance Ojc of 0.1 C.W
`cm2, the dissipated power is then 830 W/cm2, an almost 6X
`increase over the Disc Type package maximum heat flux of 150
`W/cm2. For a 77mm device, this corresponds to a continuous
`dissipation of 38KW. With double sided cooling, the overall
`specific thermal resistance would decrease to about 0.06' C/W cm2
`thereby increasing the power dissipation for a AT of 83'C to about
`1,380 W/cm2 resulting in a 9X increase in the continuous surge
`c m n t rating over standard operational ratings, e.g a 2,000A rated
`device (150 W/cmz dissipation) could be operated at a sustained
`surge cument of 18,000 A (1,3980 W/cm2 dissipation). It should be
`noted that the above value of 1.380 W/cm2 is well below the 6
`~ w / c m 2 demonstrated in the Iversen-Whitaker experimenti41..
`E. Subcooled Nucleate Bo iling
`The process of subcooled. nucleate boiling is an especially
`efficient means of heat removal. Nucleate boiling traditionally
`produces extremely high heat fluxes, and when the liquid is
`subcooled we have the advantage of a heat transfer system in which
`
`1 -
`
`only a single phase is present in the entrance and exit smams. In
`subcooled boiling. the vapor bubbles leave the heat transfer surface
`and then collapse in the liquid as illustrated in Figure 5.
`/ / " " " / / " " ~ ~ ~ ~ ~ ~ ' ~ ' ' ' '
`
`SUBCOOLED
`
`a
`
`Fig. 5 Bubble Generation and Collapse During Subcooled Boiling
`The high rates of heat transfer that occur during nucleate boiling
`are caused by the intense liquid motion that is generated by the
`growth and subsequent departure of the vapor bubbles from the heat
`transfer surface. These vapor bubbles, which generate the desired
`fluid motion, are also the source of the boiling crisis known as the
`critical heat flux or "burnout" condition. As the heat flux rises, the
`number of active nucleating sites (one of which is indicated in
`Figure 5 ) increases and the concentration of vapor bubbles in the
`neighborhood of the heat transfer surfaces increases. When
`sufficient bubble coalescence occurs, a stable vapor film develops
`and this usually leads to system failure. A high rate of vapor bubble
`removal from the heat trqnsfer surface is the key to an efficient heat
`transfer process, and there are two principal mechanisms which can
`be used to enhance the rate of removal of vapor bubbles: 1) the
`effect of shear and turbulent dispersion caused by a forced flow of
`liquid past the heat transfer surface, and 2) the effect of an increased
`body force caused by an acceleration of the liquid normal to the heat
`transfer surface. This increase in the body force can be generated by
`flow past a goncave surface.
`The effect of forced flow on the critical heat flux has been
`reviewed by Katto [21] for a wide variety of configurations. While
`the critical heat flux depends on the flow configuration and the
`nature of the heated surface, one can conclude that the critical heat
`flux is roughly proportional to the square root of the liquid velocity,
`i.e.,
`
`qc-vlR , forced flow
`(1)
`Clearly this is an approximation since experimental results can be
`found for which qc is proportional to vln and for which qc is
`proportional to vm. For our purposes the representation given by
`Equation 1 is very attractive since it nicely descriks the work of
`Gambill and Greene [2] and the follow-up study of Mayersak et a1
`[7]. The effect of shear flow on the boiling process is extremely
`complex and not yet completely understood. However, it is clear
`that a turbulent shear flow tends to break vapor bubbles away from
`the heat transfer surface and transport them into the surrounding
`liquid. This enhances the boiling process and gives rise to an
`increase in the critical heat flux as indicated by Equation 1. While
`the critical heat flux must be avoided in the operation of most
`systems, Equation 1 is still quite useful since it describes the effect
`of a shear flow.
`The influence of buoyancy effects on the nucleate boiling
`process is clearly evident in the process of "pool boiling" such as
`one observes when a pan of water is heated on a stove. In that case
`the buoyancy force, generated by the difference in the vapor and
`liquid densities and the gravitational force, causes the vapor bubbles
`to be propelled upwards away from the heat transfer surface As
`early as 1950 Kutateladze [8] was able to deduce that the critical heat
`flux during pool boiling was proportional to the fourth root of the
`acceleration normal to the heat transfer surface, i.e..
`qc - (a/g)I" , pool boiling
`is the standard
`Here a
`represents the acceleration and g
`gravitational acceleration, i.e., one "gee". Kutateladze's result was
`corroborated by the hydrodynamic stability analysis of Zuber [9]
`and confirmed by the experimental studies of Usisken and Siege1
`[ 10). The implications of Equation 2 for micro-gravity environments
`are obvious, and a survey of this general problem was presented by
`Siege1 [Ill in 1967.
`
`(2)
`
`1342
`
`Authorized licensed use limited to: Robert Durham. Downloaded on November 08,2024 at 18:49:59 UTC from IEEE Xplore. Restrictions apply.
`
`LIBERTY EXHIBIT 1042, Page 3
`
`
`
`F. Flow Past Curved Surfaces
`When a liquid flows past a concave surface at which nucleate boiling
`occurs, two flow phenomena influence the critical heat flux. First,
`the boiling process is enhanced because of the shear generated by
`the tangential fluid motion as illustrated in Figure 5 and suggested
`by Equation 1. In addition, the radial acceleration, a = v2/r, gives
`rise to a buoyance force which propels the vapor bubbles away from
`the heat transfer surface as illustrated in Figure 6.
`
`NUCLEATING SITE
`Figure 6 Bubble Generation and Collapse During Subcooled
`Boiling in a Curved Channel.
`This effect was first investigated by Gambill and Greene [2] who
`used a swirl flow to achieve a critical heat flux of 17 kw/cm2. This
`represented the highest known heat flux in 1958 and it clearly
`indicated that curved surface flow could be used to generate an
`exceptionally efficient boiling process. This exceptional efficiency
`results from the fact that the liquid velocity is used to generate a
`buoyance force that is normal to the heat transfer surface, whereas
`the drag force generated in linear flow is ginpent to the heat transfer
`surface. Thus, with curved surface flow the vapor bubbles are
`subject to a force which propels them directlv awav from the heat
`m s f e r surface and into the subcooled liquid where they collapse.
`The original discovery of Gambill and Greene [2] has been
`utilized by researchers at Hewlett-Packard Laboratories (Leslie et al
`[3]) to develop an enhanced brightness X-ray source. Using a
`cone-shaped anode with a concave radius of curvature of 2
`centimeters and a fluid velocity of 10,OOO cm/s, Leslie et a1 were
`able to obtain a heat flux of 25 kw/cm2. However, this was not a
`critical heat flux and they suggested that their curved surface device
`was capable of producing a heat flux two to three times larger than
`the measured value of 25 KW/cmz. In 1984, experiments were
`carried out by Iversen and Whitaker [4] using FC 77 as a coolant
`and a curved channel similar to that illustrated in Figure 6. With a
`radius of curvature of 2.5 centimeters and a velocity of 1340 cm/s
`(a/g = 726). a "near-bumout" heat flux of 6.3 kw/cm2 was obtained.
`On the basis of the studies of Gambill and Greene [2] and our
`own experimental work, we have developed an empirical equation
`for the critical heat flux for FC 77. This is given by
`
`(3)
`
`where qc is in kw/cm2, v is in cm/s, and the subcooling, ATsub, in
`'C. When the radial acceleration is negligible, Equation 3 reduces to
`the form given by Equation 1. When a/g is large compared to one,
`we have
`
`(4)
`and under these circumstances the critical heat flux becomes a linear
`function of the velocity
`
`qc - v, forced flow past a concave surface
`
`(5)
`A comparison of this result with Equation 1 clearly indicates a
`dramatic improvement in the efficiency of the boiling process. and
`this improvement is directly related to the radial acceleration that is
`generated by concave surfaces,
`While the heat fluxes reported by Gambill and Greene [2], Leslie
`et al[3], and Iversen and Whitaker [4] are much higher than those
`
`currently encountered in semiconductor cooling processes, the
`efficiency of curved surface nucleate boiling is not to be ignored. In
`the next section we indicate how this efficiency can be successfully
`Utilized.
`G. Semiconductor Cooling
`
`In Figure 3 we have shown a power semiconductor cooling
`configuration [12]. The semiconductor chips are bonded to the
`substrated heat sinks with each having its own curved heat transfer
`surface. Alternatively, structured cooper or a suitable silicon
`substrate could be employed. The substrate shown is molybdenum
`or tungsten which provides a low thermal resistance and a good
`match in terms of coefficients of thermal expansion. From Table III
`of Neugebauer et al [I31 we find the thermal resistance of the
`chip-solder- molybdenum assembly to be 0.1 IO'C/(W/cm2). As an
`example of the use of this type of system, we consider the following
`conditions.
`
`, radius of curvature = 3cm
`fluid = FC 77
`, hTsub - 70'c
`fluid velocity = 54 cm/s
`
`(6)
`
`For these conditions, which provide a/g = 1, we can use Equation 3
`to predict a critical heat flux of
`
`qc = 370 watts/cm2
`
`(7)
`
`If the heat flux at a semiconductor chip is 200 watts/cm2, one could
`expect to safely operate under the conditions represented by
`Equation 6. The corresponding critical heat flux for a linear flow
`system (a/g = 0) would be 185 watts/cm2 and such a system would
`burnout if the operating heat flux were 200 watts/cm2.
`The thickness of the flow channel illustrated in Figure 2 is a
`parameter in an optimization analysis; however, we have found that
`a channel depth on the order of 0.2 cm is generally acceptable. For
`this channel depth and a velocity of 54 cm/s, the pressure drop per
`centimeter of channel length is 0.004 psi when the channel is
`assumed to be hydraulically smooth. Under these circumstances a
`one meter long flow channel of the type illustrated in Figure 32 will
`give rise to a pressure drop on the order of one half pound per
`square inch. From these calculations we see that the pressure drop
`in the heat transfer channel is not a matter of serious concern. To
`emphasize this point, we remark again that experiments have been
`performed (Iversen and Whitaker [4]) in which a heat flux of 6300
`watts/cmz was obtained in a curved channel system for which the
`pressure drop was 2.70 psi per centimeter.
`As we mentioned earlier, it is the intense fluid motion generated
`by bubble growth and departure from the heat transfer surface that
`leads to the high heat fluxes associated with nucleate boiling. This
`intense fluid motion can also be obtained by the use of sufficiently
`high liquid velocities. A dramatic example of this is supplied by the
`work of Tuckerman [14] who used the classical method of extended
`surface heat transfer (Whitaker [ 151) to obtain a heat flux of 790
`watts/cmz using water in laminar flow. The absence of boiling
`would appear to give rise to a simpler heat transfer system;
`however, it leads to significant surface temperature gkdients in the
`direction of flow, high pressure drops, and relatively high
`In Table I we have shown the
`temperature driving forces.
`experimental result for water from Tuckerman's thesis [ 141, the
`conversion of these results to FC 77, and the results predicted by
`Equation 3. Both the surface temperam rise in the direction of
`flow and the pressure drop associated with Tuckerman's
`configuration indicate that laminar flow heat transfer is very
`inefficient compared to nucleate boiling at a curved surface. In
`calculating the Coriolis results listed in Table 1, we have used a
`radius of curvature of 3 cm, a liquid velocity of 143 c d s , and a
`subcooling of 70'C. While our experiments and calculations have
`been carried out with FC 77, we expect that semiconductor cooling
`would be carried out with FC 72 which boils at 56'C. At a heat flux
`of 200 watts/cm2 and a thermal resistance of 0.1 1o'C cmZ/watt, the
`temperature drop across the chip-solder-molybdenum assembly
`would be 22'C. If the steady-state superheat in the liquid were YC,
`If lower
`the maximum chip temperature would be 83'C.
`
`1343
`
`Authorized licensed use limited to: Robert Durham. Downloaded on November 08,2024 at 18:49:59 UTC from IEEE Xplore. Restrictions apply.
`
`LIBERTY EXHIBIT 1042, Page 4
`
`
`
`Table 1 Comparison Between Laminar Flow cooling and Nucleate Boiling at a Curved Surface w
`
`surface temperature change in the
`direction of flow per centimeter
`
`Tuckenn-
`Water
`22'c
`
`#
`FC 77
`49'c
`
`negligible
`
`108'C
`790 watts/cm2
`
`-10'c
`790 watts/cm2
`
`temperature driving force
`35'C
`heat flux
`790 watts/cm2
`pressure drop per centimeter
`22 psi
`temperatures are required one could use the flmrcarbon R11 which
`boils at 24' C or FC87 (32' C BP).
`Temmture Overshw
`
`36 psi
`0.022 psi
`When the temperature of the solid is increased, the pressure of the
`vapor will increase and the region occupied by the vapor will expand
`until the vapor-liquid interface reaches the position shown in Fig. 8.
`Under these circumstances, the effect of surface tension is reversed
`and the pressure of the vapor is given by
`
`The increase in the pressure of the vapor in going from the
`configuration shown in Fig. 7 to that shown in Fig. 8 is given by
`
`inagase in vapor pressure
`in site gorn
`
`the nuleation) to Be from temperature
`
`overshoot site
`
`20[&
`
`E
`
`+ k]
`
`(1 0)
`
`For most systems the superheat required to maintain steady
`nucleate boiling is on the order of 5-10' C; however, the gansient
`suDerheat or "temperature overshoot" may be considerably larger.
`This effect was apparently first observed by Cory and Foust [ 161 in
`a study of pool boiling using ether, normal pentane, and Freon 113.
`They observed temperature overshoots on the order of 10-15' C,
`and their results were comparable to those obtained by Bankoff et al.
`[ 171.using methanol. A detailed study of temperature overshoot was
`camed out by Bergles and Chu [ 181 for porous metallic surfaces,
`and they found that the temperature overshoot for Freon R-113 was
`about double that of water for pool boiling conditions. The
`maximum observed temperature overshoot for R-113 was about
`8' c.
`Bar-&hen and Simon [20] have pointed out that temperature
`overshoot can present a serious problem with the use of dielectric
`fluids such as FC77. Since the fluorocarbons characteristically have
`a low surface tension and contact angle they can penetrate deep into
`the pores and cavities that exist on any solid surface. In the absence
`of non-condensable gases, a re-entrant cavity must exist in order to
`produce a stable nucleating site. It seems clear that fluids with low
`surface tension and low contact angle will fill many potential
`nucleating sites, thus leaving only a small fraction of re-entrant
`cavities to provide nucleating sites. This situation is illustrated in
`Fig. 7 where we have shown a re-entrant cavity as a nucleation site.
`In the absence of non-condensable gases, the pressure of the vapor
`in the cavity can be expressed as
`
`Here Pvap represents the vapor pressure which can be determined as
`a function of the temperature by the Clausius-Clapeyron equation,
`Pliq represents a local ambient pressure in the liquid, and0 is the
`surface tension. The radius of curvature of the gas-liquid interface
`shown in Fig. 7 is designated by Rn, and it is important to note that
`the effect of surface tension is to reduce the pressure of the vapor in
`the cavity. It is this reduction of the pressure that generates a stable
`nucleating site.
`
`Pvap Pri-241 R"
`
`Fig. 7 Nucleating Site
`
`Fig. 8 Temperature Overshoot Site
`
`The temperature associated with this change in pressure will be
`described by the Clausius-Claypeyron equation, and if Ro is
`relatively small one can expect a large temperature overshoot. A
`further increase in the temperature will force the vapor-liquid
`interface beyond the constriction illustrated in Fig. 8 and the steady
`superheat condition shown in Fig. 9 will be achieved. Under these
`circumstances the pressure of the vapor will be given by;
`
`1344
`
`Authorized licensed use limited to: Robert Durham. Downloaded on November 08,2024 at 18:49:59 UTC from IEEE Xplore. Restrictions apply.
`
`LIBERTY EXHIBIT 1042, Page 5
`
`
`
`Fig. 9 Steady Superheat Site
`
`however, one must remember that the condition illustrated in Fig. 9
`is a dvnam ic condinon and the radius of curvature, Rs, should be
`thought of as some appropriate average value. An equation
`analogous to 4. 10 can be written as
`
`}
`
`in vapor pressure
`in going from the temperature
`overshoot site to the steady
`superheat site
`
`=
`
`4
`4
`
`-
`
`(' 2,
`
`force - pv2
`
`m
`
`loytr
`
`I
`
`bbyer
`
`Lomimr y b I o y J 1
`
`H i R q n d d s nu-
`M
`
`Fig. 10 Qualitative Description of Wall Effects in Turbulent Flow
`
` Dim region (Whitaker,
`This region of flow is known as the m h
`Sec. 8.2, 1191). On the basis of numerous experimental studies of
`flow in pipes the thickness of the laminar sublayer can be estimated
`by
`
`This result can be used to construct an estimate of the local velocity
`which is given by
`
`and a linearized version of the Clausius-Clapeyron equation can be
`used with this result to estimate the temperature overshoot as
`
`- (g), y
`
`6
`
`- v , y > 6
`
`"IOC
`
`Here y represents the distance measured from the mean radius
`illustrated in Fig. 4 and v represents the velocity in the turbulent
`core.
`It should be clear at this point that the cavik illustrated in Fig. 9
`is embedded in one of the roughnesses shown in Fig. 10. Because
`of the curved streamlines indicated in Fig. 9, the pressure in the
`liquid at the throat of the cavity is lowered by an amount which we
`estimate as
`
`{reduction} - Pvk h/r
`(18)
`Here h is the height of the protrusion illustrated in Fib. 9 and r is
`the radius of curvature of the streamlines over the protrusion. If we
`think of Eq. 9 as a static relation in which
`is determined by the
`geo
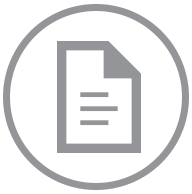
Accessing this document will incur an additional charge of $.
After purchase, you can access this document again without charge.
Accept $ ChargeStill Working On It
This document is taking longer than usual to download. This can happen if we need to contact the court directly to obtain the document and their servers are running slowly.
Give it another minute or two to complete, and then try the refresh button.
A few More Minutes ... Still Working
It can take up to 5 minutes for us to download a document if the court servers are running slowly.
Thank you for your continued patience.
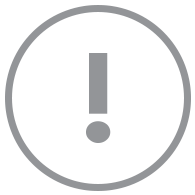
This document could not be displayed.
We could not find this document within its docket. Please go back to the docket page and check the link. If that does not work, go back to the docket and refresh it to pull the newest information.
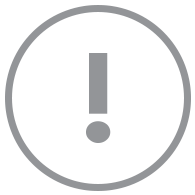
Your account does not support viewing this document.
You need a Paid Account to view this document. Click here to change your account type.
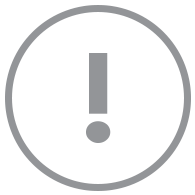
Your account does not support viewing this document.
Set your membership
status to view this document.
With a Docket Alarm membership, you'll
get a whole lot more, including:
- Up-to-date information for this case.
- Email alerts whenever there is an update.
- Full text search for other cases.
- Get email alerts whenever a new case matches your search.
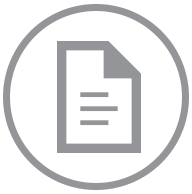
One Moment Please
The filing “” is large (MB) and is being downloaded.
Please refresh this page in a few minutes to see if the filing has been downloaded. The filing will also be emailed to you when the download completes.
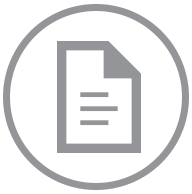
Your document is on its way!
If you do not receive the document in five minutes, contact support at support@docketalarm.com.
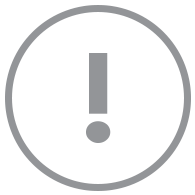
Sealed Document
We are unable to display this document, it may be under a court ordered seal.
If you have proper credentials to access the file, you may proceed directly to the court's system using your government issued username and password.
Access Government Site