`(12) Patent Application Publication (10) Pub. No.: US 2017/0222409 A1
`Oehring et al.
`(43) Pub. Date:
`Aug. 3, 2017
`
`US 20170222409A1
`
`(54) SWITCHGEAR LOAD SHARING FOR OIL
`FIELD EQUIPMENT
`(71) Applicant: US Well Services LLC, Houston, TX
`(US)
`(72) Inventors: Jared Oehring, Houston, TX (US);
`Brandon N. Hinderliter, Houston, TX
`(US)
`
`(73) Assignee: US Well Services LLC, Houston, TX
`(US)
`
`(21) Appl. No.: 15/487,694
`
`(22) Filed:
`
`Apr. 14, 2017
`
`Related U.S. Application Data
`(63) Continuation-in-part of application No. 15/235,788,
`filed on Aug. 12, 2016, which is a continuation-in
`part of application No. 15/202,085, filed on Jul. 5,
`2016, which is a continuation of application No.
`13/679,.689, filed on Nov. 16, 2012, now Pat. No.
`9,410,410, Continuation-in-part of application No.
`15/145,491, filed on May 3, 2016, which is a con
`tinuation-in-part of application No. 13/679,.689, filed
`on Nov. 16, 2012, now Pat. No. 9,410,410.
`
`(60) Provisional application No. 62/323,168, filed on Apr.
`15, 2016.
`
`Publication Classification
`
`(2006.01)
`(2006.01)
`(2006.01)
`
`(51) Int. Cl.
`HO2B 7/06
`E2IB 43/26
`E2IB 4I/00
`(52) U.S. Cl.
`CPC ............... H02B 7/06 (2013.01); E2IB 4I/00
`(2013.01); E2IB 43/26 (2013.01)
`ABSTRACT
`(57)
`A hydraulic fracturing system for fracturing a Subterranean
`formation is disclosed. In an embodiment, the system may
`include a plurality of electric pumps fluidly connected to a
`well associated with the subterranean formation and pow
`ered by at least one electric motor, and configured to pump
`fluid into a wellbore associated with the well at a high
`pressure so that the fluid passes from the wellbore into the
`Subterranean formation and fractures the Subterranean for
`mation; at least one generator electrically coupled to the
`plurality of electric pumps so as to generate electricity for
`use by the plurality of electric pumps; and at least one
`Switchgear electrically coupled to the at least one generator
`and configured to distribute an electrical load between the
`plurality of electric pumps and the at least one generator.
`
`
`
`-300-a
`
`LIBERTY EXHIBIT 1006, Page 1
`
`
`
`Patent Application Publication
`
`Aug. 3, 2017. Sheet 1 of 13
`
`US 2017/0222409 A1
`
`
`
`FIG. 1
`
`LIBERTY EXHIBIT 1006, Page 2
`
`
`
`Patent Application Publication
`
`Aug. 3, 2017. Sheet 2 of 13
`
`US 2017/0222409 A1
`
`O
`C
`CN
`
`
`
`t
`
`LIBERTY EXHIBIT 1006, Page 3
`
`
`
`Patent Application Publication
`
`Aug. 3, 2017. Sheet 3 of 13
`
`US 2017/0222409 A1
`
`
`
`
`
`-300-a
`
`
`
`LIBERTY EXHIBIT 1006, Page 4
`
`
`
`Patent Application Publication
`
`Aug. 3, 2017. Sheet 4 of 13
`
`US 2017/0222409 A1
`
`
`
`LIBERTY EXHIBIT 1006, Page 5
`
`
`
`Patent Application Publication
`
`Aug. 3, 2017. Sheet 5 of 13
`
`US 2017/0222409 A1
`
`
`
`FIG. 4
`
`LIBERTY EXHIBIT 1006, Page 6
`
`
`
`Patent Application Publication
`
`Aug. 3, 2017. Sheet 6 of 13
`
`US 2017/0222409 A1
`
`500
`
`<To Auxiliary>
`
`CTO TransformerS>
`
`CTO TransformerS>
`
`FIG. 5
`
`600
`
`
`
`<To Transformers>
`<To Auxiliary>
`
`<TO TransformerS2
`<To Auxiliary>
`
`FIG. 6
`
`LIBERTY EXHIBIT 1006, Page 7
`
`
`
`Patent Application Publication
`
`Aug. 3, 2017. Sheet 7 of 13
`
`US 2017/0222409 A1
`
`700
`
`725-a
`
`725-b-1
`
`725-b-2
`
`<To TransformerS2
`<To Auxiliary>
`
`<TO TransformerS>
`<To Auxiliary>
`
`FIG. 7
`
`800
`
`
`
`<TO TransformerSY
`
`<To Auxiliary>
`
`<TO TransformerS2
`<To Auxiliary>
`
`FIG. 8
`
`LIBERTY EXHIBIT 1006, Page 8
`
`
`
`Patent Application Publication
`
`Aug. 3, 2017. Sheet 8 of 13
`
`US 2017/0222409 A1
`
`
`
`<To TransformerS2
`<To Auxiliary>
`
`<To TransformerS2
`<To Auxiliary>
`
`FIG. 9
`
`LIBERTY EXHIBIT 1006, Page 9
`
`
`
`Patent Application Publication
`
`Aug. 3, 2017. Sheet 9 of 13
`
`US 2017/0222409 A1
`
`
`
`LIBERTY EXHIBIT 1006, Page 10
`
`
`
`Patent Application Publication
`
`Aug. 3, 2017. Sheet 10 of 13
`
`US 2017/0222409 A1
`
`LIBERTY EXHIBIT 1006, Page 11
`
`
`
`Patent Application Publication
`
`Aug. 3, 2017 Sheet 11 of 13 US 2017/0222409 A1
`
`1200
`
`1205-a
`
`1205-b
`
`1205-C
`
`1205-0
`
`1225-a-1
`
`LOng Distance
`Transmission Line
`
`1225-a-2
`
`1225-b-1
`
`1225-b-2
`
`<TO TransformerS>
`<To Auxiliary>
`
`<TO TransformerS>
`<To Auxiliary>
`
`FIG. 12
`
`LIBERTY EXHIBIT 1006, Page 12
`
`
`
`Patent Application Publication
`
`Aug. 3, 2017. Sheet 12 of 13
`
`US 2017/0222409 A1
`
`*~009)
`
`LIBERTY EXHIBIT 1006, Page 13
`
`
`
`Patent Application Publication
`
`Aug. 3, 2017 Sheet 13 of 13 US 2017/0222409 A1
`
`1400
`
`1407-b
`1407-a
`-1N- Ya
`
`
`
`<To Utility GridZ
`
`<TO TransformerS>
`<To Auxiliary>
`
`<TO TransformerS2
`
`FIG. 14
`
`1500
`
`<To Utility Grid
`
`1505-a
`
`1505-b
`
`1545-a
`
`1545-b
`
`1525-a
`
`1525-b-1
`
`1525-b-2
`
`<To Transformers>
`<To Auxiliary>
`
`<TO TransformerSl
`<To Auxiliary>
`
`FIG. 15
`
`LIBERTY EXHIBIT 1006, Page 14
`
`
`
`US 2017/0222409 A1
`
`Aug. 3, 2017
`
`SWITCHGEAR LOAD SHARING FOR OL
`FIELD EQUIPMENT
`
`CROSS REFERENCE TO RELATED
`APPLICATIONS
`0001. This application claims priority to and the benefit
`of U.S. Provisional Application Ser. No. 62/323,168, filed
`Apr. 15, 2016, and is a continuation-in-part of, and claims
`priority to and the benefit of co-pending U.S. application
`Ser. No. 15/235,788, filed Aug. 12, 2016, which is in turn a
`continuation-in-part of, and claims priority to and the benefit
`of co-pending U.S. application Ser. No. 15/202,085, filed
`Jul. 5, 2016, which is a continuation of, and claims priority
`to and the benefit of, U.S. Pat. No. 9,410,410, filed Nov. 16,
`2012, and is further a continuation-in-part of and claims
`priority to and the benefit of co-pending U.S. application
`Ser. No. 15/145,491, filed on May 3, 2016, which is a
`continuation-in-part of, and claims priority to and the benefit
`of, U.S. Pat. No. 9,410,410, filed Nov. 16, 2012, the full
`disclosures of which are hereby incorporated by reference
`herein for all purposes.
`
`BACKGROUND
`0002 1. Technical Field
`0003. This disclosure relates generally to hydraulic frac
`turing and more particularly to systems and methods for
`spare turbine power generation, which is sometimes referred
`to as reserve power.
`0004 2. Background
`0005 With advancements in technology over the past
`few decades, the ability to reach unconventional sources of
`hydrocarbons has tremendously increased. Horizontal drill
`ing and hydraulic fracturing are two Such ways that new
`developments in technology have led to hydrocarbon pro
`duction from previously unreachable shale formations.
`Hydraulic fracturing (fracturing) operations typically
`require powering numerous components in order to recover
`oil and gas resources from the ground. For example, hydrau
`lic fracturing usually includes pumps that inject fracturing
`fluid down the wellbore, blenders that mix proppant into the
`fluid, cranes, wireline units, and many other components
`that all must perform different functions to carry out frac
`turing operations.
`0006. Usually in fracturing systems the fracturing equip
`ment runs on diesel-generated mechanical power or by other
`internal combustion engines. Such engines may be very
`powerful, but have certain disadvantages. Diesel is more
`expensive, is less environmentally friendly, less safe, and
`heavier to transport than natural gas. For example, heavy
`diesel engines may require the use of a large amount of
`heavy equipment, including trailers and trucks, to transport
`the engines to and from a wellsite. In addition, such engines
`are not clean, generating large amounts of exhaust and
`pollutants that may cause environmental hazards, and are
`extremely loud, among other problems. Onsite refueling,
`especially during operations, presents increased risks of fuel
`leaks, fires, and other accidents. The large amounts of diesel
`fuel needed to power traditional fracturing operations
`requires constant transportation and delivery by diesel tank
`ers onto the well site, resulting in significant carbon dioxide
`emissions.
`0007 Some systems have tried to eliminate partial reli
`ance on diesel by creating bi-fuel systems. These systems
`
`blend natural gas and diesel, but have not been very Suc
`cessful. It is thus desirable that a natural gas powered
`fracturing system be used in order to improve safety, save
`costs, and provide benefits to the environment over diesel
`powered systems. Turbine use is well known as a power
`Source, but is not typically employed for powering fractur
`ing operations.
`0008 Though less expensive to operate, safer, and more
`environmentally friendly, turbine generators come with their
`own limitations and difficulties as well. As is well known,
`turbines generally operate more efficiently at higher loads.
`Many power plants or industrial plants steadily operate
`turbines at 98% to 99% of their maximum potential to
`achieve the greatest efficiency and maintain this level of use
`without significant difficulty. This is due in part to these
`plants having a steady power demand that either does not
`fluctuate (i.e., constant power demand), or having Sufficient
`ing if a load will change (e.g., when shutting down or
`starting up a factory process).
`0009. In hydraulic fracturing, by contrast, the electrical
`load constantly changes and can be unpredictable. This
`unpredictability is due to the process of pumping fluid down
`a wellbore, which can cause wellhead pressure to spike
`several thousand PSI without warning, or can cause pressure
`to drop several PSI unexpectedly (sometimes called a
`“break.' as in the formation broke open somewhere). In
`order to maintain a consistent pump rate, the pump motors
`are required to “throttle' up or “throttle' down (applying
`more or less torque from a variable frequency drive), draw
`ing either more or less electrical power from the turbines
`with little to no notice in many situations.
`0010 Concurrently with pressure variations, fluid rate
`variations can also occur. At any moment, the contracting
`customer may ask for an extra 5 barrels per minute (bpm) of
`pump rate or may request an instantly decreased pump rate
`with little to no warning. These power demand changes can
`vary from second to second—unlike industrial power
`demands, which may vary from hour to hour or day to day,
`allowing for planning and coordination.
`0011
`Hydraulic horsepower (HHP) can be calculated
`with the following relationship:
`
`HHP
`
`(Wellhead Pressure)x (Pump Rate)
`40.8
`
`HHP also directly correlates with the power demand from
`the turbines, where:
`HHPsElectrical Power Demand
`Therefore, if both variables (rate and pressure) are con
`stantly changing, maintaining a steady power demand can be
`difficult. Due to this, it is impossible to design the equipment
`and hold the turbine output at 98%-99% of full potential
`because a minute increase in power demand may shut the
`turbines down and may result in failure of the fracturing job.
`To prevent such turbine shutdown from happening, fractur
`ing equipment S designed to only require approximately
`70% of the maximum output of the turbine generators during
`normal and expected operating conditions. This allows the
`fleet to be able to operate against changing fracturing
`conditions, including increased fluid rate and increased
`wellhead pressure.
`
`LIBERTY EXHIBIT 1006, Page 15
`
`
`
`US 2017/0222409 A1
`
`Aug. 3, 2017
`
`0012. There are also other small loads which contribute
`to changing power demand. These include turning on or off
`Small electrical motors for hydraulic pumps, chemical
`pumps, cooling fans, valve actuators, Small fluid pumps,
`etc., or power for metering instrumentation, communication
`equipment, and other Small electronics. Even lighting or
`heating can contribute to the fluctuating power load.
`0013 Therefore it tray be desirable to devise a means by
`which turbine power generation can be managed at an output
`usable by fracturing equipment.
`
`SUMMARY
`
`0014. The present disclosure is directed to a method and
`system for providing electrical load sharing between Switch
`gear trailers acting as power hubs to combine the output of
`multiple electrical generators.
`0015. In accordance with an aspect of the disclosed
`Subject matter, the method and system of the present dis
`closure provide a hydraulic fracturing system for fracturing
`a Subterranean formation. In an embodiment, the system can
`include a plurality of electric pumps fluidly connected to the
`formation and configured to pump fluid into a wellbore at
`high pressure so that the fluid passes from the wellbore into
`the formation and fractures the formation; at least one
`generator electrically coupled to the plurality of electric
`pumps so as to generate electricity for use by the plurality of
`electric pumps; and at least one Switchgear electrically
`coupled to the at least one generator and configured to
`distribute an electrical load between the plurality of electric
`pumps and the at least one generator.
`0016. In an embodiment, the system including the plu
`rality of electric pumps, the at least one generator, and the at
`least one Switchgear can be a single electrical microgrid.
`0017. In an embodiment, the system making up the single
`electrical microgrid can be split into two or more electrical
`banks. In an embodiment, each of the two or more electrical
`banks can include at least one generator and at least one
`Switchgear. In an embodiment, when one or more of the two
`or more electrical banks is shut down, each of the other
`active electrical banks can be configured to distribute the
`electrical load between the plurality of electric pumps and
`the at least one generator associated with each active elec
`trical bank.
`0018. In an embodiment, the system can further include
`at least two Switchgear units electrically coupled to the at
`least one generator, and a tie breaker electrically coupled
`between each of the at least two switchgear units.
`0019. In an embodiment, the tie breaker can be config
`ured to evenly distribute the electrical load between the
`plurality of electric pumps and the at least one generator
`when the tie breaker is in a closed position; and isolate one
`or more of the plurality of electric pumps, the at least one
`generator, and the at least two Switchgear units when the tie
`breaker is in an open position.
`0020. In an embodiment, when the tie breaker is in the
`closed position, at least one generator is shut down and at
`least one other generator is active, the electrical load can be
`evenly distributed among the at least one other active
`generators.
`0021. In an embodiment, the tie breaker can include a
`long distance transmission line.
`
`0022. In an embodiment, the at least one switchgear can
`be configured to distribute power among any of one or more
`transformers, auxiliaries, or other Switchgear units, or a
`combination thereof.
`0023. In an embodiment, the one or more auxiliaries can
`include any of a blender, electric wireline equipment, a
`transfer pump, an electric crane, a data van, a work trailer,
`living quarters, an emergency shower, sand equipment, a
`turbine inlet chiller, a compressor Station, a pumping station,
`a second fracturing site, a drill rig, or a nitrogen plant, or a
`combination thereof.
`0024. In an embodiment, the at least one generator can be
`one of a turbine generator or a diesel generator, or a
`combination thereof.
`0025. In an embodiment, the at least one turbine genera
`tor can be powered by natural gas.
`0026. In an embodiment, wherein each component of the
`system can be modular and movable to different locations on
`mobile platforms.
`0027. In an embodiment, the system can further include
`a power connection panel associated vial the plurality of
`electric pumps. In an embodiment, the power cot panel can
`include a plurality of power connections for each of the
`plurality of electric pumps, and a system ground connection
`configured to act as a ground between the plurality of
`electric pumps and a transformer. In an embodiment, the
`transformer can be configured to provide power to the
`plurality of electric pumps.
`0028. In an embodiment, the system can further include
`a variable frequency drive connected to the at least one
`electric motor to control the speed of the at least one electric
`motor. In an embodiment, the variable frequency drive can
`frequently perform electric motor diagnostics to prevent
`damage to the at least one electric motor.
`0029. In accordance with another aspect of the disclosed
`Subject matter, the method and system of the present dis
`closure a hydraulic fracturing system for fracturing a Sub
`terranean formation. In an embodiment, the system can
`include a plurality of electric pumps fluidly connected to the
`formation and configured to pump fluid into a wellbore at
`high pressure so that the fluid passes from the wellbore into
`the formation and fractures the formation; at least one
`turbine generator electrically coupled to the plurality of
`electric pumps so as to generate electricity for use by the
`plurality of electric pumps; at least two Switchgear units
`electrically coupled to the at least one turbine generator and
`configured to distribute an electrical load between the plu
`rality of electric pumps and the at least one turbine genera
`tor; a tie breaker electrically coupled between each of the at
`least two Switchgear units and configured to evenly distrib
`ute the electrical load between the plurality of electric
`pumps and the at least one turbine generator when the tie
`breaker is in a closed position; and a variable frequency
`drive connected to the at least one electric motor to control
`the speed of the at least one electric motor, wherein the
`variable frequency drive frequently performs electric motor
`diagnostics to prevent damage to the at least one electric
`motor.
`0030. Other aspects and features of the present disclosure
`will become apparent to those of ordinary skill in the art
`after reading the detailed description herein and the accom
`panying figures.
`
`LIBERTY EXHIBIT 1006, Page 16
`
`
`
`US 2017/0222409 A1
`
`Aug. 3, 2017
`
`BRIEF DESCRIPTION OF DRAWINGS
`0031. Some of the features and benefits of the present
`disclosure having been stated, others will become apparent
`as the description proceeds when taken in conjunction with
`the accompanying drawings, in which:
`0032 FIG. 1 is a schematic example of a turbine gen
`erator in communication with an electronic equipment room,
`which connects to a Switchgear according to an embodiment
`of the disclosure.
`0033 FIG. 2 is a perspective view of an example of a
`turbine generator and electronic equipment room according
`to an embodiment of the disclosure.
`0034 FIGS. 3A and 3B are perspective views of a
`Switchgear trailer according to an embodiment of the dis
`closure.
`0035 FIG. 4 is a perspective view of cables connecting
`to a hydraulic fracturing pump trailer according to an
`embodiment of the disclosure.
`0036 FIGS. 5-15 are block diagrams of portions of a
`microgrid having a plurality of turbine generator sets and
`Switchgear units according to various embodiments.
`0037. While the disclosure will be described in connec
`tion with the preferred embodiments, it will be understood
`that it is not intended to limit the disclosure to that embodi
`ment. On the contrary, it is intended to cover all alternatives,
`modifications, and equivalents, as may be included within
`the spirit and scope of the disclosure as defined by the
`appended claims.
`
`DETAILED DESCRIPTION
`0038. The method and system of the present disclosure
`will now be described more fully hereinafter with reference
`to the accompanying drawings in which embodiments are
`shown. The method and system of the present disclosure
`may be in many different forms and should not be construed
`as limited to the illustrated embodiments set forth herein;
`rather, these embodiments are provided so that this disclo
`sure will be thorough and complete, and will fully convey its
`scope to those skilled in the art. Like numbers refer to like
`elements throughout. In an embodiment, usage of the term
`“about includes +/-5% of the cited magnitude. In an
`embodiment, usage of the term “substantially includes
`+/-5% of the cited magnitude.
`0039. It is to be further understood that the scope of the
`present disclosure is not limited to the exact details of
`construction, operation, exact materials, or embodiments
`shown and described, as modifications and equivalents will
`be apparent to one skilled in the art. In the drawings and
`specification, there have been disclosed illustrative embodi
`ments and, although specific terms are employed, they are
`used in a generic and descriptive sense only and not for the
`purpose of limitation.
`0040. Described herein is an example of a method and
`system for providing electrical load sharing between Switch
`gear trailers acting as power hubs to combine the output of
`multiple electrical generators. Adding a tie breaker between
`two switchgear trailers can eliminate the need for a third
`switchgear trailer, while still retaining the ability to evenly
`distribute power between all of the equipment, and to
`concurrently evenly distribute the electrical load between a
`plurality of turbine generator sets.
`0041. A feature of the switchgear configurations
`described herein is the capability selectively choose between
`
`either load sharing, to provide efficiency and flexibility; or
`having isolated banks of equipment, to provide protection
`and redundancy. In an embodiment, the Switchgear option
`ally includes a tie breaker. The tie breaker can synchronize
`three-phase power of a similar voltage and frequency from
`different sources to act as a common bus, and can evenly
`distribute the electrical load between a plurality of electric
`pumps and turbine generators when the tie breaker is in a
`closed position. The tie breaker will isolate one or more of
`the plurality of electric pumps, the turbine generator, and the
`Switchgear units when the tie breaker is in an open position.
`The use of a tie breaker can provide an advantage over
`previous load sharing systems because use of a tie breaker
`provides more options for the equipment operators and
`allows the fleet to be more versatile as to which mode of
`operation protection and redundancy, or efficiency and
`flexibility—is more desirable at any given moment.
`0042 Another favorable aspect of load sharing is the
`ability to shutdown turbines when peak power output is not
`required. If the power load is distributed evenly between all
`of the generator sets in the fleet, then it can be possible to
`shut down unnecessary power generation as long as the
`remaining generator sets can compensate for the loss and
`pick up the extra load placed on them. This flexibility for
`partial shutdown can allow the remaining turbines to operate
`at a higher efficiency, which can reduce wear on the fleet by
`not running every turbine continuously, and increase effi
`ciency while reducing emissions by allowing fewer turbines
`to run in a lower emissions mode. The lower emissions mode
`is called SoloNox, and can be performed due to load sharing
`using a Switchgear, because the turbines can only operate in
`this mode while operating above a 50% load. In some
`embodiments, directly powering fracturing pumps can
`involve using all turbines regardless of the required power
`load.
`0043. In an embodiment, a variable frequency drive
`(VFD)—and in Some cases, an A/C console used to keep the
`VFD from overheating can be utilized to control the speed
`of an electric motor associated with a pump powered by the
`turbine(s).
`0044. In some examples, certain tasks can be accom
`plished with fewer turbines. Instead of having redundancy or
`spare power generation available to isolated power banks,
`the reserve power generation capability can be consolidated
`across the entire fleet. Requiring fewer turbine generators
`means the equipment can now fit on Smaller well sites which
`reduces the need to clear more land and disrupt the Sur
`rounding environment to create a larger pad, and reduces the
`costs associated with Such clearing and construction.
`0045. The systems described herein are not limited to use
`in processes involving hydraulic fracturing. For example,
`the system includes electric fracturing equipment and power
`generation equipment. The power generation equipment can
`be used to Supply any oilfield equipment including com
`pressor stations, pumping stations, nitrogen plants, CO
`plants, drilling rigs, work-over rigs, barracks, coiled tubing
`units, refineries, or other systems or applications that do not
`have access to a utility provided power grid or that have a
`dynamic power load or low power factor.
`0046 FIG. 1 is a block diagram showing the basic
`components of a hydraulic fracturing well site power gen
`eration system 100 for providing electrical load sharing
`according to an embodiment. A turbine generator 105 can
`include a natural gas turbine engine coupled to a three
`
`LIBERTY EXHIBIT 1006, Page 17
`
`
`
`US 2017/0222409 A1
`
`Aug. 3, 2017
`
`phase, 60 hertz (Hz) electric generator to produce power as
`the turbine engine rotates. In an alternative, the generator
`can generate electricity at 50 Hz, or at any other power level
`useful for hydraulic fracturing fleets. In the illustrated
`embodiment, the turbine generator 105 is shown being
`electrically connected to an electronic equipment room
`(EER) 115, which can house wiring, breakers, controls,
`monitoring systems, fire Suppression Support, and a battery
`bank for secondary power when the turbine is not operating
`and there is no other power source. In some examples, the
`battery bank can power lighting, fire Suppression, emer
`gency turbine lube pumps, and onboard electronics. The
`combination of a turbine generator 105 and an EER 115 can
`be referred to as a generator set. A switchgear trailer 125 can
`provide power distribution, high Voltage breakers, and
`“lock-out, tag-out” (a safety procedure used to ensure that
`dangerous machines are properly shut off and not able to be
`started up again prior to the completion of maintenance or
`servicing work) capabilities.
`0047 Transformers can optionally be included with the
`equipment of FIG. 1. As illustrated in the embodiment
`shown in FIG. 1, an air intake filter house 110 can be
`positioned on top of or adjacent to the turbine generator 105,
`and a catwalk 120 can connect turbine generator 105 and
`EER 115 for ease of access. The system 100 as a whole can
`define an example of an electrical microgrid.
`0048 FIG. 2 shows a perspective view of an example
`system 200 having a single generator set with a turbine
`generator 205 and an overhanging filter house 210 according
`to an embodiment. A power cable 206 can connect the
`turbine generator 205 to an EER 215 with plugs 204-a,
`204-b. In some embodiments, plugs 204-a, 204-b are
`enclosed and concealed while energized. Between turbine
`205 and EER 215 is an elevated catwalk 220 with Stairs
`leading to the EER 215 for employee access, in the illus
`trated embodiment. Turbine 205 can also include mainte
`nance hatches for purposes of employee access. A plug 202
`can provide a power cable between the EER 215 and a
`Switchgear trailer (not shown).
`0049. An example 300-a of a switchgear trailer 325 is
`shown in an end perspective view in FIG. 3A. Electrical
`connections 302 for turbines and an auxiliary trailer are
`shown in recesses formed on a lateral surface of the trailer
`325. A side opposite the lateral side of the trailer 325, as
`shown in the example 300-b according to an embodiment
`illustrated in FIG.3B, can include electrical connections 302
`for transformers.
`0050 FIG. 3B illustrates in side perspective view a side
`of the switchgear trailer 325 opposite from that of shown in
`FIG. 3A. In the illustrated example, switchgear trailer 325
`can be an example of a switchgear “B” trailer. Four con
`nections 302 are visible, which are for the 13.8 kV cable that
`spans between the Switchgear and the transformers. Each
`connection 302 is a cable that contains all three electrical
`phases, a ground, and a ground check, which is different
`from the cabling configuration of FIG. 4, which relies on the
`use of multiple conductors per phase, as discussed below.
`0051. The switchgear trailer 325 can house large breakers
`and fault protection equipment required for safe operations
`and for "lock-out, tag-out of power going to selected
`equipment. The switchgear is optionally rated for 15 kV
`(1.3.8 kV), and can be designed or reconfigured for different
`voltages, such as 138 kV. 4,160 V, or 600 V, or any other
`voltage suitable for fracturing fleet operations. The switch
`
`gear can include ground fault detection, color coordinated
`cable receptacles, interlock system, and other safety fea
`tures.
`Illustrated in a side perspective view in FIG. 4 is an
`0.052
`example 400 of multiple single-conductor cables connecting
`to a fracturing pump trailer 425, according to an embodi
`ment. In the illustrated example, a 600 V power connection
`panel 401 contains power connections for two fracturing
`pumps. Each electrical phase is split into two separate
`cables. An upper row of plugs 402-a can be used to power
`one fracturing pump, while a lower row of plugs 402-b can
`be used to power a second fracturing pump on the same
`fracturing pump trailer 425.
`0053. In the illustrated example, the upper row of plugs
`402-a includes six single-phase cable connections, and the
`lower row of plugs 402-b includes six single-phase cable
`connections, allowing for two cables per phase. The plugs
`can be color-coded based on the electrical phase. The power
`connection panel 401 can also include a control power cable
`404 and a system ground cable 406. The system ground
`cable 406 can act as a ground between the fracturing pump
`trailer 425 and a 13.8 kV to 600 V transformer (not shown)
`providing power to the fracturing pump trailer 425. Addi
`tional cables can span between the 13.8 kV to 600 V
`transformer and the fracturing pump trailer 425.
`0054 FIG. 5 is a block diagram illustrating one example
`500 of a plurality of generator sets 505-a, 505-b, 505-c for
`use with a system for fracturing a Subterranean formation.
`Each generator set 505-a, 505-b, 505-C can include a turbine
`engine with Sufficient mechanical power to rotate an electric
`generator with sufficient electrical power to provide elec
`tricity to a small, closed circuit, electrical grid. This grid can
`be considered part of the microgrid.
`0055 For the sake of discussion herein, certain types of
`Switchgear units have nomenclature based on their applica
`tion; for example a switchgear “A” can distribute power to
`other Switchgear units, a Switchgear “B” can transmit power
`to transformers and auxiliaries, and a Switchgear “C” can
`transmit power to transformers. However, a Switchgear
`trailer is not limited to the previously stated configurations.
`It is possible to power more than four transformers from a
`switchgear “B” or switchgear “C”; and a switchgear “B” can
`Supply more than one auxiliary trailer if needed. Similarly,
`a switchgear “A” is not limited to connections for only three
`or four generator sets and only two Switchgear trailers. The
`denotation of A, B, C, A+, B+ and C+ Switchgear units does
`not reflect industry standards, but is a naming convention for
`use herein.
`0056. In the illustrated embodiment, switchgear “A”
`525-a is an electrical hub combining the power output of
`three 5.7 MW natural gas turbine generators from generator
`sets 505-a, 505-b,505-c. Further in this example, switchgear
`“A” 525-a can supply electrical power to two other switch
`gear units. Switchgear “B” 525-b can receive power from
`switchgear “A” 525-a and distribute the power to an auxil
`iary unit and multiple transformers, as shown. Switchgear
`“C” 525-c can also receive power from switchgear “A”
`525-a and distribute the power to one or more transformers,
`but in the illustrated embodiment does not distribute power
`to an auxiliary unit.
`0057. In this example, the illustrated lines leading
`between the generator sets 505-a, 505-b, 505-c, switchgear
`units 525-a, 525-b, 525-c, and auxiliary units and transform
`ers can be 13,800 volt, three-phase, 60 Hz, power lines. This
`
`LIBERTY EXHIBIT 1006, Page 18
`
`
`
`US 2017/0222409 A1
`
`Aug. 3, 2017
`
`example allows load distribution between all three turbines
`in generator sets 505-a, 505-b, 505-c through switchgear
`“A” 525-a. Optionally, the power demand placed on each
`generator set 505-a, 505-b, 505-c can be equal, and each
`generator set 505-a, 505-b, 505-c can run at an equal output.
`0058 FIG. 6 is a block diagram showing an embodiment
`600 illustrating a plurality of generator sets 605-a, 605-b,
`605-c for use with a system for fractur
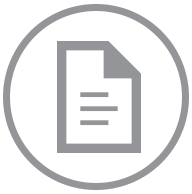
Accessing this document will incur an additional charge of $.
After purchase, you can access this document again without charge.
Accept $ ChargeStill Working On It
This document is taking longer than usual to download. This can happen if we need to contact the court directly to obtain the document and their servers are running slowly.
Give it another minute or two to complete, and then try the refresh button.
A few More Minutes ... Still Working
It can take up to 5 minutes for us to download a document if the court servers are running slowly.
Thank you for your continued patience.
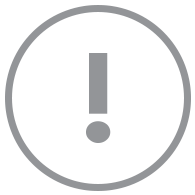
This document could not be displayed.
We could not find this document within its docket. Please go back to the docket page and check the link. If that does not work, go back to the docket and refresh it to pull the newest information.
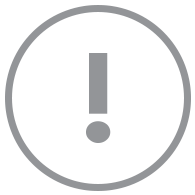
Your account does not support viewing this document.
You need a Paid Account to view this document. Click here to change your account type.
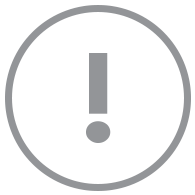
Your account does not support viewing this document.
Set your membership
status to view this document.
With a Docket Alarm membership, you'll
get a whole lot more, including:
- Up-to-date information for this case.
- Email alerts whenever there is an update.
- Full text search for other cases.
- Get email alerts whenever a new case matches your search.
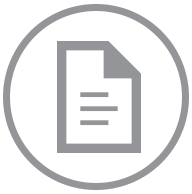
One Moment Please
The filing “” is large (MB) and is being downloaded.
Please refresh this page in a few minutes to see if the filing has been downloaded. The filing will also be emailed to you when the download completes.
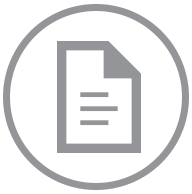
Your document is on its way!
If you do not receive the document in five minutes, contact support at support@docketalarm.com.
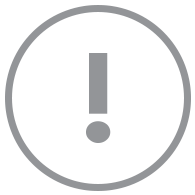
Sealed Document
We are unable to display this document, it may be under a court ordered seal.
If you have proper credentials to access the file, you may proceed directly to the court's system using your government issued username and password.
Access Government Site