`
`1111111111111111111111111111111111111111111111111111111111111
`US007821502B2
`
`c12) United States Patent
`Hristov
`
`(10) Patent No.:
`(45) Date of Patent:
`
`US 7,821,502 B2
`Oct. 26, 2010
`
`(54) TWO-DIMENSIONAL POSITION SENSOR
`
`2007/0008299 AI
`
`112007 Hristov
`
`(75)
`
`Inventor: Luben Hristov, Southampton (GB)
`
`(73) Assignee: Atmel Corporation, San Jose, CA (US)
`
`( *) Notice:
`
`Subject to any disclaimer, the term of this
`patent is extended or adjusted under 35
`U.S.C. 154(b) by 912 days.
`
`(21) Appl. No.: 11/428,670
`
`(22) Filed:
`
`Jul. 5, 2006
`
`(65)
`
`Prior Publication Data
`
`US 2007/0008299 Al
`
`Jan. 11,2007
`
`Related U.S. Application Data
`
`FOREIGN PATENT DOCUMENTS
`
`EP
`
`0609021 A
`
`8/1994
`
`OTHER PUBLICATIONS
`
`IBMTechnica!DisclosureBulletin, vol. 21, No.10, Mar. 1979, N.D.
`Lupat et a!. "One layer optically transparent keyboard for input
`display", p. 3904 to 3906.
`"Chinese Application Serial No. 200610143149.0 Office Action
`Mailed Oct. 9, 2009", 6 pgs.
`Serial
`Application
`200610143149.0,
`"Chinese
`200610143149.0, Office Action mailed Apr. 10, 2009", 8 pgs.
`* cited by examiner
`Primary Examiner-Srilakshmi K Kumar
`(74) Attorney, Agent, or Firm-Schwegman, Lundberg &
`Woessner, P.A.
`
`No.
`
`(60) Provisional application No. 60/697,613, filed on Jul. 8,
`2005.
`
`(57)
`
`ABSTRACT
`
`(51)
`
`Int. Cl.
`G06F 31041
`(2006.01)
`G06F 31044
`(2006.01)
`(52) U.S. Cl .
`.................................... 345/173; 178/18.06
`(58) Field of Classification Search ................. 345/156,
`345/173-178; 178/18.01' 18.06
`See application file for complete search history.
`
`(56)
`
`References Cited
`
`U.S. PATENT DOCUMENTS
`
`4,550,221 A
`4,954,823 A
`5,463,388 A *
`5,730,165 A
`5,844,506 A
`5,861,583 A
`6,288,707 B1
`6,466,036 B1
`
`10/1985 Mabusth
`9/1990 Binstead
`10/1995 Boie et al ..................... 341133
`3/1998 Philipp
`12/1998 Binstead
`111999 Schediwy et al.
`912001 Philipp
`10/2002 Philipp
`
`A capacitive position sensor for determining the position of
`an object along first and second directions is described. The
`sensor comprises a substrate having an arrangement of elec(cid:173)
`trodes mounted on a single surface thereof. The electrodes are
`arranged so as to define an array of sensing cells arranged in
`columns and rows to form a sensing area. Each of the sensing
`cell including a column sensing electrode and a row sensing
`electrode with the column sensing electrodes of sensing cells
`in the same column being electrically coupled together and
`the row sensing electrodes of sensing cells in the same row
`also being electrically coupled together. Row sensing elec(cid:173)
`trodes of sensing cells at opposing ends of at least one of the
`rows are connected together by an electrical connection made
`outside of the sensing area so that there is no requirement for
`electrical connections to cross within the sensing area, thus
`providing a capacitive position sensor having a sensing area
`with electrodes on only one side of a substrate.
`
`24 Claims, 8 Drawing Sheets
`
`-X I -Y1
`-X2 lUlli]Y2
`li!BX3
`iil!?Jj'jY3
`QX4 fZ2!Y4
`~Y5
`
`EXHIBIT 1004
`IPR Petition for U.S. Patent No. 8,004,497
`
`
`
`US. Patent
`
`Oct. 26, 2010
`
`Sheet 1 0f 8
`
`US 7,821,502 B2
`
`1 1
`
`vulva",
`
`"Mann";
`
`- 1, I. I I 1 2+,
`
`
`
`US. Patent
`US. Patent
`
`0a. 26, 2010
`Oct. 26, 2010
`
`Sheet 2 of8
`Sheet 2 of8
`
`US 7,821,502 B2
`US 7,821,502 B2
`
`
`
`.\
`-
`.
`=
`\Sx
`
`“mm“
`\
`s
`
`, ,
`
`n \~\
`2‘ c }
`,
`\
`\D‘L‘
`.
`,x
`s
`;
`...m.m..........‘.‘..0.‘n.,.\.,.N.mM»..m“m»““N“ww~“I“N»~~~~~~~~~~~~‘~~~\~~~~\\,,\\m\m\mwm\\m\
`
`.
`6
`\
`\
`.
`\
`\
`x
`0
`g
`\
`x
`
`
`
`
`
`
`
`
`
`§
`
`
`
`:-
`
`§
`§
`\
`E
`\
`E
`S
`\
`
`
`'
`
`.-
`..
`i
`g
`‘Q E
`>‘
`‘.mm‘m.‘:
`,.
`..
`
`,
`\
`,
`,.
`$\\V\\\\\\\\\\\\\\\\\V\\\\\\\\\\\\\\W\\N\WWWWWWW “WWWWQ
`i
`\
`4
`,
`Q {.xxmwwwxwwwwwm wwwnwwe.»xxmm».\xxxxxm“mx\\\\\\\\\\\\\\q §
`§
`,-
`x
`\
`§ % W\W&\m\\wwm\m\ \m\\\\\mwm\\mmmxmmmmxmmmmxxxxmg § §
`$
`\-
`s
`1
`
`§ % § ¥\\\\\\mmm\\\\mmmmm\\\mmw~§u\\\wfiwflfiwmmwmwmm,‘ § S g
`§
`§ § E § \vxwmmwmmmwxmfimxmfia
`mmwxmmxmxmwmwx ' § $ $ i
`\ \2‘
`3
`,
`\
`§ \
`,
`\
`-
`§ \ \ § \
`\
`‘
`\
`§ §
`-
`‘
`x \ \ \ §
`x
`‘
`\§
`§
`2“
`\
`5
`,1
`\§\\
`‘.................... p“ \
`\
`k
`0
`,
`\ v
`\\
`~.
`\ § \ W
`*
`:
`
`
`
`
`E gmm \\‘“ -
`m ‘\\\\ WW‘k § $ % E
`S §
`§
`§
`§
`\
`\
`\
`‘
`»>
`v
`‘
`\
`\ §
`§
`1
`\
`‘
`'
`‘
`x
`\
`§ \ \
`
`\
`~
`2
`\
`‘
`: W ,
`\QWWV
`E S“
`'\ .; W :
`~
`~
`§
`S §
`
`
`
`,
`~‘\Ww~~
`i S §
`§
`\“ k
`‘
`.-§ §
`t
`\
`.,
`
`‘
`i
`\<§\5\\<\~\§s§-§5\§“\
`-.
`\‘\
`g
`E
`§ g‘
`y
`
`\\\\<L\Ly.\\:\<\(\\'\§”“
`\ “‘“
`.
`.
`t
`§ §
`
`§
`\
`E
`3
`c; §
`§
`_.
`l
`\
`‘0'
`k
`‘
`$
`’f’t’r’.’
`
`
`
`
`
` ,...22,,,ay,,,,,,”m,m,,-,.mm”m“\\“\.,“,‘.,\~,~V“,\>u
`
`1”,,”,1,............./......,,..2”flyflfluflyflflflfl.......u.h.,..,..,,,,,,,.......1..,..................
`
`.-‘= “‘0
`“ -
`:11
`
`.
`
`. . \
`-,.
`I.5-,“
`
` ”x.“
`
`
`
`‘
`
`..
`.
`~z
`«-
`§;.;
`
`:
`
`a :
`
`(«HMM»MH
`
`.......‘r,‘rrr{Irrttttttrrrrrtrrvatr/III/”rddvdadd’44
`,..........‘............,...........-...........,..........
`
`,.,
`» \
`.\'
`3&3
`
`
`
`
`
`3,
`-3:
`‘»‘~»““«~«««-«
`
`
`
`
`
`
`\
`
`-.\~~~~~~~»»~»~»»~»~“»«»““«“«\\
`-..0..000000
`
`.
`.~
`,
`:\\\\\\\.\. \uuuxuuxuw»mmxmmx
`.
`.
`\
`a
`,
`§
`\. _.- c
`\
`.v
`k
`:
`~
`.-\
`:
`.
`§
`.
`.x
`\ \ 5
`k
`~
`I. ‘KKK§K\\\\\KKssK\'K\s\\KKK\K\\\\\\\\\\\\\\\E\\\,\\,\\,l,
`
`
`$$
`3““. \\\\‘.\\\\~A\m~»»» , >>.
`
`
`
`.
`1
`
`.
`i
`:
`
`
`
`\kx'
`
`
`.'.\\\\\\\\\\\\s\\\‘
`
`
`
`~\~~\
`
` \N..\.\
`\\\
`}x
`
`
`
`
`US. Patent
`U S. Patent
`
`0a. 26, 2010
`Oct. 26, 2010
`
`Sheet 3 of8
`Sheet 3 of8
`
`US 7,821,502 B2
`US 7,821,502 B2
`
`
`
`
`
`“.9
`J.A\
`.7,“
`\.,_
`
`
`f“""“"
`
`I;z
`
`[W-.
`
`I
`:0“
`I
`‘ILJJ;
`
`I.
`
`7,I5..5"
`
`‘
`§
`§
`a
`t
`0
`m
`.~'
`.
`5
`:
`§
`.
`.\
`i
`k
`t
`\'
`
`"
`
`.
`:
`‘:
`:
`
`:
`.
`'
`:
`:
`i
`i
`
`t
`t
`g
`K
`t
`
`\
`
`“‘-\
`..
`E N\\\
`:
`s
`.
`E
`.
`=
`:
`5
`g
`t
`‘
`.
`t
`-
`t
`:
`:
`t
`:
`:
`l
`:7
`t
`‘3
`'
`
`x
`
`‘
`
`
`
`‘
`1
`1
`1
`1
`4
`4
`‘
`
`:
`1
`1
`
`‘
`
`:
`1
`:
`l
`I
`:
`.
`:
`,
`.
`:
`«
`3
`:
`:
`5
`\
`
`‘
`x.‘
`w -
`i‘“"'
`was“ W \\
`a
`.
`.. no,
`,
`.
`3,“.
`
`
`
`‘
`fix
`,
`-
`§
`‘
`-
`\
`\\
`,
`0
`.
`a
`.
`.
`§
`\
`.
`§
`..
`
`§x
`A
`\
`.
`‘
`.
`.
`\
`0
`-
`§
`‘
`.
`x
`-
`Q
`0
`.
`k
`0
`.
`
`:'\
`‘i
`:
`‘
`A
`,
`Q
`‘
`k
`,
`.
`x
`k
`t
`:
`:
`,
`.
`.
`x
`~'\
`,
`-
`k
`.
`.
`,
`.
`,
`.
`.
`1
`,
`-
`k
`\1
`n
`u
`‘
`‘
`.
`,
`~
`»
`t
`:
`.
`x
`
`
`
`
`
`
`
`
`.w‘\\\\\\\\\\f.\\s\\\\‘\\\\\\\:\,\\\;\\,\'\\\\\\,\,\\,\;‘,n ,ulununuuu.x,‘“nukuuuxuuuna., .- . ,- . q , ; ~ - . ,
`
`
`
`
`
`.
`
`
`
`\x
`
`1 k
`
`
`
`‘
`.
`:
`1
`«
`‘
`.
`
`L
`\
`.
`r
`-
`>
`y
`~
`,
`
`‘
`‘
`‘
`‘
`,
`‘
`
`-
`-,
`\
`a
`.
`\
`
`
`
`.
`f... .
`... k e‘
`§ \
`.
`._ 1‘,
`\w
`
`‘
`.
`
`
`
`U S. Patent
`
`0a. 26, 2010
`
`Sheet 4 of8
`
`US 7,821,502 B2
`
`i...
`
`W
`
`at:
`
`\\\\\\\\\\\\\\~
`
`. . .
`
`
`
`‘‘‘‘‘‘‘‘‘‘‘‘‘‘‘‘‘ .4. . v I \\\\\h.l
`
`N::::
`
`m
`
`
`
`llllllll?ll lllllv
`
`i
`
`
`
`US. Patent
`U.S. Patent
`
`0a. 26, 2010
`Oct. 26, 2010
`
`Sheet 5 of8
`Sheet 5 of 8
`
`US 7,821,502 B2
`US 7,821,502 B2
`
`\
`\xxxw333'3.3Ngwxxxxxwxmmumxmm,9,333x\mo.moam\\xxmmnmmxmmmmxxmmnnmm
`x\\\xxxxxw».xmmmmmx\xmmmm\\\\\m\\m\\m\mmwmm\\\\\\\\1\\\m1\\\“
`
`‘H\\\\‘9"\\\\‘{\\\\'{\'{{\\\V\\\\‘h‘h\\\\\%\\\\\\\\\\\“\V\W\‘N\\\\\'%\\WWV\\\V\‘I\\\\\‘N\N\W\\\\\\\
`\\\\\\\\\\\\W\\\\\\\\\\\\\\\\\\\\W“WW'KW‘A‘RN§“\\\\\W\\W§§W§§%\3“»55?555$“\“
`
`V\.\WV\.\\.\\\\\\V\\\\\.\.\.\\.\.\\\\.\\.\.\.«\\§\\\%§\\
`
`\\
`‘N
`mm
`‘ER‘
`N
`'\\\
`.‘NN
`_ N
`‘x.N
`v)v:
`N‘N“:
`.\\\\....\u\w“
`KEN
`KNEE...
`N
`mm:
`N: N
`NW
`RWR‘N?
`mkxk
`
`ENNNNN\.NYENNNN
` Q§~Ox§,,,,,
`
`E\\§E§E§E§§E&E§E§%§E§§Sfi§§i
`
`§N\~§§~E§
`
`N \
`
`I?
`
`................~\\. V
`
`
`
`e!!--!..........H\\.«\:\.n
`
`,
`
`Ix\
`
`E\\\\\\\\\\\\\\§\\\\\\\\A\\\\\\\$§\\\\\\\\\\\V\\§\\\\E\\\\§\§i
`\V\\\\\\\§\\\\V\h\\h\\\s\§\\\\§§~§§\\\V§\\§\§\
`
`$E§\\\\\\§\EE\\§N
`va‘gwEYV?AVE
`
`\ N .
`\«~\>\_~\,\\
`\\\\-\.me\'\
`4‘2“
`
`“$7“th
`»»¢~\\~
`\~_\~\\,...“\.\N\\.
`\
`\
`v93“
`
`\\\\\\\\\mm
`
`.\§
`LLxv}.it
`
`N
`
`,
`
`r!\xx;
`
`“URN”
`
`\“nx‘xnnsx;
`
`nhxw‘n\w‘~\'“‘w
`.~~\»»¢\\-\~“
`
`
`
`
`
`
`
`
`
`
`
`
`US‘ Patent
`
`0a. 26, 2010
`
`Sheet 6 of8
`
`US 7,821,502 B2
`
`@
`
`wmwkwww .
`
`
`
`US. Patent
`
`0a. 26, 2010
`
`Sheet 7 of8
`
`US 7,821,502 B2
`
`LHDLLLLLLLL
`
`
`
`US. Patent
`
`0a. 26, 2010
`
`Sheet 8 of8
`
`US 7,821,502 B2
`
`B.x2“......“
`
`
` xi?\0....5“5.....Se
`$35.“.1.5....83....
`
`
`9..muan”)...H......
`
`.1...-255:-9w.\&\1\..1...‘$33.“.
`
`
`x..1.
`
`.....A.e..t..
`\wa\mm“V.ma..‘n..‘.x..awt\J..\mW.Ha..«h.J......n5.”:“xxng\\\\\\\x\\\\\\\x\v\xx\x\\\ss
`
`v‘\\\\\\\\~\\x\\\\.\.\\\\\\\\\\\\\\\\\\\\\\\\\\\\\\\\\s\\\“
`
`
`
`
`2....u“2“....“\..HI.|-.I.“I»|..
`
`.v.m....“t“.1.n\........a.\\ITmw
`
`a2“mu
`
`.a.
`
`._
`
`o“Rx-n,S..i
`U.....
`
`‘\\
`
`Pan
`
`‘.i\
`
`....nS,.x.
`
`..s...
`
`\
`
`.....1““$3.5!u“m2.m“9“m6x3a
`...?m“m““m.A.mm“m“v.x“xw““.x.Km8mx..mmm““8.......t$9..w.a.J...e“-.Ia...s\\.\
`Sm“m........““we...
`...k‘Ixa\u.0\..\...
`\5mmmawaii‘
`
`
`“Si..\..x\..u.........x......x....x....\....\....£....\.:.......\.S...........\§........\\..$t\$“‘““““‘‘x.......v.m_mKL...M.1.u“n.1.
`.““....1\..\““3.5.5
`
`
`
`
`US 7,821,502 B2
`
`1
`TWO-DIMENSIONAL POSITION SENSOR
`
`BACKGROUND OF THE INVENTION
`
`The invention relates to a capacitive position sensor for
`determining the position of an object Within a tWo-dimen
`sional sensing area.
`The use of tWo-dimensional touch-sensitive position sen
`sors is becoming more common. Examples include the use of
`position sensors in laptop computers in place of mouse point
`ing devices, as control panels for receiving user inputs to
`control an appliance, or particularly as a glass touchscreen
`apparatus having an X-Y coordinate output. Some applica
`tions require a clear sensing layer so that a display can be
`vieWed beneath the screen, While others only require an
`opaque touch surface, for example for a keypanel on a kitchen
`appliance or a PC peripheral.
`Touch-sensitive position sensors are frequently preferred
`to mechanical devices because they provide for a more robust
`interface and are often considered to be more aesthetically
`pleasing. Furthermore, because touch-sensitive position sen
`sors require no moving parts to be accessible to a user, they
`are less prone to Wear than their mechanical counterparts and
`can be provided Within a sealed outer surface. This makes
`their use Where there is a danger of dirt or ?uids entering a
`device being controlled particularly attractive.
`There exists a large body of art involving 2D touchpanels
`and screens. They can be generally divided into tWo classi?
`cations: those that report an X-Y coordinate of a more or less
`continuous nature (‘XY’ type), and those that have a discrete
`sensing surface (‘discrete’ type) having prede?ned key areas
`that are ?xed by physical geometry. The XY type ?nd domi
`nant use over LCD or other display types While the latter ?nd
`use in ?xed function key panels. There are exceptions to this,
`for example touchpad surfaces on laptops report XY position
`but are opaque. XY types invariably involve a sensing surface
`on the user-side or ‘?rst surface’ of the touch area. For
`example, both continuous resistive and capacitive touch
`screens involve a sensing layer that must be either physically
`depressed by the user or touched almost directly, or at most
`through a thin layer of insulation (as in mouse touchpads).
`These types require that the product have a beZel opening to
`alloW direct or near-direct contact by the user With the sensing
`layer. A signi?cant disadvantage of these types is that there
`has to be an opening in the panel, Which requires sealing
`against moisture and dirt and hence is expensive to mount.
`Furthermore the sensing layer is directly exposed to abuse
`and can be easily damaged by sharp objects or abrasion.
`While robust capacitive types are knoWn Which have buried
`Wires inside a glass layer (eg US. Pat. No. 5,844,506), these
`still require a beZel opening in a panel Which must be sealed,
`and require tWo sensing layers as a matrix due to the need to
`cross X andY conductors. Furthermore these screens are very
`expensive to produce and in fact cannot be produced on a
`mass scale; additionally the sensing circuitry is knoWn to be
`complex and expensive.
`In the ?eld of discrete touch buttons, it has been knoWn for
`some time that capacitive keys can be placed behind a solid
`surface having no requirement for a beZel opening. HoWever
`these types only provide for limited resolution, as prede?ned
`by the location of discrete electrode shapes. An example of
`this can be found in US. Pat. No. 4,954,823, FIGS. 4 and 6.
`While it is Well knoWn that these electrodes can be made of a
`single layer of clear conductor such as Indium Tin Oxide
`(‘ITO’) to alloW placement over a beZel-less display, for
`example by the application of the layer as a ?lm on the back
`of a subsection of a panel, nevertheless the technology is
`
`20
`
`25
`
`30
`
`35
`
`40
`
`45
`
`50
`
`55
`
`60
`
`65
`
`2
`limited to discrete touch areas based on the number, siZe, and
`placement of discrete electrodes.
`FIG. 1 schematically shoWs in plan vieW a touch pad 2 of
`the type described in US. Pat. No. 4,954,823, but laid out in
`an orthogonal array. The touch pad 2 comprises a grid of
`discrete electrodes 4 mounted on an insulating substrate 6.
`Each electrode is connected to a channel of capacitance mea
`surement circuitry in a controller 8. US. Pat. No. 5,463,388
`describes this geometry in passing in conjunction With its
`FIG. 1, to shoW hoW such an array can be used to determine a
`position of an object proximate the sensing layer via a method
`of determining a centroid of the signals from each pad. HoW
`ever U.S. Pat. No. 5,463,388 fails to shoW hoW to implement
`such a design and describes instead a matrix of conductors
`along With a centroidal calculation of continuous X-Y posi
`tion. In fact it is not practical to have so many sensing chan
`nels as one per sense pad, and a matrix arrangement is much
`more e?icient as described beloW.
`FIG. 2 schematically shoWs a position sensor 12 based on
`a matrix of conductors as described in US. Pat. No. 5,463,
`388. The position sensor 12 comprises a number of vertically
`aligned strip electrodes (columns) 14 mounted on an upper
`surface of an insulating substrate 16 and a number of hori
`Zontally aligned strip electrodes (roWs) 15 mounted on an
`opposing loWer surface of the insulating substrate. Each ver
`tical strip electrode is connected to a channel of capacitance
`measurement circuitry in a controller 18. Thus, this type of
`position sensor alloWs an X-Y coordinate output of a continu
`ous nature by means of calculation of a centroid of capaci
`tance among the roWs and columns rather than among dis
`crete pads. HoWever this type requires tWo sensing layers so
`that the matrix traces canbe routed, and does not alloW the use
`of optically clear materials.
`The ideal touch surface Would eliminate the need for a
`beZel opening (or at least, make it optional), have an inexpen
`sive sensing surface that is applied to the rear of the panel
`surface that can project through a reasonable thickness of
`panel material (eg up to 4 mm of glass or plastic), optionally
`require only one sensing layer With no crossovers in the
`sensing region, be usable With clear sensing layers such as
`ITO, have an XY type of output, and have a compact, inex
`pensive driver circuit. This set of ideal goals has not been
`achieved With any knoWn prior art.
`
`SUMMARY OF THE INVENTION
`
`According to a ?rst aspect of the invention there is provided
`a capacitive position sensor for determining the position of an
`object in a sensing area, the sensor comprising a substrate
`having a surface With an arrangement of electrodes mounted
`thereon, Wherein the electrodes de?ne an array of sensing
`cells arranged in columns and roWs to form the sensing area,
`each sensing cell including a column sensing electrode and a
`roW sensing electrode, the column sensing electrodes of sens
`ing cells in the same column being electrically coupled
`together and the roW sensing electrodes of sensing cells in the
`same roW being electrically coupled together, Wherein roW
`sensing electrodes of sensing cells at opposing ends of at least
`one of the roWs are electrically coupled to one another by
`respective roW Wrap -around connections made outside of the
`sensing area.
`Thus a position sensor having electrodes on only a single
`layer of a substrate can be provided. Furthermore, because the
`position sensor employs an intersecting array of columns and
`roWs of sensing electrodes (i.e. a matrix), feWer measurement
`channels are required than With sensors based on an array of
`discrete electrodes.
`
`
`
`US 7,821,502 B2
`
`3
`Because the position sensor is based on sensing electrodes
`on only a single surface, it can be cheaper to manufacture than
`knoWn double-sided position sensors. This also means the
`sensing electrodes can be deposited directly onto a surface for
`Which the opposing surface is inaccessible (e. g. a display
`screen). The sensing electrodes can also be deposited on an
`inside surface of a device housing, thus removing the need for
`any protective covering that might be required if electrodes
`Were also required to be on the outer surface.
`The electrical roW Wrap-around connections may comprise
`a conductive trace mounted on the substrate. This alloWs the
`connection outside of the sensing area to be made in the same
`processing step as the sensing electrodes Within it. Alterna
`tively, the roW Wrap-around connections may be made by a
`free Wire appropriately connected to the respective roW sens
`ing electrodes.
`The column sensing electrodes of a column of sensing cells
`at an edge of the sensing area may be electrically coupled to
`one another by column Wrap-around connections made out
`side of the sensing area in a similar fashion.
`The position sensor may further comprise a plurality of
`capacitance measurement channels connected to respective
`ones of the roWs of roW sensing electrodes and the columns of
`column sensing electrodes, Wherein each measurement chan
`nel is operable to generate a signal indicative of a capacitance
`betWeen its associated column or roW of sensing electrodes
`and a system ground.
`In addition, the position sensor may further comprise a
`processor operable to determine the position of the object
`along the ?rst direction by comparing signals from the col
`umns of column sensing electrodes and along the second
`direction by comparing signals from the roWs of roW sensing
`electrodes.
`This alloWs the determination of the position of a touch to
`be made using otherWise conventional circuitry connected to
`the sensing elements.
`The capacitance measurement channels may comprise
`charge transfer circuitry since this provides a reliable and
`robust Way to measure capacitances of the level that might be
`expected in a typical implementation. HoWever, other forms
`of capacitance measurement circuitry may equally be used. In
`general it is preferential to use a capacitive driver circuit that
`drives all the roWs and column connections in a substantially
`phase-synchronous manner so as to prevent the electric ?elds
`from cross-loading into adjacent roWs and columns. This is
`described also in Us. Pat. No. 5,463,388, Where all the roWs
`and column conductors are driven by a single oscillator.
`The sensing cells may be arranged into three or four col
`umns. This can provide a position sensor With su?icient reso
`lution over a typically siZed sensing area for most applica
`tions.
`The column and roW sensing electrodes in each sensing cell
`may be interleaved With one another (e. g. by spiraling around
`one another or being interlaced/intertwined), especially in
`designs Where the roW and column spacing is larger than that
`of a typical ?nger. This provides for a much more uniform
`blend of signals from the X andY drives in each intersecting
`location, alloWing better position reporting With respect to a
`?nger touching the overlying surface. This is described also in
`Us. Pat. No. 5,463,388, for example FIG. 2. In layouts Where
`the roW and column spacings are similar to or smaller than a
`human ?nger it is su?icient to use other arrangements of
`electrode pattern, for example an array of diamond shapes as
`shoWn in FIG. 8 and described further beloW.
`The position sensor may include a transparent substrate
`and transparent electrodes (e. g. formed from Indium Tin
`Oxide (ITO) deposited on the substrate). This alloWs it to be
`
`20
`
`25
`
`30
`
`35
`
`40
`
`45
`
`50
`
`55
`
`60
`
`65
`
`4
`placed over a display screen Without obscuring What is dis
`played beneath. Thus the display screen might be con?gured
`to display “virtual” buttons to a user that may be selected by
`the user placing their ?nger over the appropriate part of the
`display adjacent the position sensor. The position of the user’ s
`touch can then be compared With the positions of the “virtual”
`buttons being displayed to determine Which one has been
`selected.
`According to a second aspect of the invention there is
`provided a device comprising a position sensor according to
`the ?rst aspect of the invention. The position sensor may be
`used in many types of device. For example the device may be
`a portable/hand-held device, eg a personal data assistant
`(PDA), a multimedia player, a mobile (cell) phone, a re
`con?gurable remote controller, or a still camera or video
`camera, for example With the position sensor overlaying a
`display. Alternatively, the position sensor could equally be
`used in larger scale devices such as kitchen appliances,
`kiosks, and the like. Opaque versions can be fashioned for use
`in PC-style trackpads, keypads, and other human interface
`devices as are Well knoWn in the art.
`According to a third aspect of the invention there is pro
`vided a method of constructing a capacitively sensitive sur
`face disposed on a substrate Which reports an X-Y coordinate
`position of an object Within an active sensing region When the
`object is adjacent to said surface, comprising the steps of: (a)
`depositing a single layer of patterned conductive material in
`the active sensing region, the pattern comprising roWs and
`columns of electrodes connected to individual ones of capaci
`tive sensing channels, and Wherein at least one roW or column
`is broken into a plurality of segments Within the active region;
`(b) connecting the broken segments together With an electri
`cal conductor, Wherein the conductor is made to lie outside of
`the active sensing region; (c) connecting the roWs and col
`umns to individual sensing channels of a multi-channel
`capacitive sensor circuit having multiple outputs representing
`amplitudes of capacitance on the roWs and columns; and (d)
`providing a processor operable to process the multiple out
`puts to determine a coordinate position of the adjacent object
`as an XY location.
`The processor may be operable to compensate for position
`distortion introduced by the physical geometry of the pat
`terned conductive material.
`The processor may also be operable to calculate a centroid
`of the signals across roWs and a centroid of the signals across
`columns.
`According to a fourth aspect of the invention there is pro
`vided a capacitive position sensor for determining the posi
`tion of an object in a sensing area, the sensor comprising a
`substrate having a surface With an arrangement of conductive
`electrodes mounted thereon, Wherein the electrodes de?ne an
`array of sensing cells arranged in columns and roWs to form
`the sensing area, each sensing cell including a column sensing
`electrode and a roW sensing electrode, the column sensing
`electrodes of sensing cells in the same column being electri
`cally coupled together and the roW sensing electrodes of
`sensing cells in the same roW being electrically coupled
`together, Wherein at least one column sensing electrode com
`prises a continuous spine Within the sensing area, and the at
`least one other column is made electrically continuous via
`connections external to the sensing area.
`
`
`
`US 7,821,502 B2
`
`5
`BRIEF DESCRIPTION OF THE DRAWINGS
`
`For a better understanding of the invention and to show
`hoW the same may be carried into effect reference is noW
`made by Way of example to the accompanying drawings in
`Which:
`FIG. 1 schematically shoWs in plan vieW a knoWn tWo
`dimensional capacitive position sensor;
`FIG. 2 schematically shoWs in plan vieW another knoWn
`tWo-dimensional capacitive position sensor;
`FIG. 3 schematically shoWs in plan vieW a tWo-dimen
`sional capacitive position sensor according to an embodiment
`of the invention;
`FIG. 4 schematically shoWs in perspective vieW a device
`including the position sensor of FIG. 3;
`FIGS. 5A and 5B are graphs schematically shoWing
`capacitance as function of column number (FIG. 5A) and roW
`number (FIG. 5B) of sensing cells used to determine the
`position of an object adjacent the position sensor of the device
`shoWn in FIG. 4;
`FIG. 6 schematically shoWs in plan vieW the tWo-dimen
`sional capacitive position sensor and display screen of the
`device shoWn in FIG. 4;
`FIGS. 7 and 8 schematically shoW inplan vieW tWo-dimen
`sional capacitive position sensors according to other embodi
`ments of the invention;
`FIG. 9 schematically shoWs in plan vieW reported positions
`compared to actual positions for an object adjacent a position
`sensor according to an embodiment of the invention; and
`FIG. 10 schematically shoWs in plan vieW a display of the
`outlines of desired key positions compared to the outlines of
`reported key positions for a position sensor according to an
`embodiment of the invention.
`
`DETAILED DESCRIPTION
`
`FIG. 3 schematically shoWs in plan vieW a tWo-dimen
`sional touch-sensitive capacitive position sensor 22 accord
`ing to an embodiment of the invention. The position sensor 22
`is operable to determine the position of an object along a ?rst
`(x) and a second (y) direction, the orientation of Which are
`shoWn toWards the top left of the draWing. The sensor 22
`comprises a substrate 24 having an arrangement of sensing
`electrodes 26 mounted thereon. The sensing electrodes 26
`de?ne a sensing area Within Which the position of an object
`(eg a ?nger or stylus) adjacent the sensor may be deter
`mined. The substrate 24 is of a transparent plastics material
`and the electrodes are formed from a transparent ?lm of
`Indium Tin Oxide (ITO) deposited on the substrate 24 using
`conventional techniques. Thus the sensing area of the sensor
`is transparent and can be placed over a display screen Without
`obscuring What is displayed behind the sensing area. In other
`examples the position sensor may not be intended to be
`located over a display and may not be transparent; in these
`instances the ITO layer may be replaced With a more eco
`nomical material such as a copper laminate PCB, for
`example.
`The pattern of the sensing electrodes on the substrate 24 is
`such as to divide the sensing area into an array (grid) of
`sensing cells 28 arranged into roWs and columns. (It is noted
`that the terms “roW” and “column” are used here to conve
`niently distinguish betWeen tWo directions and should not be
`interpreted to imply either a vertical or a horizontal orienta
`tion.) By Way of example one of the sensing cell 28 is iden
`ti?ed by a dotted outline in FIG. 3. In this position sensor
`there are four columns of sensing cells aligned With the y-di
`rection and ?ve roWs of sensing cells aligned With the x
`
`20
`
`25
`
`30
`
`35
`
`40
`
`45
`
`50
`
`55
`
`60
`
`65
`
`6
`direction (tWenty sensing cells in total). The top-most roW of
`sensing cells for the orientation shoWn in FIG. 3 is referred to
`as roW y1, the next one doWn as roW y2, and so on doWn to roW
`y5. The columns of sensing cells are similarly referred to from
`left to right as columns x1 to x4. Thus the sensing cell 28
`shoWn With a dotted outline in FIG. 3 is at the intersection of
`roW y1 and column x3.
`Each sensing cell includes a roW sensing electrode 30 and
`a column sensing electrode 32. The roW sensing electrodes 30
`and column sensing electrodes are arranged Within each sens
`ing cell 28 to interleave With one another (in this case by
`squared spiraling around one another), but are not galvani
`cally connected. Because the roW and column sensing elec
`trodes are interleaved (intertWined), an object adjacent a
`given sensing cell can provide a signi?cant capacitive cou
`pling to both sensing electrodes irrespective of Where in the
`sensing cell the object is positioned. The characteristic scale
`of interleaving may be on the order of, or smaller than, the
`capacitive footprint of a typical object to be detected to pro
`vide the best results. The siZe and shape of the sensing cell 28
`can be comparable to that of the object to be detected or larger
`(Within practical limits).
`The roW sensing electrodes 30 of all sensing cells in the
`same roW are electrically connected together to form ?ve
`separate roWs of roW sensing electrodes. Similarly, the col
`umn sensing electrodes 32 of all sensing cells in the same
`column are electrically connected together to form four sepa
`rate columns of column sensing electrodes.
`The column sensing electrodes in column x2 are connected
`to one another by a connection 51, also referred to as a spine,
`made Within the sensing area by a part of one of the electrodes
`deposited on the substrate and Which runs betWeen columns
`x2 and x3. This connection runs the length ofthe sensing area.
`Thus a single continuous conductive electrode deposited on
`the substrate 24 provides the column sensing electrodes 32 of
`all of the sensing cells in column x2 and their interconnec
`tions. The column sensing electrodes in column x3 are simi
`larly connected to one another by a connection 53 made
`Within the sensing area, again running betWeen columns x2
`and x3 as a spine. Thus again a single continuous conductive
`electrode deposited in the substrate 24 provides the column
`sensing electrodes 32 of all of the sensing cells in column x3
`and their interconnections.
`The roW sensing electrodes 30 in columns x1 and x2 of roW
`y2 are also connected together by a connection made Within
`the sensing area. Thus a single continuous conductive elec
`trode 34 deposited on the substrate 24 provides the roW sens
`ing electrodes of the sensing cells in columns x1 and x2 of roW
`y2 and their interconnection. The roW sensing electrodes in
`columns x3 and x4 of roW y2 are similarly connected together
`by a connection made Within the sensing area so that a single
`continuous electrode 36 again provides these roW sensing
`electrodes and their interconnection. HoWever, because of the
`on-substrate connections (spines) running betWeen columns
`x2 and x3 to connect betWeen their respective column sensing
`electrodes, the roW sensing electrodes in columns x1 and x2
`of roW y2 cannot be connected to the roW sensing electrodes
`in columns x3 and x4 of roW y2 by a connection made on the
`surface of the substrate. Thus a connection 38 betWeen the
`roW sensing electrodes at opposing ends of this roW (i.e. in
`columns x1 and x4) is provided outside of the sensing area.
`The connection 38 runs around the outside of the sensing area
`to connect the electrode 34 providing the roW sensing elec
`trodes in columns x1 and x2 of roW y2 With the electrode 36
`providing the roW sensing electrodes in columns x3 and x4 of
`roW y2. Thus all roW sensing electrodes in this roW are elec
`trically connected together. Similar Wrap -around connections
`
`
`
`US 7,821,502 B2
`
`7
`outside of the sensing area are made to ensure the respective
`roW sensing electrodes of the other roWs are connected
`together. It is noted that although one is shoWn in FIG. 3, a
`connection outside of the sensing area betWeen the roW sens
`ing electrodes at opposing ends of roW y1 is not required
`because the spines connecting betWeen the column sensing
`electrodes of columns X2 and X3 need not extend to the very
`edge of the sensing area and a connection running along the
`top edge of the sensing area could be used to connect betWeen
`the roW sensing electrodes in roW y1 (not shoWn).
`Each column sensing electrode in column X1 is formed
`from a separate electrode on the substrate. These separate
`electrodes are connected together by connections 40 made
`external to (i.e. outside of) the sensing area. The column
`sensing electrodes in column X4 are connected together by
`connections 41 in a similar manner to those of column X1. In
`this fashion the outer tWo columns can be discontinuous
`Within the sensing area to alloW access by roW electrodes into
`cells, yet the columns are nevertheless made Whole.
`In this eXample the various connections made outside of
`the sensing area betWeen the roW sensing electrodes in sens
`ing cells at opposing ends of the respective roWs and the
`column sensing electrodes in the columns at the periphery of
`the sensing area are formed from free Wires attached to the
`electrodes of the sensing area as appropriate using conven
`tional techniques. Because the connections are established by
`free Wires, no di?iculties arise from the need for the connec
`tions made outside of the sensing area to cross one another in
`places. In an alternative design the connections made outside
`of the sensing area may be provided by conductive traces on
`the substrate similar to the electrodes forming the sensing
`ar
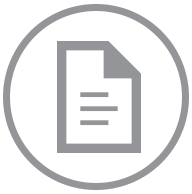
Accessing this document will incur an additional charge of $.
After purchase, you can access this document again without charge.
Accept $ ChargeStill Working On It
This document is taking longer than usual to download. This can happen if we need to contact the court directly to obtain the document and their servers are running slowly.
Give it another minute or two to complete, and then try the refresh button.
A few More Minutes ... Still Working
It can take up to 5 minutes for us to download a document if the court servers are running slowly.
Thank you for your continued patience.
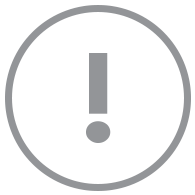
This document could not be displayed.
We could not find this document within its docket. Please go back to the docket page and check the link. If that does not work, go back to the docket and refresh it to pull the newest information.
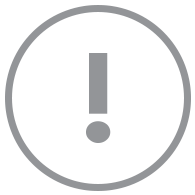
Your account does not support viewing this document.
You need a Paid Account to view this document. Click here to change your account type.
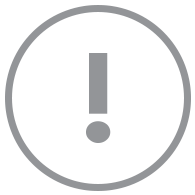
Your account does not support viewing this document.
Set your membership
status to view this document.
With a Docket Alarm membership, you'll
get a whole lot more, including:
- Up-to-date information for this case.
- Email alerts whenever there is an update.
- Full text search for other cases.
- Get email alerts whenever a new case matches your search.
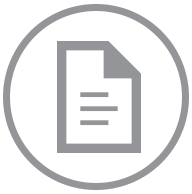
One Moment Please
The filing “” is large (MB) and is being downloaded.
Please refresh this page in a few minutes to see if the filing has been downloaded. The filing will also be emailed to you when the download completes.
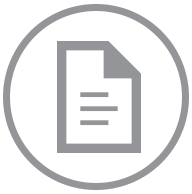
Your document is on its way!
If you do not receive the document in five minutes, contact support at support@docketalarm.com.
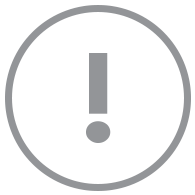
Sealed Document
We are unable to display this document, it may be under a court ordered seal.
If you have proper credentials to access the file, you may proceed directly to the court's system using your government issued username and password.
Access Government Site