`(12) Patent Application Publication (10) Pub. No.: US 2006/0264756 A1
`(43) Pub. Date:
`NOV. 23, 2006
`Lo et al.
`
`US 20060264756A1
`
`(54) ULTRASONIC MONITOR WITH A
`BIOCOMPATIBLE OIL BASED
`TRANSMISSION MEDIUM
`
`(76) Inventors: Thomas Ying-Ching Lo, Fremont, CA
`(US); Rong Jong Chang, Fremont, CA
`(Us)
`Correspondence Address:
`VIERRA MAGEN MARCUS & DENIRO LLP
`575 MARKET STREET SUITE 2500
`SAN FRANCISCO, CA 94105 (US)
`
`(21) Appl. No.:
`
`11/124,707
`
`(22) Filed:
`
`May 9, 2005
`
`Publication Classi?cation
`
`(51) Int. Cl.
`A61B 8/14
`
`(2006.01)
`
`(52) US. Cl. ............................................................ .. 600/459
`
`(57)
`
`ABSTRACT
`
`An ultrasonic monitor implemented on a PCB includes a
`transmission medium. The transmission medium may be
`biocompatible and implemented as an oil-based transmis
`sion medium, a gel pad, or a combination thereof. Ultrasonic
`signals are transmitted between the ultrasonic monitor and a
`living subject through the transmission medium. An air gap
`is formed in the PCB underneath transducer elements to
`provide for more ef?cient signal transmission. The entire
`ultrasonic monitor may be encapsulated in plastic, a trans
`mission medium, or both to provide Water resistant proper
`ties.
`
`20
`
`IN L O
`
`1 of 30
`
`FITBIT EXHIBIT 1003
`
`
`
`Patent Application Publication Nov. 23, 2006 Sheet 1 0f 16
`
`US 2006/0264756 A1
`
`10
`
`Figure 1 - Prior Art
`
`2 of 30
`
`
`
`Patent Application Publication Nov. 23, 2006 Sheet 2 0f 16
`
`US 2006/0264756 A1
`
`20
`
`3 of 30
`
`
`
`Patent Application Publication Nov. 23, 2006 Sheet 3 0f 16
`
`US 2006/0264756 A1
`
`300
`
`Remote Display
`&
`
`T
`
`Wireless
`_
`—> Transmitter '’ Recelver
`£2
`
`l
`
`l
`
`T1 4
`T2
`m 29
`
`Mirco
`
`Controller
`
`-_-——————> Local Display
`i
`@
`
`Band Pass
`Filter
`
`LQ
`
`——> RF Ampli?er
`
`m
`
`Audio
`> Mixer —> Frequency
`Ampli?er
`E
`
`350
`
`Figure 3
`
`4 of 30
`
`
`
`Patent Application Publication Nov. 23, 2006 Sheet 4 0f 16
`
`US 2006/0264756 A1
`
`@
`
`Transmit Ultrasonic Signal
`
`?g
`
`l
`
`Receive Re?ected Signal
`
`Q
`
`l
`
`Amplifv Received Signal m
`
`l
`
`Retrieve Modulated Signal m
`
`V
`
`Amplify DeModulated Signal @
`
`l
`
`Filter Demodulated Signal
`
`_@_Q
`
`l
`
`Perform Additional Processing m
`
`Figure 4
`
`5 of 30
`
`
`
`Patent Application Publication Nov. 23, 2006 Sheet 5 0f 16
`
`US 2006/0264756 A1
`
`Q
`
`Convert Analog to Digital
`
`w
`
`i
`
`Determine Absolute Value @
`
`i
`
`Filter with LPF
`
`m
`
`i
`
`Derive Heart Rate Information
`
`_54_O
`
`Figure 5
`
`6 of 30
`
`
`
`Patent Application Publication Nov. 23, 2006 Sheet 6 0f 16
`
`US 2006/0264756 A1
`
`7 of 30
`
`
`
`Patent Application Publication Nov. 23, 2006 Sheet 7 0f 16
`
`US 2006/0264756 A1
`
`8 of 30
`
`
`
`Patent Application Publication Nov. 23, 2006 Sheet 8 0f 16
`
`US 2006/0264756 A1
`
`80
`
`9 of 30
`
`
`
`Patent Application Publication Nov. 23, 2006 Sheet 9 0f 16
`
`US 2006/0264756 A1
`
`Figure 9A
`
`Figure 9B ?x .'r\
`
`\\
`
`II/IXI/I
`
`Figure 90
`
`940 910
`922 m 92
`942 T
`-|— — —
`\l
`1 /
`F
`
`I
`
`I
`
`\
`
`10 of 30
`
`
`
`Patent Application Publication Nov. 23, 2006 Sheet 10 0f 16
`
`US 2006/0264756 A1
`
`1000
`
`.__1020
`
`T Y
`
`1 030
`
`'//////////////,9
`—_+
`X
`
`Figure 10A
`
`11 of 30
`
`
`
`Patent Application Publication Nov. 23, 2006 Sheet 11 0f 16
`
`US 2006/0264756 A1
`
`1060
`
`Figure 108
`
`12 of 30
`
`
`
`Patent Application Publication Nov. 23, 2006 Sheet 12 0f 16
`
`US 2006/0264756 A1
`
`1180
`
`\ 1182
`
`1184
`
`-——-1186
`
`Figure 11A
`
`1190
`
`/11s4
`
`i )'—1182
`
`=( __
`
`Figure 118
`
`13 of 30
`
`
`
`Patent Application Publication Nov. 23, 2006 Sheet 13 0f 16
`
`US 2006/0264756 A1
`
`Fi ure 12A
`
`5
`
`0
`
`Fi ure 128
`
`C 2 1 e r u H
`
`14 of 30
`
`
`
`Patent Application Publication Nov. 23, 2006 Sheet 14 0f 16
`
`US 2006/0264756 A1
`
`Figure 138
`
`15 of 30
`
`
`
`Patent Application Publication Nov. 23, 2006 Sheet 15 0f 16
`
`US 2006/0264756 A1
`
`1424
`
`14 2
`
`14 0
`
`1 1o
`
`— — — — ' — —
`
`LE1 1;" LE1 H w -
`
`/ i _
`\1414
`Flgure 14A
`
`1456
`
`1454
`
`1430
`
`/14 8
`l
`——_“___——_/142
`1440\:—L _ 1‘—[ .__.._ _L‘—:\1 50
`LCDJ U ,lEDJ ‘—* w
`
`Mir/J
`Figure 148
`
`\1_44__4
`
`146
`
`14 o
`
`14 0
`
`16 of 30
`
`
`
`Patent Application Publication Nov. 23, 2006 Sheet 16 0f 16
`
`US 2006/0264756 A1
`
`1530
`
`1 00
`—
`
`w
`
`Figure 15A
`
`M E
`
`1570
`
`Figure 158
`
`17 of 30
`
`
`
`US 2006/0264756 A1
`
`Nov. 23, 2006
`
`ULTRASONIC MONITOR WITH A
`BIOCOMPATIBLE OIL BASED TRANSMISSION
`MEDIUM
`
`CROSS REFERENCE TO RELATED
`INVENTION
`
`[0001] The instant non-provisional application is related
`to the following patent applications, all of Which are hereby
`incorporated by reference in their entirety:
`
`[0002] US. Pat. No. 6,843,771, ?led on Jan. 15, 2003,
`entitled “ULTRASONIC MONITOR FOR MEASURING
`HEART RATE and BLOOD FLOW RATE,” having inven
`tors Thomas Ying-Ching Lo, Tolentino Escorcio, Rong Jong
`Chang;
`[0003] US. patent application Ser. No. 10/990,794, ?led
`on Nov. 17, 2004, entitled “ULTRASONIC MONITOR
`FOR MEASURING BLOOD FLOW AND PULSE
`RATES”, having inventor Thomas Ying-Ching Lo, attorney
`docket number SALU-0l002USO; and
`[0004] US. patent application Ser. No. l0/99l,ll5, ?led
`on Nov. 17, 2004, entitled “GEL PAD FOR USE WITH AN
`ULTRASONIC MONITOR”, having inventors Thomas
`Ying-Ching Lo, Rong Jong Chang, attorney docket number
`SALU-0l002USO.
`
`BACKGROUND OF THE INVENTION
`
`[0005] 1. Field of the Invention
`
`[0006] The present invention relates to ultrasonic monitors
`for measuring heart rates and pulse rates in living subjects.
`
`[0007] 2. Description of the Related Art
`[0008] Measuring heart and pulse rates in living subjects
`has become a valuable tool during physical exercise and for
`health monitoring. The heart rate and pulse rate of a subject
`are related. Heart rate may be de?ned as the number of heart
`contractions over a speci?c time period, usually de?ned in
`beats per minute. A pulse is de?ned as the rhythmical
`dilation of a vessel produced by the increased volume of
`blood forced through the vessel by the contraction of the
`heart. Since heart contractions normally produce a volume
`of blood that can be measured as a pulse, heart rate and pulse
`rate are ideally the same. HoWever, a pulse rate may differ
`from the heart rate during irregular heart beats or premature
`heart beats. In this case, a heart contraction may not force
`enough blood through a blood vessel to be measured as a
`pulse.
`[0009] A pulse rate is measured by counting the rate of
`pulsation of a subject’s artery. The heart rate is measured by
`sensing the electrical activity of the heart based on electro
`cardiograms (for example EKG or ECG). Individuals Who
`Want to increase their endurance or performance may Wish
`to exercise While maintaining target heart rates. Conversely,
`subjects With a history of heart disease or other heart related
`condition should avoid exceeding a certain heart or pulse
`rate to reduce unnecessary strain on their heart.
`[0010] Most subjects that require continuous heart rate
`readings choose a monitor that requires a chest strap.
`Though they provide heart rates continuously, chest straps
`are cumbersome and generally undesirable to Wear. In
`addition to chest strap solutions, portable patient monitors
`
`(e.g., vital signs monitors, fetal monitors) can perform
`measuring functions on subjects such as arrhythmia analy
`sis, drug dose calculation, ECG Waveforms cascades, and
`others. HoWever, such monitors are usually fairly large and
`are attached to the subject through uncomfortable Wires.
`
`[0011] Pulse rate can be measured at the Wrist. The shal
`loW depth of the radial artery in the Wrist offers a number of
`advantages for achieving continuous pulse detection at the
`Wrist. Prior sensors that monitor pressure pulses in the Wrist
`have not been effective. Pressure pulses are attenuated by the
`tissues betWeen the artery and the sensor. Most of the high
`frequency signal components are lost because of the attenu
`ation. Additionally, muscle movement may create substan
`tial noise at the pressure sensors. The loW frequency noise
`signals make it very di?icult to reliably identify loW fre
`quency blood pressure pulses.
`
`[0012] Ultrasonic monitors using sonar technology Were
`developed to overcome noise signal problems. Ultrasonic
`monitors transmit ultrasonic energy as a pulse signal. When
`a poWer source drives a transducer element, such as a
`pieZoelectric crystal, to generate the pulse signal, the ultra
`sonic pulse signal is generated in all directions, including the
`direction of the object to be measured such as a blood vessel.
`The portion of the ultrasonic pulse signal reaching the vessel
`is then re?ected by the vessel. When the blood vessel
`experiences movement, such as an expansion due to blood
`?oW from a heart contraction, the re?ected pulse signal
`experiences a frequency shift, also knoWn as the Doppler
`shift.
`
`[0013] When either the source of an ultrasonic signal or
`the observer of the sonar signal is in motion, an apparent
`shift in frequency Will result. This is knoWn as the Doppler
`effect. If R is the distance from the ultrasonic monitor to the
`blood vessel, the total number of Wavelengths 7» contained in
`the tWo-Way path betWeen the ultrasonic monitor and the
`target is 2RD». The distance R and the wavelength 7» are
`assumed to be measured in the same units. Since one
`Wavelength corresponds to an angular excursion of 2st
`radians, the total angular excursion 4) made by the ultrasound
`Wave during its transit to and from the blood vessel is 4J'cR/7t
`radians. When the blood vessel experiences movement, R
`and the phase 4) are continually changing. A change in q) With
`respect to time is equal to a frequency. This is the Doppler
`angular frequency Wd, given by
`
`Where f‘,1 is the Doppler frequency shift and VI is the relative
`(or radial) velocity of target With respect to the ultrasonic
`monitor.
`
`[0014] The amount of the frequency shift is thus related to
`the speed of the moving object from Which the signal
`re?ects. Thus, for heart rate monitor applications, the ?oW
`rate or ?oW velocity of blood through a blood vessel is
`related to the amount of Doppler shift in the re?ected signal.
`
`[0015] A pieZoelectric crystal may be used both as the
`poWer generator and the signal detector. In this case, the
`ultrasonic energy is emitted in a pulsed mode. The re?ected
`signal is then received by the same crystal after the output
`
`18 of 30
`
`
`
`US 2006/0264756 A1
`
`Nov. 23, 2006
`
`power source is turned off. The time required to receive the
`re?ected signal depends upon the distance betWeen the
`source and the object. Using a single crystal to measure heart
`rates requires high speed poWer sWitching due to the short
`distance betWeen source and object. In addition, muscle
`movement generates re?ections that compromise the signal
`to-noise-ratio in the system. The muscle movement noise
`has a frequency range similar to the frequency shift detected
`from blood vessel Wall motion. Therefore, it is very di?icult
`to determine heart rates With this method. The advantage of
`this approach, hoWever, is loW cost and loW poWer con
`sumption.
`[0016] In some ultrasonic signal systems, tWo pieZoelec
`tric elements are used to continuously measure a pulse. The
`tWo elements can be positioned on a base plate at an angle
`to the direction of the blood. In continuous pulse rate
`measurement, the Doppler shift due to blood ?oW has a
`higher frequency than the shifts due to muscle artifacts or
`tissue movement. Therefore, even if the muscle motion
`induced signals have larger amplitudes, they can be removed
`by a high pass ?lter to retain the higher frequency blood ?oW
`signals. The disadvantages of continuous mode over pulsed
`mode are higher cost and more poWer consumption
`
`[0017] Several Wrist mounted ultrasonic monitor devices
`are knoWn in the art. HoWever, ultrasonic signals are prone
`to diffraction and attenuation at the interface of tWo media
`of different densities. Thus, air in the media or betWeen the
`monitor and the subject’s skin make ultrasonic energy
`transmission unreliable. Prior ultrasonic monitors require
`applying Water or an aqueous gel betWeen the transducer
`module and the living subject to eliminate any air gap.
`Because Water and aqueous gels both evaporate quickly in
`open air, they are not practical solutions.
`
`[0018] US. Pat. No. 6,843,771 disclosed the use of ther
`moplastic and thermoset gels as the transmission medium
`for ultrasonic signals to overcome the problems associated
`With Water and aqueous gel solutions. In US. Pat. No.
`6,716,169, Muramatsu et al. disclosed a soft contact layer
`based on silicone gel, a type ofthermoset gel, as the medium
`for the ultrasonic signal transmission. These gels mainly
`consist of a large quantity of non-evaporating (at ambient
`condition) liquid diluents entrapped in a lightly cross-linked
`elastomeric netWork. These cross-linked netWorks can be
`either physical in nature, such as in the thermoplastic gels,
`or chemical in nature, such as the thermoset gels.
`[0019] Synthetic thermoset and thermoplastic gels have
`disadvantages. The liquid diluents, though entrapped in the
`elastomeric netWork, can still diffuse into the skin of a user
`upon contact over a period of time. Since silicone gels use
`silicone oil as diluents, diffusion of silicone oil is an impor
`tant health concern, Diffusion of these oils into body tissues
`can cause biological problems. Synthetic thermoset and
`thermoplastic gels also tend to be soft gels. Though a softer
`gel alloWs better contact With the skin and results in better
`ultrasonic transmission, soft gels are Weak, di?icult to
`handle and di?icult to attach to ultrasonic transmitters.
`
`[0020] E?iciency of the transmitting transducer is an
`important feature in Wrist Worn and other small heart rate
`monitors. Transmission of an ultrasonic signal by a trans
`mitting transducer can be made more e?icient by use of a
`re?ector. Transmission signals generated aWay from target
`can be re?ected using a re?ector on one or more sides of the
`
`transducer. Some heart rate monitors include a foam sub
`stance having air voids underneath the pieZoelectric crystals.
`As illustrated in FIG. 1, a foam layer 120 may be placed
`Within ultrasonic module 110 underneath transducers 130
`and 140. The foam material air voids partially inhibit
`ultrasound energy penetration and provide fairly e?fective
`re?ection of ultrasound signals. With this foam backing,
`some of the ultrasonic signals directed toWards the foam are
`re?ected toWard the desired direction. The disadvantage to
`incorporating foam layers is that they are manually installed
`during manufacture. Other prior systems increase e?iciency
`by separating the tWo pieZoelectric crystals by a channel on
`a base plate. This reduces crosstalk betWeen the transducers
`to some degree but does not eliminate the loading or
`dampening effect caused by the base plate.
`
`[0021] Heart rate monitors that provide continuous heart
`rate readings through a transmission media are useful. The
`transmission media should be biocompatible and not dry out
`during the monitoring, leave an uncomfortable Wet ?lm, or
`be di?icult to generate and apply.
`
`SUMMARY OF THE INVENTION
`
`[0022] The present invention, roughly described, pertains
`to ultrasonic monitors. The ultrasonic monitor uses ultra
`sonic signals to measure movement inside the body of a
`living subject. The movement may be a heart contraction,
`?oWing blood or movement of the blood vessel itself. From
`information collected from these movements, electronics
`Within the monitor may determine blood ?oW rate, heart
`rate, or pulse rate of the living subject.
`
`[0023] In some embodiments, a biocompatible oil-based
`transmission medium is used to transmit ultrasonic signals
`betWeen an ultrasonic monitor module and a subject. The
`biocompatible oil-based transmission medium is positioned
`in contact With the ultrasonic monitor module and the
`subject, and provides transmission of ultrasonic signals
`betWeen the ultrasonic monitor module and the subject.
`
`[0024] In some embodiments, an ultrasonic monitor may
`include a transmission transducer, a receiving transducer, a
`housing and biocompatible oil-based transmission medium.
`The transmission transducer can be con?gured to transmit an
`ultrasonic signal and the receiving transducer can be con
`?gured to receive a re?ected ultrasonic signal. The housing
`may contain the transmission transducer and the receiving
`transducer. The biocompatible oil-based transmission
`medium is in contact With the housing. The ultrasonic signal
`and re?ected ultrasonic signal are transmitted through the
`biocompatible oil-based transmission medium betWeen the
`transducers and a subject.
`
`[0025] A heart rate may be monitored by applying a
`biocompatible oil-based transmission medium betWeen an
`ultrasonic monitor module and a subject. The ultrasonic
`monitor module transmits an ultrasonic signal through the
`biocompatible oil-based transmission medium to the subject.
`A re?ected ultrasonic signal is received by the ultrasonic
`monitor module through the biocompatible oil-based trans
`mission medium from the subject. The received ultrasonic
`signal is then processed.
`
`[0026] In some embodiments, a monitor system may
`include an ultrasonic monitor and an oil-based transmission
`medium. The ultrasonic monitor may be positioned in prox
`
`19 of 30
`
`
`
`US 2006/0264756 A1
`
`Nov. 23, 2006
`
`imity to a subj ect’s blood vessel. The oil-based transmission
`medium may be positioned between the ultrasonic monitor
`and the subject’s blood vessel. The oil-based transmission
`medium may comprise a Wax component and an oil com
`ponent and be able to transmit ultrasonic signals betWeen the
`ultrasonic monitor and the subject When positioned betWeen
`the ultrasonic monitor and the subject.
`
`[0027] In some embodiments, an ultrasonic monitor may
`include an ultrasonic monitor module, a gel pad, and a
`biocompatible oil based transmission medium. The gel pad
`may be in contact With the ultrasonic monitor module. The
`biocompatible oil based transmission medium may be in
`contact With the gel pad and a subject. The gel pad and
`biocompatible oil based transmission medium may provide
`transmission of ultrasonic signals betWeen the ultrasonic
`monitor module and the subject.
`
`BRIEF DESCRIPTION OF THE DRAWINGS
`
`[0028] FIG. 1 illustrates a cross section of an ultrasonic
`monitor of the prior art.
`
`[0029] FIG. 2A illustrates one embodiment of an ultra
`sonic monitor With a physical connection to a display device.
`
`[0030] FIG. 2B illustrates one embodiment of an ultra
`sonic monitor With a Wireless connection to a display device.
`
`[0031] FIG. 3 illustrates one embodiment of a block
`diagram of an ultrasonic monitor.
`
`[0032] FIG. 4 illustrates one embodiment of a method of
`operation of an ultrasonic monitor.
`
`[0033] FIG. 5 illustrates one embodiment of a method for
`performing additional processing by an ultrasonic monitor.
`
`[0034] FIG. 6 illustrates one embodiment of a perspective
`vieW of an ultrasonic monitor on a PCB having an air gap.
`
`[0035] FIG. 7 illustrates one embodiment of a side vieW
`of an ultrasonic monitor on a PCB having an air gap.
`
`[0036] FIG. 8A illustrates one embodiment of a perspec
`tive vieW of an ultrasonic monitor on a PCB having an air
`gap With a supporting member.
`
`[0037] FIG. 8B illustrates one embodiment of a side vieW
`of an ultrasonic monitor on a PCB having an air gap With a
`supporting member.
`
`[0038] FIG. 9A illustrates one embodiment of a perspec
`tive vieW of an ultrasonic monitor on a PCB having one air
`gap shared by tWo transducers.
`
`[0039] FIG. 9B illustrates one embodiment of a side vieW
`of an ultrasonic monitor on a PCB having one air gap shared
`by tWo transducers.
`
`[0040] FIG. 9C illustrates one embodiment of a front
`vieW of an ultrasonic monitor on a PCB having one air gap
`shared by tWo transducers.
`
`[0041] FIG. 10A illustrates one embodiment of a biocom
`patible oil-based transmission medium applicator.
`
`[0042] FIG. 10B illustrates one embodiment of a gel pad.
`
`[0043] FIG. 11A illustrates one embodiment of a perspec
`tive vieW of a oil-based transmission medium component.
`
`[0044] FIG. 11B illustrates one embodiment of a side
`vieW of a oil-based transmission medium component.
`
`[0045] FIG. 12A illustrates one embodiment of a trans
`mission medium con?guration.
`
`[0046] FIG. 12B illustrates one embodiment of a trans
`mission medium con?guration.
`
`[0047] FIG. 12C illustrates one embodiment of a trans
`mission medium con?guration.
`
`[0048] FIG. 13A illustrates one embodiment of a perspec
`tive vieW of an ultrasonic monitor on a PCB With a mold.
`
`[0049] FIG. 13B illustrates one embodiment of a side
`vieW of an ultrasonic monitor on a PCB With a mold.
`
`[0050] FIG. 14A illustrates one embodiment of a side
`vieW of an encapsulated PCB board.
`
`[0051] FIG. 14B illustrates one embodiment of a side
`vieW of an encapsulated PCB board.
`
`[0052] FIG. 14C illustrates one embodiment of a side
`vieW of an encapsulated PCB board.
`
`[0053] FIG. 15A illustrates an embodiment of an ultra
`sonic monitor system With an encapsulated transmission
`medium.
`
`[0054] FIG. 15B illustrates an embodiment of an ultra
`sonic monitor system With an attached transmission
`medium.
`
`DETAILED DESCRIPTION
`
`[0055] The present invention, roughly described, pertains
`to ultrasonic monitors. The ultrasonic monitor uses ultra
`sonic signals to measure movement inside the body of a
`living subject. The movement may be a heart contraction,
`?oWing blood or movement of the blood vessel itself. From
`information collected from these movements, electronics
`Within the monitor may determine blood ?oW rate, heart
`rate, or pulse rate of the living subject.
`
`[0056] In one embodiment, the ultrasonic monitor mea
`sures blood ?oW through an artery of a person. The ultra
`sound signals re?ected by blood vessel expansion (expan
`sion due to blood moving through the vessel) have a
`frequency range similar to that of noise caused by muscle
`artifacts and tissue movement. The ultrasound signals
`re?ected by the ?oWing blood itself have a frequency range
`higher than muscle and tissue related noise. As a result, the
`signals re?ected by ?oWing blood are easier to process to
`?nd the rate values than those re?ected by expansion of the
`blood vessel itself.
`
`[0057] The terms ultrasonic and ultrasound are used inter
`changeably herein and refer to a sound Wave having a
`frequency betWeen about 30 KHZ and about 30 MHZ. An
`ultrasonic transducer, or transducer element, as used herein
`is a device used to introduce sonic energy into and detect
`re?ected signals from a living subject. Ultrasonic transduc
`ers respond to electric pulses from a driving device and
`ultrasonic pulses re?ected by a subject.
`
`[0058] The ultrasonic monitor is comprised of an elec
`tronics portion and a transmission portion. The electronics
`portion includes the electrical components required to trans
`mit, receive, and process the ultrasonic signals as discussed
`
`20 of 30
`
`
`
`US 2006/0264756 A1
`
`Nov. 23, 2006
`
`with respect to FIGS. 3-5. Processing may include ampli-
`fying, filtering, demodulating, digitizing, squaring, and other
`functions typically signal processing functions. Processing
`may be performed all or in part by digital circuitry. For
`example, the received ultrasonic signal can be digitized. The
`processing described herein to the received signal can then
`be performed by digital circuitry. The transmission portion,
`or transmission medium, may include a biocompatible oil-
`based transmission medium, gel pad, or combination of the
`two between the monitor and the subject. In some embodi-
`ments, the oil—based transmission medium can be positioned
`in direct contact with the living subject and the ultrasonic
`monitor. In some embodiments, the oil based transmission
`medium is in contact with the gel pad, and the oil based
`transmission medium and gel pad provide transmission of
`ultrasonic signals between an ultrasonic monitor and a
`subject. Both oil based transmission mediums and gel pads
`are discussed in more detail below.
`
`In one embodiment, an oil—based transmission
`[0059]
`medium used to transmit ultrasonic signals between the
`ultrasonic monitor and the subject may be biocompatible. A
`biocompatible transmission medium is one that can be in
`contact with a user’s skin without being toxic, being inju-
`rious, causing immunological rejection or otherwise result-
`ing in undesirable health effects, such as those caused by
`typical therrnoset and thermoplastic gels. In one embodi-
`ment, a biocompatible oil—based transmission medium can
`include an oil component and a wax component. Both the oil
`and wax components may be natural rather than synthetic.
`Additional components may be included as well, including
`one or more “essential oils” and water. An essential oil is a
`natural oil that provides a fragrance, moisturizes skin, or
`heals skin tissue. Tl1e ratio of wax to liquid (liquids such as
`natural oil, essential oil and water) may determine the
`consistency of the biocompatible oil—based transmission
`medium. The biocompatible oil—based transmission medium
`may be applied between an ultrasonic monitor and a user’s
`skin with an applicator device, as a disposable transmission
`medium component, or as part of the ultrasonic monitor.
`Oil—based transmission media are discussed in more detail
`below.
`
`the monitor of the present
`In one embodiment,
`[0060]
`invention is implemented on a printed circuit board (PCB).
`By implementing the circuitry 011 a PCB, the monitor system
`has a very small footprint with a much lower power require-
`ment. The transducers are mounted directly to the PCB.
`
`[0061] The PCB can implement an ultrasound signal
`refiection layer. In one embodiment, a portion of the outer
`layer of the PCB is removed to create an air gap portion.
`Transducer elements are placed over the air gap portion.
`When driven, the transmitting crystal generates an ultra-
`sound signal that travels towards the PCB in addition to the
`desired direction towards a target. The portion of the origi-
`nally transmitted ultrasound signal traveling towards the
`PCB is reflected by the thin air gap away from the PCB and
`towards the intended target.
`
`In another embodiment, the PCB can be entirely
`[0062]
`encapsulated in plastic, an adhesive, an encapsulant, a gel, or
`a combination ofthese. This provides for keeping the system
`of the ultrasonic monitor protected from debris such as dirt,
`dust and water. These advantages are discussed in more
`detail below.
`
`[0063] The ultrasonic monitor may be implemented with a
`display. FIG. 2A illustrates a wrist worn ultrasonic monitor
`system 200 in one embodiment. System 200 includes an
`ultrasonic monitor module 210, a strap 220, a display device
`230 and a transmission medium 240. Ultrasonic monitor
`module 210 detects blood flow through the radial artery at
`the subject’s wrist. Heart rate data is then provided directly
`to display module 230. In one embodiment, connecting
`wires are molded into strap 220 between the ultrasonic
`monitor module 210 and display device 230.
`
`[0064] The ultrasonic monitor can also be implemented
`with a remote display. The ultrasonic monitor system 250 of
`FIG. 2B includes monitor module 260, first strap 270
`attached to monitor module 260, remote display module 280
`and second strap 290 at'ached to remote display module 280.
`Ultrasonic monitor module 260 detects the blood llow
`through the radial artery in the wrist. Heart rate data is then
`provided to remote display module 280. Monitor 260 can
`wirelessly transmit in onnation to a remote display 280
`using a wireless transmitter. The remote display 260
`includes a receiver to receive the transmission from monitor
`260. The remote display 280 may also be a monitor screen
`or other device. The ultrasonic monitor module 280 may be
`attached to another part of the body (such as the chest over
`the subject’s heart) with a biocompatible adhesive or a
`transmission medium.
`
`[0065] Detennining what ultrasound signal frequency to
`use may depend on the particular object being monitored.
`The wrist olfers a convenient location for positioning the
`monitoring device. The relatively shallow focal depth of the
`radial artery in the wrist suggests using a high frequency
`carrier signal.
`
`[0066] The size of the transducer elements also alfects the
`ultrasound signal
`frequency. Thinner electromechanical
`resonators emit at higher frequencies. Transducer elements
`driven by high frequency signals tend to vibrate more
`rapidly and consume more power than those operating at
`lower frequencies. This is primarily due to internal loss. The
`ultrasonic monitor amplifier and demodulation circuits will
`also consume more power processing the higher frequen-
`cies.
`
`[0067] A block diagram of one embodiment of an ultra-
`sonic monitor system 300 is illustrated in FIG. 3. Ultrasonic
`monitor system 300 includes a microcontroller 310, a trans-
`mitting transducer element 320 connected to microcontroller
`310, a receiving transducer element 330, a radio frequency
`(RF) amplifier 340 connected to receiving transducer 330, a
`mixer 350 comiected to RF amplifier 340 and n1icrocontrol-
`ler 310, an audio amplifier 360 connected to mixer 350, and
`band pass (BP) filter 370 connected to audio frequency
`amplifier 360 and microcontroller 310. Ultrasonic monitor
`system 300 may optionally include a local display 380
`connected to microcontroller 310, a wireless transmitter 390
`connected to microcontroller 310, a wireless receiver 392
`receiving a wireless signal from wireless transmitter 390,
`and a remote display 394 connected to receiver 392.
`
`In one embodiment, an ultrasonic monitor can be
`[0068]
`implemented with a system similar to that represented by
`block diagram 300, but with a driver circuit and high pass
`and low pass filters. In this case, the microcontroller drives
`driver circuitry with a carrier signal. The driver circuitry
`drives transmitting transducer to transmit an ultrasonic sig-
`
`21 of 30
`
`
`
`US 2006/0264756 A1
`
`Nov. 23, 2006
`
`nal at a carrier frequency. The ultrasonic signal is refiected
`and received by receiving transducer. The received signal
`includes a frequency shift from the signal transmitted by
`transducer. The received ultrasonic signal is amplified by RP
`amplifier circuitry. The amplified ultrasonic signal is then
`processed by a mixer, which demodulates the received
`signal and generates a signal with an audio range frequency.
`The resulting signal is then amplified by an audio frequency
`amplifier circuit. The amplified audio signal is then filtered
`by a high pass filter circuit and a low pass filter circuit. The
`filtered signal is then received by the microcontroller. The
`microcontroller processes the filtered signal and provides an
`output signal to a wireless transmitter. The Wireless trans-
`mitter transmits the signal through a wireless means to a
`receiver. A display then receives the signal from the receiver
`and displays information derived from the signal.
`
`[0069] Method 400 of FIG. 4 illustrates the operation of
`one embodiment of an ultrasonic monitor such as that
`represented in FIG. 3. An ultrasound signal is transmitted at
`step 410. With respect to system 300, microcontroller 310
`drives a transmitting transducer element 320 with a carrier
`signal fC. As a result, the transmitting transducer generates
`an ultrasound signal. In one embodiment, the carrier signal
`may be Within a range of 30 KHZ to 30 MHZ. In another
`embodiment, the carrier signal may be within a range of l
`MHZ to 10 MHZ. In yet another embodiment, the carrier
`signal is about 5 MHZ.
`
`[0070] Arefleeted ultrasonic signal is received at step 420.
`The reflected ultrasonic signal is generated by the refiection
`of the ultrasonic signal of step 410 fror11 a blood vessel.
`When the ultrasonic monitor is worn on a wrist, the radial
`artery refiects the signal. The received ultrasonic signal will
`contain an ultrasonic carrier frequency that has experienced
`a Doppler shift from the signal transmitted by transmitting
`transducer 320. The received signal is then amplified at step
`430. In one embodiment, the amplifier 340 of system 300 is
`implemented as a radio frequency amplifier. The received
`ultrasonic signal is amplified by a factor that allows it to be
`processed for demodulation. Once the ultrasonic signal is
`amplified at step 430, it is processed by mixer 350 at step
`440. The mixer uses the carrier signal fc to demodulate the
`reflected ultrasonic signal in order to extract the Doppler
`signal. Accordingly, mixer 350 is driven by carrier signal fc.
`and the reflected ultrasound signal. The output signal pro-
`vided by mixer 350 is then amplified at step 450 by amplifier
`360. As the output of the mixer will have a f
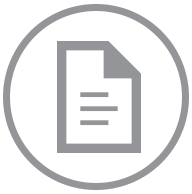
Accessing this document will incur an additional charge of $.
After purchase, you can access this document again without charge.
Accept $ ChargeStill Working On It
This document is taking longer than usual to download. This can happen if we need to contact the court directly to obtain the document and their servers are running slowly.
Give it another minute or two to complete, and then try the refresh button.
A few More Minutes ... Still Working
It can take up to 5 minutes for us to download a document if the court servers are running slowly.
Thank you for your continued patience.
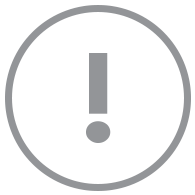
This document could not be displayed.
We could not find this document within its docket. Please go back to the docket page and check the link. If that does not work, go back to the docket and refresh it to pull the newest information.
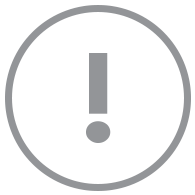
Your account does not support viewing this document.
You need a Paid Account to view this document. Click here to change your account type.
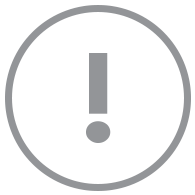
Your account does not support viewing this document.
Set your membership
status to view this document.
With a Docket Alarm membership, you'll
get a whole lot more, including:
- Up-to-date information for this case.
- Email alerts whenever there is an update.
- Full text search for other cases.
- Get email alerts whenever a new case matches your search.
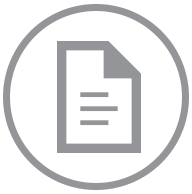
One Moment Please
The filing “” is large (MB) and is being downloaded.
Please refresh this page in a few minutes to see if the filing has been downloaded. The filing will also be emailed to you when the download completes.
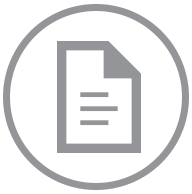
Your document is on its way!
If you do not receive the document in five minutes, contact support at support@docketalarm.com.
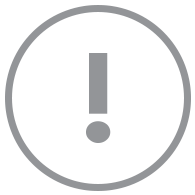
Sealed Document
We are unable to display this document, it may be under a court ordered seal.
If you have proper credentials to access the file, you may proceed directly to the court's system using your government issued username and password.
Access Government Site