`
`3,373,198
`Patented Mar. 2, 1968
`
`3,373,108
`METHOD OF PREPARing gWERBASED CAELCUM
`SJLFGNATE OL CONCENTRATES
`Robert A. Woodle, Edward H. Holst, and Robert S.
`Edwards, Nederland, Tex., assigliors to Texaco race
`New York, N.Y., a corporation of Delaware
`No Drawing. Fied Apr. 12, 1966, Ser. No. 541,949
`4 Claims. (C. 252-33)
`
`-wd
`
`ABSTRACT OF THE DISCLOSURE
`A method of producing an overbased calcium Sulfonate
`lube oil concentrate comprising contacting a mixture of
`normal calcium sulfonate, basic calcium inorganic com
`pound, an oxygenated vehicle, a lubricating oil and a thio
`phenol with carbon dioxide and separating residual Water,
`oxygenated vehicle and thiophenol from the final reaction
`mixture leaving said concentrate as residue.
`
`5
`
`0.
`
`-ammed
`
`20
`
`2
`and of sufficient size to produce an unacceptable amount
`of haze in the unfiltered and filtered product.
`We have discovered, and this constitutes our invention,
`a method of producing overbased calcium sulfonate lubri
`cating oil concentrate having a calcium metal ratio of at
`least about 2 and up to 20 and higher, preferably between
`about 10 and 18, a calcium content of at least 2 wt. per
`cent and up to 20 wt. percent and higher, preferably be
`tween about 11 and 18 wt. percent, and a total base
`number (TBN), as defined in ASTM D664, of at least
`about 20 and up to 500 and higher, preferably between
`about 280 and 450, in which the resultant overbased cal
`cium sulfonate particles are in a fine colloidal-like state,
`and therefore, do not have a tendency to precipitate upon
`storage. Further, the formed overbased sulfonate particles
`are of such fineness as to permit the passage of the crude
`concentrate through a standard clarifying means at an
`improved flow rate with reduced loss of overbased cal
`cium sulfonate to produce a product of commercially
`acceptable clarity. More particularly, we have discovered
`a particular combination of ingredients, reaction condi
`tions and reaction steps which accomplishes the foregoing
`result.
`Broadly, our process comprises forming a first reaction
`mixture consisting of (1) normal calcium sulfonate, (2)
`a basic calcium compound selected from the group con
`sisting of calcium hydroxide, a combination of calcium
`oxide and water and mixtures thereof, (3) an oxygenated
`vehicle selected from the group consisting of water, lower
`alkanol, lower alkoxy-ethanols and mixtures thereof, (4)
`a lubricating oil, and (5) a thiophenol compound of the
`formula:
`
`S.E. R. % l R
`
`30
`
`This invention relates to a method for preparing Over
`based calcium sulfonate lubricating oil concentrates of
`improved filterability and clarity containing a high pro
`portion of oil dispersible calcium.
`25
`The overbased calcium sulfonate lube oil concentrates
`are useful as detergent-dispersant additives in lubricating
`oils, e.g., in amounts between about 1 and 10 wt. percent.
`By the term “overbased calcium sulfonate lubricating
`oil concentrate' we mean a product wherein the ratio of
`filterable oil dispersible calcium equivalents to Sulfonic
`acid equivalents in the product is substantially above that
`present in ormal calcium sulfonate, that is, the equivalent
`ratio of calcium moiety to sulfonic acid moiety is Sub
`stantially greater than 1:1. The formula for the normal
`calcium salt of monosulfonic acid can be written as
`(RSO)Ca where R stands for hydrocarbyl radical. It is
`to be noted that the number of hydrogen equivalents of
`calcium and of sulfonic acid filterably dispersed in said
`normal sulfonate are each 2 and therefore the calcium
`metal ratio is 1. In contradistinction, products from our
`process have substantially higher calcium metal ratios,
`e.g., of at least 2 and as high as 20 and higher. By the
`term “calcium metal ratio' we mean the ratio of equiva
`lents of calcium to equivalents of sulfonic acid present
`45
`in the particular concentrate in a stable filterable disper
`SO.
`It is theorized that the overbased calcium Sulfonates
`contemplated herein are a complex mixture of normal
`calcium sulfonates and calcium carbonate in a physical
`50
`and/or chemical relationship with calcium carbonate Sup
`plying the excess, that is, the overbasing calcium. Further
`the overbased calcium sulfonate exists as solid, finely di
`vided particles in the lubricating oil medium of the con
`centrate.
`55
`In the past, much difficulty has been encountered in
`manufacturing overbased calcium sulfonate lube oil con
`centrates in that often substantial portions of the calcium
`values therein would undesirably precipitate during stor
`age and/or the concentrates were very turbid and required
`filtration to gain consumer acceptance. However, upon fil
`tration either an unacceptable amount of calcium values
`was lost and/or the particles of the calcium sulfonate
`calcium carbonate complex were of an undesirably large
`size to substantially block (blind) the filtering mechanism
`
`where R and R' are members, each containing less than
`13 carbon atoms, selected from the group consisting of
`hydrogen, alkyl, cycloalkyl, aryl, alkaryl, aralkyl, alkoxy,
`acyl, halogen, nitro, and amino. The mole ratio of normal
`calcium sulfonate to basic calcium compound to oxy
`genated vehicle to thiophenol is advantageously between
`about 1:2:40:10 and 1:19:5:40. When the "basic calcium
`compound” reactant is calcium oxide and water, the mole
`ratio of CaO:HO is advantageously between about 1:0.1
`and 1:5. The resultant reaction mixture is heated to a
`temperature of between about 50 and 200 F., preferably
`between 70 and 140 F., under a pressure of between
`about 0.1 and 50 atmospheres, preferably between about
`0.9 and 3 atms., for a period of between about 0.1 and
`12 hours, preferably between about 0.5 and 4 hours. At
`the end of the first reaction period, carbon dioxide is
`passed through the first reaction mixture at a temperature
`between about 50 and 200 F., preferably between about
`70 and 180 F., under a carbon dioxide pressure of be
`tween about 0.1 and 50 atmospheres, preferably between
`about 0.9 and 4 atmospheres, in an amount of between
`about 1 and 40 and higher moles of carbon dioxide per
`mole of basic calcium compound reactant. The carbon
`dioxide reaction period is normally conducted for a pe
`riod between 0.1 and 12 hours, preferably between 2 and
`6 hours. At the end of the carbon dioxide reaction period,
`
`60
`
`65
`
`Page 1 of 5
`
`ORONITE EXHIBIT 1012
`
`
`
`5
`
`10
`
`5
`
`20
`
`25
`
`3,373,108
`4.
`3.
`ent can be a synthetic lubricant such as polyoxyalkylene
`the thiophenol compound, oxygenated vehicle and any
`glycol of a molecular weight between about 200 and 4000,
`other volatilizable diluents or solvents in the carbon di
`polymerized olefin, trioctylphosphate, polymeric tetrahy
`oxide reaction mixture are removed from the carbon di
`drofuran and polyalkyl silicone polymer in a molecular
`oxide treated mixture via standard means Such as frac
`Weight range of 200 to 2000. The concentration of the
`tional distillation, e.g., at a temperature between about 300
`normal calcium sulfonate in the diluted calcium sulfonate
`and 270 F. at atmospheric or reduced pressure of be
`reactant charge material is normally between 10 and 100
`tween about 1 and 50 mm. Hg leaving crude overbased
`wt. percent and more generally between about 30 and
`calcium sulfonate lubricating oil concentrate of the type
`70 wt. percent. The term “water immiscible' denotes solu
`defined. Under the preferred conditions, the crude concen
`bility in water of less than 5 wt. percent at room tem
`trate is filtered utilizing standard filter mechanisms such
`perature.
`as passing the crude product through cloth or blotter
`It is to be noted by the term "normal calcium sul
`paper precoated with a filter aid such as inert diatoma
`fonate' we intend sulfonate reactant in its diluted as well
`ceous amorphous silica The resultant filtrate is the clari
`as its undiluted form.
`-
`fied version of overbased calcium sulfonate lube oil con
`The normal calcium sulfonate reactant is prepared by
`centrate of the invention.
`standard means such as reacting a combination of calcium
`In the foregoing procedure it is theorized the thio
`oxide and water, calcium oxide alone or calcium hy
`phenol compound reacts with the added calcium hydrox
`droxide with sulfonic acid or a double decomposition re
`ide or in situ formed calcium hydroxide to form an in
`action wherein sodium sulfonate is reacted with a calcium
`termediate calcium thiophenolate which is soluble in the
`halide such as as calcium chloride to convert the sodium
`reaction medium and then the intermediate thiophenolate
`Sulfonate to the corresponding normal calcium sulfonate.
`is converted into fine calcium carbonate particles by the
`These reactions normally take place in the aforementioned
`carbon dioxide contact with the normal calcium sulfonate
`water immiscible diluents at a temperature between about
`functioning in complex with the formed calcium carbon
`100 and 200' F. utilizing a mole ratio of inorganic cal
`ate particles to aid in their colloidal-like dispersion
`cium reactant to sulfonic acid or alkali metal sulfonate be
`throughout the final lube oil concentrate. This formation
`tween about 1:2 and 1.1:2. The normal calcium sulfonate
`of calcium carbonate particles through the intermediate
`reactant may be preformed or formed in situ in the
`formation of a reaction mixture of calcium thiophenolate
`method of the invention as a preliminary first step.
`appears to permit the creation of very fine, e.g., less than
`Specific examples of the thiophenol compounds con
`about 0.4 micron normal calcium sulfonate-calcium car
`templated herein are thiophenol, 1,4-dithiophenol; 2
`bonate particles that impart substantially less haze and
`methylthiophenol; 2,6-dimethylthiophenol; 4-cyclohexyl
`substantially more filterability and storage stability to the
`thiophenol; 4-phenylthiophenol; 4-benzylthiophenol; 404'-
`final overbased calcium sulfonate lube oil concentrate
`methylphenyl)thiophenol; 3-nitrothiophenol; 3,5-ninitro
`than if calcium carbonate is formed directly from calcium
`thiophenol; 2-hydroxythiophenol; 4-aminothiophenol; 5
`hydroxide in the reaction in situ.
`ethoxythiophenol; 5-acetylthiophenol; and 2-ethyl-4-hy
`Under most preferred conditions, the first stage reaction
`is conducted under a blanket of inert gas such as nitrogen
`droxythiophenol.
`-
`In regard to the oxygenated vehicle, this vehicle is
`in order to reduce side reactions. Further, also included in
`preferably lower alkanol, that is C to C alkanols and
`the first stage reaction is volatilizable inert liquid hydro
`preferably methanol. It can also include a lower alkoxy
`carbon diluent such as the saturated aliphatic and aro
`ethanol such as 2-methoxyethanol, 2-ethoxyethanol, 2
`matic hydrocarbons. Still further, in the final fractional
`propoxyethanol and 2-butoxyethanol.
`distillation step to remove the thiophenol, oxygenated
`In addition to the oxygenated vehicle, a volatile inert
`derivative and volatilizable diluent a stripping gas is pref
`liquid hydrocarbon diluent is also preferably included
`erably employed, this gas either being carbon dioxide or
`in the first reaction mixture to facilitate contact. Specific
`an inert gas such as nitrogen. The stripping gas rate is
`examples of such medium are liquid aromatic and sat
`normally between about 0.1 and 7 standard cubic feet/
`urated aliphatic hydrocarbon having boiling points be
`hour/gallon (s.c.f.h./gallon) of carbon dioxide treated
`tween about 190 and 290 F. Such as toluene, xylene and
`product.
`heptane. The volatile diluent normally present in the
`In regard to the normal calcium sulfonate reactant, the
`initial reaction mixture is in an amount betwen about 15
`sulfonic acid from which it is derived are any of the oil
`and 40 wt. percent.
`soluble sulfonic acids such as mahogany sulfonic acid,
`The lubricating oil employed in the initial charge can
`alkylated aromatic sulfonic acid, petrolatum sulfonic acid,
`be either mineral lubricating oil or synthetic lubricating
`paraffin wax sulfonic acid, petroleum naphthene sulfonic
`oil, for example, of the type described in connection with
`acid, polyisobutylene Sulfonic acid, mono- and poly-wax
`the Sulfo reactant. Specific examples of suitable lubricat
`or other alkyl substituted benzene sulfonic acid, mono
`ing oils are the solvent dewaxed paraffinic and naphthenic
`and poly-wax or other alkyl substituted naphthalene sul
`petroleum lubricating oils obtained in petroleum refin
`fonic acid, mono- and poly-wax or other substituted
`ing. A particularly preferred lubricating oil is naphthenic
`cyclohexyl sulfonic acid and mixtures thereof. Preferably,
`base oil since it appears to produce the clearest final com
`the sulfonic acid will have been one derived from sulfona
`positions in the concentrate. Advantageously, the lubri
`tion of a petroleum hydrocarbon fraction. The preferred
`cating oil component has an SUS viscosity between about
`sulfonic acids have a molecular weight between about 450
`70 and 900 at 100 F., preferably between about 100
`and 550 but the molecular weight of the sulfonic acid
`and 300. The total lubricating oil content of the initial
`can be as low as 350 or as high as 1500 for making suf
`charge including the lubricating oil associated with the
`ficiently oil soluble normal calcium sulfonate. Particularly
`preferred sulfonic acids are the petroleum hydrocarbon
`Sulfo reactant is advantageously between about 10
`and 50 wt. percent. The function of the lubricating oil
`sulfonic acid of a molecular weight of about 480. By the
`component is not only to facilitate contact of the over
`term "oil soluble' we means soluble in a conventional
`based calcium sulfonate product, but also to facilitate
`lubricating oil fraction to the extent of at least about 5
`introduction of the overbased sulfonate into lubricant
`wt. percent.
`compositions as an additive.
`Ordinarily, the normal calcium sulfonate reactant use
`In order to aid in the dispersion of the formed cal
`ful in the method of the invention is introduced into the
`cium sulfonate particles in a lubicating oil concentrate,
`first reaction stage in a diluted form, the diluent being
`standard dispersants are advantageously incorporated as
`an oil, water immiscible, organic medium which normally
`one of the initial charge materials such as N-octadecyl
`will be a petroleum or synthetic hydrocarbon lubricating
`Sulfo Succinamate, tetrasodium N-(1,2-dicarboxyethyl-n-
`oil, a gas oil fraction or even a lighter cut such as ben
`octadecylsulfo Succinamate, sodium dioctylsulfo succinate,
`Zene or light solvent naphtha. Alternatively, the oil dilu
`
`30
`
`3 5
`
`40
`
`50
`
`60
`
`65
`
`70
`
`Page 2 of 5
`
`
`
`3,373,108
`5
`6
`oleyl primary amine, N-"tallow' 1,3-propane diamine, and
`sulfonate lube oil concentrate as the residue. The residue
`oxylated nonyl phenols of the formula:
`was then filtered through a 2 ft. blotter paper filter uti
`lizing 1 wt. percent finely divided diatomaceous silica
`filter aid in the crude concentrate. The resultant over
`based calcium sulfonate lube oil concentrate filtrate
`weighed 9586 grams and filtered through the filter at a
`rate of 5 gallons/hour/ft. The test data on the over
`based calcium sulfonate filtrate product is reported below
`in Table II:
`
`(OCH2CH)OH
`
`Y-CoE19
`
`Table II
`12.9
`Calcium, wt. percent------------------------
`1.6
`Sulfur ------------------------------------
`335
`TBN-------------------------------------
`Specific gravity 60/60 F. ------------------ 1.1913
`Viscosity, 210 F. cs. ----------------------- 9.30
`Lumetron' -------------------------------
`5.5
`Carbon dioxide, wt. percent ----------------- 10.95
`H2S, wt. percent --------------------------- 0.004
`Sodium, wt. percent ------------------------ 0.05
`25 vol. percent of filtrate in mineral lubricating oil of an
`SUS viscosity at 100° F. of about 845.
`EXAMPLE III
`This example illustrates the preparation of the normal
`calcium sulfonate utilized as a reactant.
`The procedure employed was the same as that utilized
`in Example I except the quantities employed were 210
`lbs. of the sodium petroleum sulfonate oil solution of
`Example I, 163 lbs. of petroleum naphthene lube oil of an
`SUS viscosity of about 100 at 100 F., 18 lbs. calcium
`chloride and 54 lbs. water. The test results on the resultant
`normal calcium sulfonate-lube oil mixture were as follows:
`Table III
`
`0.
`
`20
`
`wherein n is an average integer of from 2 to 9. The
`added dispersant is desirably present in the initial reac
`tion mixture between about 0.1 and 5 wt. percent.
`The following examples further illustrate the inven
`tion, but are not to be construed as limitations thereof:
`EXAMPLE I
`This example illustrates the production of the normal
`calcium sulfonate reactant.
`To a 500 gallon stainless steel reactor there was
`charged 1750 lbs. of a mineral oil solution of sodium
`petroleum sulfonate having a molecular weight of about
`500 giving an analysis of 3 wt. percent Na. about 24
`wt. percent mineral oil, about 4 wt. percent water and
`a kinematic viscosity of about 1200 at 210 F. In addi
`tion, there was also charged 1360 lbs. of naphthenic
`base lubricating oil of an SUS viscosity of 300 at 100
`F. and 154 lbs. of calcium chloride dissolved in 462 lbs.
`of water. The reactor contents were heated to 350 F.
`with nitrogen blowing. The reactor was held at 350 F.
`for 4 hours during which time all water present in the
`reaction mixture was removed. Into the resultant normal
`calcium sulfonate-lube oil reactant mixture there was
`incorporated 1 wt. percent finely divided diatomaceous
`silica as a filter aid and said product was pressure filtered
`through blotter paper.
`The test data results on the resultant filtered normal
`calcium sulfonate reactant mixture are found below in
`Table I:
`-
`
`Table I
`
`Results
`Test:
`Calcium ------------------------------
`1.96
`Sulfur --------------------------------
`2.25
`Sodium, wt. percent -------------------- 0.07
`Specific gravity, 60/60 F. ----------- -
`0.9764
`Viscosity, 210°F, cs. -------------------
`441
`
`25
`
`30
`
`35
`
`40
`
`Results
`Tests:
`Calcium, wt. percent --------------------
`1.81
`Sulfur, wt. percent----------------------
`2.36
`Sodium, wt. percent --------------------
`0.24
`Specific gravity 60/60 F. --------------- 0.9839
`Viscosity, 210 F. CS. ------------------
`150
`EXAMPLE IV
`This example further illustrates the method of the in
`vention.
`To a stainless steel 10-gallon reactor there was charged
`2640 grams of petroleum naphthene oil of an SUS vis
`cosity of about 100 at 100 F., 7250 grams normal calcium
`sulfonate-lube oil mixture prepared as in Example III,
`3870 grams toluene, 3870 grams methanol, 700 grams
`water and 9430 grams thiophenol. The reaction mixture
`was stirred for 10 minutes while purging the reactor with
`nitrogen. The agitation and nitrogen purge were stopped
`and the reactor was charged with 2180 grams calcium ox
`ide. The stirring of the reaction mixture was reinstituted
`and rapid stirring was continued throughout the remainder
`of the run. The reactor was then vented, blown with
`nitrogen at a rate of 16 s.c.f. h. and heated over a half
`hour period in the range of 145-175 F. The nitrogen
`blowing was halted and the reactor contents were then
`refluxed for a 4-hour period at 178 F. At the end of the
`4-hour period the contents were cooled to 146 F. over a
`1.5 hour period. Carbon dioxide was then bubbled through
`the cooled reaction mass at 146 F. for a period of 3.5
`hours at a rate of 43 s.c.f.h. During this 3.5 hour period
`6820 grams of carbon dioxide were introduced. The re
`actor was then vented and the reaction mixture stripped
`at 345 F. with carbon dioxide at 20 s.c.f.h. under a pres
`sure of 20 mm. Hg to remove thiophenol, methanol,
`toluene and water as well as volatilizable by-products leav
`ing a crude overbased calcium sulfonate lube oil concen
`trate as residue. The crude residue to which was added
`finely divided diatomaceous silica in an amount of 1 wt.
`percent was filtered on a 2 ft. pressure blotter filter at
`300 F. There was recovered 11,350 grams of overbased
`
`50
`
`55
`
`60
`
`EXAMPLE
`This example illustrates the method of the invention.
`To a 10 gallon stainless steel reactor there was charged
`7248 grams of filtered calcium sulfonate-lube oil reactant
`mixture of Example i, 2633 grams of naphthenic base oil
`of a viscosity of 100 at 100° F., 3869 grams toluene, 3869
`grams methanol, 21.74 grams calcium oxide, 698 grams
`water and 8571 grams thiophenol. The resultant mixture
`being continuously stirred throughout the entire process,
`was heated to 175 F. for a 1.5 hour period and held at
`175 F. for an additional 2-hour period. The stirred mix
`ture was then cooled from 175 F. over a 0.5 hour period
`and carbon dioxide was bubbled through the stirred reac
`tion mixture at a temperature of 146 F. for a 4-hour
`period utilizing a carbon dioxide rate of 43 s.c.f.h. Dur
`ing the carbon dioxide blowing step the charged carbon
`dioxide was continuously vented from the reactor. The
`amount of carbon dioxide introduced into the system over
`65
`the 4-hour period was 6820 grams. At the end of the 4
`hour period the carbon dioxide blowing was continued
`for an additional 2 hours and during which time vacuum
`stripping by raising the temperature from 146 to 300
`F. and reducing the pressure to 20 mm. Hg was instituted.
`The resultant vacuum stripping was continued for an addi
`tional 2-hour period at a temperature range of 303 to
`350 F. substituting nitrogen for carbon dioxide as the
`stripping gas, thereby stripping out water, methanol, tol
`uene and thiophenol leaving the crude overbased calcium
`
`70
`
`Page 3 of 5
`
`
`
`5
`
`0
`
`5
`
`30
`
`35
`
`40
`
`45
`
`55
`
`60
`
`65
`
`fined.
`
`-
`
`N
`
`Results
`Tests:
`Calcium, wt. percent ------------------------
`12.8
`Sulfur, wt. percent ------------------------
`1.7
`TBN -------------------------------------
`348
`Specific gravity 60/60 F. ------------------- 1.2272
`Kinetic viscosity, 210 F. c.S. ---------------- 194A36
`Lumetron -------------------------------
`9.5
`Carbon dioxide, wt. percent ------------------
`10.8
`H2S, wt. percent --------------------------- 0.0001.
`Sodium, wt. percent ------------------------
`0.17
`125 vol. percent of filtrate in petroleum lubricating oil of an
`SUS viscosity at 100° F. of about 845.
`EXAMPLE V
`This comparative example illustrates the importance of
`employing a thiophenol compound within the scope de
`To a 2-liter stainless steel reactor there was charged 254
`grams of a filtered normal calcium sulfonate-lube oil
`solution giving the following analysis: wt. percent
`Ca=1.58
`wt. percent S=2.5, wt. percent Na=0.20, wt. percent
`HO-0.01, specific gravity 60/60 F.-0.98 le, kinetic vis
`cosity, cs. at 210 F-275. There was also charged 95
`grams methanol, 62 grams calcium oxide, 10 grams water
`and 458 grams pentanethiol. The resultant mixture being
`continuously stirred throughout the entire process, was
`heated to 140 F. for a 2-hour period and held at 140
`F. for an additional 3-hour period. The mixture was held
`between 137 and 140 F. and carbon dioxide was bubbled
`through the stirred reaction mixture at 50 p.s.i.g. for a
`4 hour period utilizing a carbon dioxide rate of 217.5
`grams/hr. During the carbon dioxide blowing step the
`charged carbon dioxide was vented continuously from the
`reactor. At the end of the 4-hour period the mixture was
`transferred to a 3 liter flask. The temperature was raised
`from 80 to 350°. F. and carbon dioxide blowing was con
`tinued for an additional 2 hours at a rate of 56 grams/hr.
`at 350° F. at a pressure of 10 mm. Hg. This vacuum
`stripping resulted in the removal of water, methanol and
`pentanethiol leaving an obviously unfilterable residue.
`We claim:
`4. A method of producing an overbased calcium sul
`fonate lubricating oil concentrate comprising:
`(a) forming a first reaction mixture composed of nor
`mal calcium sulfonate derived from an oil soluble hy
`drocarbyl sulfonic acid, a basic calcium compound
`selected from the group consisting of calcium hy
`droxide and a combination of calcium oxide and wa
`ter and mixtures thereof, an oxygenated vehicle se
`lected from the group consisting of lower alkanol
`and lower alkoxyethanol, a lubricating oil selected
`from the group consisting of mineral lubricating oil
`and synthetic lubricating oil of an SUS viscosity at
`100° F. between about 70 and 900 and a thiophenol
`compound of the formula:
`SHR
`/
`%
`
`3,373,108
`8
`7
`to form carbon dioxide treated second reaction mix
`calcium sulfonate lubricating oil concentrate as filtrate
`having the following properties:
`ture at said temperature,
`-
`- -
`(c) separating residual water, oxygenated vehicle and
`Table IV
`thiophenol from said second reaction mixture leav
`ing said concentrate as residue,
`(d) said normal calcium sulfonate, said basic calcium
`compound, said oxygenated vehicle, said thiophenol
`being present in said first reaction mixture in a mole
`ratio of between about 1:2:40:10 and 1:19:5:40,
`said lubricating oil being present in an amount be
`tween about 10 and 50 wt. percent, and the mole ratio
`of calcium oxide to water in said combination being
`between about 1:0.1 and 1:5.
`2. A method of producing an overbased calcium sul
`fonate lubricating oil concentrate comprising:
`(a) forming a first reaction mixture composed of nor
`mal calcium sulfonate derived from an oil soluble
`hydrocarby sulfonic acid, thiophenol, a basic cal
`cium compound selected from the group consisting of
`calcium hydroxide and a combination of calcium ox
`ide and water and mixtures thereof, an oxygenated
`vehicle selected from the group consisting of lower
`alkanol and lower alkoxyethanol and a lubricating
`oil selected from the group consisting of mineral
`lubricating oil and synthetic lubricating oil of an
`SUS viscosity at 100 F. between about 70 and 900,
`(b) maintaining said first reaction mixture at a tem
`perature between about 50 and 200 F. while con
`tacting said first reaction mixture with carbon dioxide
`to form carbon dioxide treated second reaction mix
`ture at said temperature,
`.
`.
`(c) separating residual water, oxygenated vehicle and
`thiophenol from said second reaction mixture leave
`ing said concentrate as residue,
`(d) said normal calcium sulfonate, said basic calcium
`compound, said oxygenated vehicle, said thiophenol
`being present in said first reaction mixture in a mole.
`ratio of between about 1:2:40:10 and 1:19:5:40,
`said lubricating oil being present in an amount be
`tween about 10 and 50 wt. percent and the mole ratio
`of calcium oxide to water in said combination being
`between about 1:0.1 and 1:5.
`3. A method of preparing an overbased calcium sul
`fonate lubricating oil concentrate comprising:
`(a) forming a first reaction mixture composed of nor
`mal calcium sulfonate derived from an oil soluble
`hydrocarbyl sulfonic acid of a molecular weight of
`between about 350 and 1500, thiophenol, a basic cal
`cium compound selected from the group consisting
`of calcium hydroxide, a combination of calcium ox
`ide and water and mixtures thereof, an oxygenated
`vehicle selected from the group consisting of lower
`alkanol and lower alkoxyethanol, a lubricating oil
`having an SUS viscosity at 100°. F. of between about
`100 and 300, and a volatilizable diluent selected
`from the group consisting of aromatic and saturated
`aliphatic hydrocarbon having a boiling point between
`190 and 300 F.
`-
`(b) heating said first reaction mixture at a temperature
`between about 50 and 200 F., subsequently passing
`carbon dioxide through said first reaction mass at
`a temperature between about 50 and 200 F. in an
`amount of carbon dioxide to basic metal compound
`of at least about one mole carbon dioxide per mole
`basic calcium compound,
`-
`(c) Subsequently stripping said first reaction mass at
`a temperature between about 300 and 370 F. under
`a pressure of between about 1 and 50 mm. Hg to
`remove thiophenol, residual water, volatizable dil
`uent and oxygenated vehicle leaving said overbased
`calcium sulfonate oil concentrate as residue,
`(d) said normal calcium sulfonate, said basic calcium
`compound, said oxygenated vehicle and said thio
`phenol in said first reaction mixture being present in
`a mole ratio between about 1:2:40:10 and 1:19:5:40,
`
`R
`where R and R' are members, each containing less
`than 13 carbon atoms, selected from the group con
`sisting of hydrogen, alkyl, cycloalkyl, aryl, alkaryl,
`aralkyl, alkoxy, acyl, halogen, nitro, and amino,
`(b) maintaining said first reaction mixture at a tem
`perature between about 50 and 200. F. while con
`tacting said first reaction mixture with carbon dioxide
`
`70
`
`Page 4 of 5
`
`
`
`3,373,108
`9
`said lubricating oil being present in an amount be
`ing oil is mineral lubricating oil of an SUS viscosity at
`tween about 10 and 50 wt. percent, the mole ratio
`100 F. between about 100 and 300.
`of calcium oxide to water in said combination being
`between about 10:0.1 and 1:5, and said volatilizable
`References Cited
`diluent being present in an amount of between 15
`UNITED STATES PATENTS
`and 40 wt. percent.
`2,616,924
`11/1952
`Asseff et al. -------- 252-33 X
`4. A method in accordance with claim 3 wherein said
`3,027,325
`3/1962
`McMillen et al. ------ 252-33
`first heating is conducted in an inert gas atmosphere, said
`3,057,896
`10/1962
`Schlicht et al. ------ 252-33 X
`oxygenated vehicle is methanol, said volatilizable diluent
`3,223,630
`12/1965
`Gragson ------------ 252-33
`is toluene, said basic compound is said combination of 10 3,256,186
`6/1966
`Greenwald ---------- 252-33
`calcium oxide and water, said normal calcium sulfonate
`is derived from a petroleum sulfonic acid having a molec
`DANIEL E. WYMAN, Primary Examiner.
`ular weight between about 450 and 550 and said lubricat
`PATRICK. P. GARVIN, Examiner.
`
`Page 5 of 5
`
`
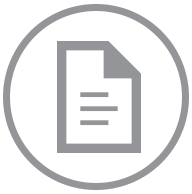
Accessing this document will incur an additional charge of $.
After purchase, you can access this document again without charge.
Accept $ ChargeStill Working On It
This document is taking longer than usual to download. This can happen if we need to contact the court directly to obtain the document and their servers are running slowly.
Give it another minute or two to complete, and then try the refresh button.
A few More Minutes ... Still Working
It can take up to 5 minutes for us to download a document if the court servers are running slowly.
Thank you for your continued patience.
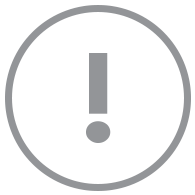
This document could not be displayed.
We could not find this document within its docket. Please go back to the docket page and check the link. If that does not work, go back to the docket and refresh it to pull the newest information.
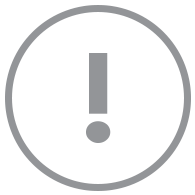
Your account does not support viewing this document.
You need a Paid Account to view this document. Click here to change your account type.
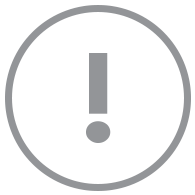
Your account does not support viewing this document.
Set your membership
status to view this document.
With a Docket Alarm membership, you'll
get a whole lot more, including:
- Up-to-date information for this case.
- Email alerts whenever there is an update.
- Full text search for other cases.
- Get email alerts whenever a new case matches your search.
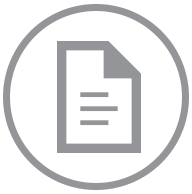
One Moment Please
The filing “” is large (MB) and is being downloaded.
Please refresh this page in a few minutes to see if the filing has been downloaded. The filing will also be emailed to you when the download completes.
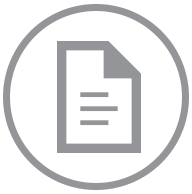
Your document is on its way!
If you do not receive the document in five minutes, contact support at support@docketalarm.com.
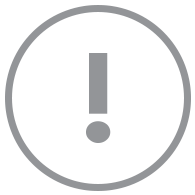
Sealed Document
We are unable to display this document, it may be under a court ordered seal.
If you have proper credentials to access the file, you may proceed directly to the court's system using your government issued username and password.
Access Government Site