`(12) Patent Application Publication (10) Pub. No.: US 2016/0273328A1
`Oehring
`(43) Pub. Date:
`Sep. 22, 2016
`
`US 20160273328A1
`
`(54)
`
`(71)
`
`(72)
`(21)
`(22)
`
`(63)
`
`(60)
`
`
`
`CABLE MANAGEMENT OF ELECTRIC
`POWERED HYDRAULCFRACTURING
`PUMP UNIT
`
`Applicant: US Well Services LLC, Houston, TX
`(US)
`Inventor: Jared Oehring, Houston, TX (US)
`Appl. No.: 15/145,491
`Filed:
`May 3, 2016
`
`Related U.S. Application Data
`Continuation-in-part of application No. 13/679,.689,
`filed on Nov. 16, 2012, now Pat. No. 9,410,410.
`Provisional application No. 62/156.303, filed on May
`3, 2015.
`
`Publication Classification
`
`(51) Int. Cl.
`E2IB 43/26
`(52) U.S. Cl.
`CPC ...................................... E2IB 43/26 (2013.01)
`
`(2006.01)
`
`ABSTRACT
`(57)
`A hydraulic fracturing system includes a pump, an electri
`cally powered motor for driving the pump, a trailer on which
`the pump and motor are mounted, and a transformer that steps
`down electricity for use by the motor. Electrical output from
`the transformer connects to a series of receptacles mounted
`onto a housing around the transformer. A similar set of recep
`tacles is provided on the trailer and which are electrically
`connected to the motor. Power cables equipped with plugs on
`their opposing ends insert into the receptacles to close an
`electrical circuit between the transformer and pump.
`
`-36A
`
`LIBERTY EXHIBIT 1012, Page 1
`
`
`
`Patent Application Publication
`
`Sep. 22, 2016 Sheet 1 of 8
`
`US 2016/0273328A1
`
`
`
`I ‘51-I
`
`LIBERTY EXHIBIT 1012, Page 2
`
`
`
`Patent Application Publication
`
`Sep. 22, 2016 Sheet 2 of 8
`
`US 2016/0273328A1
`
`
`
`s
`
`LIBERTY EXHIBIT 1012, Page 3
`
`
`
`Patent Application Publication
`
`Sep. 22, 2016 Sheet 3 of 8
`
`US 2016/0273328A1
`
`
`
`9 II
`
`LIBERTY EXHIBIT 1012, Page 4
`
`
`
`Patent Application Publication
`
`Sep. 22, 2016 Sheet 4 of 8
`
`US 2016/0273328A1
`
`
`
`LIBERTY EXHIBIT 1012, Page 5
`
`
`
`Patent Application Publication
`
`Sep. 22, 2016 Sheet 5 of 8
`
`US 2016/0273328A1
`
`
`
`LIBERTY EXHIBIT 1012, Page 6
`
`
`
`Patent Application Publication
`
`Sep. 22, 2016 Sheet 6 of 8
`
`US 2016/0273328A1
`
`
`
`LIBERTY EXHIBIT 1012, Page 7
`
`
`
`Patent Application Publication
`
`Sep. 22, 2016 Sheet 7 of 8
`
`US 2016/0273328A1
`
`
`
`LIBERTY EXHIBIT 1012, Page 8
`
`
`
`Patent Application Publication
`
`Sep. 22, 2016 Sheet 8 of 8
`
`US 2016/0273328A1
`
`
`
`112B1 112B 112B3
`
`() )
`() )
`2B 112Bs 12B
`
`118B1 118B2 118B3
`
`() is)
`) is
`
`118B4 118B 118B,
`
`Fig. 8
`
`LIBERTY EXHIBIT 1012, Page 9
`
`
`
`US 2016/0273328A1
`
`Sep. 22, 2016
`
`CABLE MANAGEMENT OF ELECTRIC
`POWERED HYDRAULCFRACTURING
`PUMP UNIT
`
`CROSS REFERENCE TO RELATED
`APPLICATIONS
`
`0001. This application is a continuation of, and claims
`priority to and the benefit of, co-pending U.S. Provisional
`Application Ser. No. 62/156.303, filed May 3, 2015 and is a
`continuation-in-part of, and claims priority to and the benefit
`of co-pending U.S. patent application Ser. No. 13/679,.689,
`filed Nov. 16, 2012, the full disclosures of which are hereby
`incorporated by reference herein for all purposes.
`
`BACKGROUND OF THE INVENTION
`
`0002 1. Field of Invention
`0003. The present disclosure relates to hydraulic fractur
`ing of subterranean formations. In particular, the present dis
`closure relates to electrical components and connections con
`nected to an electric hydraulic fracturing pump to minimize
`space and time requirements for rig up and rig down.
`0004 2. Description of Prior Art
`0005 Hydraulic fracturing is a technique used to stimulate
`production from Some hydrocarbon producing wells. The
`technique usually involves injecting fluid into a wellbore at a
`pressure sufficient to generate fissures in the formation Sur
`rounding the wellbore. Typically the pressurized fluid is
`injected into a portion of the wellbore that is pressure isolated
`from the remaining length of the wellbore so that fracturing is
`limited to a designated portion of the formation. The fractur
`ing fluid slurry, whose primary component is usually water,
`includes proppant (Such as sand or ceramic) that migrate into
`the fractures with the fracturing fluid slurry and remain to
`prop open the fractures after pressure is no longer applied to
`the wellbore. Other primary fluids sometimes used for the
`slurry include nitrogen, carbon dioxide, foam, diesel, or other
`fluids. A typical hydraulic fracturing fleet may include a data
`van unit, blender unit, hydration unit, chemical additive unit,
`hydraulic fracturing pump unit, sand equipment, electric
`wireline, and other equipment.
`0006 Traditionally, the fracturing fluid slurry has been
`pressurized on Surface by high pressure pumps powered by
`diesel engines. To produce the pressures required for hydrau
`lic fracturing, the pumps and associated engines have Sub
`stantial Volume and mass. Heavy duty trailers, skids, or trucks
`are required for transporting the large and heavy pumps and
`motors to sites where wellbores are being fractured. Each
`hydraulic fracturing pump usually includes power and fluid
`ends, as well as seats, valves, springs, and keepers internally.
`These parts allow the hydraulic fracturing pump to draw in
`low pressure fluid slurry (at approximately 100 psi) and dis
`charge the same fluid slurry at high pressures (up to 15,000 psi
`or more). Recently electrical motors have been introduced to
`replace the diesel motors, which greatly reduces the noise
`generated by the equipment during operation. After being
`transported to a wellsite electrically powered fracturing
`equipment, i.e. motors for pressurizing fracturing and
`hydraulic fluids, are connected to electrical power sources.
`Electrical connection for this equipment is time consuming,
`and the current electrical distribution configurations require
`numerous cables that occupy valuable space.
`
`SUMMARY OF THE INVENTION
`0007 Disclosed herein is an example of a hydraulic frac
`turing system for fracturing a Subterranean formation, and
`which includes first and second pumps, first and second
`motors for driving the first and second pumps, a transformer,
`a first electrical circuit between the first motor and the trans
`former, and through which the first motor and transformer are
`in electrical communication, and a second electrical circuit
`that is separate and isolated from the first electrical circuit,
`and that is between the second motor and the transformer, and
`through which the second motor and transformer are in elec
`trical communication. A cable assembly can be included
`which has an electrically conducting cable, a transformer end
`plug on one end of the cable and in electrical communication
`with the cable, and a motor end plug on an end of the cable
`distal from the transformer end plug and that is in electrical
`communication with the cable. A transformer receptacle can
`further be included that is in electrical communication with
`the transformer, and a motor receptacle in electrical commu
`nication with a one of the first or second motors, so that when
`the transformer end plug is inserted into the transformer
`receptacle, and the motor end plug is inserted into the motor
`receptacle, the transformer and a one of the first or second
`motors are in electrical communication, and wherein the
`plugs are selectively withdrawn from the receptacles. The
`hydraulic fracturing system can further include a multiplicity
`of cable assemblies, transformer receptacles, and motor
`receptacles, wherein three phase electricity is transferred
`between the transformer and the first or second motors in
`different cables. The receptacles can be strategically arranged
`so that cable assemblies that conduct electricity at the same
`phase are adjacent one another. A transformer ground recep
`tacle can further be included that is in electrical communica
`tion with a ground leg of the transformer, and a pump ground
`receptacle in electrical communication with a ground leg of
`one of the first or second pumps, so that when the transformer
`ground plug is inserted into the transformer ground recep
`tacle, and the pump ground plug is inserted into the pump
`receptacle, the transformer ground leg and the ground leg of
`one of the first or second pumps are in electrical communi
`cation, and wherein the plugs are selectively withdrawn from
`the receptacles. The hydraulic fracturing system can also
`include a platform on which the first and second pumps and
`motors are mounted, an enclosure on the platform, one or
`more variable frequency drives coupled with one or more of
`the motors and within the enclosure, and a removable panel
`on the enclosure adjacent the variable frequency drive, so that
`by removing the panel the variable frequency drive is easily
`accessible.
`0008 Another example of a hydraulic fracturing system
`for fracturing a subterranean formation includes a source of
`electricity, a row of Source receptacles that are in electrical
`communication with the source of electricity and configured
`so that some of the source receptacles receive electricity from
`the source of electricity at a phase that is different from a
`phase of electricity received by other source receptacles from
`the source of electricity, an electrically powered motor that is
`spaced apart from the source of electricity, a row of motor
`receptacles that are in electrical communication with the
`motor, and cable assemblies. The cable assemblies include a
`Source plug that is selectively insertable into a one of the
`Source receptacles, a motor plug that is selectively insertable
`into a one of the motor receptacles, and a cable in electrical
`communication with both the Source plug and motor plug, so
`
`LIBERTY EXHIBIT 1012, Page 10
`
`
`
`US 2016/0273328A1
`
`Sep. 22, 2016
`
`that when the Source plug inserts into a one of the Source
`receptacles, and the motor plug inserts into the a one of the
`motor receptacles, electricity at a designated phase is trans
`mitted from the source of electricity to the variable frequency
`drive to operate and control a motor. The source of electricity
`can be a transformer having alternating current electricity at
`three different phases. In an example, the motor is a first
`motor, the system further having a second motor, and wherein
`the first and second motors each drive fracturing pumps. In an
`embodiment, electricity conducts from the source of electric
`ity to the first motor along a first path, wherein electricity
`conducts from the source of electricity to the second motor
`along a second path, and wherein the first and second paths
`are separate and distinct from one another. In another embodi
`ment, electricity conducts from the Source of electricity to a
`single variable frequency drive which Supplies power to a
`single motor which turns more than one hydraulic fracturing
`pump. A first pair of the source receptacles can receive elec
`tricity at a first phase, so that a corresponding first pair of
`cable assemblies that have source plugs inserted into the
`Source receptacles conduct electricity at the first phase,
`wherein a second pair of the Source receptacles receive elec
`tricity at a second phase, so that a corresponding second pair
`of cable assemblies that have source plugs inserted into the
`Source receptacles conduct electricity at the second phase,
`and wherein a third pair of the source receptacles receive
`electricity at a third phase, so that a corresponding third pair
`of cable assemblies that have source plugs inserted into the
`source receptacles conduct electricity at the third phase.
`0009. A method of hydraulic fracturing is described herein
`and that includes electrically connecting a fracturing pump
`motor with a source of electricity by inserting a source end of
`a cable assembly into a source receptacle that is in electrical
`communication with the Source of electricity and inserting a
`motor end of the cable assembly, which is in electrical com
`munication with the source end of the cable assembly, into a
`motor receptacle that is in electrical communication with
`variable frequency drive, which is in electrical communica
`tion with the motor, which is in mechanical communication
`with the hydraulic fracturing pump that discharges high pres
`sure hydraulic fracturing fluid slurry to the wellbore. The
`Source of electricity transmits electricity to the Source recep
`tacle, so that electricity conducts from the source receptacle,
`to the motor receptacle, to the variable frequency drive, and to
`the motor. The source of electricity can be a transformer that
`transmits 3-phase electricity. In an embodiment, the fractur
`ing pump motor includes a first fracturing pump motor, and
`wherein the cable assembly comprises a first cable assembly,
`the method further comprising repeating the steps of electri
`cally connecting a fracturing pump motor with a source of
`electricity by inserting a source end of a cable assembly into
`a source receptacle that is in electrical communication with
`the source of electricity and inserting a motor end of the cable
`assembly, which is in electrical communication with the
`Source end of the cable assembly, into a motor receptacle that
`is in electrical communication with the fracturing pump
`motor, directing fracturing fluid to a Suction end of a fractur
`ing pump that is coupled with the fracturing pump motor, and
`causing the Source of electricity to transmit electricity to the
`Source receptacle, so that electricity conducts from the Source
`receptacle, to the Source and motor ends, to the motor recep
`tacle, and to the motor using a second fracturing pump motor
`and a second cable assembly. The method can also include
`removing the ends of the cable assembly from the receptacles,
`
`moving the Source of electricity and fracturing pump motor to
`a different location, and repeating the steps of electrically
`connecting a fracturing pump motor with a source of electric
`ity by inserting a source end of a cable assembly into a source
`receptacle that is in electrical communication with the Source
`of electricity and inserting a motor end of the cable assembly,
`which is in electrical communication with the source end of
`the cable assembly, into a motor receptacle that is in electrical
`communication with the fracturing pump motor, directing
`fracturing fluid to a Suction end of a fracturing pump that is
`coupled with the fracturing pump motor, and causing the
`Source of electricity to transmit electricity to the source recep
`tacle, so that electricity conducts from the source receptacle,
`to the source and motor ends, to the motor receptacle, and to
`the motor. The method can optionally further include repeat
`ing the step of electrically connecting a fracturing pump
`motor with a source of electricity by inserting a source end of
`a cable assembly into a source receptacle that is in electrical
`communication with the source of electricity and inserting a
`motor end of the cable assembly, which is in electrical com
`munication with the source end of the cable assembly, into a
`motor receptacle that is in electrical communication with the
`fracturing pump motor, so that multiple cable assemblies are
`connected between multiple source receptacles and multiple
`motor receptacles, so that electricity at different phases is
`conducted through the different cable assemblies to the frac
`turing pump motor. Optionally, a path of electricity between
`the Source of electricity and the first fracturing pump motor is
`separate and distinct from a path of electricity between the
`Source of electricity and the second fracturing pump motor.
`
`BRIEF DESCRIPTION OF DRAWINGS
`
`0010 Some of the features and benefits of the present
`invention having been stated, others will become apparent as
`the description proceeds when taken in conjunction with the
`accompanying drawings, in which:
`0011
`FIG. 1 is a schematic of an example of a hydraulic
`fracturing system.
`0012 FIG. 2 is schematic of an example of electrical com
`munication between a transformer and fracturing pump sys
`tem of the hydraulic fracturing system of FIG. 1.
`0013 FIG. 3 is an end perspective views of an example of
`a junction box on the transformer of FIG. 2.
`0014 FIG. 4 is an end perspective views of an example of
`a junction box on the fracturing pump system of FIG. 2.
`0015 FIG. 5 is a side perspective view of an example of a
`cable assembly for use in electrical communication between
`the transformer and fracturing pump system of FIG. 2.
`0016 FIG. 6 is a side perspective view of an example of
`the fracturing pump system of FIG. 2.
`0017 FIG. 7 is an end perspective view of the fracturing
`pump system of FIG. 6.
`0018 FIG. 8 is an end perspective view of an example of
`the transformer of FIG. 2.
`0019 While the invention will be described in connection
`with the preferred embodiments, it will be understood that it
`is not intended to limit the invention to that embodiment. On
`the contrary, it is intended to cover all alternatives, modifica
`tions, and equivalents, as may be included within the spirit
`and Scope of the invention as defined by the appended claims.
`
`LIBERTY EXHIBIT 1012, Page 11
`
`
`
`US 2016/0273328A1
`
`Sep. 22, 2016
`
`DETAILED DESCRIPTION OF INVENTION
`0020. The method and system of the present disclosure
`will now be described more fully hereinafter with reference to
`the accompanying drawings in which embodiments are
`shown. The method and system of the present disclosure may
`be in many different forms and should not be construed as
`limited to the illustrated embodiments set forth herein; rather,
`these embodiments are provided so that this disclosure will be
`thorough and complete, and will fully convey its scope to
`those skilled in the art. Like numbers refer to like elements
`throughout. In an embodiment, usage of the term “about
`includes +/-5% of the cited magnitude. In an embodiment,
`usage of the term “substantially includes +/-5% of the cited
`magnitude.
`0021. It is to be further understood that the scope of the
`present disclosure is not limited to the exact details of con
`struction, operation, exact materials, or embodiments shown
`and described, as modifications and equivalents will be appar
`ent to one skilled in the art. In the drawings and specification,
`there have been disclosed illustrative embodiments and,
`although specific terms are employed, they are used in a
`generic and descriptive sense only and not for the purpose of
`limitation.
`0022 FIG. 1 is a schematic example of a hydraulic frac
`turing system 10 that is used for pressurizing a wellbore 12 to
`create fractures 14 in a subterranean formation 16 that sur
`rounds the wellbore 12. Included with the system 10 is a
`hydration unit 18 that receives fluid from a fluid source 20 via
`line 22, and also selectively receives additives from an addi
`tive source 24 via line 26. Additive source 24 can be separate
`from the hydration unit 18 as a stand-alone unit, or can be
`included as part of the same unit as the hydration unit 18. The
`fluid, which in one example is water, is mixed inside of the
`hydration unit 18 with the additives. In an embodiment, the
`fluid and additives are mixed over a period of time to allow for
`uniform distribution of the additives within the fluid. In the
`example of FIG. 1, the fluid and additive mixture is trans
`ferred to a blender unit 28 via line 30. A proppant source 32
`contains proppant, which is delivered to the blender unit 28 as
`represented by line 34, where line 34 can be a conveyer. Inside
`the blender unit 28, the proppant and fluid/additive mixture
`are combined to form a fracturing slurry, which is then trans
`ferred to a fracturing pump system 36 via line 38; thus fluid in
`line 38 includes the discharge of blender unit 28 which is the
`suction (or boost) for the fracturing pump system36. Blender
`unit 28 can have an onboard chemical additive system, Such as
`with chemical pumps and augers (not shown). Optionally,
`additive source 24 can provide chemicals to blender unit 28:
`or a separate and standalone chemical additive system (not
`shown) can be provided for delivering chemicals to the
`blender unit 28. In an example, the pressure of the slurry in
`line 38 ranges from around 80 psi to around 100 psi. The
`pressure of the slurry can be increased up to around 15,000 psi
`by pump system 36. A motor 39, which connects to pump
`system 36 via connection 40, drives pump system 36 so that it
`can pressurize the slurry. In one example, the motor 39 is
`controlled by a variable frequency drive (“VFD). After being
`discharged from pump system 36, slurry is injected into a
`wellhead assembly 41; discharge piping 42 connects dis
`charge of pump system 36 with wellhead assembly 41 and
`provides a conduit for the slurry between the pump system 36
`and the wellhead assembly 41. In an alternative, hoses or
`other connections can be used to provide a conduit for the
`slurry between the pump system 36 and the wellhead assem
`
`bly 41. Optionally, any type of fluid can be pressurized by the
`fracturing pump system 36 to form a fracturing fluid that is
`then pumped into the wellbore 12 for fracturing the formation
`14, and is not limited to fluids having chemicals or proppant.
`Examples exist wherein the system 10 includes multiple
`pumps 36, and multiple motors 39 for driving the multiple
`pumps 36. Examples also exist wherein the system 10
`includes the ability to pump down equipment, instrumenta
`tion, or other retrievable items through the slurry into the
`wellbore.
`0023. An example of a turbine 44 is provided in the
`example of FIG. 1 and which receives a combustible fuel from
`a fuel source 46 via a feed line 48. In one example, the
`combustible fuel is natural gas, and the fuel source 46 can be
`a container of natural gas or a well (not shown) proximate the
`turbine 44. Combustion of the fuel in the turbine 44 in turn
`powers a generator 50 that produces electricity. Shaft 52
`connects generator 50 to turbine 44. The combination of the
`turbine 44, generator 50, and shaft 52 define a turbine gen
`erator 53. In another example, gearing can also be used to
`connect the turbine 44 and generator 50. An example of a
`micro-grid 54 is further illustrated in FIG. 1, and which dis
`tributes electricity generated by the turbine generator 53.
`Included with the micro-grid 54 is a transformer 56 for step
`ping down Voltage of the electricity generated by the genera
`tor 50 to a voltage more compatible for use by electrical
`powered devices in the hydraulic fracturing system 10. In
`another example, the power generated by the turbine genera
`tor and the power utilized by the electrical powered devices in
`the hydraulic fracturing system 10 are of the same Voltage,
`such as 4160 V so that main power transformers are not
`needed. In one embodiment, multiple 3500 kVA dry cast coil
`transformers are utilized. Electricity generated in generator
`50 is conveyed to transformer 56 via line 58. In one example,
`transformer 56 steps the voltage down from 13.8 kV to around
`600 V. Other example step down voltages include 4,160 V.
`480 V, or other voltages. The output or low voltage side of the
`transformer 56 connects to a power bus 60, lines 62, 64, 66.
`68.70, and 72 connect to power bus 60 and deliver electricity
`to electrically powered end users in the system 10. More
`specifically, line 62 connects fluid source 20 to bus 60, line 64
`connects additive source 24 to bus 60, line 66 connects hydra
`tion unit 18 to bus 60, line 68 connects proppant source 32 to
`bus 60, line 70 connects blender unit 28 to bus 60, and line 72
`connects motor 39 to bus 60. In an example, additive source
`24 contains ten or more chemical pumps for Supplementing
`the existing chemical pumps on the hydration unit 18 and
`blender unit 28. Chemicals from the additive source 24 can be
`delivered via lines 26 to either the hydration unit 18 and/or the
`blender unit 28. In one embodiment, the elements of the
`system 10 are mobile and can be readily transported to a
`wellsite adjacent the wellbore 12, such as on trailers or other
`platforms equipped with wheels or tracks.
`0024 Schematically illustrated in FIG. 2 is one example of
`a fracturing pump system 36A having pumps 80, 82 that are
`respectively powered by motors 84, 86. Couplings 88, 90
`mechanically affix the pumps 80, 82 with motors 84, 86 so
`that when motors 84, 86 are energized, the motors 84, 86 will
`drive pumps 80, 82 for pressurizing fracturing fluid that is
`then delivered to the wellbore 12 (FIG.1). In this example, the
`fracturing pump system 36A is mounted on a trailer 92 which
`provides a mobile Surface for transporting components of the
`fracturing pump system 36A to and from designated loca
`tions. Thus when operations at a wellsite are deemed com
`
`LIBERTY EXHIBIT 1012, Page 12
`
`
`
`US 2016/0273328A1
`
`Sep. 22, 2016
`
`plete, the fracturing pump system 36A can be transported to
`another wellsite for subsequent operations, or to a facility for
`repair or maintenance. Also schematically represented on
`trailer 92 and as part of the fracturing pump system 36A, are
`a motor control center 94 and auxiliary components 96.
`Examples of auxiliaries include heaters for the motors 84, 86,
`lights on the fracturing pump system 36A, control power for
`a variable frequency drive (not shown), heater for lube oil for
`pumps 80, 82, air blowers (not shown) for motors 84, 86, a
`hydraulic pump motor, and a hydraulic cooler motor (not
`shown). Not shown are variable frequency drives to control
`and operate motors 84, 86. In another embodiment, a single
`variable frequency drive controls and operates a single motor
`84 which turns one or more hydraulic fracturing pumps (80
`and 82).
`0025. Also shown in FIG. 2 is an example of transformer
`56A having a high voltage side HV connected to line 58A:
`junction boxes 98, 100 respectively mounted on transformer
`56A and fracturing pump system 36A provide means for
`electrical communication between transformer 56A and frac
`turing pump system 36A. Junction box 98 is mounted on a
`low voltage side LV of the transformer 56A. As will be
`described in more detail below, junction boxes 98, 100 are
`equipped with quick disconnect receptacles so that lines hav
`ing conductive wires and that conduct electricity between
`transformer 56A and fracturing pump system 36A, can be
`easily inserted and removed by operations personnel to sig
`nificantly reduce the time required for assembly and disas
`sembly of the hydraulic fracturing system 10. The electrically
`conducting lines between junction boxes 98,100 include wire
`bundles 102, 104, which as will be described below each
`include a number of wires within and that are separable and
`distinct from one another. Wire bundles 102, 104 conduct
`electrical power from transformer 56A and to junction box
`100 and which is used for energizing motors 84, 86. Also
`extending between junction boxes 98, 100 is line 106 and
`which conducts electricity that is used for powering the motor
`control center 94 and auxiliary components 96. Also extend
`ing between junction boxes 98, 100 is line 108 which is used
`as a ground between the transformer 56A and the hydraulic
`fracturing pump unit 36A. In one embodiment, the power
`generated is of the same Voltage as the power Supplied to the
`hydraulic fracturing pump unit 36. In this case, power for the
`hydraulic fracturing pump unit 36 is supplied directly without
`needing a transformer 56.
`0026 FIG.3 shows an end perspective view of an example
`of junction box 98 and having a row 110 of receptacles 112
`112. The receptacles 112-112 are each equipped with an
`opening 114-114 in which an electrical conducting plug can
`be readily inserted and removed thereby providing electrical
`communication between the plug and attached conducting
`lead (such as a cable). Set below and extending generally
`parallel with row 110 is row 116 which also includes recep
`tacles 118-118, wherein the receptacles 118-118 are each
`equipped with openings 120-120 for receiving an electri
`cally conducting plug. Set adjacent receptacle 112 is a
`ground connection 122 which connects to ground leads
`within transformer 36A (FIG. 2). Below ground connection
`122 is an auxiliary/MCC connection 124, which provides a
`source of electrical power for the auxiliary components 96
`and motor control center 94 (FIG. 2). In another embodiment,
`the receptacles can be arranged in different patterns and con
`figurations.
`
`0027 FIG. 4 shows an end perspective view of one
`example of junction box 100 which includes a row 126 of
`receptacles 128-128, wherein the receptacles each have an
`opening 130-130 on their ends distal from where they
`mount to junction box 100. Parallel with and set below row
`126 is row 132, which is made up of a line of receptacles
`134-134 each having openings 136-136. Also included
`with receptacle 100 is a ground connection 138 and an aux
`iliary/MCC connection 140. In another embodiment, the
`receptacles can be arranged in different patterns and configu
`rations.
`0028 FIG. 5 shows in a side perspective view one example
`of a cable assembly 142 which includes plugs 144, 146 and a
`cable 148 extending between the plugs 144, 146 which pro
`vides electrical communication between plugs 144, 146.
`Plugs 144, 146 as shown each have an outer periphery con
`figured so that plugs 144, 146 can be readily inserted into and
`removed from openings 114-114, 120-120, 130-130
`136-136. Optionally included with the plugs 144, 146 are
`electrodes 149 which are electrically conductive elements.
`Electrodes 149 are shown formed along the outer curved
`Surface of plugs 144, 146 and can be recessed or inlayed on
`the surface of the plugs 144, 146 or can project radially
`outward. Alternate examples of electrodes 149A resemble
`planar prongs that projectaxially outward from the respective
`ends of plugs 144, 146 opposite from their connection to
`cable 148. When the plugs 144, 146 are inserted into a one of
`the receptacles 112-112, 118-118, 128-128, 134-134
`of FIG.3 or 4, the electrodes 149, 149A come into electrically
`conducting contact with corresponding electrodes (not
`shown) provided within the receptacles 112-112, 118
`118, 128-128, 134-134; and thereby providing electrical
`communication one of the receptacles 112-112, 118-118
`disposed injunction box 98 and one of the receptacles 128
`128, 134-134 disposed injunction box 100.
`(0029 Referring back to FIG. 2, line 150 is shown within
`fracturing pump system 36A and extending from a side of
`junction box 100 opposite from cable bundle 102 and con
`necting to motor 86. Accordingly, electrical communication
`between transformer 56 and motor 86 takes place from junc
`tion box 98, through cable bundle 102, to junction box 100,
`then to line 150. Although shown as a single line, line 150 can
`be made up of a plurality of electrically conducting elements
`Such as lines or cables and may include a variable frequency
`drive. One specific example of forming cable bundle 102, six
`of the cable assemblies 142 are provided, and one of plugs
`144, 146 are inserted into each of the openings 114-114 of
`receptacles 112-112. The other one of the plugs 144, 146 of
`cable assemblies 142 is then inserted into a corresponding
`opening 130-130 of receptacles 128-128. Thus in one
`example the six cable assemblies 142 extending between the
`receptacles 112-112 to receptacles 128-128 define cable
`bundle 102 for powering motor 86. An advantage of the cable
`assemblies 142 with insertable and removable plugs 144, 146
`and receptacles 112-112 and receptables 128-128 is that
`the electrical communication between transformer 56A and
`motor 86 can be assembled in a matter of minutes, versus the
`hours that has typically been required for hardwiring the
`electrical connection between the transformer 56A and motor
`86. Similarly, cable bundle 104 is formed by providing six of
`the cable assemblies 142 and connecting them with the plugs
`144, 146 into the receptacles 118-118 and receptacles 134
`134. In similar fashion, a ground connection 108 between
`transformer 56A and fracturing pump system 36A is created
`
`LIBERTY EXHIBIT 1012, Page 13
`
`
`
`US 2016/0273328A1
`
`Sep. 22, 2016
`
`by providing cable assembly 142 and inserting one of plugs
`144, 146 into ground connection 122 and the other one of the
`plugs 144, 146 into ground connection 138. Optionally,
`simple bolton lugattachments (not shown) can be used in lieu
`of the cable assemblies 142 for the ground connections 122,
`138. Thus, while cable bundles 102, 104 each include six or
`more of the cable assemblies 142, example lines 106, 108 can
`include a single cable assembly 142. Alternatively, line 106
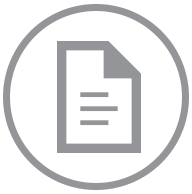
Accessing this document will incur an additional charge of $.
After purchase, you can access this document again without charge.
Accept $ ChargeStill Working On It
This document is taking longer than usual to download. This can happen if we need to contact the court directly to obtain the document and their servers are running slowly.
Give it another minute or two to complete, and then try the refresh button.
A few More Minutes ... Still Working
It can take up to 5 minutes for us to download a document if the court servers are running slowly.
Thank you for your continued patience.
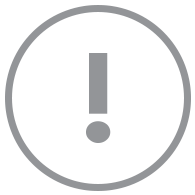
This document could not be displayed.
We could not find this document within its docket. Please go back to the docket page and check the link. If that does not work, go back to the docket and refresh it to pull the newest information.
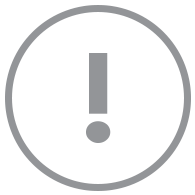
Your account does not support viewing this document.
You need a Paid Account to view this document. Click here to change your account type.
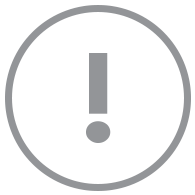
Your account does not support viewing this document.
Set your membership
status to view this document.
With a Docket Alarm membership, you'll
get a whole lot more, including:
- Up-to-date information for this case.
- Email alerts whenever there is an update.
- Full text search for other cases.
- Get email alerts whenever a new case matches your search.
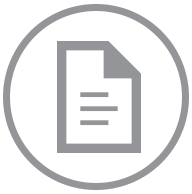
One Moment Please
The filing “” is large (MB) and is being downloaded.
Please refresh this page in a few minutes to see if the filing has been downloaded. The filing will also be emailed to you when the download completes.
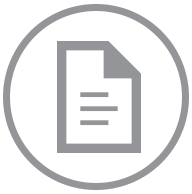
Your document is on its way!
If you do not receive the document in five minutes, contact support at support@docketalarm.com.
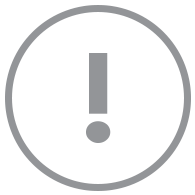
Sealed Document
We are unable to display this document, it may be under a court ordered seal.
If you have proper credentials to access the file, you may proceed directly to the court's system using your government issued username and password.
Access Government Site