`
`APPLICATION
`
`PUBLISHED
`
`UNDER THE PATENT COOPERATION
`
`TREATY (PCT)
`
`(19) World Intellectual Property Organization
`International Bureau
`
`(43) International Publication Date
`28 January 2010 (28.01.2010)
`
`(51) International Patent Classification:
`5262) 7/06 (2006.01)
`
`(21) International Application Number:
`PCT/US2008/080809
`
`(22) International Filing Date:
`
`(25) Filing Language:
`
`(26) Publication Language:
`
`22 October 2008 (22.10.2008)
`
`English
`
`English
`
`(30) Priority Data:
`60/999,961
`61/000,202
`12/255,661
`
`22 October 2007 (22.10.2007)
`2 3 October 2007 (23.10.2007)
`2 1 October 2008 (21 .10.2008)
`
`U S
`U S
`U S
`
`(71) Applicant (for all designated States except US): FOR-
`INC.
`MAX,
`[US/US];
`9150
`191st Street, Mokena,
`IL
`60448 (US).
`
`(72) Inventors; and
`(75) Inventors/Applicants (for US only): LINDEE, Scott, A .
`[US/US]; C/o Formax,
`Inc., 9150 191st Street, Mokena,
`
`(10) International Publication Number
`WO 2010/011237 Al
`
`IL 60448 (US). SANDBERG, Glenn [US/US]; C/o For¬
`max,
`Inc., 9150 191st Street, Mokena,
`IL 60448 (US).
`PASEK,
`James,
`E .
`[US/US]; C/o Formax,
`Inc., 9150
`191st Street, Mokena,
`IL 60448 (US). LAMARTINO,
`Salvatore [US/US]; C/o Formax,
`Inc., 9150 19 1st Street,
`IL 60448 (US). HANSEN, David [US/US]; C/o
`Mokena,
`Formax,
`Inc., 9150 191st Street, Mokena,
`IL 60448 (US).
`WOLCOTT,
`Thomas, C . [US/US]; C/o Formax,
`Inc.,
`9150 191st Street, Mokena,
`IL 60448 (US). HANCOCK,
`David [US/US]; C/o Formax,
`Inc, 9150 191st Street, Mo¬
`kena, IL 60448 (US).
`
`(74) Agent: ERICKSON,
`T.; 1749 S. Naperville
`Randall,
`Rd., Suite 202, Wheaton,
`IL 60189 (US).
`
`(81) Designated States (unless otherwise indicated, for every
`kind of national protection available): AE, AG, AL, AM,
`AO, AT, AU, AZ, BA, BB, BG, BH, BR, BW, BY, BZ,
`CA, CH, CN, CO, CR, CU, CZ, DE, DK, DM, DO, DZ,
`EC, EE, EG, ES, FI, GB, GD, GE, GH, GM, GT, HN,
`HR, HU, ID, IL, IN, IS, JP, KE, KG, KM, KN, KP, KR,
`KZ, LA, LC, LK, LR, LS, LT, LU, LY, MA, MD, ME,
`MG, MK, MN, MW, MX, MY, MZ, NA, NG, NI, NO,
`
`[Continued on next page]
`
`(54) Title: MULTIPLE FOOD ARTICLE HIGH SPEED SLICING MACHINE
`
`FIG,
`
`(57) Abstract: A high
`and a
`apparatus
`slicing
`speed
`conveyor
`combination
`that pro¬
`weighing and classifying
`in productivity
`by enhancing por¬
`vides plural advantages
`food hygiene by implementing
`an
`tion control and yield,
`automated
`cleanup position,
`etc., and operation
`by em¬
`ploying a laser food article end detection system. The in¬
`vention
`provides
`a mechanism and method
`for
`slicing
`multiple
`food articles,
`independent
`of feed rate, and the
`ability to weigh each product group from each food article
`to achieve optimal weight control and yield of each food
`article.
`
`Weber EX1014
`IPR2020-01557
`U.S. Patent No. 10,639,812
`
`
`
`NZ, OM, PG, PH, PL, PT, RO, RS, RU, SC, SD, SE, SG,
`SK, SL, SM, ST, SV, SY, TJ, TM, TN, TR, TT, TZ, UA,
`UG, US, UZ, VC, VN, ZA, ZM, ZW.
`
`ES, FI, FR, GB, GR, HR, HU, IE, IS, IT, LT, LU, LV,
`MC, MT, NL, NO, PL, PT, RO, SE, SI, SK, TR), OAPI
`(BF, BJ, CF, CG, CI, CM, GA, GN, GQ, GW, ML, MR,
`NE, SN, TD, TG).
`
`(84) Designated States (unless otherwise indicated, for every
`kind of regional protection available): ARIPO (BW, GH, Published:
`GM, KE, LS, MW, MZ, NA, SD, SL, SZ, TZ, UG, ZM, — with international search report (Art. 21(3))
`ZW), Eurasian (AM, AZ, BY, KG, KZ, MD, RU, TJ,
`TM), European (AT, BE, BG, CH, CY, CZ, DE, DK, EE,
`
`
`
`Multiple Food Article High Speed Slicing Machine
`
`BACKGROUND OF THE INVENTION
`
`Many different kinds of food articles or food products, such as food slabs, food
`
`bellies, or food loaves are produced in a wide variety of shapes and sizes. There are meat
`
`loaves made from various meats, including ham, pork, beef, lamb, turkey, and fish. The meat
`
`in the food loaf may be in large pieces or may be thoroughly comminuted. These meat
`
`loaves come in different shapes (round, square, rectangular, oval, etc.) and in different
`
`lengths up to six feet (183 cm) or even longer. The cross-sectional sizes of the loaves are
`
`quite different; the maximum transverse dimension may be as small as 1.5 inches (4 cm) or
`
`as large as ten inches (25.4 cm). Loaves of cheese or other foods come in the same great
`
`ranges as to composition, shape, length, and transverse size.
`
`Typically the food loaves are sliced, the slices are grouped in accordance with a
`
`particular weight requirement, and the groups of slices are packaged and sold at retail. The
`
`number of slices in a group may vary, depending on the size and consistency of the food
`
`article and the desire of the producer, the wholesaler, or the retailer. For some products,
`
`neatly aligned stacked slice groups are preferred. For others, the slices are shingled or folded
`
`so that a purchaser can see a part of every slice through a transparent package.
`
`Food articlescan be sliced on high speed slicing machines such as disclosed in U.S.
`
`Patents 5,628,237 or 5,974,925 or as commercially available as the FXl 80® slicer available
`
`from Formax, Inc. of Mokena, Illinois, USA.
`
`The FXl 80® machine can be configured as an automatically loaded, continuous feed
`
`machine, or an automatically loaded, back-clamp or gripper type machine.
`
`
`
`For an automatically loaded, continuous feed machine, side-by-side upper and lo ver
`
`conveyor pairs drive food articles into the cutting plane. A gate is located in front of the
`
`conveyors. The initial food articles are loaded with leading ends abutting the gate. The gate is
`
`lowered and the food articles proceed into the conveyors. When the initial food articles are
`
`sliced to the extent that the trailing ends of the food articles clear the gate, the gate is raised
`
`and new food articles are loaded in the feed paths, held back by the gate. Shortly thereafter
`
`the gate is lowered and new food articles slide down to where lead ends of the new food
`
`articles abut trailing ends of the initial food articles being sliced. The new food articles are
`
`driven into the cutting plane trailing the initial food articles. Food articles are sequentially
`
`and continuously loaded in this manner, lead end-to-trailing end, in abutting contact with the
`
`preceding food articles.
`
`U.S. Patent 5,628,237 and European patent EP 0 713 753 describe a back-clamp or
`
`gripper type slicing machine. According to this type of slicing machine, two food articles are
`
`loaded onto a lift tray and the lift tray is raised to a ready-to-sweep position. Two loaf
`
`grippers are retracted after the previous food articles are sliced. During retraction of the loaf
`
`grippers, loaf-to-slicing blade gate doors are closed and ends of the previous food articles are
`
`dropped through a loaf end door. After the grippers have reached the retracted position or
`
`"home position" remote from the slicing blade, a loaf sweep mechanism is activated, moving
`
`the food articles laterally together into the slicing position. A spacing mechanism moves
`
`down and spaces the food articles apart. The grippers then advance after it has been
`
`determined that the loaf sweep mechanism has moved the food articles to the slicing
`
`position. The grippers have onboard sensing mechanisms that are triggered by contact with
`
`the food articles. After sensing and gripping the food articles, the food articles are retracted
`
`slightly, and the loaf-to-slicing blade gate doors are opened and the food articles are
`
`
`
`advanced to the slicing plane of the slicing blade. The loaf sweep mechanism retracts and the
`
`loaf lift tray lowers, ready for the next reload cycle. According to this design, in practice, the
`
`reload cycle is accomplished in about eight seconds. In a high volume slicing operation,
`
`reload cycle time can be a significant limitation to optimum production efficiency.
`
`In either configuration the FXl 80® slicing machine has achieved great commercial
`
`success. However, the present inventors have recognized that it would be desirable to slice
`
`up to four food articles or more with independent feeding and weighing capabilities, with
`
`hygienic and operational enhancements.
`
`SUMMARY OF THE INVENTION
`
`The invention provides a mechanism and method for slicing multiple food articles
`
`with independency of feed rate and the ability to weigh each product group from each food
`
`article respectively to
`
`optimal weight control and yield of each food article.
`
`The present invention provides a high speed slicing apparatus and a weighing and
`
`classifying conveyor combination that provides plural advantages in productivity, food
`
`hygiene, and operation.
`
`The combination provides food hygiene advantages by use of unibody construction
`
`with minimal penetrations, double sealed door closures, self draining angled surfaces, the use
`
`of hygienic, round, sealed adjustable legs, the use of an automatic debris or scrap removal
`
`conveyor, a hygienic configuration of a food article lift and sweep mechanism. Further, the
`
`combination provides an automated cleanup position wherein, the elevated food article feed
`
`mechanism can be collapsed to a more convenience plane or maintenance position, the
`
`weighing and classifying conveyor is oriented at a distance from the slicing apparatus for
`
`ease of cleanup and maintenance, and the blade cover is automatically lifted to a cleanup
`
`
`
`position. The weighing and classifying conveyor includes way conveyor belts that are
`
`separable from their respective drive motors for ease of cleaning and maintenance.
`
`Additionally, all product contact conveyor belts throughout
`
`the combination are easily
`
`removable.
`
`The combination provides for enhanced portion control and yield. A food article
`
`feed mechanism ensures accurate feeding by the use of servo driven and controlled feed
`
`belts and grippers. The slicing mechanism includes up to four independent drives for slicing
`
`four or more food articles simultaneously. An enhanced food article gate swing is withdrawn,
`
`not laterally but longitudinally toward the knife blade to ease the food articles toward the
`
`slicing plane.
`
`Operationally, food article grippers are provided which minimize the longitudinal
`
`length of remainder ends of sliced food articles. In this regard, food article sensors have
`
`been removed from the grippers and a laser food article end detection system is employed
`
`which allows for a more compact, smaller-bite gripper.
`
`A mechanism is provided to retract the slicing blade from the slicing plane during
`
`the dwell between sliced groups to prevent scrap generation. Further, a mechanism is
`
`provided to both dynamically and mechanically brake the slicing blade to a quick stop.
`
`Laser intrusion detectors are used to shut down systems when an unwanted intrusion
`
`by an operator is detected.
`
`An onboard information carrier system utilizing a RFID target and a read/write head
`
`is provided on the slicing blade and the shear support to simplify equipment set up,
`
`operation and maintenance.
`
`An automated, sequenced food article tray loading method and apparatus is provided
`
`wherein food articles can be loaded sequentially into the lift tray into designated and
`
`
`
`separated lanes which automatically sequentially assume a preload condition, and after the
`
`food articles are loaded, food article separation is maintained on the lift tray. A food article
`
`transfer mechanism or sweep mechanism is provided which receives the food articles on the
`
`lift tray in their separated positions and transfers the food articles into the food article feed
`
`mechanism while maintaining the separated positions.
`
`A stack/draft completion feature is possible with the apparatus of the invention
`
`wherein incomplete stacks/drafts can be moved from the jump conveyor to the deceleration
`
`conveyor and new food article scrap can be offloaded to the scrap or debris conveyor for
`
`disposal. The incomplete stacks/drafts can then be reloaded to the jump conveyor for
`
`completion of the stacks /drafts.
`
`Two involute-shaped blade sizes are compatible with the slicing apparatus wherein a
`
`quick changeover between blade types is provided.
`
`The combination of the invention provides multiple configurations to slice, weigh
`
`and classifying 1, 2, 3, 4 or more food articles.
`
`Numerous other advantages and features of the present invention will become
`
`readily apparent from the following detailed description of the invention and the
`
`embodiments thereof, and from the accompanying drawings.
`
`BRIEF DESCRIPTION OF THE DRAWINGS
`
`Figure 1 is a near side elevational view of a slicing machine and a weighing and
`
`classifying conveyor combination of the present invention;
`
`Figure 2 is an elevational view of the combination of figure 1 with some panels
`
`removed or made transparent illustrating some underlying components;
`
`
`
`Figure 3 is an elevational view of the combination of figure 1 with further panels
`
`removed or made transparent and underlying components revealed;
`
`Figure 4 is a rear view of the combination shown in figure 3;
`
`Figure 4A is an elevational view of the combination of figure 1 in a clean-up, non-
`
`operational position;
`
`Figure 4B is a fragmentary, elevational, enlarged view of a portion of the slicing
`
`machine shown in figure 1;
`
`Figure 5 is a far side elevational view of the combination shown in figure 1;
`
`Figure 6 is a far side perspective view of the combination shown in figure 5;
`
`Figure 7 is a rear view of the combination shown in figure 3;
`
`Figure 8 is an enlarged, fragmentary near side elevational view of food article lift tray
`
`and food article positioning systems;
`
`Figure 8A is an enlarged fragmentary sectional view taken generally along line 8A-8A
`
`of Figure 9;
`
`Figure 9 is a fragmentary plan view of a food article lift tray;
`
`Figure 10 is a rear view of the food article lift tray shown in figure 9;
`
`Figure 11 is a rear view of the food article lift tray and food article transfer apparatus;
`
`Figure 12 is a fragmentary perspective view of the food article lift tray and food
`
`article transfer apparatus;
`
`Figure 12A is an enlarged elevational view of the food article transfer apparatus;
`
`Figure 13 is a plan view of the food article transfer apparatus;
`
`Figure 14 is a plan view of the food article feed apparatus;
`
`Figure 15 is an elevational view of the food article feed apparatus shown in figure 14;
`
`Figure 15A is a sectional view taken generally along line 15A-15A;
`
`
`
`Figure 16 is an elevational \iew of the food article feed apparatus;
`
`Figure 17 is a plan view of a gripper taken from the food article feed apparatus of
`
`figure 16;
`
`Figure 17A is a front view of the gripper taken generally along line 17A-17A of
`
`figure 17;
`
`Figure 18 is a sectional view taken generally along line 18-18 of figure 17A,
`
`Figure 19 is a fragmentary perspective view of the food article feed apparatus;
`
`Figure 20 is an enlarged sectional view of the attachment of the gripper to the belt;
`
`Figure 2 1 is a sectional view taken generally along line 20-20 of figure 16;
`
`Figure 22 is a sectional view taken generally along line 22-22 of figure 21;
`
`Figure 23 is a sectional view taken generally along line 23-23 of figure 21;
`
`Figure 24 is a plan view taken along line 24-24 figure 21;
`
`Figure 25 is an elevational \iew taken generally along line 25-25 of figure 24;
`
`Figure 26 is a fragmentary elevational view of a food article gate mechanism;
`
`Figure 27 is a near side perspective view of the food article gate mechanism and a
`
`food article end removal mechanism in a first operative position;
`
`Figure 28 is a near side perspective view of the food article gate mechanism and the
`
`food article end removal mechanism in a second operative position;
`
`Figure 29 is a far side perspective view of the food article end removal mechanism;
`
`Figure 30 is a top far side perspective view of the food article end removal
`
`mechanism;
`
`Figure 3 1 is a far side
`
`view of the food article gate mechanism and the food
`
`article end removal mechanism,
`
`Figure 32 is a sectional view taken generally along line 32-32 of figure 2;
`
`
`
`Figure 33 is a sectional view taken generally along line 33-33 of figure 32,
`
`Figure 33A is a sectional view taken generally along line 33A-33A of figure 33,
`
`Figure 34 is a perspective view of a portion of a slicing blade assembly taken from
`
`figure 32,
`
`Figure 35 is a sectional view taken generally along line 35-35 of figure 32,
`
`Figure 36 is a sectional view taken generally along line 36-36 of figure 32,
`
`Figure 37 is an enlarged fragmentary far side elevational view of the combination of
`
`figure 1 showing underlying components and features,
`
`Figure 38 is an enlarged fragmentary near side elevational view of the combination of
`
`figure 1 showing underlying components and features,
`
`Figure 39 is a plan view of mechanical components within the base section of the
`
`combination shown in figure 1,
`
`Figure 40 is a bottom perspective view of the lift tray and food article feed apparatus,
`
`Figure 4 1 is a far side perspective view of a front portion of the combination of
`
`figure 1,
`
`Figure 42 is a near side perspective view of a food article positioning apparatus and
`
`food article feed elevation adjusting apparatus,
`
`Figure 43 is a near side perspective view of a food article shear support,
`
`Figure 44 is a front elevational view of the shear support shown in figure 43,
`
`Figure 44A is a front elevational view of a slicing blade with respect to the shear
`
`support,
`
`Figure 44B is a sectional view taken generally along line 44B-44B of figure 44A,
`
`Figure 44C is a sectional view of a jump conveyor drive assembly taken generally
`
`along line 44C-44C of figure 35,
`
`
`
`Figure 45 is a front perspective view of the slicing apparatus with the weighing and
`
`classifying conveyor removed,
`
`Figure 46 is a near side perspective view of a front portion of the slicing apparatus
`
`with a cover removed to view inside components,
`
`Figure 46A is a near side elevational view of the slicing apparatus showing underlying
`
`components,
`
`Figure 47 is a far side of elevational view of the slicing apparatus showing underlying
`
`components,
`
`Figure 48 is a front elevational view of the slicing apparatus with the weighing and
`
`classifying conveyor removed;
`
`Figure 49 is a enlarged near side perspective view of the slicing apparatus;
`
`Figure 50 is an enlarged near side perspective view of the slicing apparatus and
`
`weighing and classifying conve}or,
`
`Figure 5 1 a is a diagrammatic plan view of a onboard information system according
`
`to one aspect of the invention,
`
`Figure 52 is a diagrammatic sectional view of the onboard information system taken
`
`generally along line 52-52 of figure 51,
`
`Figure 53 is a far side perspective view of a laser guard system according to another
`
`aspect of the invention,
`
`Figure 54 is a near side perspective view of the laser guard system,
`
`Figure 55 is a near side elevation view of the weighing and classifying conveyor of
`
`figure 1 showing underlying components,
`
`Figure 56 is a perspective view of a portion of a weighing conveyor with the
`
`conveyor belt and rollers removed,
`
`
`
`Figure 57 is a bottom view of a weighing conveyor belt with frame and rollers
`
`removed from the weighing conveyor shown in figure 56;
`
`Figure 58 is an enlarged elevational view of a portion of the weighing and classifying
`
`conveyor;
`
`Figure 59 is a near side elevation view of the weighing and classifying conveyor
`
`shown in a clean-up position;
`
`Figure 60 is a far side elevational view of the weighing and classifying conveyor;
`
`Figure 6OA is an end view of the weighing and classifying conveyor showing
`
`underlying components,
`
`Figure 6OB is a plan view of the weighing and classifying conveyor;
`
`Figure 6 1 is a schematic representation of the combination of figure 1 showing a
`
`four food article set up;
`
`Figure 62 is a schematic representation of the combination of figure 1 showing a
`
`three food article set up;
`
`Figure 63 is a schematic representation of the combination of figure 1 showing a two
`
`food article set up,
`
`Figure 64 is a progressive schematic diagram showing the loading of four food
`
`articles onto a food article lift tray;
`
`Figure 65 is a schematic plan view showing the weighing and classifying conveyor
`
`configured for four lanes of sliced product,
`
`Figure 66 is a schematic plan view showing the weighing and classifying conveyor
`
`configured for two lanes of sliced product;
`
`Figure 67 is a schematic plan view showing the weighing and classifying conveyor
`
`configured for one lane of sliced product ;
`
`
`
`Figure 68 is a schematic plan view showing the weighing and classifying conveyor
`
`configured for three lanes of sliced product
`
`;
`
`Figure 69 (not used)
`
`Figure 70 is a schematic rear end view of the food article lift tray showing the tray
`
`configured to hold four square cross section food articles;
`
`Figure 7 1 is a schematic rear end view of the food article lift tray showing the tray
`
`configured to hold four circular cross section food articles;
`
`Figure 72 is a schematic rear end view of the food article lift tray showing the tray
`
`configured to hold four large D-shaped food articles;
`
`Figure 73 is a schematic and view of the food article lift tray showing the tray
`
`configured to hold for large rectangular cross section food articles;
`
`Figure 74 is a schematic and view of the food article lift tray showing the tray
`
`configured to hold two large prone rectangular food articles;
`
`Figure 75 is a schematic elevational view of a round knife blade to be used with the
`
`apparatus of the present inv ention;
`
`Figure 76 is a schematic elevational view of an involute- shaped knife blade for slicing
`
`large food articles to be used with the apparatus of the present invention,
`
`Figure 77 is a schematic elevational view of an involute- shaped knife blade for slicing
`
`small food articles to be used with the apparatus the present in\ ention;
`
`Figure 78 is a near side elevational view of a laser guard system of the present
`
`invention;
`
`Figure 79 is a sectional view taken generally along line 79-79 of figure 78,
`
`Figure 80 is a plan view of a rear portion of the weighing classifying conveyor;
`
`Figure 8 1 is in elevation view taken generall}- along line 81-81 of figure 80;
`
`
`
`Figure 82 is a plan view of the rear portion of the weighing and classifying conveyor
`
`of figure 80 with deceleration conveyor belts removed for clarity, and
`
`Figure 83 is an exploded view of a portion of the deceleration conveyor taken from
`
`figure 82.
`
`DESCRIPTION OF THE PREFERRED EMBODIMENTS
`
`While this invention is susceptible of embodiment
`
`in many different forms, there are
`
`shown in the drawings, and will be described herein in detail, specific embodiments thereof
`
`with the understanding that the present disclosure is to be considered as an exemplification
`
`of the principles of the invention and is not intended to limit the invention to the specific
`
`embodiments illustrated.
`
`U.S. Patent Application No. 60/999,961 filed on October 22, 2007 and U.S. Patent
`
`Application No. 61/000,202 filed on October 23, 2007 are both herein incorporated by
`
`reference.
`
`Figures 1-3 illustrate a high speed slicing apparatus 100 and a weighing and
`
`classifying conveyor or output conveyor 102 according to a preferred embodiment of the
`
`invention. The slicing apparatus 100 includes a base section 104, a collapsible frame 105, an
`
`automatic food article loading apparatus 108 that receives food articles 110 to-be-sliced, a
`
`food article feed apparatus 120, a food article feed elevation adjusting apparatus 121, a food
`
`article end removal apparatus 122 (Figure 27), a laser safety guard system 123, a slicing head
`
`apparatus 124, and a slice receiving apparatus 130. The slicing apparatus also includes a
`
`computer display touch screen 131 that is pivotally mounted on and supported by a support
`
`132.
`
`
`
`The apparatus 100 can also include an onboard information carrier system 135
`
`(Figures 51, 52) that allots installed parts to be tagged with an information read and write
`
`data carrier that can communicate control or maintenance or other information to machine
`
`control.
`
`Base Section
`
`The base section 104 includes a compartment 136 having side walls 138a, 138b, a
`
`bottom wall 140, and an inclined top wall 142. The apparatus 100 is supported on four
`
`adjustable feet 144. The compartment 136 has a tapered side profile from back to front
`
`wherein the top wall 142 slants down from back to front. The slanted orientation of the top
`
`wall 142 ensures water drainage off the top of the compartment 136.
`
`The adjustable feet 144 are shown in figure 4B. The feet include a cylinder 144a that
`
`is bolted to the bottom wall 140. The cylinder 144a includes an internal threaded bore 144b
`
`that receives a threaded portion 144f of a shaft 144c that is mounted on a foot base 144d.
`
`The shaft 144c includes a smooth portion 144g of below the threaded portion 144f. The
`
`smooth portion 144g is sealed to the cylinder 144a by an o-nng 144h carried inside the
`
`cylinderl44a. This design prevents threads from being exposed which can collect particles
`
`and spray water from clean up.
`
`The compartment 136 includes near side doors 152,154, far side doors 156, 158
`
`(figure 5), and a rear door 162 that permit access into the compartment or to modules
`
`normally within the compartment 136. The compartment 136 typically affords an enclosure
`
`for a computer, motor control equipment, a low voltage supply, and a high voltage supply
`
`and other mechanisms as described below. The compartment may also include a pneumatic
`
`supply or a hydraulic supply, or both (not shown).
`
`
`
`Base section 104 also includes a debris or scrap conveyor 170 that can be operated to
`
`slowly circulate at all times to remove food pieces or other debris that would otherwise
`
`collect on top of the top wall 142, and delivers the debris to a collector bucket 173 located
`
`below an output end 170a of the conveyor 170.
`
`The debris conveyor 170 is shown in Figures 45 and 47-50. The debris conveyor
`
`includes a belt 163 that circulates around a rear idle roller 164a, a front tensioning roller 164b
`
`and a drum motor roller 164c. The belt circulates against a front idle roller 164d. The rollers
`
`164b and 164c are supported by side plates 165a, 165b. The side plates 165a, 165b are fixed
`
`to support shafts 166a, 166b which are attached in cantilever fashion to a far side of the
`
`machine by a triangular base plate 167 that is fastened to end nuts 2066a, 2066b of the
`
`tubular shafts 2067a, 2067b described below. The cantilever mounting allows for the belt to
`
`be removed off the rollers at a near side of the machine for cleaning.
`
`Each of the rollers 164a, 164b, 164d are rotatably carried on a pair of bearings 168
`
`that have a block shaped outer contour 168a with a recessed square block shaped region
`
`168b. The square block shaped region 168b of each bearing 168 is configured to tightly fit
`
`within a respective support bracket 169a, 169b, 169c to removably support the respective
`
`roller. The outer contour 168a captures the respective support bracket 169a, 169b, 169c by
`
`sandwiching both sides of the respective bracket 169a, 169b, 169c. The support brackets
`
`169a are J-shaped hangers located on the far side and near side of the machine. The support
`
`brackets 169b, 169b are U-shaped brackets mounted to the side plate 165a at the far side of
`
`the machine and to the front of the compartment 136 at a near side of the machine. The
`
`support brackets 169c, 169c are formed as part of the side plates 165a, 165b and are open
`
`upward.
`
`
`
`A tensioning shaft 171 extends across the conveyor 170 below the roller 164b. The
`
`shaft 171 is connected to cams I 7 Ia, 171b at positions adjacent to and outside of the side
`
`plates 165a, 165b. At a near side of the machine a handle 171h is fixed to the shaft 171. The
`
`cams 171a, 171b ride against bottoms 168c of the rectangular block shaped contours 168a of
`
`the bearings 168. Each cam 171a, 171b has a substantially flat portion 171c on its cam
`
`surface that underlies the bottoms 168c to lock the roller 164b in an elevated position to
`
`tension the belt 173
`
`To tension the belt 163, the handle 171h is turned from the pointing down position
`
`shown in Fig. 46A to the pointing up position shown in Fig 46A, i.e., turned clockwise.
`
`Collapsible Frame and Elevated Housings
`
`The base section 104 supports the collapsible frame 105 as shown in Figs. 1-4A. The
`
`collapsible frame 105 includes a foldable support mechanism 17 4 that supports a food article
`
`feed mechanism frame 190.
`
`The foldable support mechanism 174 includes a servomotor 175 that drives a gear
`
`reducer 176 having a drive shaft 178 that extends out of the gear reducer 176 at opposite
`
`ends. The dnve shaft 178 is fixed to parallel levers 180a, 180b which swing out with a
`
`turning of the dnve shaft 178 The levers 180a, 180b are pivotally connected to parallel
`
`support columns 182a, 182b via an axle joint 184. The columns 182a, 182b are pivotally
`
`connected to the frame 190 which pivotally supports the food article feed apparatus 120 on
`
`an axle 192.
`
`The food article feed mechanism frame 190 also supports a sweep mechanism
`
`housing 194, a feed conveyor drive housing 196, and a end disposal housing 198, all on the
`
`
`
`far side of the apparatus, shown in figures 5 and 6 . The frame also supports the laser safety
`
`guard system 123.
`
`For cleaning and maintenance purposes, the collapsible frame 105 is collapsed down
`
`by actuating the servomotor 175 and gear reducer 176 to rotate the levers 180a, 180b, which
`
`draws down the columns 182a, 182b as the frame 190 rotates on the axle 192. The frame
`
`190, and all equipment supported thereby, is lowered for more convenient maintenance and
`
`cleaning as illustrated in Figure 4A. In some cases this eliminates the need for ladders or
`
`platforms when servicing the slicing apparatus 100.
`
`Automatic Food Article Loading Apparatus
`
`As illustrated in figure 7-9, the automatic food article loading apparatus 108 includes
`
`a lift tray assembly 220, a lift tray positioning apparatus 228 and a food article lateral transfer
`
`apparatus 236. The lift tray assembly 220 receives food articles to-be-sliced. The tray
`
`positioning apparatus 228 pivots the tray assembly 220 to be laterally adjacent to, and parallel
`
`with, the food article feed apparatus 120. The food article lateral transfer apparatus 236
`
`moves the food articles from the lift tray assembly 220 onto the food article feed apparatus
`
`120.
`
`Lift Tray Positioning Apparatus
`
`Figures 7 , 9 and 10 illustrate the food article lift tray assembly 220 includes a frame
`
`290 that supports four movable food article support plates 302, 304, 306, 308.
`
`As illustrated in figure 8, the frame 290 is connected by a rear connection 330 and a
`
`front connection 332 to a lever 336. The lever 336 is pivotally connected to a height
`
`adjustment bar 340 at a pivot connection 342. A servomotor 350 drives a gear reducer 351
`
`
`
`that has an output shaft 352 that is fixed to a crank arm 360. The crank arm 360 is pivotally
`
`connected to a lift arm 362 at a pivot connection 364. The lift arm 362 is pivotally connected
`
`to the lever 336 at a pivot connection 366.
`
`When the servomotor 350 turns the crank arm 360 via the gear reducer 351, the
`
`crank arm 360 is turned counterclockwise in Fig 8 and the lift arm 362 is elevated to pivot
`
`the lever 336 about the pivot connection 342. This pivots and elevated the rear end of the
`
`frame 290 and the food article lift tray assembly 220.
`
`Lift Tray Assembly
`
`As illustrated in figs. 9 and 10, the support plates 302, 304 are separated by a divider
`
`312. The support plates 304, 306 are separated by a divider 314. The support plates 306,308
`
`are separated by a divider 316. The dividers 312, 314, 316 are fixed with respect to the frame
`
`290. The support plates 302, 304, 306, 308 are movable in a perpendicular direction "P" to a
`
`length direction of the frame 290 (Fig. 8). When the frame 290 is horizontally oriented,
`
`direction "P" is substantially vertical.
`
`Each food article support plate 302, 304, 306, 308 is supported by a selective lift
`
`mechanism 326 described in Figs. 8, 9 and 40. Figure 8 discloses the selective lift mechanism
`
`326 for the support plate 302 with the understanding that the selective lift mechanism 326
`
`for each of the food article support plates 302, 304, 306, 308 is identical.
`
`The support plate 302 is fastened to two parallel lift bars 370, 372. Three swing
`
`levers 380, 382, 384 are pivotally connected to transverse shafts 388, 400, 402 of the frame
`
`290, at base ends 380a, 382a, 384a of the swing lexers 380, 382, 384, respectively. Distal ends
`
`380b, 382b, 384b of the swing levers 380, 382, 384, respectively, are pivotalh. connected to
`
`the two parallel lift bars 370, 372. A pneumatic cylinder 416 is prvotally connected at a first
`
`
`
`end 416a to a transverse strut 420 of the frame 290. The cylinder 416, particularly the
`
`cylinder rod 426, is pivotally connected at a second end
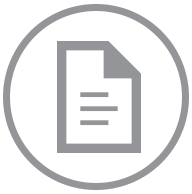
Accessing this document will incur an additional charge of $.
After purchase, you can access this document again without charge.
Accept $ ChargeStill Working On It
This document is taking longer than usual to download. This can happen if we need to contact the court directly to obtain the document and their servers are running slowly.
Give it another minute or two to complete, and then try the refresh button.
A few More Minutes ... Still Working
It can take up to 5 minutes for us to download a document if the court servers are running slowly.
Thank you for your continued patience.
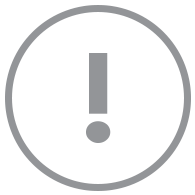
This document could not be displayed.
We could not find this document within its docket. Please go back to the docket page and check the link. If that does not work, go back to the docket and refresh it to pull the newest information.
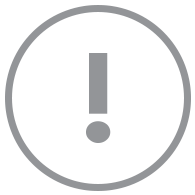
Your account does not support viewing this document.
You need a Paid Account to view this document. Click here to change your account type.
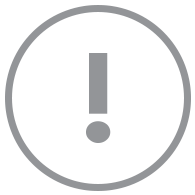
Your account does not support viewing this document.
Set your membership
status to view this document.
With a Docket Alarm membership, you'll
get a whole lot more, including:
- Up-to-date information for this case.
- Email alerts whenever there is an update.
- Full text search for other cases.
- Get email alerts whenever a new case matches your search.
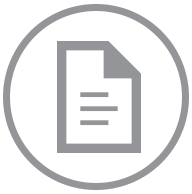
One Moment Please
The filing “” is large (MB) and is being downloaded.
Please refresh this page in a few minutes to see if the filing has been downloaded. The filing will also be emailed to you when the download completes.
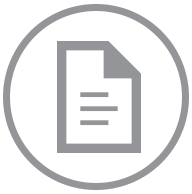
Your document is on its way!
If you do not receive the document in five minutes, contact support at support@docketalarm.com.
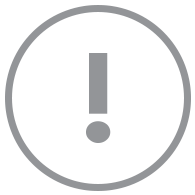
Sealed Document
We are unable to display this document, it may be under a court ordered seal.
If you have proper credentials to access the file, you may proceed directly to the court's system using your government issued username and password.
Access Government Site