`APPLICATIONS
`
`Copyright © 1999 Marcel Dekker, Inc.
`
`Page 1 of 20
`
`ORONITE EXHIBIT 1009
`
`
`
`19
`Automotive Crankcase Oils
`
`Stephen C. Lakes
`Henkel Corporation/Emery Group
`Cincinnati, Ohio
`
`INTRODUCTION
`I.
`Crankcase engine oils are the most recognizable lubricant in the automotive area. Both the indi-
`vidual and the commercial consumer equate vehicle lubrication with the engine oil. Millions in
`advertising budget are spent worldwide to promote specific brands in this area. The engines them-
`selves and the crankcase lubricants protecting them have been upgraded over the last two decades
`such that engine life for gasoline passenger cars up through heavy-duty diesel trucks is longer
`than ever before.
`Synthetic engine oils have been commercially marketed since the 1960s but have taken only
`a small share of the large engine oil market, worldwide. The European passenger car motor oil
`(PCMO) market utilizes the highest proportion of full or partially synthetic engine oils, with the
`North American and Far Eastern areas lagging behind on synthetic use for this application.
`Synthetic-based oils exhibit improved viscometric, volatility, and thermal stability properties
`over conventional petroleum-based oils. Improved engine tolerances, governmental emission
`regulations, and the corporate average fuel economy (CAFE) requirements in the United States
`are promoting improved performance engine oils and more stringent base stock requirements.
`Synthetics will play a future role both in full synthetic formulations and as base stock or additive
`component in PCMO and heavy-duty diesel oil (HDDO) partial synthetic oils.
`
`A. Engine Oil Applications
`There are several variations of internal combustion engines used as automotive power plants.
`Some use an oil sump or reservoir, and others use an oil/fuel mix for lubrication. Those engines
`with “crankcase fill” systems include four-cycle gasoline engines, four-and two-cycle diesel
`engines, and unconventional fueled engines (natural gas, liquid propane, alcohol, or vegetable
`oils). This chapter concentrates on crankcase oil lubrication systems. Outboard engines and
`engines for two-cycle motorcycles and recreational vehicles, where the internal moving parts are
`lubricated by oil injection or oil/fuel mixtures, are not considered.
`In crankcase fill engines, the lubricant is stored in the engine sump and is pumped or
`
`441
`
`Copyright © 1999 Marcel Dekker, Inc.
`
`Page 2 of 20
`
`
`
`442
`
`Lakes
`
`splashed onto the various moving parts during operation. The function of the engine oil
`encompasses lubrication of moving parts, friction reduction, wear reduction, cooling of internal
`components, and collection of combustion by-products for removal. By-product removal is
`accomplished by in-system filtration of the oil and/or a final drain of the used lubricant. Current
`automotive gasoline engines have an operating life of approximately 3000 hours and will use
`about 150 L of engine oil during that time. Most four cycle passenger car engines are scrapped for
`metal recycle, not rebuilt. On the other hand, heavy-duty diesels for commercial over-the-road
`trucks will last approximately 15,000 hours and use around 2000 L of engine oil prior to rebuild.
`Preliminary studies of unconventional fueled engines have shown comparable operating life and
`oil consumption compared to gasoline- or diesel-fueled counterparts.
`Internal combustion engine life is measured as the operating hours before overhaul or engine
`replacement. The primary areas for engine overhaul are the main bearings, the piston rings, and
`the cylinder walls. Excessive wear of the crankcase bearings will result in insufficient oil pres-
`sure in the internal galley and low oil delivery to the upper portion of the engine, leading to accel-
`erated wear and shortened life. Ring wear or sticking will result in power loss due to blowby and
`cylinder pressure leakage. Wear or glazing of the cylinder walls will result in excessive oil burn-
`ing and subsequent power loss.
`The expectations for extended engine life of the individual or fleet operator are reflected in
`increased awareness of engine oil performance. Improved cold weather starting, lower oil loss
`during operation, and engine cleanliness are attributes that the consumer recognizes and demands
`of today’s oils. Combined with longer warranty protection from the equipment manufacturer,
`these factors present an opportunity for synthetic base stock use. Synthetics can be added to
`improve mineral oil based formulations or used to make top tier fully synthetic oils.
`
`B. Performance Requirements for Engine Oils
`The viscometric requirements for engine oils are categorized and defined in a group of vis-
`cosity grades defined by the Society of Automotive Engineers under “SAE Viscosity Grades
`for Engine Oils” (see Table 1). The same document also gives the performance of engine oils
`
`Copyright © 1999 Marcel Dekker, Inc.
`
`Page 3 of 20
`
`
`
`Automotive Crankcase Oils
`
`443
`
`of different viscosity grades with respect to the high temperature/high shear requirements of
`the American Society for Testing and Materials (ASTM) and the Coordinating European
`Council (CEC) (see Table 2).
`The predominant gasoline engine oils, in use, are the 5W-30 through 10W-40 multigrade
`oils. Passenger and heavy-duty diesel engine oils are mostly 10W-40 and 15W-40 viscosity
`grades.
`After the viscosity grade has been defined, crankcase engine oils are classified into two
`major categories:
`
`gasoline engine oils: API S (service category of the American Petroleum Institute) and A-96
`(European passenger car classification from ACEA, the Association des Constructeurs
`Européens)
`diesel engine oils: API C (commercial category). B-96 (European passenger diesel), and E-96
`(European heavy-duty diesel)
`
`Alternative fuels, listed and defined in the “Alternative Automobile Fuels,” (SAE J1297,
`March 1993), and include liquid propane gas, ethanol, methanol, compressed natural gas, ethers
`(e.g., methyl t-butyl ether, t-amyl methyl ether), and higher molecular weight alcohols. No spec-
`ified oil categories are available at this time for these fuels. The matter is currently under review
`by the SAE.
`
`C. Requirements for Gasoline Engine Oils
`North American gasoline passenger car oils fall under the API and ILSAC categories. The API
`SJ service category (adopted in 1996) and ILSAC GF-2 are comprised of a set of engine tests for
`defining minimum oil performance:
`
`Sequence L-38: uses a single-cylinder test engine (42.5 CID). This test evaluates an engine oil’s
`performance in resisting copper, tin, and lead bearing wear and corrosion in the engine, and
`viscous shear loss in the lubricant.
`Sequence II-D: uses a 1978 General Motors eight-cylinder commercial engine (350 CID). This
`test evaluates an engine oil’s performance in resisting internal engine corrosion, specifically
`the valve pushrods, hydraulic valve lifters, and oil pump relief valve.
`Sequence III-E: uses a 1986 General Motors V-block six-cylinder commercial engine (231 CID).
`This test evaluates an engine oil’s ability to resist sludge formation and cam lobe and lifter
`
`Copyright © 1999 Marcel Dekker, Inc.
`
`Page 4 of 20
`
`
`
`444
`
`Lakes
`
`wear in the engine, as well as high temperature oxidation (Kinematic viscosity increase at
`100⬚C) in the lubricant.
`Sequence V-E: uses a Ford four-cylinder commercial engine (2.3 L). This test evaluates an engine
`oil’s ability to resist sludge and varnish formation, overhead valve wear in the engine, and
`formation of degradation/wear products (Kinematic viscosity increase at 100⬚C Fe, Cu, Si,
`pentane insolubles; fuel dilution) in the lubricant.
`Sequence VI-A: uses a 1993 Ford eight-cylinder commercial engine (4.6 L). This test evaluates
`the effect of the engine oil on gasoline fuel economy compared to a reference oil.
`
`Tentative European gasoline oil categories were introduced by ACEA in 1994 as replace-
`ments for the G-4 and G-5 oil categories. These were finalized in December 1995 and became
`effective in early 1996. The gasoline engine oil categories are:
`
`A1-96 Current Quality
`A2-96 Extended Drain
`A3-96 High Tier, Extended Drain
`
`These categories are defined as minimal by the ACEA:
`
`These sequences define the minimum quality level of a product for presentation to ACEA
`members. Performance parameters other than those covered by the tests shown or more strin-
`gent limits may be indicated by individual member companies.
`
`Most European OEMs require additional engine testing for specific usage and warranty
`application.
`Engine tests for minimal oil performance for ACEA include the following.
`
`Sequence III-E: same as API SJ.
`Peugeot TU3M High Temperature Test: uses a modified Peugeot TU3M/KDX in-line four-cylin-
`der engine (1.3 L). This test evaluates an engine oil’s ability, under high temperature, high
`speed conditions, to resist ring sticking and piston deposits in the engine and viscosity
`increase in the lubricant (procedure listed as CEC L-55-T-95).
`Peugeot TU3M Wear Test: uses a Peugeot TU3M/KDX commercial four-cylinder engine (1.3 L).
`This test evaluates an oil’s ability, under slow and moderate speed/low temperature condi-
`tions, to resist valve train wear (procedure listed as CEC L-38-A-94).
`Sequence V-E: same as API SJ.
`MB M111 Black Sludge Test: uses a Mercedes-Benz M111 E20 four-cylinder commercial engine
`(2.0 L). This test evaluates an oil’s ability, under varied driving conditions (urban to auto-
`bahn), to resist sludge formation in the cylinder head area, as well as piston varnish forma-
`tion and ring sticking in the engine. The lubricant is tested for viscosity change, fuel dilu-
`tion, total base number (TBN), sulfated ash, solids, and wear metals (procedure listed as
`CEC L-53-T-95).
`MB M111 Fuel Economy Test: uses a modified Mercedes-Benz M111 E20 four-cylinder engine
`(2.0 L). This test evaluates the effect of the engine oil on gasoline fuel economy compared
`to a reference oil (procedure listed as CEC L-54-X-94).
`
`The ACEA A gasoline engine oil categories also include bench testing for shear stability, high
`temperature/high shear (HTHS), NOACK volatility, sulfated ash limits, foaming properties, and
`elastomer compatibility limits.
`
`Copyright © 1999 Marcel Dekker, Inc.
`
`Page 5 of 20
`
`
`
`Automotive Crankcase Oils
`
`445
`
`D. Diesel Engine Oils
`North American diesel engine oils are predominantly for heavy-duty commercial use. The API
`CF-4 and CG-4 commercial categories and the MIL-L-2104F military category use a set of
`engine tests for defining minimum oil performance. The most current and stringent category,
`API CG-4, uses two test sequences built around the same rigs and conditions as the SG gasoline
`engine oil tests, these include the CRC L-38 and Sequence III-E (described in Section I.C). The
`CG-4 also requires three more tests, as follows.
`
`Caterpillar IN: uses a single-cylinder Caterpillar test engine (148.8 CID). This test measures an
`oil’s ability to resist formation of excess piston deposits, specifically the top land and top
`groove areas of the piston. The oil consumption is also measured, in grams per kilowatthour.
`Mack T-8: uses Mack E7-350 six-cylinder commercial diesel engine (11.93 L). This engine test
`measures an oil’s ability to resist viscosity increases due to excessive soot formation. The
`engine oil is measured for viscosity increase, soot loading, maximum oil pressure drop at the
`filter, and oil consumption.
`GMPT 6.2 L: uses a General Motors commercial engine (6.2 L). This test measures an oil’s abil-
`ity to give protection from roller follower wear in the engine.
`
`The CG-4 test program also involves the Cummins Corrosion Bench Test, the D-130 Copper
`Corrosion Test, and the ASTM D-892 Foam Test (Sequences I–IV).
`Currently, the industry is laying the groundwork for the next generation of diesel engine cat-
`egories (API PC-7 and PC-8). Driving both the North American and European changes are the
`more stringent emission requirements imposed by national legislatures. U.S. Federal Regulations
`mandate the profile shown in Fig. 1.
`The engineering challenge associated with these changes reflects the reluctance of OEM and
`end user alike to accept shorter drain intervals or shortened engine overhaul life. The industry is
`pushing for both extended oil drains and maintaining engine life.
`European diesel engine oils are designated for light to medium duty use or medium to heavy
`duty use. The ACEA members are using the following temporary designations for the develop-
`ment of the light-duty diesel categories (for passenger cars and vans):
`
`Copyright © 1999 Marcel Dekker, Inc.
`
`Page 6 of 20
`
`
`
`446
`
`B1-96 Current Quality/Economy
`B2-96 (PD-2) Extended Drain
`B3-96 (High Tier, Extended Drain
`
`Lakes
`
`Engine tests for minimal oil performance include the following:
`
`MB OM 602A: uses a Mercedes-Benz commercial engine (2.5 L). This test serves for all three
`categories and measures an oil’s ability to resist cam wear, bore polishing, sludge formation,
`and excessive oil consumption in the engine, as well as cylinder cleanliness. The engine oil
`is measured for viscosity increase and wear metals (procedure listed as CEC L-51-T-95).
`VW 1.6 L TC: uses a TC intercooled Volkswagen commercial diesel engine (1.6 L). This test
`measures an engine oil’s ability to resist ring sticking and to maintain piston cleanliness
`under high temperature conditions (procedure listed as CEC L-46-T-93).
`XUDllATE: uses a Peugeot commercial diesel engine (2.09 L). This test measures an engine oil’s
`ability to resist ring sticking and to maintain piston cleanliness (merit system). The engine
`oil is measured for viscosity increase under soot loading conditions (procedure listed as CEC
`L-56-T-95).
`
`For the development of heavy-duty diesel (trucks and off-road equipment) categories, ACEA
`is using the following temporary designations:
`
`El-96 Current Quality
`E2-96 Extended Drain Euro I
`E3-96 Extended Drain Euro II
`TD-4 Next Generation/Under Development
`
`Engine tests for minimal oil performance include the following:
`
`MB OM 602A: same test platform and conditions as B-96 categories.
`MB OM 364A: uses a Mercedes-Benz commercial diesel engine (3.97 L). This test, used in all
`three categories with different passing criteria, measures an oil’s ability to resist bore polish-
`ing, piston varnish/deposits, sludge formation, cylinder wear, and excessive oil consumption
`(procedure listed as CEC L-42-A-92).
`Mack T-8: see North American CG-4 category, above.
`
`Both the B-96 and E-96 categories also evaluate shear stability (Bosch injector), HTHS viscosi-
`ty, NOACK volatility, sulfated ash, foaming properties, and elastomer compatibility. Most
`European OEMs also require additional engine testing for specific usage and warranty
`applications.
`
`II. HISTORICAL ASPECTS OF SYNTHETIC ENGINE OILS
`A. Early Fluids
`Synthetic hydrocarbons and esters for engine lubricants were initially researched in the 1920s and
`1930s. Both F. W. Sullivan et al. of Standard Oil in the United States [1,2] and Zorn of I. G.
`Farben in Germany [3] were investigating the polymerization of olefins to form improved engine
`oil base stocks. These were the first synthetic hydrocarbons comparable to the poly(␣-olefins)
`(PAOs) of today. Ester base stocks were also under development at the same time for improved
`low temperature properties. These synthetic base stocks never realized significant engine oil
`commercialization for economic and supply reasons.
`During the 1940s, with the development of the turboprop and jet turbine aircraft engines,
`interest in ester lubricants was renewed. However, it was not until the 1960s, with the impetus
`
`Copyright © 1999 Marcel Dekker, Inc.
`
`Page 7 of 20
`
`
`
`Automotive Crankcase Oils
`
`447
`
`of military and construction requirements for arctic conditions, that synthetic engine lubricants
`had a resurgence. In the 1970s, with higher crude oil prices, interest developed in synthetic
`engine oils for the commercial market. These formulations used ester base stocks initially and
`later used PAOs in full and partial synthetic formulations. In the 1970s, several engine oil pro-
`ducers in the United States marketed products for passenger car engine oils. Synthetic products
`were also developed and marketed in Europe and Japan during this time.
`Worldwide, synthetic engine oils were very slow to be accepted and still comprise a
`small market share. Engine manufacturers are beginning to recognize the benefits of fully
`and partially synthetic oils.
`
`B. Need for Synthetic Engine Oils
`There are only three reasons for a consumer to use a synthetic or partial synthetic engine oil.
`
`It solves a technical problem.
`1.
`Its use results in improved economics.
`2.
`3. Governmental regulations.
`
`Technical requirements may involve using synthetics to satisfy high or low temperature proper-
`lies, to improve oil durability, or to improve engine test performance. In Europe, the addition of
`PAO and ester base stocks has allowed oil formulators to increased thermal/oxidative stability
`requirements and to achieve improved volatility specifications and better low temperature start-
`ing. In North America, OEMs are requiring more stringent lubricant performance in engine clean-
`liness, as well as improved volatility and low temperature pumping/starting. OEMs are starting
`to specify synthetic engine oils for some high performance applications (e.g., GM’s Chevrolet
`Corvette).
`Full synthetic arctic engine oils have been used by the U.S. military, NATO, and civilian
`companies since the early 1970s for equipment serving in extreme cold weather conditions
`MIL-L-46167B).
`The use of synthetics in engine oils has just started to show economic justification in the mar-
`ketplace. The consumer—whether an individual with a passenger car, a leasing company with
`return vehicles, or a business with a fleet of trucks—is beginning to recognize the economic
`advantage of increased engine life that is associated with the use of high performance oils. This
`advantage can be shown for extended vehicle service or residuals on resale.
`High performance, heavy-duty diesel engine oils are under development and testing to
`extend the oil drain interval and to lower maintenance costs, while maintaining or increasing
`engine operating life. Synthetic components (PAO, diester, polyol esters) are being evaluated in
`conjunction with high performance additive systems for this “next generation” HDDO. These
`components are being added at 5–30 wt % with petroleum base stock for enhanced additive and
`by-product solubility, improved engine cleanliness, good viscometric properties, and lower oil
`volatility.
`Worldwide, government regulations are starting to reflect concerns with vehicle fuel
`usage and the environmental impact of the products of the internal combustion engine. These
`regulations are affecting vehicle and engine design and formulations for the lubricants used
`in these vehicles. Fuel economy has been subject to government guidelines since the 1970s
`(CAFE in the United States). Heavy-duty diesel emissions guidelines in 1978, 1994, and 1998
`in North America and corresponding requirements in Europe and the Far East are changing
`the engines and oils. All these requirements are designed to promote more efficient energy
`usage and to diminish the environmental impact of these engines.
`
`Copyright © 1999 Marcel Dekker, Inc.
`
`Page 8 of 20
`
`
`
`448
`
`Lakes
`
`III. TYPES OF SYNTHETIC
`A. Definition
`In no other area of lubrication has the definition of “synthetic” generated as much debate or confu-
`sion as in engine oils. Technical definitions are being combined with performance attributes to pro-
`mote highly modified petroleum oils as a “synthetic” or “synthetic performing” product. The reasons
`are economic and are related to business goals. The use of the label “synthetic” has a high perform-
`ance connotation for the engine oil consumer and can justify a higher price. In this chapter, “synthet-
`ic” refers to a technical category. According to the ASTM, a synthetic lubricant is “a product which
`consists of stocks manufactured by chemical synthesis and containing necessary performance addi-
`tives.” To the chemical technologist, synthesis involves taking smaller chemical building blocks and
`combining them in a predictable, ordered reaction to form precise larger molecules.
`
`B. Synthetic Base Stocks
`For engine oils, the term “synthetic” refers to the base stock portion of the compounded oil. The
`additives and any polymers present are usually considered synthetic, being synthesized for spe-
`cific chemical purposes. The base stock constituent can be made from petroleum or synthesized
`structures (Fig. 2) or a combination of the two.
`The predominant synthetic base stocks currently used in engine oils are PAOs and carboxylic
`acid esters (diesters, polyol esters, or complex esters). Other synthetics include polyalkylene gly-
`cols (PAGs), phosphate esters, silicones, and alkylated aromatics, but these constitute only a
`small market share and, if used, are present only at additive levels in commercial engine oils.
`PAOs and esters may be used at various levels in gasoline and diesel engine oils. Most oil
`formulators consider up to 10% as an additive level treatment and 10% or higher as a base stock
`addition.
`Full synthetic gasoline engine oils are usually all PAO or a PAO/ester mixture. Full synthet-
`ics using all-ester base stock were developed and marketed in the 1970s. These oils showed good
`thermal stability and cleanliness, but seal and petroleum oil compatibility questions relegated them
`to small-niche, specific-use areas. The all-PAO and PAO/ester synthetic gasoline engine oils do not
`exhibit these deficiencies and are being successfully marketed throughout the world. Full synthet-
`ic diesel engine oils have been developed but have attained little market share for reasons of cost.
`
`Copyright © 1999 Marcel Dekker, Inc.
`
`Page 9 of 20
`
`
`
`Automotive Crankcase Oils
`
`449
`
`Partial synthetics utilize the addition of PAO, ester, or PAO/ester combination to enhance
`performance characteristics. Typical levels are 5–30 wt % in petroleum. Compared to conven-
`tional and unconventional petroleum oils (CBOs and UCBOs), PAO or ester may contribute
`desirable performance properties to the formulated oil, as indicated in Fig. 3.
`Most additive systems for engine oils were developed for a petroleum-based system and
`may not be suitable for synthetic oils. Additive selection for synthetics and partial synthetics is
`affected by the type and quantity of the base stock present. As a rule, PAO formulations show
`lower solubility for the polar additive packages than is found with petroleum. These polar addi-
`tives moderate detergent, dispersant, TBN, antiwear, and anticorrosion performance properties.
`The engine oil formulator may have to consider screening for acceptable additives or incorpo-
`rating longer alkyl chains on the additive molecules. Ester-containing formulations usually show
`higher solubility for these polar additives than is found with PAO or petroleum base stocks. A
`combination of PAO and ester may be used to “dial in” a specific polarity index to the base stock
`to maximize additive and by-product solubility. Elastomer compatibility (seals, gaskets) may
`also be accurately defined with a mixed PAO/ester system without the use of a seal swell agent.
`Polymers used for viscosity index improvement or thickening can also be affected by the
`base stock type. The use of PAO or ester can alter the polarity of the oil sufficiently to impact
`compatibility of some oligomers. In evaluating an unknown system or polymer, all formulated
`oils should be fully tested for storage and for high and low temperature compatibility as part of
`the testing regime.
`
`IV. COMPARATIVE PERFORMANCE DATA
`A. Bulk Physical Properties
`The predominant viscosity grades for synthetic base stocks in engine oils are 4 to 6 cSt (at
`100⬚C). This conforms to 100–200 SN petroleum oil. PAOs and esters (diester, polyol ester) usu-
`ally show improved viscometrics, higher viscosity index, improved low temperature properties,
`and lower volatility, compared to petroleum base stock, (Figs. 4 and 5).
`
`B. High Temperature Performance
`Automotive synthetic base stocks (PAO and ester) exhibit improved high temperature properties
`versus petroleum oils of comparable viscosity. These improvements are characterized by viscos-
`
`Copyright © 1999 Marcel Dekker, Inc.
`
`Page 10 of 20
`
`
`
`450
`
`Lakes
`
`ity retention at high temperature (due to a higher viscosity index), higher flash points, and lower
`volatility.
`Higher viscosity index base stocks, whether petroleum or synthetic, will exhibit lower vis-
`cosity loss upon temperature increase. This property will translate into higher film strength for
`hydrodynamic and elastohydrodynamic lubrication in the engine. At high temperatures this set of
`characteristics will mean improved protection for bearings (sleeve, ball, or needle) and rotating
`seals. High temperature/high shear is a test method for predicting viscosity effects for bearing
`wear for automotive engine [4]. Higher wear protection (boundary lubrication) for cams and
`valve lifters usually is handled by the antiwear additives present.
`Flash points are performed on engine oils to measure their flammability limits for storage
`and handling. Shipping requirements of the U.S. Department of Transportation (DOT) and OEM
`safety guidelines limit the flash points for commercial gasoline and diesel engine lubricants. The
`predominant test utilized for engine oils is the ASTM D-92 Cleveland open cup (COC) method.
`Petroleum-based oils have a wide range of molecular weights within a distillation fraction.
`By contrast with these refined base stocks, synthetic base stocks are more highly controlled
`for structures and composition. This results in tighter molecular weights and lower extraneous
`functional groups present, which may impact flash points. As shown in Figs. 4 and 5, PAOs
`
`Copyright © 1999 Marcel Dekker, Inc.
`
`Page 11 of 20
`
`
`
`Automotive Crankcase Oils
`
`451
`
`and esters exhibit higher flash points than petroleum base stocks of comparable viscosity. Esters,
`which contain polar functional groups, will exhibit higher flash points than petroleum or PAO
`feeds of similar molecular weight. This property is due to hydrogen bonding on the molecular
`level. Care must be exercised in the preparation and refining of esters to ensure low levels of
`unreacted acids or alcohols. These low molecular weight components will have a significant
`impact on flash point.
`Addition of synthetic components to petroleum-based engine oils will do little to improve
`the flash point. Full synthetic engine oils usually exhibit the best flash point properties. Fire
`points (temperature at which an oil will sustain combustion) is similar for petroleum-, PAO-, or
`ester-based engine oils of the same molecular weight.
`Engine oil volatility is a measure of an oil’s resistance to evaporation under high tempera-
`ture operating conditions. This is an important property for an engine lubricant because the loss
`of lower molecular weight components can significantly impact the viscosity properties. A 5W-
`30 oil that shows excessive volatility loss may end up being a 10W-40 or higher viscosity grade
`oil after several hundred miles of service. A correlation has been established between NOACK
`volatility and oil consumption [5].
`Several methods are used for measuring volatility, including the ASTM D-2887 distillation
`method and the CEC L-40-T-87 NOACK volatility test. Synthetic base stocks have lower volatil-
`ity losses by both methods [6]. (Figures 4 and 5 show comparative NOACK volatility data.) The
`addition of synthetic base stock can impact the overall volatility properties, even with small lev-
`els. The resulting final volatility will be approximately the algebraic calculation of the two com-
`ponents. Petroleum-based engine lubricants can be topped off with PAO or ester to shift the
`volatility into the passing range (Fig. 6).
`Both petroleum and synthetic low volatility base stocks have been investigated with a view
`to formulating lower volatility engine lubricants [7].
`
`C. Low Temperature Characteristics
`Full synthetic engine lubricants offer excellent low temperature flow and viscosity properties.
`PAO and ester base stocks show significantly lower pour points than petroleum oils (see Figs, 4
`and 5). This advantage is due to molecular structure and to the lack of crystalline wax particles,
`
`Copyright © 1999 Marcel Dekker, Inc.
`
`Page 12 of 20
`
`
`
`452
`
`Lakes
`
`present in some refined petroleum oils. These lower pour points translate into better low temper-
`ature flow and protection in both gasoline and diesel engine oils. Low temperature flow proper-
`ties may be measured in gasoline and diesel engine oils using laboratory viscosity methods
`(ASTM D-5293; Cold Crank Simulator, ASTM D-4684; MRV Pumping, Scanning Brookfield
`Viscosity), cold box simulation testing, and field conditions [8–12].
`The low pour properties of the synthetic base stocks allow the formulator a tool for adjust-
`ing petroleum-based engine oils for improved low temperature properties. Both PAO and ester
`may be used to achieve this improvement. For example, the addition of PAO (PAO-4) to a 5W-
`30 petroleum-based engine oil resulted in improved low temperature viscosity and pour points
`(Figs. 7 and 8).
`Typical petroleum-based engine oils contain pour point depressants that interrupt the crystal
`lattice formation of the wax content. The addition of synthetic base stock usually allows the
`removal of the pour point depressant from the additive package. Some low temperature compat-
`ibility problems (e.g., slight hazing or precipitate floc of the pour point depressant under low tem-
`perature, long-term storage) have been experienced with the use of certain pour point depressants
`and synthetics.
`
`Copyright © 1999 Marcel Dekker, Inc.
`
`Page 13 of 20
`
`
`
`Automotive Crankcase Oils
`
`453
`
`Specialty arctic engine oils have been developed for very low temperature usage, predomi-
`nantly for the military and the oil exploration industry. Full synthetics have been used for these
`applications since the mid-1970s and constitute the majority of these fluids designed for cold
`weather environments.
`
`D. Antiwear Performance
`Engine oils require a certain level of antiwear capability. This antiwear requirement ensures an
`oil’s ability to protect moving parts (e.g., rocker arm contacts, cams, cylinder ring/wall contact
`areas) under boundary lubrication conditions. In modern engine oil formulations, antiwear capa-
`bility is predominantly supplied by the additive package. The base stock portion, either petroleum
`or synthetic, has little antiwear capability. Petroleum oils may have a small amount of antiwear
`present as trace levels of sulfur, nitrogen, or phosphorus functionality from the crude petroleum
`source, but they contain an insufficient amount to provide protection for modern engines.
`The use of PAO or ester may require a higher uptreat of antiwear additive to compensate for
`the absence of these “natural” additives. PAO will be similar to petroleum for the treat level effect
`of most antiwear additive systems. Ester-containing engine oils may require an uptreat of anti-
`wear additive to achieve the same level of protection as petroleum-based systems. Esters are
`more polar than both petroleum and PAOs and may compete at the metal surface with any polar
`additives (antiwear agents, corrosion inhibitors, etc.).
`
`E. Shear Stability
`Most multigrade gasoline or diesel engine oils use a viscosity polymer for thickening the oil and
`improving the viscosity index. This allows the formulation of a cross-graded product that
`exhibits good viscometric profiles both at high temperatures (at operating conditions) and at low
`temperatures (during starting). The introduction of viscosity polymers required the industry to
`evaluate the properties of temporary and permanent viscosity loss under various shear condi-
`tions. High temperature/high shear (HTHS, ASTM D-4624 and D-4683) is used to measure the
`temporary viscosity loss under high shear load, which simulates the condition of the oil in the
`crankshaft bearings. The use of synthetic base stocks, with their higher viscosity index, may
`improve the HTHS slightly, but this effect is usually small compared to the contribution of the
`viscosity polymer.
`Permanent shear loss is measured by subjecting the motor oil to a shear force sufficient to
`cause breakage of the polymer structures, resulting in viscosity loss. Several procedures are avail-
`able for shear stability testing for engine oils. These include sonic shear (ASTM 2603), Orbahn
`shear (D-3945) and Bosch injector (CEC L-14). Synthetic automotive base stocks (PAOs, esters)
`are similar to petroleum and show little or no viscosity loss under these
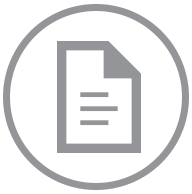
Accessing this document will incur an additional charge of $.
After purchase, you can access this document again without charge.
Accept $ ChargeStill Working On It
This document is taking longer than usual to download. This can happen if we need to contact the court directly to obtain the document and their servers are running slowly.
Give it another minute or two to complete, and then try the refresh button.
A few More Minutes ... Still Working
It can take up to 5 minutes for us to download a document if the court servers are running slowly.
Thank you for your continued patience.
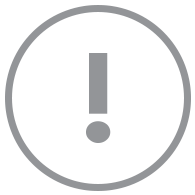
This document could not be displayed.
We could not find this document within its docket. Please go back to the docket page and check the link. If that does not work, go back to the docket and refresh it to pull the newest information.
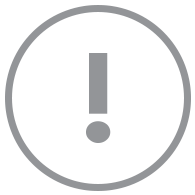
Your account does not support viewing this document.
You need a Paid Account to view this document. Click here to change your account type.
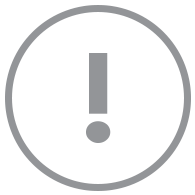
Your account does not support viewing this document.
Set your membership
status to view this document.
With a Docket Alarm membership, you'll
get a whole lot more, including:
- Up-to-date information for this case.
- Email alerts whenever there is an update.
- Full text search for other cases.
- Get email alerts whenever a new case matches your search.
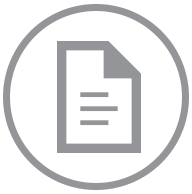
One Moment Please
The filing “” is large (MB) and is being downloaded.
Please refresh this page in a few minutes to see if the filing has been downloaded. The filing will also be emailed to you when the download completes.
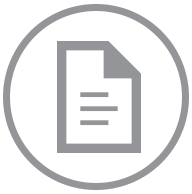
Your document is on its way!
If you do not receive the document in five minutes, contact support at support@docketalarm.com.
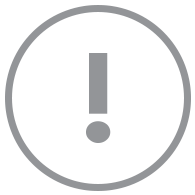
Sealed Document
We are unable to display this document, it may be under a court ordered seal.
If you have proper credentials to access the file, you may proceed directly to the court's system using your government issued username and password.
Access Government Site