`US010639812B2
`
`c12) United States Patent
`Lindee et al.
`
`(IO) Patent No.: US 10,639,812 B2
`(45) Date of Patent:
`May 5, 2020
`
`(54) HIGH SPEED SLICING MACHINE
`
`(56)
`
`References Cited
`
`(71) Applicant: FORMAX, INC., Mokena (IL)
`
`U.S. PATENT DOCUMENTS
`
`(72)
`
`Inventors: Scott A. Lindee, Mokena, IL (US);
`James E. Pasek, Tinley Park, IL (US);
`David Hancock, Morris, IL (US);
`Thomas C. Wolcott, LaGrange, IL
`(US)
`
`2,047,400 A
`4,226,176 A
`
`7/1936 Walter
`10/1980 Macchi
`(Continued)
`
`FOREIGN PATENT DOCUMENTS
`
`(73) Assignee: PROVISUR TECHNOLOGIES, INC.,
`Chicago, IL (US)
`
`DE
`DE
`
`( *) Notice:
`
`Subject to any disclaimer, the term ofthis
`patent is extended or adjusted under 35
`U.S.C. 154(b) by 127 days.
`
`(21) Appl. No.: 16/017,346
`
`(22)
`
`Filed:
`
`Jun. 25, 2018
`
`(65)
`
`Prior Publication Data
`
`Nov. 1, 2018
`US 2018/0311853 Al
`Related U.S. Application Data
`
`(62)
`
`Division of application No. 13/099,325, filed on May
`2, 2011.
`
`(51)
`
`Int. Cl.
`B26D 7122
`B26D 7101
`
`(Continued)
`
`(2006.01)
`(2006.01)
`(Continued)
`
`(52)
`
`(58)
`
`U.S. Cl.
`CPC ............... B26D 7132 (2013.01); B26D 71225
`(2013.01); B26D 5100 (2013.01); B26D 7/0683
`(2013.01);
`
`(Continued)
`Field of Classification Search
`CPC ........ B26D 7/06; B26D 7/0625; B26D 7/225;
`B26D 7/0683; B26D 7/30; B26D 7/32;
`(Continued)
`
`10/1980
`2912446
`10/1990
`3912446
`(Continued)
`
`OTHER PUBLICATIONS
`
`Machine translation of DE19525742.
`(Continued)
`
`Primary Examiner - Phong H Nguyen
`(74) Attorney, Agent, or Firm - Klintworth & Rozenblat
`IP LLP
`
`(57)
`
`ABSTRACT
`
`A high-speed food article slicing machine with a slicing
`station, a moveable frame supporting a food article feed
`mechanism frame, a food article gate, and a safety guard
`system for detecting an intrusion into the machine. Food
`articles are loaded onto a lift tray and raised to a staging
`position where food articles are in contact with a food article
`gate. The lift tray is located in line with the food article feed
`paths such that lateral shifting of food articles into the feed
`paths is not needed. Food article grippers, individually
`driven along feed paths by an overhead conveyor, move food
`articles over the food article gate towards the slicing station.
`The food article gate functions to assist in removal of food
`article end portions. The slicing machines utilizes a hori(cid:173)
`zontally radiating laser intrusion detector to shut down
`systems when an unwanted intrusion is sensed.
`
`11 Claims, 21 Drawing Sheets
`
`Weber EX1001
`IPR2020-01557
`U.S. Patent No. 10,639,812
`
`
`
`US 10,639,812 B2
` Page 2
`
`(60)
`
`Related US. Application Data
`.
`.
`.
`.
`Prov1s1onal applrcatlon No. 61/343,551, filed on May
`1, 2010.
`
`(51)
`
`(200601)
`(2006.01)
`(2006.01)
`(2006.01)
`
`Int Cl
`'
`'
`326D 7”
`B26D 5/00
`326D 7/06
`B26D 7/30
`(52) US. Cl.
`CPC .......... B26D 7/30 (2013.01); 3261) 2007/01]
`(2013.01); 3261) 2210/02 (2013.01); Y10T
`83/2074 (2015.04); Y10T 83/654 (2015.04)
`(58) Field of Classification Search
`---------------323165079528 321%?)27/1532635385
`,
`,
`,
`B26D 2007/011; B65G 15/00; B65G
`15/10; B65G 15/12; B65G 15/14; B65G
`15/16; B65G 15/30; B65G 15/50; Y1OS
`83/932; Y10T 83/6668; Y10T 83/202;
`Y10T 83/2192, Y10T 83/2194, Y10T
`83/463; Y10T 83/647; Y10T 83/6504;
`Y10T 83/6505; Y10T 83/6537; Y10T
`83/654; Y10T 83/9377; Y10T 83/2074
`See application file for complete search history.
`
`(56)
`
`References Cited
`
`U.S. PATENT DOCUMENTS
`
`4,583,435 A
`4,934,232 A
`5,191,820 A
`5 628 237 A
`5’974’925 A
`6:415:698 Bl
`2004/0016331 A1
`2004/0031363 A1
`2004/0055439 A1
`2004/0139706 A1
`
`4/1986 Fessler
`6/1990 Weber et a1.
`“993 Hartman“
`5/1997 Lindee et a1.
`11/1999 Lindee et 31.
`7/2002 Haas et a1.
`1/2004 Wolcott et a1.
`2/2004 Lindee et 31,
`3/2004 Lindee et al.
`7/2004 Drebing et a1.
`
`2005/0082147 A1
`2005/0132855 A1
`2005/0199111 A1
`2006/0289281 A1
`2007/0214969 A1
`
`4/2005 Mol
`6/2005 Weber
`9/2005 sandberg et a1,
`12/2006 Sandberg et a1.
`9/2007 Mueller et a1.
`
`2008/0185095 A1
`2008/0250944 A1
`2009/0120256 A1
`
`8/2008 Gutknecht
`10/2008 Pryor et a1.
`5/2009 Pasek
`
`FOREIGN PATENT DOCUMENTS
`
`DE
`3%
`DE
`DE
`3%
`a»
`EP
`EP
`EP
`i1}
`WO
`WO
`WO
`WO
`W0
`
`4235985
`10200§g§gjj§
`19518583
`19518595
`19150325531411?1 A1
`00547389
`0713753 A2
`2566670
`20053;;33 :1
`89/06588
`0230635
`2005/037501
`2010011237
`2011/ 139996
`
`4/1994
`$33:
`11/1996
`11/1996
`5:33;
`6/1993
`5/1996
`7/2016
`iggggg
`7/1989
`4/2002
`4/2005
`1/2010
`11/2011
`
`OTHER PUBLICATIONS
`
`Machine translation of FR2677573.
`Machine translation of JP2000-288983.
`International Search Report dated Jan. 27, 2012.
`European search Report for European Patent Application No. EP 11
`77 8126 dated Jan. 26, 2015, 3 pages.
`M h'
`t
`1 t'
`f DE102008020248
`3° {He ”“13 a?” 0
`Machine translation of DE10353114.
`Machine translation of DE2912446.
`Machine translation of 13134235985
`Machine translation of W02005037501.
`U.S.App1. No. 61/343,551, entitled “High Speed Slicing Machine,”
`filed May 1, 2010, 39 pages.
`
`'
`
`
`
`U.S. Patent
`
`May 5, 2020
`
`Sheet 1 of 21
`
`US 10,639,812 B2
`
`
`
`
`
`
`
`
`
`
`
`
`
`
`
`
`
`
`
`
`
`
`
`
`
`
`
`
`
`
`
`
`
`
`
`
`
`
`
`
`
`
`
`
`
`
`
`
`
`U.S. Patent
`
`May 5, 2020
`
`Sheet 2 of 21
`
`US 10,639,812 132
`
`199
`
`197b
`
`Fig. 1A
`
`
`
`U.S. Patent
`
`May 5, 2020
`
`Sheet 3 of 21
`
`US 10,639,812 B2
`
`
`
`
`
`U.S. Patent
`
`May 5, 2020
`
`Sheet 4 of 21
`
`US 10,639,812 B2
`
`Em
`
`m3
`
`Em
`
`
`QNmm9mm\Inh:
`,.Imnml.|_m_|l.mmmmmmmjm_nll
`“n"flhflhflhflmflifiimt:
`
`
`__'__I|.IMIIIIIIIIIIII.I'l—
`
`Qmmm3%_amm.
`
`
`
`
`
`"mml."I.-imflun_uuflnu“hu_.“unulAm_
`
`
`
`N.3
`
`m___.
`
`
`
`
`
`
`
`
`U.S. Patent
`
`May 5, 2020
`
`Sheet 5 of 21
`
`US 10,639,812 B2
`
`NE
`
`Kym-J
`
`I‘IF.||
`
`
`
`U.S. Patent
`
`May 5, 2020
`
`Sheet 6 of 21
`
`US 10,639,812 B2
`
`
`.
`
`
`A
`
`
`
`
`
`
`
`
`
`u'vv
`A.w
`I,
`
`
`
`
`
`
`
`‘ ’1‘
`I
`
`y"
`
`
`
`
`
`
`
`U.S. Patent
`
`May 5, 2020
`
`Sheet 7 0f 21
`
`US 10,639,812 B2
`
`“
`h
`E
`
`Q
`F
`h
`
`PM"?!E- VVA MAS I
`
`III--
`
`
`
`1099
`
`100
`
`
`
`_/1116
`
`I
`
`v
`
`“
`
`\
`--II--|||‘I||- §
`"I'm-“NH“? §
`”In‘fimmmffiin
`
`I
`
`Q0
`
`}
`
`10
`
`I111I’
`
`[III]!!! Illlllll I
`
`7 §
`
`2 F I/
`
`
`
`U.S. Patent
`
`May 5, 2020
`
`Sheet 8 of 21
`
`US 10,639,812 B2
`
`II
`
`6—on
`
`IIII__III_-I_IIII
`__@...
`.IIl-
`‘-E
`
`___..__IMMy...8..
`
`
`I'll-fl—IIsl
`ramsgfi
`gwfiefi
`lulu-uVII—I
`llil“.l
`_.M
`._m
`ME.
`a
`M._.___.-n
`
`:Qh
`
`BE
`
`m:e
`
`
`
`
`
`
`
`
`
`EM_____'_IIII.I..|"III|I!
`IMIIiI'IIIIIIlL-I-n
`
`
`
`cmofi
`
`awe“
`
`ummch
`
`ems“
`
`
`
`
`
`i
`
`_.M.
`
`M
`
`flMI-IIilfiIl-l-“u
`
`
`
`
`
`
`
`
`
`
`
`U.S. Patent
`
`May 5, 2020
`
`Sheet 9 of 21
`
`US 10,639,812 B2
`
`
`
`
`
`U.S. Patent
`
`May 5, 2020
`
`Sheet 10 of 21
`
`US 10,639,812 132
`
`Fig.7A
`
`
`
`U.S. Patent
`
`May 5, 2020
`
`Sheet 11 of 21
`
`US 10,639,812 132
`
`Fig.7B
`
`
`
`U.S. Patent
`
`May 5, 2020
`
`Sheet 12 of 21
`
`US 10,639,812 132
`
`
`
`Fig.7Ca
`/.-J_I_'2
`
`
`
`U.S. Patent
`
`May 5, 2020
`
`Sheet 13 0f 21
`
`US 10,639,812 B2
`
`1mmEma
`
`y/
` mg.$1"?mgafiw?M1...allw
`
`WW;m8WI;am
`nmcmvax
`
`mg
`
`mmm|
`
`E.3.
`
`
`
`
`U.S. Patent
`
`May 5, 2020
`
`Sheet 14 of 21
`
`US 10,639,812 132
`
`iflffiafflffia701Za
`
`707$?07fi7077
`
`
`
`I:II
`
`I__:I_I
`
`
`
`70Qi10Q57007.
`
`$
`
`{fa/1;:
`4:,” r” 213/ /
`0/4:- //
`..
`I!” z/
`x’
`,
`.
`{5”,
`"
`c?
`
`{5/
`
`
`
`
`
`70033,10050,700712
`
`
`
`
`
`U.S. Patent
`
`May 5, 2020
`
`Sheet 15 of 21
`
`US 10,639,812 132
`
`.1003, 7005, 1007
`
`75702, 7904, i908
`
`1017
`
`.
`
`_ $134,1135LH35
`$37,113? . 702;,
`
`’
`
`,4
`
`. 1009
`
`70an
`
`
`
`U.S. Patent
`
`May 5, 2020
`
`Sheet 16 of 21
`
`US 10,639,812 132
`
`855
`
`
`
`U.S. Patent
`
`May 5, 2020
`
`Sheet 17 of 21
`
`US 10,639,812 B2
`
`mam.
`
`
`
`
`
`
`
`
`,X:
`
`new“
`
`
`
`U.S. Patent
`
`May 5, 2020
`
`Sheet 18 0f 21
`
`US 10,639,812 B2
`
`
`
`
`
`U.S. Patent
`
`May 5, 2020
`
`Sheet 19 of 21
`
`
`
`
`
`U.S. Patent
`
`May 5, 2020
`
`Sheet 20 0f 21
`
`US 10,639,812 B2
`
`
`
`
`
`
`
`U.S. Patent
`
`May 5, 2020
`
`Sheet 21 of 21
`
`US 10,639,812 132
`
`
`
`125
`
`
`
`US 10,639,812 B2
`
`1
`HIGH SPEED SLICING MACHINE
`
`CROSS-REFERENCE TO RELATED
`APPLICATIONS
`
`This application claims the benefit of US. Provisional
`Application No. 61/343,551, filed May 1, 2010, and is a
`divisional application of US. Ser. No. 13/099,325, filed on
`May 2, 2011, the contents of which are incorporated herein
`in their entirety.
`
`BACKGROUND OF THE INVENTION
`
`Many different kinds of food articles or food products,
`such as food slabs, food bellies, or food loaves are produced
`in a wide variety of shapes and sizes. There are meat loaves
`made from various meats, including ham, pork, beef, lamb,
`turkey, and fish. The meat in the food loaf may be in large
`pieces or may be thoroughly comminuted. These meat
`loaves come in different shapes (round, square, rectangular,
`oval, etc.) and in different lengths up to six feet (183 cm) or
`even longer. The cross-sectional sizes of the loaves are quite
`different; the maximum transverse dimension may be as
`small as 1.5 inches (4 cm) or as large as ten inches (25.4 cm).
`Loaves of cheese or other foods come in the same great
`ranges as to composition, shape, length, and transverse size.
`Typically,
`the food loaves are sliced,
`the slices are
`grouped in accordance with a particular weight requirement,
`and the groups of slices are packaged and sold at retail. The
`number of slices in a group may vary, depending on the size
`and consistency of the food article and the desire of the
`producer, the wholesaler, or the retailer. For some products,
`neatly aligned stacked slice groups are preferred. For others,
`the slices are shingled or folded so that a purchaser can see
`a part of every slice through a transparent package.
`Food articles can be sliced on high speed slicing machines
`such as disclosed in Published Patent Document WO 2010/
`011237 A1 or US. Pat. No. 5,628,237 or 5,974,925; or as
`commercially available as the Power Max 4000TM and
`FX180® slicers available from Formax, Inc. of Mokena, 111.,
`USA.
`
`The FX180® machine can be configured as an automati-
`cally loaded, continuous feed machine, or an automatically
`loaded, back-clamp or gripper type machine.
`For an automatically loaded, continuous feed machine,
`side-by-side upper and lower conveyor pairs drive food
`articles into the cutting plane. A gate is located in front of the
`conveyors. The initial food articles are loaded with leading
`ends abutting the gate. The gate is lowered and the food
`articles proceed into the conveyors. When the initial food
`articles are sliced to the extent that the trailing ends of the
`food articles clear the gate, the gate is raised and new food
`articles are loaded in the feed paths, held back by the gate.
`Shortly thereafter the gate is lowered and new food articles
`slide down to where lead ends of the new food articles abut
`
`trailing ends of the initial food articles being sliced. The new
`food articles are driven into the cutting plane trailing the
`initial food articles. Food articles are sequentially and con-
`tinuously loaded in this manner, lead end-to-trailing end, in
`abutting contact with the preceding food articles.
`US. Pat. No. 5,628,237 and European patent EP 0 713
`753 describe a back-clamp or gripper type slicing machine.
`According to this type of slicing machine, food articles are
`loaded onto a lift
`tray and the lift
`tray is raised to a
`ready-to-sweep position. Loaf grippers are retracted after the
`previous food articles are sliced. During retraction of the
`loaf grippers, loaf-to-slicing blade gate doors are closed and
`
`2
`
`ends of the previous food articles are dropped through a loaf
`end door. After the grippers have reached the retracted
`position or “home position” remote from the slicing blade,
`a loaf sweep mechanism is activated, moving the food
`articles laterally together into the slicing position. A spacing
`mechanism moves down and spaces the food articles apart.
`The grippers then advance after it has been determined that
`the loaf sweep mechanism has moved the food articles to the
`slicing position. The grippers have onboard sensing mecha-
`nisms that are triggered by contact with the food articles.
`After sensing and gripping the food articles, the food articles
`are retracted slightly, and the loaf-to-slicing blade gate doors
`are opened and the food articles are advanced to the slicing
`plane of the slicing blade. The loaf sweep mechanism
`retracts and the loaf lift tray lowers, ready for the next reload
`cycle. According to this design, in practice, the reload cycle
`is accomplished in about eight seconds. In a high-volume
`slicing operation, reload cycle time can be a significant
`limitation to optimum production efficiency.
`The machine disclosed in WO 2010/011237 A1 provides
`an automated, food article tray loading method and appara-
`tus wherein food articles can be loaded into the lift tray into
`designated and separated lanes which automatically assume
`a preload condition, and after the food articles are loaded,
`food article separation is maintained on the lift tray. A food
`article transfer receives the food articles on the lift tray in
`their separated positions and transfers the food articles into
`the slicing feed paths while maintaining the separated posi-
`tions. A food article end disposal system utilizes a transport
`that laterally moves end portions outside of the feed path and
`ejects the end portions as the transport is moved back into
`the feed path to receive the subsequent end portions. The
`machine utilizes food article grippers that are fixed onto
`conveyor belts which support and drive the food articles in
`the feed paths.
`The present inventors have recognized that it would be
`desirable to slice plural food articles with independent
`feeding and weighing capabilities, with hygienic and opera-
`tional enhancements.
`
`SUMMARY OF THE INVENTION
`
`The invention provides a mechanism and method for
`slicing multiple food articles with independency of feed rate
`and the ability to weigh each product group from each food
`article respectively to achieve optimal weight control and
`yield of each food article.
`The present invention provides a high-speed slicing appa-
`ratus and a weighing and classifying conveyor combination
`that provides plural advantages in machine cost, productiv-
`ity, food hygiene, and operation.
`The invention provides a lift tray that is located in line
`with the food article feed paths and is lowered to receive
`food articles and raised into the feed paths. There is no need
`for lateral shifting of food articles into the feed paths. Food
`article grippers are driven along the feed paths by an
`overhead conveyor. A laser food article end detection system
`is employed in each feed path to detect the terminal end of
`the food article to control the positioning of the gripper for
`that path.
`The invention provides the use of an automatic debris or
`scrap removal conveyor that also provides for end portion
`removal.
`
`10
`
`15
`
`20
`
`25
`
`30
`
`35
`
`40
`
`45
`
`50
`
`55
`
`60
`
`65
`
`The invention provides an automated cleanup position
`wherein the elevated food article feed mechanism can be
`
`collapsed to a more convenience plane or maintenance
`position, and the blade cover is automatically pivoted to a
`
`
`
`US 10,639,812 B2
`
`3
`cleanup position. The combination provides for enhanced
`portion control and yield. A food article feed mechanism
`ensures accurate feeding by the use of servo driven and
`controlled feed belts and grippers. The slicing mechanism
`includes three independent drives for slicing multiple food
`articles simultaneously.
`An improved food article stop gate is provided that also
`serves as a door for the removal of food article end portions.
`A horizontally radiating laser intrusion detector is used to
`shut down systems when an unwanted intrusion by an
`operator is detected.
`An automated,
`food article tray loading method and
`apparatus is provided wherein food articles can be loaded
`into the lift tray into designated and separated lanes which
`automatically assume a preload condition, and after the food
`articles are loaded, food article separation is maintained on
`the lift tray.
`Numerous other advantages and features of the present
`invention will become readily apparent from the following
`detailed description of the invention and the embodiments
`thereof, and from the accompanying drawings.
`
`BRIEF DESCRIPTION OF THE DRAWINGS
`
`FIG. 1 is a near side elevational view of a slicing machine
`and a weighing and classifying conveyor combination of the
`present invention;
`FIG. 1A is an enlarged fragmentary view taken from FIG.
`
`1;
`
`FIG. 1B is a perspective view of the slicing machine of
`FIG. 1 in a clean-up configuration;
`FIG. 2 is a plan view of the combination of FIG. 1 with
`some panels and parts removed or made transparent illus-
`trating some underlying components;
`FIG. 2A is a bottom perspective view of a portion of FIG.
`
`2;
`
`FIG. 3 is a sectional view taken generally along line 3-3
`of FIG. 2 with some panels and parts removed or made
`transparent and underlying components revealed;
`FIG. 4 is a schematic, sectional view taken generally
`along line 4-4 of FIG. 6 with some panels and parts removed
`or made transparent and underlying components revealed;
`FIG. 5 is a schematic, sectional view taken generally
`along line 5-5 of FIG. 6 with some panels and parts removed
`or made transparent and underlying components revealed;
`FIG. 6 is a sectional view taken generally along line 6-6
`of FIG. 3 with some panels and parts removed or made
`transparent and underlying components revealed;
`FIG. 7 is a fragmentary elevational view taken generally
`along line 7-7 of FIG. 2 with some panels and parts removed
`or made transparent and underlying components revealed;
`FIG. 7A is a fragmentary perspective view of a portion of
`FIG. 7;
`FIG. 7B is an enlarged fragmentary view of apportion of
`FIG. 7A;
`FIG. 7C is an enlarged rear perspective view of a portion
`of FIG. 7;
`FIG. 7D is a top perspective view of a portion of FIG. 7;
`FIG. 7E is an enlarged fragmentary view of a portion of
`FIG. 7;
`FIG. 7F is an enlarged fragmentary view of an alternate
`embodiment of a lower conveyor.
`FIG. 8 is a fragmentary rear perspective view of the
`apparatus of FIG. 1;
`FIG. 9 is a far side perspective view of the apparatus of
`FIG. 1 with a lift tray in a lowered position;
`
`5
`
`10
`
`15
`
`20
`
`25
`
`30
`
`35
`
`40
`
`45
`
`50
`
`55
`
`60
`
`65
`
`4
`
`FIG. 10 is a top perspective rear view of the lift tray of
`FIG. 9 with a tray platform removed;
`FIG. 11 is an enlarged, fragmentary near side perspective
`view of a portion of the slicing machine of FIG. 1;
`FIG. 12 is an enlarged, fragmentary far side perspective
`view with a door removed to show underlying components;
`FIG. 13A is a schematic diagram of the loaf feed appa-
`ratus in a first stage of operation;
`FIG. 13B is a schematic diagram of the loaf feed appa-
`ratus in a second stage of operation;
`FIG. 13C is a schematic diagram of the loaf feed appa-
`ratus in a third stage of operation; and
`FIG. 13D is a schematic diagram of the loaf feed appa-
`ratus taken generally along line 13D-13D of FIG. 13C.
`
`DESCRIPTION OF THE PREFERRED
`EMBODIMENTS
`
`in
`While this invention is susceptible of embodiment
`many different forms, there are shown in the drawings, and
`will be described herein in detail, specific embodiments
`thereof with the understanding that the present disclosure is
`to be considered as an exemplification of the principles of
`the invention and is not intended to limit the invention to the
`
`specific embodiments illustrated.
`Published Patent Application No. WO 2010/011237 and
`US. Pat. No. 5,628,237 are herein incorporated by refer-
`ence.
`
`Overall Description
`
`FIGS. 1-3 illustrate a high-speed slicing apparatus 100
`and a weighing and classifying conveyor or output conveyor
`102 according to a preferred embodiment of the invention.
`The slicing apparatus 100 includes a base section 104, a
`collapsible frame 105, an automatic food article loading
`apparatus 108 that receives food articles 110 to-be-sliced, a
`food article feed apparatus 120, a food article end and scrap
`removal conveyor 122 (FIGS. 13C and 13D), a laser safety
`guard system 123, a slicing head apparatus 124, and a slice
`receiving conveyor 130. The slicing head apparatus includes
`a slicing blade 125 that defines a slicing plane and an orifice
`plate or slicing block 126 that guides food articles into the
`slicing plane, the blade cutting closely to the orifice plate.
`The slicing apparatus also includes a computer display touch
`screen 131 that is pivotally mounted on and supported by a
`support 132.
`
`Base Section
`
`The base section 104 includes a compartment 136 having
`side walls 138a, 138b, a bottom wall 140, and an inclined
`top wall 142. The apparatus 100 is supported on four
`adjustable feet 144. The compartment 136 has a tapered side
`profile from back to front wherein the top wall 142 slants
`down from back to front. The slanted orientation of the top
`wall 142 ensures water drainage of the top of the compart-
`ment 136. The compartment is supported on adjustable feet
`144.
`
`The compartment 136 includes a near side door 152, a far
`side door 156 (FIG. 9), and a rear door 162 that permit
`access into the compartment or to modules normally held
`within the compartment 136. The compartment 136 typi-
`cally affords an enclosure for a computer, motor control
`equipment, a low voltage supply, and a high voltage supply
`
`
`
`US 10,639,812 B2
`
`5
`and other mechanisms as described below. The compartment
`may also include a pneumatic supply or a hydraulic supply,
`or both (not shown).
`
`Collapsible Frame and Elevated Housings
`
`The base section 104 supports the collapsible frame 105
`as shown in FIGS. 1, 1B and 9. The collapsible frame 105
`includes a foldable support mechanism 174 that supports a
`food article feed mechanism frame 190.
`
`The foldable support mechanism 174 includes a servo-
`motor 175 that drives a gear reducer 176 having a drive shaft
`178 that extends out of far side of the compartment 136
`(FIG. 9). The drive shaft 178 is rotationally fixed to parallel
`levers 180a, 1801) which swing out with a turning of the
`drive shaft 178. The levers 180a, 1801) are pivotally con-
`nected to a column 182 via a rotary connection 184. The
`column 182 is pivotally connected at a pivot connection 192
`to the frame 190 which supports the food article feed
`apparatus 120.
`For cleaning and maintenance purposes, the collapsible
`frame 105 is collapsed down by actuating the servomotor
`175 and gear reducer 176 to rotate the levers 180a, 180b,
`which draws down the column 182 as shown in FIG. 1B.
`
`is
`The frame 190, and all equipment supported thereby,
`lowered for more convenient maintenance and cleaning as
`illustrated in FIG. 1B. In some cases, this eliminates the
`need for ladders or platforms when servicing the slicing
`apparatus 100.
`The slicing head 124 is covered by a guard 119 that is
`attached to the frame 190 such that when the frame is
`
`pivoted down as shown in FIG. 1B, the guard 119 is pivoted
`away from a slicing head base 117 to expose the slicing
`blade 125 and internals for cleaning and maintenance.
`Additionally, the elevation of the food article feed appa-
`ratus can be adjusted by using the servomotor to selectively
`pivot the levers 180a, 1801) and lower the rear of the frame
`190. At a front, the frame 190 is supported on a cross shaft
`193 that is eccentrically fixed at each end to a round cam 194
`(FIG. 1A). The cam is joumaled in a round opening 195 in
`side supports 197a, 1971) and the cam is fixed for non-
`rotation to the respective side support by fasteners 199. The
`far side is shown in FIG. 1A, with the understanding that the
`near side is mirror image identical across the longitudinal
`vertical center plane of the machine. As shown in FIG. 1A,
`because the dimension “a” is smaller than the dimension
`
`“b”, the shaft ends can be temporarily loosened by removing
`the fasteners and the shaft and cams can be rotated 180
`
`degrees about a centerline of the shaft, and the cams can be
`re-fastened to be fixed to the side supports. The elevation
`will be different between the two 180-degree adjustable
`positions. Thus, the machine will accommodate two differ-
`ent height settings for different types of food articles.
`
`Food Article Feed Apparatus
`
`An upper conveyor assembly 530 of the food article feed
`apparatus 120 is shown in FIG. 2. The conveyor assembly
`530 includes three independently driven endless conveyor
`belts 802, 804, 806. Each belt 802, 804, 806 is identically
`driven so only the drive for the belt 802 will be described.
`The belt 802 is wrapped around a toothed front drive
`roller or pulley 812 and a back-idler roller or pulley 816. The
`belt 802 preferably has teeth that engage teeth of the two
`rollers 812, 816. Each drive roller 812 includes a toothed
`outer diameter 812a and a toothed, recessed diameter 81219.
`
`10
`
`15
`
`20
`
`25
`
`30
`
`35
`
`40
`
`45
`
`50
`
`55
`
`60
`
`65
`
`6
`An endless drive belt 820 wraps around the recessed
`diameter 81219. The drive belt 820 also wraps around a drive
`roller 824 that is fixed to a drive shaft 828. The drive shaft
`
`828 extends transversely to the belt 802 and is journaled for
`rotation within a bearing 830 mounted to a near side frame
`member 836.
`
`The drive shaft 828 penetrates a far side frame member
`838 and extends to a bearing 843, coupled to a gear reducer
`842 mounted to a support frame 854. The gear reducer 842
`is coupled to a servomotor 850 that is mounted to the support
`frame 854.
`The servomotor 850 drives the drive shaft 828 which
`turns the roller 824 which circulates the belt 820 which
`rotates the roller 812 which circulates the belt 802.
`
`Three servomotors 850 are mounted to the support frame
`854 and all are located within an upper compartment 855
`that is supported by the frame 190.
`The idler rollers 816 are provided with a pair of mirror
`image identical adjustable cam belt
`tension adjustment
`mechanisms 882a, 8821). As shown in FIG. 7A, each mecha-
`nism 882a, 8821) includes a fork 885 that is braced from the
`respective side frame member 836, 838 by an adjustable cam
`883. The fork 885 is guided by upper and lower pins 886a,
`8861) so as to slide rearward and forward and has an end 891
`
`that captures an axle 889 that rotationally supports the idle
`rollers 816. For adjustment, the cam fastener 883a is loos-
`ened so as to be rotatable on the respective side frame
`member 836, 838, rotated to achieve the desired belt tension,
`and then the cam fastener is tightened to hold the cam fixed.
`FIG. 7B illustrates a gripper 894 used in cooperation with
`the belt 802. The gripper 894 is mounted to a bottom run of
`the belt 802 and is translated along the food article path by
`the belt 802. The gripper 894 is clamped to a belt joint and
`guide assembly 896 by a fixture 901 that engages the
`assembly 896 and is fixed thereto by a clamping set screw
`897. The assembly 896 comprises a pair of upper members
`899 and a lower member 900. The upper members 899 can
`include teeth 899a that mesh engage the teeth of the belt 802
`once the members 899, 900 are fastened together to splice
`the free ends 802e, 802f of the belt 802 (FIG. 7D). For
`clamping, fasteners 902, 904 (FIG. 7D) are provided which
`are inserted from above the members 899 through plain
`holes in the members 899 and tightly threaded into threaded
`holes in the member 900.
`
`The lower member 900 includes guides 906, 907 that
`contain slide bearings 906a, 907a composed of friction
`reducing material. The slide bearings 906a, 907a partly
`surround longitudinal rails 912, 913 that are in parallel with,
`and straddle the belt 802. The rails 912, 913 support the
`gripper along its working path from a retracted position to a
`fully forward position near to the slicing plane.
`For each gripper there are two rails 912, 913 to support
`and guide that gripper. Thus, there are two rails that straddle
`the belt 804 and two rails that straddle the belt 806.
`
`The gripper 894 is connected to the fixture 901 by a front
`plate 920 having a predominant lateral face and a rear plate
`922 having a predominant longitudinal face. Each gripper
`894 is provided with two air lines 930, 932 for two-way
`pneumatic gripper open-and-close operability.
`The air lines 930, 932 are guided through lower rings 940
`and upper rings 942 to an air tube storage area 950 above the
`food article feed apparatus 120 (FIG. 7D). The air tube lines
`are routed around weighted rollers or slides 951 that are
`guided by longitudinal slots 952 and extend to a source of
`pressurized air. Thus, the movement of the rollers or slides
`along the slots under force of gravity, will take up slack in
`
`
`
`US 10,639,812 B2
`
`7
`the air tubes when the grippers 894 are moving toward, and
`when in, the retracted position.
`The gripper 894 travels from the retracted home position
`shown in FIG. 7A to the advanced,
`forward position
`approaching the slicing plane.
`The grippers 894 are as described in Published Patent
`Application No. WO 2010/011237, herein incorporated by
`reference.
`
`Lower Conveyor
`
`As illustrated in FIGS. 3, 6, 7, and 7E at a front end of the
`food article feed apparatus 120, are three lower feed con-
`veyors 992, 994, 998, having endless belts 1002, 1004,
`1008, respectively. The endless belts 1002, 1004 1008 are
`independently driven and are directly opposed to presser
`plates 1003, 1005, 1007 respectively.
`FIG. 6 shows the conveyor 992 has a drive roller 1010
`having a central hub 1012 with a central bore 1014. The
`drive roller 1010 has tubular stub axles 1016, 1018 extend-
`ing from opposite ends of the central hub 1012. The tubular
`stub axles 1016, 1018 are journaled for rotation by bearings
`1020, 1022 that are fastened to carrier blocks 1023a.
`The conveyor 994 includes a drive roller 1038 having a
`central hub 1042 with a bore 1044. The drive roller 1038 has
`
`tubular stub axles 1046 and 1048 extending from opposite
`ends of the central hub 1042. The tubular stub axles 1046,
`1040 are journaled by bearings 1050, 1052 respectively that
`are attached to carrier blocks 1023b.
`
`A motor housing 1054, including a base plate 1054b and
`a cover 1054a, is mounted to an end of an upper conveyor
`support bar 1056. The base plate 1054b of each side of the
`machine is fastened to a linear actuator, such as a pneumatic
`cylinder 1055a and 1055b respectively. The cylinders
`1055a, 1055b are connected together by the support bar
`1056. Each cylinder slides on a fixed vertical rod 1057a,
`1057b respectively. Thus, controlled air to the cylinders
`1055a, 1055b can be used to uniformly raise or lower the
`near side motor housing 1054 and the far side motor housing
`1054 uniformly.
`A spindle 1060 extends through the motor housing 1054,
`through a sleeve 1064, through a coupling 1065, through the
`tubular stub axle 1016,
`through the central bore 1014,
`through the tubular stub axle 1018, through the tubular stub
`axle 1046, and partly into the bore 1044. The spindle 1060
`has a hexagonal cross-section base region 1070, a round
`cross-section intermediate region 1072, and a hexagonal
`cross-section distal region 1074. The hexagonal cross-sec-
`tion base region 1070 is locked for rotation with a surround-
`ing sleeve 1071 to rotate therewith.
`The intermediate region 1072 is sized to pass through the
`sleeve 1064, through the tubular stub axle 1016, through the
`central bore 1014, and through the tubular stub axle 1018 to
`be freely rotatable therein. The distal region 1074 is con-
`figured to closely fit into a hexagonal shaped central channel
`1078 of the tubular stub axle 1046 to be rotationally fixed
`with the tubular stub axle 1046 and the drive roller 1038.
`
`The sleeve 1064 includes a hexagonal perimeter end
`1064a that engages a hexagonal opening 106511 of the
`coupling 1065. The coupling 1065 includes an opposite
`hexagonal opening 1065a that engages a hexagonal perim-
`eter end 101611 of the tubular stub axle 1016. The coupling
`1065 couples the sleeve 1064 and the stub axle 1016 for
`mutual rotation such that the sleeve 1064 and the drive roller
`
`1010 are locked for rotation together,
`sleeve 1064 turns the drive roller 1010.
`
`i.e., turning of the
`
`5
`
`10
`
`15
`
`20
`
`25
`
`30
`
`35
`
`40
`
`45
`
`50
`
`55
`
`60
`
`65
`
`8
`Within the motor housing 1054 are two servomotors
`1090, 1092 mounted to the housing by fasteners. As shown
`in FIGS. 4 and 6, the servomotor 1090 has a vertically
`oriented output shaft 1096 that rotates about a vertical axis
`connected to a worm gear 1098 that is enmesh with and
`drives a drive gear 1100 that rotates about a horizontal axis.
`The drive gear 1100 drives the sleeve 1071 that drives the
`region 1070 of the spindle to rotate the spindle 1060.
`Rotation of the spindle 1060 rotates the drive roller 1038 via
`the hexagonal cross-section distal end region 1074.
`Adjacent to the servomotor 1090 is the servomotor 1092.
`The servomotor 1092 is configured substantially identically
`with the servomotor 1090 except the worm gear 1098, as
`shown in schematic form in FIG. 5, of the servomotor 1092
`drives a drive gear 1100 that drives the sleeve 1064 to rotate.
`The sleeve 1064 rotates independently of the round cross-
`section region 1072 of the spindle 1060, and drives a stub
`axle 1016 to rotate, which rotates the drive roller 1010.
`The sleeves 1071 and 1064 are journaled for rotation by
`bearings. The drive gears 1100, 1100 are fastened to the
`respect
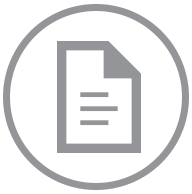
Accessing this document will incur an additional charge of $.
After purchase, you can access this document again without charge.
Accept $ ChargeStill Working On It
This document is taking longer than usual to download. This can happen if we need to contact the court directly to obtain the document and their servers are running slowly.
Give it another minute or two to complete, and then try the refresh button.
A few More Minutes ... Still Working
It can take up to 5 minutes for us to download a document if the court servers are running slowly.
Thank you for your continued patience.
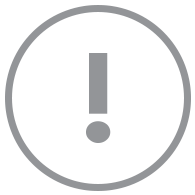
This document could not be displayed.
We could not find this document within its docket. Please go back to the docket page and check the link. If that does not work, go back to the docket and refresh it to pull the newest information.
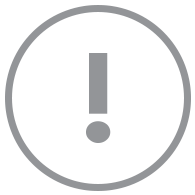
Your account does not support viewing this document.
You need a Paid Account to view this document. Click here to change your account type.
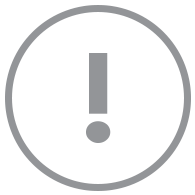
Your account does not support viewing this document.
Set your membership
status to view this document.
With a Docket Alarm membership, you'll
get a whole lot more, including:
- Up-to-date information for this case.
- Email alerts whenever there is an update.
- Full text search for other cases.
- Get email alerts whenever a new case matches your search.
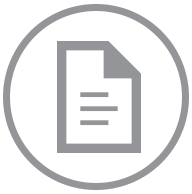
One Moment Please
The filing “” is large (MB) and is being downloaded.
Please refresh this page in a few minutes to see if the filing has been downloaded. The filing will also be emailed to you when the download completes.
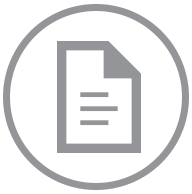
Your document is on its way!
If you do not receive the document in five minutes, contact support at support@docketalarm.com.
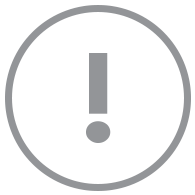
Sealed Document
We are unable to display this document, it may be under a court ordered seal.
If you have proper credentials to access the file, you may proceed directly to the court's system using your government issued username and password.
Access Government Site