`
`(12) United States Patent
`(10) Patent No.:
`US 7,666,337 B2
`
`Yang et al.
`(45) Date of Patent:
`Feb. 23, 2010
`
`(54) POLYETHYLENE OXIDE-BASED FILMS AND
`DRUG DELIVERY SYSTEMS MADE
`THEREFROM
`
`(75)
`
`Inventors: Robert K. Yang; Flushing; NY (US);
`Richard C. Fuisz; McLean; VA (US);
`Gary L. Myers; Kingsport; TN (US);
`Joseph M. Fuisz; McLean; VA (US)
`
`(73)
`
`Assignee: MonoSol RX, LLC; Portage; IN (US)
`
`(*)
`
`Notice:
`
`Subject to any disclaimer; the term of this
`patent is extended or adjusted under 35
`U.S.C. 154(b) by 619 days.
`
`(21)
`
`Appl. No.: 10/856,176
`
`(22)
`
`Filed:
`
`May 28, 2004
`
`(65)
`
`(63)
`
`Prior Publication Data
`
`US 2005/0037055 A1
`
`Feb. 17; 2005
`
`Related US. Application Data
`
`Continuation-in-part of application No. 10/768,809,
`filed on Jan. 30; 2004; now Pat. No. 7,357,891; and a
`continuation-in-part of application No. PCT/USO2/
`32575; filed on Oct. 11; 2002; and a continuation-in-
`part ofapplication No. PCT/USO2/32594; filed on Oct.
`1 1; 2002; and a continuation-in-part ofapplication No.
`PCT/USO2/32542; filed on Oct. 11; 2002.
`
`(60)
`
`Provisional application No. 60/473,902; filed on May
`28; 2003; provisional application No. 60/443,741;
`filed on Jan. 30; 2003; provisional application No.
`60/371,940; filed on Apr. 11; 2002.
`
`Int. Cl.
`
`(51)
`
`(52) U.S.C1.
`
`.................. 264/172.19; 264/212; 264/234;
`264/319; 264/344
`(58) Field of Classification Search ....................... None
`See application file for complete search history.
`
`(56)
`
`References Cited
`U.S. PATENT DOCUMENTS
`
`307,537 A
`
`11/1884 Foulks
`
`(Continued)
`FOREIGN PATENT DOCUMENTS
`
`DE
`
`2432925 B2
`
`1/1976
`
`(Continued)
`OTHER PUBLICATIONS
`
`XP-002298105; Polyethylenglykole; Internet: www.r0empp.com;
`Sep. 20, 2004.
`
`(Continued)
`
`Primary ExamineriEdmund H. Lee
`(74) Attorney, Agent, or FirmiHoffmann & Baron; LLP
`
`(57)
`
`ABSTRACT
`
`The invention relates to the film products and methods oftheir
`preparation that demonstrate a non-self—aggregating uniform
`heterogeneity. Desirably; the films disintegrate in water and
`may be formed by a controlled drying process; or other pro-
`cess that maintains the required uniformity of the film. The
`films contain a polymer component; which includes polyeth-
`ylene oxide optionally blended with hydrophilic cellulosic
`polymers. Desirably; the films also contain a pharmaceutical
`and/or cosmetic active agent with no more than a 10% vari-
`ance of the active agent pharmaceutical and/or cosmetic
`active agent per unit area of the film.
`
`329C 39/14
`
`(2006.01)
`
`30 Claims, 34 Drawing Sheets
`
`
`
`Page 1
`
`BDSI EXHIBIT 1033
`
`Page 1
`
`
`
`US 7,666,337 B2
`
`Page 2
`
`US. PATENT DOCUMENTS
`
`688446 A
`2,142,537 A
`2277038 A
`2,352,691 A
`2,501,544 A
`2,980,554 A
`3,249,109 A
`3,444,858 A
`3,536,809 A
`3,551,556 A
`3,598,122 A
`3,632,740 A
`3,640,741 A
`3,641,237 A
`3,731,683 A
`3753732 A
`3,814,095 A
`3,892,905 A
`3,911,099 A
`3,972,995 A
`3,996,934 A
`3,998,215 A
`4,029,757 A
`4,029,758 A
`4,031,200 A
`4,049,848 A *
`4,123,592 A
`4,128,445 A
`4,136,145 A
`4,136,162 A
`4,139,627 A
`4226848 A
`4,251,400 A
`4,292,299 A
`4,294,820 A
`4,302,465 A
`4,307,075 A
`4,325,855 A
`4,373,036 A
`4406708 A
`4432975 A
`4,438,258 A
`4460562 A
`4466973 A
`4,503,070 A
`4,515,162 A
`4,517,173 A
`4,529,601 A
`4529748 A
`4562020 A
`4,569,837 A
`4593053 A
`4,608,249 A
`4,615,697 A
`4,623,394 A
`4,652,060 A
`4,659,714 A
`4,675,009 A
`4,695,465 A
`4,704,119 A
`4,713,239 A
`4,713,243 A
`4,722,761 A
`4,740,365 A
`4,748,022 A
`4,765,983 A
`4,772,470 A
`4,777,046 A
`4,789,667 A
`4,849,246 A
`4,860,754 A
`
`Page 2
`
`............. 427/244
`
`12/1901 Stempel
`1/1939 Tisza
`3/1942 Cunis
`7/1944 Cunis
`3/1950 Shrontz
`4/1961 Gentile et 31.
`5/1966 Maeth etai
`5/1969 Russell
`10/1970 Applezweig
`12/1970 Klimentetai
`8/1971 anfnreni
`1/1972 Robinson etal.
`2/1972 Etes
`2/1972 Gouldet al.
`5/1973 Zaffareni
`8/1973 Bereshek
`6/1974 Lubens
`7/1975 Albert
`10/1975 DeFoney etai
`8/1976 Tsuketal.
`12/1976 Zaffaroni
`12/1976 Anderson etai
`6/1977 Mlodozeniec et 31.
`6/1977 Mlodzeniec et al.
`6/1977 Reif
`9/1977 Goodale etal.
`10/1978 Rnineretai
`12/1978 Sturzeneggeret 31.
`1/1979 Fuchs etal.
`1/1979 Fuchsetal.
`2/1979 Lane etai
`10/1980 Nagaietai
`2/1981 Columbus
`9/1981 Suzuki et al.
`10/1981 Keith etai
`11/1981 Ekenstamet 31.
`12/1981 Martin
`4/1982 Diekmann
`2/1983 Chang etai
`9/1983 Hesselgren
`2/1984 Libby
`3/1984 Graham
`7/1984 Keith etai
`8/1984 Rennie
`3/1985 Eby
`5/1985 Katsuhire
`5/1985 Kizawaetai
`7/1985 Broberg etai
`7/1985 Wieneeke
`12/1985 Hijiya etal.
`2/1986 Suzuki etai
`6/1986 JeVne
`8/1986 Otsuka etai
`10/1986 Robinson
`11/1986 Nnkaniura etai
`3/1987 Miyake _
`4/1987 Wan-Smith
`6/1987 Hymesetai
`9/1987 Kigasawa etai
`11/1987 Shaw etai
`12/1987 Babaian et a1.
`12/1987 Schiraldi et a1.
`2/1988 Canme11 etal.
`4/1988 Yukimatsu et a1.
`5/1988 Busciglio
`8/1988 Takayanagi et a1.
`9/1988 Inoue et a1.
`10/1988 Iwakura et a1.
`12/1988 Makino et a1.
`7/1989 Schmidt
`8/1989 Sharik etal.
`
`RE33,093 E
`4,876,092 A
`4,876,970 A
`4,888,354 A
`4,894,232 A
`4,900,552 A
`4,900,554 A
`4,900,556 A
`4,910,247 A
`4,915,950 A
`4,925,670 A
`4,927,634 A
`4,927,636 A
`4,937,078 A
`4,940,587 A
`4,948,580 A
`4,958,580 A
`4,978,531 A
`4,981,693 A
`4,981,875 A
`5,023,082 A
`5,024,701 A
`5,028,632 A
`5,047,244 A
`5,064,717 A
`5,089,307 A
`5,158,825 A
`5,166,233 A
`5,186,938 A
`5,229,164 A
`5,234,957 A
`5,271,940 A
`5,272,191 A
`5,346,701 A
`5,393,528 A
`5,411,945 A
`5,413,792 A
`5,433,960 A
`5,455,043 A
`5,462,749 A
`5,472,704 A
`5,518,902 A
`5,567,431 A
`5,620,757 A
`5,629,003 A
`5,700,478 A
`5,700,479 A
`5,766,525 A *
`5,766,620 A
`5,948,430 A
`6,072,100 A
`6,153,210 A
`6,177,096 B1
`6,231,957 B1
`6,284,264 B1
`6,375,963 B1
`6,488,963 B1
`2001/0006677 A1
`2001/0022964 A1
`2001/0046511 A1
`2005/0037055 A1
`2005/0118217 A1
`
`10/1989 Schiraldi et al.
`10/1989 Mizobuchiet al.
`10/1989 Bolduc
`12/1989 Chang etal.
`1/1990 Reul et a1.
`2/1990 Sanvordeker et a1.
`2/1990 Yanagibashietal.
`2/1990 Wheatleyet 31.
`3/1990 Haldar et a1.
`4/1990 Miranda et a1.
`5/1990 Schmidt
`5/1990 Sorrentino et a1.
`5/1990 Hijiya et a1.
`6/1990 Mezeiet 31.
`7/1990 Jenkins etal.
`8/1990 Browning
`9/1990 Asaba etal.
`12/1990 Keiko etal.
`1/1991 Higashi et a1.
`1/1991 Leusneretal.
`6/1991 Friedman et a1.
`6/1991 Desmarais
`7/1991 Fuisz
`9/1991 Sanvordeker et a1.
`11/1991 Suzuki et 31.
`2/1992 Ninomiya et 31.
`10/1992 Aitwirth
`11/1992 Kuroya
`2/1993 Sablotskyetal.
`7/1993 Pins et 31.
`8/1993 Mantelle
`12/1993 Clearyetal.
`12/1993 Ibrahim et al.
`9/1994 Heiber et a1.
`2/1995 Staab
`5/1995 Ozaki et 31.
`5/1995 Ninomiya etal.
`7/1995 Meyers
`10/1995 Fischel—Ghodsian
`10/1995 Rencher
`12/1995 Giancarlo et a1.
`5/1996 Ozaki et a1.
`10/1996 Vert et a1.
`4/1997 Ninomiya etal.
`5/1997 Horstmann et a1.
`12/1997 Biegajskietal.
`12/1997 Lundgren
`6/1998 Andersen et a1.
`6/1998 Herber et a1.
`9/1999 Zerbe etal.
`6/2000 Mooney et a1.
`11/2000 Roberts etal.
`1/2001 Zerbe et al.
`5/2001 Zerbe etal.
`9/2001 Zerbe et a1.
`4/2002 Repka et 31.
`12/2002 McGinity et a1.
`7/2001 McGinity et a1.
`9/2001 Leung etal.
`11/2001 Zerbe etal.
`2/2005 Yang et a1.
`6/2005 Barnhan et a1.
`
`........... 264/40.1
`
`FOREIGN PATENT DOCUMENTS
`
`DE
`DE
`DE
`EP
`EP
`EP
`EP
`EP
`
`2449865 B2
`3630603 C2
`196465392
`0241178 A1
`0219762 B1
`0259749 B1
`0200508 B1
`0273069 B1
`
`4/1976
`3/1988
`5/1998
`10/1987
`12/1990
`8/1991
`10/1991
`10/1992
`
`Page 2
`
`
`
`US 7,666,337 B2
` Page 3
`
`EP
`EP
`EP
`EP
`EP
`
`EP
`W0
`
`W0
`W0
`W0
`W0
`W0
`W0
`W0
`W0
`
`0 514 691 A2
`0250187 B1
`0452446 B1
`0 598 606 A1
`0381194 B1
`
`1 110 546 A1
`WO 91/05540 A1
`
`WO 92/15289 A1
`WO 95/05416 A2
`WO 95/18046 A1
`W0 97/31621
`WO 00/18365
`WO 00/42992
`WO 01/70194
`WO 01/70194 A1
`
`11/1992
`9/1993
`12/1993
`5/1994
`8/1994
`
`6/2001
`5/1991
`
`9/1992
`2/ 1995
`7/1995
`9/1997
`4/2000
`7/2000
`9/2001
`9/2001
`
`W0
`W0
`W0
`W0
`
`WO 01/91721 A2
`W0 03/030882
`W0 03/030883
`WO 2005/102287
`
`12/2001
`4/2003
`4/2003
`11/2005
`
`OTHER PUBLICATIONS
`
`Repka et al.; Influence of Vitamin E. TPGS on the properties of
`hydrophilic films produced by hot-melt extrusion; International Jour-
`nal of Pharmaceutics; V01. 202, pp. 63-70; 2000.
`Repka et a1.; Bioadhesive properties ofhydroxypropylcellulose topi-
`cal films produced by hot-melt extrusion; Journal of Controlled
`Release; vol. 70; pp. 341—351; 2001.
`
`* cited by examiner
`
`Page 3
`
`Page 3
`
`
`
`US. Patent
`
`Feb. 23, 2010
`
`Sheet 1 of 34
`
`US 7,666,337 B2
`
`10
`/ 74
`
`12
`
`14
`
`FIG. 1
`
`,0
`
`70,
`
`"~ 76
`FIG. 2
`
`10
`
`
`
`FIG. 5
`
`Page 4
`
`Page 4
`
`
`
`US. Patent
`
`Feb. 23, 2010
`
`Sheet 2 of 34
`
`US 7,666,337 B2
`
`
`
`
`
`.32
`
`30
`WW\ ‘. A A A
`[ain't-III.
`
`
`
`Page 5
`
`Page 5
`
`
`
`US. Patent
`
`Feb. 23, 2010
`
`Sheet 3 of 34
`
`US 7,666,337 B2
`
`4
`
`42
`
`,mw;“‘““““““““‘\““
`'IIIIIIIIIIIIIIIIIIIIIIIIIIIIIIIIIIIIIIII
`
`
`
`FIG. 7
`
`Page 6
`
`Page 6
`
`
`
`U.S. Patent
`
`Feb. 23, 2010
`
`Sheet 4 of 34
`
`US 7,666,337 B2
`
`SECTION8SECTION0
`
`SECTIONA
`
`40
`
`30
`
`40
`
`70
`
`FIG.8
`
`50
`
`50
`
`50
`
`20
`
`Page 7
`
`Page 7
`
`
`
`U.S. Patent
`
`Feb.23,2010
`
`Sheet50f34
`
`US 7,666,337 B2
`
`
`
`007
`
`FIG. 9
`
`Page 8
`
`Page 8
`
`
`
`U S. Patent
`
`Feb. 23, 2010
`
`Sheet 6 of 34
`
`US 7,666,337 B2
`
`
`
`770
`
`700
`
`FIG. 10
`
`Page 9
`
`Page 9
`
`
`
`U S Patent
`
`Feb. 23, 2010
`
`Sheet70f34
`
`US 7,666,337 B2
`
`
`
`110
`
`FIG. 11
`
`700
`
`Page 10
`
`Page 10
`
`
`
`U S. Patent
`
`Feb. 23, 2010
`
`Sheet 8 of 34
`
`US 7,666,337 B2
`
`-
`
`'1:-
`, ,v’
`95‘ v m3.
`
`1,? 4h
`
`770
`
`700
`
`FIG. 12
`
`Page 11
`
`Page 11
`
`
`
`U S. Patent
`
`Feb. 23, 2010
`
`Sheet90f34
`
`US 7,666,337 B2
`
`
`
`770
`
`700
`
`FIG. 13
`
`Page 12
`
`Page 12
`
`
`
`U S Patent
`
`Feb.23,2010
`
`Sheet100f34
`
`US 7,666,337 B2
`
`
`
`770
`
`007
`
`FIG. 14
`
`Page 13
`
`Page 13
`
`
`
`U S. Patent
`
`Feb. 23, 2010
`
`Sheet 11 of 34
`
`US 7,666,337 B2
`
`1
`
`a”;
`g,“ .‘3
`v3
`‘12:,
`
`770
`
`700
`
`FIG. 15
`
`Page 14
`
`Page 14
`
`
`
`U S Patent
`
`Feb. 23, 2010
`
`Sheet 12 of 34
`
`US 7,666,337 B2
`
`
`
`100
`
`FIG. 16
`
`Page 15
`
`Page 15
`
`
`
`US. Patent
`
`Feb. 23, 2010
`
`Sheet 13 of 34
`
`US 7,666,337 B2
`
`
`
`200
`
`FIG. 17
`
`Page 16
`
`Page 16
`
`
`
`U S. Patent
`
`Feb. 23, 2010
`
`Sheet 14 of 34
`
`US 7,666,337 B2
`
`
`
`500
`
`FIG. 18
`
`Page 17
`
`Page 17
`
`
`
`U S Patent
`
`Feb.23,2010
`
`Sheet150f34
`
`US 7,666,337 B2
`
`
`
`005
`
`FIG. 19
`
`Page 18
`
`Page 18
`
`
`
`U S Patent
`
`Feb.23,2010
`
`Sheet16of34
`
`US 7,666,337 B2
`
`5
`
`00
`
`FIG. 20
`
`Page 19
`
`Page 19
`
`
`
`U S. Patent
`
`Feb.23,2010
`
`Sheet17of34
`
`US 7,666,337 B2
`
`;
`
`.fu.2..
`
`
`
`a:
`A»..f
`
`500
`
`FIG. 21
`
`Page 20
`
`Page 20
`
`
`
`U S Patent
`
`Feb.23,2010
`
`Sheet180f34
`
`US 7,666,337 B2
`
`
`
`500
`
`FIG. 22
`
`Page 21
`
`Page 21
`
`
`
`U S. Patent
`
`Feb. 23, 2010
`
`Sheet 19 of 34
`
`US 7,666,337 B2
`
`
`
`500
`
`FIG. 23
`
`Page 22
`
`Page 22
`
`
`
` Patent
`
`Feb. 23, 2010
`
`Sheet 20 of 34
`
`US 7,666,337 B2
`
`
`
`500
`
`FIG. 24
`
`Page 23
`
`Page 23
`
`
`
`U S. Patent
`
`Feb.23,2010
`
`Sheet210f34
`
`US 7,666,337 B2
`
`
`
`500
`
`FIG. 25
`
`Page 24
`
`Page 24
`
`
`
`US. Patent
`
`Feb. 23, 2010
`
`Sheet 22 of 34
`
`US 7,666,337 B2
`
`
`
`HQ. 26
`
`Page 25
`
`Page 25
`
`
`
`U.S. Patent
`
`Feb.23,2010
`
`Sheet23of34
`
`US 7,666,337 B2
`
`
`
`FIG. 27
`
`Page 26
`
`Page 26
`
`
`
`US. Patent
`
`Feb. 23, 2010
`
`Sheet 24 of 34
`
`US 7,666,337 B2
`
`
`
`
`
`500
`
`FIG. 28
`
`Page 27
`
`Page 27
`
`
`
`U S Patent
`
`Feb.23,2010
`
`Sheet250f34
`
`US 7,666,337 B2
`
`
`
`500
`
`FIG. 29
`
`Page 28
`
`Page 28
`
`
`
`U S Patent
`
`Feb. 23, 2010
`
`Sheet 26 of 34
`
`US 7,666,337 B2
`
`
`
`500
`
`FIG. 30
`
`Page 29
`
`Page 29
`
`
`
`U S. Patent
`
`Feb. 23, 2010
`
`Sheet 27 of 34
`
`US 7,666,337 B2
`
`
`
`500
`
`FIG. 31
`
`Page 30
`
`Page 30
`
`
`
`tnetaPQMU
`
`US 7,666,337 B2
`
`488908989co?m_i=8.aqsgéagzm£22ngs:ummmw%2:m
`mwmw3,08FMI:2Mb..0eWF2
`
`:532.5588_“5.x #852925fiegwmgesa8_m5.»A383__m”a:28N852925
`
`
`
`22.52935Eatmmmssea8..E858EN:92%__m”a:2.8BEE
`
`
`coo?
`
`ww
`
`w.wnu.“
`
`
`
`.80852amom.9:homos.1920285.252
`
`Nm.OE
`
`Page 31
`
`Page 31
`
`
`
`US. Patent
`
`Feb. 23, 2010
`
`Sheet 29 of 34
`
`US 7,666,337 B2
`
`"\
`£1
`0.
`Ek
`
`
`+0szTEMP(c)
`
`B:
`t
`D~
`
`QI
`
`72
`
`17
`
`70
`
`FIG.33
`
`90
`
`80
`
`70
`
`60
`
`50
`
`40
`
`30
`
`20
`
`70
`
`Page 32
`
`Page 32
`
`
`
`US. Patent
`
`Feb. 23, 2010
`
`Sheet 30 of 34
`
`US 7,666,337 B2
`
`'\
`9.,
`u.
`EK
`
`7712
`
`70
`
`FIG.34
`
`.90
`
`80
`
`70
`
`60
`
`50
`
`40
`
`30
`
`20
`
`70
`
`Page 33
`
`o. +OVENTEMP(c)
`
`Lu
`on
`
`QC
`
`:
`
`Page 33
`
`
`
`US. Patent
`
`Feb. 23, 2010
`
`Sheet 31 of 34
`
`US 7,666,337 B2
`
`700
`
`
`
`120
`
`701
`
`702
`
`103
`
`FIG. 35
`
`Page 34
`
`Page 34
`
`
`
`US. Patent
`
`Feb. 23, 2010
`
`Sheet 32 of 34
`
`US 7,666,337 B2
`
`200
`
`
`
`207
`
`202
`
`203
`
`FIG. 36
`
`Page 35
`
`Page 35
`
`
`
`US. Patent
`
`Feb. 23, 2010
`
`Sheet 33 of 34
`
`US 7,666,337 B2
`
`/100
`
`400
`
`300
`
`200
`
`7
`
`FIG.37
`
`Page 36
`
`Page 36
`
`
`
`U.S. Patent
`
`Feb. 23, 2010
`
`Sheet 34 of 34
`
`US 7,666,337 B2
`
`IEIIII&IIIIaguehe.sE3;§Eam”3.3%3.RN2%32%a:mIIIIIIEIIIII%g-EQbask§E.E8%2%g:a.a
`
`&*3
`
`
`
`
`
`aa.-
`
`a.aigaIEIEEEEEE:wa.gIIEEEEEE-IEIIIIIIIIIIga.a3E23.3:Es£333V.»:Na§3“Ea.m
`
`aan
`
`
`
`EIIIIIIIIII%g-a§mQEek§EsE:3a.»83%g9%a.E
`
`IIIIIE6“I...ga-2%“7:£Emagass:3RN$5.3‘9%a.EIEIIIIEIIIIge.eERaeE:a3‘aE23$22»9%aaaa
`
`QN%-a“%
`mm.OE
`
`
`
`M,EE!E?E;EEEE3a.m
`
`a»E-
`
`53sEfiams£38SEEBB.3‘38a8§E§<ginamissfiamaswE«3.3E3323
`
`.3msé.SE.92a&bfisfiEgawkas}....Kmsbam
`
`8m
`
`SEs38Sha$85$555%anuéi
`
`Page 37
`
`Page 37
`
`
`
`
`
`
`US 7,666,337 B2
`
`1
`POLYETHYLENE OXIDE-BASED FILMS AND
`DRUG DELIVERY SYSTEMS MADE
`THEREFROM
`
`CROSS-REFERENCE TO RELATED
`APPLICATIONS
`
`This application claims the benefit of US. Provisional
`Application No. 60/473,902, filed May 28, 2003 and is a
`continuation-in-part of US. application Ser. No. 10/768,809,
`filed Jan. 30, 2004 now US. Pat. No. 7,357,891,which claims
`benefit to US. Provisional Application No. 60/443,741 filed
`Jan. 30, 2003 and is a continuation-in-part of:
`(a) PCT/USO2/32575 filed Oct. 11, 2002, which claims
`priority to: (1) US. application Ser. No. 10/074,272, filed
`Feb. 14, 2002 which claims benefit to US. Provisional Appli-
`cation No. 60/328,868, filed Oct. 12, 2001 and (2) US. Pro-
`visional Application No. 60/386,937, filed Jun. 7, 2002;
`(b) PCT/USO2/32594, filed Oct. 11, 2002, which claims
`priority to: (1) US. Provisional Application No. 60/414,276,
`filed Sep. 27, 2002, (2) US. application Ser. No. 10/074,272,
`filed Feb. 14, 2002, which claims benefit to US. Provisional
`Application No. 60/328,868, filed Oct. 12, 2001 and (3) US.
`Provisional Application No. 60/386,937, filed Jun. 7, 2002;
`and
`
`(c) PCT/US/02/32542, filed Oct. 11, 2002, which claims
`priority to: (1) US. Provisional Application No. 60/371,940,
`filedApr. 11, 2002, (2) US. application Ser. No. 10/074,272,
`filed Feb. 14, 2002, which claims benefit to US. Provisional
`Application No. 60/328,868, filed Oct. 12, 2001 and (3) US.
`Provisional Application No. 60/386,937, filed Jun. 7, 2002.
`
`FIELD OF THE INVENTION
`
`The invention relates to rapidly dissolving films and meth-
`ods of their preparation. The films contain a polymer compo-
`nent, which includes polyethylene oxide optionally blended
`with cellulosic polymers. The films may also contain an
`active ingredient that is evenly distributed throughout the
`film. The even or uniform distribution is achieved by control-
`ling one or more parameters, and particularly the elimination
`of air pockets prior to and during film formation and the use
`of a drying process that reduces aggregation or conglomera-
`tion of the components in the film as it forms into a solid
`structure.
`
`BACKGROUND OF THE RELATED
`TECHNOLOGY
`
`Active ingredients, such as drugs or pharmaceuticals, may
`be prepared in a tablet form to allow for accurate and consis-
`tent dosing. However, this form of preparing and dispensing
`medications has many disadvantages including that a large
`proportion of adjuvants that must be added to obtain a size
`able to be handled, that a larger medication form requires
`additional storage space, and that dispensing includes count-
`ing the tablets which has a tendency for inaccuracy. In addi-
`tion, many persons, estimated to be as much as 28% of the
`population, have difficulty swallowing tablets. While tablets
`may be broken into smaller pieces or even crushed as a means
`of overcoming swallowing difiiculties, this is not a suitable
`solution for many tablet or pill forms. For example, crushing
`or destroying the tablet or pill form to facilitate ingestion,
`alone or in admixture with food, may also destroy the con-
`trolled release properties.
`As an alternative to tablets and pills, films may be used to
`carry active ingredients such as drugs, pharmaceuticals, and
`
`10
`
`15
`
`20
`
`25
`
`30
`
`35
`
`40
`
`45
`
`50
`
`55
`
`60
`
`65
`
`2
`
`the like. However, historically films and the process of mak-
`ing drug delivery systems therefrom have suffered from a
`number of unfavorable characteristics that have not allowed
`
`them to be used in practice.
`Films that incorporate a pharmaceutically active ingredient
`are disclosed in expired US. Pat. No. 4,136,145 to Fuchs, et
`al. (“Fuchs”). These films may be formed into a sheet, dried
`and then cut into individual doses. The Fuchs disclosure
`
`alleges the fabrication of a uniform film, which includes the
`combination of water-soluble polymers, surfactants, flavors,
`sweeteners, plasticizers and drugs. These allegedly flexible
`films are disclosed as being useful for oral, topical or enteral
`use. Examples of specific uses disclosed by Fuchs include
`application of the films to mucosal membrane areas of the
`body, including the mouth, rectal, vaginal, nasal and ear areas.
`Examination of films made in accordance with the process
`disclosed in Fuchs, however, reveals that such films suffer
`from the aggregation or conglomeration of particles,
`i.e.,
`self-aggregation, making them inherently non-uniform. This
`result can be attributed to Fuchs’ process parameters, which
`although not disclosed likely include the use ofrelatively long
`drying times, thereby facilitating intermolecular attractive
`forces, convection forces, air flow and the like to form such
`agglomeration.
`The formation of agglomerates randomly distributes the
`film components and any active present as well. When large
`dosages are involved, a small change in the dimensions ofthe
`film would lead to a large difference in the amount of active
`per film. If such films were to include low dosages of active,
`it is possible that portions of the film may be substantially
`devoid of any active. Since sheets of film are usually cut into
`unit doses, certain doses may therefore be devoid of or con-
`tain an insufficient amount of active for the recommended
`
`treatment. Failure to achieve a high degree of accuracy with
`respect to the amount of active ingredient in the cut film can
`be harmful to the patient. For this reason, dosage forms
`formed by processes such as Fuchs, would not likely meet the
`stringent standards of governmental or regulatory agencies,
`such as the US. Federal Drug Administration (“FDA”), relat-
`ing to the variation of active in dosage forms. Currently, as
`required by various world regulatory authorities, dosage
`forms may not vary more than 10% in the amount of active
`present. When applied to dosage units based on films, this
`virtually mandates that uniformity in the film be present.
`The problems of self-aggregation leading to non-unifor-
`mity ofa film were addressed in US. Pat. No. 4,849,246 to
`Schmidt (“Schmidt”). Schmidt specifically pointed out that
`the methods disclosed by Fuchs did not provide a uniform
`film and recognized that that the creation of a non-uniform
`film necessarily prevents accurate dosing, which as discussed
`above is especially important in the pharmaceutical area.
`Schmidt abandoned the idea that a mono-layer film, such as
`described by Fuchs, may provide an accurate dosage form
`and instead attempted to solve this problem by forming a
`multi-layered film. Moreover, his process is a multi-step pro-
`cess that adds expense and complexity and is not practical for
`commercial use.
`
`Other US. patents directly addressed the problems of par-
`ticle self-aggregation and non-uniformity inherent in conven-
`tional film forming techniques. In one attempt to overcome
`non-uniformity, US. Pat. No. 5,629,003 to Horstmann et al.
`and US. Pat. No. 5,948,430 to Zerbe et al. incorporated
`additional ingredients, i.e. gel formers and polyhydric alco-
`hols respectively, to increase the viscosity of the film prior to
`drying in an effort to reduce aggregation ofthe components in
`the film. These methods have the disadvantage of requiring
`additional components, which translates to additional cost
`
`Page 38
`
`Page 38
`
`
`
`US 7,666,337 B2
`
`3
`and manufacturing steps. Furthermore, both methods employ
`the use the conventional time-consuming drying methods
`such as a high-temperature air-bath using a drying oven,
`drying tunnel, vacuum drier, or other such drying equipment.
`The long length of drying time aids in promoting the aggre-
`gation of the active and other adjuvant, notwithstanding the
`use of viscosity modifiers. Such processes also run the risk of
`exposing the active, i.e., a drug, or vitamin C, or other com-
`ponents to prolonged exposure to moisture and elevated tem-
`peratures, which may render it ineffective or even harmful.
`In addition to the concerns associated with degradation of
`an active during extended exposure to moisture, the conven-
`tional drying methods themselves are unable to provide uni-
`form films. The length of heat exposure during conventional
`processing, often referred to as the “heat history”, and the
`manner in which such heat is applied, have a direct effect on
`the formation and morphology of the resultant film product.
`Uniformity is particularly difficult to achieve via conven-
`tional drying methods where a relatively thicker film, which is
`well-suited for the incorporation of a drug active, is desired.
`Thicker uniform films are more difficult to achieve because
`
`the surfaces of the film and the inner portions of the film do
`not experience the same external conditions simultaneously
`during drying. Thus, observation of relatively thick films
`made from such conventional processing shows a non-uni-
`form structure caused by convection and intermolecular
`forces and requires greater than 10% moisture to remain
`flexible. The amount of free moisture can often interfere over
`
`time with the drug leading to potency issues and therefore
`inconsistency in the final product.
`Conventional drying methods generally include the use of
`forced hot air using a drying oven, drying tunnel, and the like.
`The difficulty in achieving a uniform film is directly related to
`the rheological properties and the process of water evapora-
`tion in the film-forming composition. When the surface of an
`aqueous polymer solution is contacted with a high tempera-
`ture air current, such as a film-forming composition passing
`through a hot air oven, the surface water is immediately
`evaporated forming a polymer film or skin on the surface.
`This seals the remainder of the aqueous film-forming com-
`position beneath the surface, forming a barrier through which
`the remaining water must force itself as it is evaporated in
`order to achieve a dried film. As the temperature outside the
`film continues to increase, water vapor pressure builds up
`under the surface ofthe film, stretching the surface ofthe film,
`and ultimately ripping the film surface open allowing the
`water vapor to escape. As soon as the water vapor has
`escaped, the polymer film surface reforms, and this process is
`repeated, until the film is completely dried. The result of the
`repeated destruction and reformation of the film surface is
`observed as a “ripple effect” which produces an uneven, and
`therefore non-uniform film. Frequently, depending on the
`polymer, a surface will seal so tightly that the remaining water
`is difficult to remove, leading to very long drying times,
`higher temperatures, and higher energy costs.
`Other factors, such as mixing techniques, also play a role in
`the manufacture of a pharmaceutical film suitable for com-
`mercialization and regulatory approval. Air can be trapped in
`the composition during the mixing process or later during the
`film making process, which can leave voids in the film prod-
`uct as the moisture evaporates during the drying stage. The
`film frequently collapse around the voids resulting in an
`uneven film surface and therefore, non-uniformity ofthe final
`film product. Uniformity is still affected even if the voids in
`the film caused by air bubbles do not collapse. This situation
`also provides a non-uniform film in that the spaces, which are
`not uniformly distributed, are occupying area that would oth-
`
`10
`
`15
`
`20
`
`25
`
`30
`
`35
`
`40
`
`45
`
`50
`
`55
`
`60
`
`65
`
`4
`
`erwise be occupied by the film composition. None of the
`above-mentioned patents either addresses or proposes a solu-
`tion to the problems caused by air that has been introduced to
`the film.
`
`Therefore, there is a need for methods and compositions
`for film products, which use a minimal number ofmaterials or
`components, and which provide a substantially non-self-ag-
`gregating uniform heterogeneity throughout the area of the
`films. Desirably, such films are produced through a selection
`of a polymer or combination of polymers that will provide a
`desired viscosity, a film-forming process such as reverse roll
`coating, and a controlled, and desirably rapid, drying process
`which serves to maintain the uniform distribution ofnon-self-
`
`aggregated components without the necessary addition of gel
`formers or polyhydric alcohols and the like which appear to
`be required in the products and for the processes of prior
`patents, such as the aforementioned Horstmann and Zerbe
`patents. Desirably, the films will also incorporate composi-
`tions and methods ofmanufacture that substantially reduce or
`eliminate air in the film, thereby promoting uniformity in the
`final film product.
`
`SUMMARY OF THE INVENTION
`
`The present invention is directed to rapid-dissolve film
`products containing at
`least one water-soluble polymer
`including polyethylene oxide alone or in combination with a
`hydrophilic cellulosic polymer, wherein the film product is
`free of added plasticizers.
`Another embodiment of the rapid-dissolve film product
`includes at least one water-soluble polymer containing about
`20% to 100% by weight polyethylene oxide, about 0% to 80%
`by weight hydroxypropylmethyl cellulose, and about 0% to
`80% by weight hydroxypropyl cellulose; an active compo-
`nent; sucralose; precipitated calcium carbonate;
`at least one flavoring; simethicone; water; and at least one
`colorant, wherein the film product is free of added plas-
`ticizers, surfactants, and polyalcohols.
`invention is
`Yet another embodiment of the present
`directed to an edible water-soluble delivery system in the
`form ofa film composition, which contains at least one water-
`soluble polymer comprising polyethylene oxide alone or in
`combination with a polymer selected from the group consist-
`ing of hydroxypropylmethyl cellulose and hydroxypropyl
`cellulose, wherein the edible water-soluble delivery system is
`essentially free of organic solvents, plasticizers, surfactants,
`and polyalcohols.
`The present invention is also directed to processes for
`making a film having a substantially uniform distribution of
`components, including the steps of: (a) combining at least one
`water-soluble polymer comprising polyethylene oxide alone
`or in combination with a hydrophilic cellulosic polymer, a
`solvent, and an active component to form a matrix with a
`uniform distribution of the components; (b) forming a film
`from the matrix; and (c) drying the film, wherein the film is
`free of added plasticizers.
`
`BRIEF DESCRIPTION OF THE DRAWINGS
`
`FIG. 1 shows a side view of a package containing a unit
`dosage film of the present invention.
`FIG. 2 shows a top view of two adjacently coupled pack-
`ages containing individual unit dosage forms of the present
`invention, separated by a tearable perforation.
`FIG. 3 shows a side view of the adjacently coupled pack-
`ages of FIG. 2 arranged in a stacked configuration.
`
`Page 39
`
`Page 39
`
`
`
`US 7,666,337 B2
`
`5
`FIG. 4 shows a perspective view of a dispenser for dispens-
`ing the packaged unit dosage forms, dispenser containing the
`packaged unit dosage forms in a stacked configuration.
`FIG. 5 is a schematic view of a roll of coupled unit dose
`packages of the present invention.
`FIG. 6 is a schematic view of an apparatus suitable for
`preparation of a pre-mix, addition of an active, and subse-
`quent formation of the film.
`FIG. 7 is a schematic view of an apparatus suitable for
`drying the films of the present invention.
`FIG. 8 is a sequential representation of the drying process
`of the present invention.
`FIG. 9 is a photographic representation of a film dried by
`conventional drying processes.
`FIG. 10 is a photographic representation of a film dried by
`conventional drying processes.
`FIG. 11 is a photographic representation of a film dried by
`conventional drying processes.
`FIG. 12 is a photographic representation of a film dried by
`conventional drying processes.
`FIG. 13 is a photographic representation of a film dried by
`conventional drying processes.
`FIG. 14 is a photographic representation of a film dried by
`conventional drying processes.
`FIG. 15 is a photographic representation of a film dried by
`conventional drying processes.
`FIG. 16 is a photographic representation of a film dried by
`conventional drying processes.
`FIG. 17 is a photographic representation of a film dried by
`the inventive drying process.
`FIG. 18 is a photomicrographic representation of a film
`containing fat coated particles dried by the inventive drying
`process.
`FIG. 19 is a photomicrographic representation of a film
`containing fat coated particles dried by the inventive drying
`process.
`FIG. 20 is a photomicrographic representation of a film
`containing fat coated particles dried by the inventive drying
`process.
`FIG. 21 is a photomicrographic representation of a film
`containing fat coated particles dried by the inventive drying
`process.
`FIG. 22 is a photomicrographic representation of a film
`containing fat coated particles dried by the inventive drying
`process.
`FIG. 23 is a photomicrographic representation of a film
`containing fat coated particles dried by the inventive drying
`process.
`FIG. 24 is a photomicrographic representation of a film
`containing fat coated particles dried by the inventive drying
`process.
`FIG. 25 is a photomicrographic representation of a film
`containing fat coated particles dried by the inventive drying
`process.
`FIG. 26 is a photomicrographic representation of fat coated
`particles not in film, heated for 9 minutes at 80° C.
`FIG. 27 is a photomicrographic representation of fat coated
`particles not in film, heated for 9 minutes at 80° C.
`FIG. 28 is a photomicrographic representation of fat coated
`particles at room temperature prior to processing.
`FIG. 29 is a photomicrographic representation of fat coated
`particles at room temperature prior to processing.
`FIG. 30 is a photomicrographic representation of fat coated
`particles at room temperature prior to processing.
`FIG. 31 is a photomicrographic representation of fat coated
`particles at room temperature prior to processing.
`
`10
`
`15
`
`20
`
`25
`
`30
`
`35
`
`40
`
`45
`
`50
`
`55
`
`60
`
`65
`
`6
`FIG. 32 is a graphical representation of a microarray on the
`blood of a human after ingestion by the human of a film ofthe
`present invention containing a bovine derived protein.
`FIG. 33 is a graphical representation of the temperature
`differential between the inside and outside of a film of the
`
`present invention during drying.
`FIG. 34 is a graphical representation of the temperature
`differential between the inside and outside of a film of the
`
`present invention during drying.
`FIG. 35 is a schematic representation of a continuously-
`linked zone drying apparatus in accordance with the present
`invention.
`
`FIG. 36 is a schematic representation of a separate zone
`drying apparatus in accordance with the present invention.
`FIG. 37 is a schematic representation of a extrusion device
`for use in producing films of the present invention.
`FIG. 38 provides a table of various compositions of the
`invention, as well as certain properties.
`
`DETAILED DESCRIPTION OF THE INVENTION
`
`For the purposes ofthe present invention the term non- self-
`aggregating uniform heterogeneity refers to the ability of the
`films of the present invention, which are formed from one or
`more components in addition to a polar solvent, to provide a
`substantially reduced occurrence of, i.e. little or no, aggrega-
`tion or conglomeration of components within the film as is
`normally experienced when films are formed by conventional
`drying methods such as a high-temperature air-bath using a
`drying oven, drying tunnel, vacuum drier, or other such dry-
`ing equipment. The term heterogeneity, as used in the present
`invention, includes films that will incorporate a single com-
`ponent, such as a polymer, as well as combinations of com-
`ponents, such as a polymer and an active. Uniform heteroge-
`neity includes the substantial absence of aggregates or
`conglomerates as is common in conventional mixing and heat
`drying methods used to form films.
`Furthermore, the films of the present invention have a
`substantially uniform thickness, which is also not provided by
`the use ofconventional drying methods used for drying water-
`based polymer systems. The absence of a uniform thickness
`detrimentally affects uniformity of component distribution
`throughout the area of a given film.
`The film products of the present invention are produced by
`a combination of a properly selected polymer and a polar
`solvent, optionally including an active ingredient as well as
`other fillers known in the art. These films provide a non-self-
`aggregating uniform heterogeneity of the compon
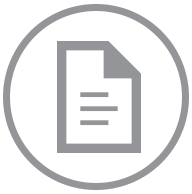
Accessing this document will incur an additional charge of $.
After purchase, you can access this document again without charge.
Accept $ ChargeStill Working On It
This document is taking longer than usual to download. This can happen if we need to contact the court directly to obtain the document and their servers are running slowly.
Give it another minute or two to complete, and then try the refresh button.
A few More Minutes ... Still Working
It can take up to 5 minutes for us to download a document if the court servers are running slowly.
Thank you for your continued patience.
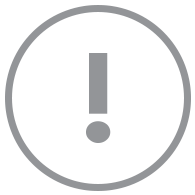
This document could not be displayed.
We could not find this document within its docket. Please go back to the docket page and check the link. If that does not work, go back to the docket and refresh it to pull the newest information.
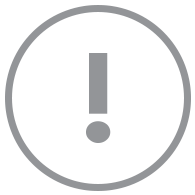
Your account does not support viewing this document.
You need a Paid Account to view this document. Click here to change your account type.
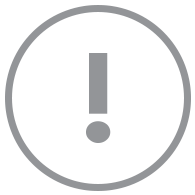
Your account does not support viewing this document.
Set your membership
status to view this document.
With a Docket Alarm membership, you'll
get a whole lot more, including:
- Up-to-date information for this case.
- Email alerts whenever there is an update.
- Full text search for other cases.
- Get email alerts whenever a new case matches your search.
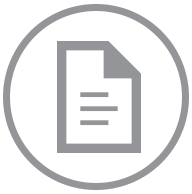
One Moment Please
The filing “” is large (MB) and is being downloaded.
Please refresh this page in a few minutes to see if the filing has been downloaded. The filing will also be emailed to you when the download completes.
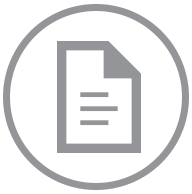
Your document is on its way!
If you do not receive the document in five minutes, contact support at support@docketalarm.com.
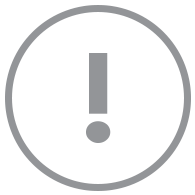
Sealed Document
We are unable to display this document, it may be under a court ordered seal.
If you have proper credentials to access the file, you may proceed directly to the court's system using your government issued username and password.
Access Government Site