`
`(12) United States Patent
`Bayyouk et al.
`
`(10) Patent No.:
`(45) Date of Patent:
`
`US 8,662,865 B2
`Mar. 4, 2014
`
`(54) OFFSET VALVE BORE INA
`RECIPROCATING PUMP
`
`(71) Applicant: S.P.M. Flow Control, Inc., Fort Worth,
`TX (US)
`
`(72) Inventors: Jacob A. Bayyouk, Richardson, TX
`(US); Donald Mackenzie, Glasgow
`(GB)
`
`(73) Assignee: S.P.M. Flow Control, Inc., Fort Worth,
`TX (US)
`
`(*) Notice:
`
`Subject to any disclaimer, the term of this
`patent is extended or adjusted under 35
`U.S.C. 154(b) by 0 days.
`(21) Appl. No.: 13/849,228
`
`(22) Filed:
`(65)
`
`Mar. 22, 2013
`Prior Publication Data
`US 2013/0216413 A1
`Aug. 22, 2013
`Related U.S. Application Data
`(63) Continuation of application No. 13/314,831, filed on
`Dec. 8, 2011.
`(60) Provisional application No. 61/421,453, filed on Dec
`9, 2010
`pp
`s
`a- - s
`s
`(51) Int. Cl.
`F04B 27/10
`(2006.01)
`F04B 39/2
`(2006.01)
`(52) U.S. Cl.
`CPC ............... F04B 39/122 (2013.01); F04B 27/10
`(2013.01)
`USPC ........................................... 417/269; 417/415
`(58) Field of Classification Search
`CPC ............................... F04B 27/10; F04B 39/122
`USPC ......... 417/415, 269; 92/61, 76, 1711; D15/7,
`D15F9
`See application file for complete search history.
`
`(56)
`
`References Cited
`U.S. PATENT DOCUMENTS
`
`2,666,026 A
`2,776,701 A
`
`1/1954 Gibbs
`1, 1957 Denis
`(Continued)
`FOREIGN PATENT DOCUMENTS
`
`AR
`AR
`
`5, 2013
`O84230 A1
`5, 2013
`O84231 A1
`(Continued)
`OTHER PUBLICATIONS
`Xie He et al.; Fatigue Prediction for Pump End of High Pressure
`Fracturing Pump; Advanced Materials Research vol. 337 (2011) pp.
`81-86.
`
`(Continued)
`Primary Examiner — Bryan Lettman
`(74) Attorney, Agent, or Firm — Haynes and Boone, LLP
`
`ABSTRACT
`(57)
`A fluid end (15) for a multiple reciprocating pump assembly
`(12) comprises at least three plunger bores (61 or 91) each for
`receiving a reciprocating plunger (35), each plunger bore
`having a plunger bore axis (65 or 95). Plunger bores being
`arranged across the fluid head to define a central plunger bore
`and lateral plunger bores located on either side of the central
`plunger bore. Fluid end (15) has suction valve bores (59 or
`89), each suction valve bore receiving a suction valve (41)and
`having a suction valve bore axis (63 or 93). Discharge valve
`bores (57 or 87), each discharge valve bore receiving a dis
`charge valve (43) and having a discharge valve bore axis (63
`or 93). The axes of at least one of suction (10) and discharge
`valve bores is inwardly offset in the fluid end from its respec
`tive plunger bore axis.
`30 Claims, 12 Drawing Sheets
`
`
`
`Page 1 of 23
`
`
`
`(56)
`
`References Cited
`
`U.S. PATENT DOCUMENTS
`
`3.35A 3.82 Erin
`3.470 O77 A
`9/1969 Higgins
`3676332 A
`7, 1972 Yohpe
`38.10716 A
`5, 1974 Abrahams et al.
`
`3,844 921 A 10, 1974 Benedict
`
`3919068 A 11, 1975 Gary
`3963,384 A
`6, 1976 Bastenhof
`4,097 357 A
`6/1978 Jacquelin
`4.339.227 A
`7, 1982 Furst
`4,370.211 A
`1, 1983 Hybler
`4,378,853 A
`4, 1983 Chia et al.
`4.412.792 A 1 1/1983 LaBorde et al.
`4520,837 A
`6, 1985 Cole et al.
`4,861241 A
`8, 1989 Gamboa et al.
`5,059 101 A 10, 1991 Valavaara
`5.02,297 A
`4, 1992 Thompson
`5,127,807 A
`7/1992 Eslinger
`5,154,589 A 10, 1992 Ruhl et al.
`5,171,136 A 12, 1992 Pacht
`5,246,355 A
`9, 1993 Matzner et al.
`D355,199 S
`2/1995 Ousey
`D361,575 S
`8, 1995 Makino
`5,584,672 A 12/1996 Simonette
`5,636.975 A
`6/1997 Tiffany et al.
`5,639,227 A
`6, 1997 Mills
`5,823,541 A 10, 1998 Dietle et al.
`5,839,468 A 11/1998 Allred
`5,848,878 A 12/1998 Conti et al.
`5,947,697 A
`9, 1999 Morrison
`D420,683 S
`2/2000 Suzuki
`6,065.453 A
`5/2000 Zych
`6,382,940 B1
`5, 2002 Blume
`6,386,751 B1
`5, 2002 Wootan et al.
`D461,733 S
`8, 2002 Iida
`D461,827 S
`8, 2002 Koebbe
`6,544,012 B1
`4/2003 Blume
`6,595.278 B1
`7/2003 Lam et al.
`6,623,259 B1
`9, 2003 Blume
`6,670,312 B2 12/2003 Sugimoto et al.
`6,705.396 B1
`3/2004 Ivannikov et al.
`6,843,313 B2
`1, 2005 Hult
`D506,210 S
`6, 2005 Selic et al.
`6,910,871 B1
`6, 2005 Blume
`7,036,688 B2
`5, 2006 Stettes et al.
`7,118,114 B2 10/2006 Burdick et al.
`7,186,097 B1
`3/2007 Blume
`7,255,163 B2
`8, 2007 Rivard
`D552,139 S
`10, 2007 Cho
`D556,861 S
`12/2007 Yokohari
`D556,862 S
`12/2007 Yokohari
`D557,286 S
`12, 2007 Pedrolo
`7,335,002 B2
`2/2008 Vicars
`7,364.412 B2
`4/2008 Kugelev et al.
`7,404,704 B2
`7/2008 Kugelev et al.
`D583,389 S
`12/2008 Bilger
`D584,320 S
`1/2009 Huang
`7,484.452 B2
`2/2009 Baxter et al.
`7,513,759 B1
`4/2009 Blume
`D603,870 S
`11/2009 Mehnert et al.
`D605,665 S
`12/2009 Falkenberg
`D606,629 S
`12/2009 Tokumoto
`D623,200 S
`9, 2010 Fulkerson et al.
`D629,423 S
`12/2010 Varini
`7,874,369 B2
`1/2011 Parker et al.
`D641,382 S
`7, 2011 Hawes et al.
`8,016,027 B2
`9/2011 Boyles
`8,074,999 B2 12/2011 Burdick et al.
`D655,314 S
`3/2012 Yoshimura et al.
`P2 i 1 13: Rie
`D6 60.191 S
`5, 2012 Asaba
`D667, 532 S
`9, 2012 Asaba
`D670,312 S
`11/2012 Alexander et al.
`D670,790 S
`11/2012 Tokumoto
`
`US 8,662.865 B2
`Page 2
`
`2/2013 Fukano et al.
`D676,111 S
`4/2013 Skurdalsvold
`D679,290 S
`4/2013 DeLeon et al.
`D679,292 S
`4/2013 DeLeon et al.
`D679,293 S
`2003/0235508 A1 12/2003 Vicars
`2004/0219042 A1 1 1/2004 Kugelev et al.
`2006,0002806 A1
`1/2006 Bazter et al.
`2006, O159573 A1
`7/2006 Inoue et al.
`2007/0051508 A1
`3, 2007 Pecorari et al.
`
`2007/0237651 A1* 10, 2007 Tojo .
`
`.
`
`.
`
`.
`
`.
`
`.
`
`.
`
`.
`
`.
`
`.
`
`.
`
`.
`
`.
`
`.
`
`.
`
`.
`
`.
`
`.
`
`.
`
`.
`
`.
`
`.
`
`.
`
`.
`
`.
`
`.
`
`.
`
`.
`
`. 417.269
`
`1, 2008 Tian et al.
`2008.0003122 A1
`6, 2008 Vicars
`2008. O1382.24 A1
`2009/0314645 A1 12/2009 Kim
`2010/03228O2 A1 12/2010 Kugelev
`2011/O189040 A1
`8, 2011 Vicars
`2011 0198072 A1
`8, 2011 Cote et al.
`2011/0308967 A1 12/2011 Byrne
`2012fOO63936 A1
`3/2012 Baxter et al.
`2012fO144995 A1
`6, 2012 Bayyouk et al.
`2012/0183424 A1
`7/2012 Bayyouk et al.
`2012fO288387 A1 11/2012 Freed et al.
`
`FOREIGN PATENT DOCUMENTS
`
`343.913
`AU
`343914
`AU
`34.6409
`AU
`2486223
`CA
`235.0047 C
`CA
`138269
`CA
`2514769
`CA
`2.716430 C
`CA
`144435
`CA
`2711206 C
`CA
`20114.8968
`CN
`101.397672
`CN
`ZL201030691447
`CN
`CN ZL201230031196.2
`CN ZL20123O337093.9
`CN ZL20123O324855.1
`CN ZL201230513325.1
`DE
`10214404
`EP
`O58O196
`EP
`1780415
`EP
`OO1944.054-0001
`EP
`OO1335699-0001
`EP
`OO1335699-00O2
`EP
`OO2125732-OOO1
`GB
`144928O
`GB
`2419642
`GB
`241681.1
`IN
`243221
`IN
`246712
`JP
`2000-170643
`RU
`2168.064
`SA
`2446
`SG
`D2012,168
`SG
`D2012,874, J
`SG
`D2012,875
`SG
`D2012/1221 J
`WO WO 2004/092538
`WO WO 2005/O15O24
`WO WO 2005/088125
`WO WO 2011/O18732
`WO WO 2011 O27 273
`WO WO 2011/O54948
`WO WO 2011, 160069
`WO WO 2012/078870
`WO WO 2012/078888
`WO WO 2012/145591
`
`8, 2012
`8, 2012
`1, 2013
`9, 2010
`10, 2010
`T 2011
`9, 2011
`5, 2012
`9, 2012
`9, 2012
`11, 2008
`4/2009
`2, 2012
`12/2012
`3, 2013
`5, 2013
`5, 2013
`10, 2003
`1, 1994
`* 5/2007 .......... FO4B 53/16
`2, 2012
`9, 2012
`9, 2012
`1, 2013
`9, 1976
`5, 2006
`9, 2009
`2, 2012
`T 2012
`6, 2000
`5, 2001
`9, 2012
`2, 2012
`9, 2012
`9, 2012
`10, 2012
`10, 2004
`2, 2005
`9, 2005
`2, 2011
`3, 2011
`5, 2011
`12/2011
`6, 2012
`6, 2012
`10, 2012
`
`OTHER PUBLICATIONS
`A. Al-Hashem et al., Cavitation Corrosion Behavior of Some Cast
`Alloys in Seawater, from Industrial Corrosion and Corrosion Control
`Technology, Pub. By Kuwait Institute for Science.
`Notice of Allowance mailed Apr. 18, 2013, by the USPTO, regarding
`Design U.S. Appl. No. 29/399,897.
`
`Page 2 of 23
`
`
`
`US 8,662.865 B2
`Page 3
`
`(56)
`
`References Cited
`
`OTHER PUBLICATIONS
`
`Notice of Allowance mailed Jan. 10, 2013, by the USPTO, regarding
`Design U.S. Appl. No. 29/411,974.
`Notice of Allowance mailed Jan. 18, 2013, by the USPTO, regarding
`Design U.S. Appl. No. 29/419,417.
`Notice of Allowance mailed Jan. 23, 2013, by the USPTO, regarding
`Design U.S. Appl. No. 29/419,425.
`Notice of Allowance mailed Apr. 12, 2013, by the USPTO, regarding
`Design U.S. Appl. No. 29.420,822.
`Office Action mailed Apr. 25, 2013, by the USPTO, regarding U.S.
`Appl. No. 13/162,815.
`Examination Report issued by Intellectual Property India, datedMar.
`28, 2013, regarding Indian Design Application No. 246713.
`Examination Report issued by Intellectual Property India, dated Jan.
`3, 2013, regarding Indian Design Application No. 248994.
`Canadian Examiner's Report issued by the CIPO, dated Jan. 10,
`2013, regarding App No. 146,660.
`U.S. Appl. No. 29/399,897, filed Sep. 18, 2011, S.P.M. Flow Control,
`Inc.
`U.S. Appl. No. 29/411,974, filed Jan. 27, 2012, S.P.M. Flow Control,
`Inc.
`U.S. Appl. No. 29/419,417, filed Apr. 27, 2012, S.P.M. Flow Control,
`Inc.
`U.S. Appl. No. 29/419,425, filed Apr. 27, 2012, S.P.M. Flow Control,
`Inc.
`U.S. Appl. No. 29/420,822, filed May 14, 2012, S.P.M. Flow Control,
`Inc.
`U.S. Appl. No. 29/424,801, filed Jun. 15, 2012, S.P.M. Flow Control,
`Inc.
`U.S. Appl. No. 29/425,284, filed Jun. 21, 2012, S.P.M. Flow Control,
`Inc.
`B.N. Cole; Strategy for Cross-Bores in High Pressure Containers;
`Journal Mechanical Engineering Science; vol. 11 No. 2 1969: pp.
`151-161.
`L.M. Masu; Cross Bore Configuration and Size Effects on the Stress
`Distribution in Thick-Walled Cylinders; Int. J. Pres. Ves. & Piping 72
`(1997) pp. 171-176.
`P Makulsawatudom et al.; Stress Concentration at Crossholes in
`Thick Cylindrical Vessels; J. Strain Analysis vol. 39 No. 5; pp. 471
`481.
`L.M. Masu; Numerical analysis of cylinders containing circular off
`set cross-bores—Abstract; International Journal of Pressure Vessels
`and Piping, vol. 75, Issue 3, Mar. 1998.
`Notice of Allowance mailed Dec. 12, 2007, by the USPTO, regarding
`U.S. Appl. No. 10/913,221, now Patent No. 7,364,412.
`Examiner Interview Summary mailed Oct. 9, 2007, by the USPTO,
`regarding U.S. Appl. No. 10/913,221, now Patent No. 7,364,412.
`Final Office Action mailed Jul. 20, 2007, by the USPTO, regarding
`U.S. Appl. No. 10/913,221, now Patent No. 7,364,412.
`Office Action mailed Mar. 29, 20007, by the USPTO, regarding U.S.
`Appl. No. 10/913,221, now Patent No. 7,364,412.
`
`Notice of Allowance mailed Mar. 27, 2008, by the USPTO, regarding
`U.S. Appl. No. 10/835,749, now Patent No. 7,404,704.
`Office Action Mailed Jan. 10, 2008, by the USPTO, regarding U.S.
`Appl. No. 10/835,749, now Patent No. 7,404,704.
`Office Action mailed Jun. 21, 2007, by the USPTO, regarding U.S.
`Appl. No. 10/835,749, now Patent No. 7,404,704.
`Office Action mailed Nov. 9, 2010, re Design U.S. Appl. No.
`29/363,376, now Patent No. D641,382.
`Notice of Allowance mailed Mar. 8, 2011, re Design U.S. Appl. No.
`29/363,376, now Patent No. D641,382.
`Final Office Action mailed Nov. 6, 2012, by the USPTO, regarding
`U.S. Appl. No. 29/411,974.
`Office Action mailed Jul 23, 2012, by the USPTO, regarding U.S.
`Appl. No. 29/411,974.
`Search Report, dated Oct. 31, 2005, from the UK Patent Office
`regarding App No. GB0516137.7.
`Search Report, dated Jan. 18, 2005, from the UK Patent Office
`regarding App No. GB0424019.8.
`First Examination Report issued by Intellectual Property India, dated
`Aug. 31, 2012, regarding Indian Design Application No. 246713.
`First Examination Report issued by Intellectual Property India, dated
`Sep. 14, 2012, regarding Indian Design Application No. 246712.
`International Preliminary Report on Patentability, issued Dec. 19.
`2012, by the International Bureau of WIPO, in connection with
`International Application No. PCT/US2011/040960.
`International Search Report and Written Opinion, mailed Nov. 1,
`2011, by the ISA/US, in connection with International Application
`No. PCT/US2011/040960.
`International Search Report and Written Opinion, mailed Jul. 20.
`2012, by the ISA/KR, in connection with International Application
`No. PCT/US2O11,063946.
`International Search Report and Written Opinion, mailed Jul. 20.
`2012, by the ISA/KR, in connection with International Application
`No. PCT/US 2011/063968.
`International Search Report and Written Opinion, mailed Jun. 29.
`2012, by the ISA/US, in connection with International Application
`No. PCT/US2012fO34397.
`Co-pending U.S. Appl. No. 29/461,771, filed Jul. 26, 2013.
`International Search Report and Written Opinion issued Apr. 8, 2013,
`by the ISA/US, regarding PCT/US2013/024172.
`Notice of Allowance mailed Jul. 26, 2013, by the USPTO, regarding
`U.S. Appl. No. 29/445,736.
`Notice of Allowance mailed May 29, 2013, by the USPTO, regarding
`U.S. Appl. No. 29/425,284.
`Office Action mailed Aug. 14, 2013, by the USPTO, regarding U.S.
`Appl. No. 13/314,745.
`Office Action mailed Jul. 17, 2013, by the USPTO, regarding U.S.
`Appl. No. 29/420,822.
`Office Action mailed Jul 22, 2013, by the USPTO, regarding U.S.
`Appl. No. 13/314,831.
`* cited by examiner
`
`Page 3 of 23
`
`
`
`U.S. Patent
`
`Mar. 4, 2014
`
`Sheet 1 of 12
`
`US 8,662,865 B2
`
`
`
`
`
`
`
`
`
`
`
`
`
`
`
`
`
`
`
`
`
`
`YYYYYYYY
`
`6?
`Sr N.N. N. N.N.
`
`Page 4 of 23
`
`
`
`U.S. Patent
`U.S. Patent
`
`Mar. 4, 2014
`Mar.4, 2014
`
`Sheet 2 of 12
`Sheet 2 of 12
`
`US 8,662,865 B2
`US 8,662,865 B2
`
`
`
`
`
`Page 5 of 23
`
`Page 5 of 23
`
`
`
`U.S. Patent
`
`Mar. 4, 2014
`
`Sheet 3 of 12
`
`US 8,662,865 B2
`
`63b
`
`-61b
`
`
`
`
`
`Page 6 of 23
`
`
`
`U.S. Patent
`
`Mar. 4, 2014
`
`Sheet 4 of 12
`
`US 8,662,865 B2
`
`
`
`6a
`65a
`59a
`
`61 C
`
`59C
`
`59b
`
`65b. 4. 65 C.
`63C
`
`FG.4
`
`Page 7 of 23
`
`
`
`U.S. Patent
`U.S. Patent
`
`Mar. 4, 2014
`Mar.4, 2014
`
`Sheet 5 of 12
`Sheet 5 of 12
`
`US 8,662,865 B2
`US 8,662,865 B2
`
`
`
`
`
`Page 8 of 23
`
`Page 8 of 23
`
`
`
`U.S. Patent
`U.S. Patent
`
`Mar. 4, 2014
`
`Sheet 6 of 12
`
`US 8,662,865 B2
`US 8,662,865 B2
`
`
`
`
`
`Page 9 of 23
`
`Page 9 of 23
`
`
`
`U.S. Patent
`U.S. Patent
`
`Mar. 4, 2014
`Mar.4, 2014
`
`Sheet 7 of 12
`Sheet 7 of 12
`
`US 8,662,865 B2
`US 8,662,865 B2
`
`
`
`89b
`
`“Boe 89d
`
`
`NLaKSNeENNe
`
`
`FIG.9
`
`Page 10 of 23
`
`Page 10 of 23
`
`
`
`U.S. Patent
`
`Mar. 4, 2014
`
`Sheet 8 of 12
`
`US 8,662,865 B2
`
`zzzzzzz
`ZZZZZZZZ
`
`F.G. 12
`
`
`
`
`
`
`
`
`
`
`
`
`
`
`
`
`
`
`
`
`
`
`
`
`
`
`
`Page 11 of 23
`
`
`
`U.S. Patent
`U.S. Patent
`
`Mar.
`4, 2014
`Mar.
`
`Sheet 9 of 12
`
`US 8,662,865 B2
`US 8,662,865 B2
`
`
`
`
`
`UZ(Z
`?No.
`VITRALZsa
`LMoei\
`
`
`
`
`
`89a
`
`89b
`
`89c
`
`89d
`
`89e
`
`Page 12 of 23
`
`Page 12 of 23
`
`
`
`
`
`
`U.S. Patent
`U.S. Patent
`
`Mar. 4, 2014
`Mar.
`
`Sheet 10 of 12
`
`US 8,662,865 B2
`US 8,662,865 B2
`
`
`
`
`
`
`
`Page 13 of 23
`
`Page 13 of 23
`
`
`
`U.S. Patent
`
`Mar. 4, 2014
`
`Sheet 11 of 12
`
`US 8,662,865 B2
`
`
`
`
`
`
`
`LES-H.HO, ZLBS-HBO „OG'!!
`
`Page 14 of 23
`
`
`
`U.S. Patent
`U.S. Patent
`
`Mar. 4, 2014
`Mar.4, 2014
`
`Sheet 12 of 12
`Sheet 12 of 12
`
`US 8,662,865 B2
`US 8,662,865 B2
`
`
`
`
`
`
`
`N N
`
`
`
`
`
`"I N
`TLR
`
`
`S
`| O
`Pitttit|gee
`i s
`i.
`93,000
`105,000
`85000
`73,000
`69000
`101,000
`97000
`89,000
`81,000
`77000
`65000
`s
`
`O
`
`O O O
`
`Page 15 of 23
`
`Page 15 of 23
`
`
`
`US 8,662,865 B2
`
`1.
`OFFSET VALVE BORE INA
`RECIPROCATING PUMP
`
`CROSS-REFERENCE TO RELATED
`APPLICATIONS
`
`This application is a Continuation of U.S. patent applica
`tion Ser. No. 13/314,831 filed Dec. 8, 2011, which claims the
`priority to U.S. Provisional Application No. 61/421,453 filed
`Dec. 9, 2010, the entire disclosures of which is incorporated
`herein by reference.
`TECHNICAL FIELD
`
`10
`
`An arrangement is disclosed whereby a valve bore is offset
`from a plunger bore in a fluid end of a reciprocating pump to
`relieve stress.
`
`15
`
`BACKGROUND OF THE DISCLOSURE
`
`In oil field operations, reciprocating pumps are used for
`various purposes. Reciprocating pumps are used for opera
`tions such as cementing, acidizing, or fracturing of a Subter
`ranean well. These reciprocating pumps run for relatively
`short periods of time, but they operate on a frequent basis and
`oftentimes at extremely high pressures. A reciprocating pump
`is mounted to a truck or a skid for transport to various well
`sites and must be of appropriate size and weight for road and
`highway regulations.
`Reciprocating pumps or positive displacement pumps for
`oil field operations deliver a fluid or slurry, which may carry
`solid particles (for example, a sand proppant), at pressures up
`to 20,000 psi to the wellbore. A known pump for oilfield
`operations includes a power end driving more than one
`plunger reciprocally in a corresponding fluid end or pump
`chamber. The fluid end may comprise three or five plunger
`bores arranged transversely across a fluid head, and each
`plunger bore may be intersected by Suction and discharge
`valve bores. In a known reciprocating pump, the axis of each
`plunger bore intersects perpendicularly with a common axis
`of the Suction and discharge valve bores
`In a mode of operating a known three plunger bore recip
`rocating pump at high fluid pressures (for example, around or
`greater than 20,000 psi), a maximum pressure and thus stress
`can occur within a given pump chamber as the plunger moves
`longitudinally in the fluid end towards top dead center (TDC),
`compressing the fluid therein. One of the other pump cham
`bers will be in discharge and thus at a very low pressure, and
`the other pump chamber will have started to compress the
`fluid therein.
`It has been discovered that, in a given pump chamber, the
`areas of highest stress occur at the intersection of each
`plunger bore with its suction and discharge valve bores as the
`plunger moves to TDC. The occurrence of high stress at these
`areas can shorten the life of the fluid end.
`JP 2000-170643 is directed to a multiple reciprocating
`pump having a small size. The pump has three piston bores in
`which the pistons reciprocate but, so that a compact pump
`configuration can be provided, the axis of each Suction valve
`bore is arranged perpendicularly to its respective discharge
`valve bore (that is, so that there is a laterally directed dis
`charge from the fluid end).
`JP 2000-170643 also teaches that a limit as to the volume of
`fluid that can be pumped by a small reciprocating pump is the
`size of Suction and discharge valve bores. Contrary to the
`embodiments disclosed herein, the teaching of JP 2000
`170643 is not concerned with reducing stresses arising at the
`
`25
`
`30
`
`35
`
`40
`
`45
`
`50
`
`55
`
`60
`
`65
`
`2
`intersection of piston, Suction and discharge bores. Rather, JP
`2000-170643 teaches moving the axes of each of the outside
`Suction and discharge valve bores outwardly with respect to
`their plunger bore axis, to enable the volume of each of the
`Suction and discharge valve bores to be increased. Thus, with
`an increased pump speed, an increased Volumetric flow can be
`achieved with a pump that still has a similar overall dimen
`sional profile. In addition, JP 2000-170643 teaches that the
`valve bores are moved outwardly without increasing the
`amount of material between the Suction and discharge bores.
`This is because the reconfiguration of the pump in JP 2000
`170643 is not concerned with reducing stresses within the
`pump in use.
`
`SUMMARY
`
`In a first aspect there is disclosed a fluid end for a multiple
`reciprocating pump assembly. The multiple reciprocating
`pump assembly may, for example, comprise three or five
`plunger bores, and may find application in oilfield operations
`and/or may operate with fluids at high pressures (for example
`as high as 20,000 psi or greater).
`When the fluid end comprises at least three plunger bores
`(for example, three or five plunger bores), each can receive a
`reciprocating plunger, and each can have a plunger bore axis.
`The plunger bores can be arranged across the fluid head to
`define a central plungerbore and lateral plungerbores located
`on either side of the central plungerbore (for example, one or
`two lateral plunger bores located on either side of the central
`plunger bore to define a fluid end with three or five plunger
`bores respectively).
`At least three respective suction valve bores (for example,
`three or five suction valve bores) can be provided for and be
`in fluid communication with the plunger bores. Each Suction
`valve bore can receive a suction valve and have a Suction valve
`bore axis.
`At least three respective discharge valve bores (for
`example, three or five discharge valve bores) can be provided
`for and be in fluid communication with the plunger bores.
`Each discharge valve bore can receive a discharge valve and
`have a discharge valve bore axis.
`In accordance with the first aspect, at least one of the axes
`of the suction and discharge valve bores, for at least one of the
`lateral plunger bores, is inwardly offset in the fluid end from
`its respective plunger bore axis.
`It has been surprisingly discovered that this inward offset
`ting can reduce stress that would otherwise occur at the inter
`section of each plunger bore with its Suction or discharge
`valve bores as the plunger moves to TDC. The reduction of
`stress can increase the useful operating life of the fluid end.
`In certain embodiments, at least one of the axes of at least
`one of the suction and discharge valve bores for each of the
`lateral plungerbores may be inwardly offset. For example, for
`the lateral plunger bores, the at least one offset axis may be
`inwardly offset to the same extent as the other at least one
`offset axis.
`In certain embodiments, the axes of both the suction and
`discharge valve bores may be inwardly offset for at least one
`of the lateral plunger bores. For example, the axes of both the
`suction and discharge valve bores are inwardly offset to the
`Same eXtent.
`In certain embodiments, for each of the plunger bores, the
`Suction valve bore may oppose the discharge valve bore. This
`arrangement is easier to manufacture, maintain and service
`than, for example, arrangements in which the axis of each
`Suction valve bore is perpendicular to the discharge valve
`
`Page 16 of 23
`
`
`
`US 8,662,865 B2
`
`3
`bore. In addition, the opposing bore arrangement may induce
`less stress in the fluid end in use than, for example, a perpen
`dicular bore arrangement.
`In certain embodiments for each of the plunger bores, the
`axes of the Suction and discharge valve bores may be aligned,
`for even greater ease of manufacture, maintenance and Ser
`vice. In certain embodiments, the at least one axis may be
`inwardly offset in an amount ranging from about 10% to
`about 60% of the diameter of the plungerbore. In certain other
`embodiments, the offset axis may be inwardly offset in an
`amount ranging from about 20% to about 50%, or from about
`30% to about 40%, of the diameter of the plunger bore.
`In other certain embodiments, the at least one axis may be
`inwardly offset in an amount ranging from about 0.5 to about
`2.5 inches. In certain other embodiments, the offset axis may
`be offset in an amount ranging from about 1.5 to 2.5 inches.
`These dimensions may represent an optimal range for many
`bore diameters of fluid end configurations employed infrack
`ing pumps in oilfield and related applications.
`Other aspects, features, and advantages will become appar
`ent from the following detailed description when taken in
`conjunction with the accompanying drawings, which are a
`part of this disclosure and which illustrate, by way of
`example, principles of the fluid end as disclosed herein.
`DESCRIPTION OF THE FIGURES
`
`4
`just the lateral suction valve bores are inwardly offset from
`their respective plunger bores, and not the discharge valve
`bores.
`FIG.9 schematically depicts a first embodiment of a quint,
`being a partial section of FIG. 1A taken on the line 2-2, to
`illustrate the two lateral valve bore pairs on either side of the
`central valve bore pair being offset inwardly from their
`respective plunger bores.
`FIG. 10 is an underside schematic view of the section of
`FIG. 9 to show a bolt pattern on a fluid end of a cylinder.
`FIG. 11 is a similar view of the quint of FIG. 9, but illus
`trates just the outermost lateral valve bore pairs being offset
`inwardly from their respective plunger bore.
`FIG. 12 is a similar view of the quint of FIG. 11, but
`illustrates just one of the outermost lateral valve bore pairs
`being offset inwardly from its respective plunger bore.
`FIG. 13 is a similar view of the quint of FIG.9, but illus
`trates just the innermost lateral valve bore pairs being offset
`inwardly from their respective plunger bore.
`FIG. 14 is a similar view of the quint of FIG. 13, but
`illustrates just one of the innermost lateral valve bore pairs
`being offset inwardly from its respective plunger bore.
`FIGS. 15 and 16 schematically depict side sectional eleva
`tions as generated by finite elementanalysis (FEA), and taken
`from opposite sides, through a triplex fluid end, to illustrate
`where maximum stress, as indicated by FEA, occurs for the
`intersection of a plunger bore with the Suction and discharge
`valve bores; with FIG. 15 showing no offset and FIG. 16
`showing 2 inches inward offset.
`FIG. 17 is a data point graph that plot Von Mises yield
`criterion (that is, for the maximum stress, in psi, as deter
`mined by FEA) against the amount of valve bore offset (in
`inches) for a single (mono) fluid end and valve bore inward
`offset for a triplex fluid end.
`FIG. 18 is a bar graph that plots Von Mises yield criterion
`(that is, for the maximum stress, in psi, as determined by
`FEA) against different amounts of valve bore offset (in
`inches) for a single (mono) fluid end and a triplex fluid end.
`DETAILED DESCRIPTION OF SPECIFIC
`EMBODIMENTS
`
`Referring to FIGS. 1A and 1B, an embodiment of a recip
`rocating pump 12 housed within a crankshaft housing 13 is
`shown. The crankshaft housing 13 may comprise a majority
`of the outer Surface of reciprocating pump 12. Stay rods 14
`connect the crankshaft housing 13 (the so-called “power
`end') to a fluid end 15. When the pump is to be used at high
`pressures (for instance, in the vicinity of 20,000 psi or
`greater), up to four stay rods can be employed for each
`plunger of the multiple reciprocating pump. The stay rods
`may optionally be enclosed in a housing.
`The pump 12 is a triplex having a set of three cylinders 16,
`each including a respective plungerbore 17. The three (or, in
`the case of a quint, five) cylinders/plunger bores can be
`arranged transversely across the fluid end 15. A plunger 35
`reciprocates in a respective plunger bore 17 and, in FIG. 1A,
`the plunger 35 is shown fully extended at its top dead centre
`position. In the embodiment depicted, fluid is only pumped at
`one side 51 of the plunger 35, therefore the reciprocating
`pump 12 is a single-acting reciprocating pump.
`Each plunger bore 17 is in communication with a fluid inlet
`or suction manifold 19 and a fluid outlet side 20 in commu
`nication with a pump outlet 21 (FIG. 1B). A suction cover
`plate 22 for each cylinder 16 and plunger bore 17 is mounted
`to the fluid end 15 at a location that opposes the plunger bore
`17. The pump 12 can be freestanding on the ground, can be
`
`10
`
`15
`
`25
`
`30
`
`35
`
`Notwithstanding any otherforms which may fall within the
`scope of the fluid end as set forth in the Summary, specific
`embodiments of the fluid end and reciprocating pump will
`now be described, by way of example only, with reference to
`the accompanying drawings.
`In the Description of the Figures and in the Detailed
`Description of Specific Embodiments, a pump that comprises
`three plunger, Suction and discharge bores is hereafter
`referred to as a “triplex’, and a pump that comprises five
`plunger, Suction and discharge bores is hereafter referred to as
`a “quint', being an abbreviation of “quintuplex.”
`In the drawings:
`FIGS. 1A and 1B illustrate, in sectional and perspective
`40
`views, an embodiment of a reciprocating pump. FIG. 1A may
`depict either a triplex or quint, although FIG. 1B specifically
`depicts a triplex.
`FIG. 2 schematically depicts a first embodiment of a tri
`plex, being a partial section of FIG. 1A taken on the line 2-2,
`to illustrate both lateral (or outside) valve bore pairs being
`offset inwardly from their respective plunger bores.
`FIG. 3 is an underside schematic view of the section of
`FIG. 2 to show a bolt pattern on a fluid end of a cylinder.
`FIG. 4 is a similar view of the triplex to FIG. 2, but illus
`trates just one of the lateral (or outside) valve bore pairs being
`offset inwardly from its respective plunger bore.
`FIG. 5 schematically depicts another embodiment of a
`triplex but using a partial section similar to FIG. 2 to illustrate
`one of the lateral valve bores being inwardly offset to its
`respective plunger bore, as well as the central valve bore
`being offset in a similar direction to its respective plunger
`bores.
`FIG. 6 is an underside schematic view, of the section of
`FIG. 5 to show a bolt pattern on a fluid end of a cylinder.
`FIG. 7 schematically depicts another embodiment of a
`triplex using a partial section similar to FIG. 2, and wherein
`just the lateral discharge valve bores are inwardly offset from
`their respective plunger bores, and not the Suction valve
`bores.
`FIG. 8 schematically depicts another embodiment of a
`triplex using a partial section similar to FIG. 2, and wherein
`
`45
`
`50
`
`55
`
`60
`
`65
`
`Page 17 of 23
`
`
`
`5
`mounted, to a trailer that can be towed between operational
`sites, or mounted to a skid such as for offshore operations.
`A crankshaft housing 13 encloses a crankshaft 25, which
`can be mechanically connected to a motor (not shown). The
`motor rotates the crankshaft 25 in order to drive the recipro
`cating pump 12. In one embodiment, the crankshaft 25 is
`cammed so that fluid is pumped from each cylinder 16 at
`alternating times. As is readily appreciable by those skilled in
`the art, alternating the cycles of pumping fluid from each of
`the cylinders 16 helps minimize the primary, secondary, and
`tertiary (et al.) forces associated with the pumping action.
`A gear 24 is mechanically connected to the crankshaft 25,
`with the crankshaft 25 being rotated by the motor (not shown)
`through gears 26 and 24. A crank pin 28 attaches to the main
`shaft 23, shown substantially parallel to axis A of the crank
`shaft 25. A connector rod 27 is connected to the crankshaft 25
`at one end. The other end of connector rod 27 is secured by a
`bushing to a crosshead or gudgeon pin 31, which pivots
`within a crosshead 29 in housing 30 as the crankshaft 25
`rotates at the one end of the connector rod 27. The pin 31 also
`functions to hold the connector rod 27 longitudinally relative
`to the crosshead 29. A pony rod 33 extends from the crosshead
`29 in a longitudinally opposite direction from the crankshaft
`25. The connector rod 27 and the crosshead 29 convert rota
`tional movement of the crankshaft 25 into longitudinal move
`ment of the pony rod 33.
`The plunger 35 is connected to the pony rod 33 for pump
`ing the fluid passing through each cylinder 16. Each cylinder
`16 includes an interior or cylinder chamber 39, which is
`where the plunger 35 compresses the fluid being pumped by
`reciprocating pump 12. The cylinder 16 also includes an inlet
`(or suction) valve 41 and an outlet (or discharge) valve 43.
`Usually the inlet and outlet valves 41, 43 are arranged in an
`opposed relationship in cylinder 16 and may, for example, lie
`on a common axis,
`The valves 41 and 43 are usually spring-loaded and are
`actuated by a predetermined differential pressure. The inlet
`(suction) valve 41 actuates to control fluid flow from the fluid
`inlet 19 into the cylinder chamber 39, and the outlet (dis
`charge) valve 43 actuates to control fluid flow from the cyl
`inder chamber 39 to the outlet side 20 and thence to the pump
`outlet 21. Depending on the size of the pump 12, the plunger
`35 may be one of a plurality of plungers, for example, three or
`five plungers may be utilized.
`The plunger 35 reciprocates, or moves longitudinally,
`toward and away from the chamber 39, as the crankshaft 25
`rotates. As the plunger 35 moves longitudinally away from
`the cylinder chamber 39, the pressure of the fluid inside the
`chamber 39 decreases, creating a differential pressure across
`the inlet valve 41, which actuates the valve 41 and allows the
`fluid to enter the cylinder chamber 39 from the fluid inlet 19.
`The fluid continues to enter the cylinder chamber 39 as the
`plunger 35 continues to move longitudinally away from the
`cylinder 17 until the pressure difference between the fluid
`inside the chamber 39 and the fluid in the fluid inlet 19 is small
`enough for the inlet valve 41 to actuate to its closed position.
`As the plunger 35 begins to move longitudinally into the
`cylinder 16, the pressure on the fluid inside of the cylinder
`chamber 39 begins to increase. Fluid pressure inside the cyl
`inder chamber 39 continues to increase as the plunger 35
`approaches the chamber 39 until the differential pressure
`across the outlet valve 43 is large enough to actuate the valve
`43 and allow the fluid to exit the chamber 39 through the fluid
`outlet 21.
`The inlet valve 41 is located within a suction
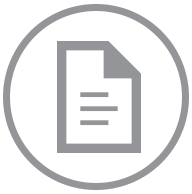
Accessing this document will incur an additional charge of $.
After purchase, you can access this document again without charge.
Accept $ ChargeStill Working On It
This document is taking longer than usual to download. This can happen if we need to contact the court directly to obtain the document and their servers are running slowly.
Give it another minute or two to complete, and then try the refresh button.
A few More Minutes ... Still Working
It can take up to 5 minutes for us to download a document if the court servers are running slowly.
Thank you for your continued patience.
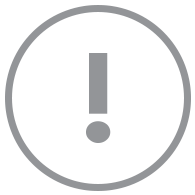
This document could not be displayed.
We could not find this document within its docket. Please go back to the docket page and check the link. If that does not work, go back to the docket and refresh it to pull the newest information.
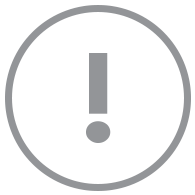
Your account does not support viewing this document.
You need a Paid Account to view this document. Click here to change your account type.
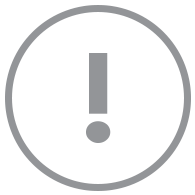
Your account does not support viewing this document.
Set your membership
status to view this document.
With a Docket Alarm membership, you'll
get a whole lot more, including:
- Up-to-date information for this case.
- Email alerts whenever there is an update.
- Full text search for other cases.
- Get email alerts whenever a new case matches your search.
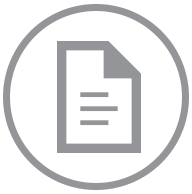
One Moment Please
The filing “” is large (MB) and is being downloaded.
Please refresh this page in a few minutes to see if the filing has been downloaded. The filing will also be emailed to you when the download completes.
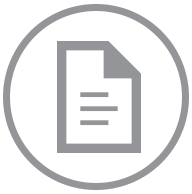
Your document is on its way!
If you do not receive the document in five minutes, contact support at support@docketalarm.com.
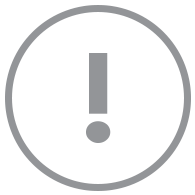
Sealed Document
We are unable to display this document, it may be under a court ordered seal.
If you have proper credentials to access the file, you may proceed directly to the court's system using your government issued username and password.
Access Government Site