`
`(10) International Publication Number
`WO 2018/201118 Al
`
`> a
`
`WIPOIPCT
`
`(19) World Intellectual Property
`Organization
`International Bureau
`
`(43) International Publication Date
`01 November 2018 (01.11.2018)
`
`(51) International Patent Classification:
`£21B 41/00 (2006.01)
`HO02P 27/04 (2006.01)
`HO02K 5/18 (2006.01)
`
`(for FR only): SERVICES PETROLIERS
`(71) Applicant
`SCHLUMBERGER[FR/FR]; 42 rue Saint Dominique,
`75007 Paris (FR).
`
`(21) International Application Number:
`
`PCT/US2018/030080
`
`(22) InternationalFiling Date:
`
`30 April 2018 (30.04.2018)
`.
`English
`English
`
`.
`ere
`(25) Filing Language:
`(26) Publication Language:
`(30) Priority Data:
`62/491,689
`28 April 2017 (28.04.2017)
`US
`(71) Applicant (for US only): SCHLUMBERGER TECH-
`NOLOGY CORPORATION[US/US]; 300 Schlumberg-
`er Drive, Sugar Land, Texas 77478 (US).
`
`(71) Applicant (for CA only): SCHLUMBERGER CANADA
`LIMITED [CA/CA]; 125 — 9 AvenueSE,Calgary, Alberta
`T2G OP6 (CA).
`
`(71) Applicant (for all designated States except CA, FR, US):
`SCHLUMBERGER TECHNOLOGY B.V.
`[NL/NL];
`Parkstraat 83, 2514 JG The Hague (NL).
`(72) Inventors: ORBAN, Jacques; 4601 Westway Park Dri-
`ve, W123, Houston, Texas 77041 (US). PRISER, Jean-
`Christophe; 23400 Colonial Parkway, Katy, Texas 77493
`(US). KRIPPNER, Nick; 9510 North Houston Rosslyn
`Rd., Houston,
`T
`77088 (US).
`7
`POUSTONS
`TEXAS
`(US)
`(74) Agent: GREENE, Rachel et al.; Schlumberger, 10001
`Rich:
`dA
`R
`4720, Houst
`T
`77042
`(Us). rerees OUSTONSEES
`‘
`(81) Designated States (unless otherwise indicated, for every
`kind of national protection available): AE, AG, AL, AM,
`AO, AT, AU, AZ, BA, BB, BG, BH, BN, BR, BW,BY, BZ,
`CA, CH, CL, CN, CO, CR, CU, CZ, DE, DJ, DK, DM, DO,
`DZ, EC, EE, EG, ES, FI, GB, GD, GE, GH, GM, GT, HN,
`HR, HU,ID,IL, IN, IR, IS, JO, JP, KE, KG, KH, KN, KP,
`KR, KW, KZ, LA, LC, LK, LR, LS, LU, LY, MA, MD, ME,
`
`(54) Title: INTEGRATED POWER AND ELECTRONICS UNIT FOR DRILLING MACHINE
`
`50
`
`FIG. 1
`
`
`
`(57) Abstract: An integrated powerand electronics unit (IPEU) operable for providing output powerfor driving an electric motor of a
`drilling rig machine. The IPEU comprises a housing,a radiator, and a VFD. Theradiator is mounted within the housing and comprises
`radiating members each extending through an opening in the housing. The VFD comprises insulated-gate bipolar transistor devices
`(IGBTs) operable to convert input powerto the output power. The IGBTsare coupled to the radiator within the housing such that heat
`generated by the IGBTsis transferred out of the housing via the radiator. The VFD also comprises a controller operable to control
`the IGBTs.
`
`[Continued on next page]
`LIBERTY EXHIBIT 1010, Page 1
`
`
`
`
`
`wo2018/201118AaMITINMITUIINIATATAUACTTACTA
`
`LIBERTY EXHIBIT 1010, Page 1
`
`
`
`WO 2018/201118 A|IMMMNMTMNIINIIMIAT IU TMT ATTAAATA
`
`MG, MK, MN, MW, MX, MY, MZ, NA, NG,NI, NO, NZ,
`OM,PA, PE, PG, PH, PL, PT, QA, RO, RS, RU, RW,SA,
`SC, SD, SE, SG, SK, SL, SM,ST, SV, SY, TH,TJ, TM, TN,
`TR,TT, TZ, UA, UG, US, UZ, VC, VN, ZA, ZM, ZW.
`
`(84) Designated States (unless otherwise indicated, for every
`kind of regional protection available): ARIPO (BW, GH,
`GM,KE, LR, LS, MW, MZ, NA, RW, SD,SL, ST, SZ, TZ,
`UG, ZM, ZW), Eurasian (AM, AZ, BY, KG, KZ, RU,TJ,
`TM), European (AL, AT, BE, BG, CH, CY, CZ, DE, DK,
`EE, ES, FI, FR, GB, GR, HR, HU,IE,IS, IT, LT, LU, LV,
`MC, MK, MT, NL, NO, PL, PT, RO, RS, SE, SI, SK, SM,
`TR), OAPI (BF, BJ, CF, CG, CI, CM, GA, GN, GQ, GW,
`KM,ML, MR, NE, SN, TD, TG).
`
`Published:
`
`with international search report (Art. 21(3))
`
`LIBERTY EXHIBIT 1010, Page 2
`
`LIBERTY EXHIBIT 1010, Page 2
`
`
`
`WO 2018/201118
`
`PCT/US2018/030080
`
`Integrated Powerand Electronics Unit for Drilling Machine
`
`Cross-Reference to Related Applications
`
`[0001]
`
`This application claims priority to and the benefit of U.S. Provisional Application No.
`
`62/491,689, titled “Integrated Power and Electronics Unit for Drilling Machine,”filed April 28,
`
`2017, the entire disclosure of which is hereby incorporated herein by reference.
`
`Backgroundof the Disclosure
`
`[0002]
`
`On an alternating-current (AC) drilling rig, an AC generator set generates the
`
`electrical power used to operate the heavy rig equipment, such as the top drive, the mud pump,
`
`and the drawworks. The AC generator set includes an AC generator poweredby a diesel engine
`
`or other prime mover. The resulting AC currentis utilized by a variable-frequency drive (VFD)
`
`associated with the rig equipment component, such that the top drive, mud pump, and drawworks
`
`may each have a dedicated VFD.
`
`[0003]
`
`The VFDs maybeinstalled in an access-controlled room, knownas a power house, a
`
`power-control room (PCR), a local electronics room (LER), and the like. While the VFDsare
`
`primarily utilized to power the main rig machines (the top drive, the mud pump, and the
`
`drawworks), smaller motors installed on or otherwise associated with the main machines (and/or
`
`perhaps other “non-main” rig equipment) may be also operated from the power house, such as
`
`cooling fans, centrifugal pumps (such as for feeding mud pumps), lubrication systems, and other
`
`examples.
`
`Summaryof the Disclosure
`
`[0004]
`
`This summary is provided to introduce a selection of concepts that are further
`
`described below in the detailed description. This summaryis not intendedto identify
`
`indispensable features of the claimed subject matter, noris it intended for use as an aid in
`
`limiting the scope of the claimed subject matter.
`
`[0005]
`
`The present disclosure introduces an apparatus including an IPEU operable for
`
`providing output powerfor driving an electric motor of a drilling rig machine. The IPEU
`
`includes a housing, a radiator, and a VFD. The radiator is mounted within the housing and
`
`includes radiating members each extending through an openingin the housing. The VFD
`
`includes insulated-gate bipolar transistor (IGBT) devices operable to convert input powerto the
`
`LIBERTY EXHIBIT 1010, Page 3
`
`LIBERTY EXHIBIT 1010, Page 3
`
`
`
`WO 2018/201118
`
`PCT/US2018/030080
`
`output power. The IGBTsare coupled to the radiator within the housing such that heat generated
`
`by the IGBTsis transferred out of the housing via the radiator. The VFD also includes a
`
`controller operable to control the IGBTs.
`
`[0006]
`
`The present disclosure also introduces an apparatus includinga drilling rig machine
`
`and an IPEU operable for providing output powerfor driving an electric motorof the drilling rig
`
`machine. The IPEU includes a housing,a radiator, anda VFD. Theradiator is mounted within
`
`the housing and includes radiating members each extending through an opening in the housing.
`
`The VFDincludes IGBTs operable to convert input power to the output power. The IGBTsare
`
`coupled to the radiator within the housing such that heat generated by the IGBTsis transferred
`
`out of the housing via the radiator. The VFD also includes a controller operable to control the
`
`IGBTs.
`
`[0007]
`
`These and additional aspects of the present disclosure are set forth in the description
`
`that follows, and/or may be learned by a person having ordinary skill in the art by reading the
`
`material herein and/or practicing the principles described herein. At least some aspects of the
`
`present disclosure may be achieved via meansrecited in the attached claims.
`
`Brief Description of the Drawings
`
`[0008]
`
`The present disclosure 1s understood from the following detailed description when
`
`read with the accompanyingfigures. It 1s emphasized that, in accordance with the standard
`
`practice in the industry, various features are not drawn to scale. In fact, the dimensions of the
`
`various features may be arbitrarily increased or reducedfor clarity of discussion.
`
`[0009]
`
`FIG. 1 is aschematic view ofat least a portion of an example implementation of
`
`apparatus according to one or moreaspects of the present disclosure.
`
`[0010]
`
`[0011]
`
`FIG. 2 is a graph depicting one or more aspects pertaining to the present disclosure.
`
`FIG. 3 is a schematic viewofat least a portion of an example implementation of
`
`apparatus according to one or moreaspects of the present disclosure.
`
`[0012]
`
`FIG.4 is a perspective view ofat least a portion of an example implementation of
`
`apparatus according to one or moreaspects of the present disclosure.
`
`[0013]
`
`FIG.5 is a front view ofat least a portion of an example implementation of the
`
`apparatus shown in FIG.4 according to one or more aspects of the present disclosure.
`
`[0014]
`
`FIG.6 is a top view ofat least a portion of an example implementation of the
`
`apparatus shownin FIG. 5 according to one or more aspects of the present disclosure.
`
`LIBERTY EXHIBIT 1010, Page 4
`
`LIBERTY EXHIBIT 1010, Page 4
`
`
`
`WO 2018/201118
`
`PCT/US2018/030080
`
`[0015]
`
`FIG.7 is a perspective view ofat least a portion of another example implementation
`
`of the apparatus shownin FIG. 4 according to one or more aspects of the present disclosure.
`
`[0016]
`
`FIG.8 is a top view of a portion of the apparatus shownin FIG. 7 according to one or
`
`more aspects of the present disclosure.
`
`[0017]
`
`FIG. 9 is a schematic view ofat least a portion of an example implementation of
`
`apparatus according to one or moreaspects of the present disclosure.
`
`[0018]
`
`FIG. 10 is a top view of a portion of an example implementation of the apparatus
`
`shown in FIG. 9 according to one or more aspects of the present disclosure.
`
`[0019]
`
`FIG. 11 is a schematic view ofat least a portion of another example implementation
`
`of the apparatus shown in FIG. 9 according to one or more aspects of the present disclosure.
`
`[0020]
`
`FIG. 12 is a schematic view ofat least a portion of an example implementation of
`
`apparatus according to one or moreaspects of the present disclosure.
`
`[0021]
`
`[0022]
`
`FIG. 13 is a sectional view of the apparatus shown in FIG. 12.
`
`FIG. 14 is a schematic view ofat least a portion of an example implementation of
`
`apparatus according to one or moreaspects of the present disclosure.
`
`[0023]
`
`FIG. 15 is a schematic view ofat least a portion of an example implementation of
`
`apparatus according to one or moreaspects of the present disclosure.
`
`[0024]
`
`FIG. 16 is a schematic view ofat least a portion of an example implementation of
`
`apparatus according to one or moreaspects of the present disclosure.
`
`[0025]
`
`FIG. 17 is a schematic view ofat least a portion of an example implementation of
`
`apparatus according to one or more aspects of the present disclosure.
`
`[0026]
`
`FIG. 18 is a schematic view ofat least a portion of an example implementation of
`
`apparatus according to one or moreaspects of the present disclosure.
`
`[0027]
`
`FIG. 19 is a schematic view ofat least a portion of an example implementation of
`
`apparatus according to one or moreaspects of the present disclosure.
`
`[0028]
`
`FIG. 20 is a schematic view ofat least a portion of an example implementation of
`
`apparatus according to one or moreaspects of the present disclosure.
`
`[0029]
`
`FIG.21 is a schematic view ofat least a portion of an example implementation of
`
`apparatus according to one or moreaspects of the present disclosure.
`
`LIBERTY EXHIBIT 1010, Page 5
`
`LIBERTY EXHIBIT 1010, Page 5
`
`
`
`WO 2018/201118
`
`PCT/US2018/030080
`
`Detailed Description
`
`[0030]
`
`It is to be understood that the following disclosure provides many different
`
`embodiments, or examples, for implementing different features of various embodiments.
`
`Specific examples of components and arrangements are described below to simplify the present
`
`disclosure. These are, of course, merely examples and are not intended to be limiting. In
`
`addition, the present disclosure may repeat reference numerals and/orletters in the various
`
`examples. This repetition is for simplicity and clarity, and doesnotin itself dictate a relationship
`
`between the various embodiments and/or configurations discussed.
`
`[0031]
`
`FIG. 1 is a schematic view of an example implementation of a VFD 50 for driving an
`
`induction motor within the scope of the present disclosure. The VFD 50 includesa rectifier
`
`circuit 10, an inverter circuit 20, and perhapsa filter circuit 30.
`
`[0032]
`
`Therectifier circuit 10 rectifies three-phase input power (VacI) from three inputs 11,
`
`12, 13 (measurable via, for example, respective current probes and/or other measurement means
`
`14, 15, 16) to generate DC power(e.g., with limited undulation). In the example implementation
`
`depicted in FIG. 1, each input 11, 12, 13 is connected between an anodeof a correspondingfirst
`
`diode 17 and a cathodeof a corresponding second diode 18. The cathodesofthe first diodes 17
`
`are connected to a positive lead 31 of the filter circuit 30, and the anodes of the second diodes 18
`
`connected to a negative lead 32 of thefilter circuit 30.
`
`[0033]
`
`Thefilter circuit 30 may be or comprise an LC (inductor-capacitor) circuit and/or
`
`other means for reducing noise generated bytherectifier circuit 10, thus smoothing the direct
`
`current voltage (Vdc) fed to the inverter circuit 20. In the example implementation depicted in
`
`FIG.1, the filter circuit 30 includes an inductor (e.g., solenoid) 33 connected in series between
`
`the positive lead 31 of the filter circuit 30 and a positive lead 21 of the inverter circuit 20, and a
`
`capacitor 34 connected between the positive and negative leads 31, 32 of the filter circuit 30.
`
`However, other implementations of the filter circuit 30 are also within the scope ofthe present
`
`disclosure.
`
`[0034]
`
`The inverter circuit 20 produces, for delivery to inputs 27, 28, 29 of the motor 40, the
`
`three-phase output VacO (measurable via, for example, respective current probes and/or other
`
`measurement means41, 42, 43) at the frequency and amplitude intended to drive the motor 40.
`
`In the example implementation depicted in FIG. 1, the inverter circuit 20 includes three single-
`
`phase inverter switches 23, 24, 25 that each includefirst and second inverters 26. The inverters
`
`26 are depicted in FIG. | as simpletransistor switches, but various other devices maybe utilized
`
`LIBERTY EXHIBIT 1010, Page 6
`
`LIBERTY EXHIBIT 1010, Page 6
`
`
`
`WO 2018/201118
`
`PCT/US2018/030080
`
`for the inverters 26, including IGBT devices. The motor input 27 is connected betweenthefirst
`
`and secondinverters 26 of the switch 23, the motor input 28 1s connected betweenthefirst and
`
`second inverters 26 of the switch 24, and the motor input 29 is connected betweenthefirst and
`
`second inverters 26 of the switch 25. However, other implementations of the inverter circuit 20
`
`are also within the scopeof the present disclosure.
`
`[0035]
`
`The VacO generated by the inverter circuit 20 may range between about 5 Hertz (Hz)
`
`and about 100 Hz, although perhapsas high as 300 Hz. The measurement means 14-16
`
`associated with the inputs 11-13, the measurement means 41-43 associated with the motor inputs
`
`27-29, and perhaps one or moreothersensors (e.g., sensor 50 connected between the filter circuit
`
`30 and the inverter circuit 20) are examples of sensors that may be utilized to monitor and
`
`perhaps provide automatic or manual feedback for operation of the motor 40. These and/or other
`
`current, voltage, and/or frequency sensors (or other measurement means) mayaid in managing
`
`the VFD 50 and other powerelectronics in relation with demand.
`
`[0036]
`
`FIG. 2 depicts an example pulse-width modulation (PWM)60 that may be used to
`
`provide the three-phase output VacO at the intended frequency and amplitudeto drive the motor
`
`40 at a target speed. The driving signal intended to be delivered to the motor input 27 is
`
`represented by sine wave 61, and is generated by the PWM signal 62 via operation of the switch
`
`23. Similarly, the driving signal intendedto be delivered to the motor input 28 is represented by
`
`sine wave 63, which is generated by the PWM signal 64 via operation of the switch 24, and the
`
`driving signal intendedto be delivered to the motor input 29 is represented by sine wave 65,
`
`whichis generated by the PWM signal 66 via operation of the switch 25. Each intended driving
`
`signal 61, 63, 65 is compared with a reference triangle wave and/or other waveform 67. When
`
`the reference waveform 671s less than the intended driving signal 61, 63, 65, the corresponding
`
`PWM signal 62, 64, 66 is at “high”state (e.g., 1), and when the reference waveform 67 is greater
`
`than the intended driving signal 61, 63, 65, the corresponding PWM signal 62, 64, 66 is at “low”
`
`state (e.g., 0).
`
`[0037]
`
`The present disclosure introduces an integrated power andelectronics unit (IPEU)
`
`that is integrated in a drilling rig machine skid, such as a mud pumpskid, a drawworksskid, and
`
`others. The IPEU alonedelivers the electrical and control support for the equipment on that skid.
`
`For example, the IPEU includes a VFD for the main motorof the primary machineofthe skid
`
`(e.g., mud pump, drawworks,top drive, efc.), a controller, and a networkinginterface. The IPEU
`
`may also include a VFD andstarter(s) for one or more motors of secondary machines/functions,
`
`LIBERTY EXHIBIT 1010, Page 7
`
`LIBERTY EXHIBIT 1010, Page 7
`
`
`
`WO 2018/201118
`
`PCT/US2018/030080
`
`such as cooling blowers, centrifugal pumps, lubricating pumps, and other examples. The IPEU
`
`may also include meansfor data acquisition, such as from sensors associated with equipment on
`
`the skid, from equipmentnot integrated in the skid (such as the main controller of the drilling ng
`
`via the networking interface), and/or from mobile electronic devices (e.g., tablet computers,
`
`smartphones, laptop computers, efc.) proximate the IPEU. The IPEU mayalso include
`
`emergency stop meansfor abruptly halting operation of one or more components of the skid.
`
`[0038]
`
`The IPEU receives electrical power from a powersourceat the wellsite via a power
`
`cable. Information exchanged between the IPEU and equipmentnot integrated in the skid (both
`
`to and from the IPEU) may bevia a cable and/or wireless communication. The IPEU mayalso
`
`share information for coordination between multiple machines on the skid, such as in
`
`implementations in which the mud pumpsystem includes multiple pumpsthat, via the
`
`information sharing, operate out of phase with respect to each other so as to reduce vibration
`
`and/or to achieve a more continuous outputflow.
`
`[0039]
`
`The IPEU andthe main motorof the skid (including the related electronics for power
`
`and control) may be a single, integrated component, such as may be sold or marketed as a single
`
`product, in contrast to an assembly of separately marketed components. The IPEU and the main
`
`motor mayalso be an integrated componentof a fully integrated skid. The integrated
`
`IPEU/motor/electronics product may be operable to perform for a predefined period of time with
`
`no (or very limited) maintenance. Moreover, the electronics and perhaps other portions of the
`
`integrated product may not be accessible by the end user, such that installation of the integrated
`
`product by the end user may be limited to connecting and disconnecting the power and
`
`communication cables, until the integrated product reaches the end of operational life andis
`
`replaced by a new or refurbished (OEM) unit.
`
`[0040]
`
`Aspects of the IPEU mayinclude: compact and low weight unit; integrated heat
`
`transfer from VFD power switches, including for dirty airflow; managementof motor braking
`
`period; managementof outdoor thermal and radiation conditions to maintain internal temperature
`
`within predetermined ranges; management of internal humidity; packaging that aids in
`
`preventing damagefrom vibration and shocks during handling, transport, and operation; and/or
`
`easy rig-up (e.g., simplified cable connection).
`
`[0041]
`
`The IPEU mayoperate without usage of AC cooling or water flow utilized to transfer
`
`the heat generated by the VFD powerswitchesto the outside the unit. The IPEU housing may
`
`contain the VFD (or part of the VFD), an associated programmable logic controller (PLC) and/or
`
`LIBERTY EXHIBIT 1010, Page 8
`
`LIBERTY EXHIBIT 1010, Page 8
`
`
`
`WO 2018/201118
`
`PCT/US2018/030080
`
`other controller, sensors and/or other means for measurement of conditions and operating
`
`parameters internal to the housing, and perhaps one or morefilter components. The IPEU
`
`electronics may control a motor having a powerrating above 100 horsepower (HP), perhaps
`
`higher than 1,000 HP, or even above 2,500 HP. The IPEUelectronics may also control two or
`
`more such motorscollectively, and mayalso control a resistor brake system. The IPEU is
`
`powered by a powersource, which may beasingle cable, and may be controlled via cable
`
`connection (e.g., metal and/or fiber-optic) and/or wireless communications.
`
`[0042]
`
`The IPEU maybe utilized for various traction motors of a drilling rig, such as motors
`
`of triplex and/or other pumping systems, drawworks systems, and top drives, among other
`
`examples. The IPEU mayalso be utilized for smaller motors on the rig, such as for a transfer
`
`pump, perhaps concurrently with the traction motors. Such implementations may be for
`
`fracturing pumping systems, such as may comprise one or moreelectrically driven triplex
`
`pumps, as well as low-pressure side components ofa fracturing system, suchaselectrically
`
`driven centrifugal pumps, conveyorbelts, mixers, agitators, and thelike.
`
`[0043]
`
`The IPEU may be mounted on the skid of a machine being powered by the VFD and
`
`perhaps controlled by the IPEU. The IPEU mayalso be mounteddirectly on the motor of such
`
`machine.
`
`[0044]
`
`FIG. 3 is a schematic view ofat least a portion of an example implementation of an
`
`IPEU 100 according to one or more aspects of the present disclosure. The IPEU 100 includes a
`
`housing(e.g., a rectangular metal box) 105. An input power bulkhead connector 110 for
`
`receiving electrical power from a power source 101, one or more communication bulkhead
`
`connectors 115 for receiving data and/or control signals from one or more data and/or control
`
`sources 116, an output power bulkhead connector 120 leading to one or more main motors 102
`
`driven by the IPEU 100, a primary radiator 125, and perhaps a secondary radiator 130 each
`
`extend through openings in the housing 105. The housing 105 may have an access door(not
`
`shown) for assembly/maintenance purposes.
`
`[0045]
`
`The IPEU 100 includes a VFD implementedvia three insulated-gate bipolar transistor
`
`(IGBT) devices 135, although another number of IGBT devices 135 may be used. The IPEU 100
`
`also includes a primary radiator 125 comprising a plate 126 secured to the housing 105 via bolts
`
`and/or other attachment means 140. The primary radiator 125 also includesfins and/or other
`
`elongated radiating members 127 extending from the plate 126 and through an opening in the
`
`housing 105, thus extending externally from the housing 105. The IGBT devices 135 are
`
`LIBERTY EXHIBIT 1010, Page 9
`
`LIBERTY EXHIBIT 1010, Page 9
`
`
`
`WO 2018/201118
`
`PCT/US2018/030080
`
`secured to the plate 126 (opposite the radiating members 127) in a manner permitting heat
`
`transfer (via conduction and/or otherwise) from the IGBTs 135 to the radiating members 127.
`
`[0046]
`
`The IPEU 100 also includes a controller 145, which may be or comprise a
`
`programmablelogic controller operable to control the IGBTs 135. However, the controller 145
`
`may also be operable to control other components of the IPEU 100, and perhaps components of a
`
`skid (not shown) comprising the IPEU 100, in addition to the IPEU. The controller 145 may
`
`include a communications interface 146 permitting communication between the controller 145
`
`and other components of the IPEU 100. The communications interface 146 may also permit
`
`communication between the controller 145 and components not included in the IPEU 100, such
`
`as other components on the skid, and perhaps other components not located on the skid. Such
`
`communication, whether internal to the IPEU 100, internal to the skid, or external to the skid,
`
`may bevia wired connection and/or via wireless communication (e.g., via antenna/receiver 147).
`
`[0047]
`
`The IPEU 100 mayalso include one or more fans 150 operable to increase airflow
`
`across the radiating members 127. In the example implementation depicted in FIG.3, the
`
`airflow is perpendicular to the page. Ducting 128 attached to the housing 105 may also be
`
`included to focus airflow across the radiating members 127. The fans 150 mayincludeelectric
`
`motors 151 energized by a secondary VFD 155 also contained within the housing 105. Control
`
`of the fans 150 may be via the secondary VFD 155 and/or the controller 145.
`
`[0048]
`
`The primary radiator 125 (and perhaps the fans 150) may be configured to
`
`sufficiently manage the heat generated by the IGBTs 135. However, the controller 145, the
`
`secondary VFD 155, and/or other internal components of the IPEU 100 may generate additional
`
`heat not sufficiently managedby the primary radiator 125 (and perhaps the fans 150). Thus, the
`
`IPEU 100 mayalso include a secondary radiator 130 and/or a secondary fan 165 internal to the
`
`housing 105 (although two or more of the secondary radiator 130 and/or the secondary fan 165
`
`may be included).
`
`[0049]
`
`A plate 131 of the secondary radiator 130 may be securedto the housing 105 via bolts
`
`and/or other attachment means 141. The secondary radiator 130 mayinclude internal fins and/or
`
`other elongated members 132 extending internally from the plate 131 within the housing 105,
`
`and external fins and/or other elongated radiating members 133 extending from the plate 131 and
`
`through an opening in the housing 105, thus extending externally from the housing 105 (opposite
`
`the internal members 132).
`
`LIBERTY EXHIBIT 1010, Page 10
`
`LIBERTY EXHIBIT 1010, Page 10
`
`
`
`WO 2018/201118
`
`PCT/US2018/030080
`
`[0050]
`
`The fan 165 may be operableto increase airflow 160 across the internal elongated
`
`members 132 of the secondary radiator 130. The fan 165 may include an electric motor 166
`
`energized by the secondary VFD 155. Control of the fan 165 may be via the secondary VFD 155
`
`and/or the controller 145. The fan 165 maycirculate air inside the IPEU 100 for improvedheat
`
`transfer from the various components generating heat (such as the controller 145) to the external
`
`environment. Such heat transfer may be from the internal air to the secondary radiator 130 by
`
`convection, through the secondary radiator 130 by conduction, and/or to the outside air by
`
`convection, perhaps simultaneously. However, the IPEU 100 may besealed to protect against
`
`rain, water splash, efc., such that there may be no exchangeofair between the inside of the IPEU
`
`100 andthe external environment.
`
`[0051]
`
`As described above, IGBTs 135 are the main source of heat within the IPEU 100, and
`
`such heat is evacuated by the airflow across the radiating members 127. Other components of
`
`the IPEU 100 generate smaller amounts of heat (controller 145, sensors, efc.). Heat may be
`
`evacuated from these components by the internal fan 165 and transmitted outside the IPEU 100
`
`through the wall of the housing 105 (conduction through the wall and convection on both sides
`
`of the wall), and/or via the secondary radiator 130. However, it may becritical to control this
`
`heat flow.
`
`[0052]
`
`For example, such control can be achieved by controlling the speed of the internal fan
`
`165 while ensuring no overheating of local elements. However, the IPEU 100 may beoperating
`
`in a low-temperature environment. In such conditions, the housing 105 provides some thermal
`
`isolation, and the heat flow from the secondary heat sources(i.e., components other than the
`
`IGBTs 135) may be transmitted to the surrounding air by the housing 105itself, or in
`
`conjunction with the secondary radiator 130. In somecases, one or more external fans 134 (such
`
`as with electric motors 136) may be addedto create forced convection against the radiating
`
`members 133. The radiating members 133 maybe inside a duct 137 with openings on both
`
`extremities to allow outside air to circulate. In extreme cold weather, the ends of the duct 137
`
`may be closed to reduce heat transfer by the secondary radiator 130. Such an implementation
`
`permits full control of heat exchange, thus permitting operating over a wider range of
`
`temperature.
`
`[0053]
`
`The IPEU 100 mayalso be protected against heat transfer by radiation. For example,
`
`a radiation shield 138 may be used to avoid overheating of the electronics of the IPEU 100 when
`
`operating in a sunny location (e.g., a desert). The radiation shield 138 mayalso aid in avoiding
`
`LIBERTY EXHIBIT 1010, Page 11
`
`LIBERTY EXHIBIT 1010, Page 11
`
`
`
`WO 2018/201118
`
`PCT/US2018/030080
`
`too much cooling when operating during cold, clear weather nights, when radiation towards the
`
`cold black sky could otherwise be excessive. The radiation shield 138 may be or comprise a roof
`
`or other structure above the housing 105, such as may be supported by structural members 139
`
`attached to the housing 105 and/or other structure near the IPEU 100. However, the radiation
`
`shield 138 may also or instead be or comprise a layer of additional thermalinsulation inside
`
`and/or outside the housing 105, and/or a highly reflective surface (silver, mirror, white, ec.)
`
`inside and/or outside the housing 105, among other examples.
`
`[0054]
`
`The IPEU 100 mayalso include various sensors operable for detecting temperature,
`
`pressure, humidity, airflow, and/or other parameters of the IPEU 100. In the example
`
`implementation depicted in FIG. 3, such sensors include a temperature sensor 170 for detecting
`
`the temperature of the plate 126, and a temperature sensor 171 for detecting the temperature of
`
`the airflow in the ducting 128. However, other sensors may also be included. The sensors may
`
`generate signals indicative of the sensed parameters, and the controller 145 may be operable to
`
`receive the signals (via wired or wireless connections) for use in operation of the IGBTs135, the
`
`fans 150, the fan 165, and/or other components, for example.
`
`[0055]
`
`FIG.4 is a schematic view of an example implementation of the radiator 125,
`
`designated in FIG. 4 by reference number 200. Thefilter 200 includesa filter 210 for blocking
`
`particles 220 that, when carried by air flow 202, would be large enoughto clog the radiating
`
`members 127. Such particles 220 are redirected by the filter 200 along an alternate path 204
`
`abovethe radiating members 127. However, the filter 210 otherwise permits passageofthe air
`
`flow 202, and perhaps smaller particles 222 that are small enough to pass throughthe radiating
`
`members 127.
`
`[0056]
`
`FIGS. 5 and 6 are front and top viewsof the radiator 200 withoutthefilter 210.
`
`Referring to FIGS. 3-6, collectively, the radiating members 127 may each be a cylinder 230
`
`made from copper and/or other materials having high thermal conductivity. Each cylinder 230
`
`extends perpendicular from the base plate 126 that supports the IGBT devices 135. The ratio of
`
`diameter to length of each radiating member 127 may be optimized to ensure proper heat flux far
`
`from the base plate 126. As also shown in FIGS. 4-6, each radiating member 127 may be
`
`equipped with radial extensions (wings) 232 also made of copper and/or other materials having
`
`high thermal conductivity, such as may increase the surface area in contact with the air flow 202.
`
`The radial extensions 232 of neighboring radiating members 127 may beinterlaced (as depicted
`
`in FIG. 5), and neighboring rowsof radiating members 127 in the array may bestaggered (as
`
`10
`
`LIBERTY EXHIBIT 1010, Page 12
`
`LIBERTY EXHIBIT 1010, Page 12
`
`
`
`WO 2018/201118
`
`PCT/US2018/030080
`
`depicted in FIG. 6), each or both of which may encourage turbulence and/or other flow
`
`disruption that increases the area and/or time of contact between the radiating members 127 and
`
`the air flow 202, thereby increasing convection and/or other transfer of heat from the radiating
`
`members 127 to the air flow 202.
`
`[0057]
`
`The filter 210 may be inclined at an angle 206 (between parallel and perpendicular
`
`relative to the direction of the air flow 202) relative to the base plate 126, as depicted in FIG.4,
`
`so that particles 220 too large to pass between the radiating members 127 can be deflected past
`
`the filter 210 (e.g., along the alternate path 204). Anotherfilter (not shown) similar to the
`
`inclined filter 210 may also extend from the inclinedfilter 210 over the radiating members 127,
`
`such as parallel with the base plate 126, to prevent the particles 220 deflected by the inclined
`
`filter 210 from dropping back downinto the array of radiating members 127. Thefilter(s) may
`
`be positioned before and/or after (relative to the direction of air flow) the fans 150 that establish
`
`the air flow 202 into the array of radiating members 127.
`
`[0058]
`
`FIG. 7 is aschematic view of another implementation of the radiator 125 shown in
`
`FIG.3, designated in FIG. 7 by reference number 250. The radiator 250 includes radiating
`
`members 252 resembling blades extendingparallel to the direct
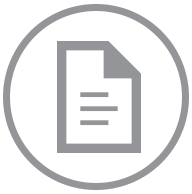
Accessing this document will incur an additional charge of $.
After purchase, you can access this document again without charge.
Accept $ ChargeStill Working On It
This document is taking longer than usual to download. This can happen if we need to contact the court directly to obtain the document and their servers are running slowly.
Give it another minute or two to complete, and then try the refresh button.
A few More Minutes ... Still Working
It can take up to 5 minutes for us to download a document if the court servers are running slowly.
Thank you for your continued patience.
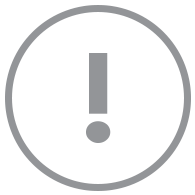
This document could not be displayed.
We could not find this document within its docket. Please go back to the docket page and check the link. If that does not work, go back to the docket and refresh it to pull the newest information.
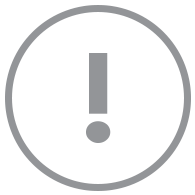
Your account does not support viewing this document.
You need a Paid Account to view this document. Click here to change your account type.
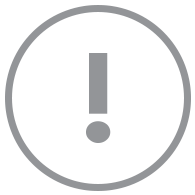
Your account does not support viewing this document.
Set your membership
status to view this document.
With a Docket Alarm membership, you'll
get a whole lot more, including:
- Up-to-date information for this case.
- Email alerts whenever there is an update.
- Full text search for other cases.
- Get email alerts whenever a new case matches your search.
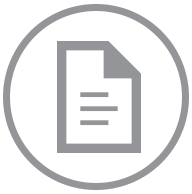
One Moment Please
The filing “” is large (MB) and is being downloaded.
Please refresh this page in a few minutes to see if the filing has been downloaded. The filing will also be emailed to you when the download completes.
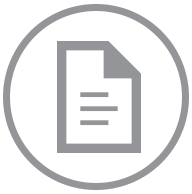
Your document is on its way!
If you do not receive the document in five minutes, contact support at support@docketalarm.com.
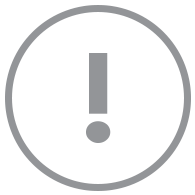
Sealed Document
We are unable to display this document, it may be under a court ordered seal.
If you have proper credentials to access the file, you may proceed directly to the court's system using your government issued username and password.
Access Government Site