`(12) Patent Application Publication (10) Pub. No.: US 2010/0307304 A1
`Weber
`(43) Pub. Date:
`Dec. 9, 2010
`
`US 20100307304A1
`
`(54) APPARATUS AND METHOD FOR THE
`SLCING OF FOOD PRODUCTS
`
`(75) Inventor:
`
`Guenther Weber, Gross Nemerow
`(DE)
`
`Correspondence Address:
`TOWNSEND AND TOWNSEND AND CREW,
`LLP
`TWO EMBARCADERO CENTER, EIGHTH
`FLOOR
`SAN FRANCISCO, CA 94111-3834 (US)
`
`(73) Assignee:
`
`Weber Maschinenbau GmbH
`Breidenbach, Breidenbach (DE)
`
`(21) Appl. No.:
`
`12/791,195
`
`(22) Filed:
`
`Jun. 1, 2010
`
`
`
`Foreign Application Priority Data
`(30)
`Jun. 3, 2009 (DE) ...................... 10 2009 O23 751.8
`Publication Classification
`
`(51) Int. Cl.
`(2006.01)
`B26D 706
`(52) U.S. Cl. ............................................ 83/13; 83/403.1
`(57)
`ABSTRACT
`An apparatus for the slicing of food products has a product
`feeder which includes a plurality of belt conveyors arranged
`parallel next to one another. The belt conveyors each include
`an endless belt serving as a product Support for a product to be
`sliced and they are drivable together in order simultaneously
`to feed a plurality of products which each lie on one of the
`belts to a cutting plane in which a cutting blade moves. The
`belt conveyors have a common drive with a drive shaft. For
`the setting of an individual single conveying speed for each
`belt conveyor, a respective setting apparatus is associated
`with them which is made to individually change the running
`diameter of the drive shaft in the region of the belt.
`
`Weber EX1007
`IPR2020-01557
`U.S. Patent No. 10,639,812
`
`
`
`Patent Application Publication
`
`Dec. 9, 2010 Sheet 1 of 4
`
`US 2010/0307304 A1
`
`17
`
`S
`
`an uwo dra - more run
`
`H.
`
`H. H.
`
`17.
`
`V
`
`11
`Ne
`
`15
`
`2s 28
`
`32
`
`25
`
`21
`
`F
`
`17.
`M5
`
`2O 15
`
`3O
`
`Fig. 1
`
`
`
`Patent Application Publication
`
`Dec. 9, 2010 Sheet 2 of 4
`
`US 2010/0307304 A1
`
`
`
`
`
`Patent Application Publication
`
`Dec. 9, 2010 Sheet 3 of 4
`
`US 2010/0307304 A1
`
`
`
`
`
`Patent Application Publication
`
`Dec. 9, 2010 Sheet 4 of 4
`
`US 2010/0307304 A1
`
`
`
`51
`
`Z 19
`
`
`
`US 2010/0307304 A1
`
`Dec. 9, 2010
`
`APPARATUS AND METHOD FOR THE
`SLCING OF FOOD PRODUCTS
`
`0001. The present invention relates to an apparatus and to
`a method for the slicing of food products.
`0002 Different types of food slicing apparatus are known
`in the prior art. For example, so-called high-performance
`slicers are used to slice food products Such as meat, sausage or
`cheese at a high cutting speed. In an endeavor further to
`increase the cutting performance, Such apparatus can have a
`product feeder which is made to feed a plurality of product
`loaves or product bars—in the following simply: products—
`parallel to one another to a common cutting blade which
`moves in a cutting plane which extends perpendicular to the
`product conveying direction. It is possible in this manner to
`utilize a single cutting apparatus—with a correspondingly
`large blade—for the simultaneous cutting of a plurality of
`products.
`0003. Such a high-performance slicer with independent
`product feeders for two products to be conveyed in parallel
`and thus to be sliced simultaneously is described in European
`patent EP 0 713 753 B1. In this slicer, each product to be
`sliced is pushed in the direction of the blade by means of a
`separate driven gripping claw which engages at the rear prod
`uct end. The gripping claws each have their own drive and can
`accordingly be driven completely independently of one
`another at different feed speeds so that it is possible to change
`the thickness of the cut product slices for the conveyed prod
`ucts by means of the individual product feeder drives inde
`pendently of one another during the slicing.
`0004 Slicers with mutually independent product feeder
`drives for two products to be sliced simultaneously are more
`over known from U.S. Pat. No. 3,605,837 and U.S. Pat. No.
`3,927.319. Each product is in this respect clamped during the
`slicing between two oppositely disposed endless belt convey
`ors which are oriented vertically and which can both hold the
`product and feed it to a cutting plane at a changeable feed rate.
`Each pair of endless belt conveyors provided for a respective
`product has its own drive for the product feeder, with the
`drives being completely independent of one another so that
`the product feeder rates of the products to be sliced can be
`changed independently of one another.
`0005. Above all the relatively high effort which is required
`for the provision of a plurality of mutually independent drives
`including the associated control devices is problematic with
`these known apparatus.
`0006. It is therefore an object of the invention to simplify
`the simultaneous slicing of a plurality of food products con
`veyed in parallel, with the thickness of the cut product slices
`being able to be changed individually for each product.
`0007. The object is satisfied, on the one hand, by an appa
`ratus having the features of claim 1.
`0008. The apparatus in accordance with the invention has
`a product feeder which includes a plurality of belt conveyors
`which are arranged parallel to one another, which each
`include an endless belt serving as a product support for a
`product to be sliced and which can be driven together in order
`simultaneously to feed a plurality of products which each lie
`on one of the belts to a cutting plane in which at least one
`cutting blade moves, in particular in a rotating and/or circu
`lating manner. The belt conveyors have a common drive
`which includes a drive shaft by which the products lying on
`the belts can be fed to the cutting plane at a common base
`
`conveying speed. Each belt has a setting apparatus associated
`with it which is made to individually change the running
`diameter of the drive shaft in the region of the belt and thus the
`individual conveying speed of the belt.
`0009. It was recognized in accordance with the invention
`that with cutting apparatus of the generic kind, products are to
`be cut up in practice which usually largely coincide with
`respect to their outer shape and which only vary to a relatively
`Small degree with respect to their cross-sections. In order
`either to produce individual product slices or portions of
`product slices of the same weight, the products can therefore
`Substantially be conveyed at the same speed, with only rela
`tively slight adaptations being required for the exact obser
`vance of the preset slice weight or portion weight These
`adaptations are themselves not only relatively slight for each
`product, but are also additionally in the same order of mag
`nitude for all products to be sliced simultaneously. The inven
`tion utilizes this circumstance.
`0010. In accordance with the invention, the construction
`and manufacturing effort can thus be considerably reduced in
`that a set of parallel belt conveyors is provided which are
`driven in common, but which are individually adjustable. For
`this purpose, a common drive having a drive shaft is provided,
`with the drive shaft defining a running Surface with a specific
`running diameter in the region of each belt. The running
`surface can in particular be formed by a drive roller rotation
`ally fixedly connected to the drive shaft. The term “running
`diameter of the drive shaft canthus also relate to one or more
`additional components rotationally fixedly connected to the
`drive shaft. The circulation speed of a belt and thus the indi
`vidual conveying speed of the respective belt conveyor
`depends on the speed of the drive shaft and on the running
`diameter for the respective belt. If the running diameter is
`variable, the individual conveying speed can be individually
`changed while keeping constant the speed of rotation of the
`drive shaft for every individual belt.
`0011. The running diameter of the drive shaft is preferably
`variable for every belt during the slicing operation with a
`circulating belt. The adaptation of the individual conveying
`speed can thus take place “online' So-to-say without a delay
`or interruption of the ongoing cutting operation being neces
`sary. Products having a cross-sectional shape changeable in
`the longitudinal direction can thus in particular also be sliced
`while maintaining a uniform slice weight or portion weight,
`which requires a constant adaptation of the individual con
`veying speed during the slicing.
`0012. In accordance with a further embodiment of the
`invention, for each belt, its individual conveying speed can be
`changed by means of the setting device whose limits are
`determined in that the base conveying speed can be reduced
`and increased by a specific maximum amount, with the base
`conveying speed, for example, being able to be decreased by
`up to 20% and increased by up to 20%. The respective then
`current value of the individual conveying speed can therefore
`vary for each of the belt conveyors by a common value which
`is given by the base conveying speed. The base conveying
`speed is therefore so-to-say only changed with a relatively
`Small range.
`0013 The running diameter of the drive shaft is preferably
`changeable in a stepless manner for each belt to ensure an
`exact adaptation of the respective individual conveying speed
`to the then current circumstances or to the respective require
`mentS.
`
`
`
`US 2010/0307304 A1
`
`Dec. 9, 2010
`
`0014. In accordance with a further embodiment, each belt
`is changeable in length by elastic stretching and/or is pro
`vided with a clamping device for the adaptation to a change of
`the running diameter. The length change associated with a
`change of the running diameter can be compensated by these
`measures in order thus always to ensure an evenly tautened
`circulation of the belt. The clamping device can e.g. be a
`clamping roller cooperating with the empty run of the belt
`conveyor and acted on by spring force.
`0.015. In accordance with a further embodiment, each set
`ting apparatus includes two conical plates which are rotation
`ally fixedly connected to the drive shaft and which are axially
`displaceable relative to one another. The conical plates can in
`particular cooperate with a V-belt whose peripheral surface is
`made as a running Surface for the belt. The conical plates
`whose tapered sides face one another form a running Surface
`pair for the symmetrical support of the V-belt side surface.
`The cross-sectional shape of the V-belt is expediently adapted
`to the conical shape. On an axial moving together of the two
`conical plates, a force transmission to the V-belt takes place
`via the corresponding oblique Surfaces of the conical plates,
`whereby said V-belt is pressed radially outwardly and accord
`ingly runs on a larger effective diameter. Conversely, the
`V-belt slips radially inwardly when the conical plates move
`apart axially.
`0016. An arrangement of axially adjustable conical plates
`is used, as is known, for belt drives which can be adjusted in
`a stepless manner to change the speed of the output shaft with
`an unchanged speed of the drive shaft. In the described
`embodiment of the invention, however, the speed of the out
`put shaft is of no interest since no output takes place via a
`common return shaft for the belts which is provided, for
`example, and which is freely journalled. What is rather impor
`tant here is the change of the track speed of the belt called a
`belt here; it can be used in an advantageous manner for the
`setting of the individual conveyor speed of the respective belt
`conveyor and indeed in particular independently of any
`change in the speed of rotation of the return shaft.
`0017. The axial relative movement of the conical plates
`can be brought about by different types of setting apparatus.
`For example, external drivers or mutually journalled hollow
`shaft sections can be provided.
`0018. The V-belt transmits the driving torque in an advan
`tageous manner from the conical plates to the circulating belt.
`Generally, however, the belt used for the conveying of the
`products and serving as a product Support could also itself be
`made in the manner of a V-belt and circulate without an
`additional interposed V-belt on the conical plates as well as
`e.g. on a freely rotatable return shaft.
`0019. In accordance with an embodiment, each V-belt
`contacts the conical plates over the full periphery. The V-belt
`can thereby take up a high driving torque from the conical
`plates. The change in the running diameter takes place while
`deforming the V-belt. The V-belt is therefore stretched when
`the conical plates move axially toward one another. The
`V-belt is relaxed accordingly when the conical plates move
`away from one another.
`0020. In accordance with an alternative embodiment, each
`V-belt has a length which is larger than the outer diameter of
`the conical plates, with the V-belt being pressed toward the
`conical plates by the belt and only contacting the conical
`plates within the active arc. The non-pressed on part of the
`V-belt is deflected and has no contact with the running sur
`faces of the conical plates. In this embodiment, no deforma
`
`tion of the V-belt is necessary to change the running diameter
`so that only relatively small axial adjustment forces are
`required and a drive provided for the adjustment can be
`dimensioned accordingly small. In addition, the V-belt in this
`embodiment can be removed particularly simply from the
`conical plates for servicing or cleaning purposes.
`0021. In accordance with an embodiment, each belt is
`pretensioned. This is in particular advantageous because the
`V-belt is in this manner pressed toward the running Surfaces
`of the conical plates by the belt so that the V-belt is also in
`friction-locking engagement with the driving conical plates
`in the presence of a loosely deflected section.
`0022. In accordance with a further embodiment of the
`invention, each belt has an upper belt associated with it which
`is made to act on the upper side of the product. Such an
`additional belt can even be made without a drive and only
`free-running so that the upper belt unit exerts a holding-down
`function, whereby a particularly reliable product positioning,
`product holding, or product guidance is achieved during the
`slicing. The product to be sliced is therefore so-to-say
`clamped between two circulating belts disposed opposite one
`another and are conveyed in this manner. It is also possible
`that each upper belt is drivable and in this respect can be
`synchronized with its lower belt, that is its “partner belt
`serving as a product Support. The product is then conveyed, as
`in the initially named prior art in this respect, by the lower belt
`and the upper belt together.
`0023 This object is satisfied, on the other hand, by a
`method having the features of claim 13.
`0024. In the method in accordance with the invention for
`the slicing of food products, a plurality of products which
`each lie on one of the belts are Supplied simultaneously to a
`cutting plane in which at least one cutting blade is moved, in
`particularina rotating and/or circulating manner, by means of
`a product feeder which includes a plurality of belt conveyors
`which are arranged in parallel next to one another and which
`each include an endless belt serving as a product Support for
`a product to be sliced. The belts are driven by means of a
`common drive and the running diameter of the drive shaft in
`the region of the belt is changed individually as required in
`order to set the thickness of product slices to be cut individu
`ally for each product
`0025. In accordance with an embodiment, the running
`diameter of the drive shaft is changed for each belt in depen
`dence on the contour of the product, with the contour of the
`product preferably being determined using a detection device
`integrated into the apparatus. As soon as a product region with
`a reduced cross-sectional Surface, for example, therefore
`moves to the cutting plane on the slicing of the product, the
`individual conveying speed of the respective belt conveyor is
`increased by a corresponding amount So that as a result the
`product slice weight remains unchanged. The cutting appa
`ratus is aware of the topography of the product and thus of the
`contour extent of the product in the conveying direction, so
`that it is also known when which product cross-sectional
`Surface arrives at the cutting plane so that a respective desired
`slice thickness can be produced by corresponding control of
`the setting apparatus, and indeed—if desired with a slice
`thickness varying from slice to slice. The principle of the
`direct change of the product feeder in dependence on the
`product contour is known per se so that this should not be
`looked at in any more detail.
`0026. The invention will be described in the following by
`way of example with reference to the drawing.
`
`
`
`US 2010/0307304 A1
`
`Dec. 9, 2010
`
`0027 FIG. 1 schematically shows a plan view of the prod
`uctfeeder region of a cutting apparatus in accordance with the
`invention;
`0028 FIG. 2 schematically shows a side view of the cut
`ting apparatus in accordance with FIG. 1;
`0029 FIG.3 shows an enlarged sectional view of a setting
`apparatus for a belt conveyor of the cutting apparatus in
`accordance with FIG. 1; and
`0030 FIG. 4 schematically shows a side view of a cutting
`apparatus in accordance with an alternative embodiment of
`the invention.
`0031. The cutting apparatus in accordance with the inven
`tion includes a product feeder 11 with, in this example, three
`belt conveyors 13 arranged next to one another and aligned
`parallel to one another. Each of the belt conveyors 13 includes
`an endless belt 15 which serves as a support for a product 17
`to be sliced. The belts 15 are driven by a common drive shaft
`19 on which respective drive rollers 20 are seated. The belts
`15 furthermore run freely around a return shaft 21 having
`return rollers 22 (FIG. 2), with the return rollers 22 being
`arranged close to a cutting plane S
`0032. A cutting blade 23 (FIG. 2) rotates in a planetary
`manner in the cutting plane S, with alternatively a cutting
`blade, in particular a scythe blade, also being able to be used
`which does not rotate in a planetary manner, but rather only
`rotates. The return rollers 22 can also be journalled separately
`instead of on the common return shaft 21.
`0033. The products 17 lying on the upper run of the belt
`conveyer 13 are fed simultaneously and parallel to one
`another along a product conveying direction F to the cutting
`plane S by driving the drive rollers 20 by means of the com
`mon drive shaft 19.
`0034. The drive of the drive rollers 20 does not have to take
`place directly by a common coaxial drive shaft 19. Depending
`on the embodiment, it is also possible that different transmis
`sion components are provided as an intermediate member
`between the drive shaft 19 and the respective drive roller 20.
`The drive shaft 19, however, ultimately represents a common
`drive for all belt conveyors 13.
`0035. The design of the drive rollers 20 will be explained
`in more detail with reference to FIGS. 2 and 3. Each drive
`roller 20 is composed of two coaxial conical plates 30, 32
`which are rotationally fixedly connected to the drive shaft 19.
`The conical plates 30, 32 form a pair of running surfaces 34,
`36 for a V-belt 38. The cross-sectional shape of the V-belt 38
`is matched to the shape of the conical plates 30, 32 so that the
`V-belt 38 contacts the running surfaces 34, 36 areally in the
`region of the active arc of the drive roller 20. The respective
`associated belt 15 is tensioned via the V-belt 38 so that the
`peripheral surface 42 of the V-belt 38 forms a running surface
`for the belt 15. The belts 15 are made as elastically stretchable
`transport belts and are under a bias. The V-belt 38 is pressed
`toward the running surfaces 34, 36 in this manner, whereby a
`friction locking is established between the conical plates 30,
`32 and the V-belt 38 as well as between the V-belt 38 and the
`belt 15.
`0036. In each of the belt conveyors 13, one of the two
`conical plates 30, 32 is axially displaceably journalled on the
`drive shaft 19 and can be adjusted relative to the other conical
`plate by means of a motor-driven setting apparatus 25. The
`V-belt 38 is displace in the radial direction by the adjustment
`and circulates on a changed running diameter, whereby a
`changed running diameter also results for the belt 15.
`
`0037. In a base state of the cutting apparatus, all the belts
`15 circulate at a common base conveying speed in the
`stretched state so that all the products are “of the same speed
`and the thickness of the cut product slices is the same for all
`belt conveyors 13. Since the circuit speed of the belts 15 and
`consequently the individual conveying speed of the belt con
`veyors 13 also depends on the running diameter of the respec
`tive belt 15 in addition to the speed of rotation of the drive
`shaft 19, the individual conveying speed of each belt conveyor
`13 can be either increased or decreased with respect to the
`value of the base conveying speed by controlling the setting
`apparatus 25. This individual variation of the individual con
`veying speeds of the belts 15 takes place despite the common
`drive of the belts 15 by the common drive shaft 19 rotating at
`a constant speed. Since a separate setting apparatus 25 is
`associated with each belt conveyor 13, the individual convey
`ing speeds can be varied individually.
`0038. As can in particular be seen from FIG. 2, each V-belt
`38 has a length which is larger than the outer diameter of the
`conical plates 30, 32 so that a loop 44 out of engagement with
`the drive roller 20 forms outside the active arc of the drive
`roller 20. Due to this design, the V-belt 38 can easily be
`removed from the conical plates 30, 32 in the service or
`cleaning case. In addition, the V-belt 38 does not have to be
`stretched to effect an increase in the running diameter, which
`is of advantage with respect to the force required for the
`adjustment of the conical plates 30, 32.
`0039. The individual setting of the individual conveying
`speeds by a different position of the products 17 with respect
`to the cutting plane S is illustrated in FIG. 1, with it being
`assumed for easier understanding that the products 17 origi
`nally had the same lengths. Accordingly, the product 17
`located at the left in FIG. 1 instantaneously runs ahead of the
`other products so that it instantaneously has the Smallest
`residual length. Since the cutting blade 23 (FIG. 2) cuts
`through all Supplied products 17 with a constant cutting fre
`quency, the product slices cut from the products 17 are the
`thicker, the higher the individual conveying speed of the
`respective belt conveyer 13 is instantaneously.
`0040. Overall, an individual change in the individual con
`veying speed of each of the belt conveyors 13 within a range
`extending around the base conveying speed is made possible
`by the arrangement in accordance with the invention. The
`adjustment range is given by the respective extreme positions
`of the conical plates 30, 32. The variation range of the indi
`vidual conveying speed is defined, for example, by an
`increase and a decrease in the base conveying speed by a
`maximum in each case of 20% This variation range is suffi
`cient for practice since normally such products 17 are to be
`conveyed and sliced simultaneously on the individual belt
`conveyors 13 which only differ with respect to their outer
`contours, in particular with respect to the extent of their
`cross-sectional Surfaces in the longitudinal direction, to a
`degree Such that, for the achieving of weight-constant slices
`orportions, a variation of the slice thickness required for this
`purpose can beachieved by comparatively small relative indi
`vidual conveying speed changes.
`0041) If a greater adaptation of the belt running speed
`should be necessary due to the properties of the products to be
`sliced than can be effected by a maximum possible adjust
`ment stroke of the clamping rollers 30, it is possible at all
`times So-to-say to realize a common offset or a common base
`state shift for all belt conveyors 32 directly via the common
`
`
`
`US 2010/0307304 A1
`
`Dec. 9, 2010
`
`drive, e.g. in the embodiment set forth here by an increase or
`decrease in the speed of rotation of the drive shaft 19.
`0.042
`FIG. 4 shows an alternative embodiment of the
`invention. In the product feeder 11', each belt 15 has a belt 51
`associated with it which acts on the supper side of the product
`17 and thus provides a more reliable product guidance during
`the conveying process. The product 17 to be conveyed is
`clamped between the oppositely disposed belts 15, 51. The
`upper belt 51 is associated with an upper belt conveyor 53
`which is designed analogously to the lower belt conveyor 13
`and includes a drive roller 55 composed of two adjustable
`conical plates. So that the running speed of the two runs
`feeding the product 17 together is the same, the upper belt
`conveyor 53 is driven synchronously to the lower belt con
`veyor 33, with the synchronization in particular being
`achieved in that the adjustment of the conical plates 30, 32 of
`the lower drive roller 20 is always accompanied by an equal
`adjustment of the conical plates of the upper drive roller 55.
`This can be achieved either by means of a correspondingly
`controlled separate adjustment drive or by a suitable
`mechanical coupling of the respective conical plates. The two
`drive shafts 19 are accordingly also synchronized.
`0043 Provision can alternatively be made that the upper
`belt conveyor 53 does not have a drive and the upper belt 51
`only circulates freely.
`0044 Since, in accordance with the invention, the indi
`vidual conveying speeds are individually adjustable, the
`thicknesses of the cut product slices are adapted individually
`for each belt conveyor 13 without a separate drive having to
`be provided for each belt conveyor 13 for this reason. The
`effort and the costs for the provision of the product feeder 11,
`11' inaccordance with the invention and thus of the total slicer
`canthus be reduced. A constant slice weight orportion weight
`can in particular be ensured for all simultaneously Supplied
`products 17 despite product cross-sectional Surfaces varying
`in the longitudinal product direction.
`
`REFERENCE NUMERAL LIST
`0045 11, 11' product feeder
`0046 13 belt conveyor
`0047 15 belt
`0048 17 product
`0049) 19 drive shaft
`0050 20 drive roller
`0051 21 return shaft
`0052 22 return roller
`0053 23 cutting blade
`0054 25 adjustment apparatus
`0055 30 conical plate
`0056 32 conical plate
`0057 34 running surface
`0058. 36 running surface
`0059) 38 V-belt
`0060 42 peripheral surface
`0061 44 loop
`0062 51 upper belt
`0063 53 upper belt conveyor
`0064. 55 upper drive roller
`0065 Scutting plane
`006.6 F product conveying direction
`1. An apparatus for the slicing of food products, in particu
`lar a high-performance slicer, comprising
`a product feeder (11,11') which includes a plurality of belt
`conveyors (13) which are arranged parallel to one
`
`another, which each include an endless belt (15) serving
`as a product support for a product (17) to be sliced and
`which can be driven together in order simultaneously to
`feed a plurality of products (17) which each lie on one of
`the belts (15) to a cutting plane (S) in which at least one
`cutting blade (23) moves, in particular in a rotating and/
`or circulating manner,
`wherein the belt conveyors (13) have a common drive
`which includes a drive shaft (19) by which the products
`(17) lying on the belts (15) can be fed to the cutting plane
`(S) at a common base conveying speed; and
`wherein each belt (15) has a setting apparatus (25) associ
`ated with it which is made to individually change the
`running diameter of the drive shaft (19) in the region of
`the belt (15) and thus the individual conveying speed of
`the belt (15).
`2. An apparatus in accordance with claim 1, characterized
`in that the running diameter of the drive shaft (19) is change
`able for each belt (15) during the slicing operation with a
`circulating belt (15).
`3. An apparatus in accordance with claim 1, characterized
`in that, for each belt (15), its individual setting speed is
`changeable by means of the setting apparatus (25) in a range
`whose limits are determined in that the base conveying speed
`can be decreased and increased by a specific maximum
`degree, with the base conveying speed preferably being able
`to be decreased by up to 20% and increased by up to 20%.
`4. An apparatus in accordance with claim 1, characterized
`in that the running diameter of the drive shaft (19) for each
`belt (15) can be changed in a stepless manner.
`5. An apparatus in accordance with claim 1, characterized
`in that each belt (15) is changeable in length and/or is pro
`vided with a clamping apparatus for the adaptation to a
`change of the running diameter by elastic stretching.
`6. An apparatus in accordance with claim 1, characterized
`in that each setting apparatus (25) includes two conical plates
`(30.32) which are rotationally fixedly connected to the drive
`shaft (19) and are axially displaceable relative to one another.
`7. An apparatus in accordance with claim 6, characterized
`in that the conical plates (30.32) cooperate with a V-belt (38)
`whose peripheral Surface (42) is made as a running Surface for
`the belt (15).
`8. An apparatus in accordance with claim 6, characterized
`in that each V-belt (38) contacts the conical plates (30, 32)
`over the full area.
`9. An apparatus in accordance with claim 6, characterized
`in that each V-belt (38) has a length which is larger than the
`outer diameter of the conical plates (30, 32), with the V-belt
`(38) being pressed toward the conical plates (30, 32) by the
`belt (15) and only contacting the conical plates (30.32) within
`the active arc.
`10. An apparatus in accordance with claim 1, characterized
`in that each belt (15) is pretensioned.
`11. An apparatus in accordance with claim 1, characterized
`in that each belt (15) has an upper belt (5) associated with it
`which is made to act on the upper side of the product (17).
`12. An apparatus in accordance with claim 11, character
`ized in that each upper belt (51) is drivable and can be syn
`chronized with a belt (15) serving as a product support.
`13. A method for the slicing of food products, wherein
`a plurality of products (17) which each lie on a respective
`belt (15), are simultaneously fed by means of a product
`
`
`
`US 2010/0307304 A1
`
`Dec. 9, 2010
`
`feeder (11,11') to a cutting plane (S) in which at least one
`cutting blade (23) moves, in particular in a rotating and/
`or circulating manner;
`wherein the product feeder includes a plurality of belt
`conveyors (13) which are arranged parallel to one
`another and which in each case include an endless belt
`(15) serving as a product support for a product (15) to be
`sliced;
`the belts (15) are driven by means of a common drive, in
`particular a drive including a common drive shaft (19)
`for the belts (15); and
`
`the running diameter of the drive shaft (19) for each belt
`(15) is changed individually as required in the region of
`the belt (15) to set the thickness of product slices to be
`cut individually for each product (17).
`14. A method inaccordance with claim 13, characterized in
`that the running diameter of the drive shaft (19) for each belt
`(15) is changed in dependence on the contour of the product
`(17), with the contour of the product (17) preferably being
`determined using a detection device integrated into the
`apparatus.
`
`
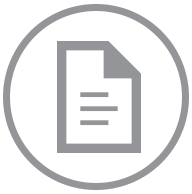
Accessing this document will incur an additional charge of $.
After purchase, you can access this document again without charge.
Accept $ ChargeStill Working On It
This document is taking longer than usual to download. This can happen if we need to contact the court directly to obtain the document and their servers are running slowly.
Give it another minute or two to complete, and then try the refresh button.
A few More Minutes ... Still Working
It can take up to 5 minutes for us to download a document if the court servers are running slowly.
Thank you for your continued patience.
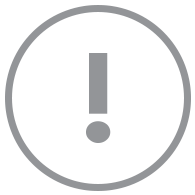
This document could not be displayed.
We could not find this document within its docket. Please go back to the docket page and check the link. If that does not work, go back to the docket and refresh it to pull the newest information.
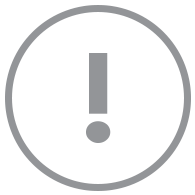
Your account does not support viewing this document.
You need a Paid Account to view this document. Click here to change your account type.
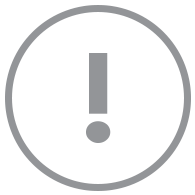
Your account does not support viewing this document.
Set your membership
status to view this document.
With a Docket Alarm membership, you'll
get a whole lot more, including:
- Up-to-date information for this case.
- Email alerts whenever there is an update.
- Full text search for other cases.
- Get email alerts whenever a new case matches your search.
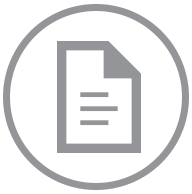
One Moment Please
The filing “” is large (MB) and is being downloaded.
Please refresh this page in a few minutes to see if the filing has been downloaded. The filing will also be emailed to you when the download completes.
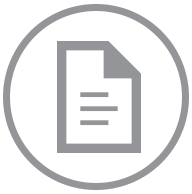
Your document is on its way!
If you do not receive the document in five minutes, contact support at support@docketalarm.com.
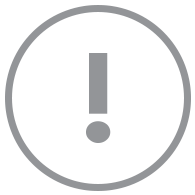
Sealed Document
We are unable to display this document, it may be under a court ordered seal.
If you have proper credentials to access the file, you may proceed directly to the court's system using your government issued username and password.
Access Government Site