`
`!
`
`.
`
`poy
`Ba
`PATENT APPLICATION TRANSMITTAL FORM
`4 v
`~~
`nm == SASSISTANT COMMISSIONERFOR PATENTS
`SS === Washington, D.C. 20231
`>.
`— ar
`{X]
`
`"PATENT" fr
`
`Case Docket No. 20021004 2 =
`= ——
`EL325202599US
`"Express Mail” mailing label number
`. Date of Deposit April 5, 2002. wo ==c
`Thereby certify that this paper or fee is being deposited with the United States Postal Service "Express Mai =n
`Post Office to Addressee" service under 37 CFR 1.10 on the date indicated above and is addressed to thew>=s5
`Assistant Commissioner for Patents, Washington, D.C. 20231.
`ie
`>
`Ly
`
`=v
`
`Regina F. Anginoli
`(Typed or printed name of person mailing paper or fee)
`
`Transmitted herewith for filing is the patent application of
`
`Inventor:
`
`For:
`
`Rolfe J. Hartley, Malcolm Waddoups
`Lubricating Oil Composition
`
`_ Enclosed are:
`
`(X]
`
`Sasso
`
`oreeeeee
`
`[xX]
`ix]
`tJ
`
`[Xx]
`
`Specification and Claims with Declaration;
`Specification and Claims without Declaration;
`sheets of informal drawings;
`sheets of formal drawings;
`An assignmentof the invention to
`The certified copy of a priority application,
`Information Disclosure Statement, Form - 1449;
`Copies ofcitations as listed on attached Form - 1449;
`Preliminary Amendment;
`
`Address all future communicationsto:
`
`Infineum USA L.P.
`Law Department
`1900 East Linden Avenue
`P.O. Box 710
`Linden, New Jersey 07036-0710
`
`[
`
`]
`
`Filed on
`Priority of application Serial No.
`in
`is claimed under 35 USC 119.
`
`(Country)
`
`[Xx]
`
`The Filing Fee is calculated below.
`
`
`
`
`
`CLAIMS AS FILED po
`
`
`
`
`
`
`
`
`
`Lindependentcaims|3=]|xsao|co
`Muitiple Dependent Claim Fee PP
`$280.00
`
`
`potorarecrcs||76.00|
`
`Please charge my Deposit Account No. 05-1710 in the amountof $
`
`776.00
`
`[X]
`
`[X]
`
`The Assistant Commissioner is hereby authorized to charge any additional fees which may be
`required during the entire pendency of the application, or credit any overpayment, to Deposit
`Account No. 05-1710. A duplicate copy of this Form is enclosed
`April 5, 2002
`Date of Signature
`
` Attomey or Agent
`
`
`Infineum USA L.P.
`Law Department
`1900 East Linden Avenue
`P.O. Box 710
`Linden, New Jersey 07036-0710
`
`acob M.Levine
`Registration No. 32,509
`Telephone No. (908) 474-2418
`Facsimile No. (908) 474-2431
`
`‘
`(For Internal Use Only: Job Ne. 813,856)
`
`Page 1 of 219
`
`ORONITE EXHIBIT 1004
`
`Page 1 of 219
`
`ORONITE EXHIBIT 1004
`
`
`
`IN THE UNITED STATES PATENT AND TRADEMARK OFFICE
`
`“LUBRICATING OIL COMPOSITION”
`
`(2002L004)
`
`Inventor(s):
`
`Rolfe J. HARTLEY
`Malcolm WADDOUPS
`
`EL325202599US
`“Express Mail’ mailing label! number
`Date of Deposit
`April 5, 2002
`| hereby certify that this paper or fee is being deposited with the
`United States Postal Service “Express Mail Post Office to Addressee”
`service under 37 CFR 1.10 on the date indicated above and is
`addressed to the Commissioner of Patents and Trademarks,
`Washington, D.C. 20231.
`
`(Typed
`
`Regina F. Anginoli
`inted name of person mailing paper or fee)
`
`
`
`
`
`Page 2 of 219
`
`Page 2 of 219
`
`
`
`LUBRICATING OIL COMPOSITION
`
`The present invention relates to lubricating oil compositions. More particularly,
`
`the present invention relates to lubricating oil compositions, which exhibit
`
`simultaneously improved low temperature valve train wear performance, excellent
`
`compatibility with fluoroelastomer materials commonly used for seals in modern
`
`internal combustion engines, and improved fuel economy properties.
`
`BACKGROUND OF THE INVENTION
`
`10
`
`Lubricating oil compositions used to lubricate internal combustion engines
`
`15
`
`20
`
`25
`
`30
`
`contain base oil of lubricating viscosity, or a mixture of such oils, and additives used
`
`to improve the performance characteristics of the oil. For example, additives are used
`
`to improve detergency, to reduce engine wear, to provide stability against heat and
`
`oxidation, to reduce oil consumption, to inhibit corrosion, to act as a dispersant, and to
`
`reduce friction loss. Some additives provide multiple benefits, such as dispersant-
`
`viscosity modifiers. Other additives, while improving one characteristic of the
`
`lubricating oil, have an adverse effect on other characteristics. Thus, to provide
`
`lubricating oil having optimal overall performance, it is necessary to characterize and
`
`understand all the effects of the various additives available, and carefully balance the
`
`additive content of the lubricant.
`
`It has been proposed in many patents and articles (for example, U.S. Patent
`
`No. 4,164,473; 4,176,073; 4,176,074; 4,192,757, 4,248,720; 4,201,683; 4,289,635;
`
`and 4,479,883) that oil-soluble molybdenum compoundsare useful as lubricant
`
`additives. In particular, the addition of molybdenum compoundsto oil, particularly
`
`molybdenum dithiocarbamate compounds, provides the oil with improved boundary
`
`friction characteristics and bench tests demonstrate that the coefficientof friction of
`
`oil containing such molybdenum compoundsis generally lower than thatof oil
`
`containing organic friction modifiers. This reduction in coefficient of friction results
`
`in improved antiwear properties and may contribute to enhanced fuel economyin
`
`gasoline or diesel fired engines, including both short- and long-term fuel economy
`
`properties (i.e., fuel economy retention properties). To provide antiwear effects,
`
`molybdenum compoundsare generally added in amounts introducing from about 350
`
`ppm up to 2,000 ppm of molybdenum into the oil. While molybdenum compounds
`
`Page 3 of 219
`
`Page 3 of 219
`
`
`
`-2-
`
`are effective antiwear agents and may further provide fuel economybenefits, such
`
`molybdenum compoundsare expensive relative to more conventional, metal-free
`
`(ashiess) organic friction modifiers
`
`U.S. Patent No. 6,300,291 discloses a lubricating oil composition having a
`
`specified Noack volatility containing a base oil of a specified viscosity index,
`
`calcium-based detergent, zinc dihydrocarbyldithiophosphate (ZDDP) antiwear agent,
`
`a molybdenum compound and a nitrogen-containing friction modifier. The
`
`molybdenum compound wasused in an amount providing the formulated lubricant
`
`10
`
`with up to 350 ppm of molybdenum. The claimed materials are described as
`
`15
`
`20
`
`25
`
`30
`
`providing fuel economy benefits compared to compositions containing only
`‘molybdenum compounds.
`
`Modern internal combustion engines include numerous gaskets and other seals formed
`of fluoroelastomer materials, such as Viton™. Nitrogen-containing additives are
`suspected of, over time, contributing to the deterioration of such materials. Therefore,
`
`it would be desirable to find a lubricating oil composition that provides improved fuel
`
`economy benefit; demonstrates excellent wear protection characteristics, is relatively.
`
`low in cost, and is free of nitrogen-containing friction modifiers.
`
`It has now been found that the addition of small amounts of one or moreoil
`
`soluble molybdenum compounds, in combination with an ashless, organic nitrogen-
`
`free friction modifier, ZDDP. and a calcium detergent provide low cost lubricating oils —
`
`having a demonstrable fuel economy benefit; excellent wear protection
`characteristics, and reduced adverseeffects on engine seals formed of Viton™ and
`similar fluoroelastomers.
`
`The present invention also provides many additional advantages that shall
`
`become apparent as described below.
`
`SUMMARY OF THE INVENTION
`
`In accordance with a first aspect, the invention provides a lubricating oil
`
`composition displaying excellent low temperature valve train wear performance,
`
`Page 4 of 219
`
`Page 4 of 219
`
`
`
`-3-
`
`improved fuel economy retention properties and compatibility with fluoroelastomer-
`based engine seals, which composition comprises an oil of lubricating viscosity
`having a viscosity index (VDofat least 95; a calcium detergent in an amount
`introducing from about 0.05 to about 0.6 wt. % calcium into the composition; an
`amount of a metal dihydrocarbyldithiophosphate compound introducing up to 0.1 wt.
`% (1000 ppm) of phosphorusinto the composition; at least one molybdenum
`compound in an amountsufficient to provide the composition with at least 10 ppm of
`molybdenum; and an effective amountofat least one organic, nitrogen-free, ashless
`friction modifier; the composition having a Noack volatility of less than 15 %.
`
`In accordance with a second aspect, the invention is directed to a method of
`improving the fuel economy,seal life and/or the wear characteristics of an internal
`combustion engine, which method comprises the steps of lubricating an internal
`combustion engine with a lubricating oil composition ofthefirst aspect and operating
`the engine.
`
`In accordance with a third aspect, the invention is directed to the use of a
`lubricating oil composition ofthe first aspect to improve the fuel economy,seal life
`and/or the wear characteristics of an internal combustion engine.
`
`Other and further objects, advantages and features of the present invention will
`be understood by referenceto the following.
`
`10
`
`20
`
`25
`
`30
`
`DESCRIPTION OF THE PREFERRED EMBODIMENTS
`The oil of lubricating viscosity can be at least one oil selected from the group
`consisting of Group I, GroupIL, or GroupIII base stocksorbase oil blends ofthe
`aforementioned base stocks providedthat the viscosity of the base oil or base oil
`blend is at least 95 and allowsfor the formulation of a lubricating oil composition
`having a Noackvolatility, measured by determining the evaporative loss in mass
`percentofan oil after 1 hour at 250°C accordingto the procedure of ASTM D5880, of
`less than 15%. In addition,the oil of lubricating viscosity may be one or more Group
`IV or Group V base stocks or combinations thereof or base oil mixtures containing
`
`Page 5 of 219
`
`Page 5 of 219
`
`
`
`-4-
`
`one or more Group IV or Group V base stocks in combination with one or more
`
`Group I, Group 0 and/or Group III base stocks.
`
`The mostpreferred oils for fuel economyretention, are:
`
`(a)
`
`Base oil blends of Group III base stocks with Group I or Group II base
`
`stocks, where the combination has a viscosity index of at least 110; or
`
`(b)
`
`Group III, IV or V base stocks or base oil blends of more than one
`
`Group III, IV or V base stocks, where the viscosity index is between
`
`about 120 to about 140.
`
`Definitions for the base stocks and baseoils in this invention are the same as
`
`those found in the American Petroleum Institute (API) publication “Engine Oil
`
`Licensing and Certification System”, Industry Services Department, Fourteenth
`
`Edition, December 1996, Addendum 1, December 1998. Said publication categorizes
`base stocks as follows:
`
`a) Group I base stocks contain less than 90 percent saturates and/or greater than 0.03
`
`percent sulfur and have a viscosity index greater than or equal to 80 andless than 120
`
`using the test methods specified in Table E-1.
`
`b) Group II base stocks contain greater than or equal to 90 percent saturates and less
`
`than or equal to 0.03 percent sulfur and have a viscosity index greater than or equal to
`80 and less than 120 using the test methods specified in Table E-1.
`
`c) GroupIII base stocks contain greater than or equal to 90 percentsaturates and less
`than or equal to 0.03 percent sulfur and have a viscosity index greater than or equal to
`
`10
`
`20
`
`25
`
`120 using the test methods specified in Table E-1.
`
`d) Group IV base stocks are polyalphaolefins (PAO).
`e) Group V base stocks include all other base stocks not included in Group I,II, IH, or
`
`Iv.
`
`30
`
`Page 6 of 219
`
`Page 6 of 219
`
`
`
`Table E-1 - Analytical Methods for Base Stock
`
`-5-
`
`
`
`
`
`
`
`Le
`
`sane
`
`
`asso
`
`
`
`
`
`
`
`
`
`
`10
`
`Forthe lubricating oil compositions of this invention, any suitable oil-soluble
`organo-molybdenum compoundhavingfriction modifying and/or anti-wear properties in
`lubricating oil compositions may be employed. As an example of such oil-soluble
`organo-molybdenum compounds, there may be mentioned the dithiocarbamates,
`dithiophosphates,dithiophosphinates, xanthates, thioxanthates, sulfides, and the like, and
`mixtures thereof. Particularly preferred are molybdenum dithiocarbamates,
`
`dialkyldithiophosphates, alkyl xanthates and alkylthioxanthates.
`
`The molybdenum compound may be mono-, di-, tri- or tetra-nuclear. Dinuclear
`and trinuclear molybdenum compoundsare preferred. The molybdenum compoundis
`preferably an organo-molybdenum compound. Morepreferably, the molybdenum
`compoundis selected from the group consisting of molybdenum dithiocarbamates
`(MoDTC), molybdenum dithiophosphates, molybdenum dithiophosphinates,
`molybdenum xanthates, molybdenum thioxanthates, molybdenum sulfides and
`mixtures thereof. Most preferably, the molybdenum compoundis present as a
`molybdenum dithiocarbamate or a trinuclear organo-molybdenum compound.
`
`20
`
`25
`
`Additionally, the molybdenum compound maybe an acidic molybdenum
`compound. These compoundswill react with a basic nitrogen compound as measured
`by ASTM test D-664 or D-2896 titration procedure andare typically hexavalent.
`Included are molybdic acid, ammonium molybdate, sodium molybdate, potassium
`molybdate, and other alkaline metal molybdates and other molybdenumsalts,e.g.,
`hydrogen sodium molybdate, MoOCl,, MoO2Brm, Mo.03Clg, molybdenum trioxide or
`similar acidic molybdenum compounds. Alternatively, the compositions of the
`
`Page 7 of 219
`
`Page 7 of 219
`
`
`
`-6-
`
`present invention can be provided with molybdenum by molybdenum/sulfur
`
`complexes of basic nitrogen compoundsas described, for example, in U.S. Patent
`
`Nos. 4,263,152; 4,285,822; 4,283,295; 4,272,387; 4,265,773; 4,261,843; 4,259,195
`
`and 4,259,194; and WO 94/06897.
`
`Among the molybdenum compoundsuseful in the compositions of this invention
`
`are organo-molybdenum compoundsofthe formulae
`
`Mo(ROCS>)4 and
`
`Mo(RSCS2)4
`
`15
`
`20
`
`wherein R is an organo groupselected from the group consisting of alkyl, aryl, aralkyl
`
`and alkoxyalkyl, generally of from 1 to 30 carbon atoms, and preferably 2 to 12 carbon
`
`atoms and most preferably alkyl of 2 to 12 carbon atoms. Especially preferred are the
`
`dialkyldithiocarbamates of molybdenum.
`
`Oneclass of preferred organo-molybdenum compoundsuseful in the lubricating
`
`compositions of this invention are trinuclear molybdenum compounds, especially those
`
`of the formula Mo3S;,L,Q, and mixtures thereof wherein L are independently selected
`
`ligands having organo groups with a sufficient number of carbon atomsto render the
`‘compoundsoluble or dispersible in the oil, n is from 1 to 4, k varies from 4 through 7, Q
`
`is selected from the group of neutral electron donating compounds such as water,
`
`amines, alcohols, phosphines, and ethers, and z ranges from 0 to 5 and includes non-
`
`stoichiometric values. At least 21 total carbon atoms should be present amongall the
`
`ligands’ organo groups, such as at least 25, at least 30, or at least 35 carbon atoms.
`
`25
`
`The ligands are independently selected from the group of
`
`——xX-——R
`
`Xy-\y—R
`
`Xy
`
`1
`
`"\ UYye y
`
`2
`
`1,
`
`2,
`
`3,
`
`R
`
`Page 8 of 219
`
`Page 8 of 219
`
`
`
`Xy
`
`
`
`Rj>)x5
`
`Ne
`
`and
`
`O-—R,Moe
`
`Xy
`
`X2
`
`O-——R,
`
`and mixtures thereof, wherein X, X), X2, and Y are independently selected from the
`
`group of oxygen and sulfur, and wherein R,, R2, and R are independently selected from
`
`hydrogen and organo groups that may be the sameor different. Preferably, the organo
`
`groups are hydrocarbyl groups such asalkyl (e.g., in which the carbon atom attached to
`
`the remainder of the ligand is primary or secondary), aryl, substituted aryl and ether
`
`groups. More preferably, each ligand has the same hydrocarbyl group.
`
`The term “hydrocarbyl” denotes a substituent having carbon atomsdirectly
`
`attached to the remainder of the ligand and is predominantly hydrocarbyl .in character
`
`within the context of this invention. Such substituents include the following:
`
`1.
`
`Hydrocarbon substituents,that is, aliphatic (for example alkyl or alkenyl), alicyclic
`
`(for example cycloalkyl or cycloalkenyl) substituents, aromatic-, aliphatic- and alicyclic-
`
`substituted aromatic nuclei and the like, as well as cyclic substituents wherein thering is
`
`completed through another portion ofthe ligand (that is, any two indicated substituents
`
`may together form an alicyclic group).
`
`2.
`
`Substituted hydrocarbon substituents, that is, those containing non-hydrocarbon
`
`groups which,in the context of this invention, do notalter the predominantly
`
`hydrocarbyl character of the substituent. Those skilled in the art will be aware of
`
`suitable groups (e.g., halo, especially chloro and fluoro, amino, alkoxyl, mercapto,
`
`alkylmercapto,nitro, nitroso, sulfoxy, etc.).
`
`10
`
`15
`
`20
`
`25
`
`Page 9 of 219
`
`Page 9 of 219
`
`
`
`-8-
`
`3.
`
`Hetero substituents, that is, substituents which, while predomimantly hydrocarbon
`
`in character within the context of this invention, contain atoms other than carbon present
`
`in a chain or ring otherwise composed of carbon atoms.
`
`Importantly, the organo groups ofthe ligands have a sufficient number of carbon
`
`atoms to render the compound soluble or dispersible in the oil. For example, the number
`
`of carbon atoms in each group will generally range between about 1 to about 100,
`
`preferably from about 1 to about 30, and more preferably between about 4 to about 20.
`
`Preferred ligands include dialkyldithiophosphate, alkylxanthate, and
`
`10
`
`dialkyldithiocarbamate, and of these dialkyldithiocarbamate is more preferred. Organic
`
`ligands containing two or more of the above functionalities are also capable of serving as
`
`ligands and binding to one or moreof the cores. Those skilled in the art will realize that
`
`formation of the compoundsofthe present invention requires selection of ligands having
`
`the appropriate charge to balance the core’s charge.
`
`Compounds having the formula Mo3S;L,Q,to have cationic cores surrounded by
`
`anionic ligands and are represented by structures such as
`
`5/\\,NZ|
`
`
`
`
`
`
`and
`
`20
`
`f|44 |a
`WsXV
`
`<<“
`
`Page 10 of 219
`
`Page 10 of 219
`
`
`
`-9-
`
`and have net charges of +4. Consequently, in order to solubilize these cores the total
`
`charge amongall the ligands must be -4. Four monoanionic ligands are preferred.
`
`Without wishing to be bound by anytheory,it is believed that two or more trinuclear
`
`cores may be boundor interconnected by means of one or more ligands and the ligands
`
`may be multidentate. This includes the case of a multidentate ligand having multiple
`
`connections to a single core. It is believed that oxygen and/or selenium may be
`
`substituted for sulfur in the core(s).
`
`Oil-soluble or dispersible trinuclear molybdenum compoundscan be prepared by
`
`10
`
`reacting in the appropriate liquid(s)/solvent(s) a molybdenum source such as
`
`15
`
`20
`
`(NH,)2Mo38;3.n(H20), where n varies between 0 and 2 and includes non-stoichiometric
`
`values, with a suitable ligand source such as a tetralkylthiuram disulfide. Other oil-
`
`soluble or dispersible trinuclear molybdenum compounds can be formed during a
`
`reaction in the appropriate solvent(s) of a molybdenum source such as of
`
`(NH4)2Mo3833.n(H20), a ligand source such as tetralkylthiuram disulfide,
`
`dialkyldithiocarbamate, or dialkyldithiophosphate, and a sulfur abstracting agent such as
`
`cyanideions, sulfite ions, or substituted phosphines. Alternatively, a trinuclear
`
`molybdenum-sulfur halide salt such as [M’]2[Mo3S7Ag¢], where M'’ is a counter ion, and A
`
`is a halogen such as Cl, Br, or I, may be reacted with a ligand source such as a
`
`dialkyldithiocarbamate or dialkyldithiophosphate in the appropriate liquid(s)/solvent(s)
`
`to form an oil-soluble or dispersible trinuclear molybdenum compound. The appropriate
`
`liquid/solvent may be, for example, aqueousor organic.
`
`A compound's oil solubility or dispersibility may be influenced by the number
`
`of carbon atomsin the ligand’s organo groups. In the compoundsof the present
`
`invention, at least 21 total carbon atoms should be present amongall the ligands’
`
`organo groups. Preferably, the ligand source chosen hasa sufficient numberof
`
`carbon atomsin its organo groups to render the compoundsoluble or dispersible in
`
`the lubricating composition.
`
`25
`
`30
`
`The terms “oil-soluble”or “dispersible” used herein do not necessarily indicate
`
`that the compoundsor additives are soluble, dissolvable, miscible, or capable of being
`
`suspended in the oil in all proportions. These do mean, however,that they are, for
`
`Page 11 of 219
`
`Page 11 of 219
`
`
`
`-10-
`
`instance, soluble or stably dispersible in oil to an extent sufficient to exert their
`
`intended effect in the environment in whichthe oil is employed. Moreover, the
`
`additional incorporation of other additives may also permit incorporation of higher
`
`levels of a particular additive, if desired.
`
`The lubricating compositions of the present invention contain the molybdenum
`compoundin an amount providing the composition with at least 10 ppm of
`molybdenum. An amountofat least 10 ppm of molybdenum from a molybdenum
`compoundhas been foundto be effective to provide a fuel economy benefit in
`combination with an ashless, organic nitrogen-free friction modifier. Preferably, the
`molybdenum from a molybdenum compoundis present in an amountof from about
`10 ppm to about 750 ppm, such as 10 ppm to 350 ppm, more preferably from about
`30 ppm to 200 ppm,still more preferably in an amount of from about 50 ppm to about
`100 ppm,based onthetotal weight of the lubricating composition. Because such
`
`molybdenum compoundsalso provide antiwearcredits to lubricating oil
`compositions, the use thereof allows for a reduction in the amount of metal
`dihydrocarbyl dithiophosphate antiwear agent (e.g., ZDDP) employed. Industry
`trends are leading to a reduction in the amount of ZDDP being addedto lubricating
`
`oils to reduce the phosphorous contentof the oil to below 1000 ppm,such as to 250
`ppm to 750 ppm, or 250 ppm to 500 ppm. To provide adequate wear protection in
`such low phosphorouslubricating oil compositions, the molybdenum compound
`should be present in an amount providing at least 50 ppm by mass of molybdenum.
`The amount of molybdenum and/or zinc may be determined by Inductively Coupled
`
`Plasma (ICP) emission spectroscopy using the method described in ASTM D5185.
`
`Organic, ashless (metal-free), nitrogen-free organic friction modifiers useful in
`the lubricating oil compositions of the present invention are known generally and include
`esters formed by reacting carboxylic acids and anhydrides with alkanols. Other useful
`friction modifiers generally include a polar terminal group (e.g. carboxyl or hydroxyl)
`covalently bondedto an oleophilic hydrocarbon chain. Esters of carboxylic acids and
`anhydrides with alkanols are described in US 4,702,850. Examples of other
`conventional organic friction modifiers are described by M.Belzerin the “Journal of
`
`10
`
`15
`20
`
`25
`
`30
`
`Page 12 of 219
`
`Page 12 of 219
`
`
`
`-il-
`
`Tribology" (1992), Vol. 114, pp. 675-682 and M. Belzer and S. Jahanmir in "Lubrication
`
`Science" (1988), Vol. 1, pp. 3-26.
`
`The organic friction modifier is included in the lubricating oil compositions of
`
`the present invention in an amount effective to allow the composition to reliably pass a
`
`Sequence VIB fuel economytest in combination with the molybdenum compound. For
`
`example, the organic ashless nitrogen-free friction modifier may be added to the
`
`molybdenum-containing lubricating oil composition in an amountsufficient to obtain
`
`a retained fuel economy improvementofat least 1.7% for an SAE 5W-20lubricant,
`
`1.1% for a 5W-30 lubricant, and 0.6% for a 1OW-30 lubricant as measured at 96 hours
`
`(Phase II performance) in the ASTM Sequence VIB Fuel Economy Test. Typically,
`
`to provide the desired effect, the organic ashless nitrogen-free friction modifieris
`
`added in an amount of from about 0.25 wt.% to about 2.0 wt.% (AD), based on the
`
`total weight of the lubricating oil composition. Preferred organic ashless nitrogen-
`
`free friction modifiers are esters; a particularly preferred organic ashless nitrogen-free
`
`friction modifier is glycerol monooleate (GMO).
`
`Ashless aminic friction modifiers excluded from compositions of the present
`
`invention include oil-soluble alkoxylated mono- and di-amines, which improve
`
`boundary layer lubrication, but may contribute to the deterioration over time of
`
`fluoroelastomer seal materials. One commonclass of such metal free, nitrogen-
`
`containing friction modifier comprises ethoxylated amines. These amines are also
`
`excluded when in the form of an adduct or reaction product with a boron compound such
`
`as a boric oxide, boron halide, metaborate, boric acid or a mono-, di- or tri-alkyl borate.
`
`Metal-containing or ash-forming detergents function both as detergents to reduce
`
`or removedeposits and as acid neutralizers or rust inhibitors, thereby reducing wear and
`
`corrosion and extending engine life. Detergents generally comprise a polar head with a
`
`long hydrophobictail, with the polar head comprising a metalsalt ofan acid organic
`
`compound. The salts may contain a substantially stoichiometric amount of the metal in
`
`which they are usually described as normal or neutral salts, and would typically have a
`
`total base number (TBN), as may be measured by ASTM D-2896of from 0 to 80. It is
`
`possible to include large amounts of a metal base by reacting an excess of a metal
`
`10
`
`15
`
`20
`
`25
`
`30
`
`Page 13 of 219
`
`Page 13 of 219
`
`
`
`-12-
`
`compound such as an oxide or hydroxide with an acid gas such as carbon dioxide. The
`
`resulting overbased detergent comprises neutralized detergent as the outer layer of a
`
`metal base (e.g., carbonate) micelle. Such overbased detergents may have a TBN of 150
`
`or greater, and typically from 250 to 450 or more.
`
`Knowndetergents include oil-soluble neutral and overbased sulfonates, phenates,
`
`sulfurized phenates, thiophosphonates, salicylates, and naphthenates and otheroil-
`
`soluble carboxylates of a metal, particularly the alkali or alkaline earth metals, e.g.,
`
`sodium, potassium,lithium, calcium, and magnesium. The most commonly used metals
`
`10
`
`are calcium and magnesium, which may both be present in detergents used in a
`
`
`20
`
`lubricant, and mixtures of calcium and/or magnesium with sodium. Particularly
`
`convenient metal detergents are neutral and overbased calcium sulfonates having TBN
`
`of from 20 to 450 TBN, and neutral and overbased calcium phenates and sulfurized
`
`phenates having TBN of from 50 to 450.
`
`In the present invention, one or more calcium-based detergents are used in an
`
`amount introducing from about 0.05 to about 0.6 wt. % calcium into the composition.
`
`The amount of calcium may be determined by Inductively Coupled Plasma (ICP)
`
`emission spectroscopy using the method described in ASTM D5185. Preferably, the
`
`calcium-based detergent is overbased and the total base numberof the overbased
`
`calcium based detergent is between about 150 to 450. More preferably, the calctum-
`
`based detergent is an overbased calcium sulfonate detergent. The compositions of the
`
`present invention may further include either neutral or overbased magnesium-based
`
`detergents, however, preferably, the lubricating oil compositions of the present
`
`25
`
`invention will be magnesium free.
`
`Metal dihydrocarbyl dithiophosphate antiwear agents that may be addedto the
`
`lubricating oil composition of the present invention comprise dihydrocarby]
`
`dithiophosphate metal salts wherein the metal may be an alkali or alkaline earth metal,
`
`30
`
`or aluminum,lead, tin, molybdenum, manganese,nickel, copper or preferably, zinc.
`
`The zinc salts are most commonly usedin lubricating oil.
`
`Page 14 of 219
`
`Page 14 of 219
`
`
`
`-13-
`
`Dihydrocarbyl dithiophosphate metal salts may be prepared in accordance with
`
`known techniquesbyfirst forming a dihydrecarbyl dithiophosphoric acid (DDPA),
`
`usually by reaction of one or more alcohol or a phenol with P2Ss5 and then neutralizing
`
`5
`
`the formed DDPA with a metal compound. For example, a dithiophosphoric acid
`may be madebyreacting mixtures of primary and secondary alcohols. Alternatively,
`multiple dithiophosphoric acids can be prepared where the hydrocarbyl groups on one
`
`are entirely secondary in character and the hydrocarbyl groups on the others are
`
`entirely primary in character. To make the metal salt, any basic or neutral metal
`
`compound could be used but the oxides, hydroxides and carbonates are most
`
`10
`
`generally employed. Commercial additives frequently contain an excess of metal due
`
`to the use of an excess of the basic metal compoundin the neutralization reaction.
`
`The preferred zinc dihydrocarby! dithiophosphates (ZDDP)are oil soluble salts
`
`of dihydrocarbyl dithiophosphoric acids and may be represented by the following
`
`15
`
`formula:
`
`S
`
`RONI
`
`P—s
`
`zn
`
`/
`R'O
`
`2
`
`
`
`
`wherein R and R’ maybe the sameor different hydrocarbyl radicals containing from
`
`1 to 18, preferably 2 to 12, carbon atoms and including radicals such as alkyl, alkenyl,
`
`aryl, arylalkyl, alkaryl and cycloaliphatic radicals. Particularly preferred as R and R’
`20~~groups are alkyl groups of 2 to 8 carbon atoms. Thus,the radicals may, for example,
`be ethyl, n-propyl, i-propyl, n-butyl, i-butyl, sec-butyl, amyl, n-hexyl, i-hexyl, n-octyl,
`
`decyl, dodecyl, octadecyl, 2-ethylhexyl, phenyl, butylphenyl, cyclohexyl,
`
`methylcyclopentyl, propenyl, butenyl. In order to obtain oil solubility; the total
`
`numberof carbon atoms(i.e. R and R’) in the dithiophosphoric acid will generally be
`
`25
`
`about 5 or greater. The zinc dihydrocarbyl dithiophosphate can therefore comprise
`
`zinc dialkyl dithiophosphates.
`
`Page 15 of 219
`
`Page 15 of 219
`
`
`
`-14-
`
`To limit the amount of phosphorusintroduced into the lubricating oil
`
`composition by ZDDPto no more than 0.1 wt. % (1000 ppm), the ZDDP should
`
`preferably be addedto the lubricating oil compositions in amounts no greater than
`
`from about1.1 to 1.3 wt. %, based upon the total weightof the lubricatingoil
`composition.
`
`Other additives, such as the following, may also be presentin lubricating oil
`
`compositions of the present invention.
`
`10
`
`20
`
`Ashless dispersants comprise an oil soluble polymeric hydrocarbon backbone
`
`having functional groups that are capable of associating with particles to be dispersed.
`
`Typically, the dispersants comprise amine, alcohol, amide, or ester polar moieties
`
`attached to the polymer backboneoften via a bridging group. The ashless dispersants
`
`may be, for example, selected from oil soluble salts, esters, amino-esters, amides, imides,
`
`and oxazolines of long chain hydrocarbon substituted mono and dicarboxylic acids or
`their anhydrides; thiocarboxylate derivatives of long chain hydrocarbons; long chain
`aliphatic hydrocarbons having a polyamineattached directly thereto; and Mannich
`
`condensation products formed by condensing a long chain substituted phenol with
`
`formaldehyde and a polyalkylene polyamine.
`
`Viscosity modifiers (VM) function to impart high and low temperature operability
`
`to a lubricating oil. The VM used may have that sole function, or may be
`
`multifunctional.
`
`Multifunctional viscosity modifiers that also function as dispersants are also
`
`known. Suitable viscosity modifiers are polyisobutylene, copolymers of ethylene and
`
`propylene and higher alpha-olefins, polymethacrylates, polyalkylmethacrylates,
`
`methacrylate copolymers, copolymers of an unsaturated dicarboxylic acid and a vinyl
`
`compound,inter polymers of styrene and acrylic esters, and partially hydrogenated
`
`30
`
`copolymers of styrene/ isoprene, styrene/butadienec, and isoprene/butadiene, as well as
`
`the partially hydrogenated homopolymers of butadiene and isoprene and
`
`isoprene/divinylbenzene.
`
`Page 16 of 219
`
`Page 16 of 219
`
`
`
`-15-
`
`Oxidation inhibitors or antioxidants reduce the tendencyof base stocks to
`deteriorate in service whichdeterioration can be evidenced by the products of oxidation
`suchas sludge and varnish-like deposits on the metal surfaces and by viscosity growth.
`Such oxidation inhibitors include hindered phenols, alkaline earth metal salts of
`alkylphenolthioesters having preferably Cs to C)2 alkyl side chains, calcium nonylphenol
`sulfide, ashless oil soluble phenates and sulfurized phenates, phosphosulfurized or
`sulfurized hydrocarbons, phosphorusesters, metal thiocarbamatesandoil soluble copper
`compoundsas described in U.S. 4,867,890.
`
`Rust inhibitors selected from the group consisting of nonionic polyoxyalkylene
`polyols andesters thereof, polyoxyalkylene phenols, and anionic alkyl sulfonic acids
`may be used.
`
`Copperand lead bearing corrosion inhibitors may be used, but are typically not
`required with the formulation ofthe present invention. Typically such compoundsare
`the thiadiazole polysulfides containing from 5 to 50 carbon atoms,their derivatives and
`
`polymers thereof. Derivatives of 1,3,4 thiadiazoles such as those described in U.S.
`
`Patent Nos. 2,719,125; 2,719,126; and 3,087,932;are typical. Other similar materials
`are described in U.S. Patent Nos. 3,821,236; 3,904,537; 4,097,387; 4,107,059;
`4,136,043; 4,188,299; and 4,193,882. Other additives are the thio and polythio
`sulfenamidesof thiadiazoles such as those described in U
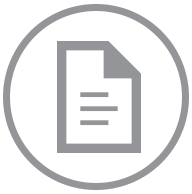
Accessing this document will incur an additional charge of $.
After purchase, you can access this document again without charge.
Accept $ ChargeStill Working On It
This document is taking longer than usual to download. This can happen if we need to contact the court directly to obtain the document and their servers are running slowly.
Give it another minute or two to complete, and then try the refresh button.
A few More Minutes ... Still Working
It can take up to 5 minutes for us to download a document if the court servers are running slowly.
Thank you for your continued patience.
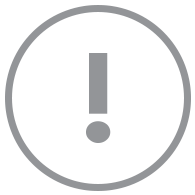
This document could not be displayed.
We could not find this document within its docket. Please go back to the docket page and check the link. If that does not work, go back to the docket and refresh it to pull the newest information.
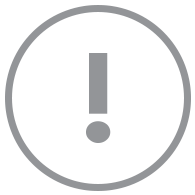
Your account does not support viewing this document.
You need a Paid Account to view this document. Click here to change your account type.
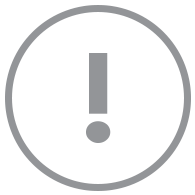
Your account does not support viewing this document.
Set your membership
status to view this document.
With a Docket Alarm membership, you'll
get a whole lot more, including:
- Up-to-date information for this case.
- Email alerts whenever there is an update.
- Full text search for other cases.
- Get email alerts whenever a new case matches your search.
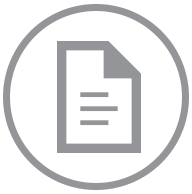
One Moment Please
The filing “” is large (MB) and is being downloaded.
Please refresh this page in a few minutes to see if the filing has been downloaded. The filing will also be emailed to you when the download completes.
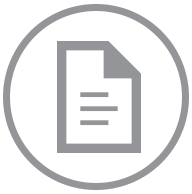
Your document is on its way!
If you do not receive the document in five minutes, contact support at support@docketalarm.com.
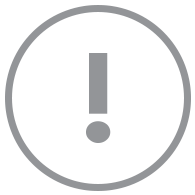
Sealed Document
We are unable to display this document, it may be under a court ordered seal.
If you have proper credentials to access the file, you may proceed directly to the court's system using your government issued username and password.
Access Government Site