`
`Page 1 of 9
`
`Samsung Exhibit 1005
`
`
`
`Vol. 132, No. 3 DIFFUSION-CONTROLLED PLASMA ETCHING 649 perature. Several investigators have reported models for diffusion-controlled plasma etching in barrel reactors (5, 6). With assumption of steady-state conditions, the ef- fect of process parameters on etch uniformity was studied. In the present work, transient removal of a film from a wafer stacked in a barrel plasma etcher is investigated. Transport and reaction phenomena are used to predict behavior and to identify dimensionless scale-up parame- ters. This study differs from past work in that transient behavior is included so that the duration of etch cycle (throughput) and of over-etch exposure may be investi- gated. While actual plasma systems are more complex, the following model provides a basic framework which may be expanded as additional refinements are added. Theoretical Formulation Let us for the moment concentrate on events happen- ing in the interwafer space, regarding the gas discharge outside the wafer stack as simply the source of etchant species. The plasma region is treated later. Figure 2, not drawn to scale, is a schematic representation of the radi- ally symmetric cell formed by two wafers facing each other. Prior to the onset of etching, a film of uniform thickness exists on the wafer surfaces. The rate of film removal depends on the concentration distribution in the interwafer gap. To an extent that depends upon operating conditions, the etch rate is highest on the periphery of the wafer. Film in this region thus clears first, and subse- quent film removal would then take place in more inac- cessible regions. Figure 2 illustrates the situation part way through the process, where film has been cleared en- tirely from the outer portion of the wafer, while the inner region is yet to clear. As etching proceeds, the concentra- tion distribution changes to conform to the reactivity dis- tribution along the wafer surface. While the film may eventually be removed everywhere, the peripheral re- gions would meanwhile be exposed to overetching condi- tions which, in many systems, adversely affect product quality. The following assumptions preserve the salient features of the system and also streamline the task of computa- tion. 1. The spacing between adjacent wafers is suffi- ciently smaller than the wafer radius so that significant concentration variations occur only in the radial direc- tion. 2. Convection is negligible with respect to diffusion ~ afer Film ~0 R r Fig. 2. Schematic of the radially symmetric region between two suc- cessive wafers. in the interwafer region owing to the large value of the diffusion coefficient. An order of magnitude calculation showed that, even if all the gas were flowing parallel to the wafer surfaces, the Pe number (=RouJD) would be less than 0.05. In practical systems, with the gas outlet at the back of the quartz barrel, most of the gas flow is nor- mal to the wafer surfaces. Thus, practical Pe numbers are even smaller. 3. The etching reaction is first order; this has been shown for photoresist stripping in oxygen (6) and Si etching in fluorine (7). 4. The etching reaction pro- ceeds to completion at or near the film surface (6) over a distance much smaller than the diffusion length of the etching species, and the reaction products do not affect the etching process (8). 5. The substrate is not etched. Hence the model is applicable to processes such as photo- resist stripping in an O2 plasma or Si etching in a CFJO2 plasma with SiO2 as the substrate. 6. The pressure re- mains constant during an etch cycle; this can be achieved by using a pressure feed-back control system. 7. Opera- tion is isothermal with no spatial variations of diffusivity or reaction rate constants. This assumption will not be valid in cases of highly exothermic etching reactions. For example, in etching Si at 0.5 ~m/min in a F containing plasma, the adiabatic temperature rise of a 10 cm diam 0.5 mm thick slice will be 1.3~ Furthermore, severe tem- perature variations will occur during start-up, unless a preheat-treatment with a N2 or Ar plasma is applied. 8. The concentration of etchant at the wafer edge remains constant during the etch cycle. However, if the etching re- action is the main loss mechanism for the etchant species, and the reaction rate distribution along the wafer surface is nonuniform, the etchant concentration at the wafer edge (Co) will change with time during a single etch cycle. This is because the amount of film remaining on the wa- fers will also change with time (loading effect). Such a change in Co could be predicted by Eq. [19] to be derived later. The calculations presented in this work did not ac- count for any changes in Co during an etch cycle (see also "Conclusions" section). 9. The concentration profiles ad- just rapidly to the gradual movement of the film front during depletion. Therefore, at any particular moment, the concentration distribution is at the steady-state distri- bution which corresponds to the reactivity conditions prevailing at that moment. This "pseudo-steady-state" ap- proximation is valid provided that the time scale over which film depletion occurs (equal to xhJk2co, see also ex- pression for z in Eq. [5]) is much greater than the "charac- teristic" diffusion time (Ro2/D). In other words, the follow- ing inequality should hold: XhoD/k2coRo 2 >> 1. For typical values of the parameters (Table I), this ratio is found to be greater than 103 . During etching, the thickness of etchable material left at a certain location and time will be given by _ [t k2 h(r,t) = ho J o --X c(r,t) dt [1] The concentration distribution c(r,t) varies with time during the etching process and is calculated by applica- tion of transport laws to the movement of etchant species. The remaining text in this section consists of three seg- ments: the general model, a limiting case valid in the ab- sence of recombination reactions, and a method for deter- mining the concentration of etching species at the edge of the wafer stack. General model.--Under the foregoing assumptions stated above, the conservation equation for the etching species is D 1 d (r dc~ 2k2 VoW ~-~ \ dr/ =--~c + 2klc2[A2]+~c with the boundary conditions c = Co at r = Ro dc -0atr=0 dr [2]
`
`Page 2 of 9
`
`
`
`650 J. Electrochem. Soc.: SOLID-STATE SCIENCE AND TECHNOLOGY March 1985 The left-hand side of Eq. [2] represents the radial diffu- sion of etchant into the region between the wafers, while the right-hand side (rhs) corresponds to the various reac- tions which occur. The first term on the rhs of Eq. [2] represents etching. Since only radial concentration gradi- ents are assumed to exist, the heterogeneous reaction rate k2c is transformed to a homogeneous rate term by multi- plication by the surface to volume ratio 2/L. Both surfaces have been assumed reactive, i.e., the wafers stand back to back during etching. When etching patterned films, this term has to be multiplied by the fraction of the surface occupied by etchable material. Note that ks = 0 for r > R, where the film no longer exists (Fig. 2). The second term on the rhs of Eq. [2] represents volume recombination re- actions of the active species of the form k, A + A + A2 ---> 2A~ [3] A2 is the parent molecule which gives A, the etching spe- cies, by electron-impact dissociation. A~ acts as a third body for recombination to occur. The presence of a third body is required to conserve momentum and energy dur- ing recombination. The reverse of reaction [3] proceeds at negligibly small rates at the low temperatures used in plasma etching [e.g., the equilibrium constant for the re- action F2 ~- 2F is ~- 10 -24 mol/cm 3 at 300 K (19)]. When the concentration of the etching products is low, [As] ~- P/RgT - [A] = P/RgT - c. The third term on the rhs of Eq. [2] ac- counts for wall recombination of the active species in re- actions of the form A + (A * wall) w A2 + wall [4] This term results by multiplying the random flux of etchant striking the wafer surfac e (1/4 VoC) by the surface to volume ratio (2/L) and by the wall recombination coefficient w, which is assumed constant throughout the wafer surface. The wall recombination reaction is first or- der since an impinging atom recombines with an atom al- ready adsorbed on the surface (9). Before proceeding further, it is convenient to rewrite the governing equations in terms of dimensionless quan- tities based on the following definitions r h ~- H=-- Ro ho [5] C k2c o C - co ~=~o t When the variables defined in Eq. [5] are introduced into Eq. [1] and [2], the following dimensionless equations arise with H = 1 - Cdr [6] d2C 1 dC --+ di 2 i d~ -- - 4%2C + aC 3 + tiC 2 + ~C [7] 2k,Ro2co 2 VoWRo 2 D 2LD [8] 2k,PRo2co 2k2 - (RgT)D ~b~ = R~ LD The dimensionless b ~undary conditions become C=lat{=l dC -0ate=0 dE Dimensionless number ~bo is comparable to the Thiele Modulus found in catalytic reactor design (17); ~bo repre- sents the relative importance of the kinetics of etching as compared to diffusion. If ~bo >> 1, for example, diffusion is the controlling step, and one may expect concentration gradients to develop in the interwafer space and the etch rate distribution to be nonuniform. Under such condi- tions, the outer edge of the wafer would be exposed to overetching, while the center is yet to clear. If Cbo << 1, the etching reaction is sluggish and the reaction rate distribu- tion is uniform all over the reacting surface. Dimensionless groupings ~ and /~ describe volume recombination vs. diffusion effects. For example, if fl >> 1, the reactive species recombine before they have any chance to diffuse and etch the wafer surface. Volume recombination reactions are strongly dependent on pres- sure. For instance, a and fi increase with the third power of pressure. Notice that since the partial pressure of the etching species is usually less than 10% of the reactor to- tal pressure, ]al ~< O.lfl. Finally, grouping ~ describes sur- face recombination vs. diffusion effects and is affected by both the surface to volume ratio and the wall recombina- tion coefficient. The latter depends critically on the na- ture and the condition of the surface. By solving Eq. [6] and [7], the effect of process parame- ters (Co, P, D, k's) and of geometric factors (L, Ro) on etch uniformity, overetch exposure, and total etch time can be determined. In particular, optimum conditions for high throughput can be identified. The above model extends previous studies by accounting for both volume and sur- face recombination reactions. In addition, the model in- cludes transient effects owing to the pseudo-steady-state clearing of the film. Note that Eq. [7] is general enough to handle more com- plex recombination reaction schemes. An example con- cerning an oxygen plasma is given in the Appendix. The solution to Eq. [6] and [7] was obtained in a step- wise manner. The wafer was divided in a number of con- centric rings of equal width. At each time step, the con- centration profile was found by linearizing Eq. [7] about a trial solution and casting the linearized equation into finite difference form by using the central difference ap- proximation. The resulting tridiagonal system was in- verted in a CDC Cyber 175. Calculations started about the trial solution obtained analytically when all reaction terms are assumed to be first order in concentration. After the true concentration profile was found, the time required to completely strip the outer ring was deter- mined, and a new film thickness distribution was com- puted by using Eq. [6]. A new concentration profile was then determined for which the wafer surface was reactive everywhere except for the ring already etched away. With the revised concentration distribution, the time necessary to completely strip the second ring was found. In a like manner, the time needed to strip each successive ring was calculated. The total etch time was the sum of the partial times. For each time step but the first, the solution found in the previous time step was used as the trial solution. No convergence problems were experienced for the values of the parameters used. Results did not differ ap- preciably by changing the number of rings from 150 to 200. Results were checked against the analytic solution for the limiting case of no recombination reactions dis- cussed below. Limiting case: no recombination reactions.--When recombination reactions can be neglected (k, = w = o), i.e., when the etchant has a long lifetime in the absence of etchable material, Eq. [2] can be simplified into the fol- lowing two equations 1 d (de) 2k2c [9] D--r--~r r--d-rr - L for 0 <- r <- R, i.e., for the region still occupied by the film, and dc r ~ = const. [10] for R ~< r ~< Ro, i.e., for the film-free region near the pe- riphery of the wafer.
`
`Page 3 of 9
`
`
`
`Vol. 132, No. 3 DIFFUSION-CONTROLLED PLASMA ETCHING 651 It is convenient to introduce the following dimension- less variables r c , 2k2 =~-,C=-- and~b 2=R* Co LD The film radius R (and not the wafer radius Ro) was used in these definitions so that, although R is changing, the value of $ is pinned at 1 for r = R. The dimensionless form of Eq. [9] is d2C 1 dC -- + - ~b2C [11] d~ 2 ~ d~ which is a Bessel equation. The boundary conditions are C = Caatr = 1 dC - 0 at $ = 0 [12] d$ The dimensionless form of Eq. [10] is dC --~ = const. with ~ = r/Ro as before in the general model. The perti- nent boundary conditions are C=latr R C=CRat~= ~oo =~ CR is eliminated by requiring the flux to be continuous at r = R. The final result for the concentration distribu- tion is Io(~) C = 0 ~< r ~< R [13] Io(~b) - ~bI,(~b) In r In R ~< r ~< Ro [14] Io(~b) - ~bll((b) In C=I+ where (x]2) 2n Io(X) = ~'~ ~=o (n!) ~ is the modified Bessel function of the first kind of order zero and ~ (x/2) 2~+1 I~(x) = nl(n + 1)I n=O is the modified Bessel function of the first kind of order one. Since R = R(t), Eq. [13] and [14] have a time depen- dence built into the equations. The overall etch rate at any given time is ~bIl((b) 21rRoLD "~r --- 2~rLDco r=Ro Io(~b) - 4~Ii(~b) In If the concentration of the etchant were Co throughout the wafer surface, the etch rate would be 2~Co(TrR 2) Thus, the "effectiveness factor" v is d-~-r ,-~Ro = 2Ii(~b) 27rRoLD ~? - 2k~co~rR 2 ~b[Io(~b) - ~bI~(~b) In (r] [15] The effectiveness factor is an expression of the actual overall reaction rate as compared to the reaction rate that would be obtained if the concentration were at the bulk value throughout the reacting surface (17). A more gen- eral expression for the effectiveness factor is 2 f:re(c)dr n = [16] R2e(Co) When the reaction rate is first order in concentration, e = k2c, Eq. [16] becomes f2 2 rc dr = R~co - 2 fo $Cd~ [17] The effectiveness factor concept is used below for the prediction of the etchant concentration in the plasma space surrounding the wafer rack. The analysis up to this point has concentrated on events occurring in between the wafers. A similar analy- sis can be applied to LPCVD processes. The recent work by Meyerson and Olbricht (24) is quite relevant. Up to this point, the plasma existing outside the wafer stack has been regarded as simply the source of etchant species. The only parameter, related to the plasma region, that is required for the solution of Eq. [6] and [7] is the etchant concentration at the edge of the wafer stack, co. This quantity depends on a complex way on reactor geometry and operating parameters such as power, pressure, flow rate, etc. Prediction of co would be less difficult for "clean" systems involving a single gas. An example of such a system is photoresist stripping in an O2 plasma. The procedures for evaluating Co are given below. Etchant concentration in the plasma.--The bulk etchant concentration (Co) can be predicted by writing a conserva- tion equation for the etchant species (10, 20). These spe- cies are generated by electron-impact dissociation of the parent molecules and are eliminated by recombination re- actions (Eq. [3] and [4]), etching, and gas flow. Rapid backmixing tends to eliminate concentration gradients in the annular region outside the wafer rack where the plasma exists, particularly when the gas is symmetrically fed through manifolds parallel to the barrel axis. A con- servative order of magnitude calculation gave a value for the Pe number less than 0.1. Thus, complete mixing can be assumed in that region (continuous stirred tank reac- tor model, CSTR). The species balance equation will then read 2ke <he> [A2] V, = ~k2Co(N~rR 2) VoW + T Spco + 2klco 2 [A2] Vp + Fco [18] The term on the left-hand side of Eq. [18] represents pro- duction of etchant species via the reaction ~e A2+e--* 2A+e The electron density has been assumed constant at the average value within the annular plasma space. This may be a good approximation if the thickness of the annular space is small compared to its length. Thus, the assump- tion is better if an etch tunnel is present. In addition, if the principal loss of electrons is a volume process (e.g., at- tachment), the electron density will tend to be uniform irrespective of the geometry. The first term on the right-hand side of Eq. [18] repre- sents loss of etchant in the etching reaction. This term de- pends on the number of wafers (N) and on the area of etchable material left on each wafer (qrR2). The last term in Eq. [18] represents etchant loss by flow. Under the as- sumption that the gas is essentially composed of A2 and A (i.e., low loading of wafers), [A2] --- P/RgT - co. Then, Eq. [18] gives P -- Co 3 9- ~ Co 2 ~Tk~IrR2N v, + vow F --+-~a +--~p +2ke<ne> 2k~ Co k e <ne> P 0 [19] k~(RgT)
`
`Page 4 of 9
`
`
`
`652 J. Electrochem. Sac.: SOLID-STATE SCIENCE AND TECHNOLOGY March 1985 The solution to the cubic Eq. [19] provides co. Note that since both R and ~? are functions of time, Co will be time dependent except in the case ~k.~rR2N/Vp < < vow/4a or F/Vp or 2ke <he>. Neglecting the volume recombination reaction (ki ~ o) results 2ke<ne> (~-~-~) co = [20] vk21rR2N vow F V~ + ~ + ~ + 2ke <ne> This equation correctly predicts the loading effect in that a plot of l/co vs. N results in a straight line (10). Both the average electron density <ne> and the dissoci- ation reaction rate constant ke depend on pressure. In par- ticular, ke depends on the EJP ratio which is a unique function of the electron temperature. In general, determi- nation of <ne> or ke is an extremely difficult task. The presence of "hot" electrons, the multiplicity of the reac- tion channels, and the large number of chemical species involved make the problem of analyzing a gas discharge a very complicated one. The papers by Kushner (21, 22) il- lustrate the complexity of the problem. A rigorous analy- sis of the discharge requires knowledge of cross-sectional data for the various collisional processes occurring. Such data are scarce for mostof the plasmas used in practice. However, the situation is less complicated when dealing with discharges of a single gas. For the 02 discharge, in particular, the required physical data are available and a reasonably accurate analysis of an 02 plasma can be real- ized. For such a discharge, the effective electric field-to- pressure ratio EJP as well as the average electron density <n~> can be evaluated for given pressure, power density, and reactor geometry from Fig. 1.19 of Ref. (11). After finding the EJP ratio, k~ can be obtained from Fig. 1.26 of the same reference. Then co can be computed by using Eq. [20] or the more complicated Eq. [19], if necessary. Hence, the effect of reactor pressure and power input on the bulk etchant concentration can be evaluated for this particular discharge. The plots in Fig. 1.19 and 1.26 of Ref. (11) can be used for analyzing etching in an O2 plasma as long as the byproducts of etching (CO2, CO, H20, etc.) are in low enough concentrations not to alter the discharge properties. Measurement of <n~> is usually done with Langmuir probes and is associated with certain experi- mental difficulties (23). The etchant concentration can be measured by optical emission spectroscopy (12) or by gas- phase titration (13, 14). Results and Discussion The foregoing model was employed to predict across- wafer uniformity, etch cycle duration, optimum through- put, and overetch exposure. Consider first the situation where recombination reac- tions are negligible, and where steady-state concentration profiles have become established but film clearing has not yet begun. Such a situation corresponds to the simple limiting case described by Eq. [13] with (r = 1. Figure 3 il- lustrates how the concentration distribution in the inter- wafer region depends upon the Thiele Modulus (~bo). For values of ~bo less than 0.3, the concentration distribution (and thus the etching rate distribution) is nearly uniform. That is, the wafer-surface is uniformly accessible to the etchant species. For a given wafer diameter and reactor pressure, small ~bo values can be achieved by increasing the wafer spacing, although such action serves also to de- crease the throughput. For high Cbo values, diffusion is sluggish compared to the etching reaction so that etching species become depleted from the interwafer region and large radial concentration gradients build up. This will be the case when the wafer spacing is small, or the diffu- sivity is low (i.e., pressure is high), or the etching reaction is rapid. A plot of the effectiveness factor ~ vs. the Thiele Modu- lus ~bo (Eq. [15]) for two values of the dimensionless film radius c~(= R/Ro) is shown in Fig. 4. When ~b = ~bo ~ << 1 (i.e., r < 0.t), Eq. [15] reduces to 1,0 0.l = 0.8-- ,-, 0.6 o o = o,4 U 0.2 o~., I 0.2 0.4 0,6 0.8 1,0 Radial Position, Fig. 3. Effect of Thiele Modulus (ha on the concentration distribu- tion in the interwofer region prior to film depletion (o- = 1, ~z =/3 = ~/= 0). 4 ~} = [21] 4 + ~bo~2(1-2 In c~) For any value of (r, the effectiveness factor tends to unity for small values of the Thiele Modulus $o- This agrees with the fact that for small ~o the concentration is at its bulk value (co) throughout the wafer surface (e.g., Fig. 3 with 4,0 = 0.1). When ~ >> 1 (i.e., ~b > 10), Eq. [15] reduces to 2 ,} - [22] ~bo~(1-~o (r In o-) Before film depletion sets in, R = Ro or ~ = 1. Then Eq. [22] becomes 2 ,7 = -- [23] ~o and a log-log plot of ~? vs. ~bo will result in a straight line with a slope of -i. (Fig. 4 for ~ = i.) For any film radius R less than the wafer radius Ro, ((r < i), and for high enough values of the Thiele Modulus ~bo so that -~boC~ In ~ >> 1, Eq. [22] becomes 2 [24] ~bo2~ 2 In cr and a log-lot plot of ,} vs. ~o will result in a straight line with slope of -2. (Fig. 4 for (r = 0.2.) Figure 5 depicts the concentration distribution in the interwafer space for several values of, in essence, the vol- 1.0 = ....... 02 _~ 0.5- 0,3-- 4J = 0,2- g W o... , ,,,,1 , , b3 , 0,5 0.7 ~ 2 3 5 7 I0 20 30 Thiele Modulus, ~0 Fig. 4. Effectiveness factor T/as a function of the Thiele Modulus r with the dimensionless film radius ~ as a parameter (Eq. [15]).
`
`Page 5 of 9
`
`
`
`Vol. 132, No. 3 DIFFUSION-CONTROLLED PLASMA ETCHING 653 0 0,6 u 0,4 (~ o 0 I I0 0,8- (~) -0,1 I I I0 i (~ -I I0 I I0 (~ -I0 I00 I I0 ; -- (E) -I00 I000 I I0 0.2 -0 0,2 0,4 0,6 0,8 1,0 Radial Position, Fig. 5. Effect of volume recombination reactions on the concentra- tion distribution in the interwafer space prior to film depletion (~ = 1). hO 0.8 0,6 8 0.4 0.2 I I I I o I I I I 0.2 0.4 0,6 0,8 1,0 Radial Position, (~ Fig. 7. Concentration distribution in the interwufer space at differ- ent cumulative etch times 7 (parameter values are the some as in Fig. 6). ume recombination reaction rate constant k,. As kl in- creases so that ]a ! >> 1 and fl >> 1, strong concentration gradients develop which result in a highly nonuniform etch rate and a longer etch time. That is, reactants recom- bine to inactive species before they can diffuse into the wafer stack and etch the film. However, if k, is low enough so that fl < 1, volume recombination reactions can be completely neglected (compare cases (j) and (~ in Fig. 5). This is true for the commonly employed O~ or/and CF4 discharges at pressures less than 1 torr. However, it may not be true for C12 discharges, where the volume recombination rates are faster. Figure 6 shows the film thickness distribution during transient film clearing with the dimensionless time as a parameter. Initially, the film has a uniform thickness ha (H = 1). After a dimensionless time of 1, the film begins to recede from the periphery. For this particular example, the film will be completely cleared after a dimensionless time of 10.1 has elapsed. The intersects with the ordinate provide the film radius R as a function of time. Figure 7 shows the time dependence of the concentra- tion profile during transient clearing of the film. After the outer rings have been cleared, the reactant penetrates more readily to the inner portion of the'wafer and thus the concentration increases with time at a given radial po- sition. This increase is less pronounced close to the center of the wafer since this region stays reactive almost throughout the cycle, Figure 6 gives the film thickness distribution as a function of time under the same condi- tions. l,O. L ' ' l ~ , 0.6 ~. 0,4 (cid:12)9 - _E =7.9 oi % ",, \, \, \ 0 0,2 0,4 0.6 0,8 I.O Radial Position, Fig. 6. Film thickness distribution at different cumulative etch times (~ = -], fl = 10, T = O, ~o2 = 25 end total etch time T O = IO.]). Exposure to overetch is to be avoided in etching most patterned films since local loading can result in rapid mask undercut after the end point has been reached. The percent overetch exposure as a function of the Thiele Modulus 6o is shown in Fig. 8 for four different radial po- sitions on the wafer surface ~ (=r/Ro). In constructing Fig. 8, only surface (not volume) recombination reactions have been included (a = fl = 0, T = 1). The percent overetch was computed by % overetch To -- = ~ x 100 T where r is the total etch time (shown in the insert Table in Fig. 8), and ~ is the time required to clear the film up to a given radial position ~. Since the portion of the wafer closer to the periphery clears first, the overetch exposure is higher for larger { values. Furthermore, as the Thiele Modulus .6o increases, the radial distribution of the reac- tion rate becomes nonuniform, resulting in an increase of the overetch exposure. A related plot is shown in Fig. 9, where the total etch time % has been plotted against the Thiele Modulus 4~o Table I. Typical parameter values for barrel plasma etchers Parameter value Comments [A2] = 6 x 10 -8 mol/cm a co = 6 x 10 -8 mo]/cm 3 D ~ 350 cm2/s ha = 10 -4 cm (1/zm) k, = 101~cmS/(mol)2/s k2 = 50 cm]s Lr = lcm P~ = 1 torr Q = 100 sccm Ro = 5 cm T = 400 K Vo = 7
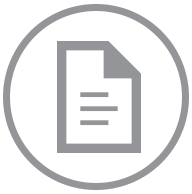
Accessing this document will incur an additional charge of $.
After purchase, you can access this document again without charge.
Accept $ ChargeStill Working On It
This document is taking longer than usual to download. This can happen if we need to contact the court directly to obtain the document and their servers are running slowly.
Give it another minute or two to complete, and then try the refresh button.
A few More Minutes ... Still Working
It can take up to 5 minutes for us to download a document if the court servers are running slowly.
Thank you for your continued patience.
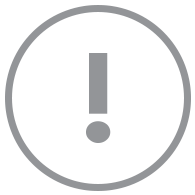
This document could not be displayed.
We could not find this document within its docket. Please go back to the docket page and check the link. If that does not work, go back to the docket and refresh it to pull the newest information.
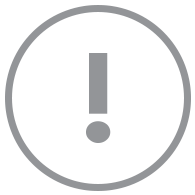
Your account does not support viewing this document.
You need a Paid Account to view this document. Click here to change your account type.
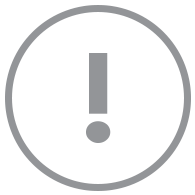
Your account does not support viewing this document.
Set your membership
status to view this document.
With a Docket Alarm membership, you'll
get a whole lot more, including:
- Up-to-date information for this case.
- Email alerts whenever there is an update.
- Full text search for other cases.
- Get email alerts whenever a new case matches your search.
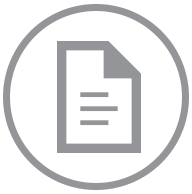
One Moment Please
The filing “” is large (MB) and is being downloaded.
Please refresh this page in a few minutes to see if the filing has been downloaded. The filing will also be emailed to you when the download completes.
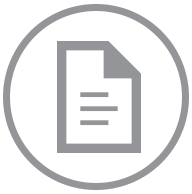
Your document is on its way!
If you do not receive the document in five minutes, contact support at support@docketalarm.com.
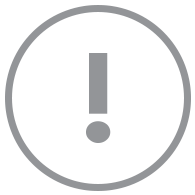
Sealed Document
We are unable to display this document, it may be under a court ordered seal.
If you have proper credentials to access the file, you may proceed directly to the court's system using your government issued username and password.
Access Government Site